Wood production is an essential industry that has been a part of human civilization for thousands of years. From building homes and furniture to producing paper and other wood-based products, the demand for wood has remained strong throughout history.
However, with growing competition and the need to meet consumer demands for faster production and higher quality, wood production companies must constantly find ways to streamline their processes.
The global market for wood-based products is expected to reach $1.2 trillion by 2027, growing at a CAGR of 4.5% from 2020 to 2027. (Source: Allied Market Research)
Streamlining wood production processes involves optimizing and improving various aspects of the production process, including automation, inventory management, employee training, and safety. By doing so, wood production companies can increase efficiency, reduce waste, improve product quality, and ultimately increase profitability.
In this article, we will provide tips and best practices for streamlining wood production processes. We will discuss the importance of assessing current production processes, utilizing automation and technology, implementing lean manufacturing principles, improving inventory management, providing employee training and ensuring safety, and continuously improving processes.
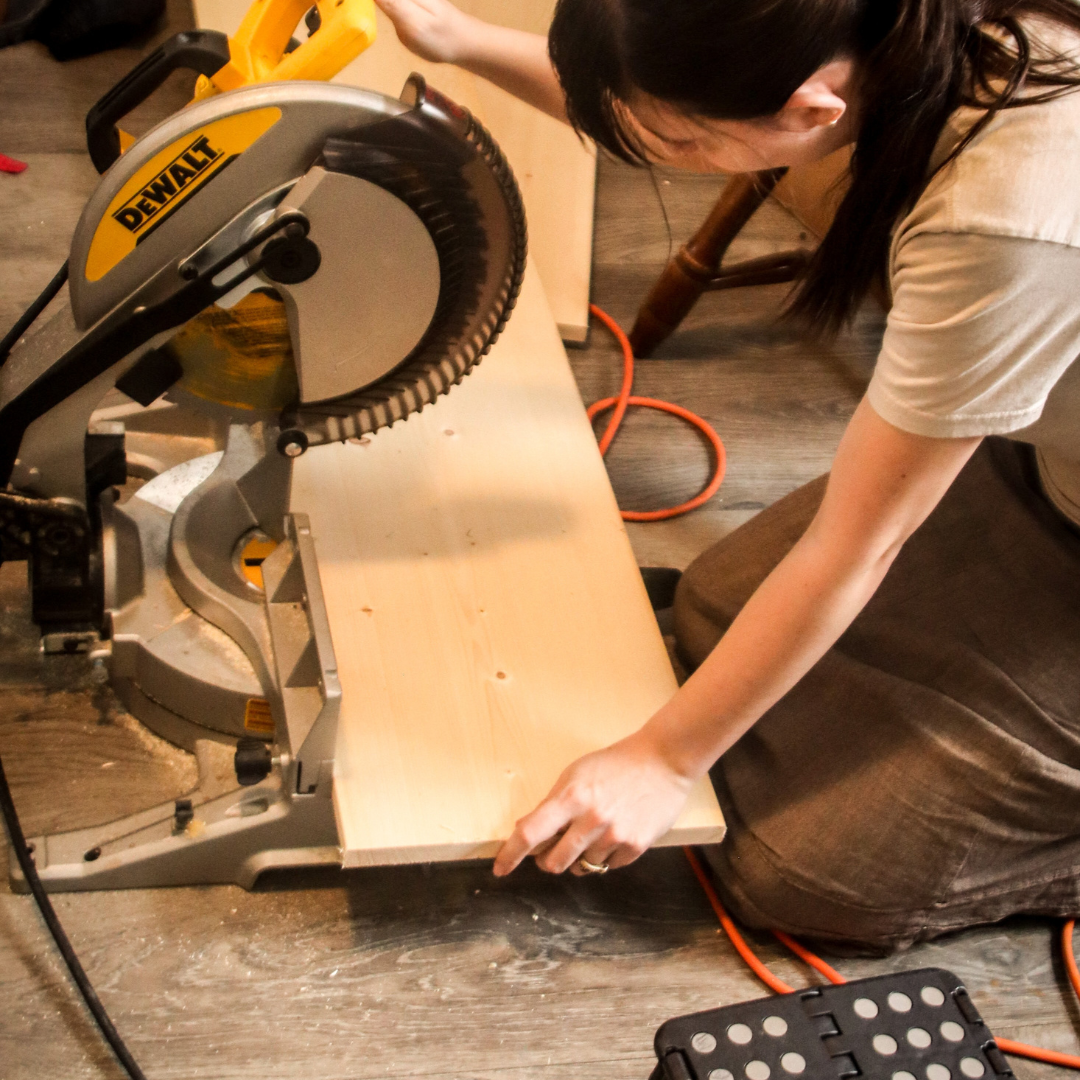
By following these tips, wood production companies can achieve a more streamlined and efficient production process, ultimately improving their bottom line and meeting the demands of their customers.
- Importance of Streamlining Wood Production Processes
- Assessing Current Wood Production Processes
- Automation and Technology
- Lean Manufacturing Principles
- Efficient Supply Chain in Wood Manufacturing
- Inventory Management
- Employee Training and Safety
- Continuous Improvement
- How can Deskera Help You?
- Key Takeaways
- Related Articles
Importance of Streamlining Wood Production Processes
Streamlining wood production processes is crucial for the success of companies in the industry. Here are some reasons why:
- Increased Efficiency: Streamlining processes helps to eliminate waste and optimize resources, leading to increased efficiency. This means that companies can produce more products with the same amount of resources, reducing production costs and increasing profitability.
