Have you ever stopped to admire the intricate design of a wooden piece of furniture or the unique texture of a wooden toy? Wood products have a timeless appeal that can add warmth and character to any space.
But have you ever wondered what goes into designing and developing these beautiful creations? From conceptualization to production, the wood manufacturing industry is a complex process that requires careful planning and execution.
According to a report by the U.S. Forest Service, in 2020, the United States produced 384 billion board feet of industrial roundwood, with the majority being used for sawlogs and pulpwood.
With the growth of the wood manufacturing industry, there is a greater need for innovative and sustainable product design and development. Companies must stay ahead of the competition by utilizing advanced technology, incorporating sustainable practices, and keeping up with changing consumer preferences.
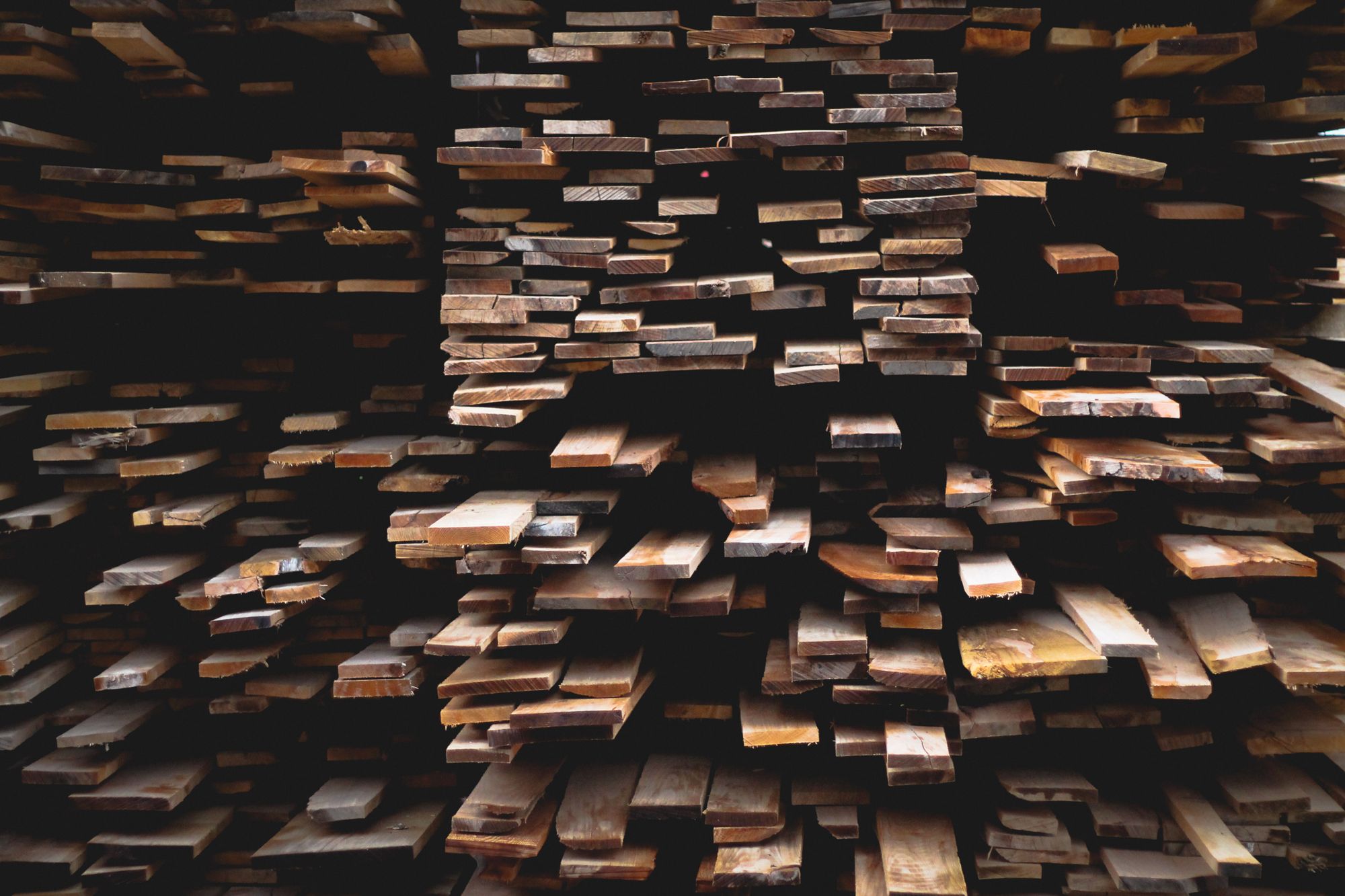
This article will explore the ins and outs of wood product design and development and their essential role in the wood manufacturing industry.
So, whether you are a furniture enthusiast, a woodworker, or simply curious about the industry, read on to discover the latest developments in wood product design and manufacturing.
Here's what we shall cover in this post:
- Introduction: Wood Product Design and Development
- Sustainable Design Practices for Wood Products
- Cost-Effective Design for Wood Products
- Embracing Digital Tools for Wood Product Design
- Packaging and Presentation in Wood Product Design
- Testing and Validation of Wood Product Design
- Conclusion
- Key Takeaways
Introduction: Wood Product Design and Development
Wood product design and development is a process of creating innovative and functional products using wood as the primary material. It involves conceptualizing, designing, prototyping, and manufacturing wood products that meet specific requirements, such as durability, aesthetics, functionality, and cost-effectiveness.
- The design process typically begins with an idea, which is then refined and translated into sketches and 3D models using various design tools and software. Once the design is finalized, a prototype is created to test and evaluate the product's functionality, usability, and marketability.
- The manufacturing process involves selecting the right type of wood, cutting, shaping, joining, and finishing the product. The choice of wood species, grain orientation, and cutting techniques can greatly influence the final product's performance and aesthetic appeal.
- In recent years, there has been an increasing demand for sustainable and eco-friendly wood products, which has led to the development of new design and manufacturing techniques that promote resource efficiency and minimize waste.
- Wood product design and development can also be a platform for promoting cultural and traditional practices and exploring new and emerging technologies. With the right skills, knowledge, and resources, designers and manufacturers can create innovative and high-quality wood products that meet the evolving needs of consumers and contribute to a more sustainable future.
Design Principles for Wood Products
Design plays a vital role in the wood product industry, directly impacting a product's aesthetics, functionality, and value. Wood product design principles encompass a wide range of considerations, from choosing wood species to selecting appropriate joinery techniques.
- Functionality: The primary goal of any wood product is to serve its intended function. The design should ensure that the product meets the needs of the user and is easy to use. This includes considering the product's size, weight, and shape.
- Durability: Wood is a durable material, but its longevity depends on the product's design. The design should take into account the expected wear and tear of the product and ensure that it can withstand the intended use.
- Aesthetics: The appearance of a wood product can be just as important as its functionality. The design should consider the overall look and feel of the product, including its color, texture, and finish.
- Sustainability: Sustainability is becoming an increasingly critical design principle in the wood product industry. Designers must consider the product's environmental impact throughout its entire lifecycle, from wood sourcing to end-of-life disposal. This involves considering the wood's origin, the manufacturing process, the product's energy efficiency, and the potential for recycling or repurposing at the end of its useful life.
- Ergonomics: The design of a wood product should take into account the ergonomics of its use. This includes considering the user's comfort and safety, as well as the ease of use and accessibility.
- Material Efficiency: The design of a wood product should aim to maximize the use of the material while minimizing waste. This includes designing products that can be made from smaller pieces of wood, using scraps and waste wood to create new products or components, and ensuring that the product can be disassembled for repair or recycling.
- Cost-effectiveness: The design of a wood product should take into account the cost of materials, labor, and production. This includes designing products that can be made efficiently, using cost-effective materials and manufacturing techniques, and ensuring that the product can be produced at a competitive price.
Innovation in Wood Product Design
Innovation is essential in every industry, and the wood product design industry is no exception. Here are some points that highlight the significance of innovation in wood product design:
- Innovation allows for new product creation: Innovation in wood product design leads to the creation of new and unique products that meet the specific needs of consumers. It enables designers to explore new ideas and experiment with different materials, shapes, and sizes, resulting in fresh and exciting products.
- Innovation improves product functionality: Innovation in wood product design can lead to the development of products that perform better than existing ones. Designers can create products that offer users greater convenience, comfort, and safety by incorporating new technologies, features, and functionalities.
- Innovation enhances aesthetic appeal: Wood products are highly valued for their visual appeal. Innovation in design can help to create products that are not only functional but also visually appealing. Designers can create aesthetically pleasing products that meet customers' expectations by experimenting with different shapes, colors, textures, and finishes.
