The most popular operations management software categories are financial, supply chain, and CRM.
In terms of technology, cloud-based solutions are becoming increasingly popular. Recent reports showed over 50% of respondents use a cloud-based system.
Operations management is the process of managing the operations of an organization. It aims to ensure the efficient use of resources to produce high-quality products. Operations management involves analyzing and managing processes and improving customer service. It is a vital part of any organization and is key to success.
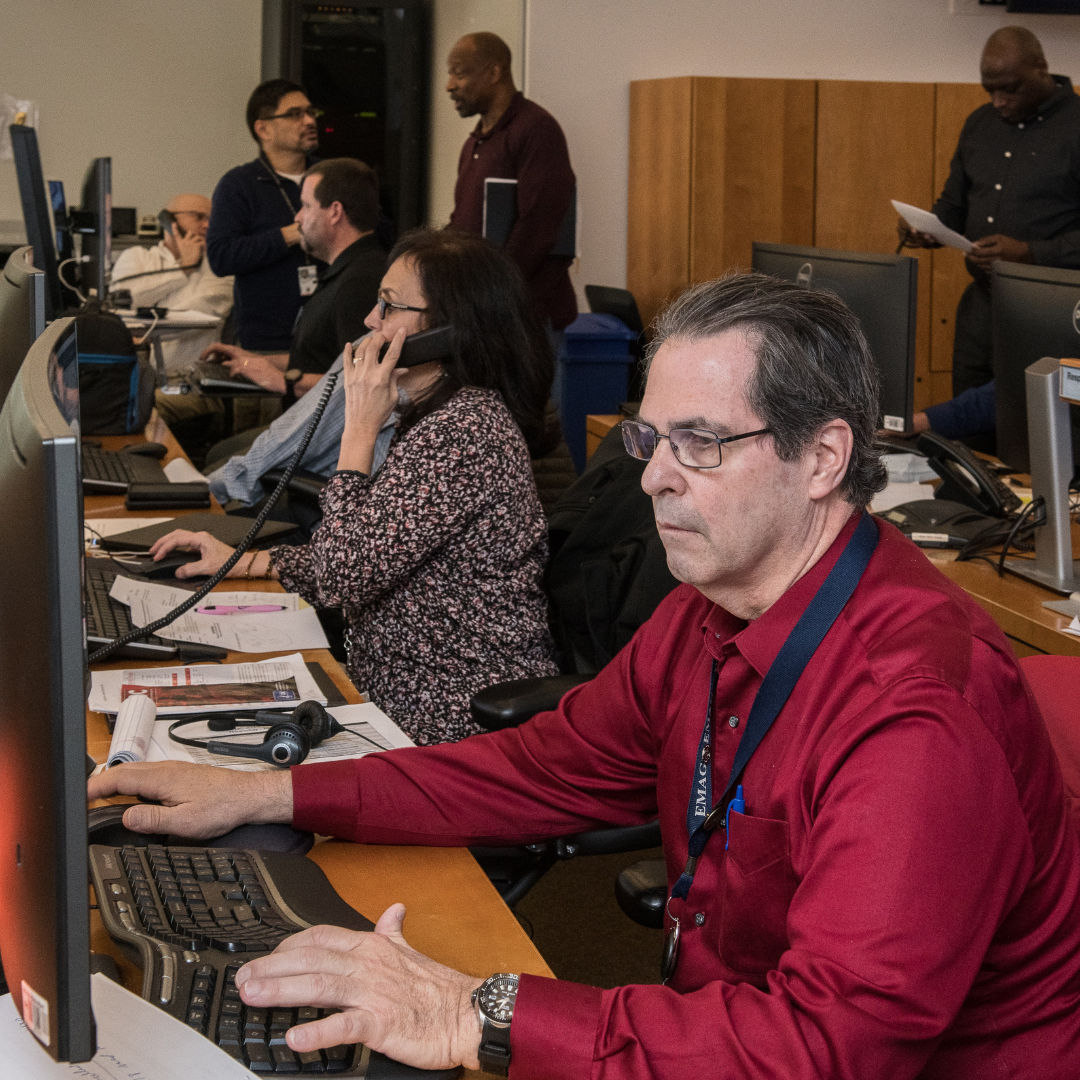
Additionally, operations management users are increasingly turning to automation. AI-assisted systems are also gaining a stronger foothold. These systems help them streamline processes and save time. Finally, the report showed that the leading operations management trend uses machine learning. This has aided to gain deeper insights into operations data.
Maintaining the competency of the products and services is of utmost importance. But how can you achieve it?
This article will provide an overview of operations management, its importance, and how it can be used to maximize efficiency.
- What is Operations Management (OM)?
- What are the Types of Operations Management?
- 4 Vs of Operations Management
- What are some Systems of Operations Management?
- What is the Role of Operations Management (OM)?
- Importance of Operations Management
- 10 Decisions of Operations Management
- Operations Management vs. Supply Chain Management
- 4 Operations Management Challenges
- Operations Management Best Practices
- What do Operations Managers Do?
- Ideal Skills of an Operations Manager
- Responsibilities in Operations Management
- What are some Examples of Operations Management?
- How does Operations Management Impact Customer Experience?
- How are Operations Management and ERP Related?
- Benefits of ERP System in Operations Management
- Conclusion
- How can Deskera Help You?
- Key Takeaways
- Related Articles
What is Operations Management (OM)?
Operations management is the branch of management that oversees the entire production timeline of a service/product. From the input to the finished stage, it includes planning, organizing, and supervising operations.
It also oversees the manufacturing and production processes. Finally, the process ends with the service delivery. This way, it achieves the desired outcome of a high-quality product/service to meet customer demands.
Simply described, operations management serves the following purpose in the administration of business:
- meet objectives
- increase productivity
- optimize profitability
Why is Operations Management the Core of every Business?
Operations management is the core of every business. This is because it is responsible for various core business activities. Production, distribution, and delivery of goods and services are some of those.
It ensures that the business runs efficiently and effectively. It helps the company meet customer needs and regulatory requirements. It is the link between the organization and its customers, suppliers, and employees.
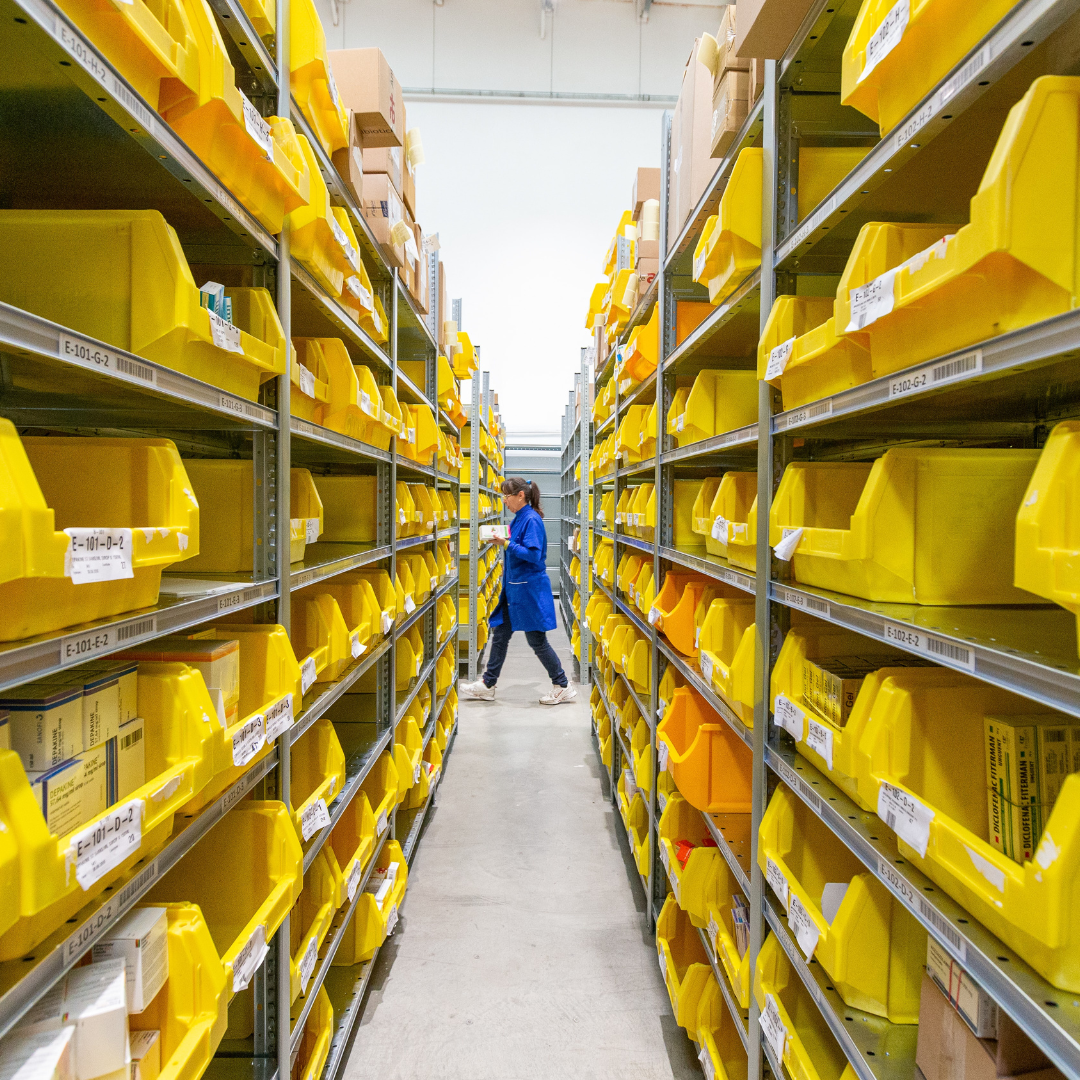
Without efficient operations management, businesses may face multiple difficulties. They would be unable to perform their duties and meet customer demands.
