Have you ever wondered what goes into the wood products that we use in our daily lives? From furniture to building materials, the quality and durability of wood products depend heavily on the ingredients used in their production. As a result, selecting the best ingredients for wood production is crucial for creating high-quality, long-lasting wood products.
With the increasing demand for sustainable wood products, businesses must be careful to select the best ingredients for wood production that are not only high-quality but also sustainable.
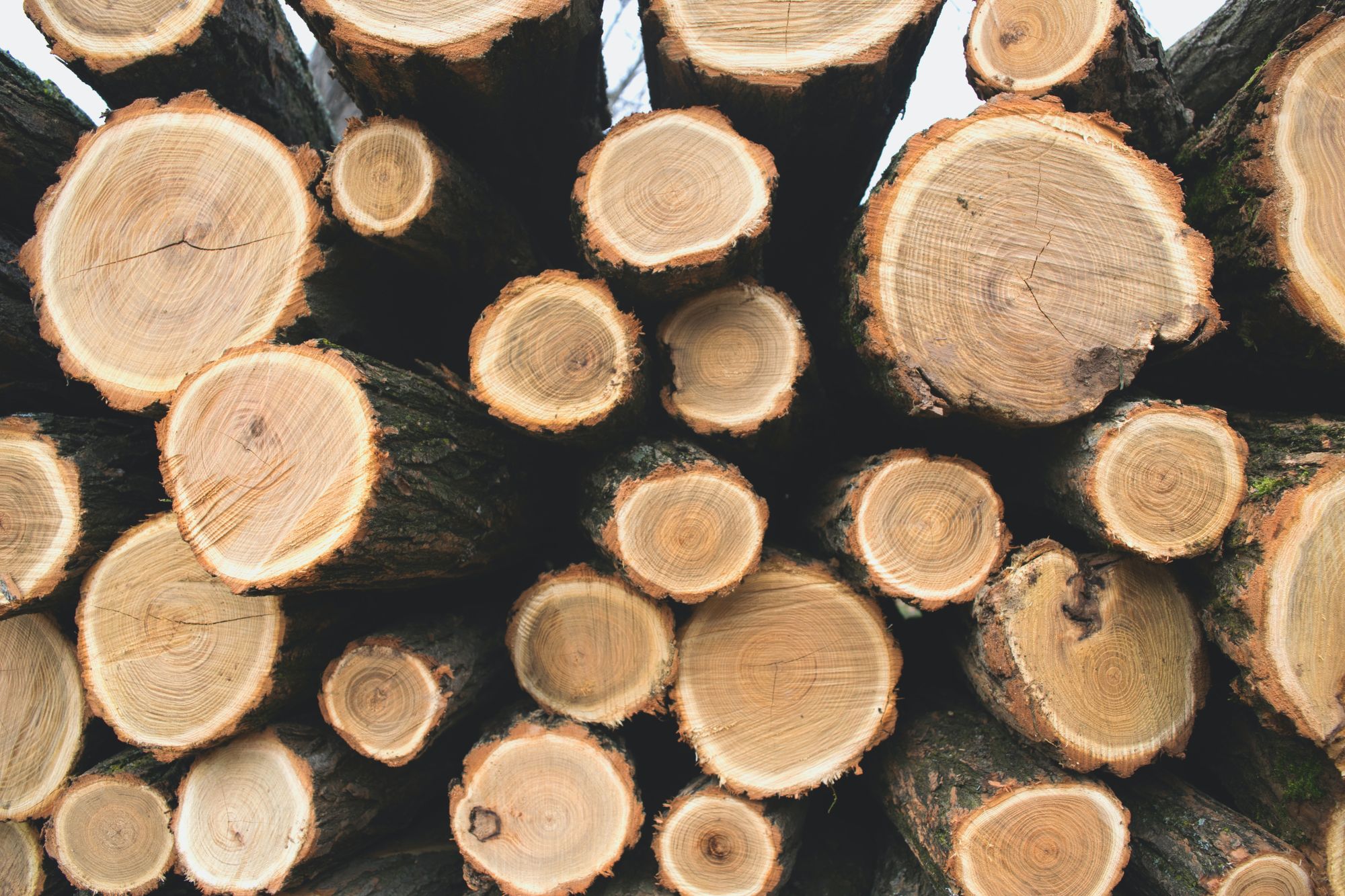
In this article, we'll explore the process of selecting the best ingredients for wood production. We'll discuss the latest trends in sustainable wood sourcing, including the use of reclaimed wood and responsible forest management.
Furthermore, we'll discuss the impact of ingredient selection on the overall sustainability of the wood products industry. Sustainable wood sourcing and responsible ingredient selection can help reduce the environmental impact of wood production, while also meeting the growing demand for environmentally friendly products.
As consumers become increasingly aware of the environmental impact of their purchasing decisions, businesses must adapt to meet changing demands. By selecting the best ingredients for wood production and embracing sustainability, wood manufacturing businesses can differentiate themselves in a crowded market and ensure the industry's long-term viability.
So, let's dive into the world of wood production and explore how to select the best ingredients for creating high-quality, sustainable wood products.
Here's what we shall cover in this post:
- Introduction: The Importance of Choosing the Right Ingredients for Wood Production
- Identifying the Key Characteristics of High-Quality Wood Ingredients
- Sourcing Wood Ingredients: Factors to Consider
- The Impact of Wood Ingredients on the Manufacturing Process
- Best Practices for Handling and Storing Wood Ingredients
- Reducing Waste and Minimizing Environmental Impact of Wood Ingredient Selection
- Addressing Common Challenges in Wood Ingredient Selection
- Conclusion
- Key Takeaways
Introduction: The Importance of Choosing the Right Ingredients for Wood Production
Wood production involves a variety of processes and materials, with the choice of ingredients playing a crucial role in the quality and sustainability of the end product.
The right ingredients can help ensure that wood products are strong, durable, and resistant to environmental factors such as moisture and decay. They can also contribute to the industry's sustainability by reducing waste and minimizing environmental impacts.