- Improved Product Quality: By optimizing production processes, companies can ensure consistent product quality. This helps to build a strong reputation for the company and increases customer satisfaction, leading to repeat business and referrals.
- Meeting Customer Demands: In today's market, customers expect fast turnaround times and high-quality products. Streamlining processes helps companies meet and forecast these demands and stay competitive in the industry.
- Employee Safety: Improving processes can help to identify potential safety hazards and mitigate them, creating a safer work environment for employees.
- Compliance with Regulations: The wood production industry is subject to various regulations related to environmental impact, health and safety, and product quality. Streamlining processes helps companies ensure compliance with these regulations, avoiding fines and other penalties.
Assessing Current Wood Production Processes
Assessing current wood production processes is a critical first step towards streamlining operations and improving efficiency in the industry. By evaluating existing processes, companies can identify areas of inefficiency, waste, and potential safety hazards, and develop strategies to address these issues.
This emphasizes the importance of conducting a comprehensive evaluation of the production process to identify areas for improvement, and sets the stage for the rest of the article, which will provide tips and best practices for assessing and streamlining wood production processes.
Need for a Thorough Assessment of Current Processes
A thorough assessment of current wood production processes is essential for identifying inefficiencies, waste, and potential safety hazards. Without a comprehensive evaluation of the production process, companies may miss opportunities for improvement and continue to operate in a less than optimal manner.
Assessing current processes can reveal areas that need improvement, such as outdated technology, poorly designed workflows, and inefficient use of resources. By identifying these areas, companies can develop strategies to address them, leading to increased efficiency, reduced costs, and improved product quality.
Furthermore, a thorough assessment of current processes can help to ensure compliance with regulations related to environmental impact, health and safety, and product quality. By identifying potential non-compliance issues, companies can take steps to rectify them before they result in fines or other penalties.
In summary, a thorough assessment of current wood production processes is critical for identifying areas for improvement, optimizing operations, and ensuring compliance with regulations. Companies that neglect this step may miss opportunities to improve their processes and ultimately fall behind their competitors in the industry.
Identifying Bottlenecks and Inefficiencies
Identifying bottlenecks and inefficiencies is a crucial component of assessing current wood production processes. Bottlenecks occur when a step in the production process slows down the entire process, reducing efficiency and increasing lead time. Inefficiencies occur when resources are not being used optimally, resulting in waste and increased production costs.
To identify bottlenecks and inefficiencies, companies should conduct a thorough evaluation of their production process. This can include analyzing production data, observing workflows, and soliciting feedback from employees.
One approach to identifying bottlenecks and inefficiencies is to create a value stream map, which is a visual representation of the production process from start to finish. This map can help to identify areas where materials or information are waiting or where there are redundant or unnecessary steps in the process.
Another approach is to use process mapping, which involves breaking down the production process into its component parts and analyzing each step to identify opportunities for improvement.
By identifying bottlenecks and inefficiencies, companies can develop strategies to address these issues, such as redesigning workflows, improving communication, and implementing new technologies. This can lead to increased efficiency, reduced costs, and improved product quality, ultimately resulting in a more competitive position in the industry.
Mapping out the Production Process
The process map provides a visual representation of the entire production process, from start to finish, including all steps and the flow of materials and information.
To create a process map, the production process is broken down into individual steps, which are then plotted on a diagram. The diagram can be created using software or on a whiteboard, and should include all inputs and outputs, as well as any decision points or quality checks.
Creating a process map can help companies to identify areas of waste and inefficiency, as well as bottlenecks and potential safety hazards. For example, a process map may reveal that materials are waiting in inventory for extended periods, or that certain steps are being repeated unnecessarily.
Once the process map is created, companies can use it to develop strategies for improvement. This may involve redesigning workflows, eliminating redundant steps, or implementing new technologies to automate certain parts of the process.
By mapping out the production process and identifying areas for improvement, companies can streamline operations, reduce costs, and improve product quality. This can lead to increased efficiency and competitiveness in the industry.
Automation and Technology
Automation and technology have revolutionized the wood production industry, offering opportunities to improve efficiency, reduce costs, and increase product quality. This thesis statement emphasizes the importance of automation and technology in the industry and sets the stage for the rest of the article, which will explore the role of automation and technology in wood production and provide examples of companies that have successfully implemented these tools in their processes.
The article will also discuss the benefits and challenges of automation and technology, and provide tips for companies considering implementing these tools in their own operations.
Role of Automation in Wood Production
Automation plays a critical role in modern wood production, offering a range of benefits that can improve efficiency, reduce costs, and increase product quality. Automation can be applied to various stages of the production process, from initial raw material processing to final product finishing.
One significant benefit of automation in wood production is increased efficiency. Automated equipment can perform tasks faster and more consistently than human workers, reducing lead times and increasing output. Automation also reduces the risk of errors and defects, leading to higher product quality.
Another benefit of automation is cost reduction. By automating repetitive and labor-intensive tasks, companies can reduce labor costs and free up employees to focus on more complex tasks. Automation can also help to reduce waste and optimize resource use, resulting in lower production costs.
However, implementing automation in wood production can also pose challenges, such as the need for significant upfront investment, and the requirement for specialized skills and training to operate and maintain automated equipment.
