Chemical production is a critical and dynamic industry that plays a significant role in our daily lives. From the medicines we take to the food we eat, chemical production has a pervasive impact on modern society. However, this industry also presents several hazards that can compromise the safety of workers, communities, and the environment.
Therefore, ensuring chemical production safety is crucial for sustainable and responsible operations.
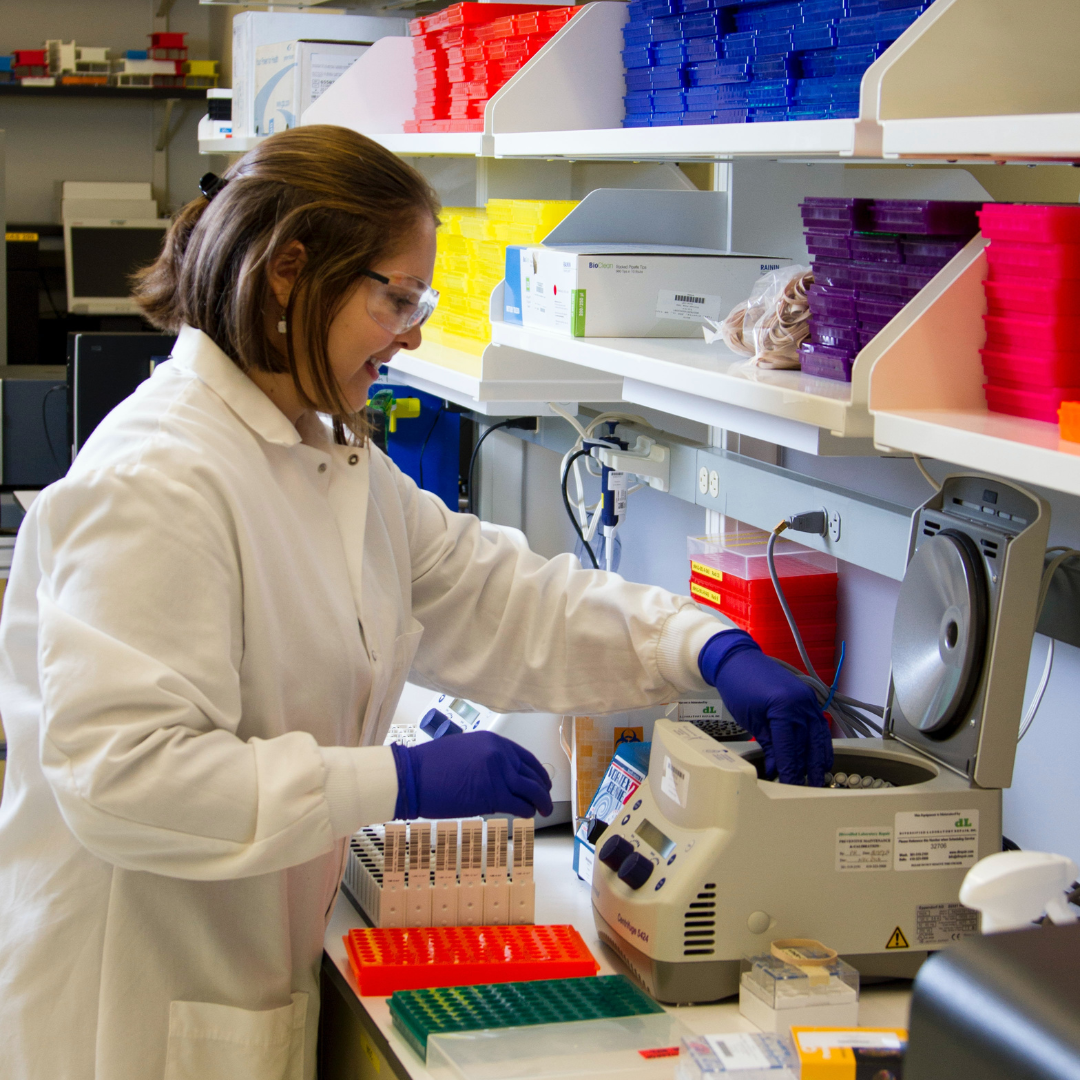
In this article, we will explore practical tips for enhancing chemical production safety, highlighting the best practices and strategies that can help mitigate risks and ensure a safer workplace.
- Why is Chemical Production Safety Important?
- Identifying Hazards
- How to Mitigate Risks Associated with Identified Hazards
- What are SOPs and Why are they Important?
- Maintaining Equipment and Machinery
- How Equipment and Machinery can Pose Safety Risks?
