According to the US Census Bureau, over 1,000 establishments in the US employed over 8,000 people in the cellular manufacturing layout sector. The total payroll for these establishments was estimated at around $2.3 billion.
Cellular manufacturing is a production system that combines the processes of a production line into a single, unified manufacturing cell. It is a type of lean manufacturing system that reduces waste and improves efficiency. It achieves this by reducing the time it takes to transfer products between machines.
Cellular manufacturing helps to reduce setup times, lower inventory costs, and simplify production scheduling. It is well suited for producing a wide variety of products in small to medium batches.
We shall be learning about the various aspects associated with cellular manufacturing in this article. Let’s take a look.
- What is Cellular Manufacturing?
- History of Cellular Manufacturing
- What are the Goals of Cellular Manufacturing?
- Types of Cellular Manufacturing Layout
- Benefits of Implementing Cellular Manufacturing
- 5 Challenges of Cellular Manufacturing
- The Process of Cellular Manufacturing
- Potential Pitfalls to Consider
- Cellular Manufacturing Vs. Traditional Layouts
- MRP Systems and Cellular Manufacturing
- Cellular Manufacturing FAQs
- Conclusion
- How can Deskera Help You?
- Key Takeaways
- Related Articles
What is Cellular Manufacturing?
Cellular manufacturing is a type of manufacturing system in which the production process is organized into individual cells, each of which is responsible for producing a particular part or component.
Cells typically consist of a few machines, sometimes a single machine, that are dedicated to producing a particular part or component. Cellular manufacturing aims to group similar operations together and reduce the amount of non-value-added movement of features and materials. This helps to reduce costs and increase the efficiency of the production process.
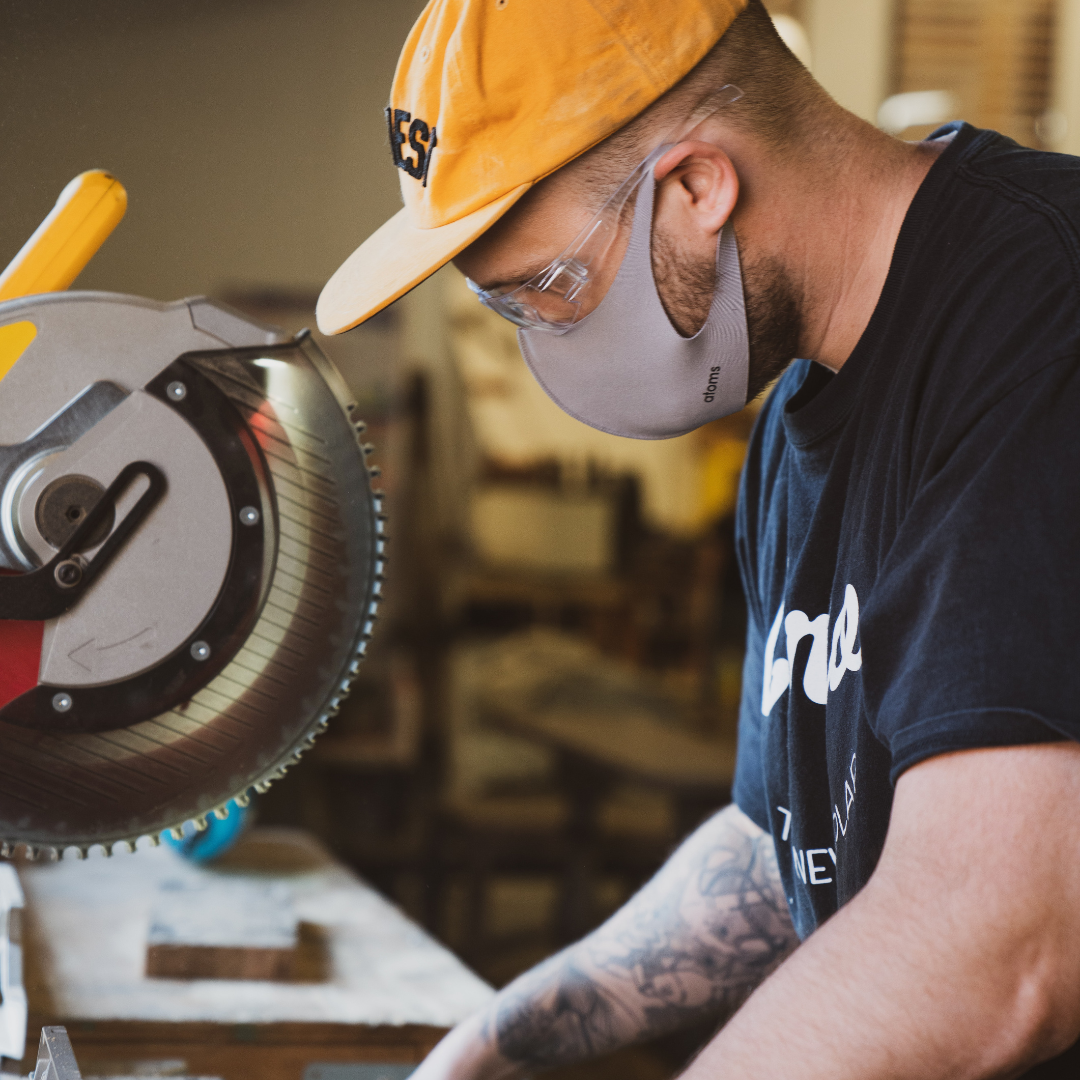
History of Cellular Manufacturing
Cellular manufacturing is a method of production that originated in Japan in the 1970s. It is a type of lean production that focuses on reducing waste and increasing efficiency by organizing production processes into individual, self-contained cells.
Each cell is designed to produce a specific type of product and has the necessary equipment, personnel, and materials to complete the task. This makes it easier to create a variety of products without having to reconfigure the production line constantly.
Cellular manufacturing has been used in various industries, including automotive, aerospace, medical device, and consumer goods. Creating smaller, more efficient production cells has enabled companies to reduce costs, improve quality and reduce lead times. The ability to quickly switch between different product types has also increased flexibility and responsiveness to demand forecasts.
In recent years, computer-aided design and manufacturing (CAD/CAM) systems have enabled manufacturers to optimize their production cells further. This has allowed them to reduce costs by eliminating the need for manual setup and to improve product quality.
What are the Goals of Cellular Manufacturing?
Cellular manufacturing aims to reduce costs, increase production efficiency, and improve product quality. This can be achieved by grouping similar machines and processes together in cells or self-contained work units designed to streamline production flow and reduce unnecessary material handling.
