Have you ever wondered how the devices we use daily—like smartphones, laptops, and smart home gadgets—are brought to life? The electronic manufacturing process is the engine behind these technological marvels, transforming raw materials into functional, reliable products that power modern life.
From the intricate design of circuit boards to the precise placement of components, electronic manufacturing involves several highly specialized stages that ensure the creation of top-quality devices.
At its core, the electronic manufacturing process is a series of interconnected steps that turn ideas into tangible, working products. It begins with the design and prototyping phase, where engineers lay the groundwork for how the product will look and function.
This is followed by sourcing essential materials, fabricating printed circuit boards (PCBs), assembling components, soldering, and rigorous testing to ensure performance. Each stage requires meticulous attention to detail and collaboration between teams of experts to ensure that the final product meets industry standards.
To streamline these complex processes, manufacturers are increasingly turning to software solutions like Deskera ERP and Deskera MRP. Deskera ERP integrates critical business operations, from inventory management to financial tracking, providing a unified platform that enhances efficiency across the supply chain.
Meanwhile, Deskera MRP specializes in production planning, material requirements, and demand forecasting—key elements in managing electronic manufacturing. By leveraging these tools, manufacturers can optimize their production workflows and respond more effectively to market demands, ensuring higher quality and faster delivery of products.
Additionally, integrating AI-driven solutions like ERP.AI can further transform electronic manufacturing by automating data analysis, enabling predictive maintenance, and enhancing decision-making through intelligent insights across operations.
This blog will guide you through the key steps of the electronic manufacturing process, highlighting the technologies, challenges, and future trends shaping this crucial industry.
What is Electronic Manufacturing?
Electronic manufacturing refers to the process of designing, assembling, and producing electronic components and devices that are integral to modern life. This process includes several stages, such as electronic design and manufacturing, material sourcing, assembly, testing, and final packaging.
It’s essential in creating products like consumer electronics, medical devices, automotive electronics, and more. Companies that specialize in these services, known as electronic manufacturing services (EMS) companies, play a critical role in delivering high-quality, functional electronics for various industries.
At the core of the electronic manufacturing industry is the Printed Circuit Board (PCB), which serves as the backbone of most electronic devices. The PCB connects essential components like resistors, capacitors, and microprocessors, all of which are mounted using techniques such as Surface Mount Technology (SMT) or Through-Hole Technology (THT).
Once assembled, these components undergo rigorous testing to ensure quality and reliability before the final product reaches consumers. Leading electronic manufacturing companies utilize cutting-edge automation and Manufacturing ERP systems to manage this complex process efficiently.
The rise of ERP for manufacturing has significantly transformed the electronic manufacturing services sector. These software solutions streamline operations from inventory management to production planning, helping electronic manufacturing companies improve efficiency and maintain strict quality control standards.
With the support of ERP systems, businesses in the electronic manufacturing industry can better manage their supply chains, optimize production workflows, and respond quickly to changes in demand.
In this evolving landscape, electronic manufacturing services companies continue to innovate, delivering advanced solutions that keep pace with technological advancements and market demands.
Key Stages of the Electronic Manufacturing Process
The electronic manufacturing process involves several key stages, each essential to ensuring the production of high-quality electronic devices. These stages are carefully coordinated to streamline manufacturing, minimize errors, and maintain strict quality standards.
Let’s explore the primary phases involved in electronic manufacturing, which are fundamental to the work of electronic manufacturing companies and electronic manufacturing services (EMS) companies.
1. Design and Prototyping
The first step in the electronic design and manufacturing process is developing a detailed blueprint of the product. Engineers create digital designs using Computer-Aided Design (CAD) tools to map out the electronic components and circuitry of the device. This phase is crucial for both functionality and manufacturability.
Prototypes are built to test the design’s feasibility, helping electronic manufacturing services companies refine the product before moving into mass production. The feedback from the prototyping phase ensures that any flaws or inefficiencies are addressed early.
2. Material Sourcing
In the next phase, manufacturers source the materials needed to build the product. This includes semiconductors, resistors, capacitors, metals, and plastics that are vital for the production of electronic manufacturing services.
Reliable sourcing is critical, as delays or defects in materials can disrupt the entire supply chain. Leading electronic manufacturing companies utilize ERP for manufacturing to manage inventory and suppliers efficiently, ensuring the right materials are always available when needed.
3. PCB Fabrication
The Printed Circuit Board (PCB) acts as the foundation of most electronic devices. PCB fabrication is a multi-step process involving etching, layering, drilling, and applying a solder mask to create the pathways that will connect the components.
This stage is highly precise and requires advanced technology to ensure that the circuits function correctly. Many electronic manufacturing services companies specialize in PCB fabrication, as it is a crucial step in ensuring the reliability of the final product.
4. Component Placement and Assembly
Once the PCB is fabricated, the components are placed onto the board. This is done using Surface Mount Technology (SMT) or Through-Hole Technology (THT), depending on the type of product being manufactured. SMT involves mounting components directly onto the surface of the PCB, while THT requires components to be placed through pre-drilled holes in the board.
This step is often automated, with electronic manufacturing companies using sophisticated machines to ensure precise placement. High-efficiency manufacturing ERP systems help coordinate these processes, optimizing the production flow.
5. Soldering
After the components are placed, they need to be securely attached to the PCB. Soldering is the process of bonding the components to the board using a molten metal alloy. Methods like reflow soldering or wave soldering are used depending on the design and scale of production.
Proper soldering ensures strong electrical connections, which is critical to the performance of the device. EMS companies take special care to automate this process for accuracy and reliability.
6. Testing and Quality Control
Before any electronic device can be shipped, it undergoes rigorous testing to ensure it meets the necessary performance standards. Various testing methods are employed, such as functional testing, burn-in testing, and automated optical inspection (AOI).
Testing ensures that the product performs as expected and that there are no defects in the circuitry or assembly. Electronic manufacturing services companies adhere to industry regulations and quality standards, such as ISO certifications, to guarantee that products are safe and reliable.
7. Final Assembly and Packaging
In the final stage, the components are assembled into the final product housing, and the device is packaged for distribution. This step involves attaching external components, such as screens, buttons, or casing, and ensuring everything is securely in place.
Packaging must also be designed to protect the device during shipping. Efficient ERP systems play a vital role here, coordinating assembly and packaging to meet production deadlines while maintaining quality.
Each of these stages is crucial to the success of the electronic manufacturing industry, and electronic manufacturing services (EMS) companies have mastered these processes through automation, testing, and ERP for manufacturing integration.
By streamlining each phase, these companies can deliver high-quality products at scale, meeting the growing demands of the global market.
Advanced Manufacturing Techniques in Electronic Manufacturing
In addition to the key stages of the electronic manufacturing process, modern electronic manufacturing companies employ several advanced techniques to improve efficiency, accuracy, and scalability.
These techniques are essential for keeping up with the ever-evolving demands of the electronic manufacturing industry and ensuring that products meet high-quality standards.
1. Automation and Robotics
Automation has revolutionized electronic manufacturing services by reducing the need for manual labor in repetitive tasks, such as component placement and soldering.
