Have you ever wondered how companies produce large volumes of goods quickly and efficiently? It is accomplished by batch production. Batch production is a manufacturing process that can help companies produce multiple items in a single run. This results in cost and time savings.
According to the US Bureau of Labor Statistics, over 12 million Americans are employed in the manufacturing industry. These workers are responsible for producing a wide variety of items, from consumer electronics to car parts.
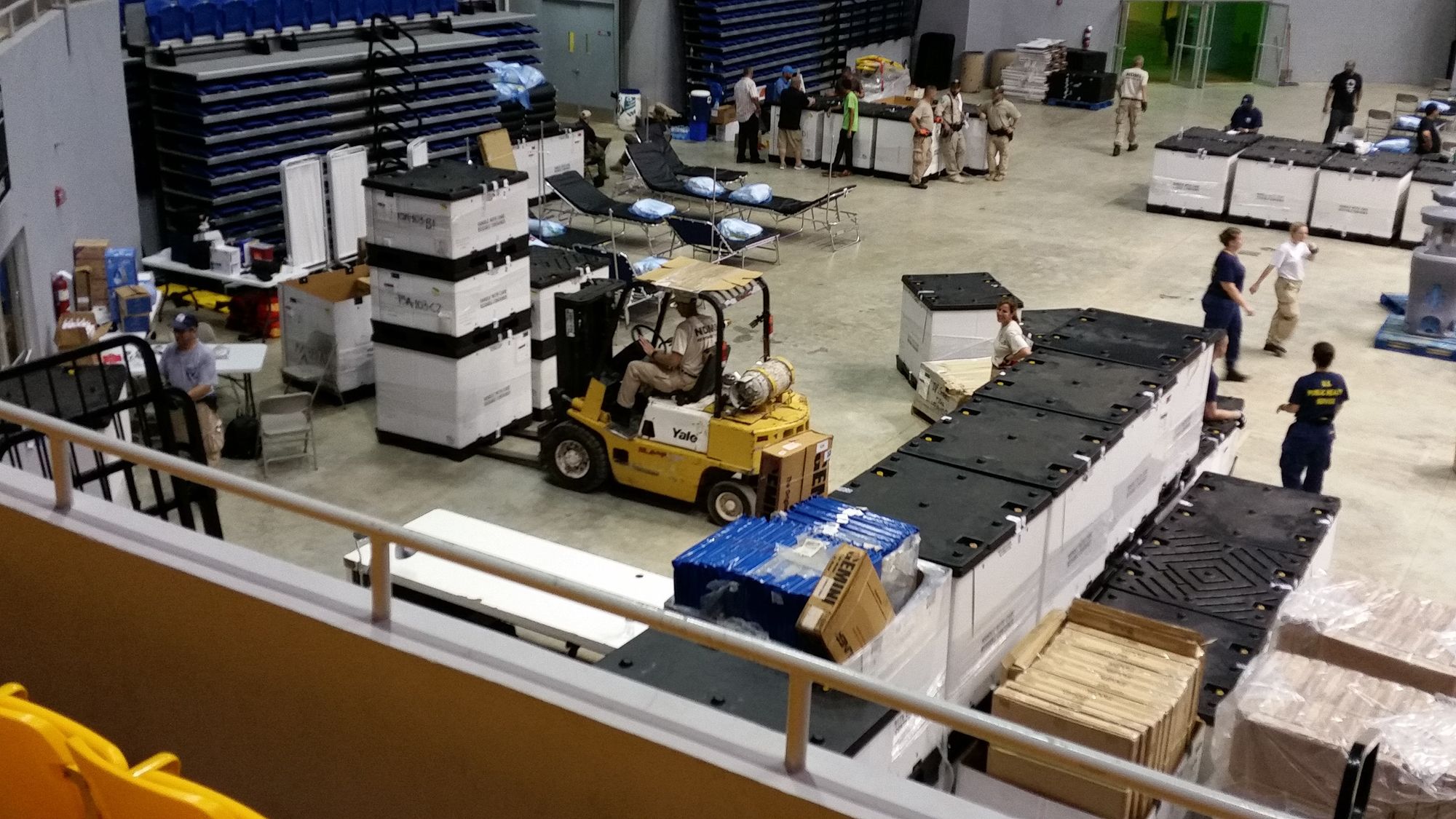
The batch production process is broken down into segments or batches, making it easier to manage and control. This manufacturing method is ideal for producing items requiring multiple steps for completion. Examples include electronics, furniture, and car parts.
In this article, we will explore the advantages and drawbacks of batch production. We will provide examples of its use in manufacturing and discuss how it can help companies reduce costs and improve profits.
- What is Batch Production?
- Why Do Manufacturers Use Batch Production?
- Master Batch Manufacturing Process
- Optimizing the Efficiency of Batch Production Systems
- Advantages and Disadvantages of Batch Production in Manufacturing
- Batch Production vs Continuous Production vs Assembly Line Production
- Conclusion
- Key Takeaways
What is Batch Production?
Batch production is a manufacturing process involving producing a certain number of products in a given quantity. It is often used to produce electronics, automotive parts, food products, and pharmaceuticals. Batch production is an economical and efficient way to produce high volumes of products.
- The production process is divided into batches, each requiring a specific amount of time to complete. Each batch is then moved on to the next process until the final product is completed.
- The batch production process begins with selecting materials and components. These materials and components are then assembled into a single unit. This unit is tested and inspected to ensure it meets the desired specifications.
- Once the unit passes all tests and inspections, it is placed into a batch and sent to the assembly line. The components are joined together, and the final product is created here. The product is then tested and inspected to ensure it meets the desired specifications.
- After the product passes all tests and inspections, it is packaged and sent to the customer.
- Batch production is a critical component of Lean Manufacturing and is used to reduce waste and increase efficiency. It also allows for greater control over the production process. It enables manufacturers to produce higher-quality products.
It is a cost-effective solution for companies that must quickly produce large amounts of products. It also allows companies to keep up with demand without purchasing additional production equipment.
Batch production also offers flexibility in terms of production scheduling. Companies can choose to produce products in batches at different times or continuously. It allows them to adjust their production schedule to meet customer demand.
Main Features of Batch Production in Manufacturing
Batch production is used in many industrial and commercial settings, from food processing to automobile manufacturing. Batch production allows companies to produce large quantities while maintaining quality control and cost-effectiveness.
Here are the main features of batch production:
- Automation: Automation is one of the main features of batch production. Automation involves using machines and robots to carry out repetitive tasks and reduce human intervention. It helps to reduce costs, improve efficiency and accuracy, and increase productivity. It also reduces the chances of errors, making it more reliable than manual processes.
- Standardization: Standardization is another important feature of batch production. Standardization involves establishing procedures and processes to be followed when producing a product. It helps to ensure that each batch of products is made with the same quality and specifications. It helps to ensure consistency and uniformity in the final product.