- In order to choose the right ingredients for wood production, it is essential to consider factors such as the species of wood being used, the intended use of the final product, and the production methods being employed. For example, different species of wood have different strengths, densities, and durability characteristics, which can affect their suitability for different types of products. Similarly, the use of different types of adhesives, coatings, and finishes can impact the strength, appearance, and longevity of wood products.
- By selecting the right ingredients for wood production, manufacturers can produce high-quality products and reduce waste and environmental impacts. For example, using environmentally-friendly coatings and finishes can help reduce air and water pollution, while the use of sustainable wood species can help promote responsible forestry practices.
- Ultimately, the choice of ingredients is a crucial factor in determining wood products' quality, sustainability, and value. As such, manufacturers must carefully consider their options and choose ingredients that will help them achieve their production goals while minimizing their environmental impact.
Understanding the Different Types of Wood Products and Their Uses
Wood is a versatile and renewable natural resource that has been used for thousands of years. Today, wood products are used in a wide range of applications, from construction to furniture and even as fuel.
However, not all wood products are created equal, and it is vital to understand the different types of wood products and their uses to make informed decisions about which products to use in specific applications.
Solid Wood Products: Solid wood products are made from lumber that has been sawn into specific shapes and sizes. These products include boards, planks, and timbers, and they are used for a wide range of applications, including construction, furniture, and decorative items.
Solid wood products are known for their strength and durability, and they can be treated with stains and finishes to enhance their natural beauty.
Composite Wood Products: Composite wood products are made from a combination of wood fibers, adhesives, and other materials. These products include particleboard, medium-density fiberboard (MDF), and plywood, and they are used in a wide range of applications, including furniture, cabinetry, and flooring.
Composite wood products are known for their consistency, stability, and affordability, and they can be manufactured in a variety of sizes and thicknesses.
Engineered Wood Products: Engineered wood products are made by bonding layers of wood veneers or adhesive strands. These products include laminated veneer lumber (LVL), oriented strand board (OSB), and glued laminated timber (glulam), and they are used in a wide range of applications, including structural components, flooring, and decorative items.
Engineered wood products are known for their strength, stability, and sustainability, and they can be manufactured to meet specific design requirements.
Wood-based Composites: Wood-based composites are made from a combination of wood particles or fibers and other materials, such as plastic or cement.
These products include wood-plastic composites (WPC), fiber-cement boards, and reinforced concrete, and they are used in a wide range of applications, including decking, siding, and cladding. Wood-based composites are known for their durability, resistance to decay, and low maintenance requirements.
Wood Fuels: Wood fuels include firewood, wood pellets, and wood chips, and they are used as a source of heat and energy. Firewood is typically used in open fires or wood-burning stoves, while wood pellets and wood chips are used in specialized boilers and furnaces.
Wood fuels are known for their renewable and sustainable nature, and they can be produced from a variety of sources, including forestry residues and sawmill waste.
Identifying the Key Characteristics of High-Quality Wood Ingredients
The quality of wood products largely depends on the quality of wood ingredients used in the manufacturing process. High-quality wood ingredients result in high-quality wood products that are durable, strong, and have an attractive appearance. Identifying the key characteristics of high-quality wood ingredients is essential for manufacturers and consumers alike.
Key characteristics of high-quality wood ingredients:
- Knots: Knots are a common feature of wood, and they are caused by the base of branches in the tree. In high-quality wood ingredients, knots are tight and small, and they do not affect the strength of the wood. Large and loose knots can weaken the wood, making it unsuitable for certain applications.
- Density: Wood density is a critical characteristic that affects its strength and durability. High-quality wood ingredients have a high density, which makes them strong and resistant to damage. Dense wood also has a low moisture content, making it less prone to warping and splitting.
- Straightness: The straightness of wood is essential for making products that require straight pieces of wood. High-quality wood ingredients have straight grains, making them easier to cut and shape. Crooked or twisted wood can weaken the final product and make it unstable.
- Color: The color of wood is another characteristic that can affect the quality of the final product. High-quality wood ingredients have a consistent color, which makes them suitable for staining or painting. Wood with inconsistent colors can create an uneven finish and affect the appearance of the product.
- Texture: The texture of the wood is determined by the size and distribution of its pores. High-quality wood ingredients have a smooth texture, which makes them easier to work with and gives them a clean appearance. Rough or uneven textures can make the final product look unpolished and unprofessional.
- Durability: Durability is a critical characteristic of high-quality wood ingredients. They should be able to resist damage from insects, moisture, and other environmental factors. Wood species with natural durability, such as teak or cedar, are excellent choices for outdoor applications.
- Grain: The grain of the wood is determined by the direction in which the wood fibers run. High-quality wood ingredients have a consistent grain pattern, making them easier to work with and giving them a polished appearance. Inconsistent grain patterns can make the final product look unprofessional.
- Moisture content: The moisture content of wood is a critical characteristic that can affect its strength and durability. High-quality wood ingredients have a low moisture content, which makes them more stable and resistant to warping and cracking. Moisture meters are often used to measure the moisture content of wood before use.
- Defects: High-quality wood ingredients are free of defects such as cracks, splits, or warps. These defects can weaken the wood and make it unsuitable for certain applications. Careful inspection of wood ingredients is essential to ensure they are free of defects.
Sourcing Wood Ingredients: Factors to Consider
Wood is a natural and renewable resource that is used extensively in the manufacturing of a variety of products. However, the sourcing of wood ingredients can be a complex and challenging process.
Many factors must be considered when selecting wood ingredients for manufacturing, including the wood type, the wood quality, and the sourcing process's environmental impact.
Sustainability
Sustainability is a key factor to consider when sourcing wood ingredients. It is crucial to ensure that the wood is sourced from forests that are managed in a sustainable manner, meaning that the forest is being maintained at a healthy level and that the wood is being harvested in a way that is not damaging to the ecosystem.
It is important to choose wood certified by a reputable organization, such as the Forest Stewardship Council (FSC), which ensures that the wood is being sourced sustainably.