Advanced robotics systems can handle intricate assembly processes with greater precision and speed than human workers, minimizing errors and reducing production time.
Many electronic manufacturing services (EMS) companies utilize automated solutions to streamline their operations, improve yield rates, and reduce costs.
2. Surface Mount Technology (SMT)
Surface Mount Technology (SMT) is a technique widely used in electronic design and manufacturing that allows components to be mounted directly onto the surface of PCBs without the need for pre-drilled holes.
SMT enables higher component density and faster assembly, making it a preferred method for producing compact, high-performance devices like smartphones and laptops.
This technology is vital for electronic manufacturing services companies aiming to increase production efficiency while maintaining quality.
3. Additive Manufacturing (3D Printing)
Additive manufacturing, also known as 3D printing, is gaining traction in the electronic manufacturing industry for rapid prototyping and small-batch production.
It allows for the creation of highly complex and customized components at a lower cost and with faster turnaround times. In addition to prototypes, 3D printing can be used to produce specialized parts that may be difficult or expensive to source through traditional methods, making it a valuable tool for electronic manufacturing companies.
4. Clean Room Manufacturing
Many electronic manufacturing services require the use of clean rooms, particularly in the production of sensitive components like semiconductors and medical devices.
Clean rooms maintain controlled environments with minimal dust, contaminants, and electrostatic discharge (ESD), which can damage delicate electronics. These environments are critical for ensuring that products meet stringent safety and quality standards, particularly in industries like aerospace, healthcare, and defense.
5. Lean Manufacturing and Just-in-Time (JIT) Production
To optimize efficiency and minimize waste, electronic manufacturing companies often implement lean manufacturing principles and Just-in-Time (JIT) production strategies. These methods focus on reducing excess inventory, streamlining workflows, and delivering products precisely when needed.
With the help of ERP systems for manufacturing, companies can closely monitor production schedules and supply chains, ensuring that resources are used efficiently while maintaining product quality.
These additional techniques are pivotal to staying competitive in the electronic manufacturing industry. By leveraging advanced methods such as automation, SMT, and 3D printing, electronic manufacturing services (EMS) companies can achieve higher production efficiency, deliver more innovative products, and maintain the rigorous standards expected in today’s tech-driven market.
Supply Chain Management in Electronic Manufacturing
Effective supply chain management is critical in the electronic manufacturing industry, where coordination between suppliers, manufacturers, and distributors must be seamless.
From sourcing materials to delivering the final product, each link in the supply chain plays a vital role in ensuring timely production and maintaining high-quality standards.
Electronic manufacturing services (EMS) companies rely heavily on optimized supply chain management to navigate complex global networks and respond to rapidly changing demands.
1. Material Sourcing and Procurement
One of the key components of supply chain management in electronic manufacturing is the sourcing of raw materials and electronic components. Manufacturers must secure reliable suppliers for critical materials, such as semiconductors, capacitors, resistors, and metals.
Any disruption in this supply chain can lead to production delays. Electronic manufacturing companies use advanced ERP systems for manufacturing to manage supplier relationships, monitor inventory levels, and automate procurement processes, ensuring materials are available when needed.
2. Inventory Management
Inventory management is a balancing act in electronic manufacturing services. Having too much stock can lead to high holding costs, while too little can result in production bottlenecks.
Manufacturing ERP solutions provide real-time visibility into inventory levels, allowing electronic manufacturing companies to implement Just-in-Time (JIT) strategies.
This approach minimizes excess inventory, reduces waste, and ensures that components are available right when they are needed, improving efficiency and cost-effectiveness.
3. Logistics and Distribution
Once the product is manufactured, it must be delivered to customers or distributors in a timely and efficient manner. Coordinating global logistics, especially for large-scale electronic manufacturing services (EMS) companies, can be challenging due to varying customs regulations, transportation costs, and delivery timelines.
Electronic manufacturing companies often leverage ERP systems to track shipments, manage international logistics, and ensure smooth transitions from factory to customer.
4. Risk Management and Supplier Diversification
In the electronic manufacturing industry, supply chain disruptions can have a significant impact on production timelines and costs. Natural disasters, political instability, or supply shortages can all create risks for manufacturers.
To mitigate these risks, electronic manufacturing companies employ strategies such as supplier diversification—working with multiple suppliers for critical components to avoid relying too heavily on one source.
Advanced ERP for manufacturing systems provide analytics and forecasting tools to help companies anticipate disruptions and adjust accordingly.
5. Sustainability and Ethical Sourcing
As sustainability becomes a greater focus for the electronic manufacturing industry, companies are under increasing pressure to ensure that their supply chains adhere to environmentally responsible practices. This includes ethical sourcing of materials like rare earth metals and ensuring that suppliers comply with environmental regulations.
Electronic manufacturing services companies are also exploring sustainable packaging and energy-efficient logistics to reduce their carbon footprint. Modern ERP systems for manufacturing help companies track and report on sustainability metrics, ensuring that they meet industry and regulatory standards.
By implementing robust supply chain management strategies, electronic manufacturing companies can better navigate the complexities of global production, optimize their workflows, and respond quickly to shifts in demand.
The integration of ERP systems enhances visibility, efficiency, and coordination across the supply chain, allowing electronic manufacturing services (EMS) companies to deliver high-quality products on time while managing costs and risks effectively.
Challenges and Risks in Electronic Manufacturing and How to Overcome Them
The electronic manufacturing industry faces a unique set of challenges and risks due to the complexity and scale of production. These obstacles, ranging from supply chain disruptions to technological advancements, can hinder operations and affect profitability.
However, with the right strategies, electronic manufacturing companies can mitigate these risks and maintain smooth operations. Below are some common challenges faced by electronic manufacturing services and solutions to combat them.
1. Supply Chain Disruptions
One of the most significant risks in electronic manufacturing is supply chain disruption. Components such as semiconductors, metals, and other critical materials may face shortages, delayed deliveries, or price fluctuations, which can stall production timelines. This risk has been heightened in recent years due to global events like pandemics and trade disputes.
Solution: To overcome this challenge, electronic manufacturing services (EMS) companies can adopt ERP systems for manufacturing that include predictive analytics and demand forecasting. These systems allow companies to anticipate potential shortages and source alternative suppliers, diversifying the supply chain to reduce dependency on a single source.
Advanced ERP solutions can also automate inventory management, helping businesses implement Just-in-Time (JIT) strategies to reduce excess stock and manage costs more effectively.
2. Rapid Technological Advancements
The electronic manufacturing industry is constantly evolving due to technological advancements. Keeping up with new technologies, production techniques, and consumer demands can be a challenge, especially for smaller electronic manufacturing services companies.
Solution: Investing in Manufacturing ERP systems that are designed to scale and adapt to technological changes is essential. ERP systems can integrate new production tools and methodologies quickly, allowing electronic manufacturing companies to stay competitive. Additionally, regular employee training on the latest technologies and trends can help teams adapt faster to new production requirements.