- Importance of Maintenance and Inspection Best Practices
- Promoting a Culture of Safety
- How can MRP system Foster Safety in the Chemical Manufacturing Sector?
- Conclusion
- How can Deskera Help You?
- Key Takeaways
- Related Articles
Why is Chemical Production Safety Important?
Chemical production safety is essential for several reasons. First and foremost, chemical production facilities handle potentially hazardous substances that can cause harm to workers, nearby communities, and the environment. Therefore, it is essential to implement measures that minimize the risk of accidents and incidents that can result in injuries, illnesses, and even fatalities.
In addition, chemical production safety is critical for regulatory compliance. Governments and regulatory agencies have established strict regulations and guidelines that mandate companies to ensure the safety of their workers, communities, and the environment. Failing to comply with these regulations can result in fines, legal consequences, and damage to a company's reputation.
Moreover, chemical production safety can help companies improve their efficiency and productivity. By implementing safety protocols, companies can reduce downtime, minimize equipment damage, and prevent accidents and incidents that can disrupt production processes. This, in turn, can lead to cost savings, increased profitability, and improved competitiveness.
Identifying Hazards
Identifying hazards is the first and most crucial step in ensuring chemical production safety. Hazards can arise from various sources, such as chemicals, equipment, processes, and human factors. Therefore, it is essential to conduct a thorough hazard assessment to identify potential risks and hazards and implement measures to control or mitigate them.
The hazard identification process involves several steps, including:
- Reviewing the chemicals and materials used in the production process: This includes assessing the toxicity, reactivity, flammability, and other properties of the chemicals used.
- Examining the equipment and machinery used in the production process: This includes assessing the risk of mechanical failure, overheating, and other hazards associated with the equipment.
- Analyzing the production process itself: This includes examining the potential hazards associated with the process, such as the risk of spills, leaks, or explosions.
- Considering human factors: This includes assessing the potential risks associated with human error, such as improper handling of chemicals or equipment.
Once potential hazards have been identified, it is essential to implement measures to control or mitigate them. This can include implementing safety protocols, providing personal protective equipment, implementing training programs for workers, and conducting regular safety inspections and audits.
How to Mitigate Risks Associated with Identified Hazards
Mitigating risks associated with identified hazards in chemical production requires a comprehensive approach that considers all aspects of the production process. Here are some steps you can take to mitigate risks associated with identified hazards in chemical production:
- Conduct a hazard analysis: Identify potential hazards in the production process, including chemical, physical, and environmental hazards. This analysis should also consider the potential consequences of these hazards and their likelihood of occurring.
- Develop a risk management plan: Based on the hazard analysis, develop a risk management plan that outlines strategies to mitigate identified risks. The plan should include measures to prevent or minimize hazards, as well as contingency plans to manage incidents if they occur.
- Implement engineering controls: Implement engineering controls such as ventilation systems, chemical storage systems, and automated safety systems to minimize risks associated with chemical production.
- Implement administrative controls: Implement administrative controls such as written procedures, training programs, and regular safety audits to ensure that all personnel understand and follow safe work practices.
- Use personal protective equipment (PPE): Provide appropriate PPE such as gloves, goggles, respirators, and protective clothing to workers to minimize their exposure to hazardous chemicals.
- Conduct regular safety inspections: Conduct regular safety inspections of the production process to identify any new hazards or risks and take appropriate measures to mitigate them.
- Provide emergency response training: Provide emergency response training to workers and establish an emergency response plan that includes procedures for responding to incidents such as spills, fires, and chemical releases.
- Continuously improve safety practices: Continuously improve safety practices by reviewing and updating hazard assessments, risk management plans, and safety procedures based on experience, new information, and best practices in the industry.
What are SOPs and Why are They Important?
SOPs stands for Standard Operating Procedures. They are detailed, step-by-step instructions that describe how to perform a specific task or operation in a consistent and safe manner.
SOPs are critical in chemical production because they ensure that all personnel are aware of and follow standardized procedures for handling chemicals and equipment, which helps to minimize risks and prevent accidents.
Here are some reasons why SOPs are important in chemical production:
- Ensuring consistency: SOPs provide a standardized approach to performing tasks, which helps to ensure consistency in the production process. This is especially important in chemical production, where variations in procedures can have serious consequences.
- Minimizing risks: SOPs describe safe work practices and precautions to be taken when handling hazardous chemicals and equipment. By following these procedures, workers can minimize risks and prevent accidents.
- Complying with regulations: Many regulations and standards require companies to have written procedures for handling hazardous materials. SOPs demonstrate compliance with these regulations and can help to prevent fines and penalties.
- Training new employees: SOPs provide a structured training program for new employees, ensuring that they are properly trained and competent in their duties.