This approach helps to reduce the costs associated with traditional manufacturing methods while also improving product quality and production output.
Here is how we can summarize the goals of cellular manufacturing:
- Minimize setup times
- Maximize flow efficiency
- Reduce work in process
- Increase flexibility
- Improve quality
- Reduce lead times
- Maximize machine utilization
- Improve cost control
- Increase product variety
- Enhance the working environment
Minimize Setup Times
Cellular manufacturing minimizes setup times by grouping machines and processes together in a cell designed to produce a family of parts. This arrangement eliminates unnecessary movements and the need for workers to move from machine to machine. Thus, reducing setup time for each new product.
By streamlining the production process, cellular manufacturing also reduces the time it takes to switch from one product to another.
Maximize Flow Efficiency
The cell manufacturing system encourages the efficient flow of materials and information throughout the entire production process, as each cell is responsible for its own production process.
Cellular manufacturing can maximize flow efficiency by streamlining the production process, improving communication between departments, and reducing bottlenecks. Additionally, using this system encourages just-in-time production and eliminates waste.
Reduce Work in Process
Cellular manufacturing can reduce work in process by reducing the number of steps and complexity involved in the production process.
Additionally, it can reduce the need for material handling and transportation between production areas, which can lead to a decrease in overall lead times. Finally, it can also help to reduce the amount of inventory needed in the production process, allowing for more efficient use of resources.
Increase Flexibility
Cellular manufacturing is a type of lean manufacturing process that produces multiple products or services by organizing production into dedicated "cells." By organizing production into cells, companies can increase flexibility by allowing the cells to be rapidly reconfigured to meet changing customer demands. This enables the company to quickly and efficiently adapt to changing product lines and customer needs.
Additionally, cellular manufacturing reduces setup times and improves throughput by eliminating product transfers between processes and departments. This allows the company to switch between different product lines and produce more products rapidly.
Improve Quality
Cellular manufacturing can improve quality by reducing the number of steps in the process and increasing the efficiency of the production process. Grouping machines can achieve this into cells responsible for producing similar components.
Having machines in the same cell working together increases the flow of production, reduces setup times, and eliminates unnecessary steps. This leads to improved quality, as fewer errors will occur due to streamlined processes and fewer defects due to fewer operations.
Reduce Lead Times
Cellular manufacturing is a production system where similar operations are grouped together in factory areas with the same resources and personnel. This allows for the production of multiple products in small batches.
By utilizing this system, lead times can be reduced since resources are allocated and organized more efficiently.
Maximize Machine Utilization
Cellular manufacturing combines machines and labor in a single work cell. This approach allows for increased machine utilization, as the devices in the cell can be used more efficiently and effectively. By grouping machines together, workers can move quickly between tasks, allowing for shorter setup times and faster production cycles.
In addition, cellular manufacturing also allows for the implementation of Just-in-Time (JIT) production, which can further maximize machine utilization by reducing downtime and unnecessary inventory. Finally, cellular manufacturing can also help to improve workflow and reduce costs by eliminating the need to move parts and materials between multiple workstations.
Improve Cost Control
Cellular manufacturing can improve cost control by reducing production costs, reducing setup time, and increasing efficiency. It also reduces inventory costs by allowing parts to move from station to station without waiting for a batch to be completed, and it reduces waste by allowing products to be produced using only the materials and resources needed for immediate use.
Additionally, cellular manufacturing can reduce costs by allowing for better scheduling for production and delivery and by reducing the amount of paperwork and administrative tasks associated with traditional production methods.
Increase Product Variety
Cellular manufacturing is a lean manufacturing technique that aims to reduce setup time by organizing production into cells that can manufacture a variety of products.
This allows for increased product variety as each cell can be set up to produce a different product.
Enhance the Working Environment
Cellular manufacturing can also improve the working environment by reducing the amount of time employees spend on setup and waiting for their tasks to be completed. This can help to reduce stress levels and improve overall morale in the workplace.
Types of Cellular Manufacturing Layout
So far, we have learned that cellular manufacturing involves a layout where machines are grouped into cells. Each cell is designed to produce a specific part or group of parts in a continuous flow. The cells are connected to a standard material handling system, which facilitates the flow of parts throughout the entire facility. This type of layout is ideal for facilities that produce a wide variety of parts.
This section takes us through the different types of layouts. Let’s take a look.
Group Technology Layout
Group Technology Manufacturing Layout is a type of layout used in manufacturing that groups machines with similar functions and processes together. This layout allows for efficient production and reduces the time and resources needed to manufacture products.
Additionally, the grouping of machine functions can improve safety and quality control in the manufacturing process.
Fixed Position Layout
Fixed position manufacturing layout is a type of layout where the location of the product is fixed, and the resources are moved to it. This is usually used for large and/or complex products, like ships, aircraft, or large machinery.
It is also used for highly specialized products like medical devices. This type of layout is designed to ensure the highest quality since the product is not moved during the production process.
Modular Manufacturing Layout
A modular manufacturing layout is a type of manufacturing system in which a factory is divided into modules or distinct production areas. Each module is designed to produce a specific product or range of products.
The modules are arranged to maximize the efficiency of production, and the parts and components that are used in the various modules are supplied from a centralized source. Modular manufacturing is often used by companies that produce a variety of products and need to switch from one product to another quickly.
Assembly Line Layout
Assembly line layout is a production layout in which workstations are arranged in a line, and materials are moved from one workstation to the next in a continuous flow. The goal of an assembly line layout is to streamline production, reduce costs, and produce products quickly and efficiently.
This type of layout is used in many industries, including automotive, electronics, and food production.
Flexible Manufacturing System (FMS) Layout
A Flexible Manufacturing System (FMS) Layout is an organized arrangement of machines, workstations, and other components used to produce a specific product or family of products. The layout of an FMS is designed to optimize production flow and maximize worker productivity.
It typically includes conveyor systems, robotic arms, automated material handling systems, and other specialized equipment. The layout is also designed to be flexible enough to accommodate changes in production requirements.
Kanban Manufacturing Layout
Kanban Manufacturing Layout is a type of Lean manufacturing system that uses visual signals to regulate the flow of material and goods through the production process. This system is based on the Japanese word “Kanban,” which means visual signal. The layout is composed of the production stage, the input sources, and the output destinations.
The material is moved through the stages using a pull system, where the demand from the downstream production stages “pulls” the material from the upstream steps. This system is designed to reduce waste and increase productivity.
