Manufacturing businesses constantly face the challenge of reducing costs while maintaining quality and meeting customer demands. Reducing costs is not only important for increasing profitability but also for remaining competitive in the market.
By implementing lean manufacturing techniques, some companies have reported reducing lead times by up to 90%, reducing inventory by up to 50%, and increasing productivity by up to 30%. (Source: Lean Enterprise Institute)
However, the task of reducing costs in manufacturing is easier said than done. There are many factors involved in the manufacturing process, and changing even a single element can have significant impacts on the overall cost structure.
In this article, we will discuss 15 ways to reduce costs in manufacturing. These strategies range from implementing lean manufacturing techniques and optimizing supply chain management to investing in automation and reducing energy costs.
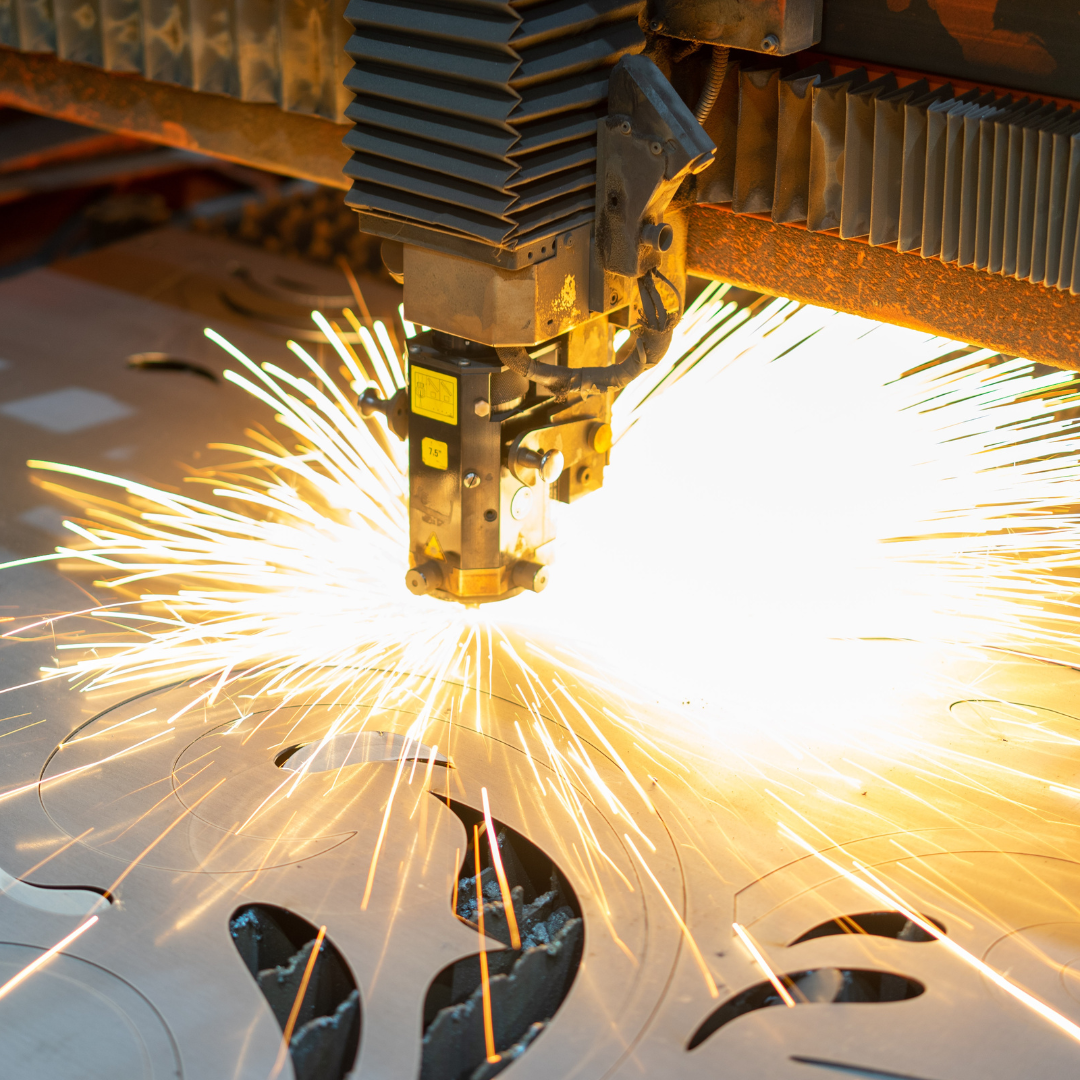
We will also explore ways to improve inventory management, negotiate with suppliers, and implement waste reduction techniques. By implementing these strategies, manufacturing businesses can reduce their costs and remain competitive in the market while also improving their bottom line.
- Importance of Cost Reduction in Manufacturing
- Brief Overview of the 15 Ways to Reduce Costs in Manufacturing
- Implement Lean Manufacturing Techniques
- Optimize Supply Chain Management
- Improve Inventory Management
- Invest in Automation
- Reduce Energy Costs
- Implement Waste Reduction Techniques
- Use Alternative Materials
- Negotiate With Suppliers
- Use Just-in-Time Inventory
- Outsource Non-Core Functions
- Improve Maintenance Procedures
- Train Employees
- Implement Quality Control Measures
- Streamline Production Processes
- Analyze and Adjust Pricing Strategies
- Role of MRP and ERP Systems in Reducing Manufacturing Costs
- How can Deskera Help You?
- Key Takeaways
- Related Articles
Importance of Cost Reduction in Manufacturing
Cost reduction is a critical element of any manufacturing business's success. By reducing costs, manufacturers can improve their profitability, increase their competitiveness in the market, and provide better value to customers. Here are some reasons why cost reduction is essential in manufacturing:
- Increases profitability: Cost reduction directly impacts a manufacturer's bottom line. By reducing costs, manufacturers can increase their profitability, which is essential for long-term success.
- Improves competitiveness: In today's competitive market, manufacturers must be able to offer high-quality products at competitive prices. By reducing costs, manufacturers can lower their prices without sacrificing quality, making them more competitive in the market.
- Enhances customer value: Customers are always looking for the best value for their money. By reducing costs, manufacturers can offer high-quality products at lower prices, providing better value to their customers.
- Enables investment in innovation: By reducing costs, manufacturers can free up funds to invest in research and development, allowing them to stay ahead of the competition and develop new and innovative products.
- Increases operational efficiency: Cost reduction initiatives often involve streamlining operations and improving efficiency, which can lead to a more productive and profitable manufacturing process.
In summary, cost reduction is critical for the success of any manufacturing business. It not only improves profitability but also enhances competitiveness, customer value, and operational efficiency.
Brief Overview of the 15 Ways to Reduce Costs in Manufacturing
Manufacturing is a highly competitive industry, and cost reduction is a top priority for businesses looking to stay ahead. There are numerous ways to reduce costs in manufacturing, and implementing these strategies can have significant impacts on a company's bottom line.
One strategy is to implement lean manufacturing techniques. Lean manufacturing is a systematic approach that focuses on eliminating waste, reducing lead times, and increasing efficiency. By optimizing their manufacturing processes, manufacturers can reduce costs and improve productivity, ultimately leading to increased profitability.
Another key strategy is to optimize supply chain management. This involves improving processes and reducing costs associated with sourcing, procurement, and logistics. By streamlining their supply chain, manufacturers can reduce costs, improve efficiency, and ensure that materials and products are delivered on time.