3. Quality Control and Product Defects
Ensuring that all products meet high-quality standards is a significant challenge in electronic manufacturing. Defects in electronic devices can lead to expensive recalls, damage to brand reputation, and customer dissatisfaction. Maintaining strict quality control during production, from design to final testing, is essential.
Solution: To combat quality issues, electronic manufacturing services companies can implement automated testing processes, such as automated optical inspection (AOI) and functional testing.
Additionally, integrating real-time data monitoring through ERP systems for manufacturing can allow for early detection of defects, reducing waste and ensuring that faulty products do not reach the market.
Lean manufacturing techniques can also be employed to minimize waste and ensure that quality is built into every step of the production process.
4. Cost Pressures
Manufacturers constantly face pressure to reduce costs while maintaining high standards of quality and efficiency. Fluctuating material costs, rising labor expenses, and the need to invest in advanced technologies can strain budgets and affect profitability for electronic manufacturing companies.
Solution: Implementing cost-effective automation solutions and utilizing ERP for manufacturing can help streamline operations and reduce manual labor costs. Lean manufacturing practices can also reduce waste, optimize resource use, and improve overall efficiency.
Moreover, electronic manufacturing companies can leverage ERP systems to manage and forecast costs, ensuring that they remain competitive without sacrificing product quality.
5. Regulatory Compliance
Compliance with environmental regulations, product safety standards, and labor laws is a critical challenge for electronic manufacturing services companies. The industry is subject to numerous regulatory frameworks, which vary by region and can be complex to navigate. Failing to meet these requirements can result in penalties, legal issues, or the inability to sell products in certain markets.
Solution: ERP systems with built-in compliance management tools can help companies stay updated with the latest regulations and ensure that all products meet the necessary standards.
These systems can track compliance across the supply chain, ensuring that all components and processes adhere to relevant environmental, safety, and labor regulations.
By addressing these challenges with modern solutions, electronic manufacturing companies can remain resilient and competitive in a fast-paced industry.
Leveraging tools like manufacturing ERP and embracing automation not only mitigates risks but also enhances operational efficiency, allowing businesses to deliver high-quality products while staying agile in the face of change.
Compliance and Standards in Electronic Manufacturing
Compliance with industry standards and regulatory frameworks is essential for electronic manufacturing companies to ensure product safety, environmental responsibility, and market access.
The electronic manufacturing industry is governed by a wide range of regulations that vary across regions, covering everything from product quality to environmental impact.
Non-compliance can lead to significant financial penalties, legal complications, and damage to a company’s reputation, making it critical for electronic manufacturing services (EMS) companies to prioritize adherence to these standards.
1. Environmental Compliance
Environmental sustainability is a growing focus in the electronic manufacturing industry, with companies required to meet strict environmental regulations to minimize their ecological footprint.
Two of the most widely recognized environmental standards are the Restriction of Hazardous Substances (RoHS) and Waste Electrical and Electronic Equipment (WEEE) directives, particularly enforced in the European Union.
These regulations govern the use of hazardous materials like lead and mercury in electronic devices and dictate the proper disposal and recycling of electronic waste.
Solution: Electronic manufacturing services companies can achieve compliance by integrating ERP for manufacturing systems that track and manage materials used in production.
These systems help manufacturers ensure that they source components that meet RoHS and WEEE standards, and allow for detailed reporting on compliance with environmental regulations.
Adopting sustainable manufacturing practices, such as reducing emissions and using eco-friendly packaging, also supports compliance efforts.
2. Product Safety and Quality Standards
To ensure that electronic products are safe for consumer use, electronic manufacturing companies must adhere to product safety standards such as ISO 9001 for quality management and UL (Underwriters Laboratories) certifications.
ISO 9001 establishes the criteria for a quality management system, ensuring that products consistently meet customer and regulatory requirements. UL certification verifies that a product has been tested and meets safety standards for electrical devices.
Solution: To maintain product safety and quality, electronic manufacturing services (EMS) companies can implement stringent quality control systems, often facilitated by manufacturing ERP solutions. These systems help monitor production processes, test components, and identify potential defects before products leave the factory.
Additionally, automated testing procedures, such as AOI (Automated Optical Inspection) and functional testing, ensure that all products comply with the relevant safety standards.
3. International Trade Compliance
For electronic manufacturing companies that operate globally, navigating international trade regulations is a critical aspect of compliance. This includes adhering to export control laws, import tariffs, and customs requirements.
Companies must also ensure compliance with international standards, such as the CE marking for products sold in the European Economic Area and the FCC regulations for electronics sold in the United States.
Solution: Advanced ERP systems can help electronic manufacturing services companies manage the complexities of international trade compliance by automating customs documentation, monitoring tariffs, and ensuring adherence to local market standards.
These systems can also track the country of origin for components, helping companies ensure that they comply with trade agreements and avoid penalties.
4. Labor and Ethical Standards
In addition to product and environmental standards, electronic manufacturing companies must comply with labor laws and ethical sourcing guidelines.
This includes ensuring safe working conditions, fair wages, and compliance with regulations such as the Fair Labor Standards Act (FLSA) and International Labour Organization (ILO) conventions.
Many global companies also commit to avoiding conflict minerals—materials sourced from conflict zones where mining may fund violence and exploitation.
Solution: Compliance with labor and ethical standards can be achieved through ERP systems for manufacturing, which help companies monitor supplier practices, track labor conditions, and ensure ethical sourcing of materials.
By maintaining transparency throughout the supply chain, electronic manufacturing services (EMS) companies can demonstrate their commitment to responsible business practices and meet the growing demand for ethically produced electronics.
Maintaining compliance with these critical standards and regulations is essential for electronic manufacturing companies to stay competitive, avoid penalties, and uphold their reputations.
By leveraging ERP systems and implementing rigorous monitoring and reporting processes, companies can ensure that their products meet all necessary requirements, both domestically and internationally.
Future Trends in Electronic Manufacturing
The electronic manufacturing industry is evolving rapidly, driven by advancements in technology, changing consumer demands, and a growing emphasis on sustainability.
Electronic manufacturing services (EMS) companies are now adapting to trends that will reshape how electronics are designed, produced, and delivered. Below are some of the key trends shaping the future of electronic manufacturing.
1. Increased Automation and Robotics
Automation has been a key driver of efficiency in electronic manufacturing, and this trend is expected to continue growing. Advanced robotics, machine learning, and artificial intelligence (AI) are increasingly being integrated into production lines to improve precision, reduce human error, and optimize workflows. Electronic manufacturing companies are investing in smart factories, where machines communicate with each other to perform tasks more efficiently.
Impact: Automation reduces production costs, increases the speed of manufacturing, and enhances quality control.
For electronic manufacturing services companies, embracing automation will be critical to staying competitive, especially in high-demand industries like consumer electronics and automotive manufacturing.
Manufacturing ERP systems will play a central role in managing these automated processes, ensuring seamless coordination between human workers and machines.