Quality
The quality of the wood ingredients is also an essential factor to consider. Different types of wood have different properties, such as density, hardness, and durability. The wood must be selected based on the specific product's requirements.
For example, high-quality wood with a tight grain structure is necessary for making musical instruments, while softer wood may be used for manufacturing furniture.
Availability
The availability of wood ingredients is another critical factor to consider. Some types of wood are more readily available than others, while others may be difficult to obtain due to their rarity or limited distribution. Choosing wood ingredients that are readily available and easily sourced is essential to ensure a consistent supply.
Cost
The cost of wood ingredients is also an important consideration. The price of wood can vary widely depending on the type, quality, and availability of the wood. It is vital to choose cost-effective wood ingredients that offer good value for money while still maintaining the necessary quality and sustainability requirements.
Environmental Impact
The environmental impact of sourcing wood ingredients must also be considered. The process of harvesting and transporting wood can have a significant impact on the environment, including deforestation, soil erosion, and greenhouse gas emissions.
Choosing wood ingredients that are sourced using environmentally friendly practices, such as sustainable forestry management and responsible transportation methods, is essential.
Legal Compliance
The legal compliance of the sourcing process is also an important consideration. Wood ingredients must be sourced in compliance with all applicable laws and regulations, including those related to forestry management, transport, and trade.
It is important to choose suppliers who can provide evidence of legal compliance, such as certification from the relevant regulatory bodies.
Reputation of Suppliers
The reputation of suppliers is an important consideration when sourcing wood ingredients. Choosing suppliers with a good reputation for quality, sustainability, and ethical practices is essential. This can help ensure that the wood ingredients are high quality, sustainably sourced, and compliant with all relevant laws and regulations.
The Impact of Wood Ingredients on the Manufacturing Process
The quality of the wood used in these processes is crucial for the final product's durability, appearance, and performance. The choice of wood ingredients, including species, grade, moisture content, and size, can significantly impact the manufacturing process's efficiency and product quality.
Species: The choice of wood species can significantly impact the manufacturing process and final product. Different species have unique physical and mechanical properties that affect the wood's strength, hardness, and flexibility.
For example, hardwoods, such as oak and maple, are known for their strength and durability and are commonly used in furniture and flooring. Softwoods, such as pine and cedar, are more lightweight and more elastic, making them ideal for building construction.
Grade: The grade of wood refers to the quality of the wood's appearance and structural characteristics. Wood is typically graded based on knots, splits, and other defects that affect its strength and appearance. Higher-grade wood is generally more expensive but offers superior quality and appearance, making it suitable for high-end products.
Moisture Content: The moisture content of wood is another critical factor that affects the manufacturing process and final product. Wood that is too wet or too dry can lead to problems such as warping, cracking, and shrinking. The ideal moisture content for wood used in manufacturing is typically between 6% and 8%.
Size: The size of wood used in manufacturing can also impact the process and final product. Wood is typically cut to size and shaped according to the product's design specifications.
Using too thick or too thin wood can affect the product's strength and stability, while wood that is too long or too short can make the manufacturing process more difficult.
Processing: The processing of wood ingredients, such as sawing, sanding, and finishing, can also affect the manufacturing process and final product. These processes can affect the wood's surface smoothness, color, and durability.
For example, sanding can remove surface imperfections, while finishing can protect the wood from moisture, sunlight, and other environmental factors.
Ensuring Consistency and Quality in Wood Ingredients
The wood industry relies heavily on consistent and high-quality wood ingredients to ensure the production of quality wood products. Any variation in the wood ingredients can significantly impact the quality of the end product, resulting in customer dissatisfaction and even loss of business.
Therefore, wood manufacturers must ensure consistency and quality in their ingredients.
Establishing a Quality Control System: To ensure consistency and quality in wood ingredients, wood manufacturers need to establish a comprehensive quality control system. This system should outline the procedures and standards that the company will follow to ensure that all wood ingredients meet the required quality standards.
The quality control system should cover all aspects of the manufacturing process, including sourcing, handling, processing, and storage of wood ingredients.
Selecting Reliable Suppliers: One of the critical factors that can impact the consistency and quality of wood ingredients is the supplier. Wood manufacturers need to select suppliers who can consistently provide high-quality wood ingredients.
To achieve this, the wood manufacturer should conduct thorough research on potential suppliers, including their reputation, experience, and quality control measures.
Using Advanced Technology: Advanced technology, such as automated grading systems, can help wood manufacturers to achieve consistency and quality in wood ingredients.
These systems use sensors and cameras to analyze wood ingredients, detecting any defects or variations. The system can then sort the wood ingredients into different categories based on their quality and characteristics.
Implementing Training Programs: The wood manufacturing industry relies heavily on skilled labor. Therefore, wood manufacturers must ensure that their employees have the necessary skills and knowledge to handle wood ingredients correctly.
Training programs can be implemented to educate employees on the best practices for handling wood ingredients, including how to identify and avoid defects, grade wood ingredients, and correctly store wood ingredients.
Regular Inspection and Maintenance: Regular inspection and maintenance of equipment used in processing wood ingredients can help ensure consistency and quality. Equipment such as saws, chippers, and grinders should be regularly inspected and maintained to ensure they function correctly.
Any defects or issues should be promptly addressed to prevent them from impacting the quality of the wood ingredients.
Best Practices for Handling and Storing Wood Ingredients
Proper handling and storage of these materials are critical to ensuring their quality and preventing damage or spoilage.
- Inspect the Delivery: Upon delivery, inspect the wood ingredients for any damage or defects, such as warping, cracks, or mold. This is important to ensure that the materials meet the required specifications and quality standards.
- Proper Transportation: During transportation, wood ingredients must be secured properly to prevent damage. The material should be covered to protect it from exposure to the elements and ensure that it arrives in good condition.
- Storage Conditions: Wood ingredients should be stored clean, dry, and well-ventilated. Exposure to moisture can cause mold and decay, while high humidity can result in warping and cracking. Storing wood materials off the ground, on pallets or racks, can prevent moisture from seeping in.