Investing in automation is another effective way to reduce costs in manufacturing. By automating repetitive and labor-intensive tasks, manufacturers can reduce labor costs, increase production, and improve efficiency. In addition, automation can help reduce errors and improve quality control, leading to cost savings and increased customer satisfaction.
Reducing energy costs is another strategy for reducing costs in manufacturing. This involves implementing energy-efficient practices such as using renewable energy sources and upgrading equipment. By reducing energy consumption, manufacturers can lower their operating costs and reduce their environmental impact.
Improving inventory management is also an effective way to reduce costs in manufacturing. This involves optimizing inventory levels, reducing excess inventory, and improving the accuracy of inventory data. By improving inventory management, manufacturers can reduce costs associated with excess inventory and improve their ability to meet customer demand.
Finally, negotiating with suppliers and implementing waste reduction techniques can also help manufacturers reduce costs. By working with suppliers to negotiate better prices and reducing waste throughout the manufacturing process, manufacturers can improve their profitability and reduce their environmental impact.
In conclusion, reducing costs is a critical element of success for manufacturing businesses. By implementing these 15 strategies, manufacturers can reduce costs, increase efficiency, and ultimately improve their bottom line.
Let’s learn about all these strategies in detail in the upcoming sections.
Implement Lean Manufacturing Techniques
Lean manufacturing is a systematic approach that focuses on eliminating waste, reducing lead times, and increasing efficiency. Implementing lean manufacturing techniques can have significant benefits for manufacturing businesses, including reducing costs, improving quality, and increasing productivity.
One key aspect of lean manufacturing is identifying and eliminating waste in the production process. This includes eliminating unnecessary movement, waiting time, overproduction, defects, overprocessing, and excess inventory. By eliminating waste, manufacturers can improve efficiency and reduce costs.
Another key aspect of lean manufacturing is reducing lead times. This involves streamlining processes and reducing the time it takes to complete each step in the production process. By reducing lead times, manufacturers can improve responsiveness to customer demand, increase productivity, and reduce costs associated with excess inventory and storage.
Implementing lean manufacturing techniques also involves improving quality control. By focusing on continuous improvement and eliminating defects, manufacturers can improve product quality and reduce the costs associated with rework and warranty claims.
Finally, implementing lean manufacturing techniques involves empowering employees to identify and solve problems. By providing training and support for employees, manufacturers can foster a culture of continuous improvement and drive innovation and cost savings.
In conclusion, implementing lean manufacturing techniques can have significant benefits for manufacturing businesses. By eliminating waste, reducing lead times, improving quality, and empowering employees, manufacturers can improve efficiency, reduce costs, and increase profitability.
Explanation of How Lean Manufacturing Reduces Costs
By implementing lean manufacturing techniques, businesses can reduce costs in several ways.
First, lean manufacturing eliminates waste in the production process. This includes eliminating unnecessary movement, waiting time, overproduction, defects, overprocessing, and excess inventory. By eliminating waste, manufacturers can reduce costs associated with excess inventory, storage, and transportation. Additionally, it can reduce costs associated with rework, scrap, and defects.
Second, lean manufacturing reduces lead times. By streamlining processes and reducing the time it takes to complete each step in the production process, manufacturers can improve efficiency and reduce costs associated with excess inventory, storage, and transportation. Additionally, by reducing lead times, manufacturers can improve responsiveness to customer demand and increase productivity.
Third, lean manufacturing improves quality control. By focusing on continuous improvement and eliminating defects, manufacturers can improve product quality and reduce the costs associated with rework and warranty claims. This can also reduce costs associated with customer complaints and lost business.
Finally, lean manufacturing empowers employees to identify and solve problems. By providing training and support for employees, manufacturers can foster a culture of continuous improvement and drive innovation and cost savings. This can lead to new ideas and ways of working that can further reduce costs and increase efficiency.
In conclusion, lean manufacturing is a powerful approach to reducing costs in manufacturing businesses. By eliminating waste, reducing lead times, improving quality, and empowering employees, manufacturers can improve efficiency, reduce costs, and increase profitability.
Examples of Lean Manufacturing Techniques
There are many examples of lean manufacturing techniques that can be implemented in manufacturing businesses. Here are a few examples:
- Value Stream Mapping: This is a technique for analyzing the flow of materials and information through the manufacturing process to identify opportunities for improvement. By mapping the flow of value through the production process, manufacturers can identify areas of waste and inefficiency and develop strategies for improvement.
- 5S: This is a technique for organizing the workplace to increase efficiency and reduce waste. The five S's stand for sort, set in order, shine, standardize, and sustain. By implementing these principles, manufacturers can improve organization, cleanliness, and safety, leading to increased efficiency and reduced costs.
- Just-in-Time (JIT): Just-in-time is a production strategy that involves producing only what is needed, when it is needed. By reducing inventory levels and producing in smaller batches, manufacturers can reduce costs associated with excess inventory, storage, and transportation.
- Kanban: This is a visual system for managing inventory and production. By using visual signals, such as cards or containers, manufacturers can signal when inventory needs to be replenished and when production needs to be adjusted to meet customer demand.
- Poka-Yoke: This is a technique for mistake-proofing the production process. By designing processes and equipment to prevent errors, manufacturers can improve quality and reduce costs associated with rework and defects.
- Kaizen: This is a philosophy of continuous improvement that involves making small, incremental changes to processes over time. By fostering a culture of continuous improvement, manufacturers can drive innovation, reduce waste, and improve efficiency.
These are just a few examples of lean manufacturing techniques that can be implemented in manufacturing businesses. By applying these principles and techniques, manufacturers can improve efficiency, reduce costs, and increase profitability.
Optimize Supply Chain Management
Optimizing supply chain management is critical for businesses to improve efficiency, reduce costs, and enhance customer satisfaction through timely delivery of high-quality products, and this can be achieved through effective inventory management, streamlined logistics, and strategic supplier partnerships
Explanation of Supply Chain Management and How it Affects Costs
Supply chain management refers to the coordination of activities involved in the production and delivery of goods and services from raw materials to the end user. This includes sourcing raw materials, manufacturing, transportation, warehousing, and delivery. Effective supply chain management can lead to reduced costs, increased efficiency, and improved customer satisfaction.
One of the key ways that supply chain management affects costs is through inventory management. Maintaining excessive inventory levels can tie up capital and increase storage and handling costs.
On the other hand, insufficient inventory levels can lead to stockouts, lost sales, and dissatisfied customers. Effective supply chain management can help to balance inventory levels and reduce costs associated with excess inventory and stockouts.
Another way that supply chain management affects costs is through logistics. By optimizing transportation routes, consolidating shipments, and reducing transit times, businesses can reduce transportation costs and improve delivery times. Additionally, effective supply chain management can help to reduce costs associated with warehouse storage and handling.
Finally, supply chain management can affect costs through strategic supplier partnerships. By developing strong relationships with suppliers, businesses can negotiate better pricing and terms, reduce lead times, and improve quality. Additionally, effective supplier management can reduce the risk of supply chain disruptions and the costs associated with production delays and lost sales.
In conclusion, supply chain management plays a critical role in determining the costs of production and delivery for businesses. Effective supply chain management can help to reduce costs through inventory management, logistics optimization, and strategic supplier partnerships.
