In the highly competitive landscape of modern production management, organizations strive for optimal efficiency, streamlined processes, and impeccable quality control.
In this pursuit, job cards have emerged as indispensable tools that drive productivity, coordination, and effective resource management. Job cards provide a structured framework for tracking, coordinating, and documenting work activities, enabling organizations to achieve greater operational success.
The relevance of job cards in modern production management cannot be overstated, as they facilitate clear task assignments, enhance communication and collaboration, and ensure adherence to quality standards. By examining their impact on productivity, efficiency, and decision-making, we can gain valuable insights into how job cards revolutionize production management practices.
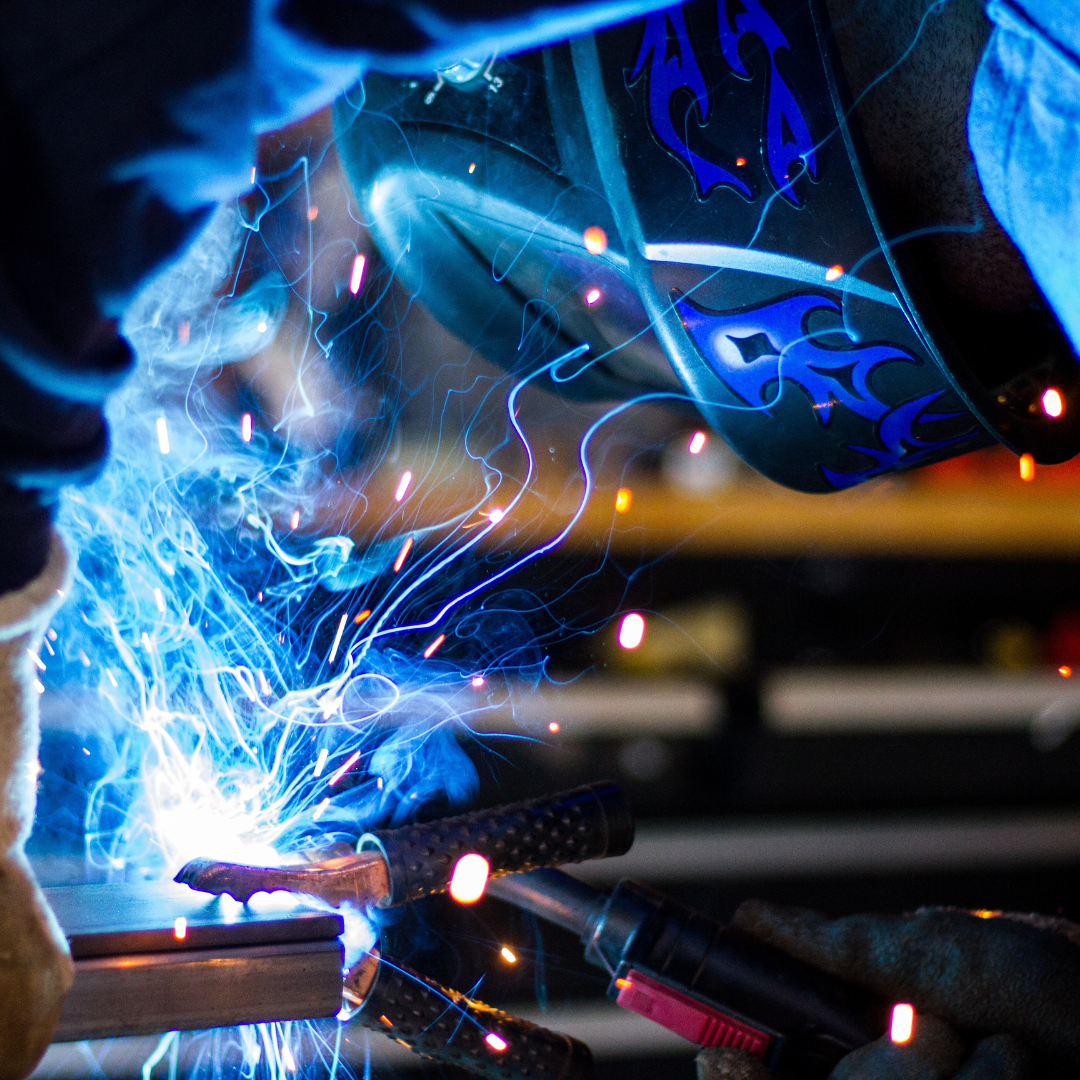
Here are some important stats we must know:
- According to a survey by the International Journal of Production Economics, 85% of organizations reported improved productivity after implementing job cards into their production management systems.