2. Rise of the Internet of Things (IoT)
The Internet of Things (IoT) is transforming not only the products being manufactured but also the manufacturing process itself. IoT-enabled devices collect real-time data from production lines, enabling manufacturers to monitor equipment performance, predict maintenance needs, and reduce downtime. Additionally, IoT technology is being used to improve supply chain visibility by tracking components from supplier to final product.
Impact: IoT helps electronic manufacturing companies enhance operational efficiency, reduce waste, and optimize energy use. Electronic manufacturing services will benefit from the integration of IoT technologies into ERP systems, which can process and analyze the vast amounts of data generated by IoT devices to improve decision-making.
3. Sustainability and Green Manufacturing
Sustainability is becoming increasingly important in the electronic manufacturing industry as consumers and regulators push for more environmentally responsible practices.
Reducing carbon footprints, minimizing electronic waste, and improving energy efficiency are all key concerns for electronic manufacturing services (EMS) companies. As a result, manufacturers are exploring sustainable materials, green energy sources, and eco-friendly production processes.
Impact: Companies that prioritize sustainability will gain a competitive advantage by meeting consumer demand for greener products and complying with stricter environmental regulations.
Manufacturing ERP systems can help track sustainability metrics, manage energy use, and ensure compliance with environmental standards, such as RoHS and WEEE.
4. Additive Manufacturing (3D Printing)
Additive manufacturing, or 3D printing, is poised to revolutionize the electronic manufacturing process by enabling rapid prototyping and small-scale production. This technology allows manufacturers to create complex electronic components with greater flexibility and speed, reducing the need for traditional, time-consuming manufacturing methods.
Impact: Additive manufacturing will enable electronic design and manufacturing companies to bring products to market faster and at a lower cost. It also supports greater customization, allowing manufacturers to produce small batches of specialized components without the expense of retooling traditional machinery.
5. Advanced Materials and Miniaturization
The demand for smaller, more powerful electronic devices is driving innovation in materials and component design. Advances in nanotechnology, flexible electronics, and high-performance materials like graphene are enabling manufacturers to create smaller, lighter, and more energy-efficient devices. This trend is particularly important for industries such as wearable technology, medical devices, and telecommunications.
Impact: Electronic manufacturing services companies that can adopt these advanced materials will be better positioned to meet the demands of cutting-edge industries. ERP for manufacturing systems will play a crucial role in managing the complexities of producing and integrating these advanced materials, ensuring high-quality production standards are maintained.
6. Globalization and Localized Manufacturing
While globalization has long been a defining characteristic of electronic manufacturing, there is a growing shift toward localized manufacturing. This trend is being driven by the need for faster time-to-market, supply chain resilience, and customization for local markets. Localized manufacturing allows companies to reduce lead times, lower transportation costs, and address regional regulatory requirements more easily.
Impact: Electronic manufacturing companies that invest in localized production facilities will benefit from greater agility and the ability to respond more quickly to changing consumer demands. ERP systems for manufacturing will be essential for coordinating global and local operations, ensuring consistency and compliance across different markets.
By embracing these future trends, electronic manufacturing services companies can stay at the forefront of the industry, driving innovation and maintaining a competitive edge.
The integration of ERP systems and emerging technologies will be crucial in managing the complexities of these trends, ensuring efficiency, sustainability, and agility in an increasingly dynamic market.
How AI Enhances Manufacturing Processes
AI algorithms analyze real-time data to optimize production workflows, reduce machine downtime through predictive maintenance, and ensure quality control by detecting defects early.
AI also helps manufacturers manage inventory more accurately, forecast demand, and automate routine tasks, allowing teams to focus on innovation and strategy.
By unifying data and streamlining operations across departments, AI not only enhances productivity but also enables faster decision-making and cost savings.
How Deskera ERP and MRP Can Enhance Electronic Manufacturing ?
In the rapidly evolving electronic manufacturing industry, efficiency, precision, and real-time data are critical to success.
Deskera ERP and Deskera MRP offer powerful solutions to help electronic manufacturing companies streamline their operations, optimize production, and maintain compliance with industry standards.
By integrating ERP and MRP systems into their processes, manufacturers can achieve greater visibility and control over every stage of production.
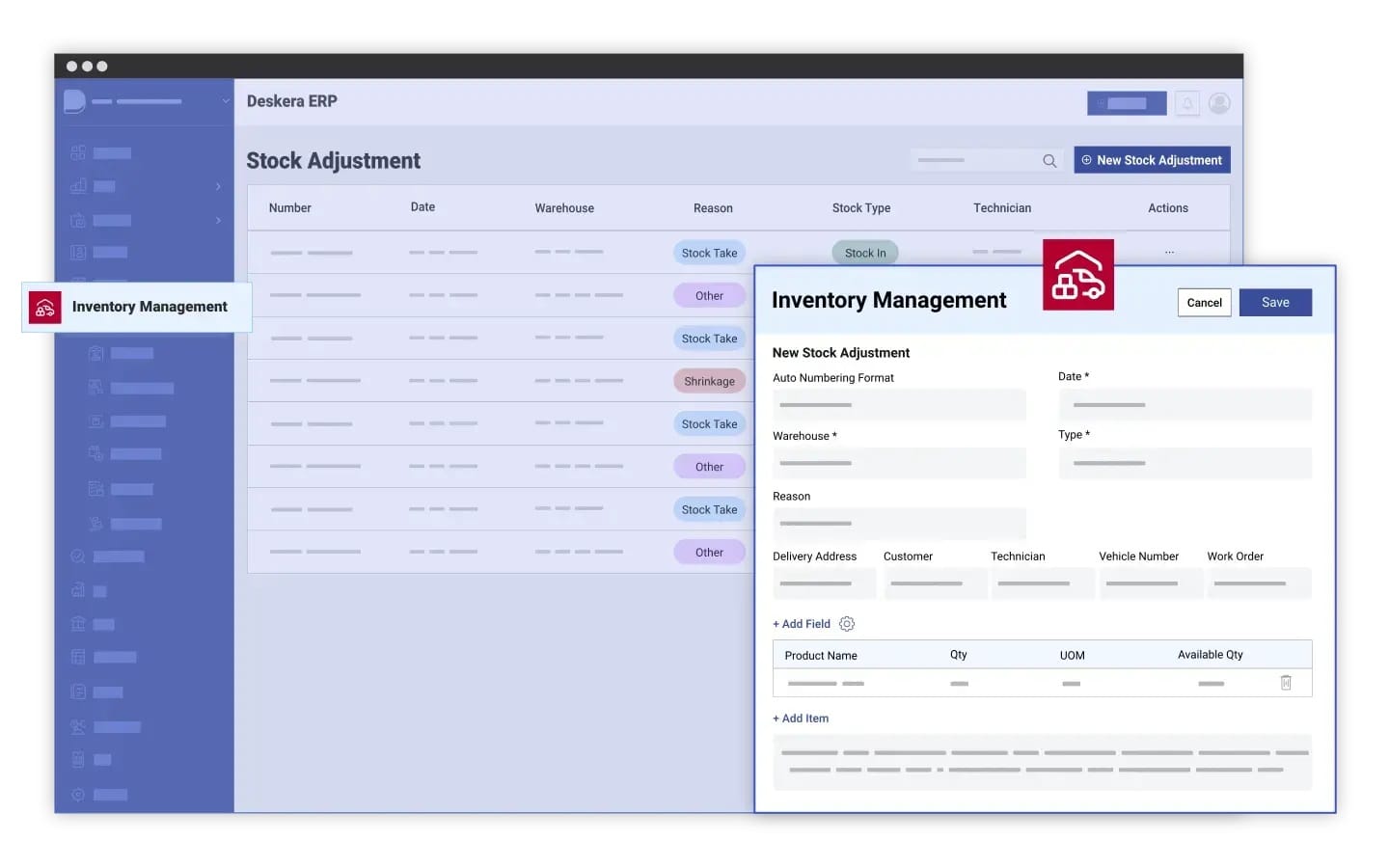
1. Streamlined Inventory Management
One of the most significant challenges in electronic manufacturing is managing complex inventories with numerous components and materials. Deskera ERP provides real-time tracking of inventory levels, ensuring that manufacturers have the parts they need when they need them. This prevents production delays due to stockouts and minimizes excess inventory, reducing overall costs.