What are the Types of Operations Management (OM)?
There are numerous types of operations management. The role of an operations manager can vary significantly based on the size of the company and the industry. They may have a wide variety of responsibilities or specialize in one area.
Product Design and Development
Product design and development in OM is the process of creating a new product or improving an existing one. This includes research, concept development, design, testing, and production. Finally, it comprises packaging, marketing, and product management.
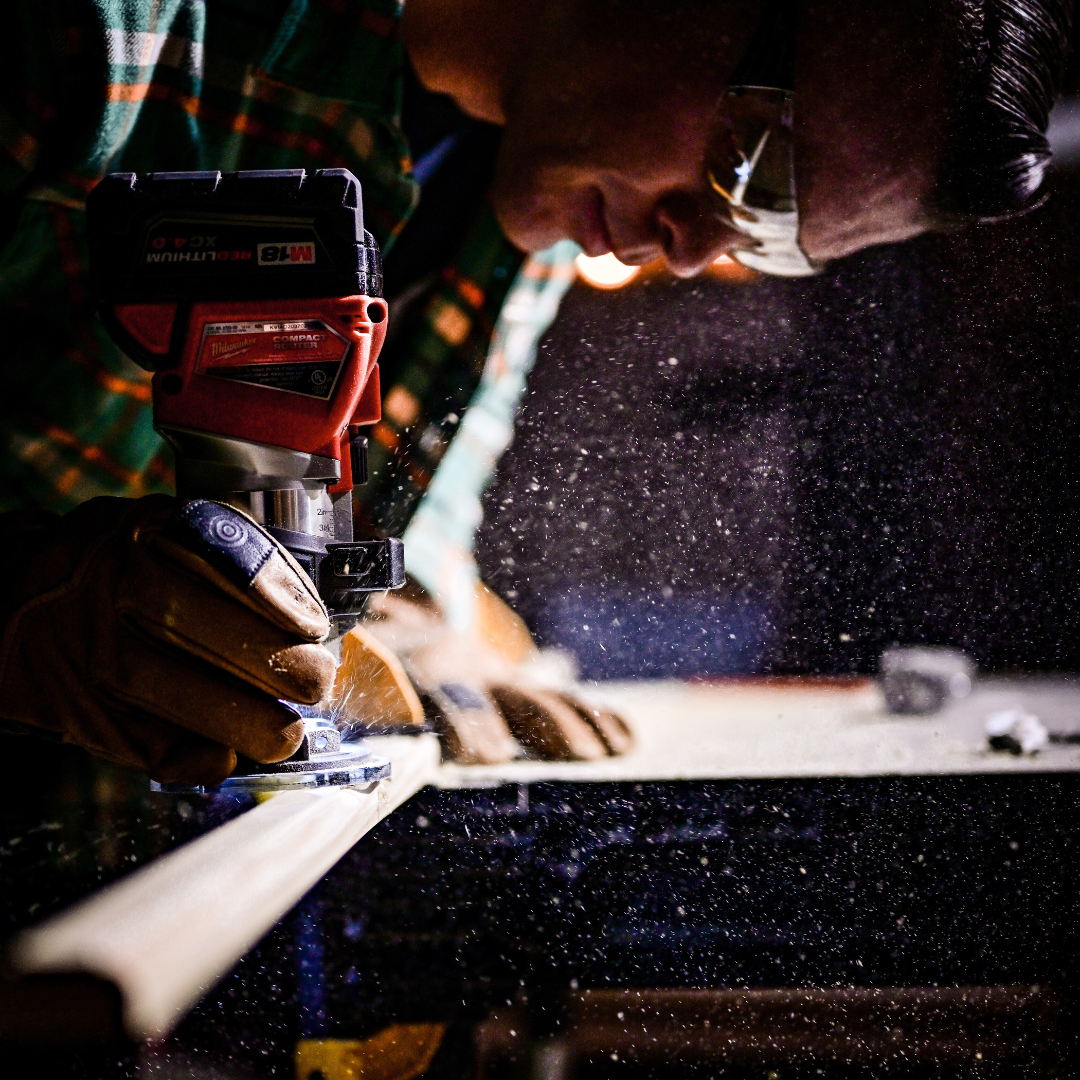
It includes market research, product design, product testing, prototyping, and product launch. The goal of product design and development is to create a product that meets the needs of customers. Also, it must be cost-effective for customers and profitable for the company.
Purchasing and Procurement
It is the process of obtaining goods and services from suppliers for use in an organization. It includes market research, selecting suppliers, and negotiating contracts. This is followed by evaluating bids and selecting the best supplier for a product or service.
This process is essential for ensuring that companies have the resources to produce goods.
Forecasting
This is the process of predicting demand for a product or service based on historical data and current trends. It is used to help businesses plan their operations and production to meet customer demand. It also helps them to minimize waste.
Forecasting helps organizations plan their staffing and inventory levels. Additionally, the companies can plan capital investments to maximize efficiency and profits.
Capacity Planning
This is the process of determining the production capacity. An organization needs it to meet changing demands for its products. It is an integral part of operations management. This is because it aims to keep costs to a minimum and meet customer demand.
Capacity planning involves analyzing current production and identifying future production needs. This is followed by formulating strategies for meeting those needs. Methods may involve increasing capacity through the following:
- Automation
- Hiring additional staff, or
- Investing in new equipment
Quality Management
This type of operations management focuses on the quality of products and services produced by an organization. It involves the identification of customer requirements. Also, it aims to develop quality control plans. Finally, it emphasizes the implementation of quality assurance measures.
Process Management
This type of operations management involves designing and managing processes that create products. It includes the identification of customer needs and the development of efficiency. Further, it highlights the cost-effective methods to meet those needs.
Inventory Management
This type of OM deals with the management of inventories, such as raw materials, finished products, and supplies. It involves the planning, tracking, and control of inventory levels.
Project Management
This type of operations management focuses on the management of projects. These include the planning, scheduling, and execution of tasks associated with the project. It consists of the identification of project goals and the development of project plans. It also monitors project progress.
Supply Chain Management
This type of operations management deals with managing the entire supply chain. It starts from the acquisition of raw materials to the delivery of finished products.
4 Vs of Operations Management
Companies operate their manufacturing processes in various ways. And each has objectives to remain relevant and effective in their respective markets. The four Vs of operations management define a company's core product deliveries.
Let’s take a look at these 4 Vs of operations management.
1. Volume
It refers to the precise number of product units required to meet client demand. This dimension is harmful to businesses that value mass production and high production output. Volume is a major concern for them. However, they must also ensure that the quality of each item meets market standards.
2. Variety
This dimension describes how diverse a company's product portfolio is. The range of goods and services that a company sells is referred to as its variety. Having a diverse product portfolio avoids relying on a single product for success and profitability.
A diverse product range also broadens the company's target audience. It exposes it to new client demographics.
3. Variation
The degree to which external influences affect demand over time is referred to as variation.
Consider your product and its audience to discover how the variation affects your firm. Understand factors that drive your target audience to purchase more or less of your product. Determine what additional elements influence possible production modifications. Take them into account when making development decisions.