- A study conducted by McKinsey & Company found that organizations using job cards experienced an average reduction of 20% in production delays and bottlenecks.
- A report by Deloitte highlighted that companies that effectively use job cards in their production management processes have a 70% higher on-time delivery rate compared to those that don't.
These statistics underscore the significant impact of job cards on productivity, efficiency, and overall performance in modern production management.
Let’s look at what we shall discover in this post:
- Definition of Job Cards
- Overview of Modern Production Management
- Importance of Job Cards in Modern Production Management
- Features and Components of Job Cards
- Benefits of Using Job Cards in Modern Production Management
- Challenges and Considerations in Implementing Job Cards
- Conclusion
- How can Deskera Help You?
- Key Takeaways
- Related Articles
Definition of Job Cards
A job card is a document or form used in production management to track and manage specific tasks or jobs within a manufacturing or service-oriented organization. It serves as a central reference point that contains essential information related to a particular job, including job details, task breakdown, resource allocation, time tracking, quality standards, and instructions for completion.
Job cards provide a structured framework for organizing and documenting work activities, facilitating efficient coordination, monitoring progress, and ensuring adherence to quality and efficiency standards. They are commonly used in industries such as manufacturing, construction, maintenance, and project management.
Overview of Modern Production Management
Modern production management refers to the application of advanced methodologies, technologies, and principles to effectively plan, control, and optimize the production processes within an organization. It involves the coordination and integration of various resources, including personnel, materials, equipment, and technology, to achieve efficient and cost-effective production outcomes.
Key features of modern production management include:
Lean Manufacturing: The adoption of lean principles, such as waste reduction, continuous improvement, and just-in-time production, to eliminate non-value-added activities and streamline production processes. This approach aims to maximize efficiency, minimize costs, and improve overall quality.
Automation and Digitalization: The utilization of advanced technologies, such as robotics, artificial intelligence, and data analytics, to automate and optimize production operations. This includes the use of smart sensors, machine learning algorithms, and real-time monitoring systems to enhance productivity, accuracy, and decision-making.
Supply Chain Integration: The integration of suppliers, manufacturers, and distributors into a cohesive network to ensure seamless flow of materials, information, and resources. This involves efficient inventory management, demand forecasting, and collaboration with key stakeholders to optimize production planning and meet customer demands.
Quality Management: The implementation of rigorous quality control measures, including Total Quality Management (TQM) principles and quality assurance techniques, to ensure that products or services meet or exceed customer expectations. This includes robust inspection processes, adherence to industry standards, and continuous monitoring and improvement of quality metrics.
Agile and Flexible Manufacturing: The ability to quickly adapt to changing market demands and customize production processes to accommodate varying customer requirements. This includes agile production systems, flexible manufacturing technologies, and cross-functional teams that can rapidly respond to market shifts and deliver products efficiently.
Sustainability and Environmental Considerations: The integration of environmentally friendly practices and resource conservation strategies into production processes. This includes minimizing waste, reducing energy consumption, recycling materials, and adhering to environmental regulations to create sustainable and eco-friendly production operations.
Collaborative and Cross-functional Approach: Modern production management emphasizes collaboration and communication among different departments and stakeholders involved in the production process. Cross-functional teams work together to identify and solve problems, optimize processes, and enhance overall productivity and efficiency.
Overall, modern production management aims to optimize production processes, increase productivity, reduce costs, and improve product quality while adapting to changing market dynamics and customer demands. It leverages advanced technologies, data-driven insights, and streamlined processes to achieve operational excellence and sustainable growth in today's competitive business landscape.
Importance of Job Cards in Modern Production Management
In modern production management, efficient tracking, coordination, and documentation of work activities are crucial for achieving optimal productivity and maintaining high-quality standards. Job cards play a vital role in this regard, serving as valuable tools that enable organizations to effectively manage tasks, allocate resources, ensure quality control, and facilitate seamless communication and coordination among teams.
By examining the relevance of job cards in modern production management, we can understand their significance in enhancing efficiency, accountability, and overall operational success.