Read more about Push and Pull Systems in Manufacturing Management
Hybrid Manufacturing Layout
Hybrid Manufacturing Layout is a layout that combines different types of manufacturing and automation processes in order to increase efficiency and reduce production costs. This type of layout is typically used in larger manufacturing facilities looking to maximize output while minimizing costs.
The layout typically involves a combination of traditional manual production, automated production, and even robotic production. This type of manufacturing layout is designed to increase flexibility, reduce waste, and improve overall quality.
Linear or I-shaped Cellular Layout
A linear or I-shaped cellular manufacturing layout is a factory floor plan where machines are arranged in a linear sequence to produce a product. This type of layout is designed to reduce the movement and labor required to make a product, resulting in shorter production times, lower costs, and improved quality.
Additionally, this type of layout is helpful in providing quick and easy access to parts and materials.
U-shaped Cellular Manufacturing Layout
A U-shaped cellular manufacturing layout is a production line layout where machines are arranged in a U-shape, allowing for easy access to each station by the operator.
This type of configuration has the advantage of allowing for quick and efficient workflows, and the proximity of machines to each other often allows for reduced cycle times. It also makes it easier to track and monitor the production process and identify any potential problems quickly.
O-shaped Cellular Manufacturing Layout
An O-shaped cellular manufacturing layout is an arrangement of machines and workstations in which each workstation is located in a separate, distinct area (cell) within the production facility. The machines and workstations are arranged in an 'O' shape, with the devices located at the outside of the 'O' and the workstations located in the middle of the 'O'.
This type of layout facilitates the flow of materials, reduces material handling costs, and allows for quick product changeover. The layout also encourages machine operators to work together as a team and helps reduce production costs.
T-shaped Cellular Manufacturing Layout
A T-shaped cellular manufacturing layout is an arrangement of production equipment and workers in a factory in which machines are arranged in the shape of a “T,” with the vertical line representing the main production line and the horizontal line representing the secondary production line.
This layout facilitates the efficient movement of materials and workers between the production lines, allowing for a more efficient production process.
S-shaped Cellular Manufacturing Layout
An S-shaped Cellular Manufacturing Layout is a manufacturing production system in which machines are arranged in a U- or S-shaped configuration. This arrangement allows for more efficient production. It is because the machines are set in a continuous loop, and the products can move from one machine to the next without having to be transported between multiple workstations.
This arrangement allows for the elimination of wasted motion, which in turn leads to increases in productivity and cost savings.
Benefits of Implementing Cellular Manufacturing
Cellular manufacturing can benefit both the company and its customers. Companies benefit from increased productivity, improved quality, lower costs, and shorter lead times. Customers benefit from the increased delivery speed and improved product availability.
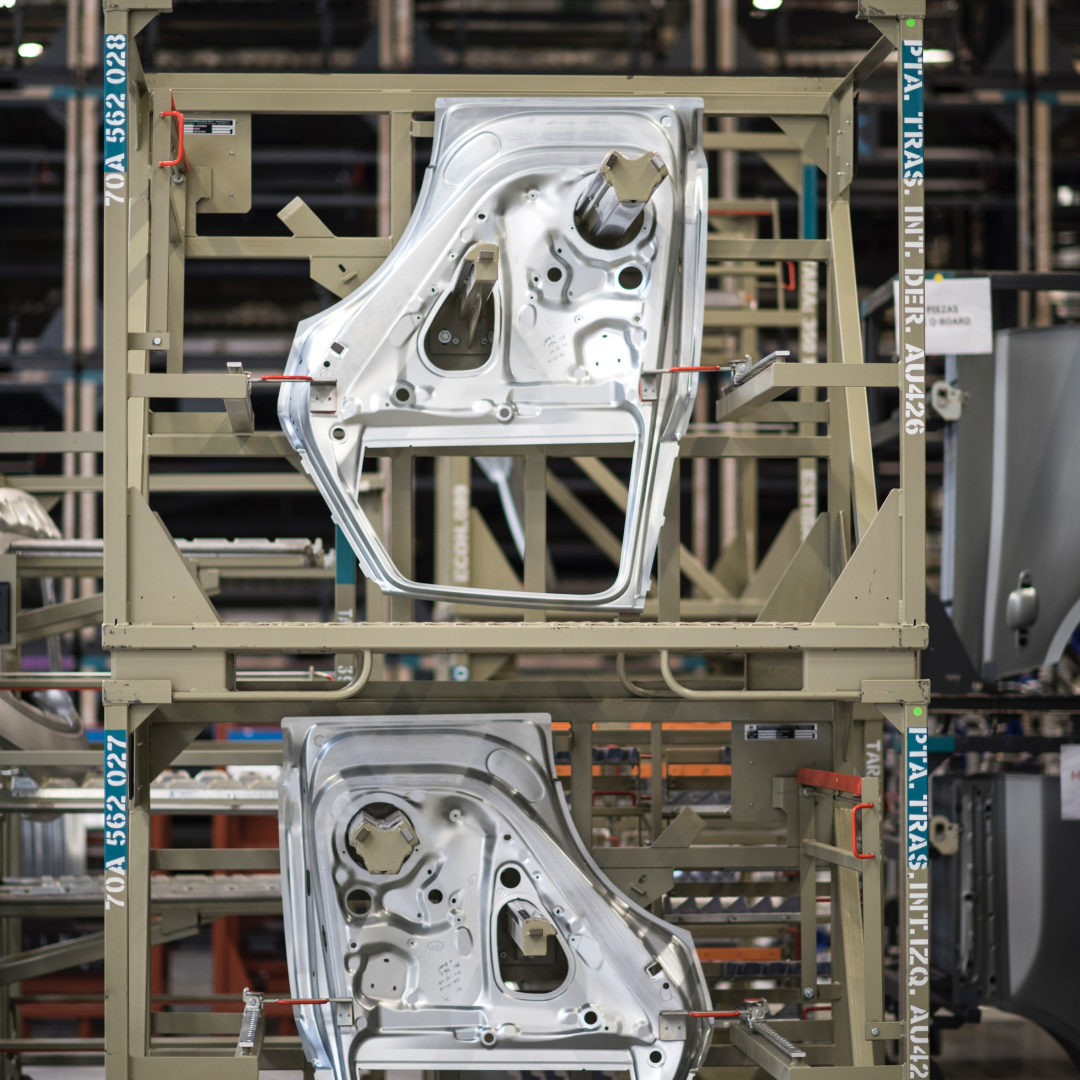
In addition, cellular manufacturing can also reduce inventory levels, leading to lower overhead and improved customer satisfaction. The implementation of cellular manufacturing can also benefit employees by providing them with improved working conditions and a more streamlined, efficient workplace. It also results in higher employee motivation and enhanced employee morale due to the increased sense of job security and improved work environment.
