According to the latest statistics from the Plastics Industry Association, the US plastics industry continues to thrive, with a total of $432 billion in shipments and an estimated workforce of 989,000 in 2021.
With such a significant contribution to the country's economy, manufacturers are looking for ways to enhance their plastic production processes to remain competitive.
As technology continues to advance, plastic manufacturers are constantly looking for new and better ways to increase efficiency, reduce waste, and improve the overall quality of their products. In recent years, the use of the latest tools and technologies in plastic manufacturing has become more prevalent, and this trend is expected to continue into the future.
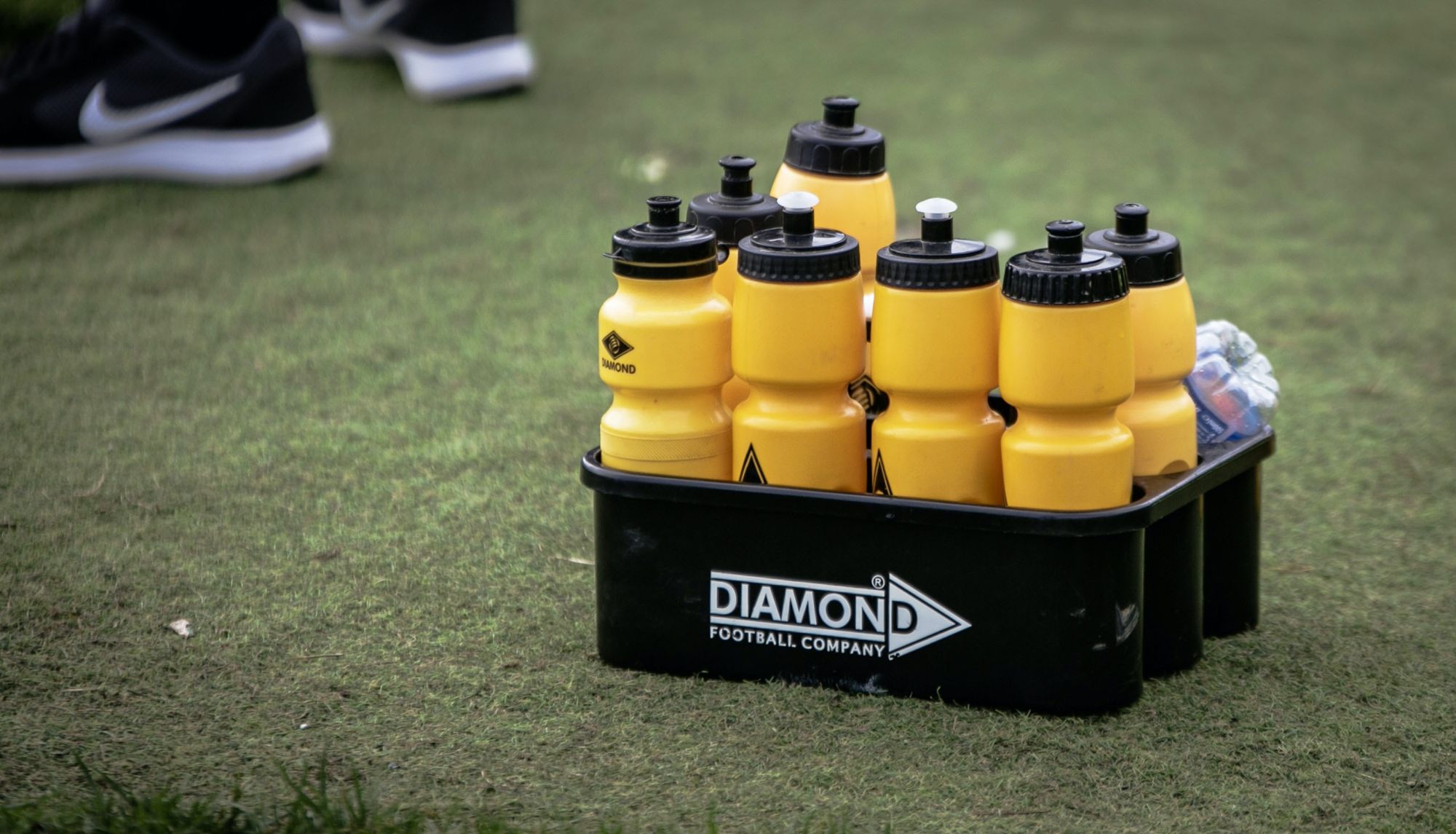
Are you ready to dive into the world of plastic manufacturing? From injection molding to blow molding, the technology used in the plastic manufacturing industry is constantly evolving. With new tools and techniques being developed every day, it can be challenging to keep up with the latest trends. But fear not, we've got you covered!
In this article, we'll explore the latest tools and technologies in plastic manufacturing and how they are changing the game. From 3D printing to automation, we'll take a deep dive into the future of plastic manufacturing.
Here's what we shall cover in this post:
- Overview of the Latest Tools and Technologies in Plastic Manufacturing
- Benefits of Incorporating Advanced Technologies in Plastic Production
- Computer-Aided Design (CAD) Software for Plastic Manufacturing
- Internet of Things (IoT) and Industry 4.0 in Plastic Manufacturing
- Virtual and Augmented Reality (VR/AR) in Plastic Manufacturing
- Nanotechnology in Plastic Production
- Biodegradable and Sustainable Plastics: Meeting the Demands of a Green Economy
- Quality Control and Testing in Plastic Production
- Conclusion
- Key Takeaways
Overview of the Latest Tools and Technologies in Plastic Manufacturing
Plastic manufacturing is a constantly evolving industry that requires adaptation to new technologies and tools to stay ahead of the competition. In recent years, significant advances have been made in the tools and technologies used in plastic manufacturing. These advancements have led to improvements in efficiency, cost-effectiveness, and the quality of plastic products.
- As the demand for plastic products grows, plastic manufacturers continuously seek ways to improve their production processes.
- To achieve this, manufacturers are investing in new tools and technologies to enhance their production capabilities.
- One of the most significant advancements in plastic manufacturing is 3D printing. 3D printing technology has revolutionized the manufacturing industry by allowing the creation of complex geometries with high precision and accuracy.
- In plastic manufacturing, 3D printing creates prototypes, produces low-volume production parts, and even end-use plastic parts.
- Another key technology in plastic manufacturing is injection molding. Injection molding is a manufacturing process that involves melting plastic pellets and injecting them into a mold to create a specific shape.
- Injection molding is used to manufacture a wide range of plastic products, from automotive parts to medical devices.
- Plastic manufacturers are also adopting new technologies such as robotics, automation, and artificial intelligence (AI) to streamline their production processes.
Overall, the latest tools and technologies in plastic manufacturing are helping manufacturers to produce high-quality plastic products with greater efficiency and at a lower cost. These technologies are also helping manufacturers to address environmental concerns by adopting more sustainable materials and reducing waste.
As the demand for plastic products continues to grow, manufacturers must continue to adapt to new tools and technologies to stay competitive in the industry.