By optimizing the supply chain, businesses can improve efficiency, reduce costs, and enhance customer satisfaction.
Tips for Optimizing Supply Chain Management
Here are some tips for optimizing supply chain management:
- Develop a robust supplier management program: By developing strong relationships with suppliers, businesses can improve pricing, reduce lead times, and improve quality. Conduct regular supplier evaluations to ensure they meet your business needs and expectations.
- Implement inventory management best practices: Effective inventory management can help to balance inventory levels and reduce costs associated with excess inventory and stockouts. Use demand forecasting tools to ensure that inventory levels match customer demand and avoid overproduction.
- Use technology to streamline logistics: Transportation and logistics are critical components of supply chain management. By leveraging technology such as GPS tracking and route optimization software, businesses can reduce transportation costs, improve delivery times, and enhance visibility into the supply chain.
- Continuously monitor and evaluate supply chain performance: Regularly measure and monitor performance metrics such as on-time delivery, order accuracy, and lead times. Use this data to identify areas for improvement and develop strategies to enhance supply chain performance.
- Develop contingency plans for supply chain disruptions: Despite best efforts, supply chain disruptions can occur. Develop contingency plans and risk management strategies to mitigate the impact of disruptions such as natural disasters or supplier bankruptcies.
- Foster collaboration across the supply chain: Collaboration across the supply chain can improve communication, reduce lead times, and increase efficiency. Encourage open communication and collaboration among suppliers, distributors, and customers to improve supply chain performance.
By implementing these tips, businesses can optimize supply chain management and improve efficiency, reduce costs, and enhance customer satisfaction.
Improve Inventory Management
Effective inventory management is crucial for businesses to reduce costs, improve operational efficiency, and enhance customer satisfaction, and this can be achieved through proper demand forecasting, accurate inventory tracking, and optimal inventory levels.
Explanation of Inventory Management and its Impact on Costs
Inventory management refers to the process of overseeing the flow of goods from the manufacturer to the end user, including the storage, tracking, and management of inventory levels. Effective inventory management is essential for businesses to balance supply and demand, reduce costs, and improve customer satisfaction.
Poor inventory management can result in excess inventory, stockouts, and other inefficiencies that can increase costs. Excess inventory ties up capital, increases storage and handling costs, and may lead to spoilage or obsolescence. Stockouts, on the other hand, can result in lost sales, dissatisfied customers, and increased shipping and handling costs to replenish inventory.
Effective inventory management can help to reduce costs by optimizing inventory levels to match customer demand. By accurately forecasting demand, businesses can reduce excess inventory and ensure that they have the right inventory levels to meet customer needs. This can help to reduce storage and handling costs, minimize spoilage and obsolescence, and avoid stockouts.
Additionally, effective inventory management can help to reduce costs associated with shipping and handling. By accurately tracking inventory levels, businesses can reduce the need for emergency shipments and expedited shipping, which can be costly.
In conclusion, effective inventory management is critical for businesses to reduce costs, improve operational efficiency, and enhance customer satisfaction. By properly forecasting demand, accurately tracking inventory levels, and maintaining optimal inventory levels, businesses can reduce costs associated with excess inventory, stockouts, and shipping and handling.
Tips for Improving Inventory Management
Here are some tips for improving inventory management:
- Conduct regular demand forecasting: Accurate demand forecasting is critical for effective inventory management. Businesses should regularly analyze historical sales data, market trends, and other factors that may impact demand to forecast future demand and adjust inventory levels accordingly.
- Implement an inventory tracking system: Accurate inventory tracking is essential for effective inventory management. Implement a system to track inventory levels, including stock quantities, location, and movement. This can help businesses identify slow-moving inventory, reduce stockouts, and improve order fulfillment.
- Use inventory optimization software: Inventory optimization software can help businesses to identify optimal inventory levels, reorder points, and safety stock levels. This can help to balance inventory levels with customer demand and minimize the risk of excess inventory or stockouts.
- Establish inventory control policies: Establishing inventory control policies can help to ensure that inventory levels remain at optimal levels. This may include policies for ordering, receiving, and storing inventory, as well as policies for disposing of slow-moving or obsolete inventory.
- Conduct regular inventory audits: Conduct regular inventory audits to ensure that inventory levels are accurate and up to date. This can help to identify discrepancies, reduce inventory shrinkage, and improve inventory management.
- Use just-in-time (JIT) inventory management: JIT inventory management is a strategy that involves ordering inventory just in time to meet customer demand. This can help to reduce inventory levels, minimize the risk of excess inventory, and reduce storage and handling costs.
By implementing these tips, businesses can improve inventory management, reduce costs associated with excess inventory, stockouts, and shipping, and enhance customer satisfaction.
Invest in Automation
Investing in automation can help manufacturing businesses improve efficiency, reduce labor costs, and increase production capacity, ultimately resulting in a competitive advantage in the marketplace.
Explanation of Automation and How it Reduces Costs
Automation refers to the use of technology and machinery to perform tasks that were previously done by humans. Automation can help manufacturing businesses to reduce costs by improving efficiency, reducing labor costs, and increasing production capacity.
One of the primary ways that automation reduces costs is by improving efficiency. Automated machinery can perform tasks more quickly and accurately than humans, leading to faster production times and higher output levels. This can help businesses to meet customer demand more efficiently and reduce the time and resources required to complete a job.
Automation can also help businesses to reduce labor costs. By replacing human workers with automated machinery, businesses can reduce the costs associated with salaries, benefits, and training. Additionally, automated machinery can operate continuously, reducing the need for shift work and overtime pay.
Finally, automation can increase production capacity, allowing businesses to produce more products in less time. This can help businesses to meet customer demand more efficiently and quickly, improving customer satisfaction and reducing the risk of lost sales due to stockouts.
While investing in automation can require a significant upfront investment, the long-term cost savings can be substantial. By reducing labor costs, improving efficiency, and increasing production capacity, businesses can achieve a competitive advantage in the marketplace and improve profitability.
Examples of Automation in Manufacturing
Here are some examples of automation in manufacturing:
- Robotic assembly lines: Robotic assembly lines are used to automate the assembly process, reducing labor costs and improving efficiency. Robots can perform repetitive tasks with speed and accuracy, allowing for faster production times and higher output levels.
- Automated material handling systems: Automated material handling systems use conveyor belts, automated guided vehicles (AGVs), and other machinery to move materials and products throughout the production process. This can help to reduce the time and labor required for manual material handling.
- CNC machines: Computer numerical control (CNC) machines use computer software to control the operation of machinery, such as lathes and mills. CNC machines can perform complex tasks with speed and precision, reducing the need for manual labor and improving accuracy.
- 3D printing: 3D printing uses digital design files to create three-dimensional objects by layering materials. This technology can be used to automate the production of small parts and prototypes, reducing the time and labor required for manual production.
- Automated inspection systems: Automated inspection systems use machine vision and other technologies to inspect products for defects and quality control. This can help to reduce the risk of human error and improve product quality.
- Automated packaging systems: Automated packaging systems use machinery to package products quickly and efficiently, reducing the time and labor required for manual packaging.
Overall, automation can be applied to various stages of the manufacturing process to improve efficiency, reduce labor costs, and increase production capacity.
Reduce Energy Costs
By implementing energy-saving measures, manufacturing businesses can reduce energy costs, improve sustainability, and enhance their bottom line.