Additionally, Deskera MRP helps manufacturers plan their material requirements more effectively, ensuring that the right materials are ordered at the right time. This is particularly crucial for electronic manufacturing services (EMS) companies that must balance high demand with tight production schedules.
2. Production Planning and Scheduling
Efficient production planning is key to staying competitive in the electronic manufacturing industry. Deskera MRP helps companies optimize their production schedules by analyzing demand forecasts, material availability, and labor capacity. This ensures that production runs smoothly, with minimal disruptions or downtime.
With Deskera ERP, manufacturers can track production progress in real-time, enabling them to make quick adjustments if issues arise. This level of control is essential for electronic manufacturing services companies that need to meet tight deadlines and deliver high-quality products on time.
3. Compliance and Quality Control
Adhering to strict industry regulations and maintaining high product quality are critical for electronic manufacturing companies. Deskera ERP allows manufacturers to track every step of the production process, ensuring that products meet regulatory requirements and quality standards.
Deskera MRP can be used to schedule routine quality checks and automate testing procedures, to catch any defects early. This helps reduce waste, improve product reliability, and ensure compliance with standards like ISO 9001, RoHS, and WEEE.
4. Improved Supply Chain Management
Managing suppliers and logistics is a complex task in electronic manufacturing. Deskera ERP offers integrated supply chain management features, allowing manufacturers to track shipments, manage supplier relationships, and ensure timely delivery of materials. With real-time visibility into the supply chain, manufacturers can reduce lead times and avoid disruptions that can affect production.
By leveraging Deskera ERP and MRP, electronic manufacturing services companies can also maintain better collaboration with suppliers, ensuring they receive high-quality components and materials while minimizing costs.
5. Cost Control and Financial Management
Managing costs is crucial for profitability in the highly competitive electronic manufacturing industry. Deskera ERP helps companies gain a clear view of their financials, tracking expenses, revenue, and profitability across all operations. With real-time financial data, manufacturers can make informed decisions to reduce costs and improve margins.