Despite these challenges, many companies in the wood production industry have successfully implemented automation, resulting in significant improvements in efficiency, quality, and cost savings. As technology continues to advance, the role of automation in wood production will likely continue to grow, offering new opportunities for companies to stay competitive in the industry.
Types of Technology that can be Used for Automation
There are various types of technology that can be used for automation in wood production. Some of the most commonly used types of technology include:
- Robotics: Industrial robots can be used to automate tasks such as material handling, cutting, and finishing. Robots can perform tasks faster and more consistently than human workers, leading to increased efficiency and productivity.
- Computer Numerical Control (CNC) machines: CNC machines use computer programming to control the movement of tools, allowing for precise and repeatable cutting and shaping of wood products.
- Internet of Things (IoT) devices: IoT devices such as sensors and cameras can be used to monitor the production process and provide real-time data on machine performance, material usage, and product quality.
- Automated guided vehicles (AGVs): AGVs are mobile robots that can be used to transport materials and products throughout the production process. They can be programmed to follow specific paths and can help to reduce the need for manual material handling.
- Artificial intelligence (AI): AI can be used to optimize production processes by analyzing data on machine performance and product quality, and identifying opportunities for improvement.
- Augmented reality (AR): AR can be used to provide workers with real-time information and guidance, such as assembly instructions or maintenance procedures, improving efficiency and reducing errors.
By leveraging these types of technology, companies can automate various stages of the wood production process, leading to increased efficiency, improved quality, and reduced costs.
Examples of Companies Using Automation in Their Wood Production Processes
Many companies in the wood production industry have successfully implemented automation in their production processes. Here are some examples:
- IKEA: The Swedish furniture giant has invested heavily in automation, using robots to cut and shape wood for its flat-pack furniture. IKEA's automated production lines can produce up to 500,000 pieces of furniture per day.
- Boise Cascade: Boise Cascade, a US-based wood products manufacturer, has implemented automated packaging systems that can package up to 110 pieces of lumber per minute. The system uses sensors to measure the length and width of each piece of lumber and automatically adjusts the packaging to fit.
- Binderholz: Binderholz, an Austrian wood products company, has implemented an automated production line for cross-laminated timber (CLT), a type of engineered wood used in construction. The production line uses robots to lay out and glue the layers of wood together, resulting in a precise and consistent product.
- Stora Enso: Stora Enso, a Finnish paper and wood products company, has implemented IoT devices in its wood processing facilities to monitor machine performance and reduce downtime. The company has also implemented AI-powered predictive maintenance systems to optimize machine maintenance schedules.
- Canfor: Canfor, a Canadian wood products company, has implemented AGVs in its production facilities to transport materials and products throughout the production process. The AGVs have helped to reduce manual material handling and improve efficiency.
These companies demonstrate the benefits of automation in wood production, from increased efficiency and productivity to improved product quality and reduced costs. By implementing automation, companies can stay competitive in the industry and meet the demands of a changing market.
Lean Manufacturing Principles
Lean manufacturing principles can significantly improve efficiency, reduce waste, and increase profitability in wood production processes. These principles involve optimizing all aspects of the production process, including material flow, equipment utilization, and worker productivity.
By focusing on the elimination of waste and continuous improvement, lean manufacturing can help wood production companies to produce higher quality products while reducing costs. Key components of lean manufacturing include value stream mapping, 5S organization, just-in-time (JIT) production, and continuous improvement through the use of tools such as Kaizen events and Six Sigma methodologies.
Implementing these principles can lead to a more efficient and effective wood production process, resulting in increased profitability and customer satisfaction.
Explanation of Lean Manufacturing Principles
Lean manufacturing is a set of principles and practices aimed at maximizing efficiency and minimizing waste in the production process. This approach focuses on the creation of value for the customer while eliminating waste from all aspects of the production process. Some of the key principles of lean manufacturing include:
- Value stream mapping: This involves analyzing the entire production process to identify areas of waste and inefficiency. By creating a map of the production process, companies can identify opportunities for improvement and prioritize actions that will have the greatest impact on efficiency.
- 5S organization: This involves organizing the workplace to improve efficiency and productivity. The 5S principles include sorting, straightening, shining, standardizing, and sustaining. By organizing the workplace and minimizing clutter, companies can reduce waste and improve worker productivity.
- Just-in-time (JIT) production: This involves producing only what is needed, when it is needed, and in the amount needed. By using JIT production, companies can minimize inventory and reduce waste from overproduction.
- Continuous improvement: This involves constantly evaluating and improving the production process. Tools such as Kaizen events and Six Sigma methodologies can be used to identify areas of waste and inefficiency and implement improvements.
By implementing these principles, wood production companies can improve efficiency, reduce waste, and increase profitability. By focusing on value creation and waste elimination, lean manufacturing can help companies produce higher quality products while reducing costs.
Application of Lean Manufacturing Principles To Wood Production Processes
Lean manufacturing principles can be applied to wood production processes to improve efficiency, reduce waste, and increase profitability. Here are some ways in which these principles can be applied:
- Value stream mapping: By creating a map of the entire production process, wood production companies can identify areas of waste and inefficiency, such as excessive material handling or waiting times. By addressing these areas of waste, companies can streamline the production process and reduce costs.
- 5S organization: By organizing the workplace and minimizing clutter, wood production companies can improve worker productivity and reduce the risk of accidents. By implementing the 5S principles, companies can also reduce waste from excess inventory or overproduction.