Explanation of Energy Costs in Manufacturing and Their Impact on Costs
Energy costs can be a significant expense for manufacturing businesses, as they require large amounts of energy to power machinery and equipment. In fact, energy costs can account for up to 30% of a manufacturer's operating expenses, depending on the industry and the size of the business.
The impact of energy costs on a manufacturing business can be substantial. High energy costs can reduce profit margins and make it difficult for businesses to compete in the marketplace. Additionally, volatile energy prices can create uncertainty and make it difficult to forecast expenses, leading to financial risk for businesses.
Reducing energy costs can have a positive impact on a manufacturing business's bottom line. By implementing energy-saving measures, businesses can reduce their energy consumption, lower their energy bills, and improve their profitability. Additionally, reducing energy consumption can help businesses to improve their sustainability and reduce their carbon footprint, which can be a selling point for customers and stakeholders who prioritize environmental responsibility.
There are many ways that manufacturing businesses can reduce their energy costs, including the following:
- Upgrading to more energy-efficient equipment
- Implementing energy-efficient lighting systems
- Installing building insulation to reduce heating and cooling costs
- Implementing a regular maintenance program to keep equipment running efficiently
- Optimizing production processes to reduce energy waste
- Implementing renewable energy sources, such as solar panels or wind turbines.
By reducing energy costs, manufacturing businesses can improve their profitability, enhance their sustainability, and gain a competitive advantage in the marketplace.
Tips for Reducing Energy Costs
Here are some tips for reducing energy costs in manufacturing:
- Conduct an energy audit: Before implementing any energy-saving measures, it's important to understand where your energy is being used and identify areas where you can make improvements. An energy audit can help you to pinpoint opportunities for reducing energy consumption and prioritize your efforts.
- Upgrade to energy-efficient equipment: Upgrading to energy-efficient machinery and equipment can significantly reduce energy consumption and lower energy costs over time. Look for equipment that is ENERGY STAR certified or meets other energy efficiency standards.
- Optimize production processes: Optimizing production processes can help to reduce energy waste and improve efficiency. Consider implementing lean manufacturing techniques to reduce waste and eliminate inefficiencies in your production processes.
- Implement an energy management system: An energy management system can help you to track your energy usage, identify opportunities for improvement, and monitor the results of your energy-saving efforts.
- Implement energy-efficient lighting: Replacing traditional lighting with energy-efficient LED lighting can reduce energy consumption and lower energy costs.
- Use renewable energy sources: Consider installing solar panels or wind turbines to generate your own renewable energy. While there may be upfront costs associated with this, the long-term savings can be significant.
By implementing these energy-saving measures, manufacturing businesses can reduce their energy costs, improve their sustainability, and gain a competitive advantage in the marketplace.
Implement Waste Reduction Techniques
By implementing waste reduction techniques, manufacturing businesses can reduce costs, improve efficiency, and promote sustainability by minimizing waste and utilizing resources more effectively.
Explanation of Waste Reduction and How it Reduces Costs
Waste reduction in manufacturing refers to minimizing the amount of waste generated in the production process and maximizing the use of resources. This can include reducing scrap material, optimizing inventory levels, and minimizing energy consumption.
Waste reduction is essential for improving a manufacturing business's bottom line by reducing costs associated with wasted materials, labor, and energy consumption.
Implementing waste reduction techniques can have a significant impact on a manufacturing business's profitability. By reducing waste, businesses can save money on materials and disposal costs, reduce labor costs associated with managing waste, and minimize energy consumption, leading to lower utility bills.
Additionally, reducing waste can improve efficiency by streamlining production processes and minimizing downtime associated with waste management.
Waste reduction also has environmental benefits. By minimizing waste, businesses can reduce their environmental impact, conserve natural resources, and enhance their sustainability. This can be a selling point for customers and stakeholders who prioritize environmental responsibility.
Overall, waste reduction is a critical component of a manufacturing business's sustainability strategy. By minimizing waste and utilizing resources more effectively, businesses can reduce costs, improve efficiency, and promote sustainability.
Examples of Waste Reduction Techniques
Here are some examples of waste reduction techniques that can be implemented in manufacturing:
- Lean manufacturing: Implementing lean manufacturing techniques can help to reduce waste by eliminating inefficiencies in the production process. This can include reducing excess inventory, improving quality control, and streamlining production processes.
- Recycling and reusing materials: Recycling and reusing materials can help to minimize waste and reduce the need for new materials. This can include implementing a recycling program, reusing scrap material, and using recycled or refurbished equipment.
- Energy efficiency measures: Implementing energy efficiency measures, such as upgrading equipment or optimizing production processes, can help to minimize energy waste and reduce energy costs.
- Composting: Composting organic waste can help to minimize waste and promote sustainability. This can include composting food waste or using compostable materials for packaging.
- Water conservation: Implementing water conservation measures, such as installing low-flow fixtures or optimizing water use in production processes, can help to minimize water waste and reduce water bills.
- Training and education: Providing training and education to employees can help to promote waste reduction practices and encourage a culture of sustainability.
By implementing these waste reduction techniques, manufacturing businesses can minimize waste, reduce costs, and promote sustainability.
Use Alternative Materials
Using alternative materials in manufacturing can help reduce costs, improve product quality, and promote sustainability by sourcing materials that are cheaper, more efficient, and environmentally friendly.
Explanation of How Using Alternative Materials can Reduce Costs
Using alternative materials in manufacturing can help reduce costs in several ways. First, alternative materials may be less expensive than traditional materials, leading to cost savings on raw materials. Additionally, alternative materials may be more efficient to work with, requiring less processing time and labor costs.
Using alternative materials can also lead to improved product quality, resulting in fewer product defects and waste, and ultimately lower costs associated with rework or replacement.
Finally, using environmentally friendly materials can help companies meet sustainability goals and potentially qualify for government incentives or certifications, leading to cost savings and increased brand reputation.
Examples of Alternative Materials in Manufacturing
Here are some examples of alternative materials that can be used in manufacturing:
- Bio-based materials: These are materials made from renewable sources, such as corn, sugarcane, or wood chips. Bio-based materials can be used as a substitute for traditional materials, such as plastics or metals, and can offer similar or improved performance.
- Recycled materials: These are materials made from waste products, such as recycled plastics or recycled metals. Using recycled materials can reduce waste and the need for virgin materials, while also providing cost savings.
- Nanomaterials: These are materials with unique properties at the nanoscale, which can be used to improve the performance of products. For example, adding nanomaterials to a polymer can improve its strength, durability, or resistance to wear.
- Natural fibers: These are materials made from natural sources, such as cotton, wool, or bamboo. Natural fibers can be used as a substitute for synthetic materials, offering similar performance at a potentially lower cost.
- Composite materials: These are materials made by combining two or more different materials, such as carbon fiber and resin. Composite materials can offer improved performance and lower weight compared to traditional materials, leading to cost savings in transportation or energy consumption.
By using alternative materials in manufacturing, businesses can reduce costs, improve product quality, and promote sustainability, while also potentially differentiating themselves in the market.
Negotiate With Suppliers
Negotiating with suppliers can lead to cost savings in manufacturing by securing better pricing, terms, and quality on raw materials and components, and building long-term partnerships that benefit both parties.
Explanation of Supplier Negotiations and their Impact on Costs
By negotiating with suppliers, companies can secure better pricing, terms, and quality on raw materials and components, which can result in significant cost savings.