- Quality Control: Quality control is a vital component of batch production. Quality control involves checking each batch of products for any flaws or defects before it is released for sale. It helps to ensure that customers receive a product that meets their expectations.
- Flexibility: Flexibility is also an essential aspect of batch production. Flexibility involves adjusting the production process depending on the product's specifications. It helps to keep up with changes in demand or the introduction of new products. It also allows the production process to be adapted to suit different materials.
- Cost-effectiveness: Cost-effectiveness is another important feature of batch production. Batch production helps to reduce costs by reducing the time and resources required to produce a batch of products. It helps to reduce overhead costs and maximize profits.
- Scalability: Scalability is one of the other features of batch production. Scalability involves adjusting the production process to accommodate larger batches of products. It helps to increase production efficiency and reduce costs. It also makes it easier to switch between different production processes depending on the changing needs of the business.
Overall, it saves companies time and money while still meeting customer demands and maintaining quality control. Batch production is versatile, allowing companies to produce goods in multiple sizes and shapes. It can also be used in multiple quantities.
Stages in Batch Production
Batch Production is one of the most efficient and cost-effective ways to mass-produce items. Here is a breakdown of the significant stages in batch production.
Planning: The first batch production stage includes planning. It involves the preparation of a production plan and schedule. It involves determining the quantity of the product, the resources required, the time and cost associated with production, and the production schedule.
This stage also consists of identifying a suitable production process, selecting machines and other equipment, and selecting the personnel responsible for production.
Preparation: After the planning process is completed, the next step is to prepare the materials, equipment, and tools needed for the production process. It includes setting up the work area and ensuring the materials and tools are in good condition. The production line is correctly set up.
Manufacturing: The third stage of batch production is the actual manufacturing of the product. This stage involves the preparation of the raw materials, the setting up of the machines and other equipment, the placement of the personnel in the appropriate positions, and the actual production of the product.
Final Testing: After the product has been assembled, it is tested to ensure it meets the specified requirements. This stage includes running the product through a series of tests to ensure it is safe, efficient, and compliant with industry standards.
Packaging: The fifth batch production stage is the product's packaging. It involves the selection of suitable packaging materials, the designing of the packaging, and the printing of labels, logos, and other information.
The product's packaging is done to ensure that the product is protected from damage and deterioration during storage and shipment.
Shipping: The sixth batch production stage is the product's shipping. It involves the selection of suitable carriers and the preparation of the required documents.
Then the product is loaded into the container or trailer for shipment. This stage also involves tracking the shipment to ensure the product reaches its destination on time.
Maintenance: The seventh stage of batch production involves the maintenance of the machines and other equipment used in the production process. It involves regular servicing and repairing the equipment, replacing worn-out parts, and adjusting the devices to ensure they function correctly. This stage also consists of cleaning and maintaining the production area to ensure it is safe and conducive.
By following these steps, businesses can ensure that their production process is successful. Their products are of the highest quality.
Why Do Manufacturers Use Batch Production?
Manufacturers use batch production for a variety of reasons. These include cost reduction, increased efficiency, and improved quality control. Here are some of the reasons why manufacturers use batch production:
- Manufacturers use batch production to take advantage of cost savings associated with batch production. Batch production is the process of producing multiple products in one go. It means that they can make a large number of products in one production run.
- It saves on costs associated with starting and stopping the production process. It also reduces the need for frequent changes in the production process. It minimizes wastage and reduces operational costs.
- Batch production allows manufacturers to control the quality of the goods produced, as they can be tested and inspected before being released into the market. It ensures that the goods are of the highest quality and meet customer expectations.
- Batch production allows manufacturers to produce goods in different sizes and shapes. It helps them meet the needs of various customers, as they can make goods with different specifications. It helps them to remain competitive in the market and develop a wide range of products.
- Batch production is much faster than other manufacturing processes. It allows manufacturers to produce goods quickly and efficiently. It reduces the time taken to manufacture goods. It helps to reduce overall production costs. It will enable manufacturers to meet customer demands quickly.
- Lastly, batch production can be used for production planning. Manufacturers can easily plan their production schedule by producing batches of similar products. It ensures that all products are made on time. It allows manufacturers to meet customer needs and deadlines better.
Overall, batch production is an effective way for manufacturers to reduce costs and increase efficiency.
When to Use Batch Production?
The primary purpose of using batch production is to save time and money. This type of production is generally more efficient than individual production. It allows multiple items to be produced at the same time. It can result in significant cost savings, eliminating the need for multiple setups and production runs.
Additionally, it also reduces the risk of errors and wasted materials, as all items are produced at the same time.
- Batch production is also beneficial for products requiring a specific set of conditions. For example, products that need to be heated, cooled, or pressurized require particular temperatures and settings.
- Batch production ensures that all of the items are produced consistently. It also helps reduce the risk of contamination, as all items are made in the same environment.
- Batch production is only sometimes the most efficient option for production, however. This type of production is generally best suited for items that require a lot of time and energy.
- The setup and production runs can be time-consuming. Additionally, items with a short shelf life, such as food items, are unsuitable for batch production. The items may not be used before they expire.
When deciding whether to use batch production, it is essential to consider the product, production volume, and cost. For items requiring a lot of time and energy to produce or specific production settings. Batch production can be the most efficient option.
However, for items with short shelf life or items that do not require much time and energy to produce. Individual products may be more cost-effective.
Examples of Batch Production
Batch Production is one of the manufacturing industry's most commonly used production methods. Here are some examples of Batch Production:
1. Food Processing: Batch Production is common in the food processing industry. This type of production allows for high-volume production with minimized costs.
It is beneficial for maintaining food safety and quality standards. For example, a company may use batch production to produce prepackaged meals. It allows them to make meals in large quantities while still meeting food safety standards.
2. Pharmaceuticals: Batch Production is also used in the pharmaceutical industry. This type of production allows companies to produce large quantities of medication in a short amount of time. It is also beneficial for maintaining the quality and safety of drugs.
For example, a pharmaceutical company may use batch production to produce different types of medication. These types of medications include pills and capsules.
3. Electronics: Batch Production is also used in the electronics industry. This type of production allows companies to produce items in large quantities with minimal costs. It is also beneficial for ensuring quality standards are met.
For example, a company may use batch production to produce cell phone cases or other electronic accessories. It allows them to create large quantities of items in a short amount of time while still maintaining quality standards.
4. Automotive: Batch Production is also used in the automotive industry. This type of production allows companies to produce large quantities of car parts in a short amount of time. It is also beneficial for maintaining quality standards and reducing costs.
For example, a company may produce car doors or other parts in batch production. It allows them to produce large quantities of parts quickly and efficiently while still ensuring quality standards are met.
4. Textile Manufacturing: Textile manufacturing is another common application of batch production. This process involves producing a limited number of garments at a time.