- Just-in-time (JIT) production: By producing only what is needed, when it is needed, and in the amount needed, wood production companies can reduce inventory costs and minimize waste from overproduction. JIT production also allows companies to respond quickly to changes in demand.
- Continuous improvement: By constantly evaluating and improving the production process, wood production companies can identify areas of waste and inefficiency and implement improvements. This can be done through tools such as Kaizen events or Six Sigma methodologies.
Overall, by implementing lean manufacturing principles, wood production companies can improve efficiency, reduce waste, and increase profitability. By focusing on value creation and waste elimination, companies can produce higher quality products while reducing costs and meeting the demands of a changing market.
Benefits of Implementing Lean Manufacturing Principles in Wood Production Processes
Implementing lean manufacturing principles in wood production processes can provide several benefits, including:
- Improved Efficiency: By eliminating waste and optimizing the production process, companies can reduce lead times, improve throughput, and increase productivity. This can lead to reduced production costs and increased profitability.
- Enhanced Quality: Lean manufacturing principles promote a focus on quality at every stage of the production process. By implementing quality control measures and reducing defects, companies can produce higher quality products that meet customer requirements.
- Increased Flexibility: Just-in-time production and value stream mapping allow companies to respond quickly to changes in demand, enabling them to adjust production levels and schedules as needed.
- Improved Worker Safety and Morale: By implementing 5S organization and other safety measures, companies can create a safer work environment that promotes worker well-being and job satisfaction.
- Enhanced Customer Satisfaction: By producing higher quality products in a more efficient manner, companies can meet customer demands and expectations more effectively, leading to increased customer satisfaction and loyalty.
Overall, implementing lean manufacturing principles in wood production processes can help companies become more competitive, improve profitability, and meet the demands of a changing market. By focusing on efficiency, quality, flexibility, worker safety and satisfaction, and customer satisfaction, companies can create a sustainable and successful production process.
Efficient Supply Chain in Wood Manufacturing
An efficient supply chain is essential for streamlined wood production processes because it ensures a reliable flow of materials and equipment to the production line, thereby minimizing production downtime and delays. When the supply chain is managed effectively, materials and equipment are delivered to the right place at the right time, allowing production to proceed smoothly without interruptions. This, in turn, reduces lead times and enables the company to fulfill customer orders more quickly and efficiently.
An efficient supply chain can also help to reduce costs by optimizing inventory levels, eliminating excess inventory, and reducing waste. By partnering with reliable suppliers and vendors, wood production companies can negotiate favorable terms and secure the best pricing for materials and equipment. This can lead to cost savings that can be reinvested in the business to improve production processes, enhance product quality, or expand the product line.
Best Practices for Efficient Supply Chain
Here are some best practices for efficient supply chain management in wood production:
- Establish strong relationships with suppliers and vendors: Building strong relationships with suppliers and vendors can help ensure a reliable flow of materials and equipment to the production line.
- Implement a just-in-time inventory system: A just-in-time inventory system can help minimize inventory levels and reduce waste, while ensuring that materials and equipment are available when needed.
- Use technology to manage the supply chain: Technology such as enterprise resource planning (ERP) and material requirements planning (MRP) systems can help track inventory levels, monitor demand, and optimize the supply chain.
- Implement a vendor management program: A vendor management program can help ensure that suppliers and vendors meet quality and delivery standards, while also promoting collaboration and continuous improvement.
- Conduct regular supplier evaluations: Conducting regular supplier evaluations can help identify opportunities for improvement and ensure that suppliers are meeting quality and delivery standards.
- Monitor demand and adjust supply accordingly: Monitoring demand and adjusting supply levels accordingly can help ensure that the right materials and equipment are available at the right time, reducing the risk of production downtime and delays.
- Maintain open communication with suppliers and vendors: Maintaining open communication with suppliers and vendors can help ensure that they are aware of production schedules and can adjust their operations accordingly.
By implementing these best practices, wood production companies can streamline their supply chains and ensure a reliable flow of materials and equipment to the production line, thereby minimizing production downtime, reducing costs, and improving customer satisfaction.
Inventory Management
Effective inventory management is essential for wood production companies to optimize their operations and improve profitability. The efficient management of inventory can help companies to reduce costs, increase efficiency, and improve customer satisfaction.
A proper inventory management system ensures that raw materials and finished products are available when required, preventing stock-outs or overstocking. By implementing inventory management techniques such as ABC analysis, just-in-time (JIT) inventory, and safety stock management, wood production companies can minimize inventory costs while ensuring that they have the necessary inventory to meet customer demands.
An effective inventory management system also provides companies with valuable data for forecasting and planning, enabling them to make informed decisions and remain competitive in the market.
Importance of Efficient Inventory Management in Wood Production
Efficient inventory management is crucial for wood production companies to achieve optimal performance, reduce costs, and improve profitability. The following are some of the reasons why efficient inventory management is important in wood production:
- Preventing Stock-Outs: Efficient inventory management ensures that raw materials and finished products are available when required, preventing stock-outs that can delay production and compromise customer satisfaction.
- Avoiding Overstocking: Overstocking can lead to increased inventory holding costs, waste, and obsolescence. By implementing inventory management techniques such as just-in-time (JIT) inventory and safety stock management, companies can avoid overstocking and reduce costs.
- Cost Reduction: Efficient inventory management can help companies to reduce inventory holding costs, transportation costs, and procurement costs, leading to cost savings and improved profitability.