Negotiating with suppliers can also help build long-term partnerships, which can lead to better communication, faster delivery times, and improved product quality. Additionally, suppliers may be more willing to work with companies that have established relationships, offering discounts or other incentives that can further reduce costs.
Effective supplier negotiations can help companies improve their bottom line, build stronger supply chains, and ultimately deliver better value to customers.
Tips for Negotiating With Suppliers
Here are some tips for negotiating with suppliers:
- Do your research: Before entering into negotiations with a supplier, it's important to research the market and understand the pricing and quality standards for the materials or components you need. This will give you a better understanding of what you should be paying and what quality you should expect.
- Build relationships: Building a strong relationship with your supplier is key to effective negotiations. Regular communication and showing an interest in their business can help build trust and a mutual understanding of each other's needs.
- Be clear about your requirements: Clearly communicating your requirements, such as quality standards, delivery times, and payment terms, can help suppliers understand what they need to deliver and avoid misunderstandings that can lead to additional costs.
- Consider long-term partnerships: Long-term partnerships with suppliers can offer benefits such as discounts, better payment terms, and priority delivery, which can result in cost savings.
- Be willing to compromise: Effective negotiations involve compromise, and it's important to be willing to give and take to reach a mutually beneficial agreement. Look for creative solutions that benefit both parties and can result in long-term cost savings.
Use Just-in-Time Production
Just-in-Time (JIT) production is a manufacturing philosophy that emphasizes producing goods only when they are needed, and it reduces costs by minimizing inventory, reducing lead times, and improving quality.
Explanation of Just-in-Time Production and How it Reduces Costs
Just-in-Time (JIT) production can help reduce costs for manufacturers. JIT is a manufacturing philosophy that focuses on producing products only when they are needed, in the quantities required, and at the highest level of quality. JIT helps to eliminate waste, reduce inventory costs, and minimize lead times.
By producing goods on a just-in-time basis, manufacturers can reduce the amount of inventory they need to hold, which can free up space, reduce the cost of storage, and minimize the risk of stock obsolescence. In addition, by producing only what is needed, manufacturers can avoid overproduction, which can result in excess inventory, wasted resources, and increased costs.
JIT production can also help improve quality by allowing manufacturers to focus on producing high-quality products in smaller quantities, rather than focusing on mass production at the expense of quality. This can result in fewer defects, reduced rework, and lower costs associated with scrap and warranty claims.
Overall, JIT production can help manufacturers streamline their operations, reduce waste, and lower costs, making it a valuable tool for cost reduction in manufacturing.
Examples of Just-in-Time Production in Manufacturing
There are many examples of just-in-time (JIT) production being used in manufacturing today. Here are a few:
- Toyota: Toyota is perhaps the most well-known example of a company that uses JIT production. The company pioneered the approach in the 1950s and has since become known for its lean manufacturing processes.
- Dell: Dell uses a just-in-time approach to produce custom-built computers. The company does not maintain a large inventory of parts or finished goods; instead, it waits for customer orders and then produces the computers to meet those orders.
- Harley-Davidson: Harley-Davidson has implemented JIT production in its motorcycle manufacturing process. The company uses a "pull" system to produce bikes only when customer demand requires it, which has allowed it to reduce inventory levels and improve efficiency.
- Intel: Intel uses JIT production in its semiconductor manufacturing process. The company uses a "just-in-time" approach to order materials and components, which helps it to minimize inventory levels and reduce costs.
- Boeing: Boeing has implemented JIT production in its aircraft manufacturing process. The company uses a "flow" approach to production, which allows it to produce aircraft components in a continuous flow, reducing the need for inventory and improving efficiency.
Overall, JIT production is used in many industries and can be a valuable tool for reducing costs, improving efficiency, and improving quality.
Outsource Non-Core Functions
By delegating tasks to third-party providers, manufacturers can focus on their core competencies while reducing expenses associated with non-essential activities such as IT support, customer service, or payroll.
Outsourcing can also provide access to specialized expertise and technology that may not be available in-house, leading to improved efficiency and overall cost savings. However, careful consideration should be given to outsourcing decisions to ensure that quality, security, and other critical factors are not compromised.
Explanation of Outsourcing Non-Core Functions and its Impact on Costs
Outsourcing non-core functions refers to the practice of hiring external service providers to handle tasks that are not central to a manufacturer's core operations. These functions can include anything from administrative tasks to production and assembly processes.
Outsourcing can have a significant impact on costs, as it allows manufacturers to focus their resources on core activities while reducing the expenses associated with non-essential functions.
One of the primary benefits of outsourcing is cost savings. By outsourcing non-core functions, manufacturers can avoid the expenses associated with hiring and training in-house staff. Additionally, outsourcing can provide access to specialized expertise and technology, leading to increased efficiency and cost savings in the long term. Outsourcing can also help manufacturers to scale up or down quickly as business needs change, without the need for significant investment in new resources.
However, outsourcing also has potential downsides. Manufacturers must carefully evaluate potential outsourcing partners to ensure that quality, security, and other critical factors are not compromised.
Additionally, outsourcing can result in a loss of control over the outsourced functions, which may impact the manufacturer's ability to respond quickly to changing business needs. Despite these challenges, outsourcing non-core functions remains a popular strategy for manufacturers looking to reduce costs and improve efficiency.
Examples of Non-Core Functions that can Be Outsourced
Manufacturers can outsource a variety of non-core functions to external service providers. Some common examples include:
- Accounting and bookkeeping: Outsourcing accounting and bookkeeping functions can be cost-effective and can free up internal resources for more strategic activities.
- Human resources: External service providers can handle recruiting, payroll, benefits administration, and other HR-related tasks.
- Information technology: Outsourcing IT functions can provide access to specialized expertise and technology without the need for significant investment in infrastructure and personnel.
- Customer service: Manufacturers can outsource customer service functions, including call center support, email correspondence, and social media management, to improve responsiveness and enhance the customer experience.
- Logistics and transportation: Outsourcing logistics and transportation functions can provide access to expertise in supply chain management, reduce shipping costs, and improve delivery times.
- Marketing and advertising: Manufacturers can outsource marketing and advertising functions to external agencies to improve brand awareness and increase sales.
- Assembly and production: Some manufacturers outsource production and assembly processes to third-party providers to reduce costs and improve efficiency.
Overall, manufacturers can outsource any non-core functions that are not central to their operations, allowing them to focus on core activities and achieve cost savings.
Improve Maintenance Procedures
Improving maintenance procedures is crucial for manufacturers looking to reduce costs and maximize efficiency. By minimizing equipment downtime and extending machinery lifespan, manufacturers can lower their overall expenses and increase productivity.
Proper maintenance also ensures that equipment operates at optimal levels, reducing the likelihood of breakdowns and the need for costly repairs. By prioritizing maintenance procedures, manufacturers can create a more efficient and cost-effective operation.
Explanation of the Importance of Maintenance Procedures in Reducing Costs
Maintenance procedures are crucial for manufacturers as they help to reduce costs in several ways. Firstly, proper maintenance helps to prevent unexpected equipment downtime, which can lead to loss of production, missed deadlines, and increased costs.
This can be achieved by regularly inspecting and servicing equipment, as well as conducting preventative maintenance to detect potential problems early.
Secondly, well-maintained equipment is less likely to break down, reducing the need for costly repairs and replacement parts. This is particularly important for critical equipment and machinery, which can be expensive to replace. By extending the lifespan of equipment, manufacturers can also reduce capital expenditures and lower their total cost of ownership.