- Improving efficiency: SOPs can help to streamline processes and improve efficiency by identifying best practices and eliminating unnecessary steps.
How to Develop Effective SOPs?
Developing effective SOPs for the chemical production sector involves a comprehensive approach that considers all aspects of the production process. Here are some steps to develop effective SOPs for chemical production:
- Identify the task or process: Identify the specific task or process for which an SOP is required. This should be based on a thorough analysis of the production process, including all potential hazards and risks.
- Determine the scope: Determine the scope of the SOP, including the specific steps and procedures that will be included. Consider factors such as the chemicals being used, the equipment involved, and the specific safety precautions that must be taken.
- Develop the SOP: Develop the SOP in a clear and concise manner, using simple language and easy-to-follow instructions. The SOP should include step-by-step procedures for performing the task or process, as well as safety precautions and any required PPE.
- Include relevant information: Include all relevant information in the SOP, such as chemical names and quantities, required safety equipment, and emergency response procedures. Also, make sure to include any regulations or standards that must be followed.
- Review and revise: Review the SOP with key stakeholders, including workers, supervisors, and safety professionals. Revise the SOP as needed to ensure that it is clear, accurate, and effective in addressing the identified hazards and risks.
- Train personnel: Train personnel on the SOP, ensuring that they understand the procedures and safety precautions. This training should include hands-on practice and verification of competency.
- Update as needed: Review and update the SOP as needed, based on changes in the production process, regulations, or best practices in the industry.
How to Implement and Enforce SOPs in the Workplace?
Implementing and enforcing SOPs in the workplace is critical for ensuring that all personnel are aware of and follow safe work practices. Here are some steps to implement and enforce SOPs in the chemical manufacturing sector:
Communicate the importance of SOPs
Explain the importance of SOPs to all personnel, including the potential hazards and risks associated with chemical production. Make it clear that following SOPs is critical for maintaining a safe workplace.
Provide training
Provide training to all personnel on the SOPs, including hands-on practice and verification of competency. Ensure that workers understand the procedures and safety precautions, and are able to perform the tasks safely.
Monitor Compliance
Monitor compliance with the SOPs to ensure that all personnel are following the procedures correctly. This can be done through regular inspections, audits, and spot-checks.
Provide Feedback
Provide feedback to workers on their performance, both positive and negative. This can help to reinforce the importance of following SOPs and encourage compliance.
Address Non-compliance
Address any instances of non-compliance with the SOPs, including providing additional training and coaching as needed. Also, consider disciplinary action for repeated violations.
Continuously Improve SOPs