Benefits of Incorporating Advanced Technologies in Plastic Production
Improved Efficiency and Productivity
Advanced technologies such as robotics, artificial intelligence, and automation can greatly improve the efficiency and productivity of plastic production. With the use of robots and automated systems, production processes can be streamlined, reducing the need for human intervention and increasing production speed.
By reducing human error and variability, advanced technologies can also improve the quality and consistency of plastic products.
Reduced Costs
The incorporation of advanced technologies can also lead to cost savings for plastic production operations. Companies can save money on production costs by reducing labor costs and increasing production speed.
Additionally, advanced technologies can help minimize waste and reduce material costs, further reducing the overall cost of plastic production.
Enhanced Safety
The use of advanced technologies in plastic production can also improve worker safety. For example, the use of robotic systems can reduce the need for workers to perform repetitive and potentially hazardous tasks.
Additionally, advanced sensors and monitoring systems can help identify potential safety hazards and alert workers to potential dangers in real time, reducing the risk of accidents and injuries.
Improved Sustainability
Advanced technologies can also help improve the sustainability of plastic production operations. For example, the use of automation and artificial intelligence can help optimize production processes, reducing the amount of waste generated during production.
Additionally, advanced materials and recycling technologies can help reduce the environmental impact of plastic production by creating more sustainable and eco-friendly products.
Increased Flexibility and Customization
Advanced technologies can also make plastic production operations more flexible and customizable. With the use of automation and robotics, production processes can be quickly reconfigured and adjusted to accommodate changes in production requirements.
Additionally, with the use of 3D printing and other advanced manufacturing techniques, companies can create highly customized plastic products tailored to the needs of individual customers.
Computer-Aided Design (CAD) Software for Plastic Manufacturing
Computer-aided design (CAD) software is an essential tool for plastic manufacturers. It allows designers and engineers to create and test designs digitally before they are physically produced, which can save time and money while improving accuracy and reducing waste.
Here are some of the benefits of using CAD software in plastic manufacturing:
- Improved Design Quality: CAD software provides designers with advanced tools to create detailed 3D models of products. This allows designers to visualize the final product and make necessary modifications before production, reducing the risk of design errors and improving the quality of the final product.
- Faster Time-to-Market: Designers can create and test product designs much faster than traditional methods with CAD software. This can significantly reduce the time it takes to bring a new product to market, giving manufacturers a competitive edge.
- Reduced Costs: By identifying and correcting design issues before production, manufacturers can avoid costly mistakes and reduce waste. CAD software also enables manufacturers to optimize their designs for efficient use of materials, which can lead to further cost savings.
- Enhanced Collaboration: CAD software enables multiple team members to work on a single project simultaneously, regardless of their location. This allows for seamless collaboration between designers, engineers, and other stakeholders, reducing the risk of miscommunication and ensuring that everyone is working towards a common goal.
- Improved Productivity: With CAD software, designers can automate many repetitive tasks, freeing up time for more complex design work. This can significantly improve productivity and efficiency in the design process, leading to a faster time-to-market and increased profitability.
- Better Visualization: CAD software allows designers to create detailed, realistic 3D models of products, which can be viewed from all angles. This provides a more accurate and detailed visualization of the product, helping designers and stakeholders to better understand the product's features, functionality, and aesthetics.
- Improved Documentation: CAD software provides detailed documentation of the design process, including design iterations, changes, and modifications. This can be useful for future reference and help ensure the design process is transparent and well-documented.
3D Printing in Plastic Manufacturing
3D printing, also known as additive manufacturing, has revolutionized the way products are manufactured in various industries, including the plastic manufacturing industry.
Rapid Prototyping: One of the key advantages of 3D printing is that it allows for the rapid prototyping of plastic parts.
This means that designers and engineers can quickly create and test different product design iterations before settling on the final version. This can save time and money in the product development process.
Customization: 3D printing also allows for greater customization of plastic parts. With traditional manufacturing processes, creating custom parts can be time-consuming and expensive.
However, with 3D printing, the process is relatively simple and cost-effective, making it ideal for creating custom parts for a range of applications.
Complex Geometries: Another advantage of 3D printing is that it allows for the creation of parts with complex geometries that would be difficult or impossible to produce with traditional manufacturing methods.
This opens up new design possibilities and allows for the creation of more complex and intricate products.
Reduced Waste: With traditional manufacturing methods, excess material is often generated during production, leading to wastage. However, with 3D printing, material wastage is significantly reduced as only the required amount of material is used in production.
Lower Costs: 3D printing can also result in lower costs compared to traditional manufacturing methods, especially for low-volume production runs. This is because the cost of tooling and setup is significantly reduced with 3D printing, making it a cost-effective option for small-scale production.
Tooling Production: 3D printing is also being used to produce tooling for plastic manufacturing processes.
With 3D printing, tooling can be produced more quickly and at a lower cost than with traditional tooling production methods. This allows for greater flexibility in the manufacturing process and reduces the time required to produce new tooling.
End-Use Parts: While 3D printing was initially used primarily for prototyping, it is now increasingly used to produce end-use plastic parts. With advances in 3D printing technology and materials, it is now possible to produce parts that meet the same quality and performance standards as those produced with traditional manufacturing methods.
Sustainability: 3D printing is also a more sustainable option for plastic manufacturing.
As mentioned earlier, it reduces material wastage and can also reduce energy consumption compared to traditional manufacturing methods. Additionally, 3D printing allows for the creation of more sustainable products by using recycled materials and designing products for efficient use of resources.
Robotics and Automation in Plastic Production
Robotics and automation have transformed the manufacturing industry by streamlining processes and boosting efficiency. In the plastic production industry, robotics and automation have played a crucial role in improving productivity, quality, and safety.
Here are some points that explain the role of robotics and automation in plastic production:
Improved accuracy and speed: Robotics and automation have improved the accuracy and speed of plastic production processes.
Robots can perform repetitive tasks with precision and consistency, reducing the likelihood of errors that can occur during manual operations. This can lead to increased production rates and reduced lead times.
Enhanced safety: Robotics and automation can help reduce the risk of workplace injuries in the plastic production industry. Robots can perform tasks that are hazardous to human workers, such as handling hot plastic or operating heavy machinery.
This can improve workplace safety and reduce workers' compensation claims.
Lower costs: Robotics and automation can help reduce labor costs in plastic production.
Robots can work around the clock, without the need for breaks or rest periods, increasing production rates and reducing the need for additional staff. Additionally, automation can help reduce waste and rework, leading to cost savings.
Increased efficiency: Automation can help streamline plastic production processes, reducing the time and resources required to produce a product. Automated systems can monitor and adjust process parameters, reducing variability and ensuring consistent quality.
Flexibility: Robotics and automation can be programmed to perform a variety of tasks, making them flexible and adaptable to changing production needs. This can help companies respond quickly to changing customer demands and production requirements.
Quality control: Robotics and automation can help improve quality control in plastic production. Automated systems can monitor and inspect products during production, detecting defects and ensuring that products meet required specifications.
This can help reduce the likelihood of defective products reaching customers and improve overall product quality.
Improved data collection and analysis: Automation can provide real-time data on production processes, allowing companies to monitor and analyze production performance. This data can be used to identify inefficiencies, make process improvements, and optimize production.