Finally, it can also lead to increased customer satisfaction, as the company is able to meet customer needs and expectations better.
The benefits of cellular manufacturing can be further summarized as follows:
- Increased Efficiency: Cellular manufacturing increases the efficiency of production by allowing for the same production tasks to be done in smaller, more manageable batches. This reduces the amount of time spent on each task and allows for more efficient production.
- Reduced Costs: Cellular manufacturing reduces costs by reducing the amount of time spent on each task and eliminating the need for many machines and workers. Smaller batches of products can be produced more quickly, leading to reduced production costs.
- Improved Quality: By reducing production times and increasing efficiency, cellular manufacturing can help to improve the overall quality of manufactured goods. This is due to the fact that fewer errors are likely to occur, and production lines are better able to focus on the quality of each product.
- Higher Customer Satisfaction: Because of the improved efficiency and quality of production, customers are more likely to be satisfied with the products that are produced using cellular manufacturing. This leads to higher customer retention and repeats business.
- Easier to Train Employees: The organized nature of cellular manufacturing makes it easier for new employees to learn the production process. This can reduce the amount of time and money that is needed for training.
- Reduced Wasted Space: By organizing the workplace into cells, it reduces wasted space as everything is placed in an efficient manner. This helps to reduce costs as well as the waste of resources.
5 Challenges of Cellular Manufacturing
The Challenges of Cellular Manufacturing can affect a company in many ways, including decreased efficiency, increased costs, and lowered morale. Decreased efficiency can be a result of the complexity of the process, as well as the need for more flexibility when dealing with changes in customer demand.
Additionally, a lack of communication between cells can lead to disruptions and inefficiencies. Increased costs can arise from the need to purchase specialized equipment and increased labor costs.
Lastly, employee morale can suffer due to the need for more continuity and cooperation between cells. This can lead to turnover rates that are higher than average, resulting in a loss of experienced workers.
Here are the challenges that cellular manufacturing can pose:
- High Setup Costs: The upfront cost of setting up a cellular manufacturing system can be high. This is due to the fact that it requires significant investment in new equipment, technology, and training for workers.
- Complex Logistics: Another challenge of cellular manufacturing is the increased complexity of logistics. This is because the process requires the movement of parts and materials between different production cells.
- Complex Scheduling: The scheduling of activities within a cellular manufacturing system can be complex. This is because each production cell must be coordinated with the others to ensure the most efficient use of resources.
- Limited Flexibility: The highly structured nature of cellular manufacturing systems can limit flexibility and adaptation to changing market conditions.
- Difficult to Monitor: Cellular manufacturing systems can be difficult to monitor and control. This is because production cells are located in different locations, and it can be challenging to track progress and identify potential problems.
The Process of Cellular Manufacturing
The cellular manufacturing process entails the following steps:
- Assess the Production Environment: The first step of cellular manufacturing is to assess the production environment and identify the production processes and materials used. This includes evaluating the current layout of the production space and the machines and tools used to manufacture products. It also involves understanding the customer needs and expectations and the products that need to be produced.
- Design the Production Cells: The next step is to design the production cells. This involves determining the number of production cells and the type of machines needed for each cell. This includes choosing the size and location of each cell and the layout of the machines within each cell.
- Develop a Process Flow Chart: After the production cells are designed, a process flow chart needs to be developed. This chart should outline the specific steps and processes that need to be completed in order to produce the desired products.
- Assign Resources: Once the process flow chart is created, the resources needed to complete the production process must be assigned. This includes assigning personnel, machines, tools, and materials to each production cell.
- Monitor and Analyze Performance: After the production cells are set up, they need to be monitored and analyzed to ensure that they are running efficiently.
Potential Pitfalls to Consider
Cellular manufacturing can be challenging to implement. Different organizations can face struggles while trying to execute them. Potential difficulties you must consider with cellular manufacturing are as follows:
Limited Resources
This can be a challenge in cellular manufacturing in a number of ways. For example, limited resources can limit the number of machines, personnel, and parts available to be used in the cell.
This can lead to increased production time and potentially lower quality due to a lack of resources available to complete the job. Additionally, it can be difficult to scale up production when resources are limited.
Finally, limited resources can lead to higher costs due to buying more parts or machines to make up for the lack of available resources.
Manufacturing cellular phones require plenty of resources, including raw materials, parts, and labor. Depending on the size of the manufacturing operation, there may need to be more resources available to meet the demand for the product. This could lead to delays in production and customer dissatisfaction.
Quality Control
One of the biggest challenges with cellular manufacturing is maintaining quality control. It isn't easy to maintain high-quality standards when parts are continually moving through different machines and processes. It is also difficult to pinpoint which method or machine is causing quality issues.
Additionally, it is difficult to trace the issue back to its source if a quality issue is identified as parts are moved through multiple machines. Finally, as machines are shared for multiple processes, it can be not easy to set up and maintain efficient quality control systems.
Quality control is essential to the success of any manufacturing operation. Poor quality control can lead to defective products that could harm the customer or cause them to return the product. RMA (returns process) can further be tedious for most companies.
Cost
Implementing a cellular manufacturing system can be expensive, as it requires significant investment in equipment, personnel, and training. Additionally, labor costs can be high due to the need for skilled workers.
Companies must also consider the cost of training and implementing new systems and processes. Finally, there are often costs associated with integrating the systems and processes within the existing production environment.
Additionally, if the system is not properly maintained, costs can increase due to inefficiencies and downtime.
Market Trends
Market trends can be a challenge for cellular manufacturing due to the ever-changing consumer demand. The demand for certain products can be unpredictable and can cause production lines to become obsolete over time.
Additionally, technological advances can lead to changes in product design and manufacturing processes, meaning that cellular manufacturing may need to be adapted to keep up with the market. Finally, the availability and cost of materials can also fluctuate with market trends, making it difficult to plan and budget for production.
As technology evolves, so do the needs of the customer. Keeping up with the latest trends in the cellular industry can take time and effort. If the manufacturer is not able to meet the customer’s needs, they may not be able to stay competitive in the market.
Regulatory Compliance
Regulatory compliance can be a challenge in cellular manufacturing due to the increased complexity of operations. Cellular manufacturing requires a higher degree of coordination between multiple workstations, which can be difficult to manage and ensure compliance with applicable regulations.
Additionally, the smaller, more specialized production lines used in cellular manufacturing can make it harder to ensure that all required safety and quality control measures are in place. Moreover, the fast-paced nature of the production process can make it difficult to keep up with changing regulations or ensure that all processes are being conducted in accordance with required standards.