It allows production to be efficient and ensures that the quality of the garments is consistent. For example, a clothing company may produce 100 shirts in a single day.
As you can see, batch production is a widely used production method in the manufacturing industry. It involves producing a limited number of items simultaneously and is used for various products, from automobiles to electronics. This production method has been used for centuries and is still widely used today.
Master Batch Manufacturing Process
The master batch manufacturing process is a technique used to produce a homogeneous mixture of a polymer and a colorant or other additives. It produces many colors and effects in plastic and rubber products.
The process involves melting, blending, and cooling the components to create the desired product. The following outlines the steps of the master batch manufacturing process.
- Selection of Raw Materials: The first step in the master batch manufacturing process is selecting the raw materials used to make the master batch. It includes selecting the base polymer, the additives, and other components used in the process. The selection of the raw materials will depend on the desired characteristics of the final product.
- Compounding and Mixing: Once the raw materials have been selected, they must be compounded and mixed to create the master batch. It is usually done in a compounding machine that combines the components in a specific ratio. The compounding machine also adds any other components that are needed, such as colorants and UV stabilizers.
- Pelletization: After the components have been compounded and mixed, the mixture is then pelletized. This process involves forming the mixture into small pellets, which can be used in the final product. Any pellets that do not meet the quality requirements are discarded. The process is repeated until the desired quality is achieved.
- Quality Control: Quality control is essential in the master batch manufacturing process. It involves testing the quality of the pellets to ensure they are up to the required standards. Any pellets that do not meet the quality requirements are discarded, and the process is repeated until the desired quality is achieved.
- Packaging: The final step in the master batch manufacturing process is packaging the master batch pellets. It is done to protect the pellets from damage during storage and transportation. The packaging can be done in various ways, such as in bags, boxes, or cartons.
Master batch manufacturing is a complex process that requires a great deal of attention to detail. It is to achieve the desired results. It is crucial to ensure that all the steps are followed correctly and that the quality control measures are strictly adhered to. It is to produce a superior quality master batch.
What Equipment Are Used in Batch Production?
The production of products in batches is usually much more efficient than making each item individually. It is essential to have the right equipment and machinery to ensure the process runs smoothly. Here is a look at some of the equipment needed to support batch production.
Robots:
Robots are becoming an increasingly popular option for businesses to use in batch production. They can be programmed to perform various tasks such as lifting and moving heavy items, welding, and painting. It helps to reduce the amount of manual labor required and can increase the speed and accuracy of the production process.
- In some cases, robots can even assemble complex parts and products. Robots can also be programmed to detect any product defects, allowing them to be quickly identified and fixed.
- Robots can work quickly and accurately, making them ideal for batch production. They can also operate 24/7, meaning production can be increased without employing more staff.
- Robots are also more cost-efficient than manual labor, as they require less maintenance and are not paid for their work.
- Despite their advantages, robots have some drawbacks to batch production. Robots cannot think for themselves. Robots require detailed programming and instruction to perform the necessary tasks. It can be costly in terms of both time and money.
- Additionally, robots are not able to adapt to changes in their environment. It means they may be unable to cope with sudden changes or unexpected problems.
Using robots for batch production can be a cost-effective and efficient way to increase production. However, it is crucial to consider the advantages and disadvantages of using robots before deciding.
CNC Machines:
Computer Numerical Control (CNC) machines are also used in batch production. These machines are programmed with instructions to cut, shape, and form materials into the desired product.
- CNC machines are computer-controlled tools that use numerical codes to cut and shape various materials. They are used in manufacturing to produce parts with high precision and accuracy.
- CNC machines are used in batch production to create high-volume, repeatable parts with consistent quality. They often create parts for cars, electronics, and other items that require precise shapes and dimensions.
- By using CNC machines, manufacturers can reduce costs and increase production speed and accuracy. They can also eliminate manual labor. Moreover, CNC machines allow manufacturers to produce complex parts quickly and accurately. It reduces waste and scrap.
- CNC machines are available in different types, such as milling machines, lathes, routers, etc. Each type of CNC machine is suitable for different types of production and application.
- CNC machines can produce parts with extremely tight tolerances and repeatability. It makes them ideal for producing high-volume, consistent parts.
3D Printers:
3D printing is becoming increasingly popular in batch production. 3D printers use a computer-aided design (CAD) program to create a 3D model of the desired product. The 3D printer uses various materials, such as plastic, metal, and ceramic, to create the product.
- It is a great way to quickly create numerous identical products without needing tooling or other expensive equipment.
- 3D printing is the most efficient way to produce large batches of products because it eliminates the need for costly tooling. It can be completed in a fraction of the time. It also allows for greater design flexibility and customization. It allows for more efficient production.
- 3D printing technology allows for greater design flexibility and customization. It allows for more efficient production. The technology also allows for improved quality control and accuracy. This results in better products.
Injection Moulders:
Injection moulders are another type of equipment used in batch production. These machines use heated plastic resin to create moulds of the desired product. The moulds are then used to inject the plastic into the desired shape, creating the product quickly and efficiently. Injection moulders can be used to create a variety of products, such as toys, automotive parts, and packaging.
- The main advantage of injection moulding is that it is speedy. Unlike other plastic part production methods, injection moulding is much faster. It allows for large quantities to be produced quickly and efficiently.
- Injection moulding requires relatively little labor as the machines are automated. It allows for a faster production cycle.
- Injection moulders can produce a wide range of products, from small plastic parts to large and complex items. This versatility makes it ideal for creating a variety of products in large quantities.
- Injection moulding is a cost-effective method of production. The moulds used can be reused multiple times, meaning the cost per unit decreases with each use. Additionally, the machines are inexpensive, making them an excellent investment for businesses.
Conveyor Belts:
Conveyor belts are crucial pieces of equipment used to move materials and products during production. They are often used to transport materials from one point to another and can reduce the amount of manual labor required. They are also used to transport finished products from the production line, helping to keep the process running smoothly.
- Conveyor belts come in various styles and sizes to suit different applications. The most common types are flat belts, roller belts, and chains. Each type has its advantages and disadvantages, so choosing the right one for the job is essential.
- Conveyor belts provide an efficient and cost-effective way to move materials from one station to another. They are also safe, as they reduce the risk of accidents associated with manual handling. Additionally, conveyor belts can reduce labor costs, as fewer workers are needed.
- Conveyor belts require regular maintenance, as they can become worn or damaged over time. Additionally, they can be noisy and can disrupt the workplace.
- Conveyor belts are typically used in the food, beverage, automotive, and pharmaceutical industries. They are used to transport components or materials to and from production stations. They can also be used to transport more oversized items, such as pallets and boxes.
Optimizing the Efficiency of Batch Production Systems
Batch production systems are an efficient way of producing many items relatively quickly. However, to maximize the efficiency of your batch production system, there are several things you can do to optimize the system.