- Temperature Control: Temperature control is also critical in storing wood ingredients. Extreme temperatures can cause shrinkage, expansion, or cracking of the material. The optimal temperature for storing wood products is between 60-80°F.
- Pest Control: Wood materials are susceptible to insect and rodent infestations, which can cause significant damage to the product. To prevent infestations, store wood ingredients clean and organized, free of debris and food sources for pests.
- Handling Techniques: When handling wood ingredients, avoid dragging or dropping them, as this can cause damage or splintering. Using equipment such as forklifts, pallet jacks, or hand trucks for moving materials is recommended.
- Regular Inspection: Regular inspection of wood ingredients is crucial to detect any issues early on. Inspect the materials for mold, decay, cracks, or warping signs. Any materials found to be defective should be separated and disposed of properly.
- Labeling: Proper labeling of wood ingredients is essential to avoid confusion and ensure that the right materials are used for the intended purpose. Labels should include information such as the product name, grade, and date of receipt.
Maximizing the Efficiency of Wood Ingredient Utilization
Here are some best practices for maximizing the efficiency of wood ingredient utilization:
- Optimize cutting patterns: It is important to optimize cutting patterns to maximize the amount of wood used from each log. This involves identifying the most efficient way to cut the logs into lumber while minimizing waste. Computer software can be used to help identify the best cutting patterns.
- Utilize residual materials: Residual materials such as sawdust and wood chips can be used in a variety of ways, such as for energy generation, pulp and paper production, and even in the production of composite materials. Finding ways to utilize residual materials can help reduce waste and increase efficiency.
- Implement process improvements: Process improvements such as optimizing machine settings, improving maintenance practices, and reducing downtime can help increase the efficiency of wood processing. Regular equipment inspections can also help identify areas for improvement.
- Minimize transportation costs: Transporting wood ingredients can be costly, so it is essential to minimize transportation costs where possible. This can be achieved by locating processing facilities close to the source of the wood, using efficient transportation methods such as rail or barge, and optimizing transportation routes.
- Implement inventory management practices: Effective inventory management practices help ensure that the right amount of wood ingredients are available at the right time. This can help reduce waste by preventing excess inventory and minimizing stockouts resulting in production delays.
- Use technology to track and optimize utilization: Technology such as RFID tags and barcodes can be used to track wood ingredients throughout the supply chain. This can help identify areas for improvement and optimize utilization.
- Implement lean manufacturing principles: Lean manufacturing principles can help reduce waste and increase efficiency in wood processing. This involves identifying and eliminating non-value-added activities, optimizing production flow, and continuously improving processes.
By implementing these best practices, wood manufacturers can maximize the efficiency of wood ingredient utilization, reduce waste, and improve the sustainability of their operations.
Reducing Waste and Minimizing Environmental Impact of Wood Ingredient Selection
- Adopting sustainable wood sourcing practices: The first step in minimizing the environmental impact of wood ingredient selection is to adopt sustainable wood sourcing practices. This includes selecting wood suppliers that are certified by reputable third-party organizations such as the Forest Stewardship Council (FSC) and the Programme for the Endorsement of Forest Certification (PEFC). These certifications ensure that wood is harvested responsibly and sustainably.
- Using alternative wood sources: In addition to sustainable wood sourcing practices, using alternative wood sources such as wood waste and byproducts can help minimize waste and reduce the environmental impact of wood production. For example, sawdust, wood chips, and wood shavings can produce wood pellets or fuel for biomass boilers.
- Implementing efficient wood processing methods: Efficient wood processing methods can help reduce waste and minimize the environmental impact of wood production. These methods include using computer-aided design (CAD) software to optimize the use of wood materials and reducing the thickness of wood components to minimize waste.
- Recycling and reusing wood materials: Recycling and reusing wood materials can also help minimize waste and reduce the environmental impact of wood production. For example, sawdust can be used to produce wood composite materials and wood pallets can be reused or repurposed.
- Implementing responsible disposal methods: Proper disposal of wood waste is also essential in minimizing the environmental impact of wood production. This includes implementing responsible disposal methods such as composting or using wood waste as fuel for biomass boilers.
Monitoring and Evaluating Wood Ingredient Selection Processes
Monitoring and evaluating the wood ingredient selection process is crucial for ensuring that the right ingredients are selected and used in manufacturing. This helps ensure consistent quality, minimize waste, and reduce environmental impact.
Here are some key points to consider:
- Establish clear criteria: It is essential to establish clear criteria for selecting wood ingredients, based on factors such as quality, sustainability, and cost. This helps to ensure that all suppliers are evaluated using the same criteria, making the selection process more objective and transparent.
- Regular audits and assessments: Regular audits and assessments of suppliers help ensure that they adhere to the established criteria and that their practices are sustainable and ethical. These assessments can be conducted internally or by a third-party organization.
- Performance metrics: Establishing performance metrics can help to monitor and evaluate the effectiveness of the wood ingredient selection process. Metrics such as waste reduction, environmental impact, and cost savings can be tracked over time to identify areas for improvement.
- Continual improvement: Continual improvement is essential for ensuring that the wood ingredient selection process remains effective and efficient. Regular reviews and evaluations help identify improvement areas and ensure the process is continually optimized.
- Collaboration: Collaboration with suppliers and other stakeholders can help to ensure that the wood ingredient selection process is effective and sustainable. Suppliers can provide valuable input on the availability and quality of wood ingredients, while other stakeholders can provide insights into the environmental and social impact of the process.
- Training and education: Providing training and education to employees involved in the wood ingredient selection process can help ensure they have the knowledge and skills needed to make informed decisions. This helps ensure that the right ingredients are selected and used, minimizing waste and reducing environmental impact.
- Communication: Clear communication with all stakeholders is essential for ensuring that the wood ingredient selection process is effective and sustainable. This includes communicating the established criteria, performance metrics, and any changes or improvements to the process.
Addressing Common Challenges in Wood Ingredient Selection
Inconsistent Quality: One of the biggest challenges in wood ingredient selection is the inconsistency in the quality of the wood. This can be due to a variety of factors, such as variations in growing conditions, harvesting methods, and processing techniques.