Enhanced sustainability: Automation can help improve the sustainability of plastic production processes by reducing waste and energy consumption. Automated systems can optimize processes, reducing the amount of material used and the energy required to produce a product.
Additionally, automation can help reduce the environmental impact of plastic production by reducing emissions and improving waste management practices.
Internet of Things (IoT) and Industry 4.0 in Plastic Manufacturing
The Internet of Things (IoT) and Industry 4.0 are transforming the plastic manufacturing industry by connecting machines and data, leading to better performance and efficiency. Here are some key points on how IoT and Industry 4.0 are impacting plastic manufacturing:
- Real-time monitoring and control: IoT enables real-time monitoring and control of machines and processes in plastic manufacturing, leading to better performance and reduced downtime. Sensors and cameras can be used to monitor the machines and processes, and the data can be analyzed to identify any anomalies or issues that need to be addressed.
- Predictive maintenance: IoT allows for predictive maintenance in plastic manufacturing, where machines can be monitored and analyzed to predict when they will need maintenance. This can help to prevent unexpected downtime and reduce maintenance costs.
- Supply chain optimization: IoT can be used to optimize the supply chain in plastic manufacturing by providing real-time data on inventory levels, production rates, and shipping times. This can help to reduce waste and improve overall efficiency.
- Improved quality control: IoT can be used to improve quality control in plastic manufacturing by providing real-time data on product quality and detecting any defects or issues that need to be addressed.
- Automated data collection and analysis: IoT enables automated data collection and analysis in plastic manufacturing, reducing the need for manual data entry and analysis. This can save time and improve accuracy in data collection and analysis.
- Integration with other technologies: IoT can be integrated with other technologies such as robotics, automation, and artificial intelligence to further improve efficiency and performance in plastic manufacturing.
- Increased transparency: IoT and Industry 4.0 can increase transparency in plastic manufacturing by providing real-time data on processes and performance, enabling better decision-making and collaboration between teams.
- Reduced costs: By improving efficiency, reducing downtime, and optimizing the supply chain, IoT and Industry 4.0 can help to reduce costs in plastic manufacturing.
Artificial Intelligence (AI) and Machine Learning in Plastic Production
Artificial Intelligence (AI) and Machine Learning (ML) are rapidly transforming industries around the world, and plastic manufacturing is no exception. With AI and ML, manufacturers can improve their processes, reduce waste, and enhance the quality of their products.
Predictive Maintenance: Another application of AI and ML in plastic manufacturing is predictive maintenance. By analyzing data from sensors and machines in real time, manufacturers can detect potential issues before they occur, such as equipment failures or production slowdowns.
This helps reduce downtime, improve efficiency, and lower maintenance costs.
Process Optimization: AI and ML can also be used to optimize plastic production processes. By analyzing data from sensors, machines, and other sources, manufacturers can identify inefficiencies and bottlenecks in their processes and make data-driven decisions to improve them.
This can help increase throughput, reduce waste, and improve the overall efficiency of the production line.
Product Design: AI and ML can also play a role in product design. Manufacturers can use AI-powered algorithms to generate optimized designs for plastic products by analyzing customer preferences, market trends, and materials. This can lead to better products that meet customer needs more effectively.
Autonomous Operations: As AI and ML technologies continue to develop, they may also play a role in autonomous operations in plastic manufacturing. This would involve machines and processes being able to operate independently, making decisions and adjustments based on real-time data.
This would help reduce the need for human intervention, lower the risk of errors, and improve overall efficiency.
Virtual and Augmented Reality (VR/AR) in Plastic Manufacturing
The plastic manufacturing industry has always been at the forefront of technological advancements. With the introduction of virtual and augmented reality (VR/AR) technologies, the industry has further enhanced its capabilities in the areas of design, production, and training.
Design: VR/AR technologies allow designers to create and view 3D models in real time, providing a more immersive and interactive experience. This technology enables designers to visualize and manipulate a design before it's produced, making it easier to spot design flaws and make necessary adjustments.
The use of VR/AR technology also speeds up the design process, as designers can quickly make changes and see how they affect the final product.
Training: VR/AR technologies can potentially revolutionize how employees are trained in the plastic manufacturing industry. With VR/AR, employees can receive hands-on training without the risk of injury or damage to equipment.
This technology enables employees to practice various scenarios, such as troubleshooting and machine operation, in a safe and controlled environment. VR/AR also provides a more engaging and interactive learning experience, which can improve knowledge retention and overall performance.
Quality Control: VR/AR technologies are also being used to improve quality control in plastic manufacturing. These technologies allow manufacturers to create virtual environments that mimic real-world production lines, enabling them to identify potential issues and make necessary adjustments before production begins.
This technology also allows manufacturers to simulate different production scenarios, optimizing production processes and reducing waste.
Assembly: VR/AR technologies can also be used to aid in the assembly process of plastic products. By creating a virtual environment, manufacturers can provide employees with step-by-step instructions on how to assemble a product.
This technology enables employees to visualize the assembly process more interactively and engagingly, making it easier for them to understand and follow the instructions.
Sales and Marketing: VR/AR technologies are also being used to enhance sales and marketing efforts in the plastic manufacturing industry. Manufacturers can showcase their products more interactively and engagingly by creating virtual product demonstrations.
This technology also lets customers visualize how a product will look and function before making a purchase, increasing customer satisfaction.
Digital Twin Technology in Plastic Production
Digital twin technology has become increasingly popular in the manufacturing industry, including plastic production. It refers to a virtual replica of a physical system, allowing for real-time simulation and analysis of its behavior.
In plastic manufacturing, digital twins can be used to create virtual models of machines, production lines, and even entire factories. This technology has numerous benefits, including predictive maintenance, optimization, and improved efficiency.
Optimization: Digital twins can also be used to optimize production processes. By analyzing data from sensors and other sources, manufacturers can identify inefficiencies and bottlenecks in their production lines.
This information can then be used to make adjustments and improvements, leading to increased productivity and cost savings. Digital twins can also be used to simulate different scenarios, allowing manufacturers to test and refine their production processes before implementing them in the physical world.
Improved efficiency: By using digital twin technology, manufacturers can better understand how their production processes work.
This can help identify areas where efficiency can be improved, reducing waste and increasing output. Digital twins can also be used to simulate different operating conditions, allowing manufacturers to optimize their processes for different scenarios.
Real-time monitoring: Digital twin technology can provide real-time monitoring of production processes. By collecting data from sensors and other sources, manufacturers can monitor the performance of individual machines and production lines.
This can help to identify potential issues before they occur, allowing for proactive maintenance and repairs. Real-time monitoring can also be used to optimize production processes and improve efficiency.
Cost savings: Digital twin technology can help manufacturers reduce costs in several ways. Manufacturers can reduce downtime and increase productivity by facilitating predictive maintenance and optimizing production processes.
This can lead to cost savings through increased efficiency and reduced waste. Digital twins can also be used to simulate different scenarios, allowing manufacturers to test and refine their processes before implementing them in the physical world.