- Innovation drives market competitiveness: Innovation in wood product design is critical for businesses to remain competitive in the market. By introducing new and innovative products, companies can stay ahead of the competition, attract more customers, and increase their market share.
- Innovation supports sustainability: Innovation in wood product design can also contribute to sustainability efforts. By exploring new materials and manufacturing process, designers can create environmentally friendly products and promote sustainable practices.
- Innovation requires collaboration: Innovation in wood product design requires collaboration between designers, engineers, manufacturers, and suppliers. By working together, they can share ideas, insights, and resources to develop products that meet the needs of consumers while also being economically viable and sustainable.
Sustainable Design Practices for Wood Products
Sustainable design practices are critical for ensuring that wood products are produced in an environmentally friendly way and that they are safe and healthy for consumers. Here are some principles of sustainable design practices for wood products:
- Material Selection: Choosing the right materials for wood products is essential in sustainable design. Using FSC (Forest Stewardship Council) certified wood helps protect forests and maintain biodiversity. Other sustainable options include recycled wood, bamboo, and composite wood products.
- Energy Efficiency: Using energy-efficient machines and equipment can reduce the energy used in wood product manufacturing. Using renewable energy sources like wind and solar can also help reduce the carbon footprint of wood product manufacturing.
- Minimal Waste: Sustainable design practices for wood products focus on reducing waste in the production process. This can be achieved through the use of computer-aided design (CAD) and prefabrication to optimize the use of wood and through recycling and reusing wood waste.
- Durability and Longevity: Sustainable wood products should be designed to last for a long time, reducing the need for replacements and minimizing waste. This can be achieved through the use of durable wood species and through the application of protective coatings to extend the life of the product.
- Disassembly and Recycling: Sustainable design practices for wood products should include disassembly and recycling at the end of the product's life. This can be achieved by using fasteners and connectors that allow for easy disassembly and by using materials that are easy to recycle.
- Life Cycle Assessment: Sustainable design practices for wood products should consider the product's life cycle, including its environmental impact at every stage of production, use, and disposal. Life cycle assessment (LCA) can help identify areas for improvement and optimize sustainable design practices.
- Use of Non-Toxic Materials: The use of non-toxic materials in wood product manufacturing can improve the safety and health of consumers, workers, and the environment. Non-toxic finishes and adhesives can be used instead of traditional finishes and adhesives that contain harmful chemicals.
- Local Sourcing: Sourcing wood products from local suppliers can reduce the carbon footprint of transportation and support the local economy. This can also ensure that the wood is harvested sustainably and legally.
User-Centered Design for Wood Products
User-centered design (UCD) is a design approach that places the end-users at the center of the design process. The primary goal of UCD is to create products that meet the needs and preferences of the users, leading to better product acceptance and increased user satisfaction. In the context of wood products, UCD can help create products that are functional, aesthetically pleasing, and easy and intuitive to use.
Here are some of the key benefits and steps involved in adopting a user-centered design approach for wood products:
Benefits of User-Centered Design in Wood Products:
- Improved User Satisfaction: By involving end-users in the product design process, designers can better understand their needs and preferences. This can lead to wood products that are better suited to the target audience's needs, resulting in higher user satisfaction.
- Reduced Development Costs: UCD can help identify potential issues early in the design process, which can be corrected before production begins. This can lead to cost savings by reducing the need for product rework or redesign.
- Increased Product Value: Wood products that are designed with the end-user in mind are more likely to be perceived as valuable by the target audience. This can lead to increased sales and higher profit margins.
- Improved Marketability: Products that are designed with the end-user in mind are more likely to meet market needs, making them more attractive to potential customers. This can lead to increased sales and market share for the manufacturer.
- Better Brand Perception: A product that is designed with the end-user in mind can help improve the overall brand perception. This can lead to increased brand loyalty and repeat business.
- Higher Quality Products: UCD helps identify potential issues early in the design process, which can result in higher quality products that meet or exceed customer expectations.
- Competitive Advantage: A wood product that is designed with the end-user in mind can give manufacturers a competitive advantage over their rivals. This can help companies differentiate themselves in the marketplace and gain a competitive edge.
- Increased Collaboration: UCD requires close collaboration between designers, developers, and end-users. This can lead to a more collaborative and inclusive work environment, which can improve overall team performance.
- Reduced Risk: By involving end-users in the design process, manufacturers can reduce the risk of producing products that fail to meet customer expectations. This can help minimize the risk of product recalls and negative brand perception.
- Improved Design Process: UCD can help streamline the design process by identifying potential issues early in the process. This can reduce the number of design iterations required, resulting in faster time to market for new products.
Steps involved in User-Centered Design for Wood Products:
- Identify the target users: The first step in UCD is to identify the users who will be using the wood product. This involves understanding their demographics, needs, and preferences. For example, if the product is a wooden chair, the target users may include people of different ages, sizes, and weights.
- Conduct user research: Once the target users are identified, the next step is to conduct user research. This involves gathering data on their needs, behaviors, and preferences. The data can be collected through surveys, interviews, and observations. The goal is to deeply understand the users' needs and pain points.
- Create user personas: User personas are fictional characters that represent the target users. They are based on the data collected during user research. The personas include information such as the users' goals, needs, and behaviors. They are used to guide the design process and ensure that the product meets the needs of the target users.
- Develop design concepts: Based on the user personas and research data, design concepts are developed. These are rough sketches and ideas for the product design. The goal is to create multiple design concepts that address the users' needs and preferences.
- Prototype and test: Prototypes are created once the design concepts are developed. Prototypes can be physical or digital models of the product. They are used to test the design concepts and gather feedback from the users. The feedback is used to refine the design and create a final product that meets the users' needs.
- Implement the design: After the design is finalized, it is time to implement it. This involves creating detailed drawings, selecting materials, and creating a manufacturing plan. The goal is to ensure that the final product is high-quality, aesthetically pleasing, and functional.
- Evaluate the product: Once the product is manufactured, it is important to evaluate its performance. This involves gathering feedback from users and assessing the product's performance in real-world settings. The goal is to identify any issues and make improvements to the design.
Cost-Effective Design for Wood Products
Cost-effective design is an essential aspect of wood product development. Here are some points to consider when designing a cost-effective wood product:
- Define product requirements:
The first step in achieving cost-effective design is to clearly define the product requirements. This involves understanding the customer's needs and expectations and any regulatory requirements. By defining product requirements, manufacturers can focus their design efforts on features that add value to the customer while eliminating unnecessary features that increase costs.
- Optimize material usage:
Wood is the primary raw material used in the wood product industry, and optimizing its usage can significantly reduce costs. This can be achieved by designing products that require minimal material usage, using standard sizes and shapes, and minimizing waste during production. Additionally, selecting cost-effective materials and suppliers can help reduce overall material costs.
- Simplify design:
Simplifying the design of wood products can also help reduce costs. This involves designing products with fewer parts and simpler manufacturing processes. Simple designs also reduce the likelihood of production errors, which can increase costs through rework and product recalls.
- Use efficient production methods:
Efficient production methods can significantly reduce production costs. This can be achieved by using automation, implementing lean manufacturing principles, and optimizing production workflows. Manufacturers can reduce lead times, minimize waste, and improve overall efficiency by streamlining production processes.
- Implement quality control measures:
Quality control measures are essential to ensure that wood products meet customer requirements and quality standards. This involves testing products throughout the production process to identify defects and non-conformances. Manufacturers can minimize rework and scrap by detecting and addressing quality issues early in the production process, reducing costs.
- Incorporate sustainability:
Incorporating sustainability into product design can also help achieve the cost-effective design. This involves designing products with materials that are environmentally friendly, optimizing material usage to minimize waste, and designing products that are recyclable.
Additionally, incorporating sustainable practices into production processes can reduce energy consumption, minimize waste, and improve overall sustainability.
Designing for Durability and Longevity of Wood Products
Selecting appropriate wood species
The choice of wood species is critical to the longevity of the finished product. Different wood species have varying degrees of hardness, durability, and resistance to decay and insects.
Designers should select a wood species suitable for the product's intended use and environment. For instance, if the product is exposed to moisture, a rot-resistant species such as teak, redwood, or cedar would be more suitable.
Proper joinery techniques
Joinery techniques such as mortise and tenon, dovetail, and tongue and groove joints, among others, are essential for creating a strong and durable product. Proper joinery ensures that the wood pieces are securely held together, preventing warping, cracking, or splitting. Additionally, designers can incorporate mechanical fasteners such as screws or bolts to reinforce the joints.
Surface treatment
Surface treatment techniques such as sanding, staining, and finishing can help enhance the durability and longevity of wood products. Sanding smooths out rough spots and reduces the chances of splintering. Staining and finishing protect the wood from moisture, UV rays, and other environmental factors that may cause decay or discoloration.