To address this challenge, businesses should work with reliable and trusted suppliers who have a proven track record of providing consistent and high-quality wood ingredients. Regular testing and monitoring of the wood quality can also ensure consistency.
Limited Availability: Certain types of wood ingredients can also be challenging, particularly if they are rare or in high demand. In some cases, businesses may need to look for alternative wood ingredients that can offer similar properties and benefits.
Alternatively, businesses can work with suppliers to secure long-term contracts and ensure a steady supply of the needed wood ingredients.
Sustainability Concerns: There is growing concern over the environmental impact of wood harvesting and processing. To address this challenge, businesses can seek suppliers committed to sustainable practices and certifications, such as Forest Stewardship Council (FSC) or Sustainable Forestry Initiative (SFI) certification.
Businesses can also explore alternative wood sources, such as reclaimed wood or wood from sustainably managed forests.
Cost and Pricing: The cost of wood ingredients can be a significant factor in the selection process. However, it's essential to consider the long-term costs and benefits of using different wood ingredients, such as the durability and lifespan of the wood.
Businesses can also negotiate with suppliers for better pricing or explore bulk purchasing options to help reduce costs.
Ethical Concerns: There is also growing concern over the ethical practices of some wood ingredient suppliers, such as forced labor or unsustainable harvesting practices.
To address this challenge, businesses should conduct thorough due diligence on their suppliers and look for suppliers who are committed to ethical and sustainable practices.
Regulatory Compliance: Finally, businesses must also ensure that they comply with local and national regulations regarding sourcing and processing wood ingredients. This may include requirements for certification or documentation to ensure that the wood ingredients are legally and sustainably sourced.
How Deskera Can Assist You?
Deskera MRP allows you to closely monitor the manufacturing process. From the bill of materials to the production planning features, the solution helps you stay on top of your game and keep your company's competitive edge.
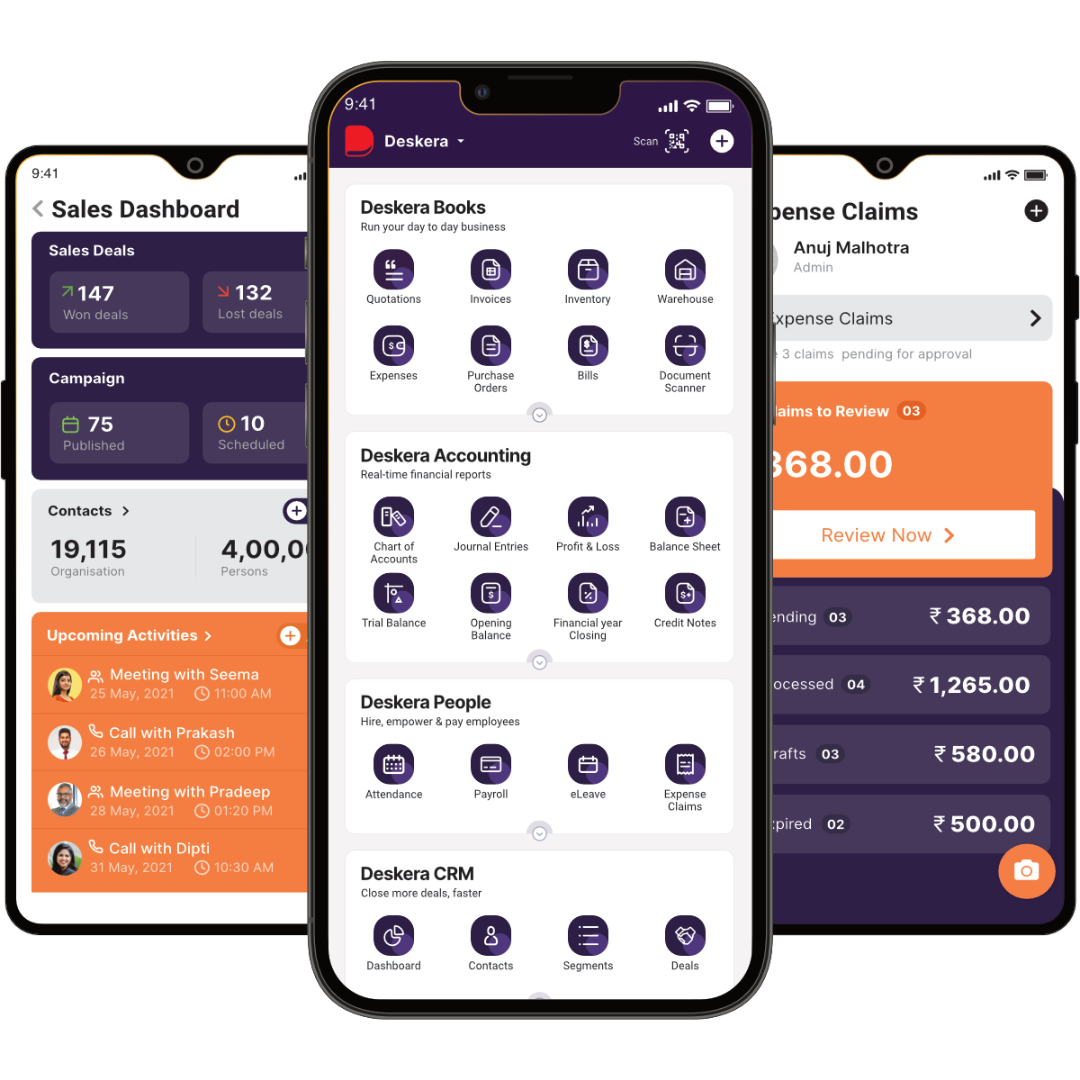
Deskera ERP and MRP system can help you:
- Manage production plans
- Maintain Bill of Materials
- Generate detailed reports
- Create a custom dashboard
Deskera ERP is a comprehensive system that allows you to maintain inventory, manage suppliers, and track supply chain activity in real-time, as well as streamline a variety of other corporate operations.