Advanced Materials and Additives for Plastic Manufacturing
Improved Performance: Advanced materials and additives can improve the performance of plastic products. For example, adding glass fibers to plastic materials can increase their strength and stiffness, while adding fillers such as talc or calcium carbonate can improve their dimensional stability and reduce shrinkage.
Similarly, adding flame retardants can improve fire resistance, and UV stabilizers can enhance weather ability.
Sustainable Production: Advanced materials and additives can also help in making plastic production more sustainable.
For example, biodegradable plastics made from plant-based materials such as cornstarch or cellulose can be used as an alternative to traditional petroleum-based plastics. Additionally, recycled plastic materials can be used in manufacturing to reduce waste and conserve resources.
Health and Safety: Advanced materials and additives can also improve the health and safety of plastic products. For example, using phthalate-free plasticizers can reduce the risk of health hazards, while using antimicrobial additives can prevent the growth of harmful bacteria on plastic surfaces.
Innovation: Advanced materials and additives also enable manufacturers to create new and innovative products. For example, using self-healing polymers can create materials that can repair themselves when damaged, while using shape-memory polymers can create materials that can change shape in response to temperature changes.
Nanotechnology in Plastic Production
Nanotechnology is a rapidly evolving field that involves the manipulation of materials at the nanoscale, typically 1-100 nanometers. In plastic production, nanotechnology is used to improve the performance of plastics by enhancing their mechanical, thermal, and barrier properties.
Here are some of the key ways that nanotechnology is being used to create high-performance plastics:
- Nano-fillers: Nano-fillers such as nano clays, carbon nanotubes, and graphene are used to reinforce plastics, improving their strength and stiffness. They can also improve thermal and barrier properties, making them useful for applications such as food packaging.
- Nano-coatings: Nano-coatings can be applied to plastic surfaces to improve scratch resistance, reduce friction, and enhance barrier properties. They are commonly used in applications such as automotive parts, electronic devices, and medical devices.
- Nanocomposites: Nanocomposites are made by combining nanoparticles with a polymer matrix, resulting in a material with enhanced mechanical, thermal, and barrier properties. They can be used in a wide range of applications, including automotive parts, aerospace components, and electronic devices.
- Nanofibers: Nanofibers can be produced by electrospinning, a process that creates ultra-thin fibers from a polymer solution. They have a high surface area and can be used to create filters, membranes, and wound dressings.
- Nanoporous materials: Nanoporous materials have a high surface area and can be used to create materials with excellent adsorption and catalytic properties. They are used in water purification, gas separation, and catalysis applications.
The benefits of using nanotechnology in plastic production are numerous. By enhancing the performance of plastics, nanotechnology can enable the development of new applications and products that were previously not possible. Some of the key benefits of using nanotechnology in plastic production include the following:
- Improved mechanical properties: Nano-fillers and nanocomposites can significantly improve the strength, stiffness, and toughness of plastics, making them suitable for a wider range of applications.
- Enhanced thermal properties: Nano-fillers and nanocomposites can improve the thermal stability of plastics, making them suitable for high-temperature applications.
- Improved barrier properties: Nano-coatings and nanocomposites can enhance the barrier properties of plastics, making them useful for applications such as food packaging.
- Improved sustainability: By improving the performance of plastics, nanotechnology can enable the development of more sustainable products. For example, nanotechnology can be used to create biodegradable plastics that have improved mechanical properties and are more environmentally friendly.
Despite the numerous benefits of using nanotechnology in plastic production, some potential risks and challenges need to be considered. Some of the key challenges and risks include:
- Cost: The cost of producing nanomaterials can be higher than traditional materials, making it challenging to scale up production.
- Health and safety: There is still limited information on the potential health and safety risks associated with the use of nanomaterials in plastic production. It is important to ensure that appropriate safety measures are taken to protect workers and consumers.
- Environmental impact: The environmental impact of nanomaterials is still poorly understood, and there is a risk that they could negatively impact the environment.
Biodegradable and Sustainable Plastics: Meeting the Demands of a Green Economy
What are biodegradable and sustainable plastics?
Biodegradable plastics are designed to break down naturally into harmless substances when exposed to the environment. They are made from renewable materials such as corn, potato, or cellulose and do not release harmful chemicals when decomposing.
On the other hand, sustainable plastics are made from renewable or recycled materials and have a lower environmental impact than conventional plastics. They are designed to be reused, recycled, or biodegraded at the end of their lifecycle.
Benefits of biodegradable and sustainable plastics
One of the main benefits of biodegradable and sustainable plastics is their lower environmental impact. They produce fewer greenhouse gas emissions and are less harmful to wildlife and ecosystems when disposed of properly.
These plastics also have the potential to reduce the dependence on non-renewable resources such as petroleum, as they are made from renewable or recycled materials.
Furthermore, using biodegradable and sustainable plastics can help companies meet the growing demand for sustainable products, leading to increased customer loyalty and market share.
Challenges of biodegradable and sustainable plastics
While biodegradable and sustainable plastics offer many benefits, there are also challenges associated with their production and use. For example, producing biodegradable plastics often requires more energy and resources than conventional plastics, which can offset their environmental benefits.
There is also the waste management issue, as biodegradable plastics require specific conditions to break down properly and can contaminate recycling streams if not disposed of correctly.
Finally, the cost of biodegradable and sustainable plastics can be higher compared to conventional plastics, which may limit their adoption in certain industries.
Applications of biodegradable and sustainable plastics
Biodegradable and sustainable plastics are being used in a growing number of applications, from packaging materials to consumer goods.
In the packaging industry, biodegradable plastics are used to create food packaging, shopping bags, and other products designed to be disposed of after use.
In the automotive industry, sustainable plastics are being used to create interior and exterior parts that are durable and lightweight, reducing the weight of the vehicle and improving fuel efficiency.
Environmental Monitoring and Control in Plastic Manufacturing
Plastic manufacturing has always been a controversial industry due to its impact on the environment. However, with the rise of sustainability and green practices, plastic manufacturers are now more responsible for minimizing their environmental footprint. In this context, environmental monitoring and control have become crucial in ensuring compliance and safety in plastic manufacturing.
Advanced technologies and tools are being used to monitor and control the environmental impact of plastic manufacturing.
The Importance of Environmental Monitoring and Control in Plastic Manufacturing
Environmental monitoring and control in plastic manufacturing are critical for two main reasons. First, plastic manufacturing significantly impacts the environment, and it is necessary to monitor and control this impact to minimize environmental damage.
Second, environmental monitoring and control are essential to ensure compliance with local and international regulations.
Tools and Technologies for Environmental Monitoring and Control in Plastic Manufacturing
Plastic manufacturers can use several tools and technologies for environmental monitoring and control. Some of the most common ones include:
- Air Pollution Monitoring Systems: Air pollution monitoring systems are used to monitor the emissions from plastic manufacturing facilities. These systems can detect the presence of harmful gases and particulate matter in the air and alert plant managers when emissions exceed permissible limits. Advanced air pollution monitoring systems can also automatically adjust the plant's operations to minimize emissions.
