Are you looking for a way to improve your company's productivity and performance? If so, Total Quality Management (TQM) may be the solution for you. TQM is a management approach that seeks to optimize the quality and efficiency of all aspects of a company's operations.
By implementing TQM, organizations can improve customer satisfaction, reduce costs, and enhance their competitiveness. TQM emphasizes continuous improvement, customer focus, and employee empowerment.
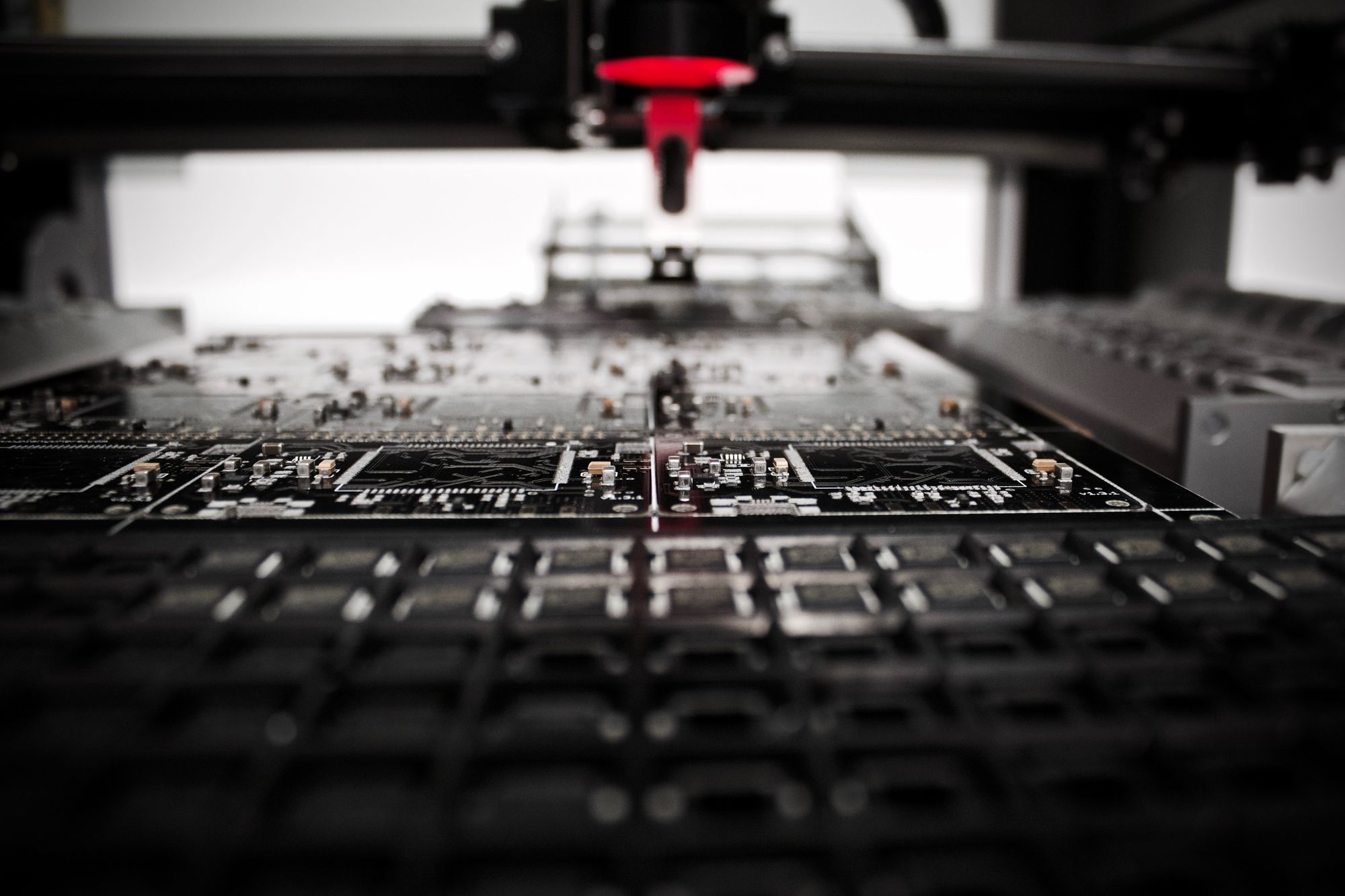
It involves a holistic approach to quality management encompassing all business areas, including product design, production processes, supply chain management, and customer service. The goal of TQM is to create a culture of quality throughout the organization, with everyone working together toward the common goal of excellence.
In this article, we will explore the principles and benefits of TQM and provide insights into how it can be successfully implemented in modern businesses. So, let's dive into the world of Total Quality Management and see how it can transform your business.
Here's what we shall cover in this post:
- Introduction to Total Quality Management
- Principles of Total Quality Management
- Challenges of Implementing Total Quality Management
- Developing a Total Quality Management Strategy
- Continuous Improvement and Total Quality Management
- Tools and Techniques for Implementing Total Quality Management
- Measuring Total Quality Management Effectiveness
- Common Total Quality Management Frameworks and Certifications
- Conclusion
- Key Takeaways
Introduction to Total Quality Management
Total Quality Management (TQM) is an approach to management that emphasizes continuous improvement and customer satisfaction.
- TQM is a philosophy focused on improving the overall quality of an organization's products, services, and processes.
- The concept of TQM is based on the idea that quality should be an integral part of an organization's culture and that everyone in the organization should be responsible for ensuring that quality standards are met.
- TQM involves various techniques and tools used to improve processes and eliminate defects, such as statistical process control, root cause analysis, and continuous improvement teams.
- TQM is often associated with manufacturing and industrial settings, but it can be applied to any organization that is focused on improving quality and customer satisfaction.
- TQM requires a commitment to continuous improvement and a willingness to change processes and systems to achieve better results.
- TQM is not a one-time initiative but a long-term commitment to improving quality and customer satisfaction.
The Importance of Quality in Business
Quality is an essential aspect of business that cannot be ignored if a company wants to remain competitive in the market. It is the cornerstone of customer satisfaction, which is the ultimate goal of any business. The importance of quality can be seen in the following ways:
- Customer satisfaction: Quality is critical in ensuring customer satisfaction. Customers expect high-quality products and services and are willing to pay a premium for it. By providing quality products and services, businesses can create a loyal customer base and establish their reputation in the market.
- Competitive advantage: High-quality products and services can set a business apart from its competitors. Customers are willing to pay more for quality products and services, which gives the company a competitive edge in the market. This can result in increased market share and profitability.
- Reduced costs: Quality can result in reduced costs for the business. When products and services are of high quality, there are fewer defects and less waste, which can lead to cost savings. Additionally, quality products and services require less rework, which can save time and money.
- Improved efficiency: Quality can also enhance the efficiency of business operations. When products and services are of high quality, there are fewer errors and less rework, which can save time and resources. This can result in improved productivity and profitability.
- Better decision-making: Quality data and information can help businesses make better decisions. By tracking quality metrics, companies can identify areas for improvement and make data-driven decisions to improve quality and efficiency.
History of Total Quality Management
Here is a brief history of TQM:
Early Origins
- The concept of quality can be traced back to ancient times when craftspeople took pride in their work and were rewarded for their skill.
- During the Industrial Revolution, quality control became more formalized with the use of inspection and statistical analysis.
Quality Control Movement
- In the early 20th century, the Quality Control Movement emerged in response to the growing demand for mass-produced goods and the need for more efficient manufacturing processes.
- Walter A. Shewhart, an engineer at Bell Telephone Laboratories, developed the first statistical process control (SPC) charts, which enabled manufacturers to identify and control sources of variation in their processes.
Total Quality Control
- In the 1940s, Japanese manufacturers embraced quality control and developed their own methods, including the "Five S's" of workplace organization and the "Kaizen" philosophy of continuous improvement.
- In the 1950s, Dr. W. Edwards Deming, an American statistician and quality expert, introduced his principles of Total Quality Control, which focused on continuous improvement, employee involvement, and the use of statistical methods.
Total Quality Management
- In the 1980s, Total Quality Management emerged as a comprehensive management approach that incorporated all aspects of quality control, including customer satisfaction, employee involvement, and continuous improvement.
- TQM became popular in the United States and Europe as a response to increased competition from Japan, where quality management had become a key driver of success.
Contemporary Approaches
- Today, TQM has evolved to include new technologies and methodologies, such as Lean Six Sigma and Agile, which incorporate principles of efficiency, continuous improvement, and customer focus.
- TQM remains critical to business success, enabling organizations to identify and address customer needs, improve operational efficiency, and achieve long-term sustainability.
