The wood industry is facing challenges to reduce waste and increase efficiency to meet the growing demand for sustainable and cost-effective products. Inefficient processes, lack of automation, and outdated technology can lead to increased waste and reduced productivity.
The same report states that the wood products industry has the potential to reduce waste by up to 25% through improved efficiency and technology.
Implementing best practices to reduce waste and maximize efficiency is essential for the success and sustainability of wood production processes. Companies can benefit from adopting lean manufacturing principles, implementing automation and technology, and improving inventory management and employee training and safety.
Additionally, an efficient supply chain plays a crucial role in reducing waste and maximizing efficiency. By streamlining the entire process from sourcing materials to delivering finished products, companies can minimize waste and optimize production.
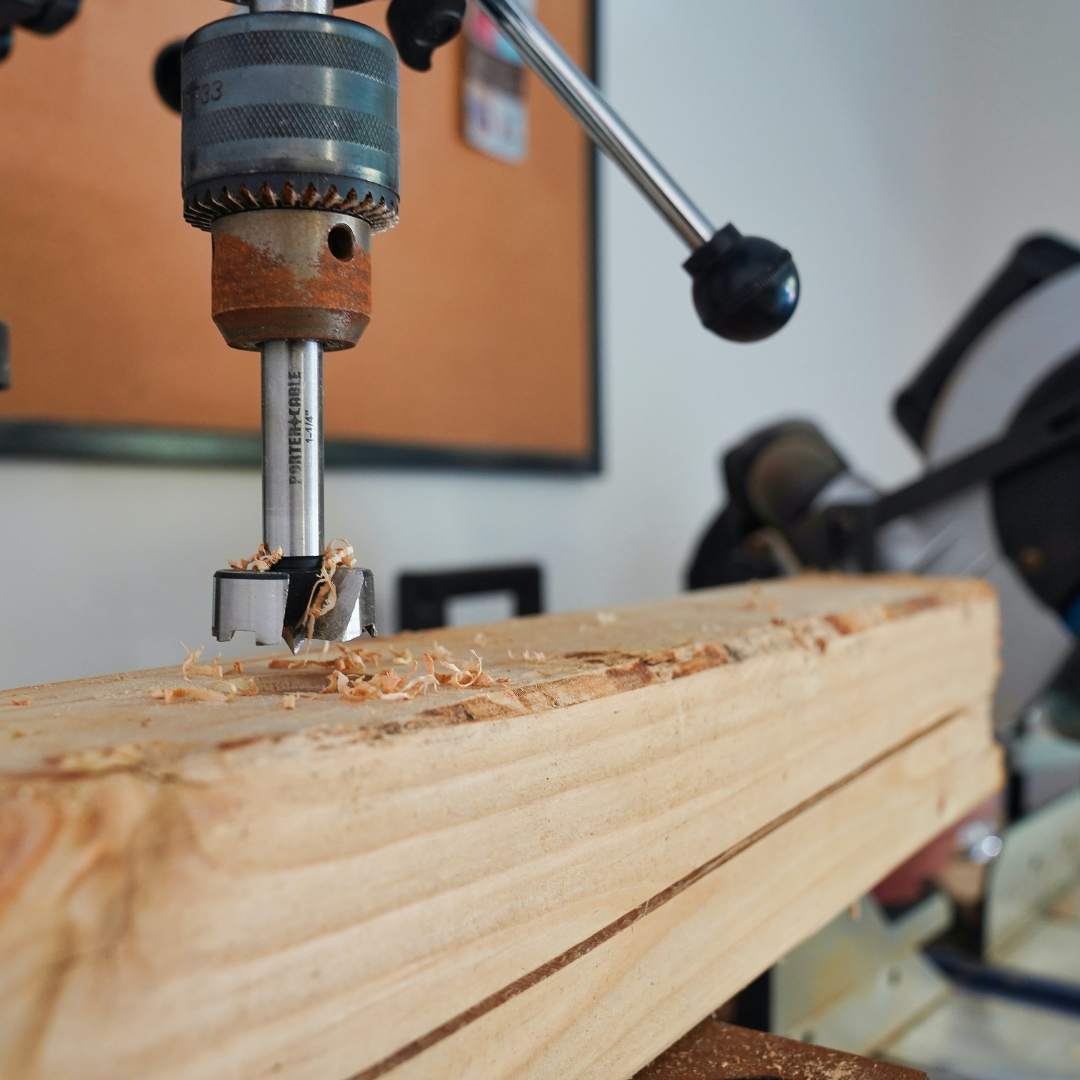
In this article, we will explore various best practices and examples of companies that have successfully reduced waste and maximized efficiency in their wood production processes.