Lastly, proper maintenance procedures can improve the overall efficiency of equipment, reducing energy consumption and other operating costs. For example, regular cleaning of machinery can improve its performance and reduce the amount of energy required to run it.
Additionally, ensuring that equipment is well-lubricated can also reduce energy consumption by reducing friction between moving parts.
Tips for Improving Maintenance Procedures
Improving maintenance procedures is essential for reducing costs in manufacturing. Here are some tips that can help:
- Develop a maintenance schedule: A maintenance schedule helps to ensure that machines are regularly serviced, reducing the likelihood of breakdowns and expensive repairs.
- Train maintenance personnel: Properly trained maintenance personnel can identify potential problems and perform maintenance tasks more efficiently, reducing costs associated with extended downtime.
- Use predictive maintenance techniques: Predictive maintenance involves using data to anticipate when equipment is likely to fail, allowing maintenance to be scheduled before the failure occurs, reducing the risk of unplanned downtime.
- Use high-quality parts: Using high-quality replacement parts can reduce the frequency of equipment breakdowns and the need for frequent repairs, ultimately saving money in the long run.
- Implement a computerized maintenance management system (CMMS): A CMMS can help to streamline maintenance procedures, ensuring that maintenance tasks are performed on time, reducing the risk of breakdowns, and optimizing maintenance costs.
Train Employees
Properly trained employees are better equipped to identify and resolve issues, reducing the risk of errors, injuries, and accidents. Training programs can also improve employee retention, reducing the costs associated with turnover and rehiring.
Additionally, well-trained employees can optimize production processes, reduce waste, and contribute to overall cost savings. Thus, investing in employee training can yield significant returns for manufacturers in the long run.
Explanation of How Training Employees can Reduce Costs
Investing in employee training can have a significant impact on reducing costs in manufacturing. Properly trained employees are more efficient and productive, leading to increased output and reduced labor costs.
Well-trained employees also have a better understanding of the manufacturing process and can identify areas for improvement, such as reducing waste or streamlining workflows.
Training can also lead to improved product quality, reducing the risk of defects and the need for rework or recalls, which can be costly. Overall, training employees can improve manufacturing processes, reduce errors, and increase efficiency, all of which can contribute to significant cost savings for a company.
Examples of Employee Training Programs in Manufacturing
Some examples of employee training programs in manufacturing include:
- Safety training: This type of training is important to ensure that employees are aware of the potential hazards in the workplace and how to avoid them. Safety training can include topics such as proper use of equipment, handling of hazardous materials, and emergency procedures.
- Quality control training: Quality control training can help employees understand the importance of maintaining high standards in the production process. This training can cover topics such as inspection procedures, measuring and testing techniques, and defect analysis.
- Lean manufacturing training: Lean manufacturing techniques are designed to eliminate waste and streamline production processes. Training in lean manufacturing can include topics such as value stream mapping, 5S methodology, and continuous improvement techniques.
- Technical skills training: Technical skills training can include topics such as machine operation, equipment maintenance, and programming. This type of training is important to ensure that employees have the skills and knowledge necessary to perform their job duties effectively.
- Leadership and management training: This type of training is important for employees who are in supervisory or management roles. Leadership and management training can cover topics such as communication skills, team building, and performance management.
Implement Quality Control Measures
Ensuring that products meet quality standards helps to reduce waste, rework, and the cost of customer returns or complaints. Furthermore, incorporating quality control into the manufacturing process can lead to fewer errors, higher productivity, and lower costs associated with inspections.
By investing in quality control measures, manufacturers can achieve greater operational efficiency, reduce costs, and ultimately, increase profitability.
Explanation of Quality Control Measures and their Impact on Costs
Quality control measures refer to the procedures and techniques used to ensure that products meet or exceed the required quality standards. Implementing quality control measures can have a significant impact on manufacturing costs, as it reduces the number of defects, reworks, and returns, which can be expensive.
By ensuring that the products are made to the desired specifications and standards, manufacturers can reduce the costs associated with scrapping or reworking products, increase customer satisfaction, and build a positive reputation.
Tips for Implementing Quality Control Measures
Implementing quality control measures is crucial for any manufacturing business looking to reduce costs. This process ensures that products meet customer expectations, which reduces the chances of product defects, returns, and the associated costs.
Tips for implementing quality control measures include setting clear quality standards, investing in quality control equipment, training employees on quality control, implementing statistical process control, and continuously monitoring the quality of products. Implementing quality control measures can also lead to improved customer satisfaction, increased sales, and enhanced brand reputation.
Streamline Production Processes
Streamlining production processes can significantly reduce manufacturing costs by eliminating inefficiencies and optimizing workflow. This can be achieved through various methods such as automation, lean manufacturing, and continuous improvement initiatives.
Explanation of The Importance of Streamlining Production Processes in Reducing Costs
Streamlining production processes is crucial for manufacturers to reduce costs and improve efficiency. By eliminating unnecessary steps, reducing downtime, and minimizing errors, manufacturers can produce more goods in less time, with fewer resources.
This leads to a reduction in waste and costs, while increasing overall productivity and profitability. Implementing lean manufacturing principles and investing in automation technology can help streamline production processes and optimize resource utilization.
Furthermore, continuous process improvement through data analysis and employee involvement can lead to even greater efficiency gains.
Tips for Streamlining Production Processes
Here are some tips for streamlining production processes:
- Analyze your current processes: Conduct a thorough analysis of your current production processes to identify areas of waste and inefficiency.
- Eliminate non-value-added activities: Eliminate activities that do not add value to the production process, such as unnecessary inspections or redundant paperwork.
- Standardized work procedures: Develop and standardize work procedures to ensure that everyone is performing tasks in the same way and to the same quality standard.
- Optimize production flow: Optimize production flow by arranging equipment and workstations in a logical sequence that minimizes unnecessary movement of materials or people.
- Use visual management tools: Implement visual management tools such as Kanban cards, Andon lights, and production boards to help monitor production processes and identify issues quickly.
- Invest in automation: Consider investing in automation technologies such as robotics, automated guided vehicles, and conveyor systems to improve production efficiency and reduce labor costs.
- Continuously improve: Continuously monitor and improve production processes through the use of tools such as root cause analysis, value stream mapping, and Kaizen events.
Analyze and Adjust Pricing Strategies
By carefully evaluating market trends, competition, and production costs, companies can optimize their pricing structures to achieve maximum profitability. Additionally, adopting dynamic pricing strategies, such as price skimming or penetration pricing, can provide manufacturers with greater flexibility and agility in response to changing market conditions.
However, companies must balance the desire for increased profits with the need to maintain customer loyalty and brand reputation through fair and transparent pricing practices.
Pricing Strategies Impact on Costs
Pricing strategies can have a significant impact on costs in several ways. Setting prices too high can lead to decreased demand and lost sales, while setting prices too low can result in lower profit margins.
By analyzing and adjusting pricing strategies, businesses can optimize their prices to increase profitability and reduce costs associated with overproduction, excess inventory, and lost sales due to price sensitivity. Pricing strategies can also impact the supply chain and logistics costs, as changes in pricing can affect transportation, warehousing, and distribution costs.
Tips for Analyzing and Adjusting Pricing Strategies
Here are some tips for analyzing and adjusting pricing strategies:
- Conduct Market Research: Research on your target market to understand their purchasing habits, preferences, and behaviors. This will give you insight into what they are willing to pay for your products and services.