Principles of Total Quality Management
Total Quality Management (TQM) is a business management strategy that aims to enhance the quality of products, services, and customer satisfaction through continuous improvement of processes, teamwork, and communication. The principles of TQM provide a framework for organizations to deliver high-quality products and services that meet or exceed customer expectations.
Here are some of the key principles of Total Quality Management:
- Customer focus: TQM puts the customer at the center of everything an organization does. It involves understanding customer needs and expectations and delivering products and services that meet or exceed them. This requires a focus on customer satisfaction and continuous improvement.
- Continuous improvement: TQM emphasizes the importance of ongoing improvement in all aspects of an organization, from processes and products to people and culture. Continuous improvement is achieved through a plan-do-check-act (PDCA) cycle, which involves identifying improvement areas, implementing changes, measuring results, and adjusting the process as needed.
- Employee involvement: TQM recognizes that employees are the key to delivering high-quality products and services. It involves empowering employees to take ownership of their work and encouraging them to contribute their ideas and insights to improve processes.
- Process improvement: TQM emphasizes the importance of process improvement to deliver high-quality products and services. This involves identifying and eliminating waste, streamlining processes, and improving quality control measures.
- Data-driven decision-making: TQM relies on data to make informed decisions about process improvement and customer satisfaction. It involves collecting and analyzing data to identify areas for improvement and monitor progress.
- Leadership involvement: TQM requires leadership involvement and support to be successful. Leaders must set the organization's vision, values, and goals and provide the resources and support needed to achieve them.
- Supplier relationships: TQM recognizes the importance of supplier relationships in delivering high-quality products and services. It involves developing strong relationships with suppliers to ensure they meet the organization's quality standards and deliver on time and on budget.
Challenges of Implementing Total Quality Management
Resistance to Change
One of the most significant challenges of implementing TQM is resistance to change. Employees may be comfortable with their current ways of doing things, and the prospect of change can be daunting.
This resistance can be overcome by involving employees in the process and providing them with the necessary training and support.
Lack of Management Support
Without support from top management, it can be challenging to implement TQM effectively. Management must be committed to the process and actively involved in its implementation. This can be achieved by providing resources and support and leading by example.
Inadequate Resources
Implementing TQM requires resources, including financial, technological, and human resources. Organizations that do not allocate the necessary resources may find it challenging to implement TQM effectively. To overcome this challenge, organizations should allocate resources according to their strategic priorities and plan accordingly.
Lack of Employee Involvement
Employees are essential to TQM, and their involvement is crucial to its success. Employees may feel left out of the process or unsure of their role in TQM. Organizations should involve employees from the outset, provide them with training, and recognize their contributions to overcome this challenge.
Difficulty Measuring Results
Measuring the effectiveness of TQM can be challenging, as it often involves intangible benefits such as improved customer satisfaction and employee morale. To overcome this challenge, organizations should establish clear metrics for success and regularly evaluate their progress.
Inadequate Training
Implementing TQM requires a significant amount of training, including training in quality principles and tools. Inadequate training can lead to a lack of understanding and support for TQM.
To overcome this challenge, organizations should invest in comprehensive training programs that provide employees with the knowledge and skills they need to support TQM.
Lack of Customer Focus
One of the primary goals of TQM is to improve customer satisfaction. However, organizations may lose sight of this goal and focus solely on internal processes. To overcome this challenge, organizations should maintain a customer-focused approach and regularly seek feedback from customers.
Developing a Total Quality Management Strategy
Total Quality Management (TQM) aims to involve every member of an organization in the pursuit of quality excellence. Developing a TQM strategy involves various steps that organizations must undertake to establish and maintain a robust quality management system.
Define the Organization's Mission and Vision
A clear and concise mission and vision statement helps an organization define its purpose, values, and goals. A TQM strategy must align with an organization's mission and vision statement to ensure that all quality management initiatives align with the organization's overall objectives.
Establish a Quality Policy
A quality policy outlines an organization's commitment to delivering quality products and services. It should be based on the organization's mission and vision and guide quality management practices. The policy should be communicated to all employees and stakeholders to ensure understanding and adherence.
Identify Key Performance Indicators (KPIs)
KPIs are essential metrics that help organizations track performance, identify areas for improvement, and measure progress toward goals. TQM strategies should identify relevant KPIs that align with an organization's objectives and establish a system for monitoring and reporting on these KPIs.
Conduct a Gap Analysis
A gap analysis identifies the current state of an organization's quality management system compared to the desired state. It helps identify gaps, deficiencies, and opportunities for improvement. The analysis should involve all levels of the organization to ensure comprehensive and accurate results.
Develop a Continuous Improvement Plan
A TQM strategy should outline a continuous improvement plan that identifies specific improvement initiatives, assigns responsibilities, and establishes timelines for implementation. The plan should be regularly reviewed and updated to ensure that it remains relevant and effective.
Establish Communication and Training Programs
Effective communication and training programs are essential for ensuring that all employees understand and support an organization's quality management system. The programs should include training on quality management principles, tools, techniques, and communication channels for feedback and suggestions.
Implement Quality Management Tools and Techniques
There are various quality management tools and techniques that organizations can use to improve processes and outcomes. These include process mapping, statistical process control, benchmarking, and root cause analysis.
A TQM strategy should identify the appropriate tools and techniques for an organization's specific needs and ensure that employees are trained in their use.
Monitor and Evaluate Progress
A TQM strategy should establish a system for monitoring and evaluating progress toward achieving quality goals and objectives. This should include regular performance reviews, audits, and customer feedback. The results should be used to identify improvement areas and adjust the TQM strategy accordingly.
Continuous Improvement and Total Quality Management
Continuous Improvement and Total Quality Management (TQM) are interrelated concepts that aim to achieve better results in organizations.
TQM is a management philosophy that focuses on customer satisfaction by meeting their needs and expectations, while continuous improvement refers to the ongoing efforts to enhance the organization's products, services, and processes.
Understanding the Concept of Continuous Improvement: Continuous improvement is an ongoing effort to improve an organization's products, services, and processes.
It involves identifying areas that need improvement, developing a plan to address those areas, implementing the plan, and evaluating the results. Continuous improvement is not a one-time event but a continuous process involving all organizational levels.
Importance of Continuous Improvement in TQM: Continuous improvement is an essential element of TQM because it helps organizations continuously improve their processes and products.
TQM's primary goal is to provide customers with high-quality products and services by continuously improving processes, products, and services. Continuous improvement helps organizations to achieve this goal by identifying areas that need improvement and implementing changes to address those areas.
Implementing Continuous Improvement in TQM: Implementing continuous improvement in TQM requires the following steps:
- Identify areas that need improvement: The first step in implementing continuous improvement is to identify areas that need improvement. This can be done by collecting data on customer complaints, analyzing the process for quality, and identifying areas where the process can be improved.
- Develop a plan to address those areas: Once areas for improvement are identified, the next step is to develop a plan to address those areas. The plan should include specific actions that will be taken to address the areas of improvement, who will be responsible for implementing the plan and a timeline for implementation.
- Implement the plan: The responsible parties should implement the plan, and the progress should be monitored regularly. The implementation process should involve all employees in the organization, and everyone should be aware of the plan's objectives.
- Evaluate the results: After the plan is implemented, the results should be evaluated to determine if the plan was successful. The evaluation should include feedback from customers and employees to identify any further improvements that can be made.
Benefits of Continuous Improvement in TQM: Continuous improvement in TQM can result in several benefits, including:
- Increased efficiency: Continuous improvement helps organizations to identify and eliminate inefficiencies in their processes, resulting in increased efficiency.
- Cost reduction: By eliminating inefficiencies and waste, organizations can reduce their costs, which can result in increased profitability.
- Improved quality: Continuous improvement helps organizations identify and address quality issues, resulting in improved product and service quality.
- Increased customer satisfaction: By improving product and service quality, organizations can increase customer satisfaction, resulting in increased customer loyalty and repeat business.
- Employee engagement: Involving employees in the continuous improvement process can increase their engagement and motivation, resulting in increased productivity and job satisfaction.
The Role of Leadership in Total Quality Management
The success of Total Quality Management (TQM) heavily relies on effective leadership that fosters a culture of quality and continuous improvement throughout the organization. Here are some points on the role of leadership in Total Quality Management:
- Vision and strategy: Leaders must set a clear vision and strategy for the organization, including a commitment to quality and continuous improvement. They should communicate this vision and strategy to all employees to ensure that everyone is working towards a common goal.
- Leading by example: Leaders must lead by example and model behaviors and values that are consistent with a culture of quality. They should set the tone for the organization by demonstrating their commitment to quality and continuous improvement through their actions and decisions.