- Analyze the Production Process: It is essential to analyze the production process to optimize the efficiency of a batch production system. It will help to identify areas of inefficiency. It includes studying the production process for bottlenecks, delays, idle time, and other inefficient areas.
- Utilize Automation and Robotics: Automation and robotics can help optimize the efficiency of batch production systems. Automated systems can run more frequently and can be programmed to carry out complex tasks quickly and accurately. It reduces errors and increases the speed of production.
- Implement Just-in-Time Production: Just-in-time production is a manufacturing strategy aiming to reduce inventory levels by producing components and products only when needed. It can reduce waste and optimize the efficiency of the batch production system.
- Utilize Predictive Maintenance: Predictive maintenance is a proactive approach to maintenance that uses data and analytics to anticipate potential problems and take preventive measures. It can reduce downtime and optimize the efficiency of the batch production system.
- Monitor Equipment Performance: Regularly monitoring the performance of equipment used in batch production systems can help identify potential problems and inefficiencies. It helps to minimize delays and reduce production costs while improving output quality.
- Reduce Set-up Times: Minimizing time to set up equipment and materials for batch production can help increase efficiency. This can be done by streamlining processes. It can be done by using standardized components and utilizing automated systems.
- Implement Lean Manufacturing Principles: Lean manufacturing is a production philosophy that aims to reduce waste and improve efficiency. It includes using fewer resources, reducing waste, and streamlining processes. Implementing lean principles can optimize the efficiency of a batch production system.
- Improve scheduling: Optimizing batch production scheduling can reduce downtime and increase efficiency. It can be done by implementing an effective scheduling system. Using automated scheduling tools and real-time data to adjust production times as needed.
- Invest in Training and Development: Training and development programs can improve workforce skills. It can optimize the efficiency of the batch production system. It includes providing employees with access to the necessary training and resources and investing in development and career progression opportunities.
By optimizing the efficiency of your batch production system, you can ensure that your system is running at its maximum efficiency. It can reduce costs, improve quality, and save time, resulting in a more productive and profitable operation.
Leveraging Automation in Batch Production Manufacturing
The advancement of technology has revolutionized modern manufacturing processes. Manufacturers have turned to automation to streamline their operations and reduce costs. Automation can be used for batch production manufacturing to increase efficiency and accuracy. Batch production manufacturing can reduce the need for manual labor.
- Automation has enormously impacted the production process of modern batch production manufacturing. Automation has enabled manufacturers to improve efficiency, increase productivity and reduce costs.
- Automation in batch production manufacturing can help reduce labor costs, increase throughput and enhance product quality. Automation can also reduce lead times and improve safety. It can also help to eliminate manual labor and errors that can result from human error.
- Automation also allows for more accurate data collection and analysis, which can be used to make better decisions. There are various types of automation used in batch production manufacturing. These include robotics, computer numerical control (CNC) machines, 3D printing, and automated material handling systems.
Automation Technologies: Automation technologies such as artificial intelligence (AI), machine vision, and predictive analytics are also being used to improve the efficiency of batch production operations.
AI can be used to optimize production processes, and machine vision can be used to detect defects and quality issues. Predictive analytics can be used to anticipate and prevent problems before they occur.
Advantages and Disadvantages of Batch Production in Manufacturing
Advantages of Batch Production in Manufacturing
Batch production is an efficient and cost-effective manufacturing process. It enables businesses to produce large quantities of products quickly and efficiently. It benefits businesses that make a wide range of products or have a high demand for particular items. The six main benefits of batch production include the following:
1. Cost Savings: Batch production allows manufacturers to reduce costs by producing multiple items simultaneously. It results in fewer materials being used and less labor being required. Additionally, batch production is generally more efficient than traditional production methods. Batch production can lead to further cost savings.
2. Improved Quality Control: Batch production enables manufacturers to control the quality of their products better. Through batch production, manufacturers can ensure that each item is produced with the same materials and processes. This results in a higher-quality product.
3. Increased Efficiency: Batch production is more efficient than traditional production methods. By producing multiple items at once, manufacturers can reduce the time it takes to create each item. This results in faster production times and more efficient use of resources.
4. Greater Flexibility: Batch production allows manufacturers to adapt quickly to changes in demand. Manufacturers can promptly adjust the production process to meet changing customer needs by producing multiple items at once.
5. Reduced Waste: Batch production helps to reduce waste by using fewer materials and energy. Additionally, batch production can reduce waste by producing items that are of a higher quality and have a longer life span.
Finally, batch production helps to improve inventory control. Businesses can better manage their inventory by producing large quantities of a product or range of products in one go. This benefits companies that produce a wide range of products or have a high demand for particular items.
Disadvantages of Batch Production in Manufacturing
Batch production is a manufacturing process that produces goods in batches rather than single items. It is a popular production method, but it has its disadvantages. Here are six of the most common disadvantages of batch production:
- Batch production usually requires more time and resources than single-item production. This results in increased costs. It can be especially true for businesses that need to regularly switch between the production of different goods.
- Batch production can lead to inefficient use of resources. Batch production requires more setup time and more materials than single-item production. It can result in higher costs and lead to production delays.
- Batch production often results in a higher rate of defective products due to the complexity and variability involved. It can lead to higher quality assurance activities costs and customer dissatisfaction.
- Batch production could be more flexible and difficult to adjust to changing customer needs or market conditions.
- Batch production usually takes longer than single-item production. It leads to longer lead times and results in customer dissatisfaction.
- Automation is often difficult with batch production. It results in higher costs and reduced efficiency.
These are some of the significant disadvantages of batch production. While it can be a valuable and cost-effective production method for some businesses, it is essential to be aware of its drawbacks before committing to this type of production.
Batch Production vs Continuous Production vs Assembly Line Production
Continuous Production:
In contrast to batch production, continuous production is a process wherein goods are produced in a continuous and uninterrupted flow. This production process is used to manufacture goods that are identical in terms of size and shape.
Continuous production is ideal for producing goods in large quantities. It allows for greater efficiency and cost savings. This production process is also suitable for goods that require frequent servicing. The production line can be stopped and restarted quickly and easily.
Advantages of Continuous Production:
- Continuous production helps to improve efficiency by eliminating downtime. It also reduces the amount of time spent on setup and changeover. It streamlines the production process. It leads to faster production times and higher-quality products.
- By eliminating the need for lengthy setup and changeover times. Continuous production reduces the cost of production. It means lower production costs and increased profits.
- Continuous production requires fewer workers since it eliminates downtime. It also minimizes the need for setup and changeover. It reduces the reliance on manual labor, which can be expensive. Continuous production helps to guarantee a higher level of quality control.
- Eliminating downtime and ensuring that each step of the production process is monitored. It is easier to produce higher-quality products.
- Continuous production is easily scalable, allowing it to be adapted to meet the needs of different businesses. It makes it an ideal choice for businesses of any size.