4. Visibility
The term relates to a company's image in the marketplace. It also shows how customers perceive its product or service. This component is critical for businesses that depend on marketing to capture the attention of their audience. This includes making certain that all advertising is factual and simple.
Another important part of visibility is providing a good user experience. Is your product simple to comprehend? Can the audience learn about it easily? Is it easily accessible?
Is your product's purchasing process clear and straightforward? Products that are difficult to obtain have fewer consumers.
Modern businesses have implemented more ways for customers to obtain visibility. They consider an internal tracking tool. Or they can simply provide the updated delivery information. Open communication and visibility foster trust. It promotes positive evaluations and encourages customer retention.
What are some Systems of Operations Management?
There are four theories that underpin modern operations management:
Business Process Redesign
Business process redesign (BPR) is the process of assessing and redesigning a company's workflow. It also works on making business processes more adept. BPR's purpose is to assist businesses in restructuring their organizations.
Reconfigurable Manufacturing Systems
These are built to accommodate rapid changes in structure. This is done in terms of both hardware and software. This enables systems to respond quickly to changes in the capacity to continue production. It can also respond to the efficiency with which they function in response to market or fundamental system changes.
Six Sigma
The term is a quality-focused methodology. The term "six" refers to the control limits. These are set at six standard deviations from the mean of the normal distribution. Trending charts, probable defect estimations, and other ratios are tools used in the Six Sigma process.
It is structured using DMAIC roadmap.
D is for Define. This stage is about defining and identifying key issues.
M is for Measure. Gather product data to identify future growth prospects.
A is for Analyze. Conduct a thorough examination of product concerns and identify potential causes.
I is for Improve. Gather data from analysis to develop a plan of action for problem resolution. Put those solutions into action.
C is for Control: Keep an eye on newly installed solutions to ensure a beneficial outcome.
Lean Manufacturing
This is the systematic removal of waste from the production process. Lean manufacturing strives to remove as many unnecessary resource expenditures as feasible.
What is the Role of Operations Management (OM)?
Operations management encompasses various duties, from product development to project management.
- Capacity planning entails determining how many items or services a company can sell or deliver in a certain time period.
- Quality control is often referred to as quality management or quality assurance. It is concerned with monitoring services or goods at each stage of the manufacturing process. It also evaluates service operations for any difficulties or errors.
- Process improvement and optimization entail assessing the steps in a process. It can determine rebuilding the process or reorganizing the efforts to enhance efficacy.
- Operations management is also in charge of high-level strategy and planning.
- Supply chain management entails managing the supply chain process. It includes controlling supply sourcing and manufacturing. It also covers inventory management, sales, and distribution at reasonable rates. As a result, overhead expenses are reduced, and production is more efficient. Also, items are delivered on time.
- Product design/service design entails coming up with fresh ideas. It focuses on developing a service or product that matches the customers’ needs and expectations. Operations management must examine a product's cost efficiency. This ensures that it meets the needs of customers.
Importance of Operations Management
Operations management works as the heart of an organization. The following points will help you understand the significance of operations management.
- Organizations need operations management to run their daily operations smoothly.
- Operations management oversees all processes and deals. This may concern system design, operation, maintenance, and improvement. It also ensures that products and services are produced smoothly and on time. It also helps prepare for unexpected circumstances.
- Operations management supports an organization's reputation. Thus, leading to a favorable effect on its capacity to achieve growth and stability goals. Operations management guarantees that products satisfy quality standards. Fulfilling the requirements of customers is an additional duty here. Thus, delighted consumers repeat purchases and recommend more. This increases brand value and provides a competitive advantage in the market.
- Understanding and refining the processes is part of operations management. Thus, operations management promotes the sale of more products/services. All this happens while lowering costs. Thus, resulting in improved revenues and increased organizational growth.
- Employee productivity is increased when operation management inspires them to do their jobs.
10 Decisions of Operations Management
Many essential and strategic decisions are essential in a company's operations management. These keep things functioning properly and optimized. Thus, an operations manager and team must consider ten important decisions.
Quality Management
Quality management entails making decisions on the status of the offered products. Companies understand that customers have the final say. They are the ones who dictate the quality of the product! Therefore, the decisions made here center around the desires of the client.
Managing quality ensures that every item supplied is in sellable condition. Conducting quality control checks is critical in operations management. It must be accomplished for an efficient manufacturing process.
Goods and Services
This comprises all elements of the product's creation. These include production costs and resource allocation. It also primarily relies on substantial market research and target audience analysis. Thus, making it a decision that goes beyond operations management. All departments and teams should be included in the final decision-making.
Some businesses use product portfolio management at this stage. It helps them to optimize their firm offerings to satisfy market needs.
Location
Companies must establish the most efficient way of transportation in manufacturing. Therefore, location becomes a critical issue. This covers the actual location of the business and production areas. Moreover, it comprises the order in which things move inside production.
An ideal location must be large enough for production, manufacturing, and distribution. The company's location must include enough space for each of these operations. Furthermore, it must offer extra space for inventory and marketing initiatives.
Process and Capacity Design
The tactics utilized in the manufacturing phase of product development are crucial to the process and capacity design. This comprises manufacturing materials, technology, and automation. Besides, it also consists of all elements that ensure smooth processes. Companies should focus on building a coherent production map at this stage.
The process design map describes each stage of the process. It must enlist all required components at each level. Also, the desired outcome must be well-defined.
Human Resources and Defining Roles
Human resources are concerned with ensuring that all corporate employees are happy. Equally important is that they must be well-equipped to do their jobs. Thus, the HR unit must conduct employee evaluations regularly. They could take the help of satisfaction surveys, too.
Employee assessments should be used to discover strengths and deficiencies. Additionally, the HR team can gauge employee performance through this step.
Discovering the main strengths and shortcomings might reveal significant insights. It could be an opportunity to use individuals with specific specializations. Or identify employees who no longer love their current conditions in other production sectors.
Satisfaction surveys also ensure that all team members are happy with their working conditions. The surveys can showcase any issues that need immediate attention.
Layout Design and Strategy
Layout design selections are made in order to optimize all physical resources. This includes identifying the most efficient way to organize desks and machinery. It counts in inventories and ensures employee safety.
The layout is critical in ensuring that the process is efficient and feasible.
Inventory
The primary purpose of the inventory is to establish a well-organized environment for the manufacturing process. Inventory management can help to organize sales orders and SCM operations. Additionally, it takes care of deliveries, purchases, and other activities.
A correct inventory management approach ensures that all necessary resources are available. It also checks if production supplies are accessible.
Supply Chain Management
SCM in terms of operations is accomplished by maintaining continuous contact with stakeholders. It also includes working with suppliers closely. Decisions on sourcing suppliers and who those suppliers should be are included in SCM.
Scheduling
The scheduling decisions are based on the timing of the entire manufacturing process. It also accommodates the timing of the teams involved. This comprises a lot of factors.
- how many items can be manufactured at a given time
- how many personnel are required to achieve quotas
- how production speed may be optimized
These are some of the questions that need to be answered before scheduling. Obtaining these data is reliant on those who are involved in the production process. Those key individuals can provide crucial insight into how production works. They can provide insights into scheduling modifications.
Collecting this data expedites the operation as a whole. Scheduling might also consider whether automation can help with the process.
Maintenance
This step guarantees smooth running operations long after manufacturing has commenced. It includes securing resources when they are required. It also includes performing frequent machinery and workplace inspections. Finally, it keeps accurate tallies of raw materials and finished goods as they are consumed.
Maintenance is a continuous process. Therefore, some companies have established entire maintenance teams. These teams ensure that everything required for production is always accessible.
Operations Management vs. Supply Chain Management
We know that both SCM and OM work closely to eliminate problems. They are both instrumental in streamlining workflow. Yet, there are a few differences between the two. We must learn about them.
There is a most notable distinction between operations management and SCM. Their involvement with both internal and external aspects of manufacturing and distribution.
Operations management focuses heavily on the internal parts of manufacturing. It is primarily concerned with how things operate within the boundaries of the company. It also checks how those aspects affect product development. These include staff satisfaction and company ethics.
Supply chain management is all about how a product moves through production. Particularly when it leaves company premises. A supply chain manager gathers supplies before making and distributing completed products. Whereas an operations manager manages staff and internal inventory.
Another distinction between them is the people with whom they engage. An operations manager is in charge of monitoring everyday operations. They maintain employee well-being at work. A supply chain manager devotes more time to communicating with external stakeholders. These include the suppliers and customers.
Nevertheless, operations and supply chains rely on one another to ensure a smooth production process. Supply chain management provides operations management with the tools to generate a product.