- Water Quality Monitoring Systems: Water quality monitoring systems are used to monitor the quality of water used in plastic manufacturing processes. These systems can detect the presence of harmful chemicals and pollutants in the water and alert plant managers when the water quality is compromised. Advanced water quality monitoring systems can also automatically adjust the plant's operations to minimize water usage and optimize wastewater treatment.
- Noise Monitoring Systems: Noise monitoring systems are used to monitor the noise levels in and around plastic manufacturing facilities. These systems can detect excessive noise levels and alert plant managers when the noise exceeds permissible limits. Advanced noise monitoring systems can also automatically adjust the plant's operations to minimize noise levels.
- Energy Monitoring Systems: Energy monitoring systems are used to monitor the energy consumption of plastic manufacturing facilities. These systems can detect excessive energy consumption and alert plant managers when energy usage exceeds permissible limits. Advanced energy monitoring systems can also automatically adjust the plant's operations to minimize energy consumption.
- Environmental Management Systems: Environmental management systems (EMS) are used to manage and control the environmental impact of plastic manufacturing processes. EMS typically consists of a set of procedures and policies that help plant managers identify and control environmental risks. Advanced EMS can also incorporate real-time monitoring systems and automatic control mechanisms to minimize environmental impact.
Benefits of Environmental Monitoring and Control in Plastic Manufacturing
- There are several benefits of environmental monitoring and control in plastic manufacturing. Some of the most significant benefits include:
- Reduced Environmental Impact: Environmental monitoring and control can help plastic manufacturers reduce their environmental footprint by minimizing emissions, conserving water, and reducing energy consumption.
- Compliance with Regulations: Environmental monitoring and control can help plastic manufacturers comply with local and international regulations, avoiding fines and penalties for non-compliance.
- Enhanced Corporate Social Responsibility: Plastic manufacturers can demonstrate their commitment to sustainable practices and enhance their corporate social responsibility by implementing environmental monitoring and control measures.
- Improved Operational Efficiency: Environmental monitoring and control can help plastic manufacturers optimize their operations, reduce waste, and increase efficiency, ultimately improving their bottom line.
Quality Control and Testing in Plastic Production
Quality control and testing play a crucial role in the production of plastic products. The use of advanced technology in quality control and testing ensures that the produced products meet the required standards and are of high quality.
Here are some key points on the importance of quality control and testing in plastic production:
- Ensuring Consistency: Quality control and testing play a vital role in ensuring that the plastic products produced are consistent in terms of quality, strength, durability, and other parameters. This helps to prevent any defects or flaws that may result in product failures, which can lead to safety issues and financial losses.
- Meeting Customer Requirements: Quality control and testing are critical to meeting customer requirements and specifications. With the use of advanced technology, manufacturers can produce high-quality products that meet customer expectations and comply with industry standards and regulations.
- Preventing Defects: Quality control and testing can help prevent defects in production. By identifying any defects early in the manufacturing process, manufacturers can take corrective action to prevent further defects and ensure that the final product meets the desired quality standards.
- Improving Efficiency: Quality control and testing can also help to improve efficiency in the production process. By identifying any potential issues early on, manufacturers can minimize downtime and avoid the need for costly rework or product recalls.
- Ensuring Safety: Quality control and testing are also essential for ensuring product safety. By testing products for their strength, durability, and other properties, manufacturers can ensure that their products are safe for use and will not pose any risks to consumers.
- Non-Destructive Testing: Non-destructive testing (NDT) is a type of quality control and testing that does not damage the product being tested. This method is commonly used to produce plastic products to identify defects or flaws without damaging the product itself.
- Advanced Testing Techniques: Advanced testing techniques, such as spectroscopy, thermal analysis, and microscopy, are commonly used in the production of plastic products. These techniques can help to identify any defects or flaws in the product and provide valuable information on the product's properties and performance.
- Testing Standards and Regulations: Manufacturers must comply with various testing standards and regulations in producing plastic products. These standards and regulations ensure that the products produced meet specific quality requirements and are safe for use.
Maintenance and Troubleshooting in Plastic Manufacturing
Develop a Maintenance Plan: A comprehensive maintenance plan is critical to ensuring that all equipment and machinery operate efficiently.
A maintenance plan should outline specific tasks and schedules for routine maintenance, including cleaning, lubrication, and replacing worn or damaged parts. It should also include procedures for addressing unexpected downtime and emergency repairs.
Regularly Inspect Equipment: Regular inspections can help identify potential problems before they become major. Inspections should include visual checks for signs of wear and damage and tests for the proper functioning of all components. The frequency of inspections will depend on the equipment and the specific manufacturing process.
Invest in Condition Monitoring: Condition monitoring involves using sensors and other technology to continuously monitor equipment performance and identify potential problems.
This approach can help to detect issues early before they result in downtime or quality issues. Advanced condition monitoring systems can provide real-time data and predictive analytics to help optimize performance and reduce maintenance costs.
Train Staff: Proper training is critical to ensuring that staff can identify and address potential issues. Training should include general safety procedures and specific procedures for each piece of equipment.
Regular refresher training can help ensure that all staff is current on the latest maintenance and troubleshooting practices.
Use Data Analytics: Data analytics can be used to monitor equipment performance and identify trends and patterns that can help to predict future issues. This approach can help to optimize maintenance schedules and minimize downtime. Advanced analytics can also optimize production processes and improve product quality.
Have a Contingency Plan: Despite best efforts, unexpected downtime can still occur. Having a contingency plan in place can help to minimize the impact of these events.
This plan should include procedures for quickly identifying the cause of the downtime, identifying potential workarounds or backup equipment, and mobilizing repair teams.
Invest in Remote Monitoring: Remote monitoring involves using sensors and other technology to monitor equipment performance remotely. This approach can help to identify issues quickly and minimize downtime, as repair teams can be mobilized quickly.
Remote monitoring can also provide real-time data and predictive analytics to help optimize performance and reduce maintenance costs.
How Deskera Can Assist You?
Deskera MRP allows you to closely monitor the manufacturing process. From the bill of materials to the production planning features, the solution helps you stay on top of your game and keep your company's competitive edge.