- Importance of Reducing Waste and Maximizing Efficiency in Wood Production
- Rise of Sustainability and Environmental Responsibility in Modern Manufacturing Processes
- Assessing Current Processes
- Lean Manufacturing Principles
- Automation and Technology
- Inventory Management
- Employee Training and Safety
- Continuous Improvement
- Efficient Supply Chain
- Case Studies
- How can Deskera Help You?
- Key Takeaways
- Related Articles
Importance of Reducing Waste and Maximizing Efficiency in Wood Production
Reducing waste and maximizing efficiency in wood production is crucial for several reasons.
Firstly, it can lead to significant cost savings for companies in the wood products industry. By reducing waste, companies can save money on raw materials and disposal costs, as well as increase their productivity and profitability through more efficient use of resources.
Secondly, reducing waste is also beneficial for the environment. Wood waste can contribute to deforestation, air pollution, and greenhouse gas emissions. By minimizing waste and maximizing efficiency, companies can reduce their impact on the environment and promote sustainability.
Additionally, improving efficiency in wood production can lead to faster turnaround times and increased customer satisfaction. Customers expect products to be produced quickly and efficiently, and a streamlined production process can help companies meet those demands.
Overall, reducing waste and maximizing efficiency in wood production is important for economic, environmental, and customer satisfaction reasons.
Rise of Sustainability and Environmental Responsibility in Modern Manufacturing Processes
In recent years, there has been a growing emphasis on sustainability and environmental responsibility in modern manufacturing processes, including those in the wood products industry. As consumers become more aware of the impact of manufacturing on the environment, there is a greater demand for sustainable and eco-friendly products.
Manufacturers are responding to this demand by adopting more sustainable practices, such as using renewable resources, reducing waste, and minimizing their carbon footprint. This shift towards sustainability is also driven by government regulations and industry standards, which are pushing companies to reduce their environmental impact.
In the wood products industry specifically, there has been a move towards using certified sustainable wood sources and reducing waste through recycling and repurposing. Many companies are also exploring alternative materials and production methods to further reduce their impact on the environment.
The rise of sustainability and environmental responsibility in modern manufacturing processes is a positive step towards a more sustainable future. By adopting more eco-friendly practices, manufacturers can not only meet consumer demand but also contribute to a healthier planet.
Assessing Current Processes
Assessing current wood production processes is crucial to identify inefficiencies, bottlenecks, and areas for improvement, which can help streamline operations, enhance productivity, and reduce costs. By examining every aspect of the manufacturing process, from the sourcing of raw materials to the final product, companies can identify potential issues and develop targeted solutions to improve their production processes.
Through this approach, companies can identify inefficiencies, reduce waste, and improve overall performance, leading to increased profitability and competitiveness in the marketplace. Therefore, conducting a comprehensive assessment of current processes is a crucial step for companies seeking to optimize their wood production processes.
Need for a Thorough Assessment of Current Processes to Identify Inefficiencies and Areas for Improvement
A thorough assessment of current wood production processes is critical to identify inefficiencies, bottlenecks, and areas for improvement. By conducting a comprehensive review of each step of the manufacturing process, from raw material sourcing to product delivery, companies can identify areas where resources are being wasted, costs are being inflated, and productivity is being hindered.
This information can then be used to develop targeted solutions that optimize the production process, reduce waste, and enhance overall efficiency. Without a thorough assessment, companies risk overlooking crucial inefficiencies and failing to capitalize on opportunities for improvement.
Thus, a detailed analysis of current processes is an essential step for companies seeking to optimize their wood production processes and remain competitive in the industry.
Tools and Methodologies for Assessing Current Processes, such as Process Mapping and Value Stream Mapping
To assess the current processes in wood production, various tools and methodologies can be used to identify inefficiencies and areas for improvement.
Two popular techniques are process mapping and value stream mapping. Process mapping involves creating a visual representation of the current production process, including the steps, inputs, outputs, and any bottlenecks or inefficiencies. This helps identify areas where processes can be streamlined or eliminated.
Value stream mapping is a more in-depth process that maps the entire value stream of a product from raw materials to delivery to the customer. This helps identify waste and inefficiencies in the entire process, including material flow, information flow, and people flow.
By using these tools, wood production companies can identify opportunities to optimize their processes and improve overall efficiency.
Lean Manufacturing Principles
Implementing Lean Manufacturing Principles is crucial for reducing waste and maximizing efficiency in wood production processes, as it promotes continuous improvement, waste reduction, and efficient resource utilization. By adopting lean methodologies, wood manufacturers can streamline their processes, improve productivity, reduce lead times, and enhance customer satisfaction.
The implementation of lean manufacturing principles requires a holistic approach, including employee involvement, supplier partnerships, and continuous monitoring and improvement. The application of lean principles in wood production involves identifying areas of waste and inefficiency, implementing standardized work procedures, establishing visual management systems, and fostering a culture of continuous improvement.