- Empowering employees: Leaders must empower employees by providing them with the necessary tools, resources, and training to do their jobs effectively. This includes giving employees the autonomy to make decisions and take ownership of their work.
- Creating a supportive environment: Leaders must create a supportive environment that encourages and rewards innovation, creativity, and risk-taking. This means allowing employees to experiment and learn from their mistakes without fear of retribution.
- Continuous improvement: Leaders must embrace the concept of continuous improvement and encourage employees to continually look for ways to improve processes, products, and services. This requires a willingness to change and adapt to new ideas and technologies.
- Measuring and monitoring performance: Leaders must measure and monitor performance to ensure the organization meets its quality objectives. This includes setting benchmarks and targets for improvement and tracking progress towards those goals.
- Feedback and recognition: Leaders must provide regular feedback and recognition to employees for their contributions to quality and continuous improvement. This helps to reinforce the importance of quality and encourages employees to continue to strive for excellence.
- Commitment to customer satisfaction: Leaders must demonstrate a strong commitment to customer satisfaction by listening to customer feedback and using that feedback to improve products and services. This includes setting customer service standards and regularly measuring customer satisfaction levels.
Tools and Techniques for Implementing Total Quality Management
Here are some of the common tools and techniques used to implement TQM.
Process Mapping
Process mapping is a technique used to represent the steps involved in a process visually. It helps to identify inefficiencies and bottlenecks in the process, which can then be improved upon.
Benefits of Process Mapping:
- Process mapping helps to visualize the entire process from start to finish, making it easier to identify inefficiencies and areas for improvement.
- It provides a clear understanding of the process, which helps to eliminate confusion and miscommunication among team members.
- Process mapping helps to identify bottlenecks in the process that can cause delays and reduce productivity.
- It helps to reduce waste by identifying unnecessary steps in the process that can be eliminated.
- Process mapping provides a basis for process improvement by identifying areas where changes can be made to increase efficiency and reduce costs.
Creating a Process Map:
- Identify the process to be mapped. What is the process that you want to improve?
- Gather information about the process. Who are the stakeholders in the process? What are the inputs and outputs of the process? What are the steps involved in the process?
- Create a draft of the process map. Use a tool like a flowchart or a swim lane diagram to create a visual representation of the process.
- Review the draft with stakeholders. Get feedback from the people who work in the process to ensure that the map is accurate and complete.
- Finalize the process map. Make any necessary changes to the map based on the feedback you received.
Tips for Creating Process Maps
Here are a few tips for creating process maps:
- Use simple language and symbols. The process map should be easy for everyone who works in the process to understand.
- Be as detailed as possible. The more detail you include in the process map, the easier it will be to identify areas for improvement.
- Use consistent terminology. Use the same terms throughout the process map to avoid confusion.
- Keep the process map up to date. As the process changes, make sure to update the process map accordingly.
Here are some of the most common symbols used in process mapping:
- Start/End: These symbols represent the beginning and end of the process.
- Process: This symbol represents a step in the process.
- Decision: This symbol represents a point in the process where a decision must be made.
- Input: This symbol represents an input to the process.
- Output: This symbol represents an output from the process.
Once you have created the process map, review it with the people who work in the process. This will help to ensure that the map is accurate and that everyone involved understands the process.
Types of Process Maps:
Flowchart
Flowcharts are one of the most widely used types of process maps in Total Quality Management. They use symbols and arrows to depict the sequence of activities and decision points within a process. Flowcharts provide a clear visual representation of the flow of work, showing the inputs, outputs, and the order in which activities are performed.
They can include different types of symbols, such as rectangles for activities, diamonds for decision points, and arrows for flow direction. Flowcharts are versatile and can be used to represent both simple and complex processes.
Benefits of Flowcharts:
- Easy to understand and communicate.
- Highlight the logical flow of activities.
- Identify decision points and branching paths.
- Visualize inputs, outputs, and interactions.
- Identify bottlenecks and inefficiencies.
Applications of Flowcharts:
- Documenting existing processes.
- Analyzing process flow and identifying improvement opportunities.
- Communicating process steps to stakeholders.
- Training employees on process workflows.
- Supporting process improvement initiatives, such as Lean or Six Sigma projects.
Swimlane Diagram
Swimlane diagrams, also known as cross-functional flowcharts, are process maps that visually separate the responsibilities of different individuals or departments involved in a process.
Each participant or department is assigned a "swimlane," which represents their specific activities and responsibilities within the process. Swimlane diagrams help to clarify the roles and interactions between different stakeholders, enhancing cross-functional collaboration and accountability.
Benefits of Swimlane Diagrams:
- Clearly defines roles and responsibilities.
- Visualizes interactions between different stakeholders.
- Identifies handoffs and potential bottlenecks between departments.
- Supports process improvement by highlighting ownership and accountability.
- Enhances cross-functional collaboration and understanding.
Applications of Swimlane Diagrams:
- Visualizing end-to-end process flows.
- Analyzing interdepartmental handoffs and communication gaps.
- Identifying areas for process optimization and streamlining.
- Enhancing collaboration and communication between teams or departments.
- Documenting complex processes involving multiple stakeholders.
Value Stream Map
Value Stream Mapping (VSM) is a type of process map that focuses on capturing the end-to-end flow of materials, information, and activities within a process. It provides a holistic view of the value stream, from the customer's initial request to the delivery of the final product or service.
Value Stream Maps highlight both value-adding and non-value-adding activities, allowing organizations to identify waste and opportunities for improvement. VSM is commonly associated with Lean principles and is used to support continuous improvement initiatives.
Benefits of Value Stream Maps:
- Provides a holistic view of the value stream.
- Identifies waste and non-value-adding activities.
- Helps visualize the flow of materials and information.
- Facilitates identification of improvement opportunities.
- Supports Lean principles and continuous improvement.
Applications of Value Stream Maps:
- Analyzing end-to-end process flow.
- Identifying and eliminating waste in processes.
- Improving process cycle times and reducing lead times.
- Enhancing value delivery to customers.
- Supporting Lean manufacturing and service improvement initiatives.
SIPOC Diagram
SIPOC (Supplier, Inputs, Process, Outputs, Customer) diagrams provide a high-level overview of a process, emphasizing the key stakeholders and their interactions. SIPOC diagrams identify the suppliers of inputs, the process steps, the outputs, and the customers.
They help organizations understand the boundaries of the process, the inputs required, and the expected outputs. SIPOC diagrams provide a framework for process understanding and serve as a starting point for more detailed process analysis.
Components of the SIPOC Diagram
The SIPOC diagram consists of five main components:
Suppliers: Suppliers are the entities or individuals who provide the inputs required for the process. They can be internal or external to the organization. In the SIPOC diagram, suppliers are identified to ensure that the necessary inputs are available for the process to function effectively.
Inputs: Inputs are the materials, data, or resources required to carry out the process. They are the raw materials or information that undergo transformation within the process. Identifying the inputs helps in understanding the quality and availability of resources required for the process.
Process: The process component represents the sequence of activities or steps involved in transforming the inputs into outputs. It outlines the actions, decisions, and transformations that take place within the process. Defining the process helps in identifying the critical steps and potential areas for improvement.
Outputs: Outputs are the results or deliverables generated by the process. They can be products, services, reports, or any other tangible or intangible outcomes. Identifying the outputs helps in understanding the value created by the process and assessing its effectiveness in meeting customer requirements.
Customers: Customers are the recipients or beneficiaries of the process outputs. They can be internal or external to the organization and may include individuals, departments, or other stakeholders. Identifying the customers helps in understanding their needs, expectations, and satisfaction levels, which is essential for delivering high-quality outputs.
Statistical Process Control (SPC)
SPC is a tool used to monitor and control a process by analyzing data. It helps to identify when a process is out of control and provides feedback on how to bring it back into control.
History: SPC was developed in the early 20th century by Walter A. Shewhart, a statistician at Bell Labs. Shewhart's work laid the foundation for modern quality control and quality assurance methods.
Key Principles of Statistical Process Control:
SPC is guided by several key principles:
Process Variation: SPC recognizes that every process exhibits variation. It distinguishes between two types of process variation: common cause variation and special cause variation.
Common cause variation is inherent to the process and represents the natural variability that occurs over time. Special cause variation, on the other hand, is caused by specific factors that can be identified and addressed.
Control Charts: Control charts are the primary tool used in SPC. They provide a graphical representation of process performance over time. Control charts have a center line that represents the process average and upper and lower control limits that define the acceptable range of variation.
By plotting data points on the control chart, organizations can determine if the process is stable or exhibiting special cause variation.