Because the two are so closely related, several businesses seek to combine them. It is an opportunity to save money and improve performance.
4 Operations Management Challenges
There are various problems that operations managers confront. They must plan and implement the production process for simplification. These issues include both internal and external elements. They may affect both everyday corporate operations and future decisions.
- Adaptation to Globalization
Globalization is the process by which products and services are distributed internationally. Globalization is when a corporation functions and sells items on a global scale. With the benefits of globalization comes increased competition for operation managers.
As a company's global target market expands, so do opportunities for international competitors.
Apart from this, there is another issue with globalization. It is reaching out to a plethora of new audience members. Different demographics have unique needs. Thus, product planning, inventory management, and marketing can become tough for operation managers.
2. Maintaining a sustainable balance
Sustainability is all about ensuring that a product or service will remain in the market with the same operations. This can also be done on a broad scale. Some businesses attempt to ensure that their sustainability policies do not have a detrimental impact on the globe.
Sustainability is often regarded as a problem by companies. This is because it requires businesses to prioritize long-term planning above short-term planning. Some businesses prioritize short-term earnings. Whereas a sustainable business will aim for long-term growth and development. They do this to build a more long-lasting reputation. It helps them to use that reputation to market an ethical good or service.
3. Making effective communication possible
Miscommunications can cause many problems inside a business. They could be expensive mistakes. Creating an operations management team to promote strong communication fosters a productive work environment.
There could be communication gaps between internal and external stakeholders. Operations management departments are responsible for bridging these gaps.
This includes ensuring that everyone from the part-time intern to the CEO is on the same page. Everyone must be aware of essential issues including the company's aims and objectives.
4. Cultivating ethical behavior
Ethics is a top responsibility when it comes to revamping business processes. However, with multiple operating parts in an organization, this is difficult. Companies that want to achieve long-term success must ensure ethical behavior, publicly and privately.
Operations Management Best Practices
We shall learn about a few methods to get the best out of operations management. These best practices provide areas of attention for improving everyday operations. Let’s start.
Keep up to date
This is a key step. Every component of a business, particularly technology, is continuously changing and evolving. Learn what the market demands. This will ensure a wide acceptability of the product.
Keeping up with market developments might be costly in terms of both time and money. Yet, the competitive advantages far exceed the drawbacks. Training your staff to understand new technology can be a good starting point. Organizations should prioritize updating that technology to the most recent version.
Inventory Management
Successful inventory management allows businesses to know what resources are available. They can then plan to replenish them as needed. Sound inventory management helps avoid overspending on unneeded things.
There are various methods of inventory management. You may utilize any of these:
- ABC analysis
- LIFO - Last In First Out
- FIFO - First In First Out
- Economic Order Quantity or EOQ
- Just in Time or JIT
Maintain Employee Satisfaction
Successful daily operations process depend on employee satisfaction. When employees are content, company operations run more smoothly. Employees that are happy are also more willing to volunteer their time to help the organization.
Providing practical training is another way to ensure employee satisfaction. Employees that receive training are more secure in their particular responsibilities. Also, they have less uncertainty about their function in the business.
Employees who like their jobs will be able to identify areas for development. They feel comfortable expressing their observations with management. Creating a safe and healthy work atmosphere allows for inquiries and concerns. It is essential to address them to improve how the firm runs.
Automate the Procedure.
You may find managing each stage manually too time-consuming. Try incorporating automation into your regular operations. Using the correct technology to automate operations management saves time, money, and resources.
The best software for your business is one that maintains a constant flow of communication between departments. It prevents potential issues from occurring. Also, it streamlines time-consuming processes.
With all this, it leaves little room for problems. Thereby, it assists in identifying areas for growth.
Maintain Open Lines of Communication.
There is no such thing as overcommunicating. Maintaining open lines of communication between all parts of an organization reduces the possibility of errors. This should be done especially at all phases of production.
Miscommunications cost time and money to correct and reverse. Open communication increases productivity. It develops trust that everyone in the organization understands each other.
Demand Predictions
Companies must clearly define their output expectations. This shall help them to properly manage operations. It includes doing precise analysis and forecasting demand.
Begin planning for future demand and identify external factors influencing production. Examine previously acquired historical data and obtain numerous internal and external perspectives. You can also differentiate KPIs and closely track market changes.
Develop a thorough awareness of client satisfaction. Learning about forthcoming demands allows you to plan for unanticipated changes. Thus, you may capitalize on potential growth possibilities.
Gather Information
Historical data generates future prospects. Gathering corporate data aids in the identification of prospective production challenges. It is vital for the identification of essential adjustments. Collecting that data electronically also enables improved communication. This is because all information is always up to date and available.
What do Operations Managers do?
The responsibilities of the operations managers can be understood through the following points:
- Define strategic objectives. Set objectives and goals to ensure the smooth and efficient running of operations.
- Plan resources. Analyze and plan resources such as staff, budget, materials, and time.
- Monitor performance. Monitor and evaluate the performance of staff and operations to ensure objectives are being met.
- Manage projects. Oversee projects to ensure they are completed within budget and on time.
- Develop strategies. Develop strategies to increase efficiency, reduce costs, and improve customer service.
- Monitor compliance. Ensure operations adhere to all legal, safety, and quality standards.
Ideal Skills of an Operations Manager
The ideal skills of an operations manager can be summed up through the following points:
- Leadership: The ability to motivate, delegate, and lead teams to success.
- Communication: The ability to communicate clearly with all departments and stakeholders.
- Problem Solving: The ability to identify problems and create solutions in a timely manner.
- Decision-Making: The ability to make sound decisions quickly and confidently.
- Strategic Thinking. The ability to understand the bigger picture and develop strategies to achieve goals.
- Organizational: The ability to manage multiple tasks and prioritize according to deadlines.
- Adaptability: The ability to remain flexible and adjust to changing conditions.
- Financial Management: The ability to monitor and control budget and costs.
- Analytical Skills: The ability to analyze data and draw meaningful conclusions
- Technology: The ability to use and understand technology to improve operations.
Responsibilities in Operations Management
Responsibilities in Operations Management may vary based on the sector. Yet, a majority of the fundamental tasks are the same. Let’s check them in this section here:
- Establishing and Maintaining Processes. Developing and implementing standard operating procedures to ensure consistency and quality.
- Managing Resources. Ensuring resources are available and used efficiently to support operations.
- Monitoring Performance. Monitoring performance indicators to identify and address any issues.
- Training and Developing Staff. Providing training and development opportunities to ensure staff is knowledgeable and competent.
- Improving Efficiency. Using data to identify areas for improvement and implementing changes to increase efficiency.
- Risk Management. Identifying and mitigating risks associated with operations.
- Customer Service. Developing and maintaining relationships with customers to ensure customer satisfaction.
- Budgeting. Planning and managing the operational budget to ensure resources are used wisely.
What are some Examples of Operations Management?
There are numerous examples across industries because every organization needs operations management. Furthermore, any industry can have a diverse set of operations functions.
Eight sectors where operations management is utilized are as follows:
Manufacturing and Production
A company that manufactures household appliances has processes for procuring materials. It also has a defined process for managing factories, maintenance, inventory control, and QA.
Healthcare
A healthcare facility's operations manager is often in charge of ensuring efficiency in delivering high-quality care. This can include controlling administrative expenditures, claims and billing. Furthermore, ensuring legal compliance is integral to the sector.
Retail
This is an industry that can range from brick-and-mortar to e-commerce. Thus, from single stores to chains, company operations can include a variety of operations. Sourcing, inventory, staffing, store management, and customer support are some examples.
Education
The role of an Operations Manager in the education sector is to ensure the efficient daily operations of the institution. This includes overseeing administrative, financial, and technological operations.
Thus, ensuring compliance with policies and regulations and providing guidance to staff. They must also resolve operational issues and manage budgets. The Operations Manager also develops strategic plans to achieve the school's long-term goals.
Logistics
Operations management in the logistics sector involves planning, coordinating, and overseeing daily operations. It tracks all activities related to transportation and logistics. This includes managing staff and optimizing operations and workflow. Also, overseeing the maintenance of vehicles and equipment is significant.
The process must ensure compliance with regulations and resolve customer service issues. They also manage budgets and develop and implement processes to improve efficiency. Overall, they must work with other departments to ensure the timely delivery of goods.
Banking and Financial Services
This field involves ensuring that the financial operations of an organization are conducted in a secure manner. The operations manager handles all the processes associated with financial operations. This may include accounting and financial reporting. Also, investment operations and cash management are some other areas they support.