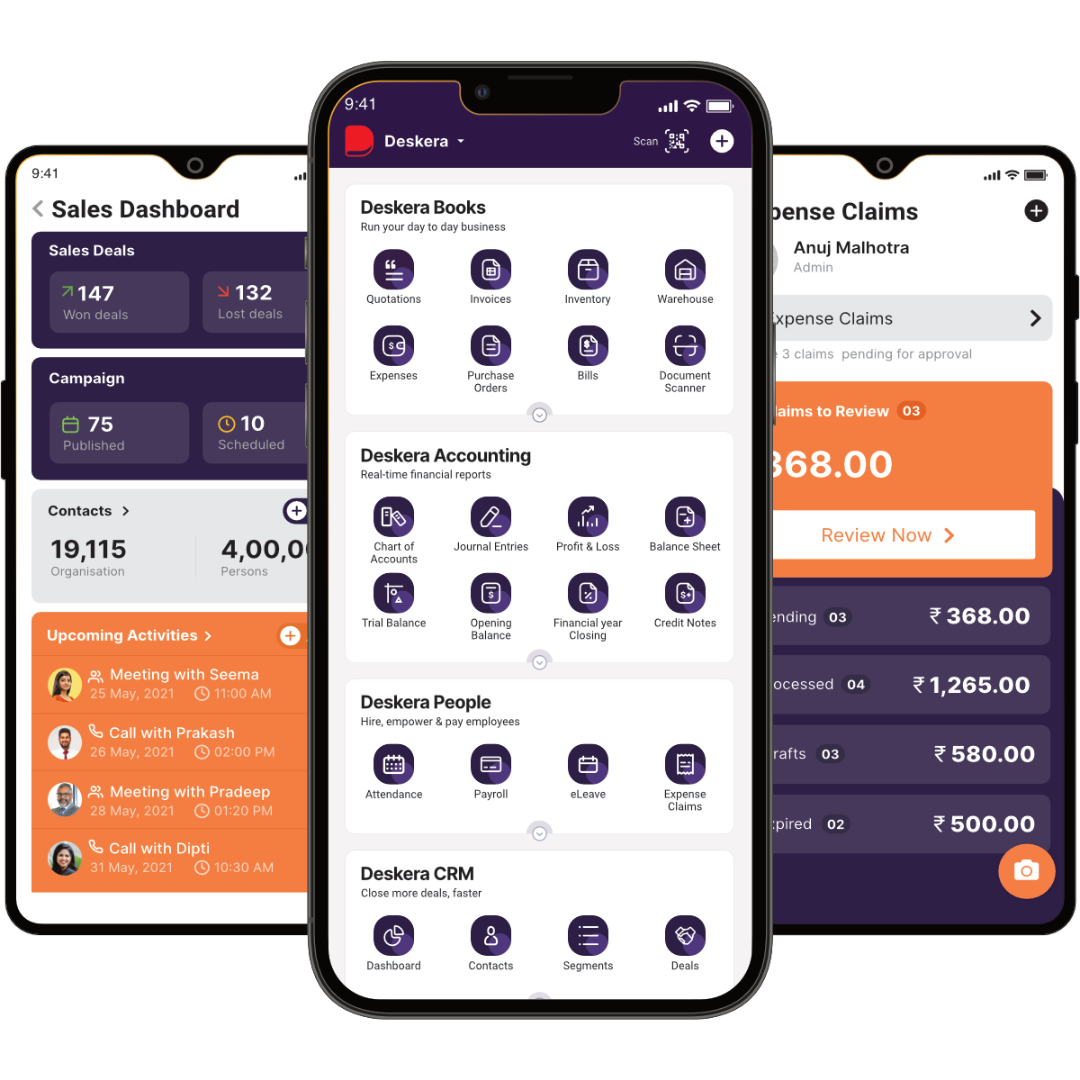
Deskera ERP and MRP system can help you:
- Manage production plans
- Maintain Bill of Materials
- Generate detailed reports
- Create a custom dashboard
Deskera ERP is a comprehensive system that allows you to maintain inventory, manage suppliers, and track supply chain activity in real-time, as well as streamline a variety of other corporate operations.
Deskera Books enables you to manage your accounts and finances more effectively. Maintain sound accounting practices by automating accounting operations such as billing, invoicing, and payment processing.
Deskera CRM is a strong solution that manages your sales and assists you in closing agreements quickly. It not only allows you to do critical duties such as lead generation via email, but it also provides you with a comprehensive view of your sales funnel.
Deskera People is a simple tool for taking control of your human resource management functions. The technology not only speeds up payroll processing but also allows you to manage all other activities such as overtime, benefits, bonuses, training programs, and much more. This is your chance to grow your business, increase earnings, and improve the efficiency of the entire production process.
Conclusion
Plastic manufacturing is a complex and dynamic process that requires precision, efficiency, and safety. With the rapid advancement of technology, various tools, and technologies are available to streamline plastic manufacturing and optimize the process.
These tools range from 3D printing to AI-powered robots and augmented reality (AR) to IoT devices that can track and monitor every aspect of the manufacturing process. When combined with expert knowledge and experience, these tools and technologies can help manufacturers create high-quality plastic products that meet the needs of consumers and industries worldwide.
However, it's important to remember that implementing new technologies also requires careful planning, risk assessment, and ongoing monitoring and maintenance to ensure they function safely and efficiently.
By staying up-to-date with the latest developments in plastic manufacturing and utilizing the right tools and technologies, manufacturers can improve their operations and stay competitive in a constantly evolving industry.
Key Takeaways
- Utilizing the latest tools and technologies in plastic manufacturing can greatly enhance the efficiency and productivity of the process.
- One of the most important technologies for plastic manufacturing is 3D printing, which enables the creation of complex plastic parts with great accuracy.
- Another important tool is computer-aided design (CAD) software, which enables engineers to design and test plastic parts before manufacturing.
- Robotic automation is also a valuable technology in plastic manufacturing, as it can perform repetitive and labor-intensive tasks with great accuracy and speed.
- Advances in material science are also driving innovation in plastic manufacturing, as new materials are being developed that offer greater strength, durability, and flexibility.
- Smart sensors and internet of things (IoT) devices are also being integrated into plastic manufacturing processes to monitor production and ensure quality control.
- The use of renewable energy sources, such as solar or wind power, is becoming increasingly popular in plastic manufacturing as companies strive to reduce their carbon footprint.
- Collaborative robots, or cobots, are becoming more prevalent in plastic manufacturing as they can work alongside human workers to enhance efficiency and safety.
- Augmented reality (AR) and virtual reality (VR) technologies are also used in plastic manufacturing to train workers and simulate production processes.
- Cloud computing and big data analytics are also playing a role in plastic manufacturing, enabling companies to analyze production data and identify areas for improvement.