Types of Control Charts:
There are several types of control charts used in Statistical Process Control. The selection of the appropriate control chart depends on the type of data being measured and the characteristics of the process being monitored. The most commonly used control charts include:
- X-Bar and R Chart: The X-Bar and R chart is used to monitor the process mean (average) and process variation. It consists of two charts: the X-Bar chart, which tracks the process mean, and the R chart, which monitors the process range (the difference between the maximum and minimum values). This control chart is suitable for variable data, where measurements are taken on a continuous scale.
- X-Bar and S Chart: Similar to the X-Bar and R chart, the X-Bar and S chart is used to monitor the process mean and process variation. However, instead of tracking the process range, it monitors the process standard deviation (S). This control chart is also suitable for variable data.
- Individuals (I) Chart: The Individuals chart is used to monitor individual measurements of a process. It tracks the data points over time and helps identify any unusual or out-of-control conditions. The Individuals chart is suitable for variable data where individual measurements are taken.
- p Chart: The p chart is used to monitor the proportion of non-conforming items or defects in a process. It is based on attribute data, where items are classified as either conforming or non-conforming. The p chart tracks the proportion of non-conforming items in a sample over time and helps identify any significant deviations from the expected proportion.
- c Chart: The c chart is similar to the p chart but is used when the count of defects or non-conformities is being monitored. It tracks the count of defects in a sample and helps identify variations in the defect count.
Purpose of Control Charts in Statistical Process Control:
The primary purpose of control charts is to:
- Monitor Process Performance: Control charts allow organizations to monitor process performance over time. By collecting and plotting data, organizations can visually assess the stability and consistency of their processes. Control charts provide a baseline for process performance, enabling organizations to identify when the process is operating within acceptable limits and when it requires attention.
- Detect Variations: Control charts help organizations detect variations in process performance. Variations can be categorized as common causes or special causes. Common cause variations are inherent to the process and represent natural variability, while special cause variations are caused by specific factors that can be identified and addressed. Control charts visually highlight these variations, making them easier to detect.
- Assess Process Stability: Control charts provide a visual indication of process stability. When data points fall within the control limits on the chart, the process is considered stable. However, when data points exhibit non-random patterns or fall outside the control limits, it suggests instability or the presence of special causes. Process stability is essential for delivering consistent quality and meeting customer expectations.
- Make Data-Driven Decisions: Control charts facilitate data-driven decision-making. By analyzing the patterns and trends on the chart, organizations can identify areas for improvement and make informed decisions about process adjustments or corrective actions. Control charts provide objective information about process performance, reducing reliance on subjective opinions and promoting evidence-based decision-making.
Histograms: Histograms are used in SPC to analyze the distribution of process output. They show how frequently different values occur and can be used to identify outliers and other sources of variation.
Constructing a histogram involves several steps:
- Data Collection: The first step is to collect the data relevant to the process being analyzed. The data could represent measurements, observations, or any other variable of interest.
- Determine the Number of Bins: The next step is to determine the appropriate number of bins or classes for the histogram. This can be done using various methods, such as the square root rule, Sturges' formula, or Scott's normal reference rule. The number of bins should be sufficient to capture the distribution characteristics while avoiding excessive detail or oversimplification.
- Define Bin Intervals: Once the number of bins is determined, the range of data is divided into intervals or bins. The width of each bin is determined by dividing the range of data by the number of bins.
- Count Data Points: The data points are then counted or grouped into their respective bins. Each data point is assigned to the appropriate bin based on its value.
- Plot the Histogram: Finally, the histogram is plotted by representing each bin on the x-axis and the frequency or count of data points falling within each bin on the y-axis. The height of each bar represents the frequency or count.
Pareto charts: Pareto charts are used in SPC to identify the most significant sources of variation. They show the frequency of different types of defects or other quality problems and can help prioritize improvement efforts.
Construction of a Pareto Chart:
To construct a Pareto chart, you will need to collect data on the frequency of occurrence of different types of defects or problems. This data can be collected manually or using automated tools.
Once you have collected the data, you will need to sort it by frequency of occurrence. The most frequently occurring defects or problems should be listed at the top of the chart, and the least frequently occurring defects or problems should be listed at the bottom of the chart.
Next, you will need to create a bar chart for each type of defect or problem. The height of each bar should represent the frequency of occurrence of that type of defect or problem.
Finally, you will need to draw a line across the chart that represents the 80% threshold. This line will help you to identify the types of defects or problems that are causing the most problems.
Interpreting a Pareto Chart:
Once you have constructed a Pareto chart, you can use it to identify the most important causes of problems. The types of defects or problems that are represented by the tallest bars on the chart are the most important causes of problems.
By focusing corrective action on these areas, you can have the greatest impact on improving the quality of your products or services.
Using Pareto Charts in TQM:
Pareto charts are a valuable tool for TQM. They can be used to identify the most important causes of problems in any process. By focusing corrective action on these areas, you can have the greatest impact on improving the quality of your products or services.
Pareto charts can also be used to track the progress of improvement efforts. By comparing Pareto charts from different time periods, you can see which areas are improving and which areas still need attention.
Data Collection and Analysis: SPC relies on the collection and analysis of data to monitor process performance. Data can be collected in real-time or at regular intervals. The data is then analyzed using statistical techniques to calculate control limits and identify trends, patterns, and deviations from the expected process performance.
- Benefits: SPC can provide a number of benefits, including improved product quality, reduced defects and rework, increased efficiency, and improved customer satisfaction.
- Implementation: Implementing SPC requires a commitment to quality from all levels of an organization. It typically involves training and education for employees, establishing process control teams, and using statistical software to collect and analyze data.
- Limitations: SPC is not a panacea for all quality problems. It requires a significant investment of time and resources and may not be appropriate for all types of processes. Additionally, SPC is only effective if the process is stable and predictable.
Quality Circles
Quality circles are groups of employees who come together to identify and solve problems related to quality. A supervisor or manager typically leads these groups and can be a powerful tool for continuous improvement.
History of Quality Circles
Quality circles were first developed in the 1960s in Japan by Dr. Kaoru Ishikawa, a renowned quality control expert. Companies like Toyota and Nissan initially used them to improve product quality and reduce costs. Quality circles became popular in the United States in the 1970s and 1980s and were embraced by organizations seeking to improve quality and productivity.
Objectives of Quality Circles
The primary objective of quality circles is to identify and solve problems related to product or service quality, efficiency, or safety.
Employee Empowerment and Engagement: Quality Circles empower employees by involving them in decision-making and problem-solving processes. They provide a platform for employees to contribute their knowledge, skills, and ideas to improve work processes and outcomes.
This involvement enhances employee engagement and fosters a sense of ownership and pride in their work.
Problem Identification and Solution Generation: Quality Circles enable employees to identify and address problems or challenges in their work areas. Through brainstorming sessions and collective discussions, they generate innovative solutions that may have otherwise gone unnoticed.
This bottom-up approach ensures that problems are addressed at their source and solutions are tailored to the specific context.
Skill Development: Quality Circles provide a platform for employees to enhance their problem-solving, communication, teamwork, and leadership skills. Participation in Quality Circles allows individuals to develop a broader understanding of the organization, its processes, and the interdependencies between different functions.
These skills are transferable and contribute to the overall development of employees.
Cost Reduction and Efficiency: Quality Circles contribute to cost reduction and process efficiency by identifying and eliminating non-value-added activities, reducing rework, and optimizing resource utilization.
The collective intelligence and diverse perspectives of Quality Circle members enable organizations to implement practical and cost-effective solutions.
Process of Quality Circles
Quality circles typically follow a structured process that includes the following steps:
- Selecting a problem or issue to address
- Gathering information about the problem and its root causes
- Analyzing the information and identifying possible solutions
- Selecting the best solution and developing an action plan
- Implementing the action plan and monitoring its effectiveness
- Evaluating the results and making adjustments as necessary
Benefits of Quality Circles: Quality circles can provide a range of benefits for organizations, including:
- Improved product or service quality and customer satisfaction
- Increased efficiency and productivity
- Reduced costs and waste
- Improved employee engagement and job satisfaction
- Enhanced teamwork and communication
- A culture of continuous improvement and innovation
Challenges of Quality Circles: Despite their many benefits, quality circles can also present challenges for organizations. Some of the most common challenges include:
- Lack of management support and commitment
- Resistance to change from employees or other stakeholders
- Limited time and resources for quality circle activities
- Inadequate training or facilitation for quality circle members
- Difficulty in measuring the impact and effectiveness of quality circles
Best Practices for Quality Circles: To maximize the benefits of quality circles, organizations can follow some best practices, such as:
- Providing adequate training and support for quality circle members
- Ensuring management support and commitment to quality circle activities
- Encouraging participation and input from all employees
- Focusing on the most critical issues and problems
- Measuring and tracking the impact of quality circle activities on organizational goals and objectives
Six Sigma
Six Sigma is a data-driven methodology used to improve quality by identifying and eliminating defects in a process. It involves the use of statistical analysis and other tools to identify the root cause of problems and implement solutions.