Finally, they must oversee regulatory compliance. The operations manager must also ensure that all financial information is accurate. It must be compliant with applicable laws and regulations. In addition, the operations manager ensures that the financial resources effectively maximize returns.
Defense and Aerospace
Here, the OM involves the efficient use of resources to ensure that military operations are conducted in a safe manner. This includes managing the supply chain, personnel, and equipment. It also ensures the highest levels of quality, safety, and security are maintained.
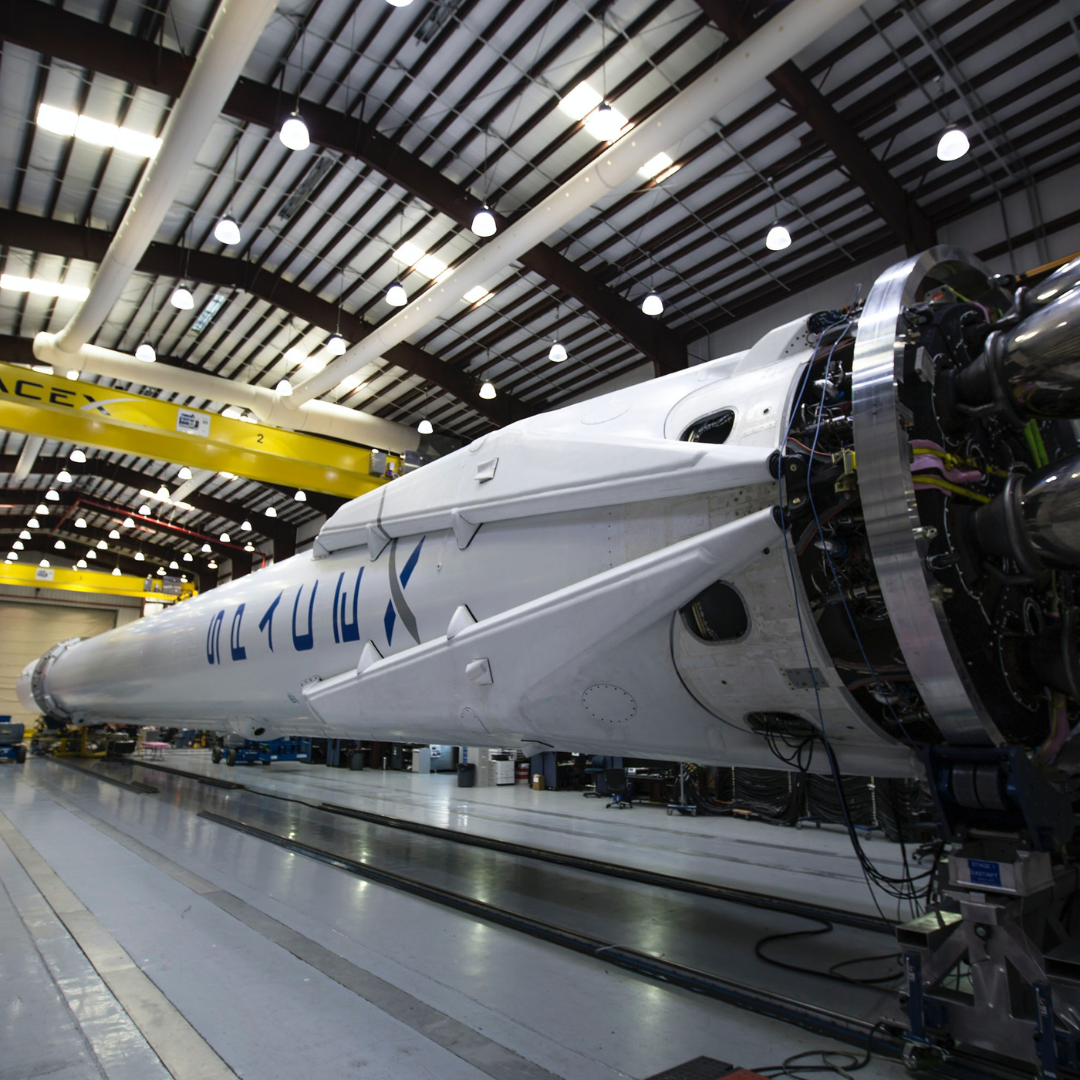
Operations managers must consider a variety of factors, such as operational risk and readiness. They must ensure that all military operations are in sync with applicable laws and regulations.
Telecommunications
Operations management, in this case, ensures the management of telecommunications technologies and systems. It is also necessary to efficiently manage and maintain those systems. It involves implementing policies to ensure the effective use of telecommunications systems.
It also seeks the optimization of their performance. Additionally, it involves understanding customer needs and developing strategies to meet those needs.
How does Operations Management Impact Customer Experience?
Operations management has a major impact on customer experience. It involves overseeing, designing, and controlling the process of production. It also takes care of the activities associated with it.
Improve Customer Satisfaction
Managing the operations of a business can ensure customer satisfaction. Other factors like safety and quality of products are also covered. Additionally, it allows businesses to understand customer needs and expectations.
Timely Delivery of Products
Based on these, they can create processes and improve customer experience. Operations management can help businesses deliver quality customer service. Moreover, they may ensure the timely delivery of products and ensure cost-effectiveness. Responding quickly to customer complaints can also be achieved easily.
Enhance Customer Loyalty
Aside from this, operations management can help businesses improve customer loyalty. By creating efficient processes, businesses can ensure that customers get the expected service. It can also help businesses identify areas in which they can improve their customer service. This can be done by providing better training or improved communication.
By understanding customer needs, they can have efficient processes in place. Eventually, businesses can ensure customers have a positive experience with their products.
How are Operations Management and ERP Related?
Operations management and ERP (Enterprise Resource Planning) are closely related. Operations management is the process of planning, organizing, and supervising production, and delivery.
ERP is a software system that helps organizations to manage their business processes and operations. ERP is a tool used by operations managers to streamline their processes. It helps them improve efficiency and reduce costs.
ERP systems provide the data and information needed to make decisions. They assist operations managers to make the most of their resources. ERP systems are used to automate and integrate operations management activities. These are supply chain, inventory, production planning, and customer service.
Benefits of ERP System in Operations Management
ERP is essential in operations management. It aids in the management of the organization's activities. ERP system automates all business activities by standardizing the format for the organization.
ERP software is instrumental in reducing the time and effort required to run a firm. Before implementation, a project report on ERP must be created. Measures must be taken to plan the business accordingly. ERP software aids in increasing the company's profits.
ERP facilitates the movement of information across departments. It enables a clear insight into the business structure. Simply put, an ERP system is a data management system that aids in the processing and administration of data within an organization.
Enterprise software becomes an important aspect of the organization and facilitates information access.
Here is how we can lay down the benefits of ERP in operations management:
Customer Relationship Management
An ERP system can store and provide accurate customer information. This can be accessed later for sales and marketing. Thus, it makes customer-centric approaches for a profitable business.
SCM and Warehouse Coordination
The supply chain module of the ERP streamlines the supply chain operations. It also lets the companies deal in various currencies and languages.
With automation, all the supply chain activities can turn out flawless. A powerful supply chain can manage different warehouse processes efficiently. Serial tracking, lot number, and multi-location stock can all be done swiftly.
Enhance Production Scheduling
ERP can aptly handle the raw material that arrives in the unit. It also keeps track of their lifecycle and order history. ERP aids effective scheduling and maintenance of employees. This further aids in improving asset performance and production schedule.
Human Resources
All aspects of human resources can be structured to improve business operations. ERP can automate a lot of human resource activities. This eventually helps the HR department to work on other challenges for better performance.
Conclusion
Overall, operations management is a crucial part of any organization. It ensures that the company runs smoothly and efficiently. It is important to have the right people in place to manage the operations. It also incorporates the right structures and processes.
Sound operations management can help organizations increase their efficiency and reduce costs. It also improves customer satisfaction. By having a clear understanding of the operations of the company, the necessary changes and improvements can be made. This helps ensure the most successful outcomes.
How can Deskera Help You?
Deskera can help with operations management by providing businesses with an integrated suite. The use of cloud-based business software solutions can be tremendously helpful. This includes accounting, project management, inventory management, customer management, and more.
Deskera also offers real-time data analytics. Thus allowing businesses to make informed decisions quickly and easily. Additionally, Deskera provides automated workflows for streamlining operations and improving efficiency.
Here are some of the ways Deskera ERP and MRP systems can help you:
- Make a manufacturing schedule
- Maintain a Bill of Materials
- Produce detailed reports
- Create your own dashboard, among other things!