By embracing lean manufacturing principles, wood manufacturers can enhance their competitiveness, increase profitability, and achieve long-term sustainability.
Overview of Lean Manufacturing Principles and their Applicability to Wood Production Processes
Lean Manufacturing Principles can be applied to wood production processes to help reduce waste, increase efficiency, and optimize production. The principles of lean manufacturing, such as Just-in-Time (JIT) production, Total Productive Maintenance (TPM), and Kaizen, focus on identifying and eliminating waste in all its forms, including excess inventory, overproduction, waiting time, defects, and unnecessary processing.
By implementing these principles, wood production companies can improve their overall production processes, reduce lead times, and increase customer satisfaction.
JIT production is particularly relevant for wood production processes as it emphasizes the need for a smooth flow of materials and components through the production process. This can help to reduce inventory and minimize the risk of stockpiling raw materials or unfinished products.
Similarly, TPM principles can be used to optimize equipment maintenance and reduce the likelihood of breakdowns and downtime, which can impact production and increase costs. Kaizen, which is focused on continuous improvement, can help to drive efficiency gains and ensure that processes are continually refined and improved.
Automation and Technology
Automation and technology have become essential components in modern manufacturing.
The use of automation and technology has been found to significantly improve efficiency and productivity while reducing costs and waste. In wood production, automation and technology can be utilized in various ways, such as improving the accuracy of cutting and processing wood, reducing material waste, and increasing safety for workers.
Adopting automation and technology in wood production processes can also enhance the quality of finished products and help companies meet increasing demands from consumers for sustainable and environmentally responsible practices.
However, it is important to carefully assess the cost-benefit of implementing automation and technology, as well as ensuring that workers are adequately trained to operate and maintain these systems.
Role of Automation and Technology in Reducing Waste and Maximizing Efficiency in Wood Production
Automation and technology play a crucial role in reducing waste and maximizing efficiency in wood production processes. By automating repetitive and labor-intensive tasks, companies can increase production rates and reduce the likelihood of errors.
Technology, such as sensors and monitoring systems, can help identify areas of inefficiency and waste, allowing for targeted improvements. Additionally, the use of advanced software systems, such as MRP and ERP, can optimize supply chain and inventory management, further reducing waste and improving efficiency. By adopting these technologies and integrating them into existing production processes, companies can achieve significant improvements in productivity, quality, and sustainability.
However, it is important to note that the implementation of automation and technology should be balanced with appropriate training and safety measures to ensure the well-being of employees and the continued success of the production process.
Examples of Technologies that Can Be Used for Automation
CNC machines and robotic systems are some examples of technologies that can be used for automation in wood production. CNC machines can be programmed to perform precise cuts, drilling, and shaping of wood materials, while robotic systems can be used for tasks such as material handling and assembly.
Other examples of technologies that can be used for automation in wood production include laser cutters, computer-aided design (CAD) software, and automated material handling systems. These technologies can help reduce waste, improve accuracy, and increase production speed, ultimately leading to more efficient wood production processes.
It is worth noting that while automation and technology can bring significant benefits to wood production processes, it is important to carefully consider the costs and potential risks associated with implementing these systems. Proper training and maintenance are also crucial to ensure the safe and effective operation of these technologies.
Inventory Management
Inventory management is a crucial aspect of the manufacturing process, including wood production. It refers to the process of overseeing the ordering, storage, and use of materials and products within an organization. Efficient inventory management helps to ensure that the company has the necessary materials and products to meet customer demand while minimizing costs associated with excess inventory or stockouts.
In wood production, proper inventory management is particularly important due to the nature of the raw materials involved. Wood is a natural resource, and the availability and quality of wood can vary depending on factors such as weather conditions, harvesting practices, and transportation issues.
Efficient inventory management helps wood manufacturers to ensure that they have sufficient wood supplies to meet production demands, reduce waste and spoilage, and minimize the risk of stockouts that can lead to production delays.
Effective inventory management involves the use of a variety of tools and techniques, such as demand forecasting, safety stock management, and just-in-time (JIT) inventory management. These methods help to ensure that wood manufacturers have the right materials and products available when they need them while minimizing costs and reducing waste.
With the help of modern inventory management tools and technologies, wood manufacturers can optimize their inventory management processes to achieve maximum efficiency, productivity, and profitability.
Importance of Efficient Inventory Management in Reducing Waste and Maximizing Efficiency in Wood Production
Efficient inventory management is crucial for the success of any manufacturing process, including wood production. Excessive inventory can result in increased storage costs and the possibility of damage or obsolescence. On the other hand, insufficient inventory can lead to production delays, lost sales, and decreased customer satisfaction. Therefore, it is important to maintain an optimal level of inventory to meet production demands and customer needs.