- Origins of Six Sigma: Six Sigma was first developed by Motorola in the mid-1980s as a way to reduce defects in their manufacturing processes. The methodology was later adopted and popularized by General Electric in the 1990s.
- The goal of Six Sigma: Six Sigma aims to achieve a level of quality where the number of defects is minimized, ideally to the point where there are no defects at all. This level of quality is known as a Six Sigma level, which means that there are no more than 3.4 defects per million opportunities.
- The DMAIC process: Six Sigma is typically implemented using the DMAIC process, which stands for Define, Measure, Analyze, Improve, and Control. Each step in the process involves specific activities, such as gathering data, analyzing it, identifying areas for improvement, and implementing changes.
- The role of data: Data is a critical component of Six Sigma, as it is used to identify the root causes of defects and to track progress toward improvement. Data is typically collected and analyzed using statistical tools, which help to identify patterns and trends.
- The use of statistical tools: Six Sigma makes extensive use of statistical tools such as control charts, histograms, and process capability analysis. These tools help to identify areas where improvements can be made and to track progress toward improvement goals.
- The importance of leadership support: Six Sigma requires strong leadership support to succeed. Leaders must be committed to the methodology and must provide the resources necessary for its implementation.
Total Productive Maintenance (TPM)
TPM is a methodology used to improve the overall effectiveness of equipment by maximizing its uptime and reducing downtime. It involves a systematic approach to maintenance, including regular inspections and preventative maintenance.
- Understanding the equipment: The first step in TPM is to gain a thorough understanding of the equipment, including its design, operation, and maintenance requirements.
- Maintenance prevention: TPM emphasizes the importance of preventing equipment failures through regular maintenance activities such as cleaning, lubrication, and inspection.
- Maintenance improvement: TPM also focuses on improving maintenance activities through the use of advanced maintenance techniques such as predictive maintenance and reliability-centered maintenance.
- Autonomous maintenance: This involves empowering operators to take responsibility for routine maintenance tasks, such as cleaning and lubrication, in order to prevent equipment failures.
- Equipment management: TPM also involves managing equipment through a comprehensive asset management system that identifies and addresses equipment-related issues such as reliability, availability, and maintainability.
- Training and development: TPM requires developing a skilled workforce capable of operating and maintaining equipment effectively.
- Continuous improvement: TPM is a continuous improvement process that involves identifying opportunities for improvement and implementing changes to equipment and processes in order to achieve better results.
Benchmarking
Benchmarking is the process of comparing a company's performance to that of other companies in the same industry. It helps to identify areas for improvement and best practices that can be adopted.
Types of Benchmarking: There are several types of benchmarking, including:
- Internal benchmarking involves comparing an organization's performance to its previous performance to identify areas where it can improve.
- Competitive benchmarking: This involves comparing an organization's performance to that of its direct competitors.
- Functional benchmarking involves comparing an organization's performance to other organizations in similar functional areas.
- Generic benchmarking involves comparing an organization's performance to those of organizations in unrelated industries.
Benefits of Benchmarking: Benchmarking offers several benefits to organizations, including:
- Identifying areas for improvement: Benchmarking helps organizations identify areas where they can improve their performance and gain a competitive advantage.
- Improving quality and productivity: By benchmarking against other organizations, companies can learn best practices that will enhance quality and productivity.
- Enhancing customer satisfaction: By improving quality and productivity, companies can increase customer satisfaction, leading to increased loyalty and revenue.
- Creating a culture of continuous improvement: Benchmarking helps organizations create a culture of continuous improvement, where employees are encouraged to identify and implement best practices.
- Providing a basis for goal setting: Benchmarking provides a basis for setting performance goals and targets, helping organizations improve their overall performance.
Lean Manufacturing
Lean manufacturing is a methodology that focuses on minimizing waste and maximizing value. It involves identifying and eliminating non-value-added activities in a process.
Key Principles:
- Identify and Eliminate Waste: Lean manufacturing aims to identify and eliminate waste in all its forms, including overproduction, waiting, excess inventory, unnecessary transportation, overprocessing, defects, and unused talent. The goal is to streamline the production process and reduce costs while improving quality.
- Focus on Continuous Improvement: Lean manufacturing is a continuous improvement process involving all organization employees. The focus is on making small, incremental improvements in the production process every day rather than waiting for a major problem to occur. This approach leads to a culture of continuous improvement and innovation.
- Create a Pull System: Lean manufacturing uses a pull system, where production is based on customer demand rather than on forecasts or projections. This approach minimizes inventory and reduces the risk of overproduction, which can lead to waste and excess costs.
- Empower the Workforce: Lean manufacturing empowers the workforce to identify and solve problems. The focus is on creating a culture of teamwork and collaboration, where employees are encouraged to share ideas and participate in decision-making.
Kaizen
Kaizen is a Japanese term that means "continuous improvement." It involves a systematic approach to identifying and eliminating waste and improving efficiency.
- Principles of Kaizen: The key principles of Kaizen are continuous improvement, teamwork, respect for people, and waste reduction. Kaizen involves everyone in the organization, from top management to front-line employees, in identifying opportunities for improvement and making incremental changes to improve processes and products.
- Benefits of Kaizen: The benefits of Kaizen include improved quality, increased productivity, reduced costs, enhanced customer satisfaction, and better employee engagement. Kaizen also helps organizations stay competitive by adapting to changes in the market and improving their processes and products to meet customer needs.
- Implementation of Kaizen: Implementing Kaizen involves several steps, including setting goals, identifying improvement opportunities, analyzing processes, implementing changes, and evaluating results. The process is ongoing and requires a commitment to continuous improvement from all members of the organization.
- Kaizen Tools: There are several tools and techniques used in Kaizen, including the 5S method for workplace organization, value stream mapping for process analysis, and visual management tools such as Kanban boards.
- Examples of Kaizen: Kaizen has been successfully implemented in many industries, including manufacturing, healthcare, and service industries. For example, Toyota is known for its use of Kaizen to improve its production processes and products continuously.
Poka-Yoke
Poka-Yoke is a technique used to prevent errors from occurring in a process. It involves the use of devices or systems that make it impossible for errors to occur.
Key Principles of Poka-Yoke:
- Prevention over Detection: The Poka-Yoke technique focuses on preventing mistakes from occurring rather than detecting and correcting them after they have occurred. This principle helps to reduce costs associated with quality control and rework.
- Simplification: Poka-Yoke is a simple technique that involves designing processes in such a way that they are easy to understand and follow. This principle helps to eliminate confusion and errors caused by complex processes.
- Mistake-Proofing: Poka-Yoke aims to create a process that is mistake-proof or error-proof. This principle involves designing the process in such a way that it is impossible or difficult to make mistakes.
- Continuous Improvement: The Poka-Yoke technique is an ongoing process of continuous improvement. It involves identifying areas for improvement and implementing changes to eliminate errors and improve quality.
- Involvement of Employees: The employees who perform the process are involved in the Poka-Yoke process. They are encouraged to identify potential errors and suggest improvements to prevent them.
Types of Poka-Yoke:
- Contact Method: This type of Poka-Yoke involves physically preventing an error from occurring by using a device that stops the process if a mistake is made. For example, a machine that automatically stops when a part is not correctly inserted.
- Fixed-Value Method: This type of Poka-Yoke involves setting a limit or a fixed value to a process to prevent an error from occurring. For example, a machine that stops automatically when a certain weight is reached.
- Motion-Step Method: This type of Poka-Yoke involves designing a process in such a way that a sequence of steps must be followed to prevent errors from occurring. For example, a machine cannot be operated unless a certain sequence of buttons is pressed.
- Sequence Method: This type of Poka-Yoke involves designing a process in such a way that it is impossible to proceed to the next step until the current step has been completed correctly. For example, a software program requires all fields to be filled in before the user can move to the next screen.
5S
5S is a methodology used to organize the workplace and improve efficiency. It involves the use of five principles: Sort, Set in order, Shine, Standardize, and Sustain.
Sort (Seiri): The first step in 5S is to sort or separate the items in the work area into those that are necessary and those that are not. Unnecessary items should be removed to create a more organized workspace, making it easier for employees to find what they need quickly.