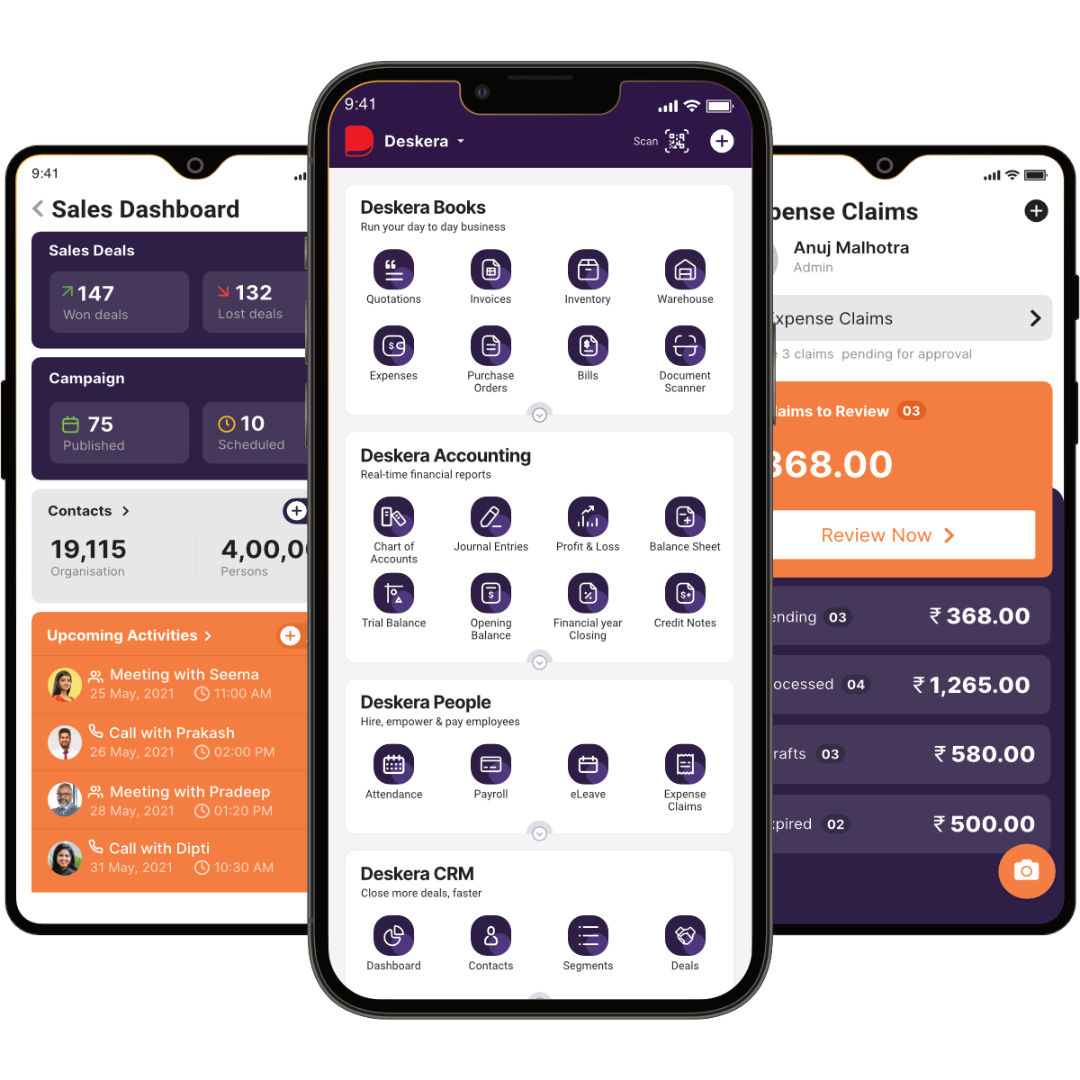
Deskera Books, a Deskera ERP accounting specialist, automates all of your accounting activities. Invoicing, billing, costs, payments, and taxes are all part of the package. There is reporting, approval flows, various currency payments, payment getaways, and much more.
Deskera CRM makes it simple to expand your customer base. Email marketing, CTA buttons, landing pages, and support desk options are some methods you can use. Furthermore, automating sales and transactions is now straightforward. Moving them through the sales process and collecting real-time data is also simple.
Deskera People is a straightforward tool for centralizing human resource management duties. Payroll processing is quick and easy using this technology. It also helps you with overtime, employee benefits, training programs, and a variety of other things.
Key Takeaways
- Operations management is the process of managing the operations of an organization.
- It aims to ensure the efficient use of resources to produce high-quality products.
- Operations management involves analyzing and managing processes and improving customer service. It is a vital part of any organization and is key to success.
- Operations management is the branch of management that oversees the entire production timeline of a service/product.
- There are various types of operations management. Product design, purchasing & procurement, and quality management are some of these. Other include forecasting, process management, inventory management, and so on.
- Six sigma, lean manufacturing, and reconfigurable manufacturing are some systems of operations management.
- Capacity planning, quality control, and SCM are some of the roles fulfilled by operations management.
- Operations management is essential for refining processes. It also aids employee productivity and the reputation of the business.
- People in charge of operations management are called operations managers. They are responsible for various activities.
- Defining objectives and developing strategies are some of their important responsibilities.
- Leadership, communication, and problem-solving are significant skills an operations manager must possess.
- Risk management and budgeting are some aspects the managers are expected to excel at.
- There are numerous examples of operations management as every organization needs operations management.
- Healthcare, retail, education, and banking are some common examples.
- OM can help businesses by improving customer loyalty and experience. Thus, generating better profits.
- Operations management and ERP (Enterprise Resource Planning) are closely related. ERP systems are used to automate and integrate operations management activities. These are supply chain, inventory, production planning, and customer service.
- CRM, SCM, and better production schedules are a few benefits of ERP in operations management.
- It helps coordinate SCM and warehouse. Serial tracking, lot number, and multi-location stock can all be done swiftly.
- Operations management is a crucial part of any organization. It ensures that the company runs smoothly and efficiently.
- OM is important to have the right people in place to manage the operations. It also incorporates the right structures and processes.
- The four Vs of operations management define a company's core product deliveries. These are Volume, Variety, Visibility, and Variation.
- Location, inventory, maintenance, and scheduling are among the 10 important decisions of operations management.