Efficient inventory management can also help reduce waste and maximize efficiency in wood production. By implementing lean manufacturing principles, manufacturers can identify areas of waste in their inventory management processes, such as overproduction, excess inventory, and unnecessary processing steps. By eliminating or minimizing these wasteful activities, manufacturers can reduce costs, improve efficiency, and enhance customer satisfaction.
Moreover, effective inventory management can lead to better production planning and scheduling, which can minimize idle time and increase machine utilization. By accurately tracking inventory levels and demand forecasts, manufacturers can optimize their production schedules and avoid the risk of stockouts or overproduction.
In summary, efficient inventory management is essential for reducing waste and maximizing efficiency in wood production processes. By implementing best practices in inventory management, manufacturers can reduce costs, improve production planning and scheduling, and enhance customer satisfaction.
Best Practices for Inventory Management
Effective inventory management is critical for ensuring smooth and efficient wood production processes while reducing waste and costs. Best practices for inventory management include just-in-time inventory and vendor management programs.
Just-in-time inventory involves minimizing the inventory to the minimum level required to meet production needs. This helps to reduce storage costs, minimize waste from obsolescence, and improve cash flow. It is important to have a reliable supplier network and production planning system in place to ensure that materials are available when needed.
Vendor management programs involve developing long-term relationships with suppliers and managing their performance to ensure reliable and high-quality delivery of materials. This can include negotiating contracts and service level agreements, monitoring supplier performance, and collaborating with suppliers to identify opportunities for improvement.
Other best practices for inventory management include implementing barcode or RFID tracking systems to monitor inventory levels and reduce errors, conducting regular audits to identify discrepancies, and using data analytics to forecast demand and optimize inventory levels.
By implementing these best practices, wood production companies can improve their inventory management processes, reduce waste and costs, and enhance overall efficiency.
Employee Training and Safety
Employee training and safety are crucial components of any manufacturing process, including wood production. It is important to ensure that employees are properly trained to operate equipment, handle materials, and follow safety protocols to prevent accidents and injuries. Training programs should be designed to provide employees with the knowledge and skills they need to perform their jobs safely and effectively.
In addition to training, it is important to establish and enforce safety protocols, such as using personal protective equipment (PPE), conducting regular safety inspections, and providing ongoing safety training. Proper safety measures not only protect employees from harm, but also help to prevent equipment damage, production delays, and other issues that can result in waste and inefficiency.
Effective employee training and safety programs also promote a positive workplace culture that values employee well-being and helps to build trust between management and workers. This can lead to increased job satisfaction and productivity, as well as reduced turnover and absenteeism.
Overall, employee training and safety are critical components of a successful wood production process. By investing in these areas, companies can create a safe and efficient work environment that supports sustainable business practices and maximizes profitability.
Best Practices for Employee Training and Safety
Implementing best practices for employee training and safety is essential in reducing waste and maximizing efficiency in wood production. Regular safety training sessions for employees can improve awareness of workplace hazards and how to prevent accidents, leading to fewer work-related injuries and less downtime.
Furthermore, ergonomics assessments can help identify work areas that may cause fatigue or injury, allowing for adjustments to be made to improve employee comfort and productivity.
Other best practices for employee training and safety include providing proper personal protective equipment, conducting regular equipment maintenance and inspections, and having emergency response plans in place. Encouraging employees to report unsafe conditions and near-miss incidents can also help identify potential hazards and prevent accidents before they occur.
By implementing these best practices, companies can create a culture of safety in the workplace, resulting in fewer accidents, increased productivity, and improved employee morale. Investing in employee training and safety not only benefits the workers but also contributes to the overall success and sustainability of the wood production process.
Continuous Improvement
Continuous improvement is a crucial aspect of modern manufacturing that helps companies stay competitive in today's dynamic business environment. The pursuit of continuous improvement enables companies to identify and eliminate inefficiencies, optimize processes, and enhance product quality, resulting in increased productivity and profitability.
This section aims to explore the concept of continuous improvement in wood production processes and its impact on waste reduction and efficiency maximization.
Furthermore, the study will examine the role of technology and automation in continuous improvement and how they can facilitate the identification and elimination of inefficiencies.
Finally, the section will explore the benefits of implementing a continuous improvement program in wood production processes and how it can lead to increased customer satisfaction and profitability. Ultimately, it seeks to highlight the significance of continuous improvement in wood production processes and the critical role it plays in ensuring the sustainability and competitiveness of wood manufacturers in today's market.
Need for Continuous Improvement in Wood Production Processes to Maintain Efficiency and Sustainability
In today's competitive and rapidly evolving business environment, it is crucial for wood production companies to continuously improve their processes to maintain efficiency and sustainability.
Continuous improvement is a systematic approach that involves constantly evaluating and enhancing the performance of the production process. This approach can help companies reduce waste, increase productivity, and improve product quality.