- Continuous production helps to improve safety by reducing the need for manual labor. It also eliminates the risks associated with setup and changeover. It helps to ensure that workers stay safe and that the production process is safe for the environment.
Disadvantages of Continuous Production:
- Continuous production requires significant capital investment. The cost of setting up a continuous production system can be pretty expensive.
- Continuous production systems are prone to breakdowns due to the complexity of the machinery. It can lead to unexpected delays and disruptions in production.
- Continuous production systems are designed to produce one specific good. It means that any variation in the product must be programmed into the system, which can be a time-consuming and costly process.
- As the machines are used for continuous production run for long periods, there is a greater risk of contamination. It is because proper safety protocols are not followed.
Assembly Line Production:
Assembly line production is a process wherein goods are assembled on an assembly line. This production process is suitable for producing goods in large quantities. It allows for greater efficiency and cost savings. Assembly line production involves the use of special machines and tools. These are used to assemble the components of a product in a specific order. This production process allows for the efficient assembly of a product as it reduces the amount of time and labor required for assembly.
Advantages of Assembly Line Production:
- Assembly line production offers a more efficient and cost-effective way to produce products. By having the same process repeated over and over with minimal variation. Production times can be shortened significantly. It allows for greater output in a shorter period of time.
- Assembly line production allows workers to specialize in a single task, which can help to reduce labor costs. It is because workers do not need to be trained in multiple processes. They can therefore produce products more quickly and efficiently.
- Assembly line production allows for a high level of quality control. Having the same process repeated over and over allows any product flaws to be easily identified and corrected. It helps to ensure that the end product is of high quality.
- Assembly line production can be automated. It means that the process requires minimal human intervention. It helps to reduce costs and can also help to improve safety as robots can perform tasks that may be too dangerous for humans to complete.
- Assembly line production offers an increased level of productivity. By having the same process repeated over and over, production times can be reduced significantly. It allows more products to be produced in a shorter time.
Disadvantages of Assembly Line Production:
- Setting up an assembly line requires a large upfront investment in specialized equipment, tools, and machines. The cost of setting up an assembly line is high. It can significantly burden a company's finances, and the investment can be wasted if the assembly line is unsuccessful.
- Assembly line production is designed for the mass production of one particular product. It's not easy to change the line, so if a new product needs to be produced, a new line must be created. It is time-consuming and expensive.
- Working on an assembly line can be tedious and monotonous, as workers are tasked with performing the same job over and over again. It can lead to burnout and even injuries due to repetitive motions.
- Because workers perform the same task repeatedly, making mistakes is easy. It can lead to defects in the product, which can lead to costly recalls.
Differences:
- Batch production is used to produce small quantities of products with low complexity. Continuous production is typically used for high-volume items such as cars, aircraft, and consumer electronics.
- Batch production involves producing a specified number of items in a single production run. Continuous production requires a steady and uninterrupted flow of raw materials and components.
- Assembly line production requires specialized production equipment. Batch production requires minimal capital investment.
- Assembly line production has higher production rates than batch production. Continuous production has the highest production rate out of the three.
- Batch production is best suited for small-scale production. Continuous production is better for large-scale production.
All production processes are batch, continuous, and assembly line production. These processes are suitable for different types of production. Each production process has its advantages and disadvantages. It is important to choose the production process which is the most ideal for your particular product.
Batch Production vs. Mass Production vs. Job Shop Manufacturing
Mass Production:
Mass production is a manufacturing process in which a large number of identical products or components are produced. It is done quickly and efficiently. It is a process that increases productivity and efficiency.
- It utilizes specialized machinery, labor, and assembly lines. Mass production has been used for centuries to make clothing, furniture, and electronics. Its significance has grown over time as technology has advanced. Here are some critical points about mass production:
- Mass production is a manufacturing process that increases productivity and efficiency. It consists of utilizing specialized machinery, labor, and assembly lines. It allows for the production of a large number of identical products or components quickly and efficiently.
- Mass production has been used for centuries to make clothing, furniture, and electronics. However, its significance has grown over time as technology has advanced.
- The mass production process involves specialized machinery, labor, and assembly lines. It helps to reduce production costs and increase the process's efficiency.
Advantages of Mass Production:
- Mass production helps to reduce the cost of production by making use of economies of scale. It means that the cost of production is lower per unit when large quantities of the same product are produced.
- Mass production allows for a more efficient production process. All the parts and components used in the production process are the same. It eliminates the need for manual adjustment and labor-intensive processes.
- Mass production helps to ensure that all the products produced are of the same high quality. Since the same production process is used, it is easier to maintain control over the quality of the output.
Disadvantages of Mass Production:
- Mass production often relies on automation and other labor-saving technologies. These can reduce the need for manual labor. It can lead to fewer job opportunities for workers. It can lead to reduced job security and lower wages for those who can find employment.
- Mass production often results in the production of large amounts of waste. This waste can be toxic or otherwise damaging to the environment, leading to pollution and a decrease in air and water quality.
- Mass production is designed to produce large amounts of a product quickly, but it can also lead to a decrease in creativity. Creative processes like designing and engineering are often sacrificed in favor of efficiency. It leads to a reduction in product innovation and creativity.
Job Shop Manufacturing:
Job Shop Manufacturing is a manufacturing process in which orders for custom-made products are produced on demand. It involves producing individual parts or components according to a customer's specifications.
This process usually involves a lot of manual labor and often requires much customization. The process begins with a customer placing an order for a specific product. The product is then designed and engineered to meet the customer's needs. The product is then fabricated using specialized tools, machines, and materials.
Advantages of Job Shop Manufacturing:
- Job shop manufacturing is cost-effective for businesses that produce small batches of products. It is also cost-effective for companies that produce low-volume customized products. It eliminates the need to invest in expensive machines and other equipment. These may be necessary for large-scale production.
- Job shop manufacturing is ideal for producing various products of different styles and sizes. It allows businesses to satisfy the individual needs of their customers.
- Job shop manufacturing allows businesses to customize their products to the customer's exact specifications. It helps to ensure that the customer is satisfied with the finished product.
- Job shop manufacturing enables businesses to produce and deliver customized products quickly. It is done in short lead times. It helps to ensure that companies can meet their customers' delivery requirements.
Disadvantages of Job Shop Manufacturing:
- Job shop manufacturing requires a large number of skilled workers for the production process. It increases labor costs, as the job shop has to pay higher wages and benefits to attract and retain skilled workers.
- Job shop manufacturing is less efficient than mass production. It has a longer lead time and requires more resources to produce a product. It can lead to higher production costs, as more resources and time are needed to create a product.
- The capacity of its machinery limits job shop manufacturing. It means that a job shop cannot produce a large number of products in a short time.
- Job shop manufacturing is not suited for high-volume production. It makes it difficult to schedule production and plan.
Differences:
Batch production is generally more expensive as it requires more labor, materials, and equipment. Mass production is cheaper as it involves fewer labor costs and materials.