Improve the SOPs regularly based on feedback from workers, changes in the production process, and new information or best practices in the industry. Regularly review and update the SOPs to ensure that they remain effective in minimizing risks and preventing accidents.
Establish a Culture of Safety
Establish a culture of safety in the workplace, where following SOPs is seen as a critical part of maintaining a safe environment. Encourage workers to report any potential hazards or unsafe practices, and take prompt action to address them.
Maintaining Equipment and Machinery
Maintaining equipment and machinery is crucial for improving safety in chemical manufacturing companies. Here are some ways in which maintaining equipment and machinery can improve safety:
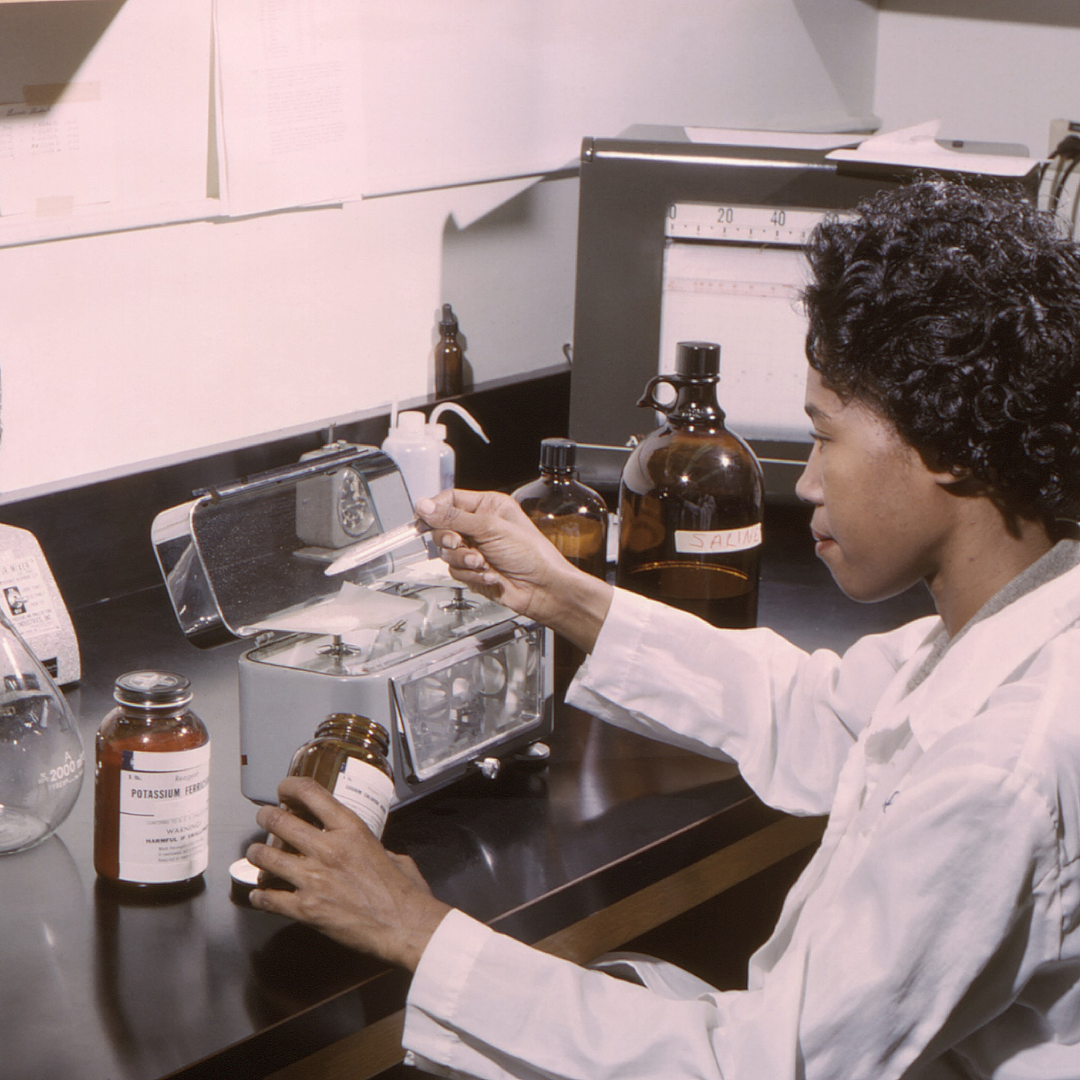
- Minimizes breakdowns: Regular maintenance helps to identify and address potential issues before they become major problems, reducing the likelihood of breakdowns and malfunctions that can lead to accidents.
- Reduces downtime: Preventive maintenance can reduce downtime for repairs, keeping equipment in good working order and minimizing the need for costly repairs or replacements.
- Increases efficiency: Properly maintained equipment and machinery operate more efficiently, reducing the need for overexertion by workers and decreasing the likelihood of accidents caused by equipment failure.
- Improves safety features: Proper maintenance can ensure that safety features are functioning correctly, such as emergency stop buttons, safety interlocks, and alarms.
- Enhances worker safety: Maintained equipment and machinery reduces the likelihood of accidents and injuries caused by malfunctioning equipment, increasing worker safety.
- Compliance with regulations: Proper maintenance of equipment and machinery can help ensure that companies comply with safety regulations and standards.
- Cost-effective: Regular maintenance can extend the life of equipment and machinery, reducing the need for costly replacements and repairs and providing cost savings over time.
How Equipment And Machinery Can Pose Safety Risks?
Equipment and machinery used in chemical manufacturing can pose significant safety risks if they are not properly maintained or operated. Here are some ways in which equipment and machinery can pose safety risks in chemical manufacturing:
Mechanical hazards
Equipment and machinery can have moving parts, pinch points, and other hazards that can cause injuries such as cuts, burns, and bruises.
Electrical hazards
Electrical equipment and machinery can pose risks such as electrocution and fire if they are not properly installed and maintained.
Chemical hazards
Chemical manufacturing involves the use of hazardous substances, and equipment and machinery can pose risks such as chemical spills and leaks, which can lead to exposure and health risks for workers.
Heat and fire hazards
Some equipment and machinery generate heat, and this can pose risks such as fire if there are combustible materials nearby.
Noise hazards
Equipment and machinery can generate high levels of noise that can cause hearing damage if workers are not properly protected.
Ergonomic hazards
Poorly designed equipment and machinery can pose ergonomic risks such as repetitive motion injuries and strains.
Lack of training
If workers are not properly trained in the operation of equipment and machinery, they may not be aware of the risks and how to avoid them, leading to accidents and injuries.