With the increasing focus on sustainability and environmental responsibility, continuous improvement has become even more critical as it enables companies to reduce their carbon footprint and achieve their sustainability goals.
Wood production processes involve various stages, including harvesting, sawing, drying, and finishing. Each stage presents an opportunity to optimize the process and reduce waste. For example, by improving sawing techniques, companies can minimize the amount of wood waste generated during the process.
Continuous improvement can also enhance worker safety by identifying and mitigating potential hazards in the production process.
To remain competitive in the wood production industry, companies must adopt a continuous improvement mindset and seek out opportunities to optimize their processes. This requires a commitment to ongoing training, process evaluation, and investment in technology and automation.
By implementing continuous improvement, wood production companies can increase their efficiency, reduce waste, and achieve long-term sustainability.
Ways to Continually Improve Processes
Implementing continuous improvement in wood production processes is crucial for maintaining efficiency and sustainability. One way to achieve this is through a Kaizen program, which involves identifying inefficiencies and making small, incremental improvements to eliminate waste and streamline processes. Another way is to conduct regular performance evaluations to identify areas for improvement and implement solutions to optimize processes.
Process automation and technology can also aid in continuous improvement efforts, allowing for increased efficiency and productivity. Regular training and development of employees can also lead to continuous improvement by keeping workers up-to-date on best practices and new technologies.
Furthermore, incorporating Lean Manufacturing principles, such as value stream mapping and 5S methodology, can also help to identify inefficiencies and improve processes. By continually analyzing and improving production processes, companies can reduce waste, increase productivity, and improve their bottom line.
Overall, the need for continuous improvement in wood production processes is essential for companies to remain competitive in a constantly evolving market. By continually assessing and improving processes, companies can optimize operations, reduce costs, and increase overall sustainability.
Efficient Supply Chain
An efficient supply chain is a critical component of any manufacturing process, including wood production. It involves the movement of raw materials and finished goods from suppliers to the manufacturing facility and then to the end customers.
An effective supply chain management system ensures that the right materials are available at the right time, at the right cost, and in the right quantity to support the manufacturing process. Efficient supply chain management reduces waste and improves overall efficiency by reducing lead times, minimizing inventory costs, and optimizing transportation.
Effective supply chain management practices in wood production include working closely with suppliers to ensure timely delivery of materials, developing strong relationships with transportation providers to ensure on-time delivery of finished products, and implementing technology solutions such as warehouse management systems (WMS) to streamline inventory management.
Additionally, adopting a lean manufacturing philosophy and utilizing just-in-time inventory management can help to optimize supply chain efficiency.
Role of An Efficient Supply Chain in Reducing Waste and Maximizing Efficiency in Wood Production
An efficient supply chain plays a crucial role in reducing waste and maximizing efficiency in wood production processes. The supply chain includes all the steps involved in sourcing, manufacturing, and delivering raw materials and finished products to customers.
Inefficient supply chain processes can lead to delays, increased costs, and waste, which can have a negative impact on the overall efficiency of the production process. An efficient supply chain helps to ensure that the right materials are available when needed, and that finished products are delivered to customers in a timely manner.
This can help to reduce the amount of waste that is generated, as well as improve overall efficiency by reducing the time and resources needed to complete production processes. Additionally, an efficient supply chain can help to improve sustainability by reducing the environmental impact of transportation and reducing the amount of waste that is generated.
By implementing best practices such as just-in-time inventory management and vendor management programs, wood production companies can optimize their supply chain and improve overall efficiency and sustainability.
Best Practices for Efficient Supply Chain Management
Effective supply chain management is essential for reducing waste and maximizing efficiency in wood production processes. A well-designed supply chain can minimize the time, cost, and resources needed to move raw materials and finished products through the production process. This, in turn, can reduce the risk of waste and improve the overall efficiency of the production process.
To ensure an efficient supply chain, best practices include establishing strong relationships with suppliers to ensure timely and reliable delivery of materials, implementing just-in-time inventory systems to minimize inventory costs and waste, and leveraging technology such as automated inventory tracking systems to improve accuracy and efficiency.
Additionally, supply chain managers should regularly analyze their processes to identify areas for improvement and optimization.
Other best practices for efficient supply chain management include creating a clear and effective communication channel between all parties involved in the supply chain, implementing standardized processes and procedures to minimize errors and inefficiencies, and continually evaluating and refining the supply chain strategy to adapt to changes in demand, market conditions, and other external factors.
Case Studies
Case studies provide a practical and tangible way of understanding the concepts and principles discussed in the context of real-world examples. In the field of wood production, case studies can showcase the successful implementation of strategies and practices aimed at reducing waste and maximizing efficiency.
By examining specific companies and their processes, we can gain insights into what works, what doesn't, and what can be improved upon. Additionally, case studies can demonstrate the benefits of adopting a sustainable and environmentally responsible approach to manufacturing.