- Improved Customer Satisfaction: By ensuring that products are available when required and delivered on time, companies can improve customer satisfaction and loyalty.
- Accurate Forecasting: Efficient inventory management provides companies with valuable data for forecasting and planning, enabling them to make informed decisions and remain competitive in the market.
Best Practices for Inventory Management
Implementing the following best practices can help wood production companies to efficiently manage their inventory:
- ABC Analysis: Classify inventory items into three categories based on their value and usage frequency. This will help the company prioritize and manage inventory more efficiently.
- Just-in-Time (JIT) Inventory: Implement JIT inventory to minimize inventory holding costs and reduce waste by only ordering and receiving inventory when it is needed.
- Safety Stock Management: Maintain a safety stock of inventory to ensure that unexpected demand or production disruptions do not cause stock-outs.
- Cycle Counting: Regularly count and verify inventory levels to ensure accuracy and identify any discrepancies.
- Real-time Inventory Management System: Implement an inventory management system that provides real-time visibility into inventory levels, locations, and movements.
- Demand Forecasting: Use historical data and market trends to forecast demand and adjust inventory levels accordingly.
- Regular Review: Review inventory levels regularly to identify slow-moving or obsolete inventory and take appropriate actions such as reducing production or liquidating inventory.
By following these best practices, wood production companies can effectively manage their inventory, reduce costs, and improve operational efficiency. Implementing an efficient inventory management system can also provide valuable data for forecasting and planning, enabling companies to make informed decisions and remain competitive in the market.
Examples of Companies with Effective Inventory Management Practices
There are several wood production companies that have effectively implemented inventory management practices to optimize their operations and improve profitability. Some of the examples include:
- Weyerhaeuser: Weyerhaeuser has implemented a real-time inventory management system that provides visibility into inventory levels, locations, and movements. They also use demand forecasting and safety stock management to ensure that inventory is available when required.
- Georgia-Pacific: Georgia-Pacific uses an ABC analysis to prioritize inventory management and optimize inventory levels. They also implement cycle counting and regular inventory review to maintain accuracy and identify any discrepancies.
- Boise Cascade: Boise Cascade uses just-in-time (JIT) inventory and safety stock management to reduce inventory holding costs and avoid stock-outs. They also use an inventory management system that provides real-time visibility into inventory levels and movements.
- International Paper: International Paper has implemented a demand forecasting system that uses historical data and market trends to forecast demand and adjust inventory levels accordingly. They also use safety stock management and regular inventory review to maintain optimal inventory levels.
Employee Training and Safety
Employee training and safety are critical components of wood production processes that significantly impact the productivity and profitability of a company. Proper employee training helps to improve efficiency, quality, and safety in the workplace.
Similarly, implementing safety measures ensures that employees are protected from workplace hazards and reduces the likelihood of workplace accidents and injuries.
By prioritizing employee training and safety, wood production companies can create a culture of safety that fosters employee satisfaction and loyalty, reduces workplace accidents, and increases productivity and profitability.
Importance of Employee Training and Safety in Wood Production Processes
Employee training and safety are crucial for wood production companies for several reasons, including:
- Improved Efficiency: Proper employee training helps to improve efficiency by ensuring that employees understand their roles and responsibilities, leading to increased productivity and reduced downtime.
- Enhanced Quality: Employee training can also improve product quality by ensuring that employees are trained on the correct methods and procedures for producing high-quality wood products.
- Safety: Implementing safety measures ensures that employees are protected from workplace hazards and reduces the likelihood of workplace accidents and injuries.
- Compliance: Compliance with health and safety regulations is critical for wood production companies to avoid fines and penalties.
- Employee Satisfaction: Providing adequate training and ensuring a safe work environment can improve employee satisfaction and reduce employee turnover.
By prioritizing employee training and safety, wood production companies can create a positive work environment, reduce workplace accidents, and increase productivity and profitability.
Best Practices for Employee Training and Safety
Here are some best practices for employee training and safety in wood production processes:
- Develop a comprehensive training program: A well-designed training program should cover all aspects of the job, including safety procedures, equipment operation, and quality standards.
- Use hands-on training: Hands-on training can help employees better understand their job responsibilities and the potential hazards of their work environment.
- Implement safety procedures: Implementing safety procedures, such as wearing personal protective equipment (PPE) and following safety protocols, is crucial to prevent accidents and injuries.
- Conduct regular safety audits: Regular safety audits can help identify potential hazards and improve safety procedures in the workplace.
- Encourage employee involvement: Encouraging employee involvement in safety programs can help to promote a culture of safety and increase employee engagement and satisfaction.
- Provide ongoing training: Providing ongoing training can help to reinforce safety procedures and keep employees up-to-date on new equipment and technology.
By implementing these best practices, wood production companies can create a safe and productive work environment that prioritizes the well-being of their employees.
Continuous Improvement
Continuous improvement is an essential aspect of wood production processes, as it enables companies to identify areas for improvement and implement changes that enhance efficiency and productivity. By adopting a continuous improvement mindset, wood production companies can stay competitive, reduce waste, and improve product quality.
Through regular evaluation of production processes, identification of inefficiencies, and implementation of corrective actions, companies can achieve sustainable improvements in their operations. Continuous improvement also fosters a culture of innovation, employee engagement, and problem-solving, which can lead to new products, better customer experiences, and higher profits.