- Review Your Costs: Analyze your costs, including direct and indirect costs, to ensure that you are setting prices that cover your expenses while maintaining a profit margin.
- Monitor Competitor Prices: Keep an eye on your competitors' pricing strategies to ensure that your prices are competitive and attractive to customers.
- Test Different Pricing Strategies: Experiment with different pricing strategies, such as tiered pricing or promotional pricing, to determine what works best for your business.
- Evaluate and Adjust: Continuously monitor your pricing strategies and evaluate their effectiveness. Adjust your pricing strategies as needed to optimize profitability and customer satisfaction.
Role of MRP and ERP Systems in Reducing Manufacturing Costs
MRP (Material Requirements Planning) and ERP (Enterprise Resource Planning) systems are essential tools for managing production planning, inventory, and supply chain activities in manufacturing. MRP systems enable manufacturers to optimize their inventory levels, plan production schedules, and ensure the timely delivery of raw materials and finished products.
ERP systems provide a broader view of the organization's operations, including manufacturing, finance, human resources, and customer relationship management. By integrating and automating key business processes, MRP and ERP systems can improve efficiency, reduce waste, and lower costs across the manufacturing process.
These systems can also provide real-time data and analytics to support informed decision-making, allowing manufacturers to continually refine their operations for maximum cost savings.
How can Deskera Help You?
Deskera ERP and MRP systems help you to keep your business units organized. The system's primary functions are as follows:
- Keep track of your raw materials and final items inventories
- Control production schedules and routings
- Keep a bill of materials
- Produce thorough reports
- Make your own dashboards