A. Tracking and documentation of work progress
Here is how tracking and documentation of the work progress can take place:
Monitoring individual tasks and milestones: Job cards provide a structured framework for monitoring and tracking individual tasks and milestones within a production process. Each job card typically includes a breakdown of specific tasks or activities required for the job. By assigning these tasks to individuals or teams and recording their progress on the job card, production managers can easily monitor the status of each task.
This allows for real-time visibility into the progress of work, enabling timely interventions if any tasks are falling behind schedule. By tracking individual tasks and milestones, job cards facilitate efficient project management and ensure that production processes stay on track.
Recording time spent on each job: Job cards also serve as a means to record the time spent on each job or task. Production managers can document the start and end times of individual tasks on the job card. This time tracking feature helps in analyzing the efficiency and productivity of production processes. It provides valuable data on the time required for each task, allowing for accurate estimation of future projects and better resource allocation.
Time tracking through job cards also enables organizations to identify bottlenecks, streamline processes, and optimize workflow to reduce time spent on repetitive or inefficient tasks. Additionally, this information can be utilized for performance evaluation and determining the profitability of different projects or job types.
B. Resource allocation and scheduling
Resource allocation and scheduling are among the key factors in production management. Here is how these can be accomplished:
Assigning tasks to appropriate personnel: Job cards play a crucial role in assigning tasks to the most suitable personnel within an organization. Each job card typically specifies the tasks or activities involved in a particular job and allows production managers to allocate those tasks to individuals or teams with the necessary skills and expertise. By clearly outlining the responsibilities and requirements for each task, job cards ensure that the right personnel are assigned to the right job.
This helps optimize productivity and efficiency, as tasks are handled by individuals who possess the relevant knowledge and experience. Additionally, by tracking task assignments on job cards, production managers can monitor the workload of each employee, identify any potential bottlenecks, and make necessary adjustments to ensure a balanced distribution of work.
Estimating material and equipment requirements: Job cards provide a platform for estimating the material and equipment requirements for each job or task. By detailing the specific tasks involved, job cards enable production managers to identify the materials, tools, and equipment needed to complete the job successfully.
This information can be recorded on the job card, allowing for accurate planning and procurement of necessary resources. With a clear understanding of material and equipment requirements, organizations can effectively manage their inventory, ensure timely availability of resources, and minimize delays or disruptions in the production process.
Job cards also enable better cost estimation and budgeting, as they provide a comprehensive overview of the resources needed for each job, allowing organizations to allocate their resources efficiently and avoid unnecessary expenses or shortages.
C. Quality control and assurance
Quality is an important aspect in production. Accomplishing standards of quality can be done in the following manner:
Documenting specifications and standards for each job: Job cards serve as a platform for documenting the specifications and standards that need to be adhered to for each job. This includes capturing the required quality criteria, performance benchmarks, and any specific guidelines or instructions related to quality control.
By outlining these specifications on the job card, production managers ensure that all individuals involved in the job have clear visibility and understanding of the quality requirements. This documentation helps maintain consistency and uniformity in the production process, ensuring that products or services meet or exceed the expected quality standards.
Job cards also enable organizations to track and compare actual performance against specified quality metrics, facilitating continuous improvement and adherence to quality guidelines.
Conducting inspections and audits: Job cards provide a mechanism for conducting inspections and audits as part of the quality control process. Production managers can use job cards to schedule and record inspections at various stages of the production process. This ensures that quality checks are performed systematically and consistently.
Job cards may include checkpoints or milestones where inspections should take place, and they can also serve as a repository for documenting inspection results and any required corrective actions. Conducting regular audits and inspections based on the information provided in job cards helps identify and rectify quality issues in a timely manner.
It allows for the early detection of deviations from quality standards, enabling organizations to take corrective actions promptly and prevent the production of defective or substandard products. By integrating quality control measures into job cards, organizations can foster a culture of quality assurance and ensure customer satisfaction.
D. Communication and coordination
Communication is a crucial aspect for efficient functioning of an organization. Transparent communication paves the way for greater decision-making and better coordination among the teams.
Facilitating effective communication between teams and departments: Job cards play a crucial role in facilitating effective communication between different teams and departments involved in the production process. Each job card contains essential information about the job, including task details, requirements, and timelines.