Thus, continuous improvement is vital for the long-term success of wood production companies.
Need for Continuous Improvement in Wood Production Processes
Wood production processes can be complex and involve multiple stages, from raw material sourcing to final product delivery. To stay competitive in the industry, wood production companies need to continually evaluate and improve their processes.
Continuous improvement helps companies identify areas for improvement and implement changes that enhance efficiency, reduce waste, and improve product quality. By adopting a culture of continuous improvement, wood production companies can stay ahead of the competition, improve their bottom line, and create a better work environment for their employees.
Additionally, continuous improvement can lead to innovation, new product development, and increased customer satisfaction, all of which are essential for the long-term success of wood production companies.
Ways to Continually Improve Processes
Here are some ways that wood production companies can continually improve their processes:
- Regular evaluation: Regular evaluation of production processes helps companies identify areas for improvement. This evaluation can involve tracking key performance indicators, monitoring production efficiency, and analyzing customer feedback.
- Employee engagement: Employees are often the most knowledgeable about the production process and can provide valuable insights for improvement. Engaging employees through training, meetings, and other communication channels can help identify inefficiencies and generate ideas for process improvement.
- Process automation: Automation can help reduce production time, improve accuracy, and minimize waste. Implementing automation technology such as robotics and sensors can help streamline processes and improve efficiency.
- Lean manufacturing principles: Adopting lean manufacturing principles can help reduce waste and improve efficiency. This can involve optimizing the production flow, reducing inventory levels, and eliminating non-value-added activities.
- Continuous training: Providing employees with regular training and development opportunities can help improve their skills and knowledge, which can translate into better production processes.
By continually evaluating production processes, engaging employees, implementing process automation, adopting lean manufacturing principles, and providing continuous training, wood production companies can continually improve their operations, stay competitive, and meet the needs of their customers.
Adopting MRP and ERP Systems for a Streamlined Wood Production Process
Materials Requirements Planning (MRP) and Enterprise Resource Planning (ERP) systems can be valuable tools for streamlining wood production processes. MRP systems help companies plan and manage their production schedules, inventory levels, and material orders. ERP systems are more comprehensive and can integrate data from multiple departments, including production, inventory management, finance, and human resources.
By implementing MRP and ERP systems, wood production companies can:
- Improve production planning: MRP systems can help companies create more accurate production schedules and ensure that materials are available when needed.
- Reduce inventory levels: By managing inventory levels more effectively, companies can reduce waste, improve cash flow, and increase efficiency.
- Improve order accuracy: MRP and ERP systems can help reduce errors and ensure that orders are fulfilled accurately and on time.
- Increase transparency: By integrating data from multiple departments, ERP systems can provide a more comprehensive view of the business and help managers make more informed decisions.
Some examples of wood production companies that have successfully implemented MRP and ERP systems include Weyerhaeuser, Georgia-Pacific, and Roseburg Forest Products. By adopting these systems, these companies have been able to improve production efficiency, reduce waste, and increase customer satisfaction.
How can Deskera Help You?
Deskera ERP and MRP systems help you to keep your business units organized. The system's primary functions are as follows:
- Keep track of your raw materials and final items inventories
- Control production schedules and routings
- Keep a bill of materials
- Produce thorough reports
- Make your own dashboards
Deskera's integrated financial planning tools enable investors to better plan and track their investments. It can assist investors in making faster and more accurate decisions.
Deskera Books allows you to better manage your accounts and finances. Maintain good accounting practices by automating tasks like billing, invoicing, and payment processing.
Deskera CRM is a powerful solution that manages your sales and helps you close deals quickly. It not only enables you to perform critical tasks like lead generation via email, but it also gives you a comprehensive view of your sales funnel.
Deskera People is a straightforward tool for centralizing your human resource management functions.
Key Takeaways
- Conduct a thorough assessment of current processes to identify bottlenecks and inefficiencies.
- Map out the production process to gain a better understanding of how materials, people, and equipment are utilized.
- Consider automation and technology solutions to improve production efficiency and reduce manual labor.
- Implement lean manufacturing principles to reduce waste and optimize production flow.
- Adopt efficient inventory management practices to reduce excess inventory and improve cash flow.
- Provide comprehensive employee training and safety programs to ensure workers are equipped to perform their jobs safely and efficiently.
- Prioritize continuous improvement to identify and address areas for optimization and enhancement.
- Partner with suppliers and vendors to optimize supply chain management and reduce lead times.
- Use data and analytics to inform decision-making and identify opportunities for improvement.
- Collaborate with industry experts and peers to stay up-to-date on best practices and emerging trends in wood production.