Batch production is more flexible as it allows for changes in the production process or the product itself. Mass production is much more rigid, requiring a set production process with no room for change.
Batch production typically yields higher-quality products. Batch production involves careful monitoring and production processes. Mass production may produce lower-quality products as it relies on a more streamlined process with no room for error.
- The setup time for batch production is usually shorter than for job shop production. It is because all batch items are processed the same way, allowing for more efficient setup times. Job shop production is more flexible than batch production. It can easily accommodate changes in customer needs or design changes. Batch production is less flexible as it requires all items in a batch to be processed in the same way.
- Batch production usually requires shorter cycle times than job shop production, as the same process is repeated for all items in a batch. Job shop production usually takes longer as each product is processed differently and requires more setup time.
How can Deskera Help You?
Deskera software is a cloud-based business software. It is designed to help you manage and streamline your business operations. It offers a complete suite of integrated applications for business management.
These include inventory control, order management, accounting, and more. It is an ideal solution for businesses that need to manage batch production. Batch production is the process of creating large quantities of a single item.
Deskera MRP is the one tool that lets you do all of the above. With Deskera, you can:
- Control production schedules
- Compile a Bill of Materials
- Produce thorough reports
- Make your own dashboard.
Deskera ERP is a complete solution that allows you to manage suppliers, track supply chain activity in real time, and streamline a range of other company functions.
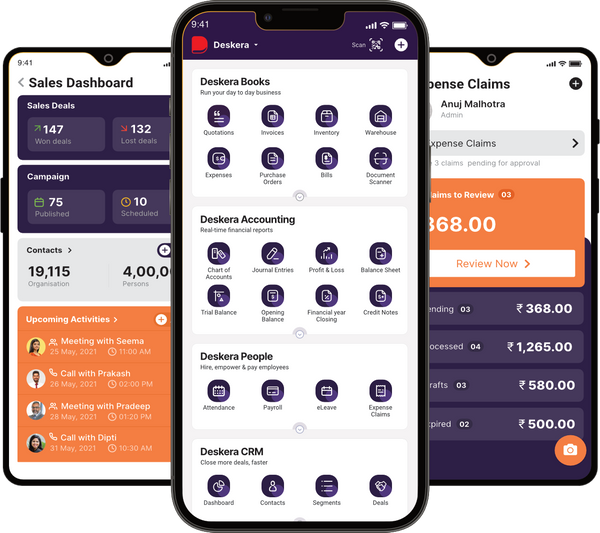
Deskera Books allows you to manage your accounts and finances better. It helps maintain good accounting standards by automating billing, invoicing, and payment processing tasks.
Deskera CRM is a powerful tool that organizes your sales and helps you close deals rapidly. It enables you to perform crucial tasks like lead generation via email and gives you a comprehensive view of your sales funnel.
Deskera People is a straightforward application for centralizing your human resource management activities. Not only does the technology expedite payroll processing, but it also helps you to handle all other operations such as overtime, benefits, bonuses, training programs, and much more.
Conclusion
Batch production has been a critical component of manufacturing for many years. It is a cost-effective production method that can produce large quantities of products in a single run. This production method is versatile and can be adapted to meet the needs of different industries.
It is a production system used by many kinds of businesses in various industries and can be tailored to meet specific needs. It is a process that can be tailored to meet the needs of any type of business in any industry.
It allows large quantities of products to be produced in a single run, which helps keep costs down. The versatility of batch production also allows it to be adapted to meet specific needs. Although batch production has been used for many years, businesses must consider other production methods for their manufacturing needs.
Other production methods may be more suitable or cost-effective depending on the manufactured products. It is also essential for businesses to remain up-to-date with the latest manufacturing technologies and processes. It is to remain competitive.
Hence, Batch production is a reliable and proven manufacturing process that has been used for centuries and is still used today.
Key Takeaways
- Batch production in manufacturing is used to produce a particular product in large quantities. This production method is ideal for items requiring a large amount of labor and materials.
- Batch production is used in a variety of industries. These industries include automotive, electronics, textiles, and food processing. It is also beneficial for companies that must produce a limited number of products. It is to meet customer demands quickly and efficiently.
- Batch production is cost-effective for companies that must produce many products simultaneously. It is because the cost of materials and labor can be spread over a more significant number of items, resulting in lower unit costs.
- The main advantage of batch production is its scalability. Companies can quickly increase or decrease the number of items they produce depending on customer demand. It makes it an ideal production method for companies that need to produce many products.
- Batch production also allows for a high degree of automation. It helps to reduce labor costs, increase efficiency, and improve the quality of the finished products.
- Batch production requires careful planning and coordination to succeed. Companies need to determine the size of the batches they will produce, the materials used, and the processes used to create the final products.
- Companies must ensure they have the necessary materials and labor to produce the batches on time. It requires careful inventory management and scheduling of production activities.
- Batch production can also be used to produce custom products. Companies can create batches of items with different features, colors, or sizes to meet customer demands.
- Companies must ensure that their batch production process is efficient and produces high-quality products. It includes ensuring that all materials are properly inspected and tested. The final products meet customer specifications.