Cellular manufacturers must comply with government regulations in order to operate. Failing to comply can lead to fines and other penalties. The manufacturer must be aware of any changes in regulations to avoid any potential problems.
Cellular Manufacturing Vs. Traditional Layouts
There are various differences between cellular manufacturing and traditional layouts. Let’s see what they are:
- Cellular manufacturing increases resource utilization and flexibility by grouping together similar processes, allowing for faster product cycle times.
- Traditional layouts require more extensive facilities and more resources in order to accommodate all the different techniques needed to produce a product.
- Cellular manufacturing allows for the efficient flow of materials and machines, with little or no extra movement of personnel or equipment.
- Traditional layouts may lead to increased waiting times for materials and machines and improved transport costs. This is due to having to move materials and machines around the facility.
- Cellular manufacturing reduces setup times and scrap rates as the machines and processes are organized in close proximity.
- Traditional layouts can lead to higher levels of inventory, as each process is separated from the others and requires its own inventory.
MRP Systems and Cellular Manufacturing
MRP systems can be very beneficial in cellular manufacturing by helping to streamline and optimize production. MRP systems can help to reduce lead times and inventory levels by providing detailed information on materials and components needed for manufacturing. They can also help to improve scheduling, forecasting, and cost control.
Additionally, MRP systems provide visibility into production processes, allowing for better decision-making and improved efficiency.
- Reduced Inventory: MRP systems can help reduce the amount of inventory that is kept in stock by calculating the exact amount of materials needed for manufacturing, resulting in improved inventory accuracy.
- Reduced Lead Times: MRP systems can help reduce lead times by forecasting customer demand and providing accurate information about the availability of materials and components.
- Reduced Costs: MRP systems can help reduce costs by eliminating the need for manual data entry and providing more accurate data for better decision-making.
- Improved Communication: MRP systems can help improve communication between different departments, allowing for better collaboration and improved decision-making.
- Improved Visibility: MRP systems can provide visibility into the production process and inventory levels, allowing for better control and quicker response times.
- Improved Quality: MRP systems can help improve quality by providing accurate information about the production process.
- Providing Real-time Updates: MRP systems can help increase efficiency by providing real-time information regarding production and inventory levels, which can be used to streamline processes and reduce waste.
Cellular Manufacturing FAQs
Let’s walk through some of the commonly asked questions on cellular manufacturing:
Q: Where is cellular manufacturing used?
A: Cellular manufacturing is used in a variety of industries, including automotive, aerospace, electronics, and medical device manufacturing. It is also used in the food and beverage industry to produce a variety of products, from essential snacks to more complex items such as frozen meals.
Q: How does Cellular Manufacturing reduce costs?
A: Cellular manufacturing reduces costs by eliminating waste, reducing setup times, and improving quality. Having all the necessary tools and machines in the same location eliminates the need to move parts from one station to the next. This reduces setup times, as the pieces don’t need to be moved around, and it reduces material handling costs.
Q: How is material flow managed in a Cellular Manufacturing system?
A: Material flow in a Cellular Manufacturing system is managed by the use of flexible conveyors and other automated equipment. Conveyors can be used to move materials from one cell to another and from the storage area to the cells.
Automated equipment, such as robots and transfer machines, can also be used to move materials within the cells. A manufacturing control system coordinates the material flow and ensures that it is efficient and accurate.
Q: What types of materials are typically used in Cellular Manufacturing?
A: Cellular manufacturing typically uses a variety of materials, such as metal, plastic, composites, and wood. It also requires a variety of tools, such as lathes, saws, drills, and presses. Additionally, it may require specialized materials, such as die castings, forgings, and extrusions.
Q: Are assembly line layout and I-shaped layout in cellular manufacturing the same?
A: No, they are not the same. An assembly line layout is a traditional manufacturing system in which each worker is assigned a specific task within a larger product-producing process. An I-shaped layout is a type of cellular manufacturing system in which the production process is organized into individual cells, each of which contains the necessary equipment and tools to produce a specific component or sub-assembly of the product.
Conclusion
At the end of the day, cellular manufacturing is a highly efficient and cost-effective way to streamline production and create a more organized and productive workflow. It is an effective way to ensure that each step of the manufacturing process is completed with maximum efficiency and accuracy. It also allows for more customization and flexibility to accommodate the needs of customers.
The ability to quickly and accurately produce products, as well as maintain quality control, makes cellular manufacturing an ideal choice for many businesses. By combining the principles of lean manufacturing with the power of automation, cellular manufacturing can provide a competitive advantage in today's global marketplace.
How can Deskera Help You?
Deskera can help in cellular manufacturing by streamlining the production process and providing real-time data. Deskera's cloud-based ERP solutions provide access to production data from any location and make it easier to monitor production, record and track inventory, and manage orders.
Here are some of the ways Deskera ERP and MRP systems can help you:
- Make a manufacturing schedule
- Maintain a Bill of Materials
- Produce detailed reports
- Create your own dashboard, among other things!