Related Articles
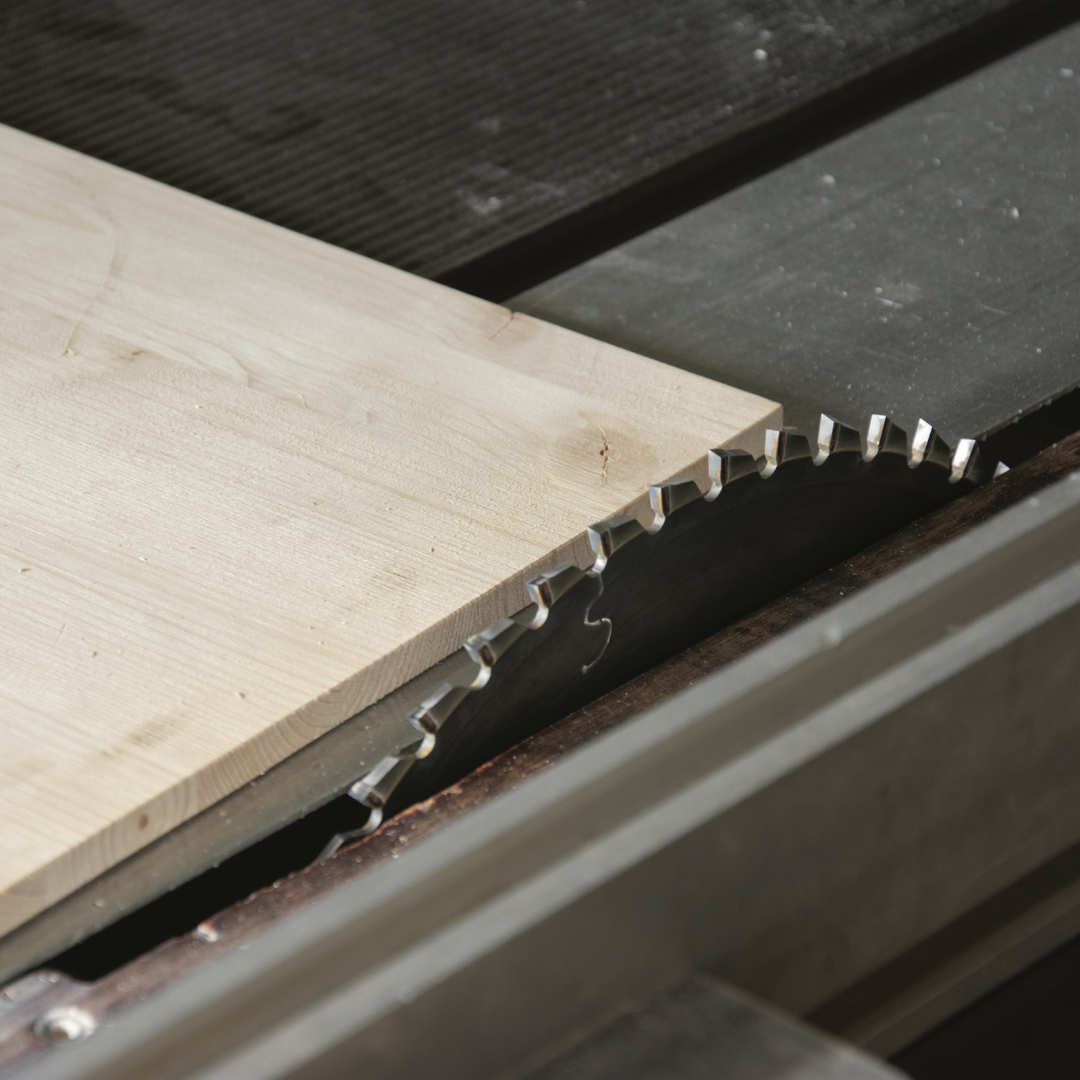