Design for ease of maintenance
Designing wood products for ease of maintenance can go a long way in extending their lifespan. Designers can incorporate features such as removable parts or surfaces, easy-to-clean finishes, and instructions for care and maintenance.
Engineering design
Engineering design principles can also be applied to enhance the durability and longevity of wood products. For instance, designers can use computer-aided design (CAD) software to create 3D models of their products and test them for structural stability and load-bearing capacity before the actual production process.
Importance of Designing for Durability and Longevity
- Sustainable production: Designing products that last longer reduces the need for frequent replacement, reducing waste and conserving resources. By choosing materials that are durable and designing products that withstand wear and tear, manufacturers can create products that have a smaller impact on the environment.
- Reduced costs: Creating products that have a longer lifespan can help reduce costs for both the manufacturer and the consumer. For the manufacturer, designing products with durability in mind can help reduce production costs, as fewer replacements and repairs will be needed. For the consumer, a product that lasts longer means fewer replacements, which translates to cost savings in the long run.
- Customer satisfaction: Customers are more likely to be satisfied with a product that lasts longer and performs well over time. By designing products with durability in mind, manufacturers can build brand loyalty and reputation for quality, which can lead to increased sales and profitability.
- Safety: A product that is designed to last longer is less likely to fail unexpectedly, which can help prevent accidents and injuries. This is especially important for products that are used in high-risk environments, such as construction or industrial settings.
- Compliance with regulations: Many countries have regulations in place to encourage the production of durable and long-lasting products. By designing products with durability in mind, manufacturers can ensure compliance with these regulations and avoid penalties and fines.
Design Considerations for Durability and Longevity of Wood Products
- Material selection: The type of wood used in a product significantly impacts its durability. Hardwoods like oak, maple, and cherry are more durable than softwoods like pine, spruce, and cedar. Moreover, selecting wood that has been sustainably sourced and appropriately treated for pests and moisture can increase its lifespan.
- Structural design: The structural design of a wood product affects its strength and durability. A well-designed product can distribute loads and stress evenly, reducing the risk of damage or failure. Designing for appropriate loading and deflection factors is also critical to avoid excessive stress on the product.
- Joint design: Joints are a weak point in wood products and can be prone to failure if not designed correctly. Mortise and tenon joints, for example, are stronger than butt joints or nails. A well-designed joint can help distribute stress and load evenly, improving the product's durability.
- Surface treatment: The surface treatment of a wood product can affect its durability and longevity. Applying a protective coating such as varnish, lacquer, or wax can help prevent moisture and UV damage, prolonging the product's lifespan. Additionally, applying a stain or paint can help change the product's aesthetic appeal.
- Maintenance: Proper maintenance is crucial to ensuring the durability and longevity of wood products. Providing guidelines for the proper use and care of the product, including cleaning, oiling, or waxing, can help prevent damage and prolong the product's lifespan.
Designing for Repair and Maintenance of Wood Products
Designing wood products with repair and maintenance in mind can help extend their useful life and reduce waste.
Design for accessibility: One key principle to consider when designing for repair and maintenance is accessibility. Designing a product with easy access to key components or areas that may require repair can reduce the time and effort needed to perform repairs and make it more likely that repairs will be done properly.
This can also help reduce the need for specialized tools or expertise, making repairs more accessible to a wider range of users.
Choose durable materials: Another important consideration when designing for repair and maintenance is the choice of materials. Choosing durable materials that are resistant to wear and tear can help extend a product's life and reduce the need for repairs. For example, using hardwoods for furniture frames or ceramic tiles for flooring can make these products more resistant to damage and easier to repair.
Design for modularity: Modularity is another key principle to consider when designing for repair and maintenance. By designing products with modular components that can be easily replaced or repaired, designers can reduce the time and cost of repairs and minimize waste.
For example, a modular bookshelf system might consist of individual shelves that can be replaced as needed rather than requiring the entire unit to be replaced in the event of damage.
Consider maintenance requirements: In addition to designing for repair, designers should also consider maintenance requirements when designing wood products. This might include considerations such as ease of cleaning or the need for regular oiling or other treatments to maintain the appearance and condition of the product.
By designing products with these maintenance requirements in mind, designers can make it easier for users to keep their products in good condition and avoid the need for more extensive repairs.
Use simple and reliable fastening methods: Finally, designers should consider the use of simple and reliable fastening methods when designing for repair and maintenance. This might include using screws, bolts, or other fasteners that can be easily removed and replaced rather than relying on adhesives or other more permanent methods.
By using reliable fastening methods, designers can make it easier for users to perform repairs and reduce the risk of further damage or failure.
Designing for Recycling and Upcycling of Wood Products
Sustainability has become a critical consideration for many designers and manufacturers, and this is particularly true in the case of wood products.
As a renewable resource, wood has long been an attractive choice for designers and manufacturers, but the need to create products that are more sustainable, recyclable, and upcycle has become increasingly important.
Designers and manufacturers are now challenged to create products that can be easily recycled or upcycled at the end of their useful life, and this requires careful consideration of the design and materials used.
Here are some key points to consider when designing for recycling and upcycling of wood products:
Choose materials that are easy to recycle or upcycle
The choice of materials is crucial in designing for the recycling and upcycling of wood products. Designers should choose materials that are easy to recycle or upcycle, such as untreated or minimally treated wood, which can be easily repurposed or recycled into new products.
Composite materials made from wood and other materials, such as plastics or adhesives, may be more difficult to recycle, and designers should avoid them whenever possible.
Use modular design and construction
Modular design and construction allow for easy disassembly of products at the end of their useful life, making it easier to recycle or upcycle the various components. Modular design also makes it easier to replace individual components rather than replacing the entire product, extending the product's useful life and reducing waste.
Design for disassembly
Designing for disassembly involves creating products that can be easily removed without damaging the individual components. This can involve the use of fasteners, such as screws or bolts, instead of adhesives or other permanent connections. Designers can also consider using interlocking components that can be easily taken apart or designing products with easily removable parts, such as legs or handles.
Consider the product's entire lifecycle
Designers should consider the entire lifecycle of the product when designing for recycling and upcycling. This includes the end-of-life and manufacturing, distribution, and use stages.
Choosing materials and production methods that minimize waste and energy consumption, designing durable and long-lasting products, and creating products that can be easily transported and stored can all contribute to a more sustainable product lifecycle.
Explore upcycling opportunities: Upcycling involves turning waste materials into new products or materials. Designers can explore opportunities to upcycle wood waste or other materials from manufacturing into new products or materials, reducing waste and creating a more sustainable supply chain.
Embracing Digital Tools for Wood Product Design
As technology continues to evolve, digital tools are becoming increasingly popular in the wood product design process. The use of digital tools allows for greater efficiency and accuracy in the design process, as well as increased creativity and innovation.
Enhanced 3D Visualization
Digital tools such as CAD (Computer-Aided Design) and BIM (Building Information Modeling) software allow designers to create highly detailed 3D models of their designs. These models can be easily manipulated and modified to test different design iterations and options. This enables designers to visualize the product in a realistic way and identify any potential issues early on in the design process.
Collaboration and Communication
Digital tools enable designers to collaborate and communicate with other stakeholders, such as engineers, manufacturers, and clients. These tools provide a platform for seamless communication and sharing of design files and ideas. This helps to ensure that all stakeholders are on the same page and that the design meets everyone's needs and requirements.
Improved Accuracy and Precision
Digital tools allow designers to create highly accurate and precise designs, reducing the risk of errors and mistakes in the final product. This is particularly important for complex designs that require a high level of precision.
Rapid Prototyping and Manufacturing
Digital tools can be used to quickly and efficiently prototype the product. This enables designers to test the product's functionality and aesthetics before moving to the manufacturing stage. Additionally, digital tools can be integrated with CNC (Computer Numerical Control) machines to create highly precise and intricate designs.
Increased Customization and Personalization
Digital tools allow for greater customization and personalization of wood products. Designers can easily modify the design to meet the specific needs and preferences of the customer. This helps to increase customer satisfaction and loyalty.
Sustainability and Efficiency
Digital tools can help to improve the sustainability and efficiency of the wood product design process. By reducing the need for physical prototypes and mock-ups, designers can reduce waste and minimize their environmental impact. Additionally, digital tools can help to streamline the design process, reducing the time and resources required to create a high-quality product.
Materials and Finishes for Wood Product Design
Materials and finishes are essential components of wood product design, as they affect the final product's appearance, durability, and functionality.
Types of Materials:
- Solid Wood: Solid wood is a popular material choice for wood product design because of its natural beauty, durability, and versatility. It can be cut and shaped into different forms, and its grain patterns and textures can add character and uniqueness to the finished product. However, solid wood can be expensive and can be prone to cracking, warping, and splitting if not properly seasoned and maintained.