Related Articles
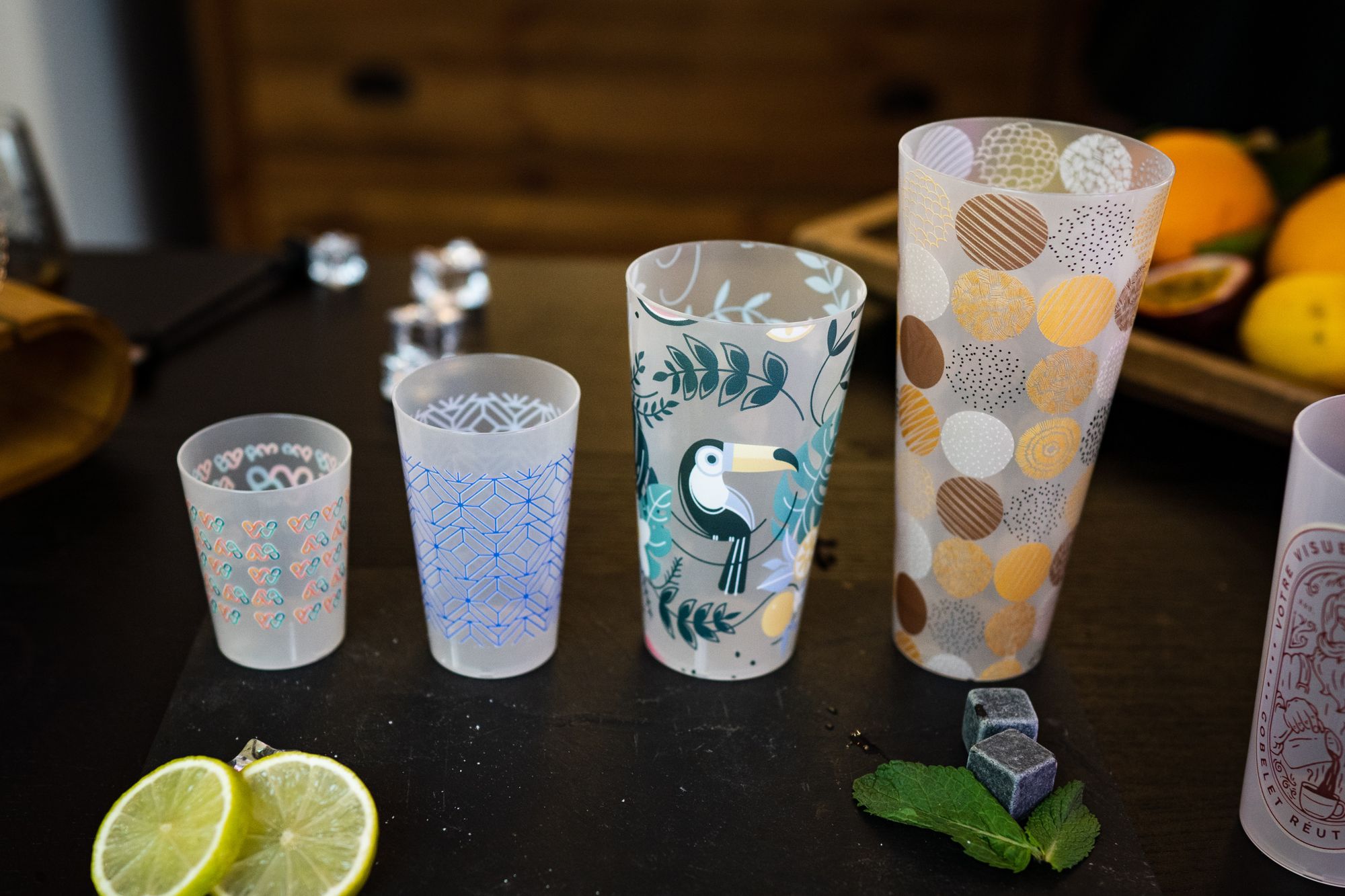
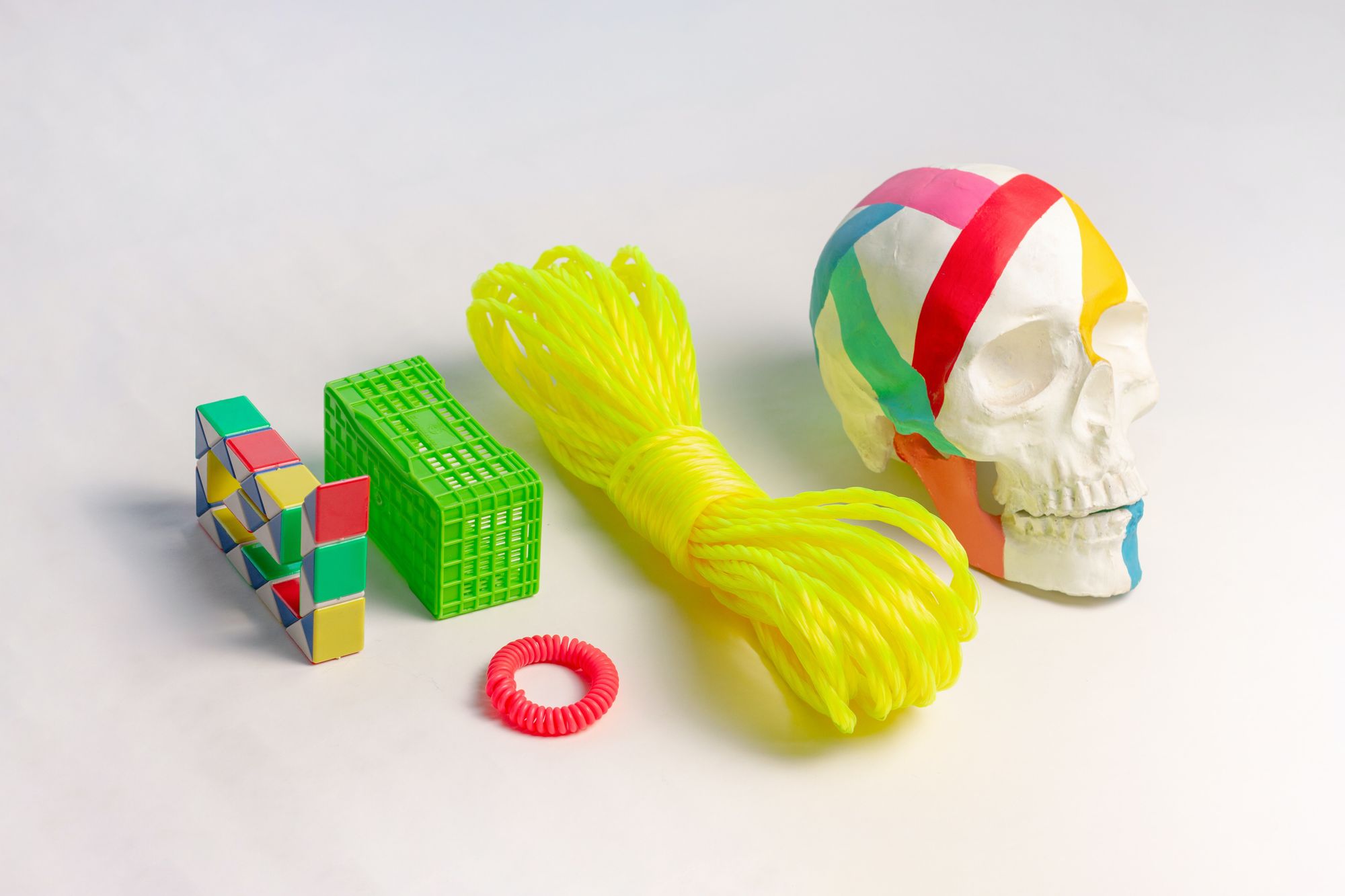