This also helps reduce clutter, which can lead to accidents, mistakes and lost productivity.
Set in Order (Seiton): After sorting, the next step is to set in order or arrange the necessary items in a logical and efficient manner. This step aims to improve productivity by ensuring that items are easy to find, access, and return.
Labels, color-coding, and shadow boards can be used to identify items and their proper location, making it easier for employees to work efficiently and reduce the time spent searching for tools or materials.
Shine (Seiso): The third step in 5S is to shine or clean the work area. This step involves removing all dirt, dust, and debris from the work area to create a clean and safe workspace.
Regular cleaning and maintenance not only help improve the appearance of the workspace but also improve employee morale and safety by reducing the risk of accidents.
Standardize (Seiketsu): The next step is to standardize the process once the first three steps of 5S are complete. This involves developing standard procedures and guidelines for maintaining the work area's cleanliness and organization.
Standardizing the process ensures that the improvements made during the first three steps are sustained over time, leading to long-term benefits.
Sustain (Shitsuke): The final step in 5S is to sustain or maintain the improvements made in the first four steps. This step requires continuous effort and dedication to ensure that the work area remains clean, organized, and efficient.
Regular audits, training, and monitoring can help sustain the improvements made during the 5S process.
Measuring Total Quality Management Effectiveness
Establish clear and measurable objectives
Establishing clear and measurable objectives is one of the first steps in measuring TQM effectiveness. These objectives should be aligned with the organization's overall goals and objectives.
The objectives should be specific, measurable, achievable, relevant, and time-bound (SMART). Without clear and measurable objectives, measuring the effectiveness of TQM implementation will be difficult.
Develop Key Performance Indicators (KPIs)
KPIs are the metrics that organizations use to measure their progress toward achieving their objectives. When implementing TQM, developing KPIs that align with the TQM objectives is essential.
The KPIs should be meaningful, actionable, and measurable. The KPIs should provide a clear picture of the organization's performance in terms of quality, productivity, customer satisfaction, and employee satisfaction.
Implement a robust data collection and analysis system
To measure TQM effectiveness, it is important to have a robust data collection and analysis system in place. The system should capture relevant data on the organization's performance, and the data should be analyzed to identify trends and patterns.
The data analysis should provide insights into the effectiveness of TQM implementation, and the insights should be used to identify areas for improvement.
Conduct regular audits and reviews
Regular audits and reviews are essential to measure TQM effectiveness. Audits and reviews should be conducted to assess the organization's compliance with TQM principles and identify improvement areas.
The audits and reviews should be conducted by independent auditors or review teams to ensure objectivity and impartiality.
Use customer feedback to measure the effectiveness
Customer feedback is an essential tool for measuring TQM effectiveness. Customer feedback should be collected regularly to gauge customer satisfaction and identify areas for improvement. The feedback should be analyzed, and the insights should be used to make changes to the organization's processes and procedures.
Implement continuous improvement
Continuous improvement is an essential aspect of TQM, and it is critical to measure the effectiveness of continuous improvement initiatives. The effectiveness of continuous improvement initiatives should be measured using the KPIs developed earlier.
The data collected should be analyzed to identify trends and patterns, and the insights should be used to make improvements to the organization's processes and procedures.
Common Total Quality Management Frameworks and Certifications
Here are some common TQM frameworks and certifications:
ISO 9000
The International Organization for Standardization (ISO) is a non-governmental organization that develops and publishes international standards for various industries. ISO 9000 is a set of quality management standards that provides guidelines for the implementation of a quality management system.
It includes requirements for documentation, management review, and continuous improvement. Organizations can obtain certification to ISO 9000 to demonstrate their commitment to quality management.
Baldrige Performance Excellence Program
The Baldrige Program is a framework developed by the United States government to help organizations achieve performance excellence. It includes leadership, strategy, customer focus, measurement, workforce, operations, and results criteria.
The Baldrige Program provides a comprehensive approach to TQM and is used by organizations of all sizes and types.
EFQM Excellence Model
The European Foundation for Quality Management (EFQM) Excellence Model is a framework that helps organizations assess their performance and identify areas for improvement.
It includes criteria for leadership, strategy, people, partnerships and resources, processes, products and services, and customer results. The EFQM Excellence Model is widely used in Europe and has been adopted by organizations around the world.
How can Deskera Help You?
Deskera is an all-in-one cloud-based business management software that can help manage quality control in firms. Here are some ways in which Deskera can help:
Deskera ERP: It is a comprehensive system that allows you to maintain inventory, manage suppliers, and track supply chain activity in real-time, as well as streamline a variety of other corporate operations.
Deskera MRP: It allows you to closely monitor the manufacturing process. From the bill of materials to the production planning features, the solution helps you stay on top of your game and keep your company's competitive edge.
Quality Control Management: Deskera provides a complete quality control management module that can help you create and manage quality control plans, track quality control metrics, and manage quality control processes from end to end.
Analytics and Reporting: Deskera provides advanced analytics and reporting capabilities, allowing you to track quality control metrics and identify areas for improvement.
Compliance Management: Deskera helps you ensure that your quality control processes meet regulatory requirements.
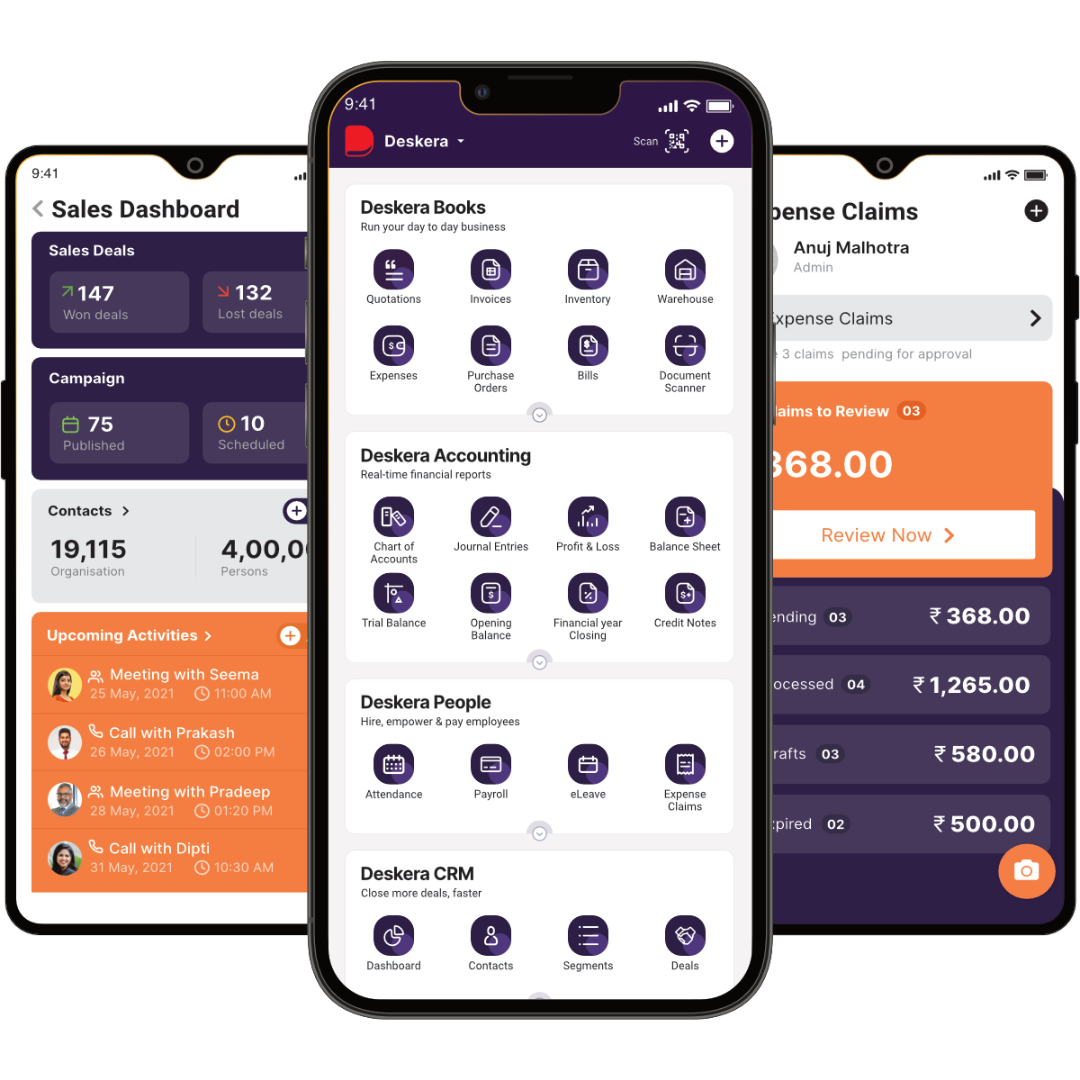
Conclusion
Total Quality Management is a holistic approach to quality management that involves all members of an organization to improve their products and services to meet customer satisfaction continuously. TQM requires a cultural shift within an organization, emphasizing the importance of quality and customer satisfaction and involving all levels of the organization.