Importance of Maintenance and Inspection Best Practices
Maintenance and inspection best practices are critical for ensuring safety in chemical manufacturing. Here are some reasons why maintenance and inspection are important:
- Prevents equipment failure: Regular maintenance and inspection can identify and address potential issues before they lead to equipment failure, reducing the likelihood of accidents and downtime.
- Minimizes risks: Maintenance and inspection can identify potential safety risks associated with equipment and machinery, allowing companies to take steps to mitigate these risks.
- Extends equipment lifespan: Proper maintenance and inspection can extend the life of equipment and machinery, reducing the need for costly replacements and repairs.
- Compliance with regulations: Regular maintenance and inspection can help companies comply with safety regulations and standards.
- Improves efficiency: Properly maintained equipment and machinery operate more efficiently, reducing the need for overexertion by workers and decreasing the likelihood of accidents caused by equipment failure.
- Enhances worker safety: Maintained equipment and machinery reduces the likelihood of accidents and injuries caused by malfunctioning equipment, increasing worker safety.
- Cost-effective: Regular maintenance can be more cost-effective than waiting for breakdowns to occur, which can be more expensive to repair and lead to costly downtime.
Promoting a Culture of Safety
A culture of safety in chemical manufacturing requires a comprehensive approach that involves leadership commitment, employee involvement, training and resources, communication, safety audits, recognition of safe behavior, and continuous improvement. By prioritizing safety, companies can protect their employees, the environment, and their reputation, while also ensuring compliance with safety regulations.
Here are some ways to promote a culture of safety:
How can MRP system Foster Safety in the Chemical Manufacturing Sector?
Material Requirements Planning (MRP) systems are commonly used in manufacturing to optimize production processes, manage inventory, and schedule production. While the primary goal of an MRP system is to improve efficiency and reduce costs, it can also have a positive impact on safety in chemical manufacturing. Here are some ways that an MRP system can foster safety:
Improved Inventory Management
An MRP system can help ensure that the right amount of inventory is on hand, which can reduce the likelihood of accidents or spills due to overstocking or understocking of materials.
Accurate Forecasting
By accurately forecasting demand for materials and finished products, an MRP system can help prevent overproduction or underproduction, which can lead to safety hazards.
Real-time Monitoring
An MRP system can provide real-time monitoring of production processes and inventory levels, which can help identify potential safety hazards in a timely manner.
Automated Alerts
An MRP system can be programmed to send automated alerts when inventory levels reach a critical point, or when there are deviations from standard operating procedures, which can help prevent safety incidents.
Improved Traceability
An MRP system can improve traceability of materials and finished products, which can help identify the source of a safety incident and prevent similar incidents from occurring in the future.
Enhanced Compliance
An MRP system can help ensure compliance with safety regulations by providing accurate and up-to-date information about inventory levels, production processes, and product quality.
Conclusion
Chemical production safety is of paramount importance for the well-being of workers, the environment, and the community. By implementing practical tips and best practices, chemical manufacturing companies can significantly enhance safety and reduce the likelihood of accidents, incidents, and injuries.
These practical tips include developing effective SOPs, maintaining equipment and machinery, promoting a culture of safety, and encouraging employee engagement in safety efforts. Additionally, the use of modern technologies such as MRP systems can improve safety by providing real-time monitoring, automated alerts, and enhanced compliance.
Ultimately, the success of safety efforts in chemical production depends on the commitment of the entire organization, from top management to frontline workers, to prioritize safety as a core value and integrate it into all aspects of the business.
How can Deskera Help You?