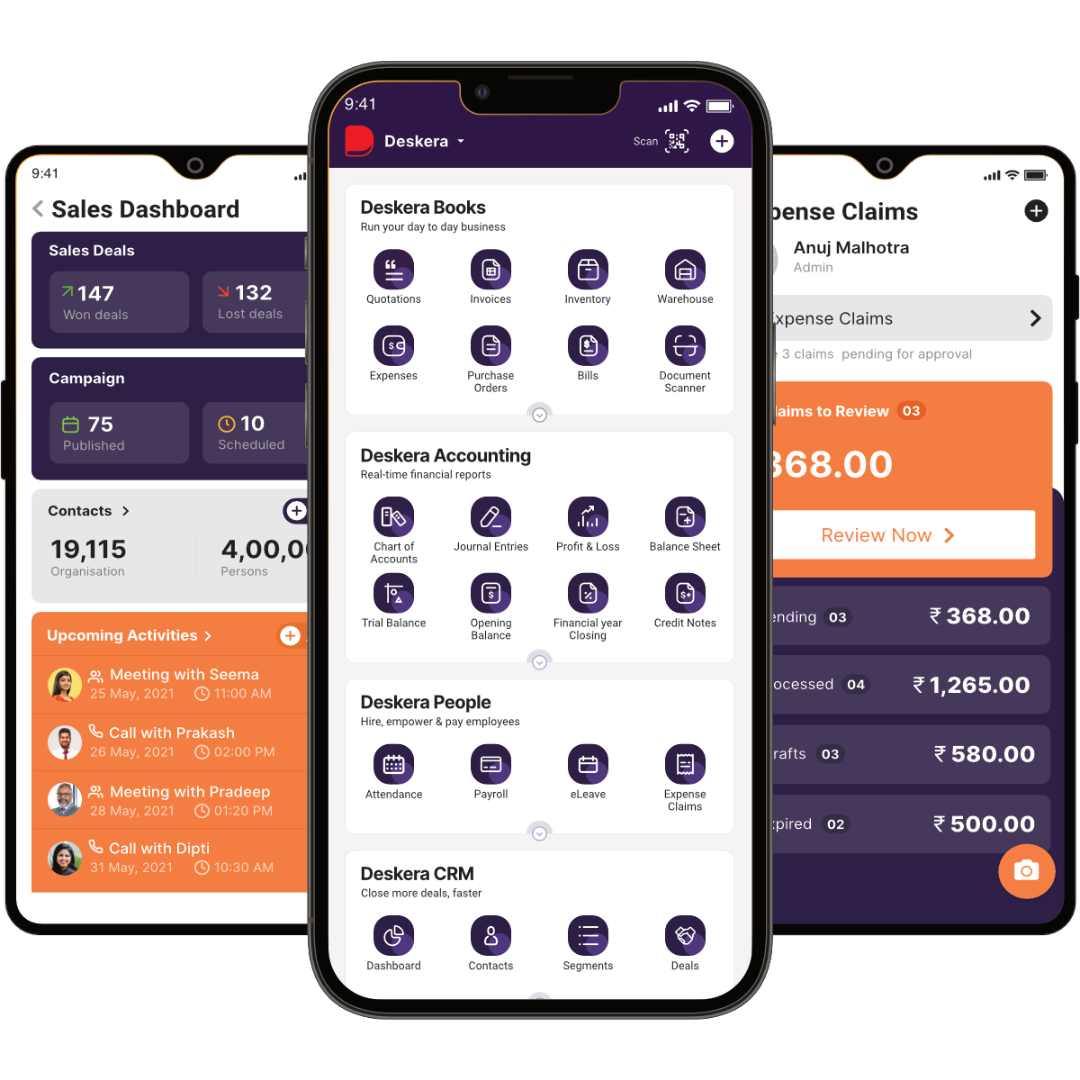
Deskera Books is a cloud-based accounting and bookkeeping software designed to help small and medium businesses manage their finances, bookkeeping, and accounting operations. Deskera Books has a mobile app available for iOS and Android devices, allowing users to access their financial data anytime, anywhere.
Deskera CRM is a cloud-based customer relationship management (CRM) software that helps businesses manage their customer data, sales, marketing, and service operations. It also provides insights into customer needs and preferences, so that businesses can better understand their customers and build stronger relationships.
Deskera People is an all-in-one HR solution designed to help streamline HR operations and improve employee productivity. It provides tools for employee onboarding, performance management, payroll, benefits, and more.