Deskera Books enables you to manage your accounts and finances more effectively. Maintain sound accounting practices by automating accounting operations such as billing, invoicing, and payment processing.
Deskera CRM is a strong solution that manages your sales and assists you in closing agreements quickly. It not only allows you to do critical duties such as lead generation via email, but it also provides you with a comprehensive view of your sales funnel.
Deskera People is a simple tool for taking control of your human resource management functions. The technology not only speeds up payroll processing but also allows you to manage all other activities such as overtime, benefits, bonuses, training programs, and much more. This is your chance to grow your business, increase earnings, and improve the efficiency of the entire production process.
Conclusion
Selecting the best ingredients for wood production is critical in achieving high-quality and durable wood products. The choice of raw materials, additives, and processing techniques can significantly impact the final product's strength, durability, and appearance.
To select the best ingredients for wood production, manufacturers must consider various factors such as the intended application, environmental considerations, and cost-effectiveness. They must also ensure that the chosen ingredients meet relevant regulatory requirements and are sourced sustainably.
In addition, manufacturers must continually monitor and evaluate their ingredient selection processes to identify areas for improvement and innovation. By adopting best practices in ingredient selection and incorporating the latest technologies and processes, wood manufacturers can produce superior products that meet the demands of today's market.
Ultimately, the key to selecting the best ingredients for wood production is to prioritize quality, sustainability, and innovation while also ensuring that the final product meets the needs of customers and end-users.
Key Takeaways
- The quality of wood products is heavily influenced by the selection of raw materials and additives used in production.
- Raw materials such as lumber, veneer, and composite wood products are commonly used in wood production, and each has its advantages and disadvantages.
- Manufacturers should prioritize sustainability in their ingredient selection process by using responsibly sourced raw materials and environmentally friendly additives.