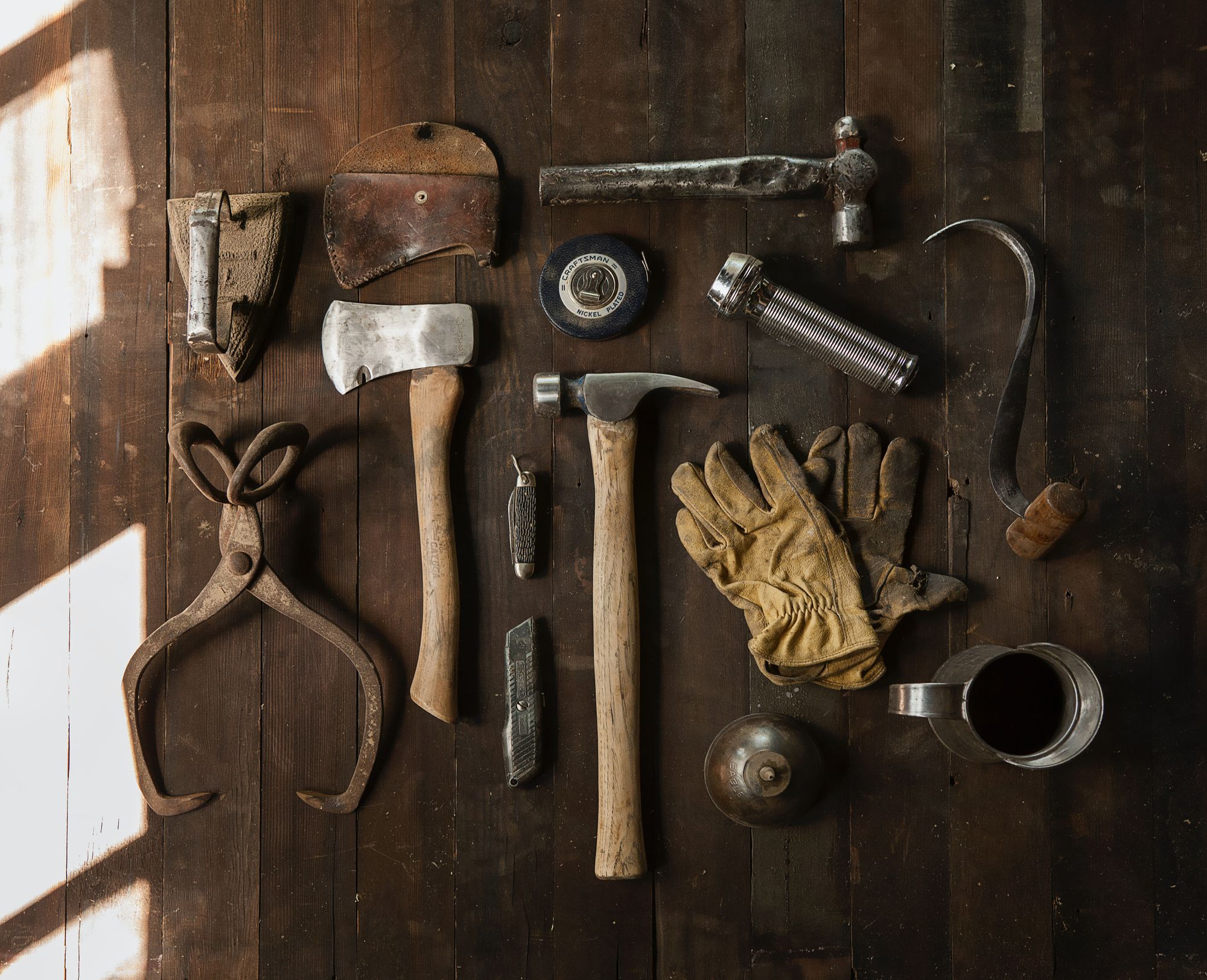
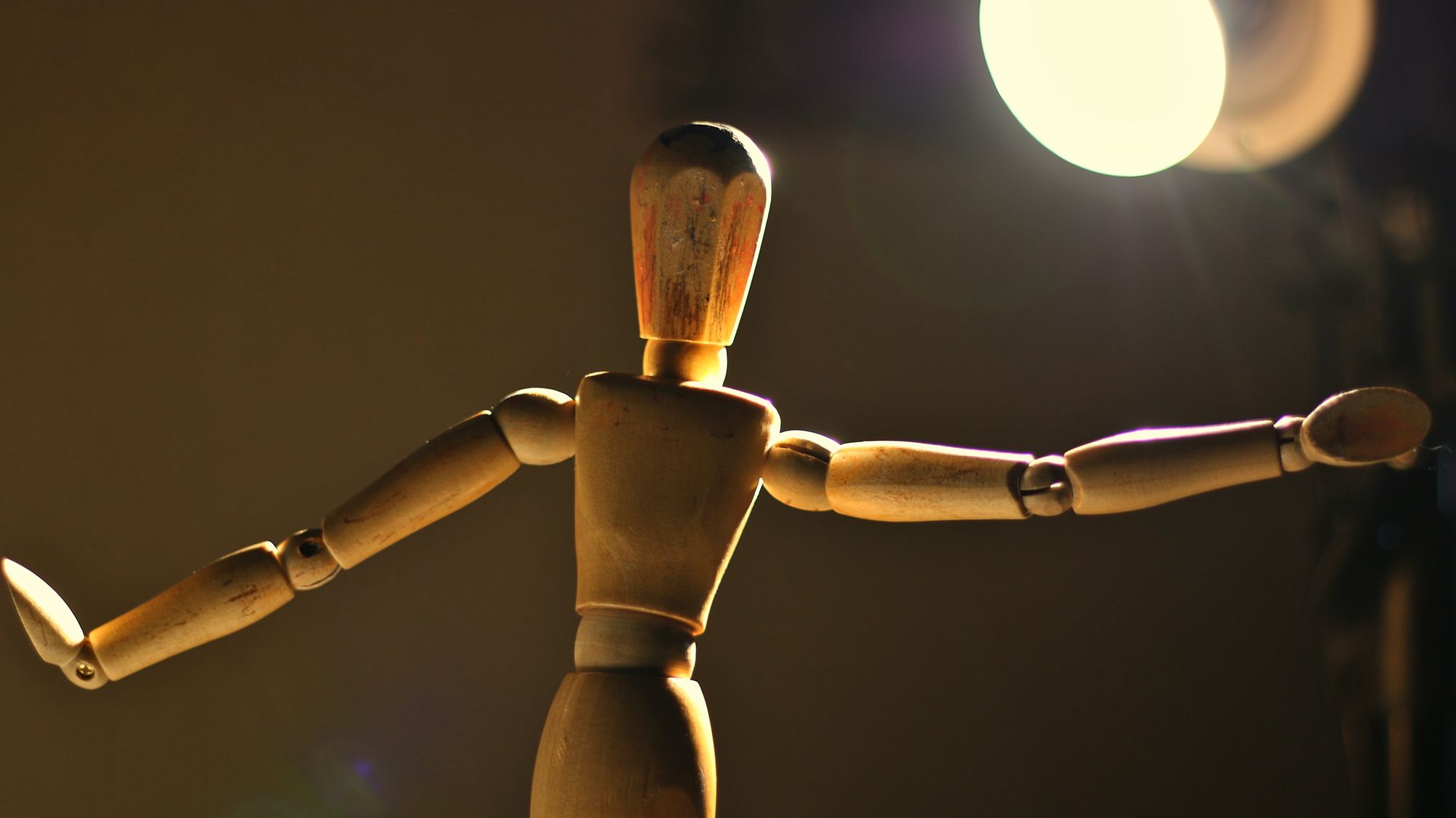