Key Takeaways
- Cellular manufacturing is a production system that combines the processes of a production line into a single, unified manufacturing cell.
- Cellular manufacturing aims to group similar operations together and reduce the amount of non-value-added movement of features and materials. This helps to reduce costs and increase the efficiency of the production process.
- It is a type of lean production that focuses on reducing waste and increasing efficiency by organizing production processes into individual, self-contained cells.
- Minimizing setup times, maximizing flow efficiency, reducing work in process, and increasing flexibility are among the goals that cellular manufacturing aims to achieve.
- Fixed position layout, modular layout, group technology, and Kanban manufacturing are some of the design layouts observed and utilized in cellular manufacturing.
- Companies can achieve better efficiency, quality, and customer satisfaction by implementing cellular manufacturing. Also, they can lower costs and reduce wasted space in the process.
- Higher setup costs, complicated logistics, and difficulty in monitoring are some of the challenges in cellular manufacturing.
- MRP systems can be very beneficial in cellular manufacturing by helping to streamline and optimize production. MRP systems can help to reduce lead times and inventory levels by providing detailed information on materials and components needed for manufacturing.
Related Articles
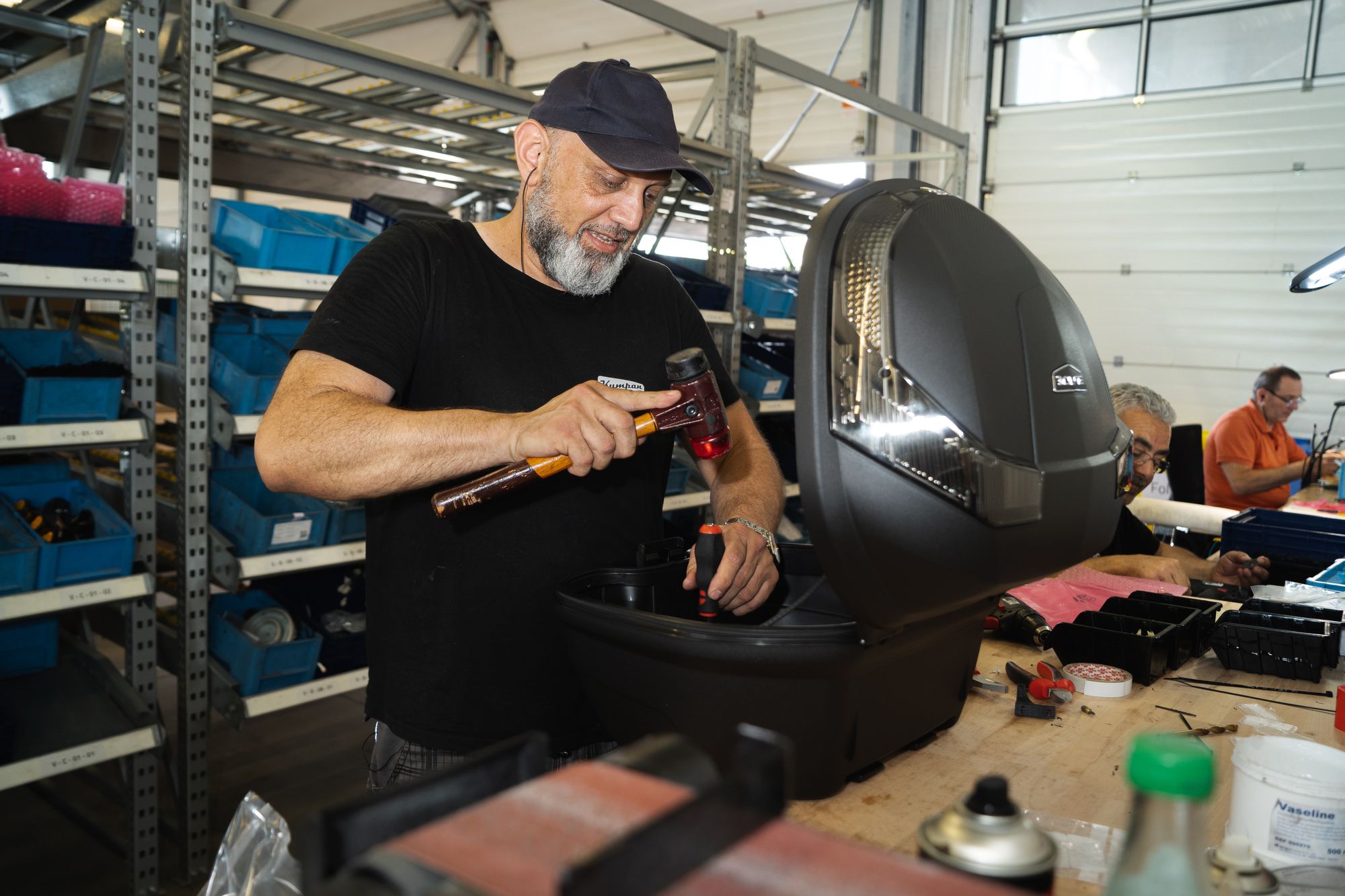
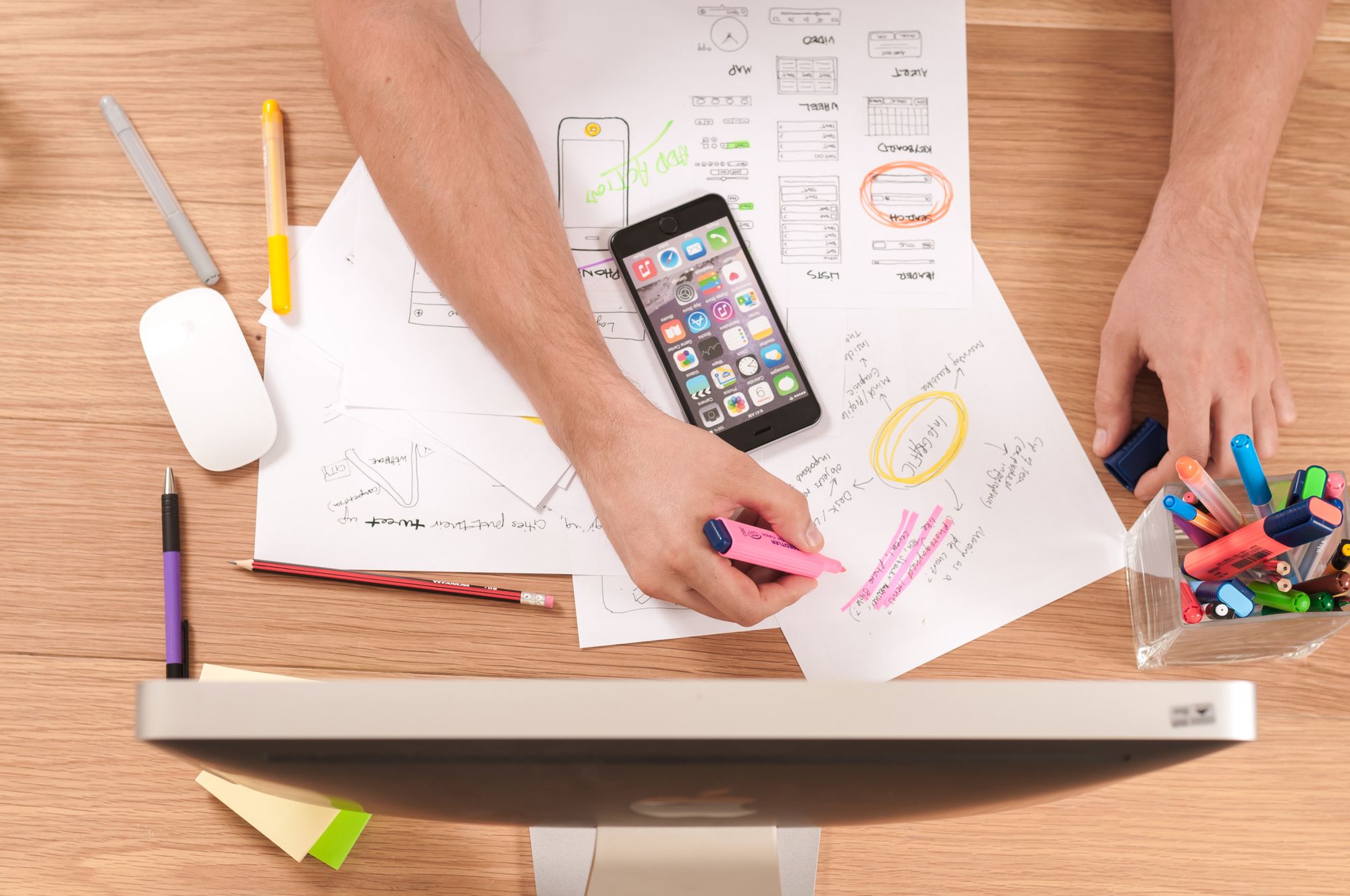
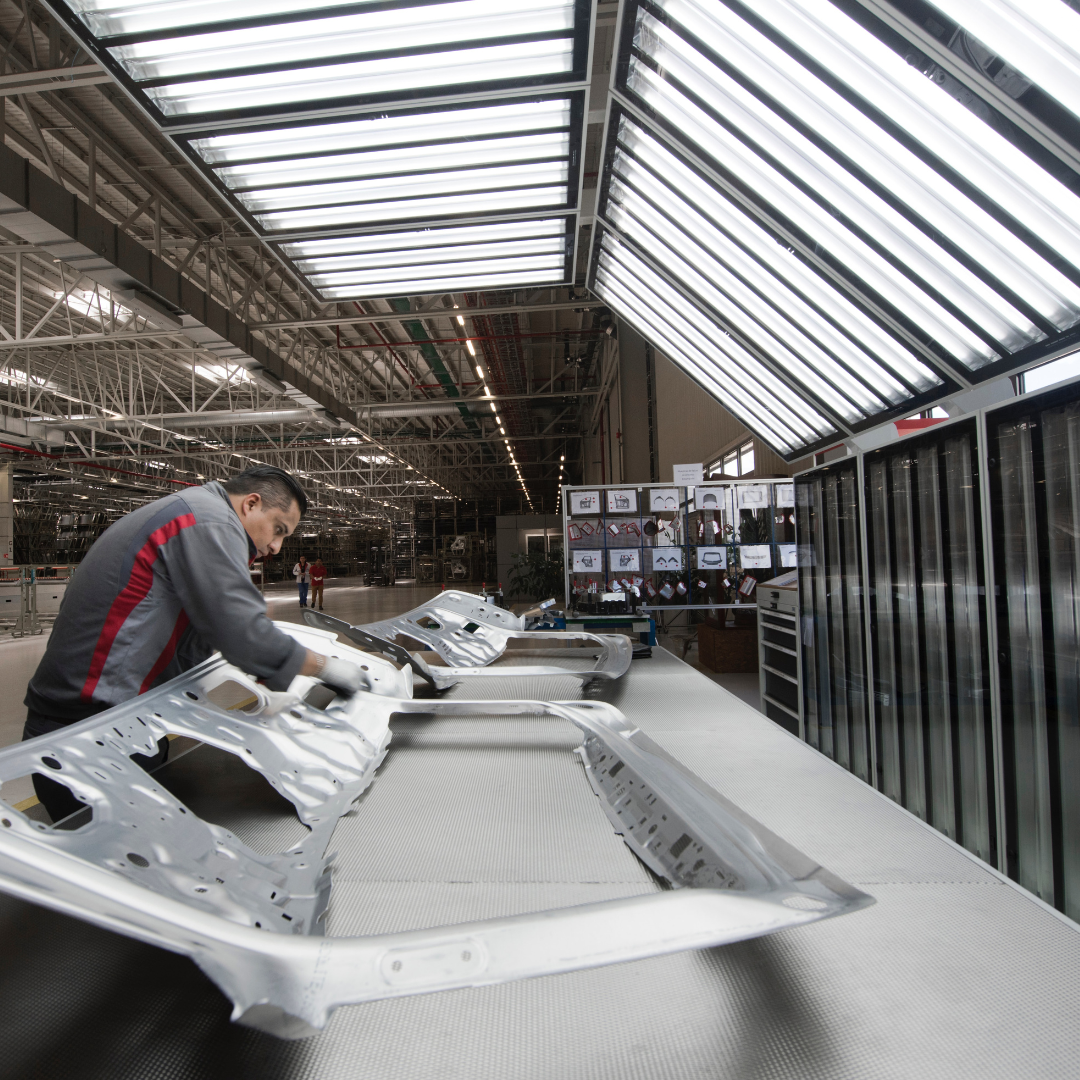
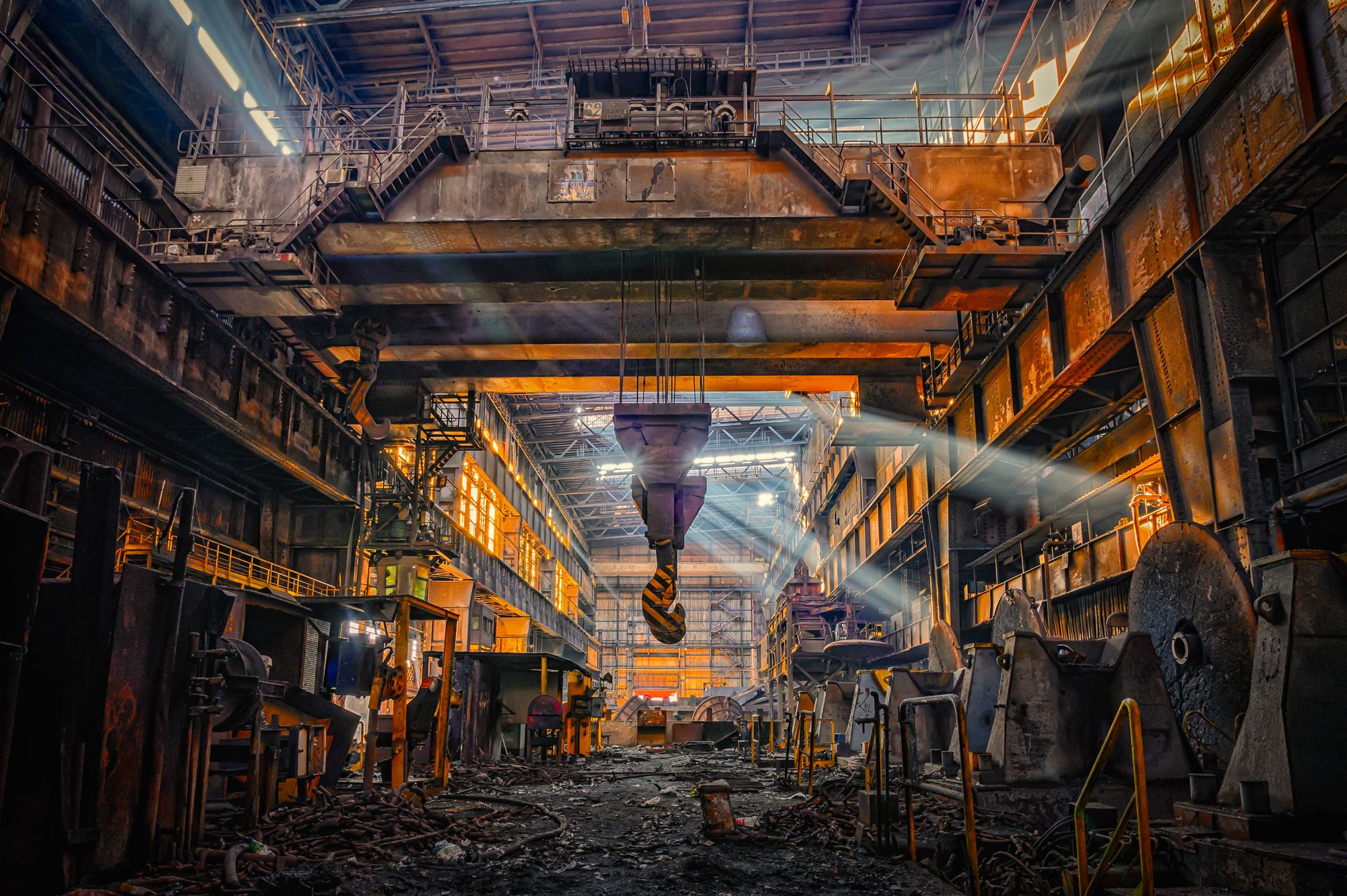