By automating routine financial tasks, such as invoicing and payroll, Deskera ERP also reduces the risk of errors and frees up valuable time for financial teams to focus on strategic planning.
Deskera ERP and MRP provide electronic manufacturing companies with the tools they need to stay competitive, maintain product quality, and streamline operations. From inventory management and production planning to compliance and financial control, Deskera’s solutions help manufacturers thrive in a fast-paced, dynamic industry.
Key Takeaways
- The electronic manufacturing process encompasses various stages, from design and prototyping to production and assembly, making it crucial for developing reliable and innovative electronic products.
- Electronic manufacturing involves the production of electronic components and assemblies, playing a pivotal role in various industries, including consumer electronics, automotive, and telecommunications.
- Understanding the key stages of electronic manufacturing—design, prototyping, production, assembly, and testing—is essential for ensuring product quality and meeting market demands.
- Incorporating advanced manufacturing techniques such as Surface Mount Technology (SMT), Through-Hole Technology, and Additive Manufacturing can enhance efficiency and flexibility in electronic manufacturing.
- Effective supply chain management is critical for electronic manufacturers to ensure timely delivery of components, minimize disruptions, and maintain product quality.
- The electronic manufacturing industry faces challenges such as supply chain disruptions, technological changes, and regulatory compliance; proactive strategies are essential for mitigating these risks.
- Adhering to industry standards and regulations (like ISO, RoHS, and WEEE) is vital for ensuring product safety, quality, and environmental responsibility in electronic manufacturing.
- The future of electronic manufacturing is characterized by increased automation, the rise of IoT, sustainable practices, and the adoption of advanced materials, driving innovation and efficiency.
- Deskera ERP and MRP provide essential tools for electronic manufacturers to streamline operations, optimize inventory management, and improve production planning, ensuring competitiveness in the industry.
Related Articles
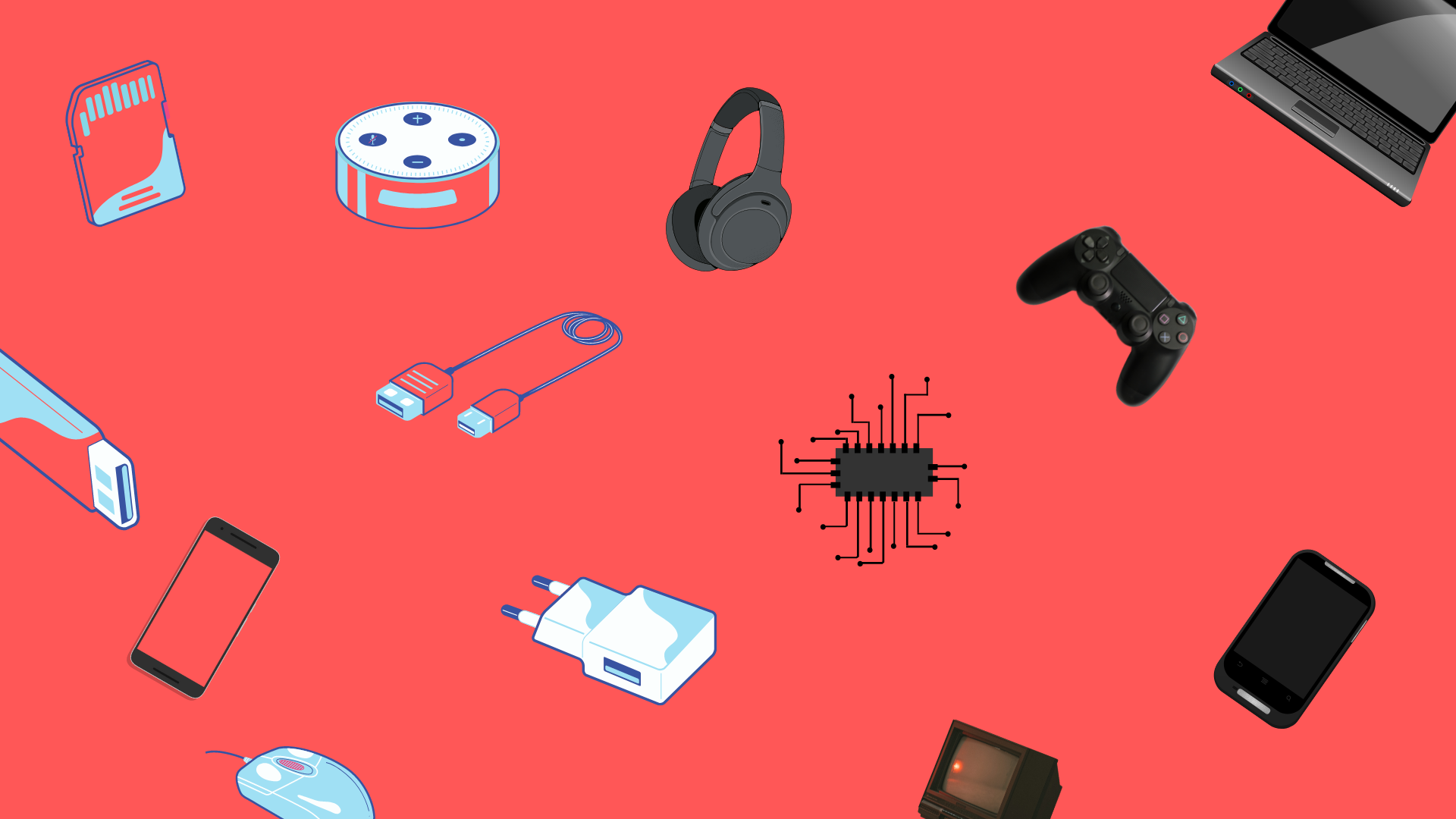
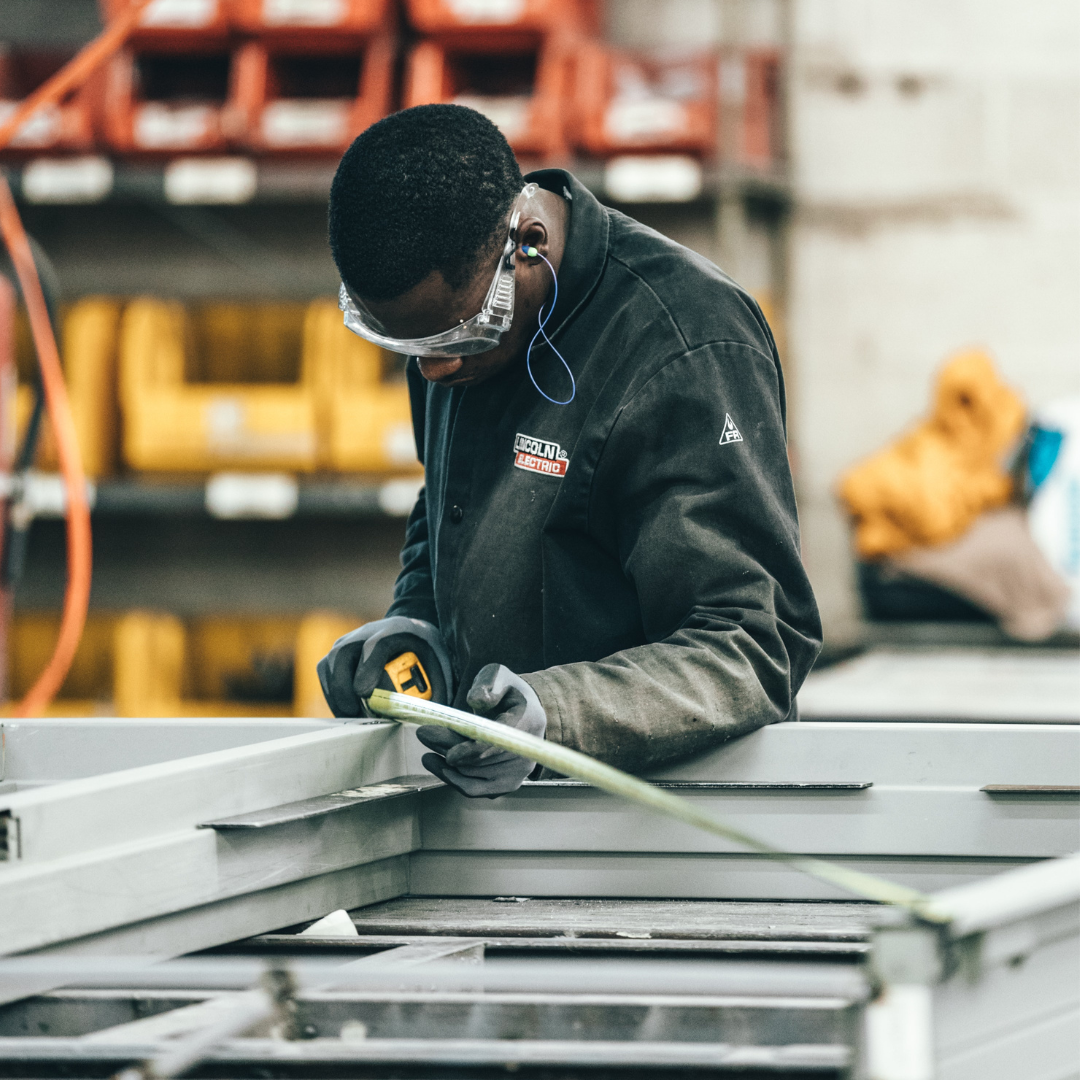
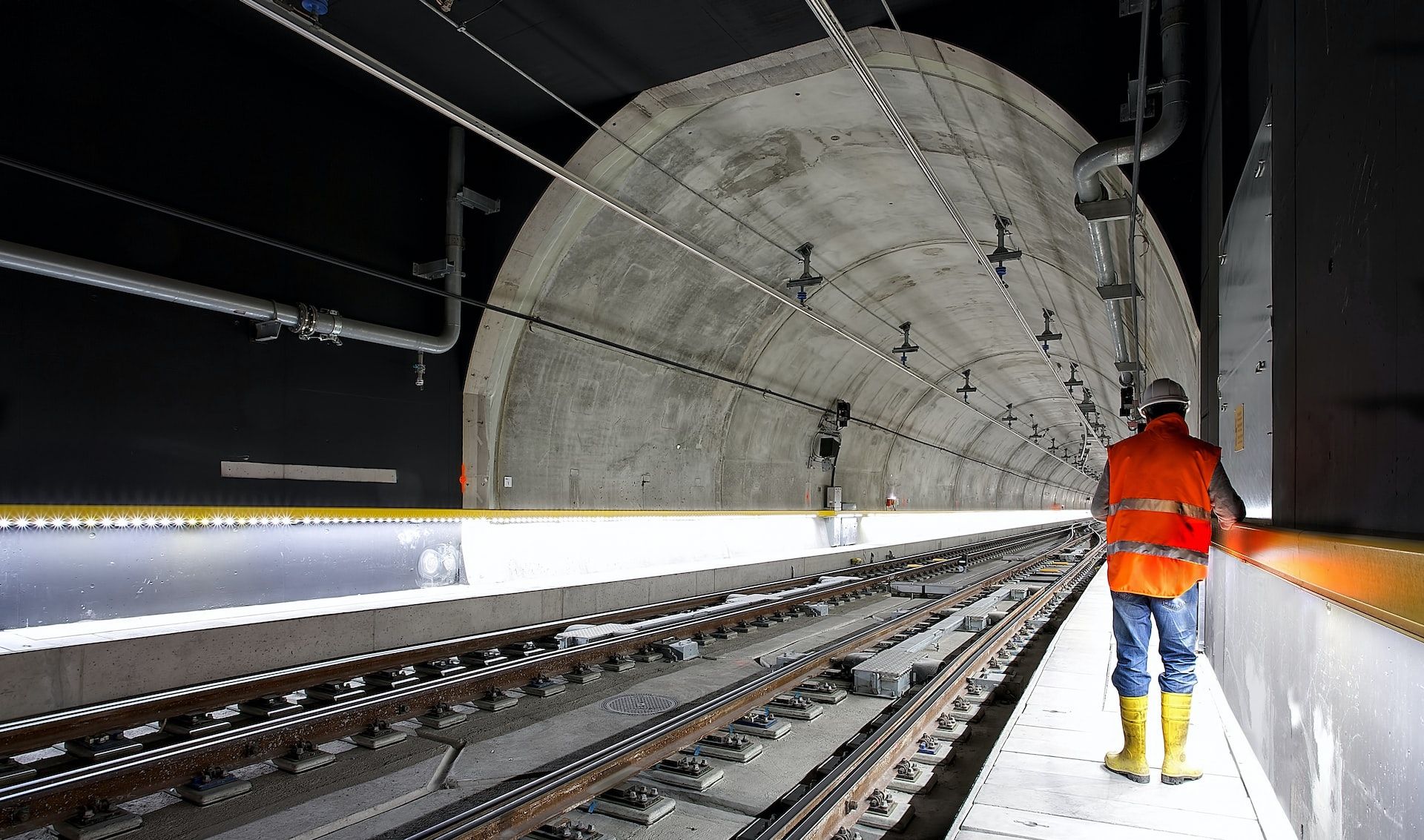
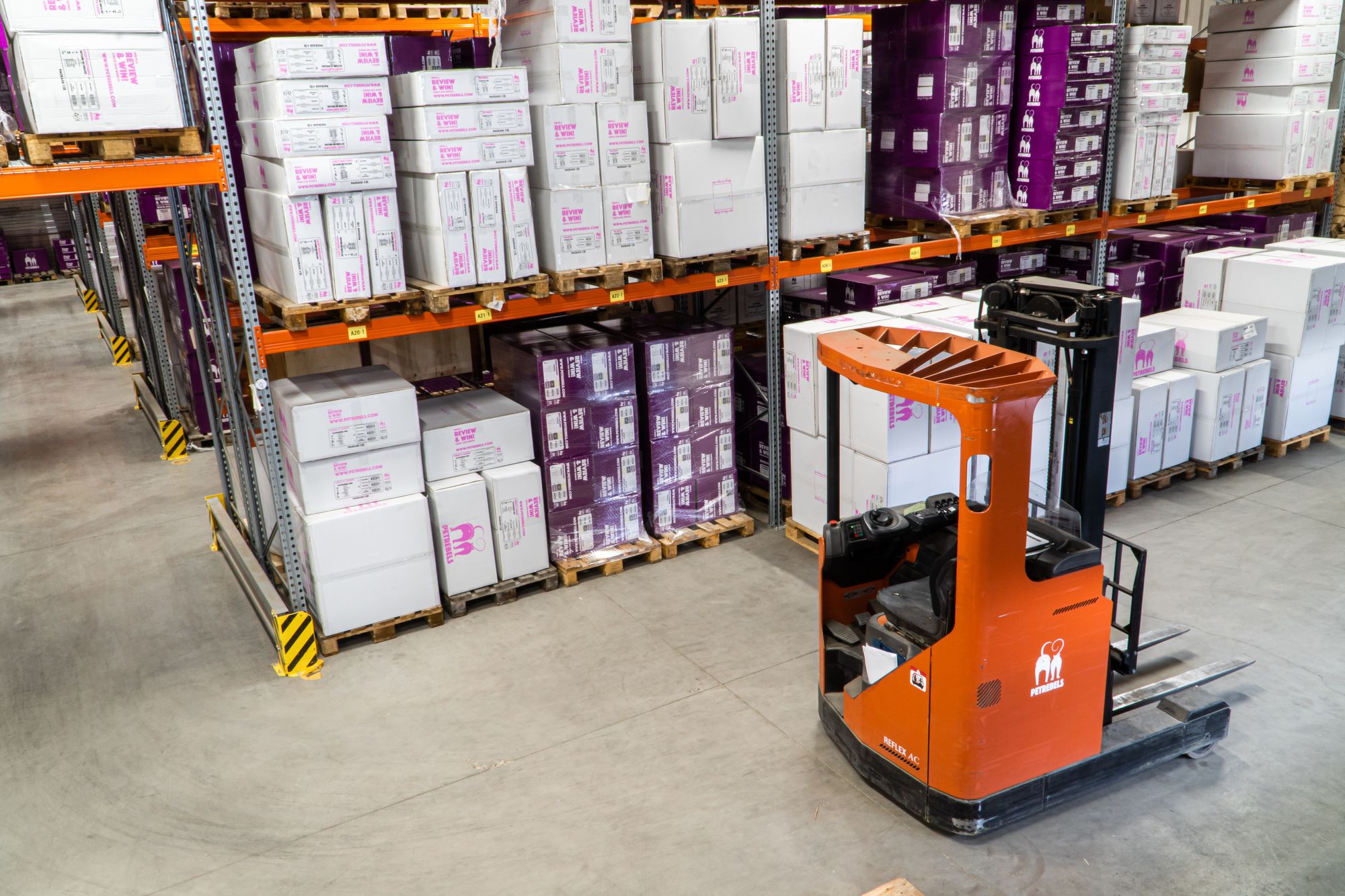
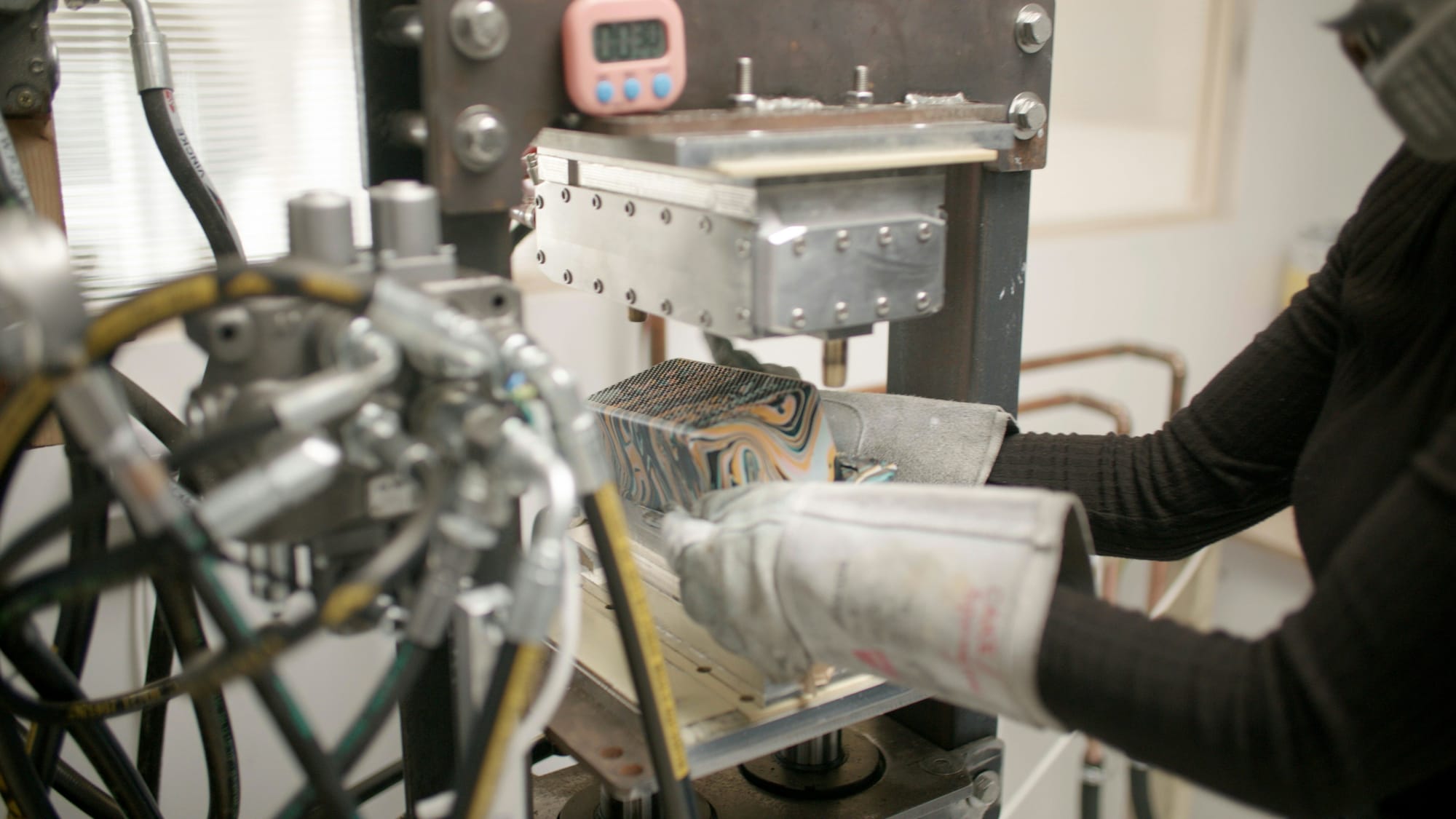
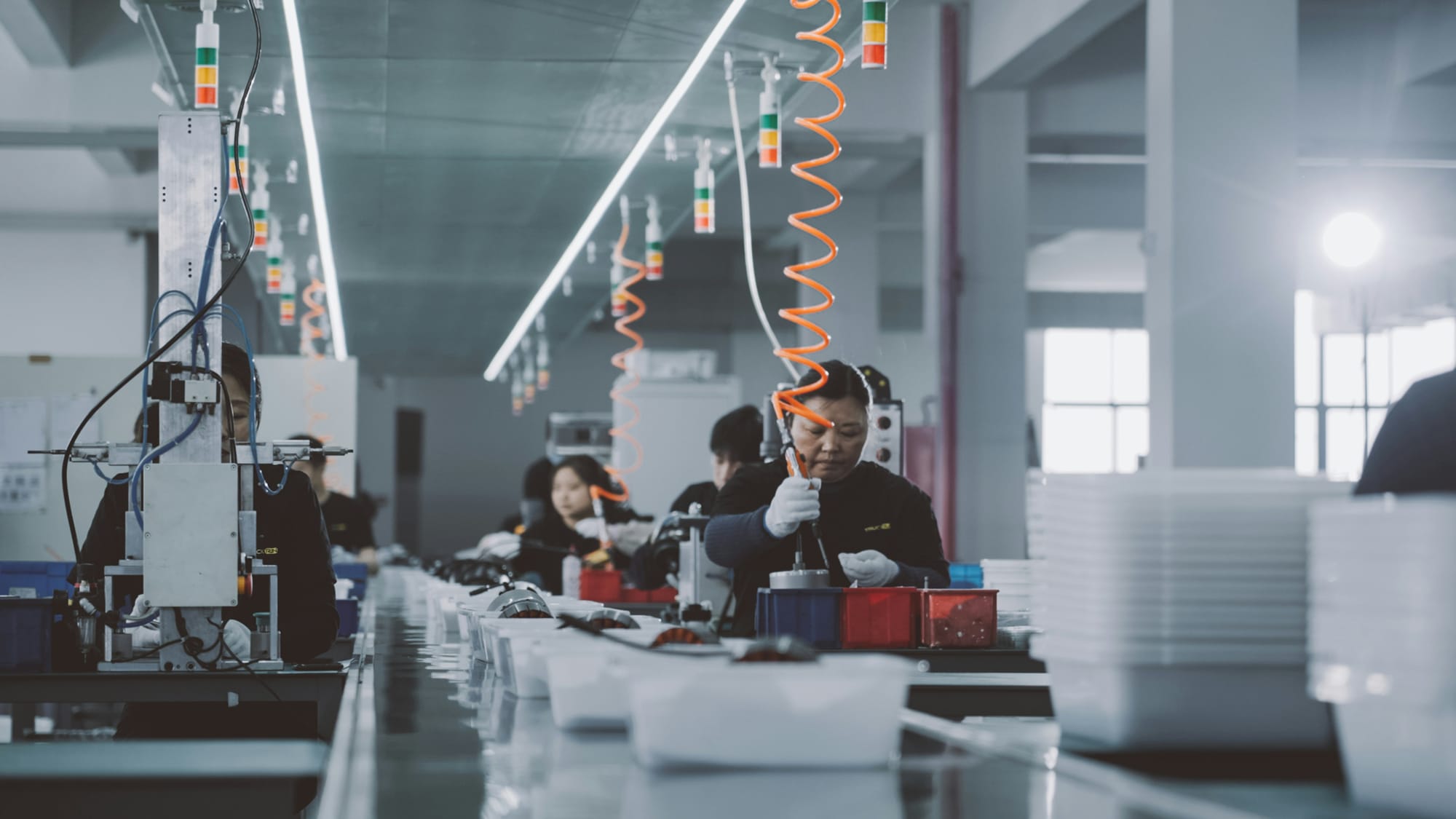