In this section, we will explore several case studies that highlight the importance of reducing waste and maximizing efficiency in wood production, and examine the strategies and practices that have contributed to their success.
Examples of Companies in the Wood Production Industry that have Successfully Reduced Waste and Maximized Efficiency
here are some examples of companies in the wood production industry that have successfully reduced waste and maximized efficiency:
- Weyerhaeuser: This company has implemented a lean manufacturing program across all of its operations, resulting in significant improvements in efficiency and waste reduction.
- West Fraser Timber: Through the implementation of technology such as laser scanners and automation, West Fraser Timber has been able to increase efficiency and reduce waste in their production processes.
- Georgia-Pacific: This company has implemented a closed-loop manufacturing system, where waste from one process is used as a raw material for another process, resulting in significant waste reduction.
- Boise Cascade: By implementing a just-in-time inventory system and optimizing their production processes through lean principles, Boise Cascade has been able to reduce waste and increase efficiency.
- Canfor: This company has implemented a program called Canfor Optimization, which uses technology to optimize production processes and reduce waste.
How can Deskera Help You?
Deskera ERP and MRP systems help you to keep your business units organized. The system's primary functions are as follows:
- Keep track of your raw materials and final items inventories
- Control production schedules and routings
- Keep a bill of materials
- Produce thorough reports
- Make your own dashboards
Deskera's integrated financial planning tools enable investors to better plan and track their investments. It can assist investors in making faster and more accurate decisions.
Deskera Books allows you to better manage your accounts and finances. Maintain good accounting practices by automating tasks like billing, invoicing, and payment processing.
Deskera CRM is a powerful solution that manages your sales and helps you close deals quickly. It not only enables you to perform critical tasks like lead generation via email, but it also gives you a comprehensive view of your sales funnel.
Deskera People is a straightforward tool for centralizing your human resource management functions.
Key Takeaways