Related Articles
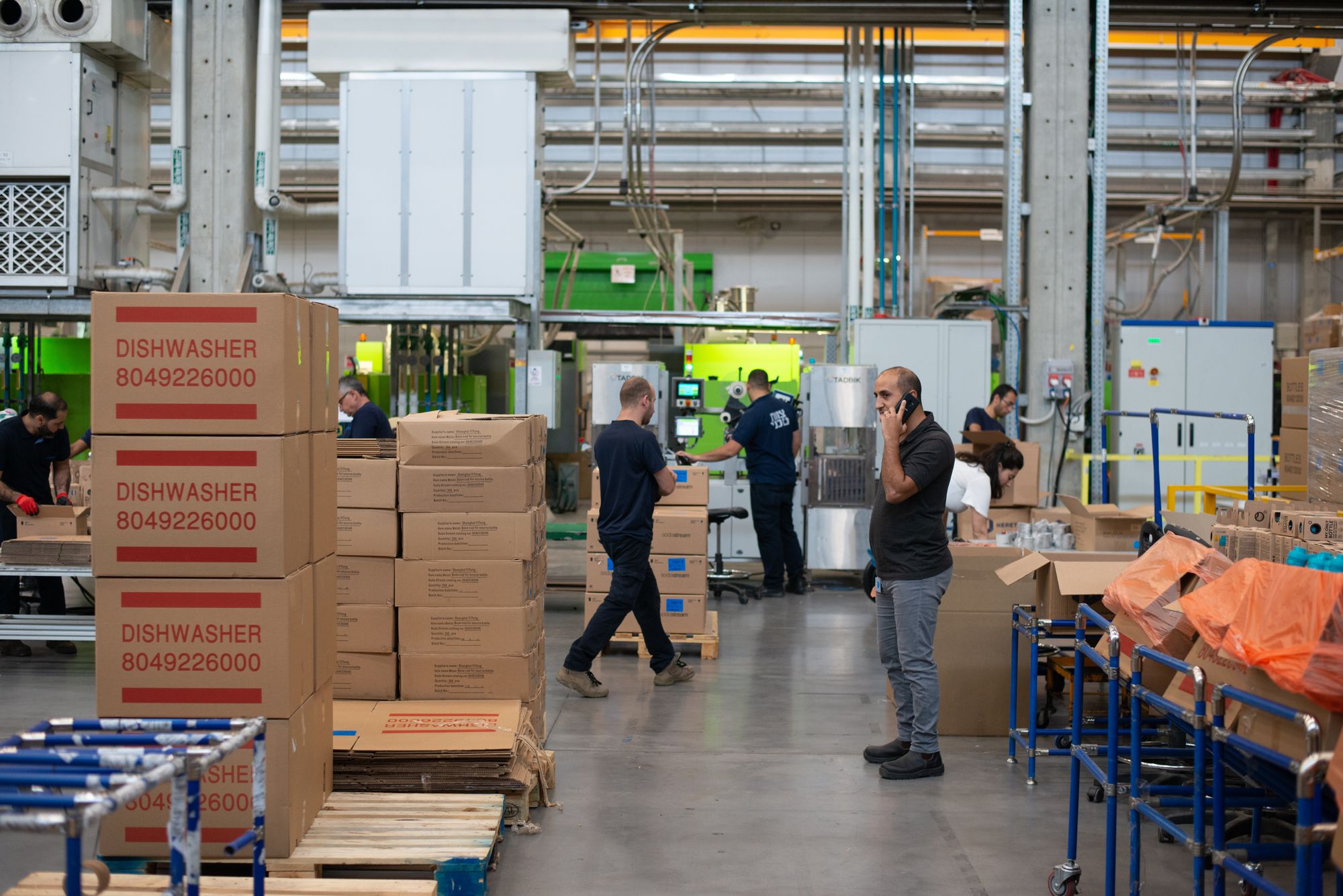
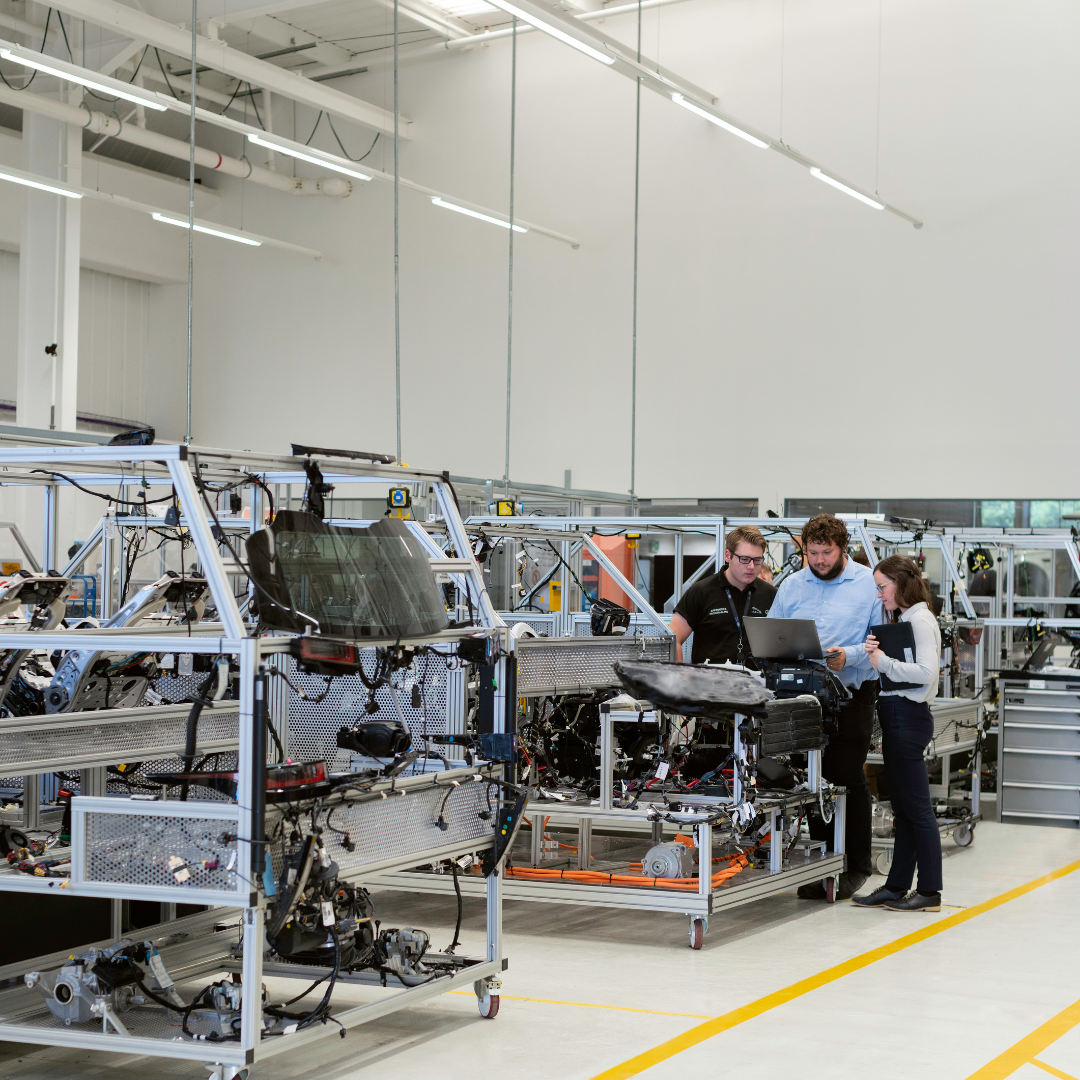