Deskera's integrated financial planning tools enable investors to better plan and track their investments. It can assist investors in making faster and more accurate decisions.
Deskera Books allows you to better manage your accounts and finances. Maintain good accounting practices by automating tasks like billing, invoicing, and payment processing.
Deskera CRM is a powerful solution that manages your sales and helps you close deals quickly. It not only enables you to perform critical tasks like lead generation via email, but it also gives you a comprehensive view of your sales funnel.
Deskera People is a straightforward tool for centralizing your human resource management functions.
Key Takeaways
- Implementing lean manufacturing techniques can reduce waste and improve efficiency.
- Investing in automation can increase productivity and reduce labor costs.
- Just-in-time production can reduce inventory costs and improve cash flow.
- Negotiating with suppliers can help reduce material costs.
- Outsourcing non-core functions can reduce labor costs and improve focus on core competencies.
- Improving maintenance procedures can reduce downtime and maintenance costs.
- Training employees can improve efficiency and reduce errors.
- Implementing quality control measures can reduce defects and improve customer satisfaction.
- Streamlining production processes can improve efficiency and reduce costs.
- Analyzing and adjusting pricing strategies can improve profitability.
- Using alternative materials can reduce material costs.
- Investing in energy-efficient equipment can reduce energy costs.
- Implementing waste reduction techniques can reduce waste and disposal costs.
- Improving inventory management can reduce carrying costs and increase efficiency.
- Utilizing MRP and ERP systems can improve visibility and control over the supply chain.
Related Articles
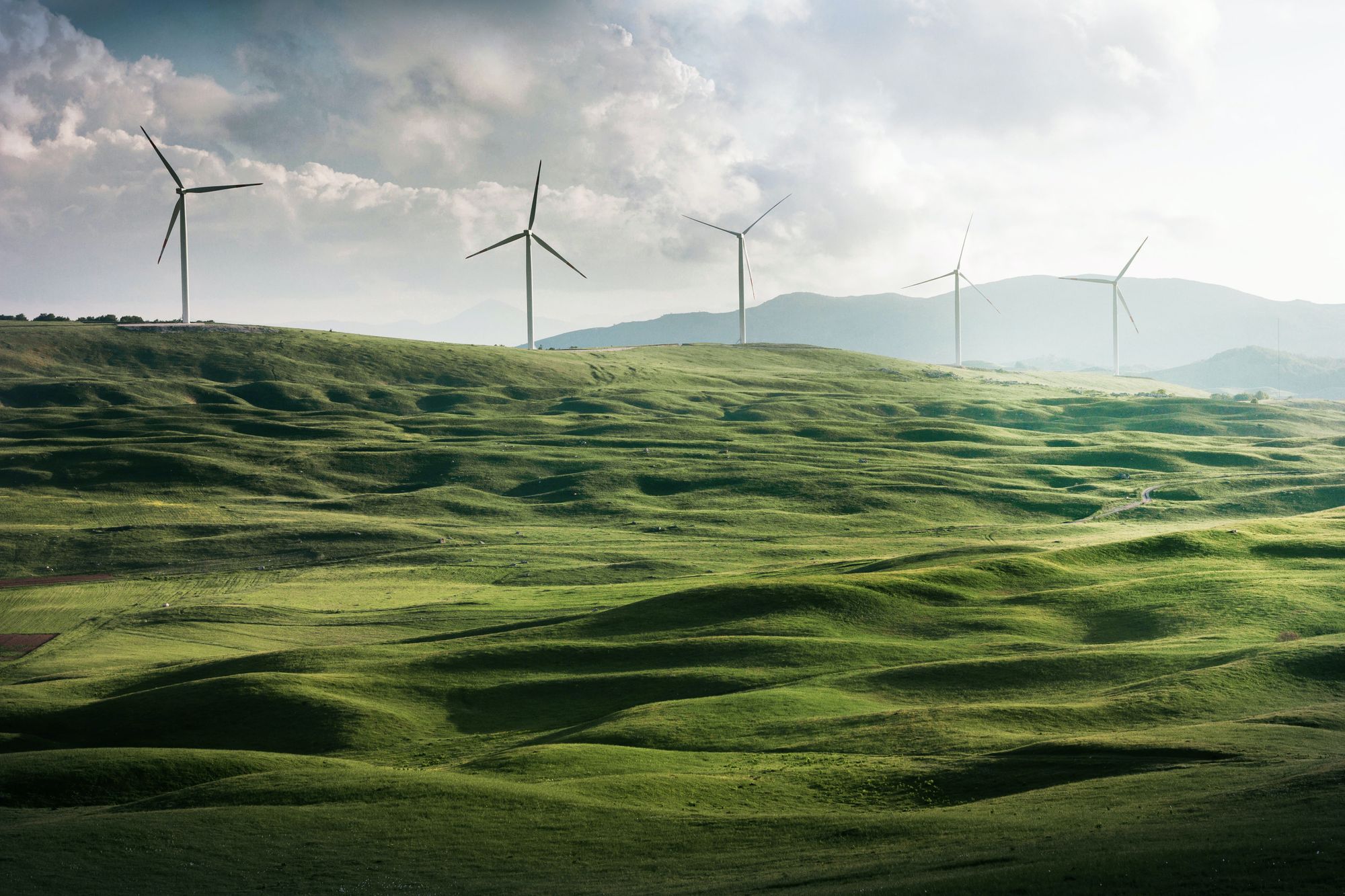
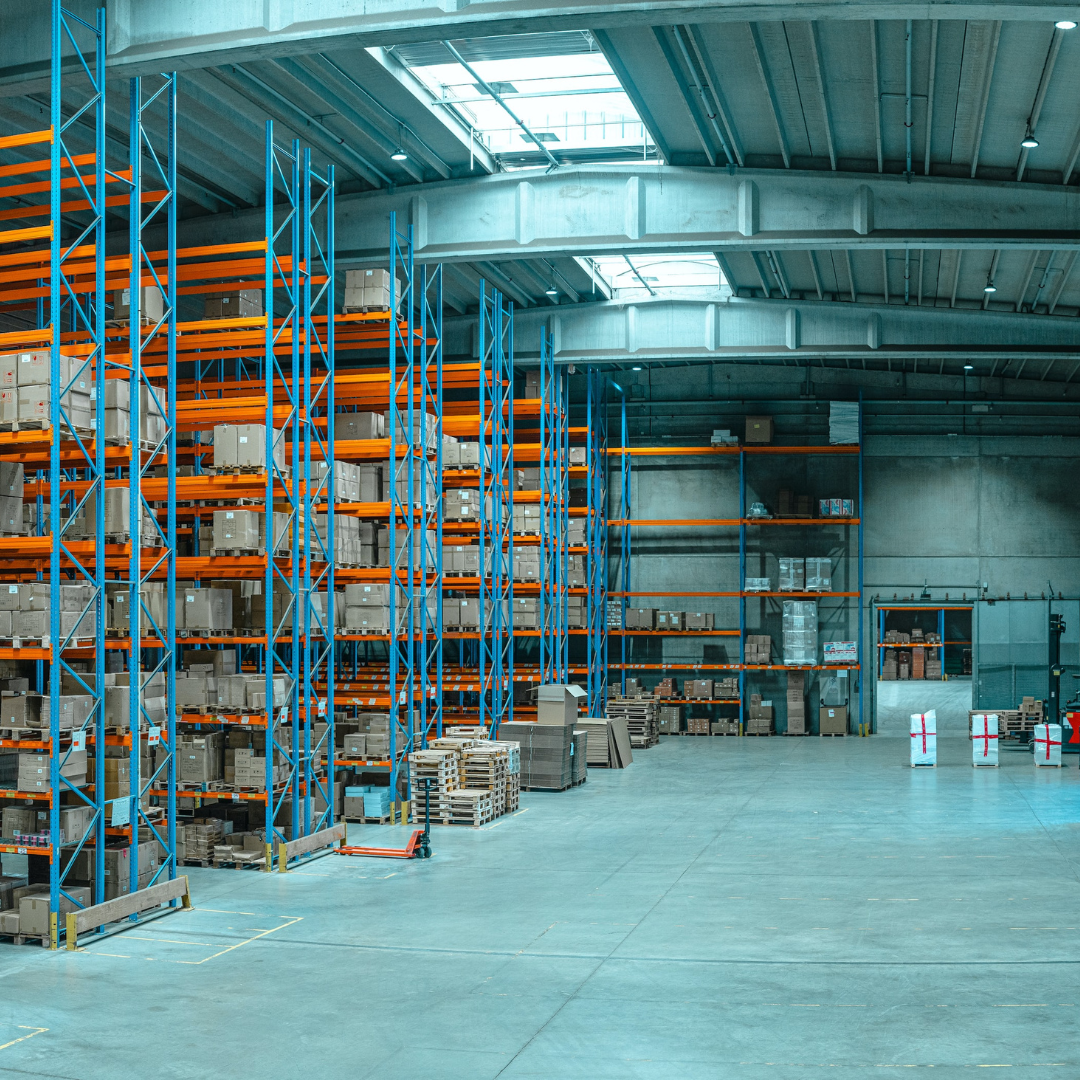
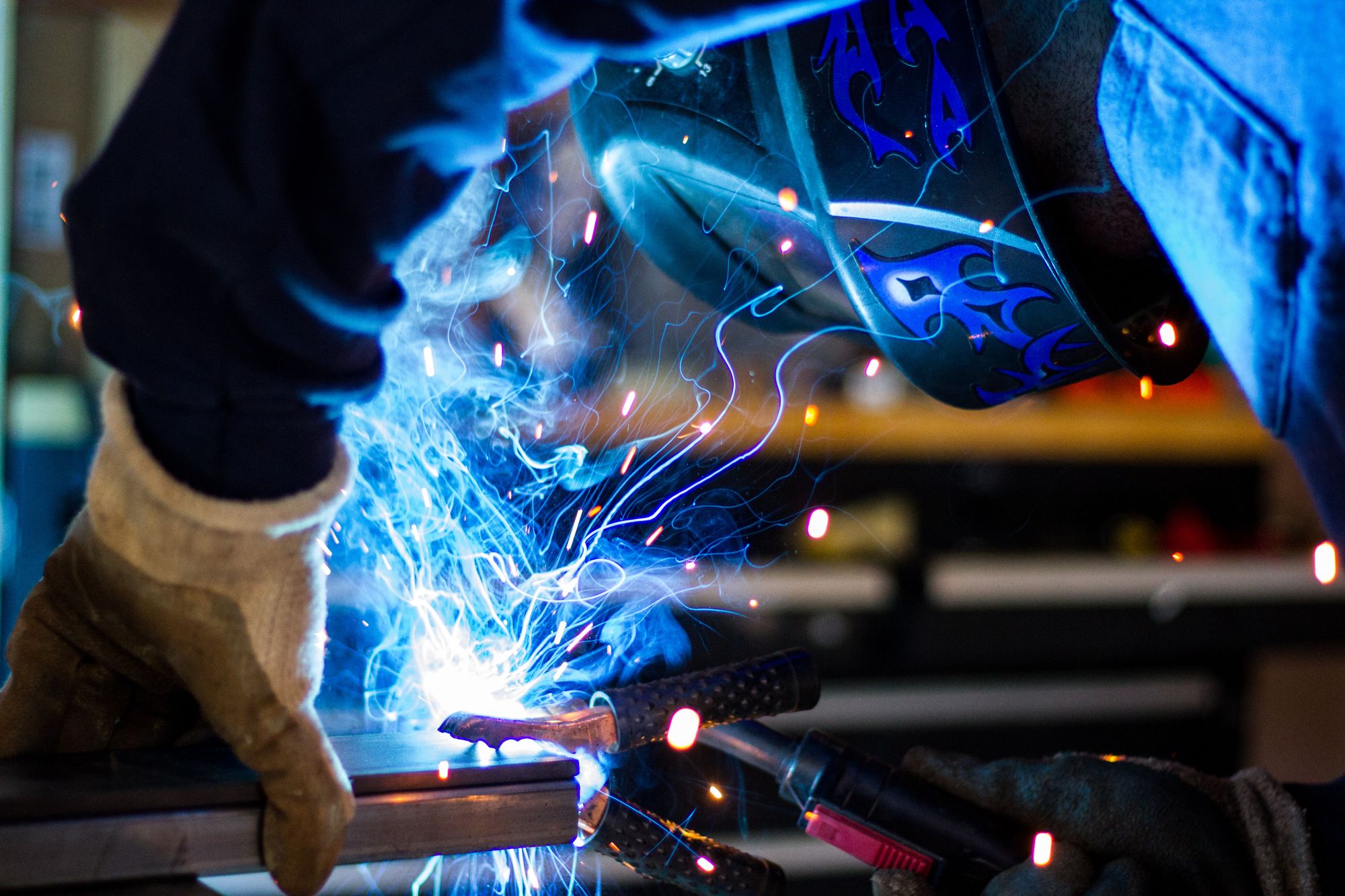