- Reducing waste and maximizing efficiency is crucial for sustainable and profitable wood production.
- Assessing current processes, implementing lean manufacturing principles, and using automation and technology can help reduce waste and maximize efficiency.
- Process mapping and value stream mapping are effective tools for assessing current processes.
- Automation technologies, such as CNC machines and robotic systems, can help improve efficiency and reduce waste.
- Inventory management techniques, such as just-in-time inventory and vendor management programs, can help reduce waste and improve efficiency.
- Employee training and safety are critical components of reducing waste and maximizing efficiency.
- Continuous improvement programs, such as Kaizen, can help identify inefficiencies and areas for improvement.
- Implementing an efficient supply chain with strong supplier relationships and just-in-time inventory systems can help reduce waste and improve efficiency.
- Case studies of successful companies, such as IKEA and Weyerhaeuser, demonstrate the effectiveness of these methods in reducing waste and maximizing efficiency.
Related Articles
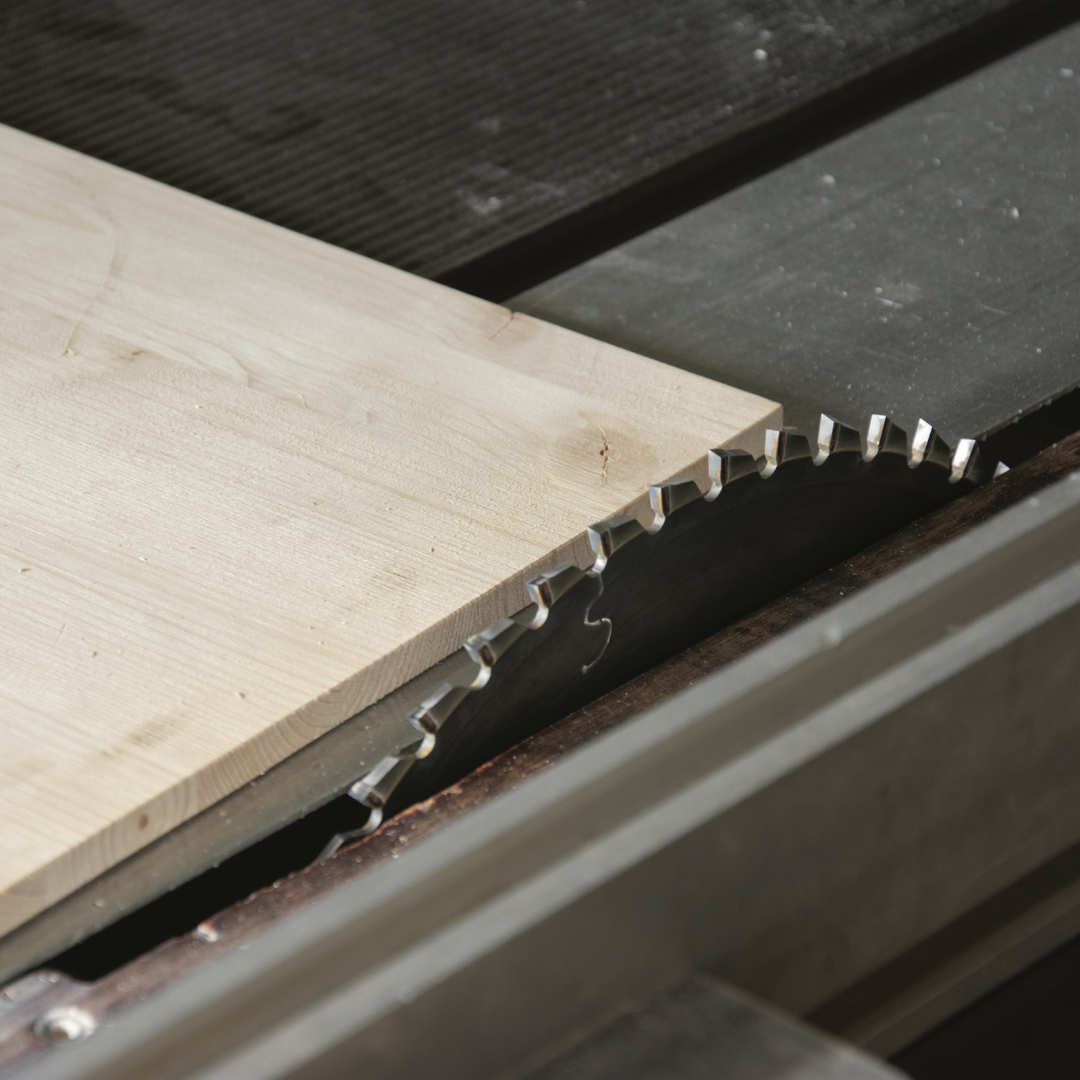
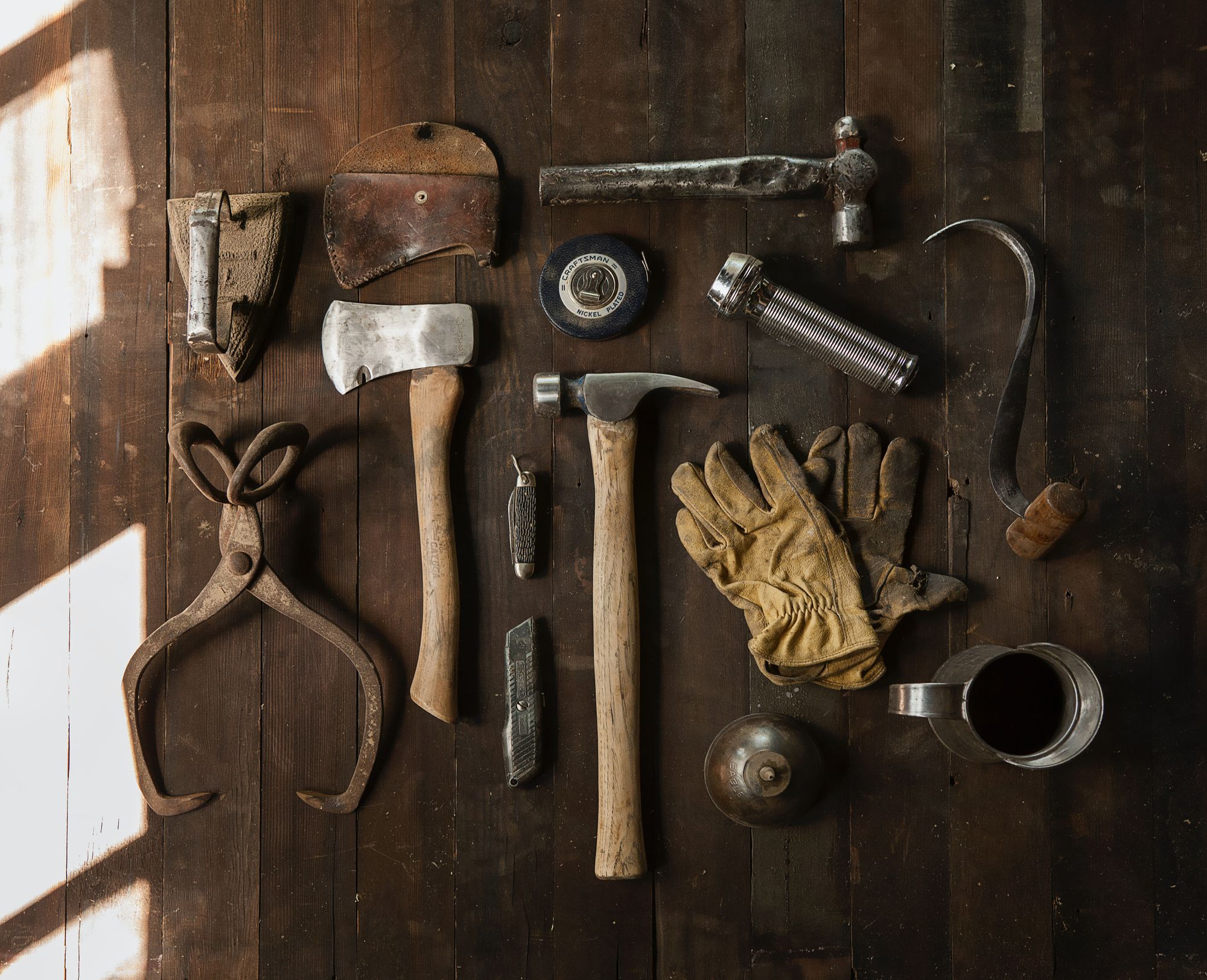
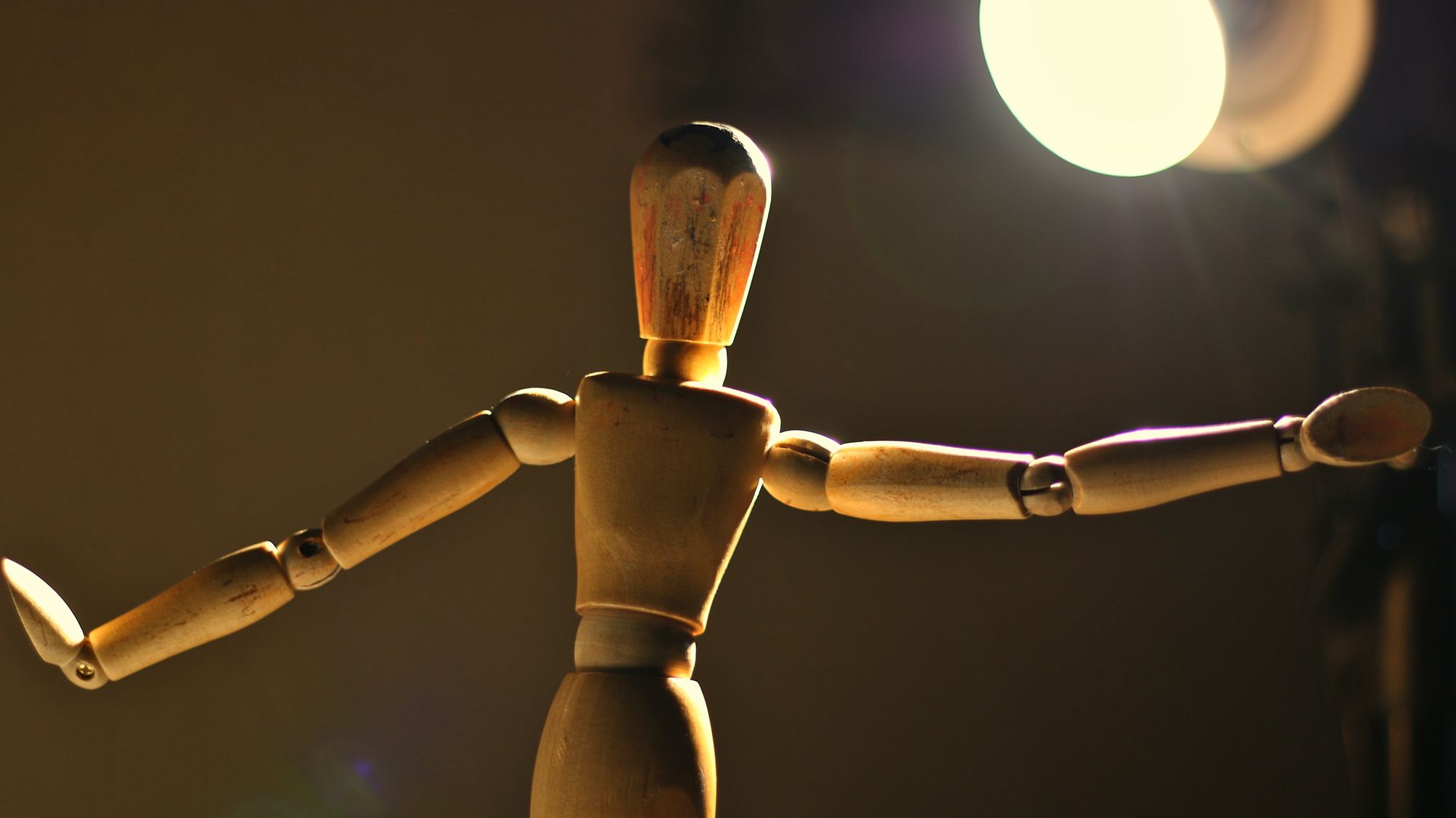