Deskera ERP and MRP systems help you to keep your business units organized. The system's primary functions are as follows:
- Keep track of your raw materials and final items inventories
- Control production schedules and routings
- Keep a bill of materials
- Produce thorough reports
- Make your own dashboards
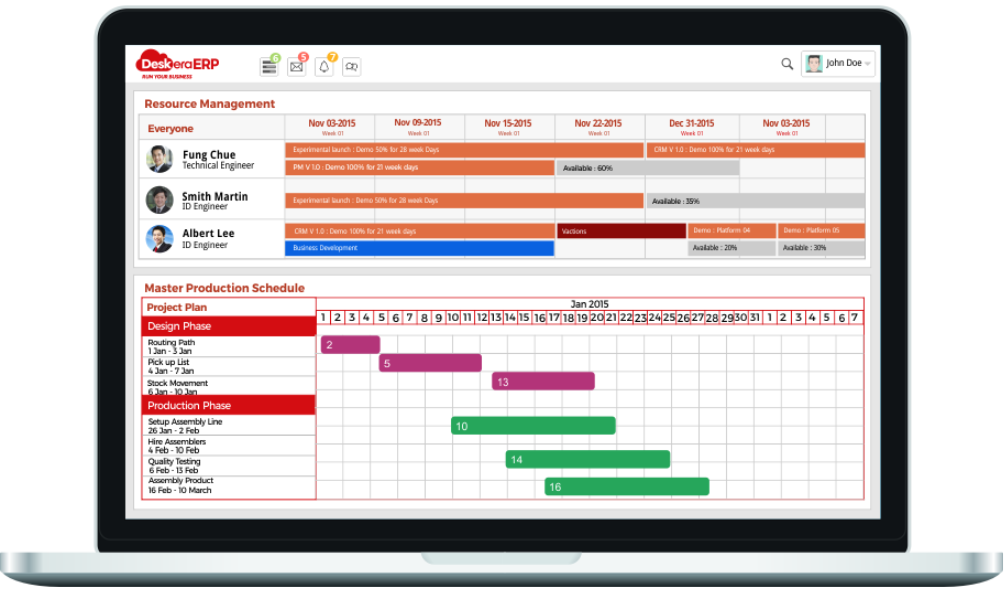
Deskera Books is accounting software that assists small businesses in managing their finances and accounts.
Deskera People provides employee onboarding, leave management, time and attendance monitoring, payroll processing, compensation and benefits, and other features and capabilities.