- Regulatory requirements such as the US Environmental Protection Agency's Formaldehyde Emission Standards for Composite Wood Products must be considered when selecting ingredients.
- Advanced technologies such as nanotechnology can be used to improve wood product properties and reduce the need for certain additives.
- Manufacturers must continually monitor and evaluate their ingredient selection process to identify areas for improvement and innovation.
- Effective ingredient selection can improve product quality, durability, and performance, ultimately leading to increased customer satisfaction and loyalty.
- Cost-effectiveness should be considered in ingredient selection, but it should not come at the expense of product quality or sustainability.
- Manufacturers must balance the benefits of using certain ingredients with the potential environmental and health risks associated with them.
- By prioritizing sustainability, innovation, and customer needs, wood manufacturers can select the best ingredients to produce high-quality, durable products that meet the demands of today's market.
Related Articles
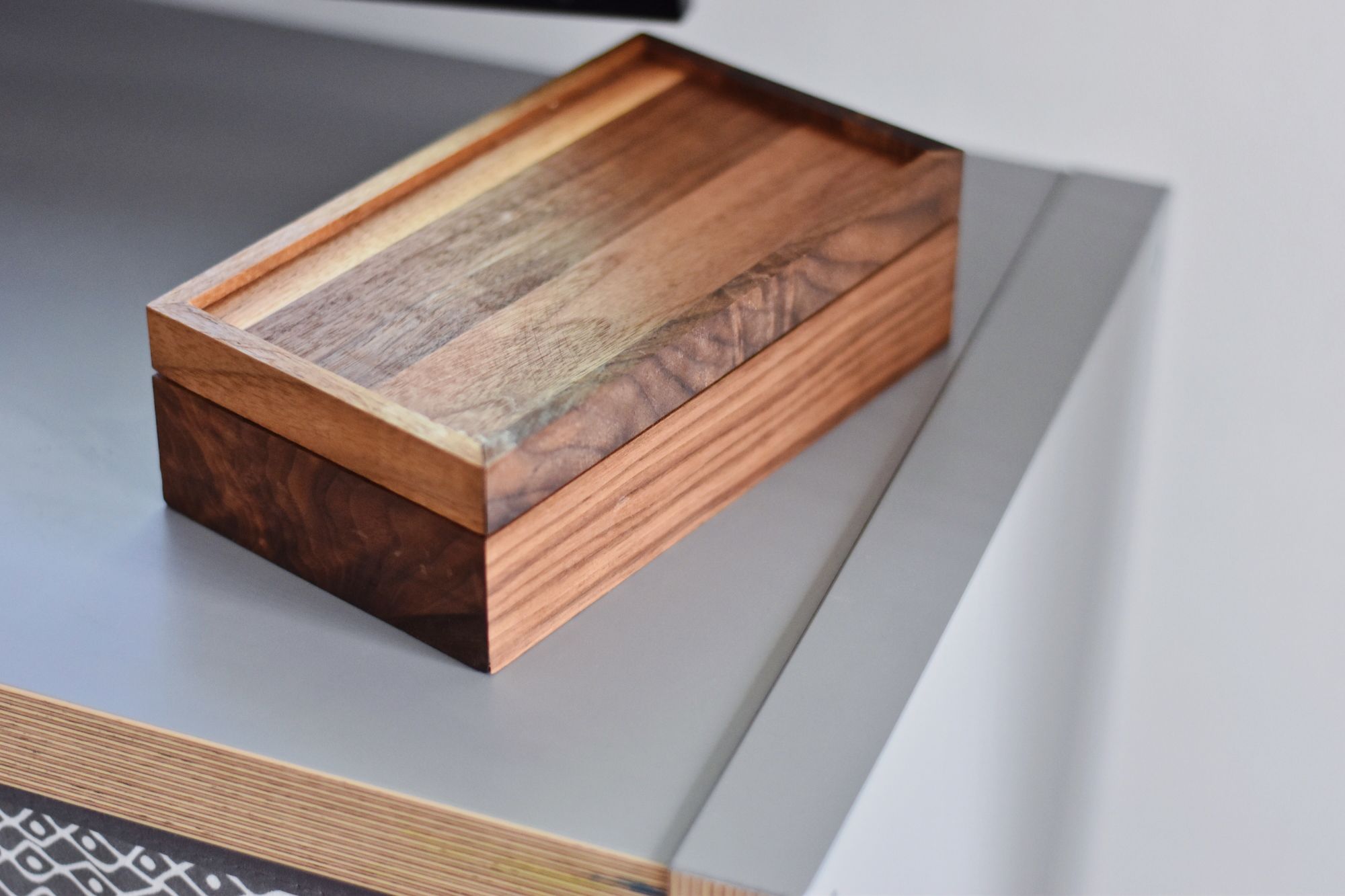
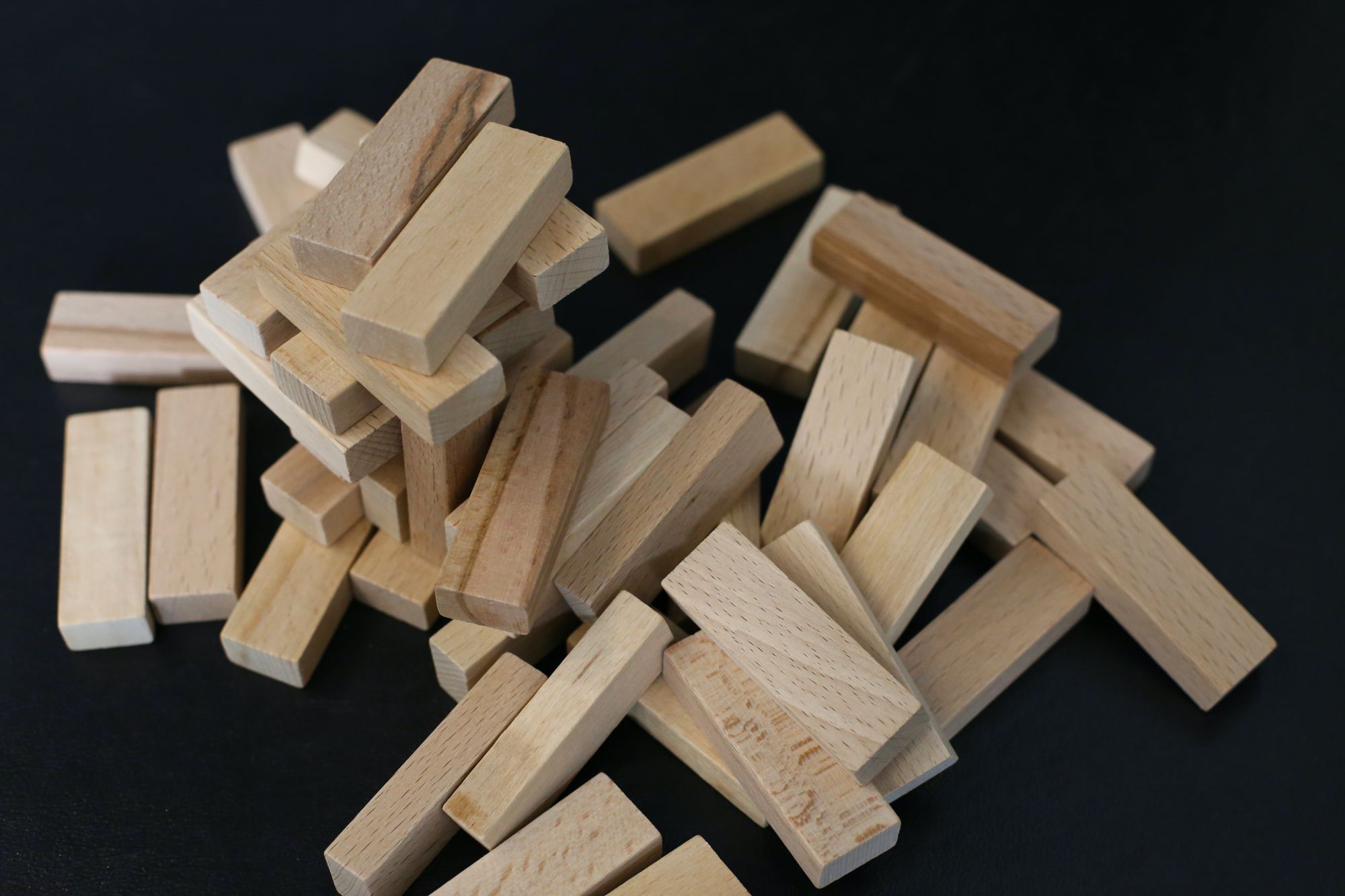
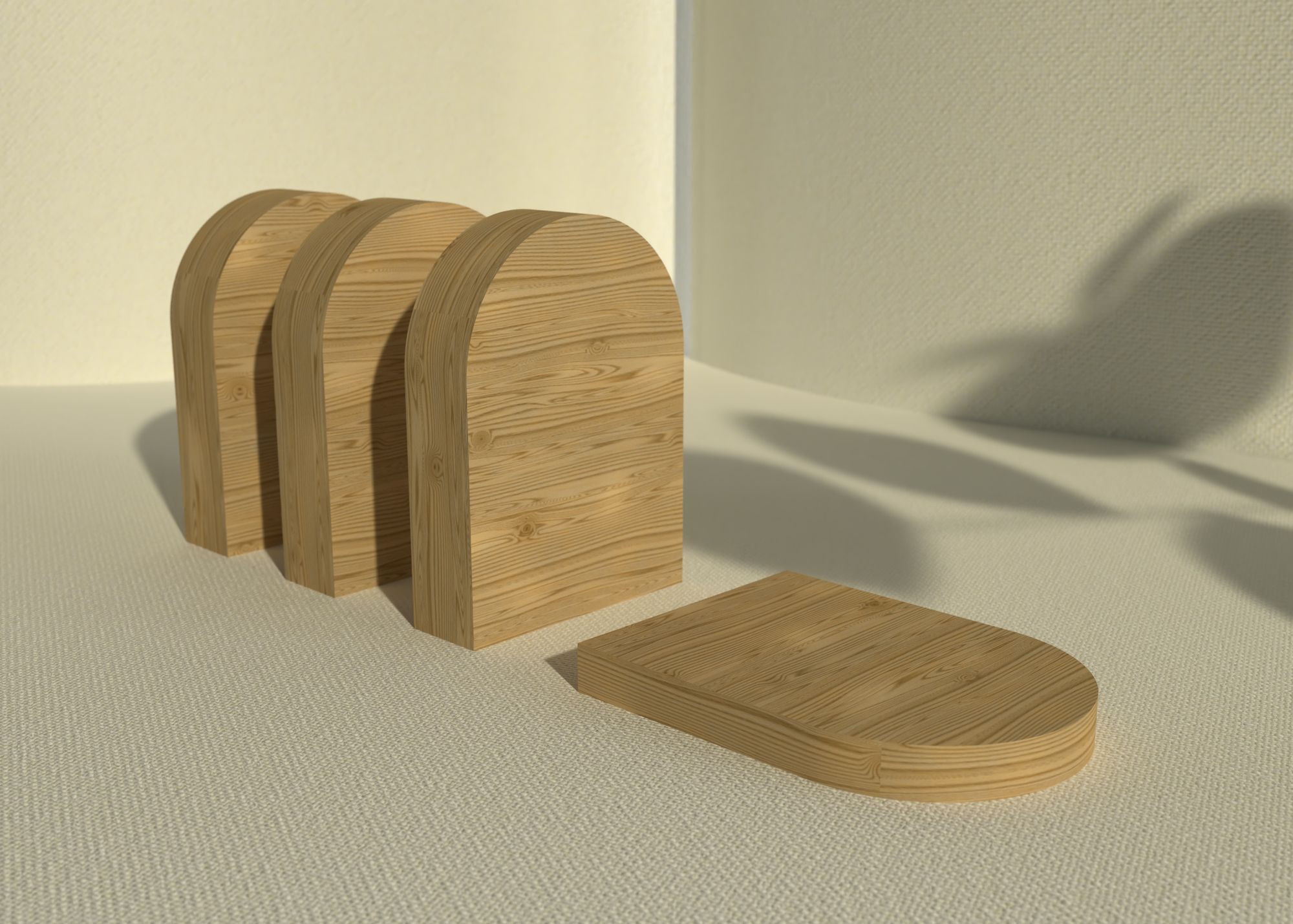
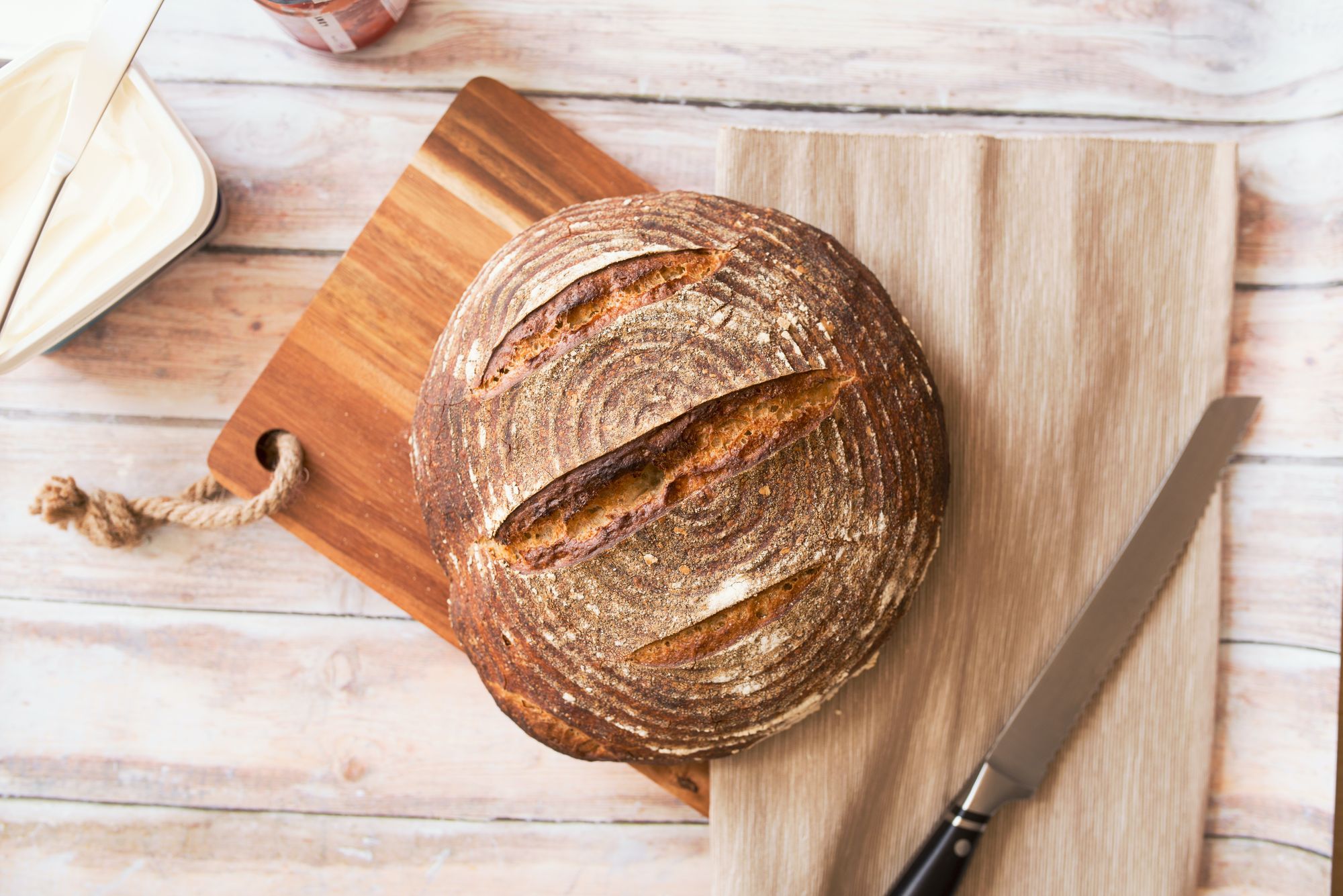