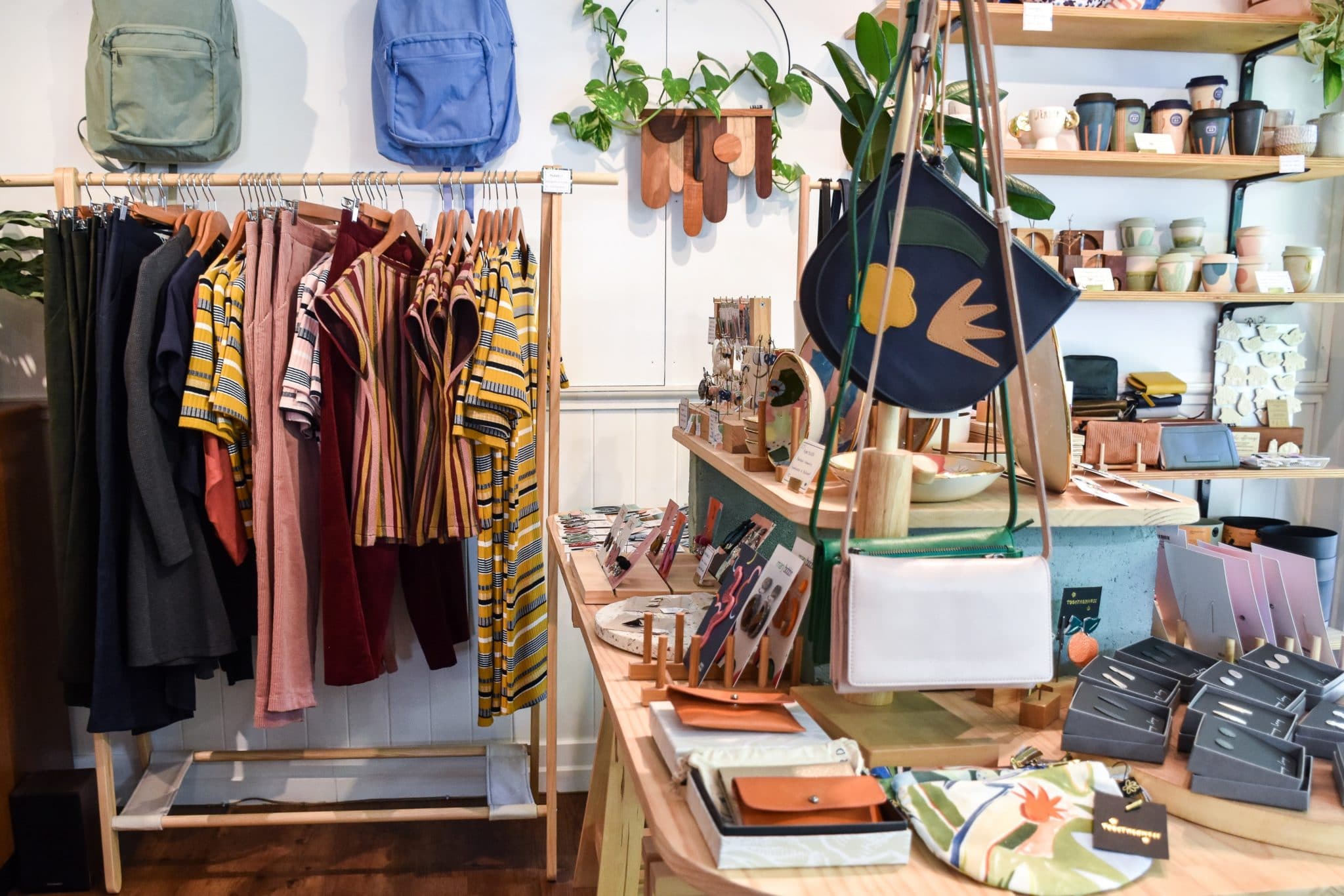
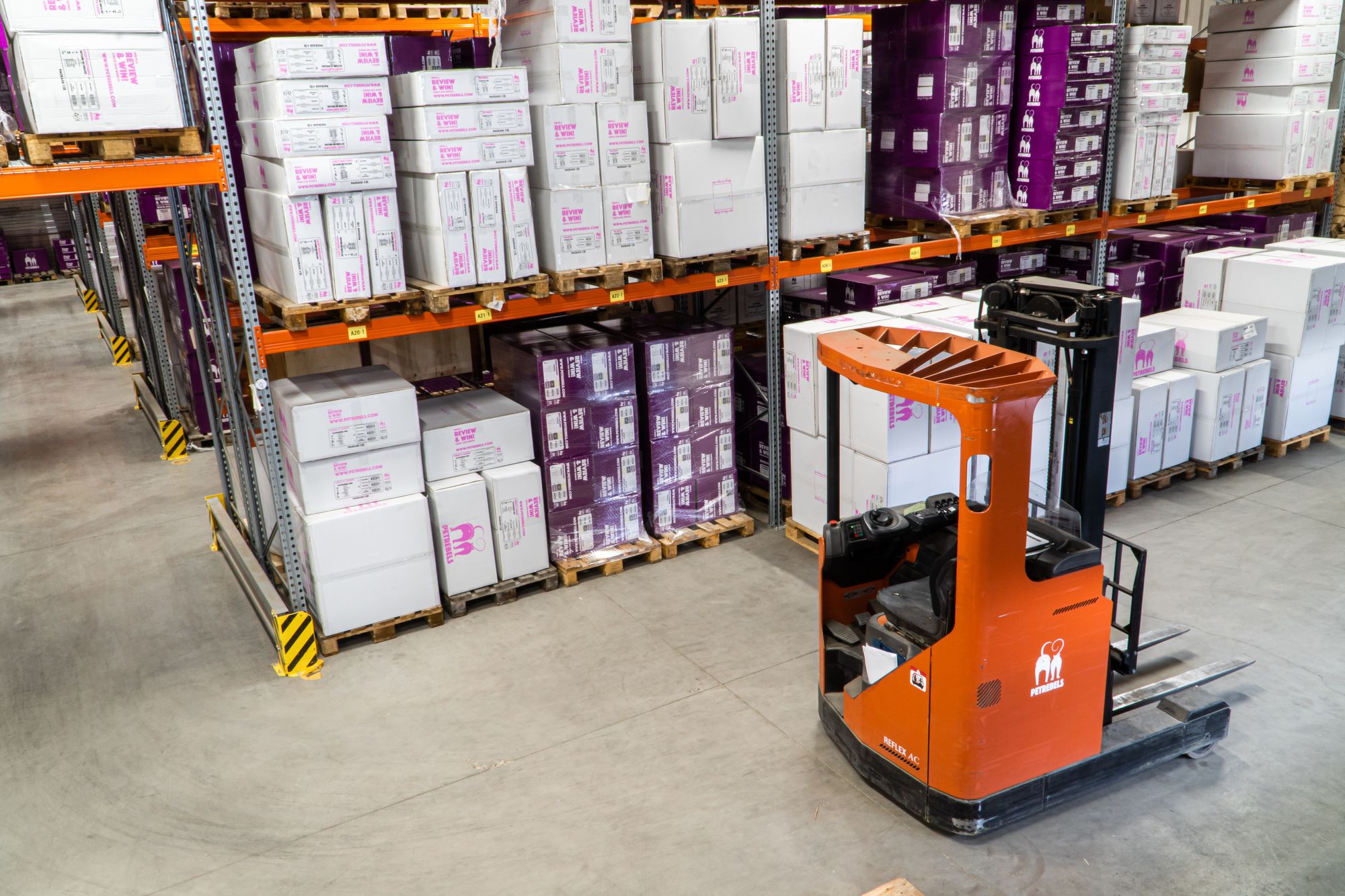