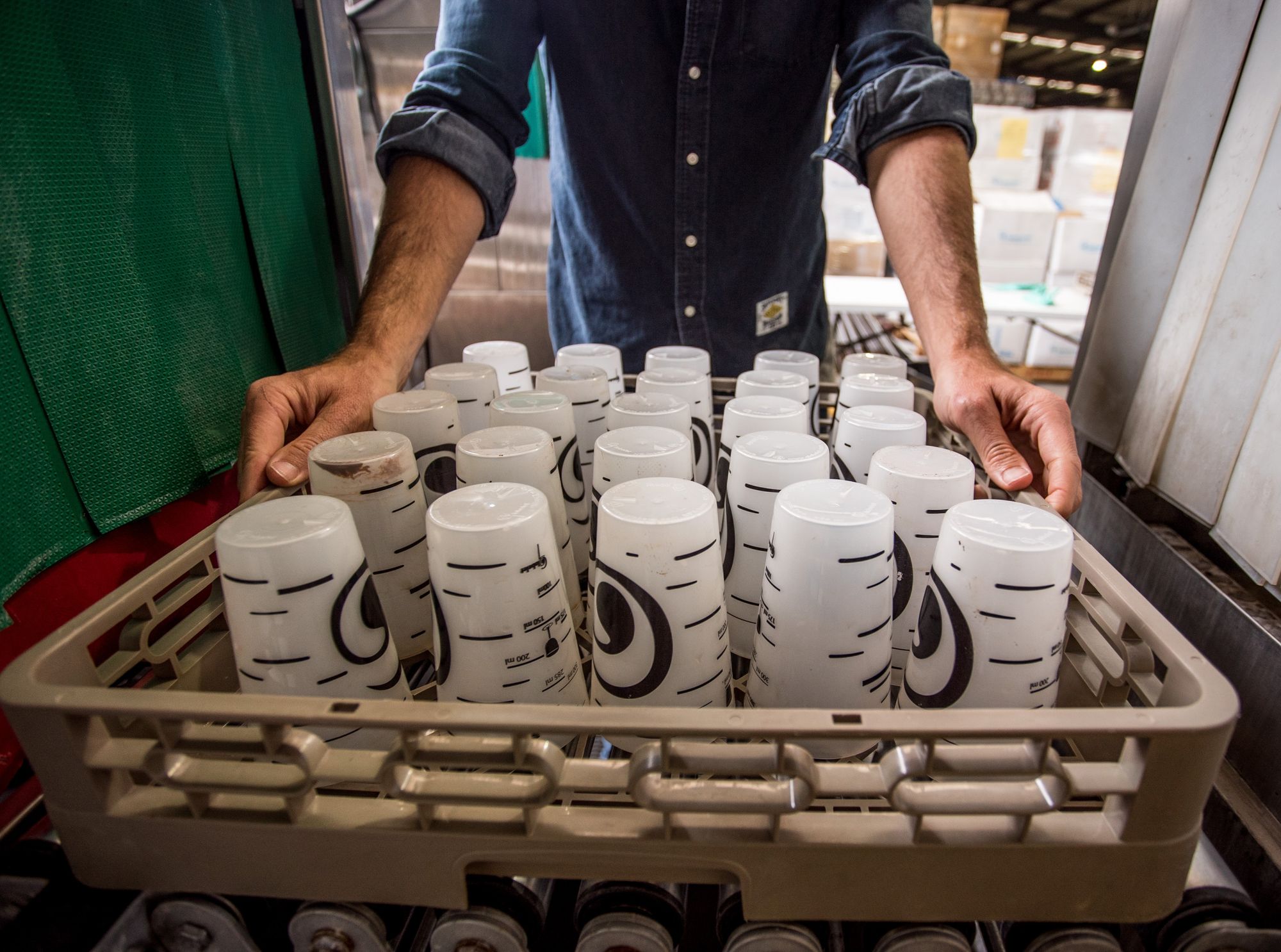
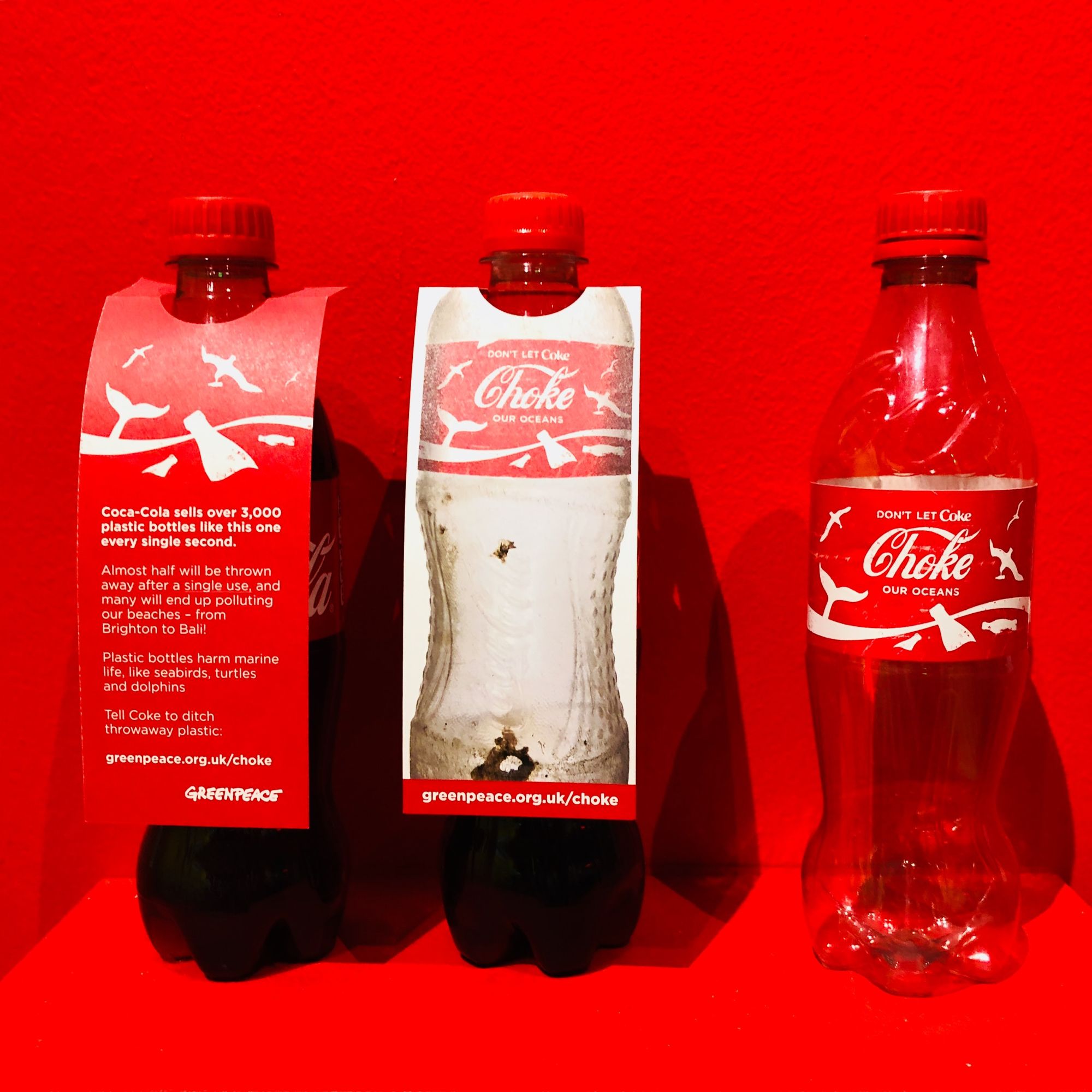