Deskera CRM is a comprehensive customer relationship management solution that enables businesses of all sizes to better manage their client interactions.
Key Takeaways
- Developing effective SOPs is critical for ensuring consistency and clarity in safety procedures.
- Regular maintenance and inspection of equipment and machinery can prevent safety hazards and reduce the likelihood of accidents.
- Promoting a culture of safety is essential for creating a safe work environment and preventing incidents.
- Encouraging employee engagement in safety efforts through training, communication, and recognition can improve safety performance and foster a sense of ownership.
- Using modern technologies such as MRP systems can improve safety by providing real-time monitoring, automated alerts, and enhanced compliance.
- Continuous improvement of safety processes is necessary to adapt to changing conditions and prevent complacency.
Related Articles
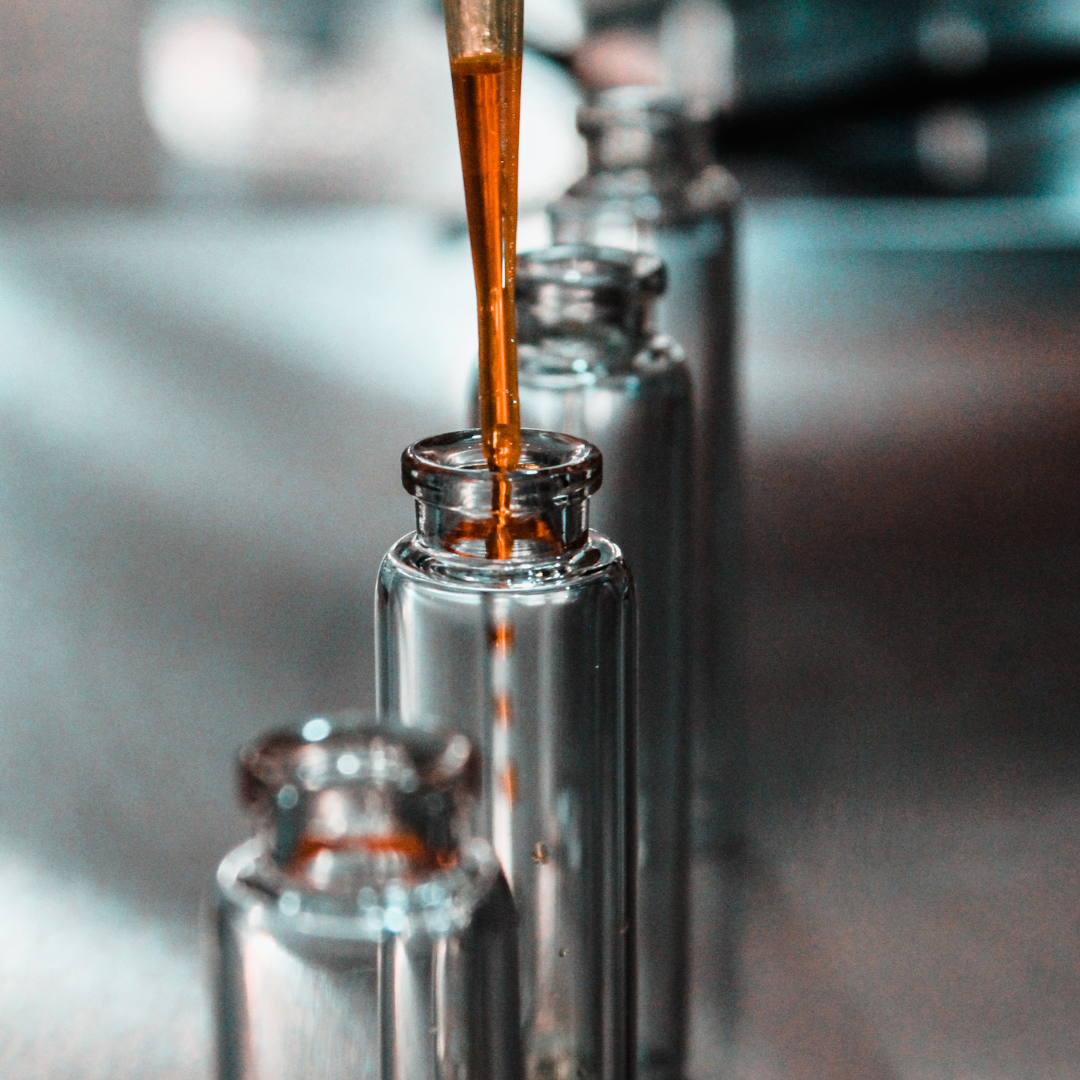
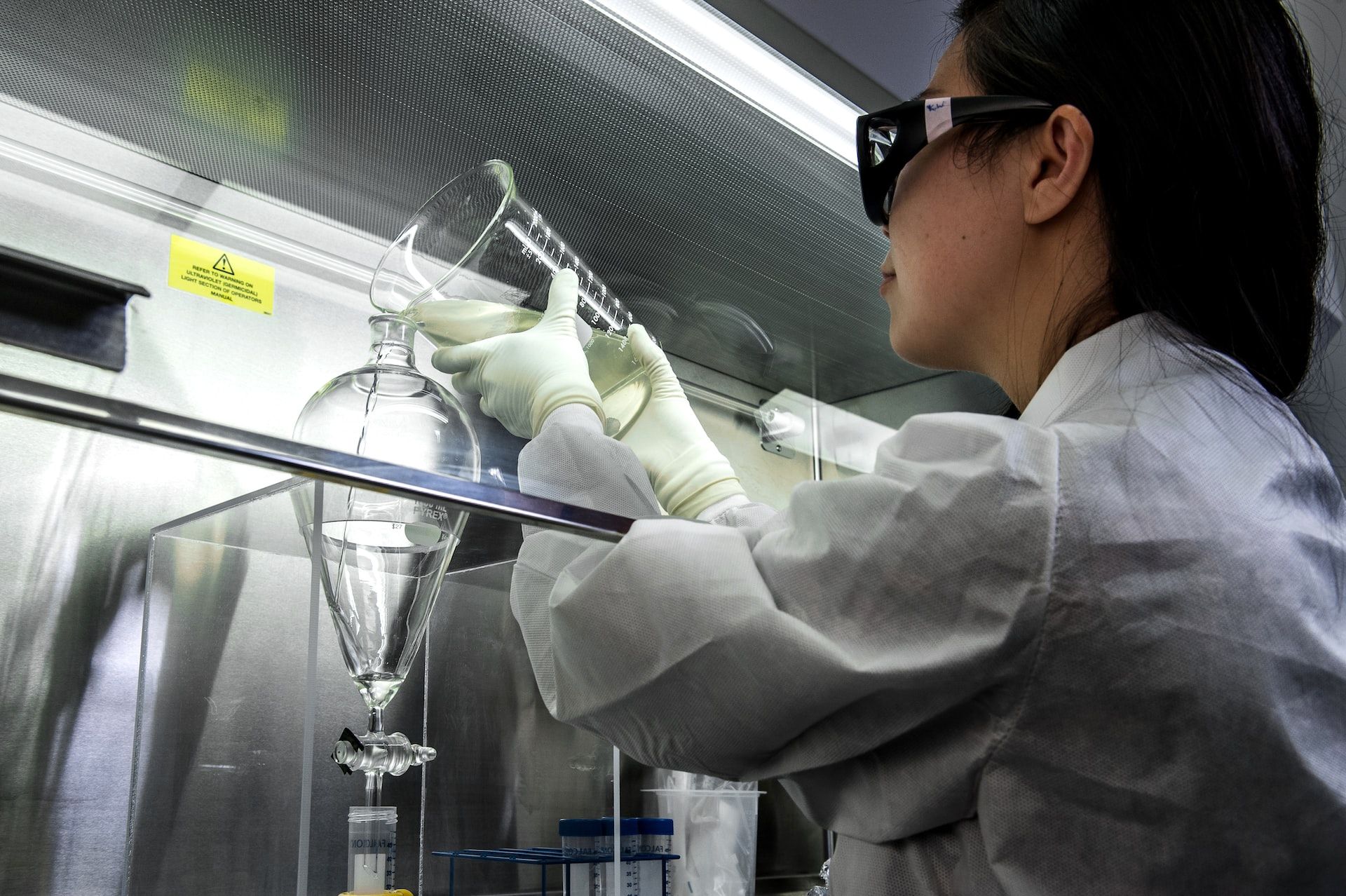
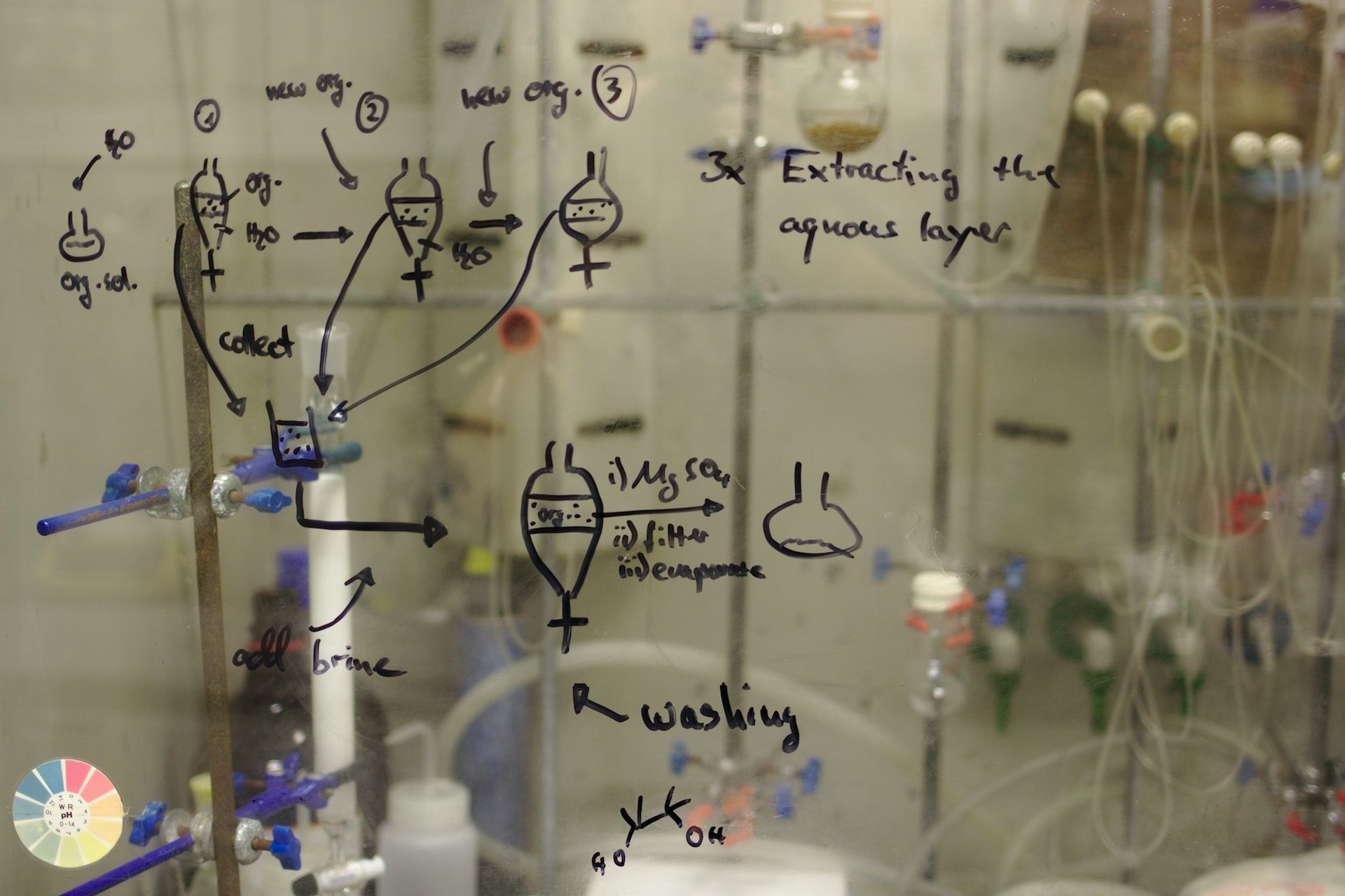