- Plywood: Plywood is a sheet material made from thin layers of wood veneer that are glued together. It is a cost-effective alternative to solid wood and is commonly used in furniture, cabinetry, and paneling. Plywood is known for its strength and stability, as well as its resistance to warping and shrinking. It can also be painted or stained to achieve various finishes.
- Medium Density Fiberboard (MDF): MDF is a composite material made from wood fibers and resin, which are pressed together under high pressure and heat. MDF is a popular material choice for wood product design because of its smooth surface, uniform density, and low cost. It can be easily cut, shaped, and painted, making it suitable for a wide range of applications.
- Particleboard: Particleboard is another composite material made from wood particles and resin, which are compressed under high pressure and heat. Particleboard is a low-cost alternative to plywood and is commonly used in furniture and cabinetry. It is not as strong as plywood, but it can be reinforced with a veneer or laminate to improve its durability and resistance to moisture.
- Bamboo: Bamboo is a renewable and sustainable material that is becoming increasingly popular for wood product design. It is known for its strength, durability, and natural beauty. Bamboo can be used in a variety of applications, from flooring and furniture to kitchen utensils and accessories.
- Engineered Wood: Engineered wood is a composite material made from wood fibers, adhesives, and other materials. It is designed to be stronger and more durable than solid wood and is commonly used in construction, flooring, and furniture. Some examples of engineered wood include laminated veneer lumber (LVL), oriented strand board (OSB), and cross-laminated timber (CLT).
Types of Finishes:
- Oil Finishes
Oil finishes are the most traditional type of finish and are ideal for enhancing the natural grain of the wood. They are easy to apply and maintain, and can be re-coated without sanding. Oil finishes penetrate the wood, creating a protective layer that repels water and other liquids. However, they can take a long time to dry and are not very durable.
- Wax Finishes
Wax finishes are a popular choice for furniture and decorative items. They offer a soft, subtle sheen that enhances the natural beauty of the wood. Wax finishes are easy to apply and can be buffed to a high shine. However, they are not very durable and require regular maintenance.
- Varnish Finishes
Varnish finishes are a popular choice for outdoor furniture and wooden boats. They provide a hard, durable finish that is resistant to water and UV radiation. Varnish finishes can be glossy or matte, and can be tinted to any color. However, they are difficult to apply and require several coats to achieve a smooth finish.
- Lacquer Finishes
Lacquer finishes are a popular choice for high-end furniture and musical instruments. They offer a hard, durable finish that is resistant to scratches and water. Lacquer finishes are easy to apply and can be sanded and polished to a high shine. However, they are not very heat resistant and can be difficult to repair.
- Stain Finishes
Stain finishes are used to enhance the color of the wood and provide a protective layer. They come in various colors and can be applied to softwoods and hardwoods. Stain finishes can be used alone or in conjunction with other finishes. However, they do not offer much protection against UV radiation and are not very durable.
Factors to Consider: When selecting materials and finishes for wood product design, several factors should be considered:
- Durability: the materials and finishes should be selected based on the intended use and lifespan of the product.
- Sustainability: the materials and finishes should be selected based on their environmental impact and the sustainability of their sourcing and production.
- Aesthetics: the materials and finishes should be selected based on their appearance and how well they complement the product's overall design.
- Safety: the materials and finishes should be selected based on their potential health hazards, such as toxicity and flammability.
Trends in Wood Product Design:
- Natural finishes: there is a growing trend towards using natural finishes that allow the beauty of the wood to shine through without excessive coatings or stains.
- Reclaimed wood: there is also a trend towards using reclaimed wood, which is repurposed from old structures and furniture, giving the product a unique and sustainable touch.
- Sustainable materials: there is an increasing demand for wood products made from sustainable materials, such as bamboo and cork, that have a lower environmental impact than traditional wood products.
Ergonomics and Comfort in Wood Product Design
Ergonomics and comfort are important aspects to consider when designing wood products, especially those that are intended for daily use. The ergonomic design aims to create products that fit the user's needs and body dimensions, allowing for comfort, ease of use, and reduced strain on the body.
Anthropometry and Biomechanics: Anthropometry is the study of the measurements and proportions of the human body, while biomechanics is the study of the mechanics of human movement. These two fields are essential in designing wood products that fit the user's body and movements.
By considering the intended user's height, weight, and body proportions, designers can create products that are comfortable and easy to use.
User-Centered Design: User-centered design involves understanding the needs and preferences of the user and designing products that meet those needs. In the case of wood products, this may involve considering the user's grip strength, range of motion, and the way they use the product.
By involving users in the design process, designers can ensure that their products are comfortable and ergonomic.
Posture and Movement: Posture and movement are essential considerations in designing wood products. Products that are used while sitting, such as chairs, should provide adequate support for the user's back and encourage proper posture.
Products that require reaching, such as shelves, should be designed to minimize strain on the arms and shoulders. By considering the user's posture and movement, designers can create comfortable and safe products.
Materials and Finishes: The materials and finishes used in wood products can also impact their comfort and ergonomics. Smooth, rounded edges are more comfortable to hold than sharp, angular edges. Soft, cushioned seats and backrests are more comfortable than hard, rigid ones. The choice of wood and finish can also impact the feel of the product in the user's hands.
Testing and Evaluation: Testing and evaluation are essential steps in ensuring wood products' ergonomic design and comfort. Users can test prototypes to identify any issues with comfort or usability. Evaluation can also be done through surveys and feedback from users. This information can be used to make improvements and modifications to the design.
Importance of Ergonomics in Wood Product Design:
Ergonomics is crucial in wood product design as it ensures that the products are designed to fit the user's body and movements, reducing discomfort and preventing injuries.
Ergonomic design increases productivity, reduces the risk of injury, and improves the user's overall experience with the product. Uns ergonomically designed products can cause discomfort, pain, and injury to the user, leading to decreased productivity and increased absenteeism.
Considerations for Ergonomic Wood Product Design:
- User demographics: One of the most important ergonomic wood product design considerations is the target user demographic. Products designed for children, for example, will have different ergonomic requirements than products designed for older adults. It's important to take into account factors like height, weight, and physical abilities when designing products.
- Posture: Poor posture can lead to a variety of physical problems, including back pain, neck pain, and repetitive strain injuries. When designing wood products, it's important to consider the user's natural posture and ensure that the product promotes good posture. For example, chairs should be designed to provide lumbar support, and desks should be adjustable to accommodate different body types.
- Movement: Another important consideration for ergonomic wood product design is movement. Products should be designed to accommodate the user's natural movement and should not require repetitive or awkward motions that can lead to injury. For example, a saw designed with an ergonomic handle that allows the user to maintain a natural grip can help reduce strain on the wrist and forearm.
- Comfort: Ergonomic wood products should also be designed for user comfort. This includes things like padding on seats and armrests, as well as the use of materials that don't irritate the skin. For example, using softwood for handles can provide a more comfortable grip.
- Accessibility: Wood products should also be designed to be accessible for users with disabilities. This can include things like wider doorways and hallways for wheelchairs, as well as adjustable work surfaces and seating to accommodate different levels of mobility.
- Safety: Safety is a key consideration in ergonomic wood product design. Products should be designed to minimize the risk of injury, including things like sharp edges and pinch points. It's also important to ensure that products meet safety standards and regulations.
- Aesthetics: Finally, while ergonomics is an important consideration, aesthetics shouldn't be overlooked. Wood products should be visually appealing and fit in with the overall design aesthetic of the space they are used in. This can help to increase user satisfaction and promote productivity.
Techniques for Achieving Ergonomic and Comfortable Wood Product Design:
- Anthropometric data: Anthropometric data refers to the measurements of the human body. Designers can use this data to determine the optimal size and shape of their products. By understanding the range of human sizes and shapes, designers can create products that are comfortable for a wider range of users.
- Task analysis: Task analysis involves breaking down a task into its component parts to understand the physical and cognitive demands placed on the user. By analyzing the tasks that users will perform with the product, designers can identify potential ergonomic issues and make adjustments to improve comfort and reduce the risk of injury.
- Mockups and prototypes: Mockups and prototypes are physical or digital models of a product that allow designers to test the ergonomics and comfort of their designs. By creating mockups and prototypes, designers can identify areas of the design that need improvement and make adjustments before the product goes into production.
- User testing: User testing involves gathering feedback from actual users of the product. By observing users as they interact with the product, designers can identify areas where the design is uncomfortable or awkward to use. This feedback can be used to make adjustments to the design before it goes into production.