Related Articles
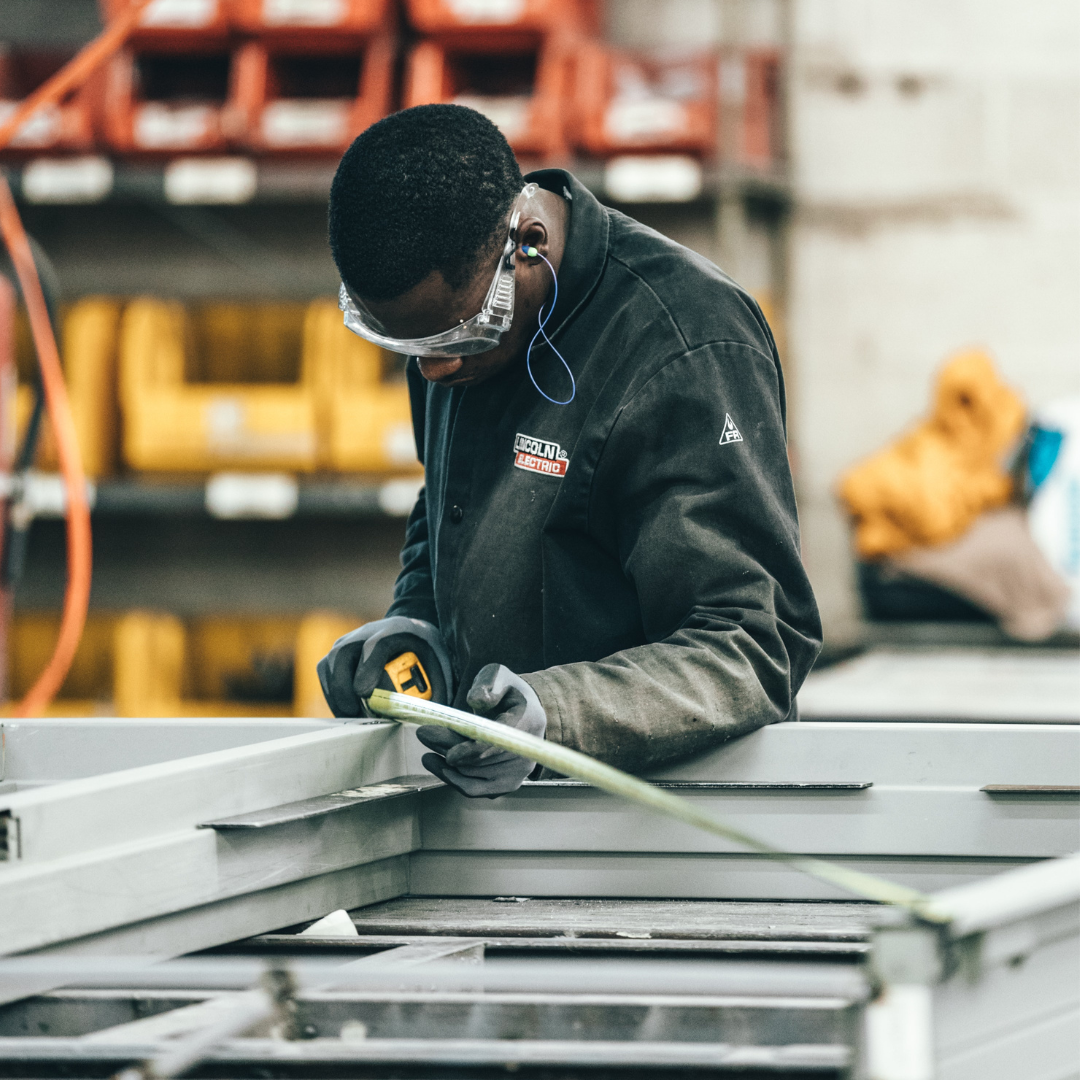
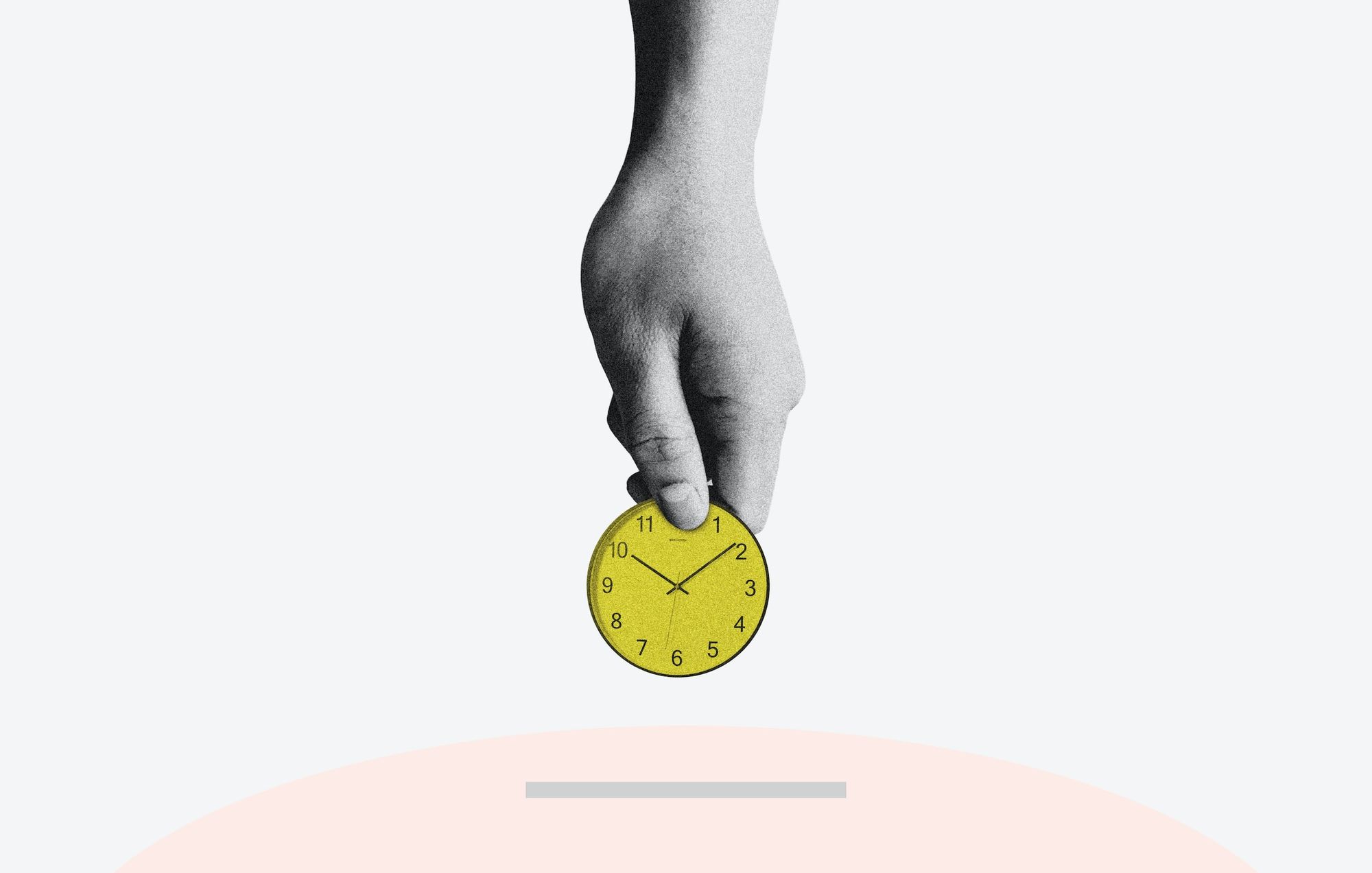