This approach involves various techniques, such as quality planning, quality control, and quality improvement. The successful implementation of TQM leads to increased efficiency, reduced costs, and increased customer satisfaction.
TQM has been adopted by organizations globally as a competitive advantage in the market. The principles of TQM can be applied in various industries, including manufacturing, healthcare, and service industries. It has been widely accepted that TQM helps to improve organizational performance, increase customer satisfaction, and improve the bottom line.
Key Takeaways
- Total Quality Management is a management philosophy that aims to improve the quality of products and services continuously.
- It involves every employee, from top management to the front-line workers, in the pursuit of quality excellence.
- The implementation of Total Quality Management requires a long-term commitment to the process, as it involves changes in organizational culture, structure, and processes.
- Total Quality Management emphasizes the importance of customer satisfaction and seeks to exceed customer expectations.
- It focuses on prevention rather than inspection, encouraging proactive measures to prevent defects and errors from occurring.
- Total Quality Management involves continuous improvement through the use of data and statistical analysis to identify areas for improvement.
- It encourages employee involvement, empowerment, and ownership in the quality improvement process.
- Total Quality Management involves the implementation of quality standards, such as ISO 9001, to ensure consistency and conformity to customer requirements.
- It emphasizes the importance of leadership and management commitment in driving the Total Quality Management process.
- Total Quality Management involves the use of tools and techniques such as statistical process control, Six Sigma, and lean manufacturing to achieve quality improvement.
Related Articles
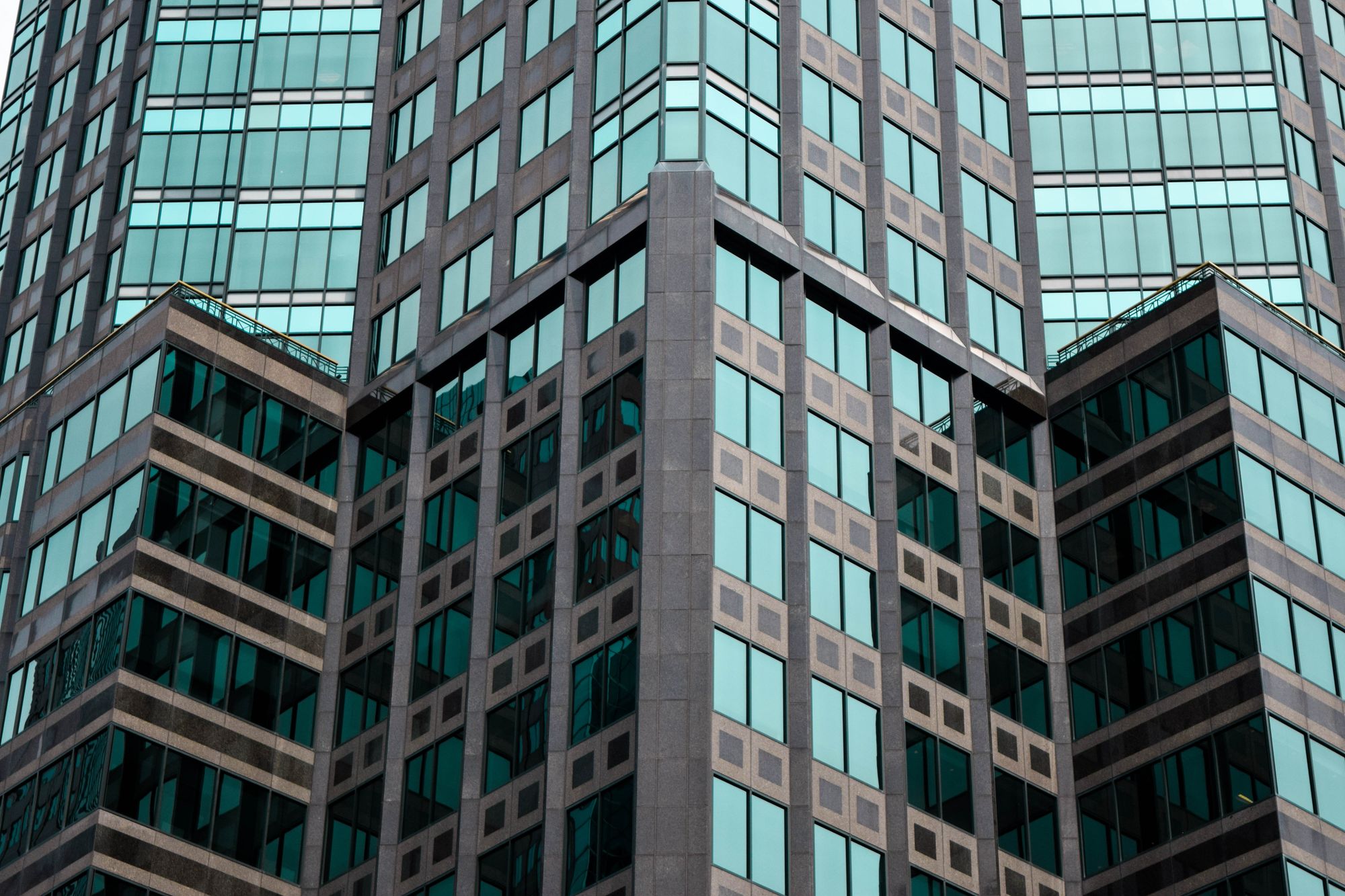
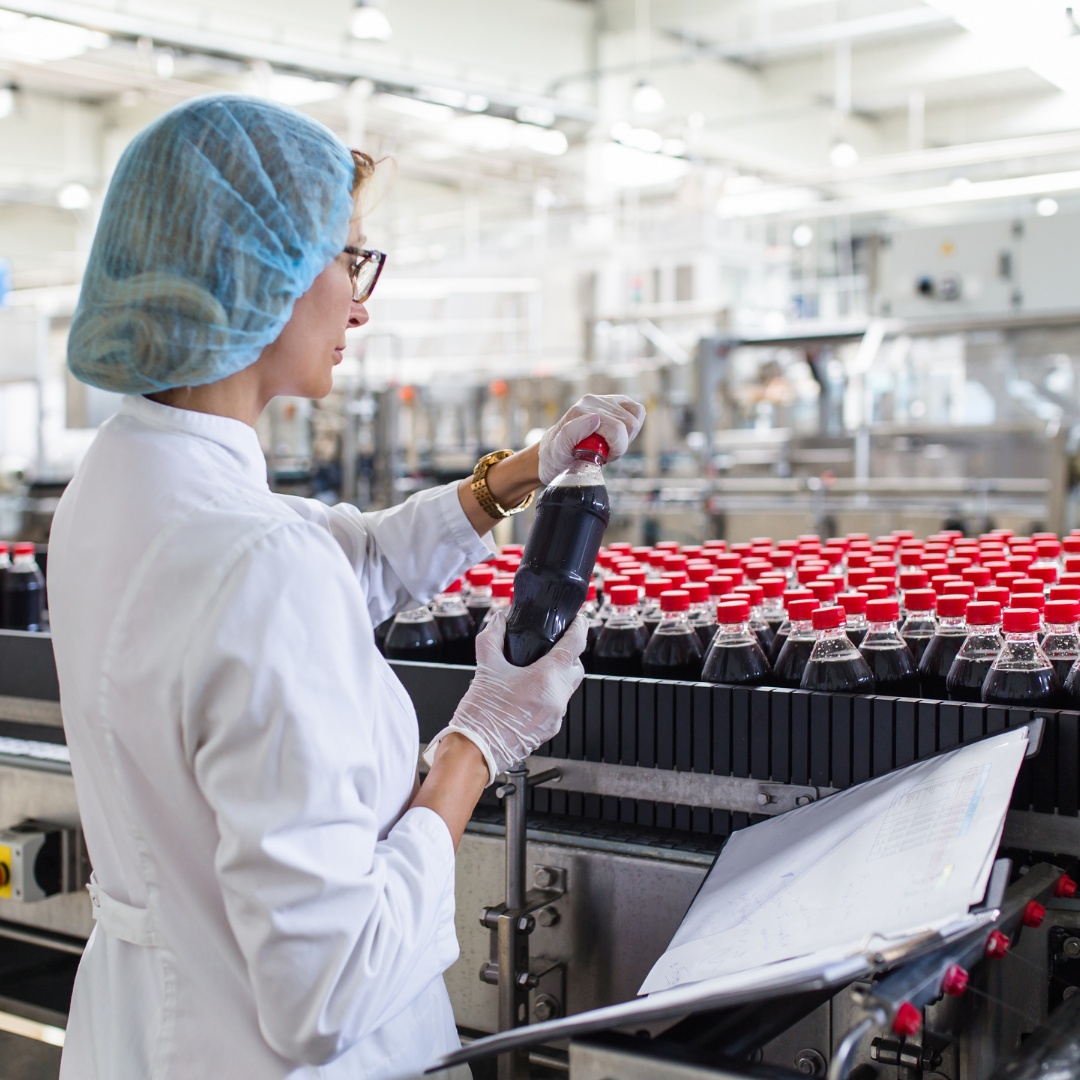
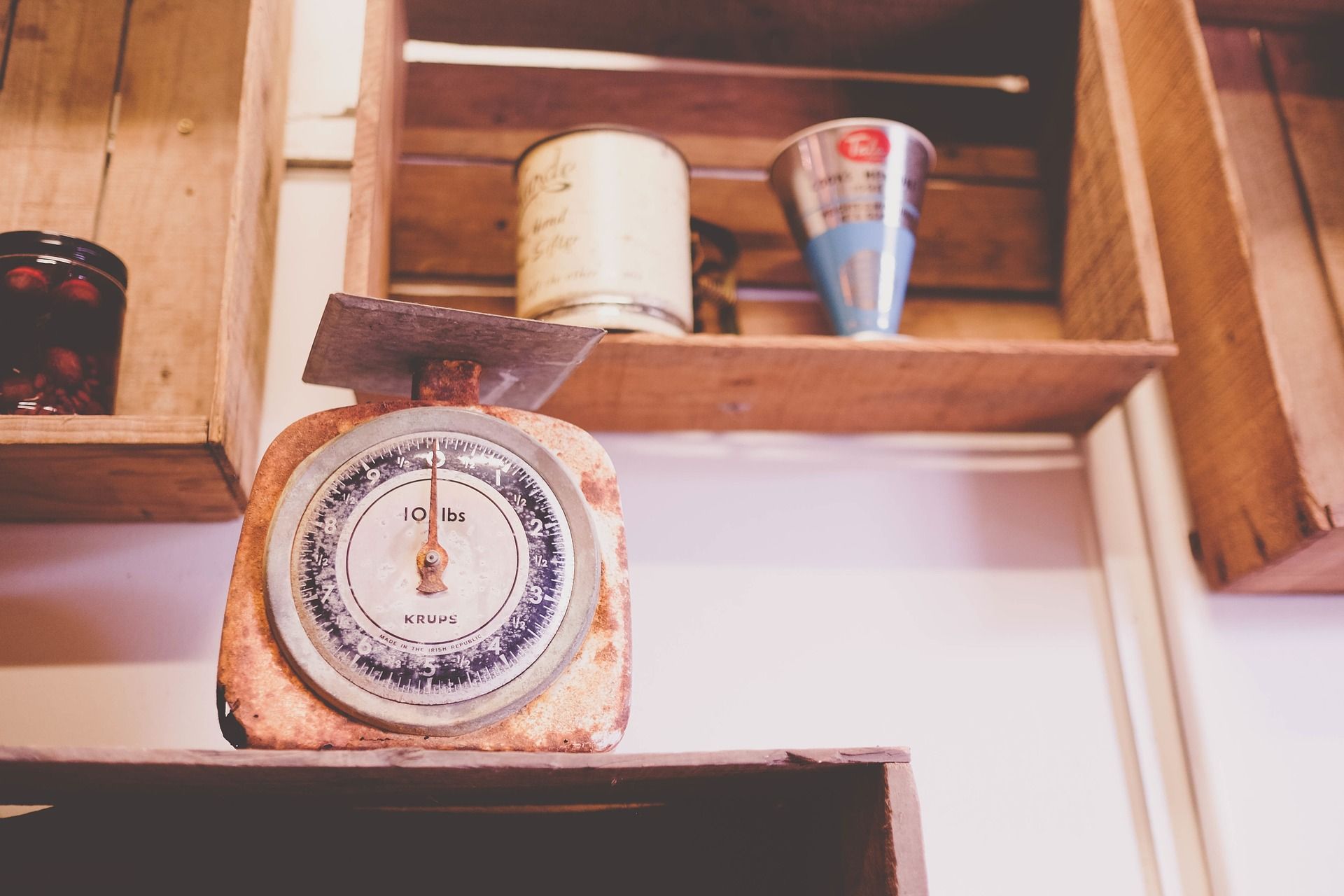
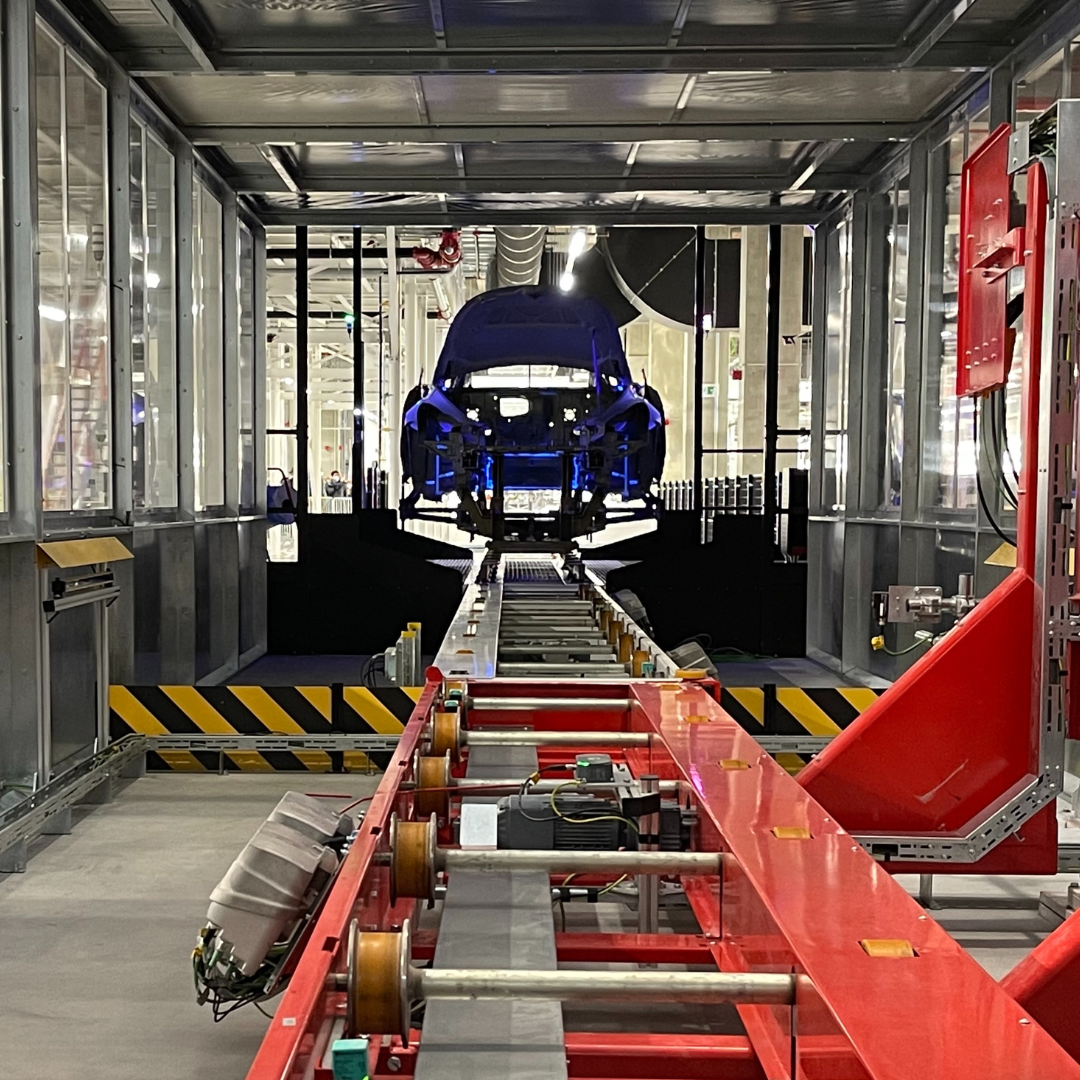