- Material selection: The materials used in a product can have a significant impact on its ergonomics and comfort. Designers should carefully consider the properties of different materials and choose materials that are comfortable to touch and use, as well as durable and long-lasting.
- Shape and form: The shape and form of a product can greatly impact its ergonomics and comfort. Designers should consider the size, shape, and weight of the product, as well as the location of any handles or other gripping surfaces. By optimizing the shape and form of the product, designers can improve its comfort and ease of use.
- Adjustability: Designers can improve the ergonomics of a product by making it adjustable. Adjustable features such as height, angle, and tilt can help users find a comfortable position for using the product. This is particularly important for products that will be used for long periods of time, such as chairs or desks.
- Feedback mechanisms: Feedback mechanisms such as vibration, sound, or visual cues can help users understand how to use the product properly and prevent injury. For example, a vibrating handle on a power tool can alert the user when they are applying too much pressure, reducing the risk of injury.
Packaging and Presentation in Wood Product Design
Packaging and presentation are essential aspects of wood product design that contribute to the overall success of a product. The way a product is packaged and presented can significantly impact a consumer's decision to purchase it.
- Designing for packaging: The packaging design for a wood product should complement the product's design and appeal to the target audience. The packaging should protect the product during transportation and storage and be easy to open.
- Sustainable packaging: Sustainable packaging is becoming increasingly important in today's environmentally conscious society. Designers should consider using eco-friendly materials for packaging and reducing the amount of waste generated.
- Branding and labeling: Effective branding and labeling are essential for marketing a wood product. The packaging should prominently display the brand name, logo, and product information to make it easy for consumers to identify the product.
- Presentation: The way a product is presented can influence a consumer's perception of its quality and value. Wood products should be presented in a way that showcases their unique features and benefits.
- Visual merchandising: Visual merchandising is the art of presenting products in a way that is visually appealing and encourages customers to make a purchase. The use of attractive displays, lighting, and signage can significantly impact sales.
- Product photography: High-quality product photography is essential for showcasing a wood product's design and features. The photographs should be clear, well-lit, and show the product from different angles to provide a complete view.
- Informational materials: Providing customers with informational materials such as brochures, catalogs, or instructional manuals can help them make an informed purchase decision. These materials should be well-designed and contain relevant information about the product.
- Unboxing experience: The unboxing experience can leave a lasting impression on customers. Designers should consider the experience of opening and unwrapping a product and create a positive, memorable experience.
Importance of Packaging and Presentation:
- First Impressions: Packaging and presentation are the first things that a customer sees when they encounter a product. A well-designed package can catch the eye and create a positive first impression, which can increase the likelihood of a purchase.
- Protection: Packaging provides protection to the product during shipping and storage, ensuring that it arrives at the customer in good condition. This is particularly important for fragile wood products that can easily be damaged during transportation.
- Branding: Packaging and presentation can be used to reinforce a brand's image and message. Consistent branding across all aspects of a product, including packaging and presentation, can create a sense of trust and familiarity with the customer.
- Differentiation: Well-designed packaging and presentation can set a product apart from its competitors. Unique, eye-catching designs can attract attention and make a product stand out on store shelves or online marketplaces.
- Information: Packaging and presentation can provide important information about the product, such as features, benefits, and usage instructions. This information can help customers make informed purchasing decisions.
Considerations for Packaging and Presentation:
- Design for Convenience: The packaging design should be convenient for the customer to handle, carry and store. The package's size, shape, and weight should be appropriate for the product and its purpose.
- Cost-Effective: The packaging and presentation design should not add to the overall cost of the product. It should be designed to minimize material usage while still providing adequate protection.
- Environmental Considerations: Packaging and presentation designs should be sustainable and environmentally friendly. The use of eco-friendly packaging materials, recycled materials, or biodegradable packaging options can contribute to reducing environmental waste.
- Visual Appeal: Aesthetics play a significant role in packaging and presentation design. The package design should be visually appealing and attract customers' attention.
- Product Information: The packaging should provide information about the product, such as its features, benefits, and instructions for use.
- Product Storage: The packaging should be designed to facilitate easy storage of the product in retail stores, warehouses, and homes.
- Ease of Disposal: The packaging design should make it easy for customers to dispose of the packaging after use.
Intellectual Property Protection for Wood Product Design
Intellectual property (IP) protection is essential in the wood product design industry to safeguard the originality and creativity of designers' works. Designers and manufacturers invest significant amounts of resources in developing innovative and unique products, and without proper protection, their ideas may be replicated and used by others without permission or compensation.
- Patents: A patent is a legal document that gives an inventor the exclusive right to make, use, and sell an invention for a specified period. In the wood product design industry, patents can protect unique and innovative designs of furniture, fixtures, or other products. The patent owner can prevent others from making, using, or selling the patented product without permission.
- Trademarks: Trademarks protect logos, brand names, slogans, and other distinct signs that identify a product or service from others. By obtaining a trademark, a designer can protect the name, logo, or other designations associated with their product and prevent others from using similar marks that could cause confusion.
- Copyrights: Copyright protection extends to original works of authorship, such as designs, drawings, and plans. In the wood product design industry, copyright protection can cover product designs, graphic designs, and other creative works. The owner of a copyrighted work can prevent others from reproducing, distributing, or displaying their work without permission.
- Trade Secrets: A trade secret is a confidential information that provides a competitive advantage to a business. In the wood product design industry, trade secrets may include manufacturing processes, formulas, or designs. A trade secret owner can prevent others from using their confidential information without permission or compensation.
- Design Patents: Design patents are a type of patent that protects the ornamental or aesthetic features of a product. In the wood product design industry, design patents can protect unique shapes, patterns, and surface designs of furniture, fixtures, or other products.
In addition to these types of intellectual property protection, there are also some practical steps designers can take to secure their works:
- Keep detailed records: It is essential to keep detailed records of the design process, including sketches, drawings, and any other documentation. This documentation can serve as evidence in case of any infringement or dispute.
- Mark your products: Marking your products with a patent, trademark, or copyright symbol can inform others that intellectual property rights protect the product. This marking can act as a deterrent to potential infringers.
- Conduct regular searches: Regular searches can help identify any potential infringement of intellectual property rights. This search can be conducted manually or with the help of specialized software tools.
- Work with legal professionals: Working with legal professionals, such as lawyers or patent agents, can help designers navigate the legal complexities of intellectual property protection. These professionals can help file patent applications, draft licensing agreements, and protect the designer's rights.
Collaborative Design and Development in Wood Product Manufacturing
Collaborative design and development play a significant role in the wood product manufacturing industry. It is a process that involves different stakeholders, such as designers, engineers, manufacturers, and end-users, working together to create a product that meets everyone's needs.
- Improved product quality: Collaborative design and development bring together the expertise of different stakeholders in the product development process. This collaboration leads to the creation of a product that meets everyone's needs, resulting in a higher quality product.
- Cost-effective: Collaborative design and development also result in cost savings. By bringing everyone together early in the product development process, issues can be identified and resolved early, reducing the likelihood of costly redesigns or rework.
- Faster time to market: Different stakeholders collaborating in the design and development process can result in a faster time to market. By working together, tasks can be completed more efficiently, and everyone is on the same page, which can result in faster decision-making.
- Increased innovation: Collaborative design and development also increase innovation. By bringing different perspectives to the table, new ideas can be generated, leading to innovative and creative product designs.
- Enhanced communication: Collaborative design and development require open communication between stakeholders. This communication leads to a better understanding of everyone's needs and expectations, ultimately leading to a better product.
- Customer satisfaction: Collaborative design and development result in a product that meets everyone's needs, including the end-user. This leads to a higher level of customer satisfaction and loyalty.
- Risk mitigation: Collaborative design and development can also help mitigate risks associated with product development. By bringing everyone together early in the process, issues can be identified and addressed early, reducing the likelihood of product failures or recalls.
Testing and Validation of Wood Product Design
Testing and validation of wood product design are critical steps in the design and development process to ensure that the product meets the necessary standards and is fit for use.
Importance of Testing and Validation of Wood Product Design: Testing and validation of wood product design is crucial in ensuring that the product meets the requirements of the end-user and the industry standards. This helps in avoiding costly mistakes that may arise from poor design or substandard products. Testing and validation also ensure that the wood product is safe to use, durable, and functional.
Methods Used for Testing and Validation of Wood Product Design: There are different methods used for testing and validation of wood product design, and they include:
- Computer-Aided Design (CAD) Simulation:
CAD simulations are an effective method for testing and validating wood product designs. This method allows designers to create a virtual model of the product, which can be subjected to various tests and simulations to evaluate its performance under different conditions.
CAD simulations can be used to test the strength, durability, and stability of a design, as well as its resistance to various external factors such as temperature, humidity, and impact.