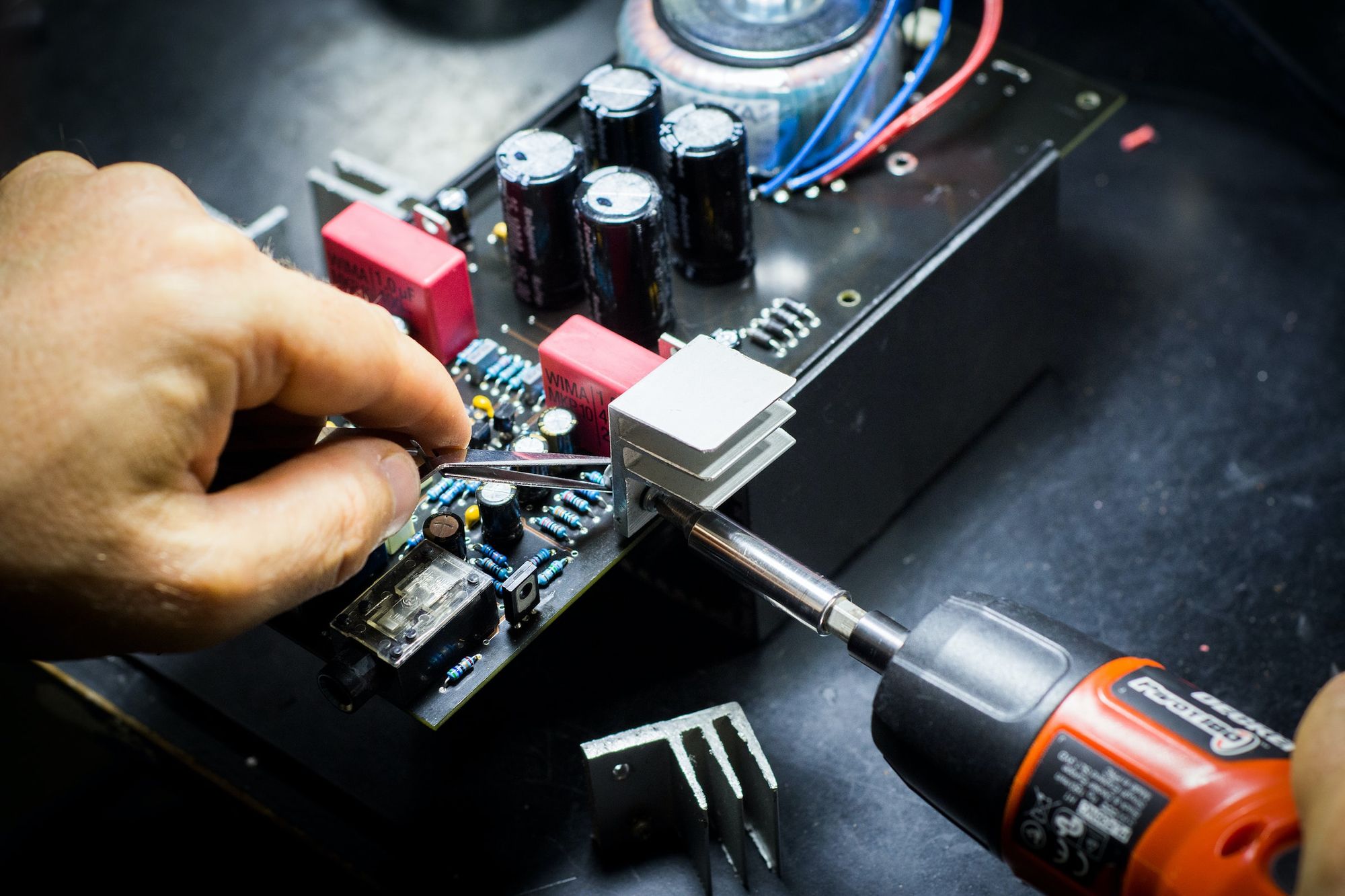
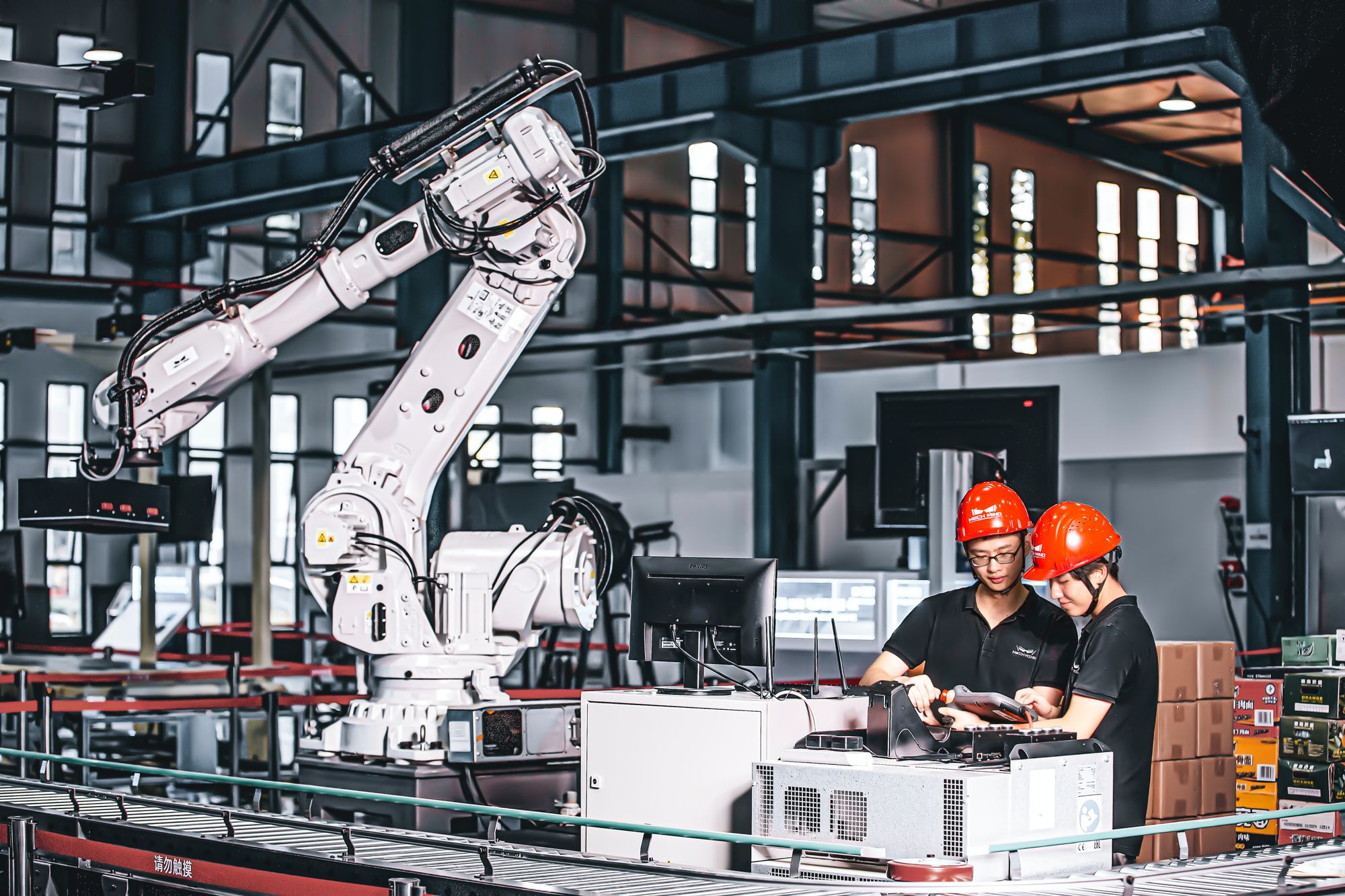
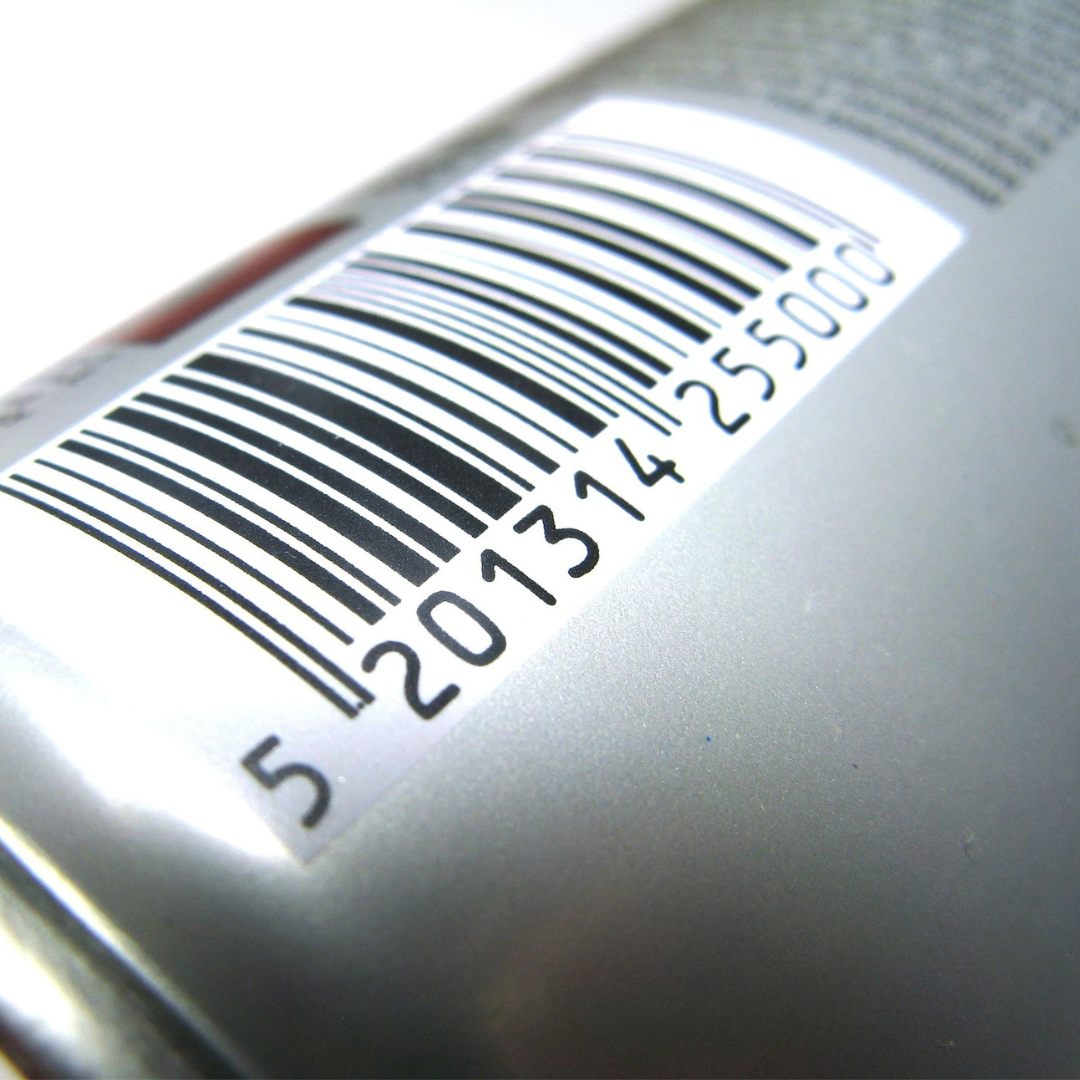