- Prototype Testing:
Prototype testing involves creating a physical model of the wood product and subjecting it to various tests and evaluations to ensure that it meets the desired requirements. This method is particularly useful for evaluating a product design's functionality, ergonomics, and ease of use. Prototype testing can also help identify design flaws or issues that need to be addressed before manufacturing.
- Finite Element Analysis (FEA):
FEA is a computer-based method that can be used to simulate the behavior of a wood product design under various conditions. This method involves dividing the design into small elements and subjecting them to various tests and simulations. FEA can be used to evaluate a design's stress, strain, and deformation, as well as its ability to withstand various external factors such as wind, water, and impact.
- Materials Testing:
Materials testing involves subjecting the materials used in the wood product design to various tests and evaluations to determine their strength, durability, and other properties. This method is particularly useful for evaluating the suitability of a material for a specific application.
Materials testing can also help identify any weaknesses or issues with the materials used in a design that may need to be addressed before manufacturing.
- User Testing:
User testing involves evaluating the wood product design by having potential users interact with it in a real-world setting. This method can help identify any usability issues, design flaws, or areas for improvement. User testing can also provide valuable feedback on the aesthetics, ergonomics, and overall user experience of a product design.
Tools and Equipment Used for Testing and Validation of Wood Product Design:
Different tools and equipment are used for testing and validation of wood product design, and they include:
- Force and Load Measuring Equipment:
Force and load measuring equipment are essential tools for testing the strength and durability of wood products. They measure the load, torque, and forces that a product can withstand before it fails. This equipment includes tensile testing machines, compression testing machines, and bending testing machines.
- Environmental Testing Chambers:
Environmental testing chambers are used to test the effect of various environmental factors on wood products, such as temperature, humidity, and exposure to light. This equipment helps determine the product's durability and performance under various conditions. Examples of environmental testing chambers include climate chambers, humidity chambers, and thermal shock chambers.
- Optical Measuring Devices:
Optical measuring devices accurately measure the geometry and dimensions of wood products. These tools include laser scanners, coordinate measuring machines (CMM), and optical profilometers. They are used to ensure that the product meets the design specifications and tolerances.
- X-ray and Imaging Equipment:
X-ray and imaging equipment are used to inspect the internal structure of wood products, such as composite wood products, to detect defects, voids, or other irregularities. This equipment includes X-ray microscopes, computed tomography (CT) scanners, and magnetic resonance imaging (MRI) machines.
- Acoustic Testing Equipment:
Acoustic testing equipment is used to measure the sound and vibrations generated by wood products. These tools are used to determine the product's acoustic properties, such as sound absorption, transmission, and reflection. Examples of acoustic testing equipment include sound level meters, vibration meters, and impedance tube systems.
- Durability Testing Equipment:
Durability testing equipment is used to evaluate the product's ability to withstand wear, tear, and other environmental factors. This equipment includes abrasion testers, impact testers, and scratch testers. It helps to determine the product's lifespan and how it performs over time.
- Software and Simulation Tools:
Software and simulation tools are used to analyze the product's performance and behavior under various conditions. This equipment includes finite element analysis (FEA) software, computational fluid dynamics (CFD) software, and modeling software. It helps to predict the product's performance before it is manufactured, reducing the cost and time required for physical testing.
Benefits of Testing and Validation of Wood Product Design:
Testing and validation of wood product design offer several benefits, including:
- Ensuring product safety: Testing and validation ensure that the wood product is safe to use and meets the necessary safety requirements.
- Improving product quality: Testing and validation help to identify design flaws and weaknesses, which can be rectified before the product is released to the market, improving the product quality.
- Enhancing customer satisfaction: Testing and validation help to ensure that the product meets the needs and requirements of the end-user, enhancing customer satisfaction.
- Reducing cost: Testing and validation help to identify design flaws and weaknesses early in the design process, reducing the cost of rectifying these flaws later.
How Deskera Can Assist You?
Deskera MRP allows you to closely monitor the manufacturing process. From the bill of materials to the production planning features, the solution helps you stay on top of your game and keep your company's competitive edge.
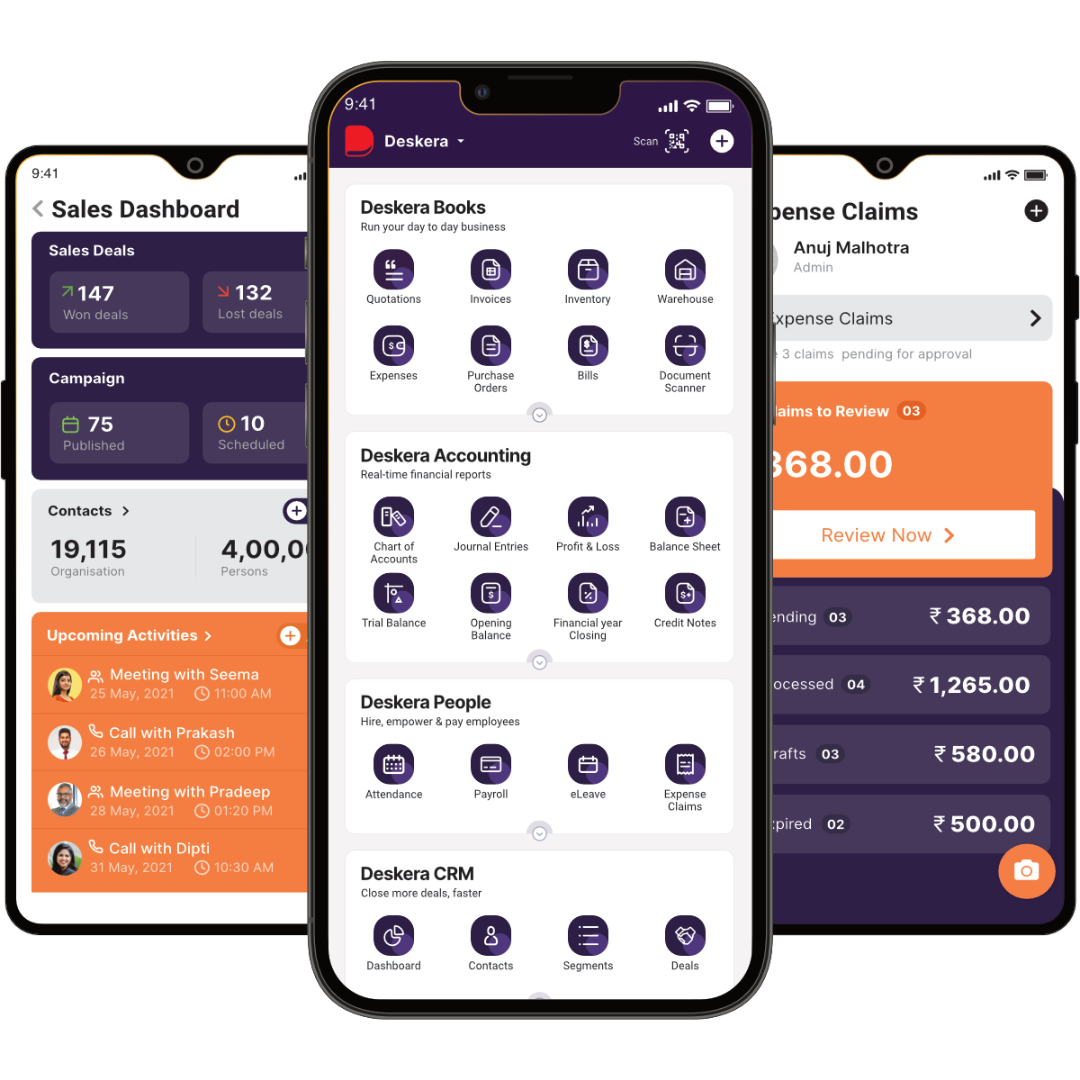
Deskera ERP and MRP system can help you:
- Manage production plans
- Maintain Bill of Materials
- Generate detailed reports
- Create a custom dashboard
Deskera ERP is a comprehensive system that allows you to maintain inventory, manage suppliers, and track supply chain activity in real-time, as well as streamline a variety of other corporate operations.
Deskera Books enables you to manage your accounts and finances more effectively. Maintain sound accounting practices by automating accounting operations such as billing, invoicing, and payment processing.
Deskera CRM is a strong solution that manages your sales and assists you in closing agreements quickly. It not only allows you to do critical duties such as lead generation via email, but it also provides you with a comprehensive view of your sales funnel.
Deskera People is a simple tool for taking control of your human resource management functions. The technology not only speeds up payroll processing but also allows you to manage all other activities such as overtime, benefits, bonuses, training programs, and much more. This is your chance to grow your business, increase earnings, and improve the efficiency of the entire production process.
Conclusion
Designing and developing wood products require a creative approach, sound technical knowledge, and attention to detail. The process involves multiple stages, from ideation to prototyping, testing, and manufacturing. Wood product designers must deeply understand the characteristics and properties of different types of wood, as well as the latest design trends and customer preferences.
Moreover, they need to collaborate with other stakeholders, such as manufacturers, engineers, marketing teams, and customers, to ensure that the product meets the desired specifications and fulfills the intended purpose.
Innovative manufacturing techniques, such as CNC machining, laser cutting, and 3D printing, have revolutionized the way wood products are designed and produced, offering greater precision, efficiency, and customization. However, these technologies also pose some challenges, such as the need for specialized skills, high investment costs, and environmental concerns.
To succeed in the wood product design and development field, designers must stay abreast of the latest industry trends, innovations, and regulations. They need to leverage technology and data analytics to optimize their design process and enhance the user experience. Furthermore, considering the environmental and society's impact, they should adopt a sustainable and responsible approach to wood sourcing, production, and disposal.
Key Takeaways
- Wood product design and development is a crucial stage in manufacturing that helps create innovative and functional products.
- Understanding the target audience and their needs before designing a product is essential.
- Careful consideration of the material properties and manufacturing techniques is necessary for creating high-quality and durable products.
- Designers need to have a solid understanding of woodworking tools and techniques to create precise and intricate designs.
- Collaboration with skilled craftsmen and manufacturers is essential to ensure that the final product is of high quality and meets the desired specifications.
- Using computer-aided design (CAD) software can help streamline the design process and allow for more complex designs to be created.
- Prototyping and testing are essential to ensure that the design is functional and meets the required standards.
- Product design and development is an iterative process, and revisions and improvements are often necessary to create a successful product.
- Attention to detail is crucial in wood product design, as small variations or imperfections can affect the overall quality of the final product.
- Sustainable and environmentally friendly design practices should be considered throughout the product design and development process.
Related Articles
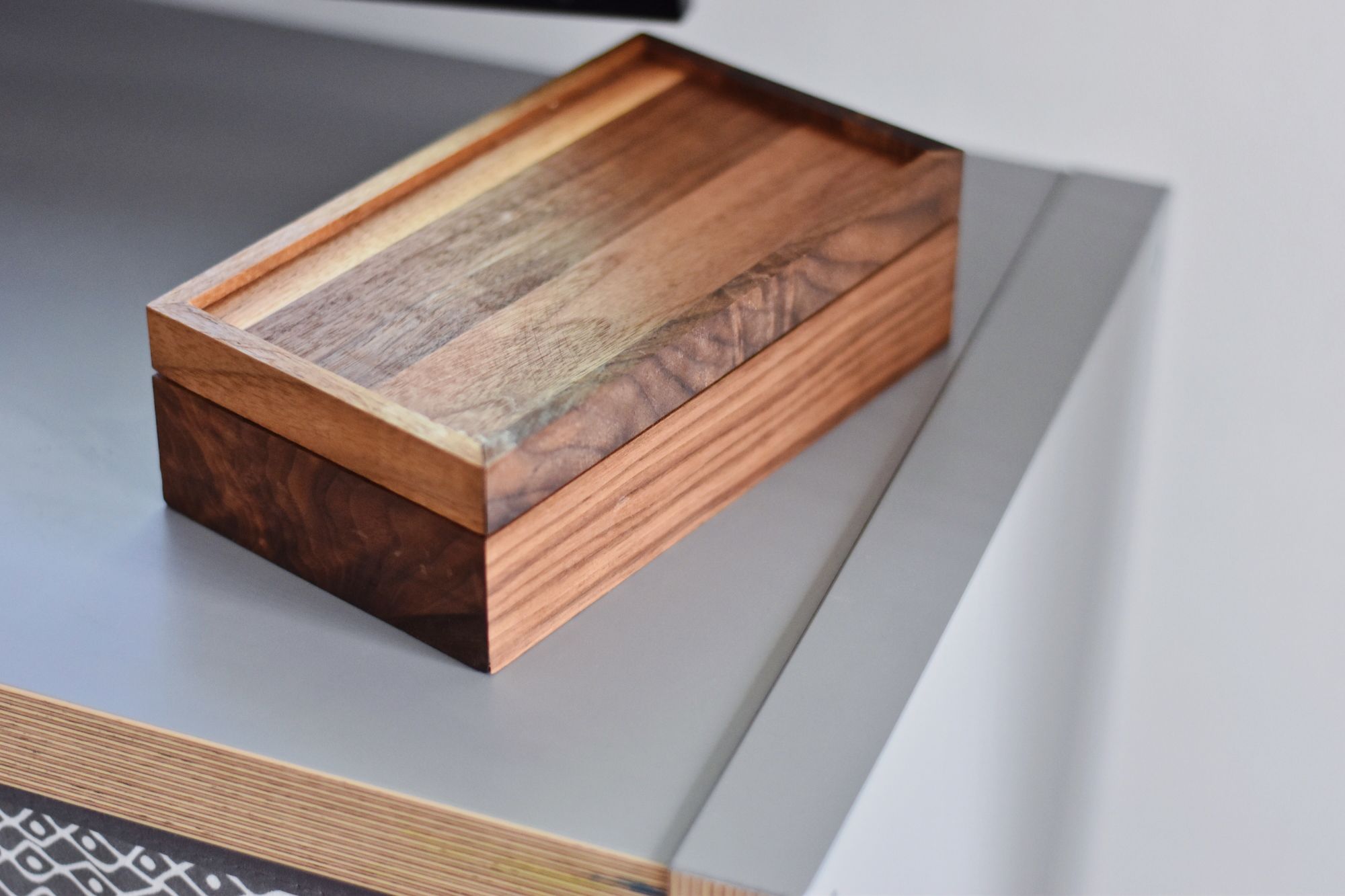
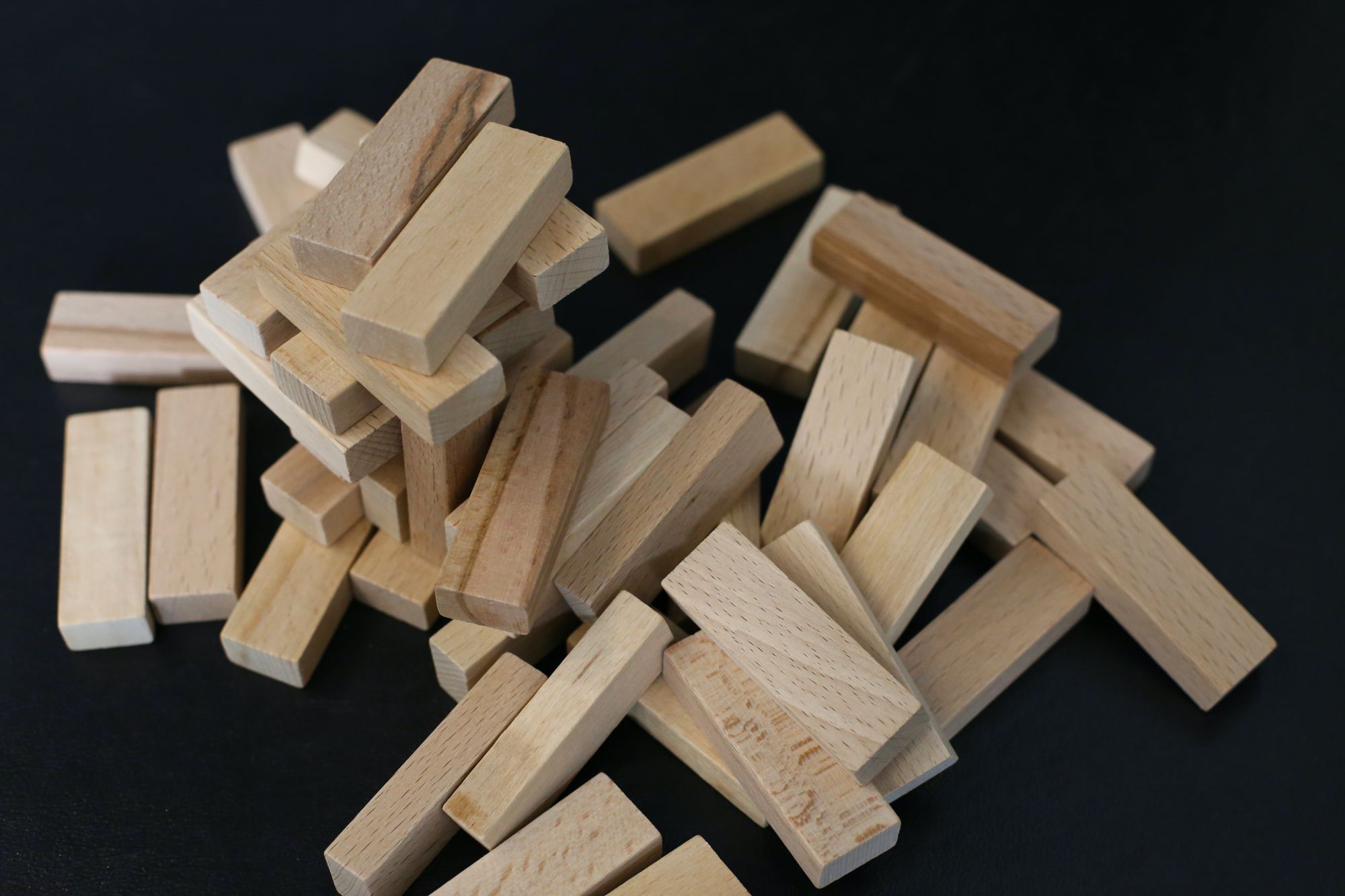
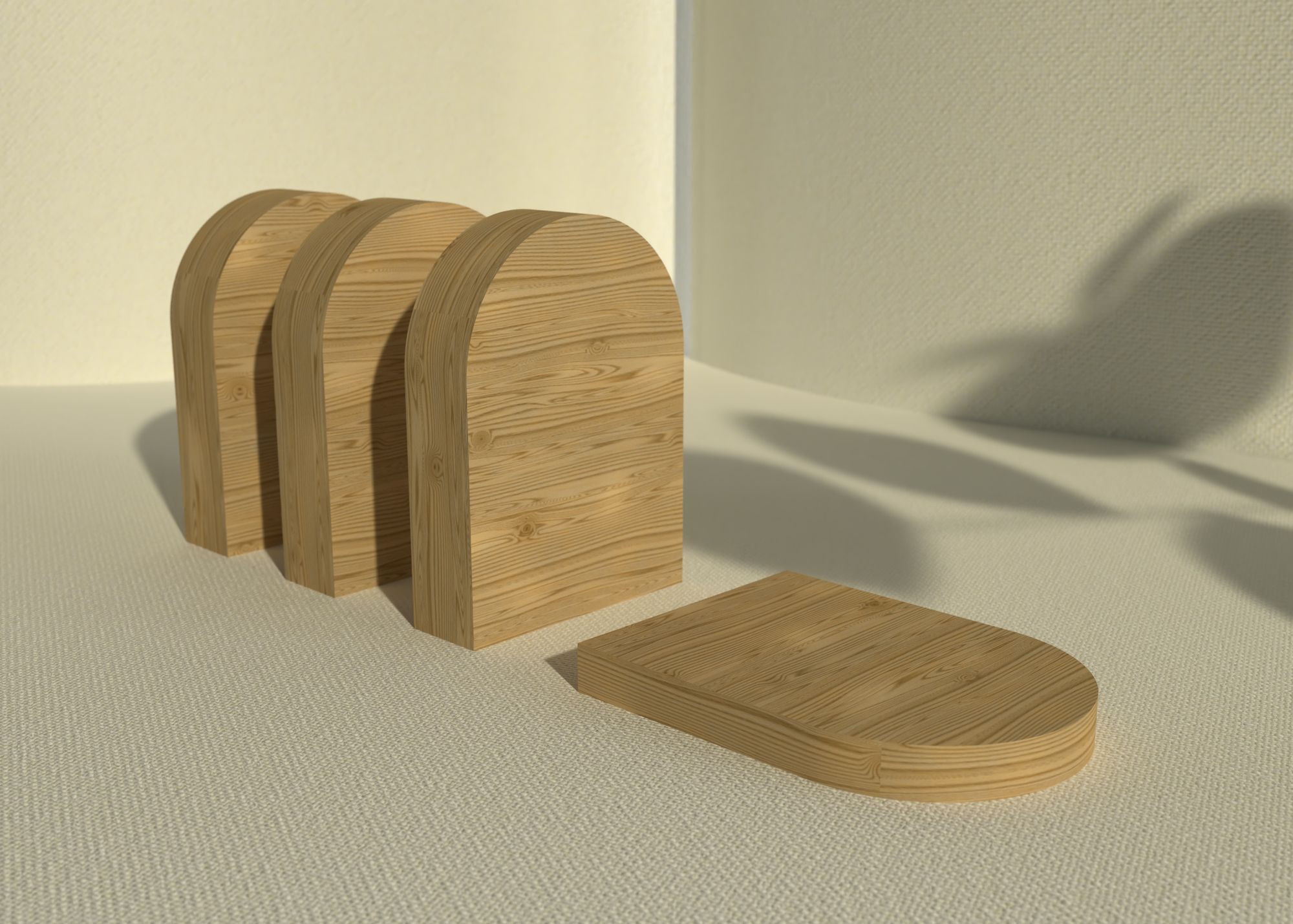
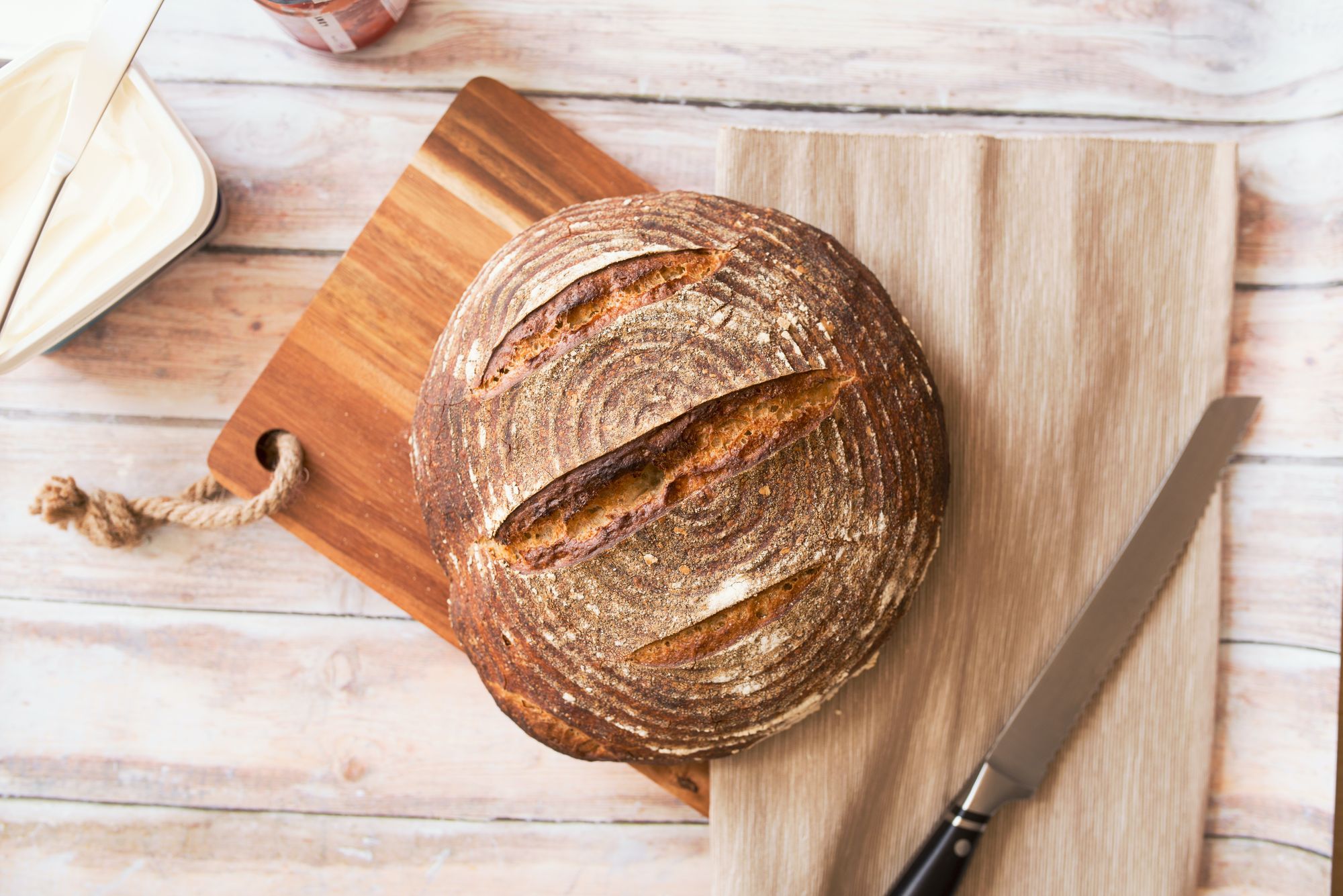