This information serves as a reference point for teams to communicate and collaborate effectively. It ensures that all relevant stakeholders have access to the necessary information, allowing them to align their activities, share updates, and address any issues or concerns.
Job cards can be shared electronically or physically, enabling seamless communication across departments, shifts, or even different locations. By providing a standardized format for sharing job-related information, job cards promote clarity, reduce misunderstandings, and foster efficient communication channels among teams and departments.
Enhancing coordination and collaboration among employees: Job cards contribute to enhancing coordination and collaboration among employees involved in the production process. When tasks and responsibilities are clearly defined on job cards, employees can easily understand their roles and dependencies within the overall workflow.
This clarity enables smooth coordination between different individuals or teams, as they can see how their work aligns with others and how their tasks contribute to the larger project. Job cards also serve as a platform for employees to share updates, progress, and any relevant information related to the job.
This information sharing fosters collaboration, as employees can provide insights, seek assistance, or offer suggestions to improve efficiency and quality. By promoting effective coordination and collaboration, job cards help streamline the production process, minimize delays, and ensure that everyone is working towards the same goals and objectives.
Features and Components of Job Cards
The features and components of job cards are crucial elements that contribute to their effectiveness in modern production management. By examining the various components and functionalities of job cards, we can gain a deeper understanding of their role in organizing and documenting work activities.
These features encompass essential details such as job identification, task breakdown, time and resource tracking, as well as quality standards and specifications.
Understanding the components of job cards provides insights into how they facilitate efficient production management, resource allocation, and quality control processes, ultimately contributing to enhanced productivity and operational success.
A. Job details and identification
Job cards include essential details such as the job title, description, and customer information.
Job title, description, and customer information:
The job title provides a concise and clear identification of the specific job or project being undertaken. The description elaborates on the scope and requirements of the job, outlining the tasks and activities involved. Customer information includes details about the client or customer for whom the job is being performed.
By capturing these job details, job cards provide a comprehensive overview of the job's purpose, scope, and target audience, ensuring that all individuals involved have a clear understanding of the job's context and objectives.
Unique identification number or code: Job cards are typically assigned a unique identification number or code to ensure proper tracking and management of each job. This identification number serves as a reference point for easy retrieval and organization of job-related information.
It allows for efficient categorization and sorting of job cards, enabling production managers to quickly locate specific jobs and access relevant details. The unique identification number also facilitates communication and coordination, as it becomes a common reference when discussing or referring to a particular job.
This numbering or coding system helps eliminate confusion, streamline processes, and maintain accurate records of job-related activities.
By including job title, description, customer information, and a unique identification number or code, job cards provide a comprehensive and identifiable framework for tracking and managing individual jobs within the production management system. These components ensure that each job is clearly defined, easily distinguishable, and can be effectively monitored throughout its lifecycle.
B. Task breakdown and instructions
The task breakdown ensures that all essential activities are identified and assigned, while detailed instructions provide employees with the necessary guidance to perform their tasks accurately and efficiently. This level of clarity and structure helps streamline the production process, enhance productivity, and ensure consistency in the delivery of products or services.
List of specific tasks and activities: Job cards provide a detailed breakdown of the specific tasks and activities that need to be accomplished for a particular job. This includes a comprehensive list of the individual steps or actions required to complete the job successfully.
The task breakdown ensures that all necessary activities are identified and accounted for, providing a clear roadmap for the job's execution. By listing specific tasks and activities on the job card, production managers can ensure that nothing is overlooked, and all essential components of the job are addressed.
Detailed instructions and guidelines for each task: In addition to listing the tasks, job cards often include detailed instructions and guidelines for each task. These instructions provide clear guidance on how each task should be executed, including any specific procedures, techniques, or requirements.
Detailed instructions help standardize the execution of tasks, ensuring consistency and quality throughout the production process. They provide employees with clear directions on what needs to be done, how it should be done, and any critical considerations or safety precautions.
By incorporating a comprehensive breakdown of tasks and providing detailed instructions, job cards enable effective planning and execution of jobs within the production management system.
C. Time and resource tracking
By tracking the start and end times of tasks and recording the required equipment, materials, and tools, job cards provide valuable insights into the utilization of time and resources within the production management system. This information facilitates efficient planning, resource allocation, and scheduling, enabling organizations to optimize productivity, minimize wastage, and ensure timely completion of jobs.
Start and end time of each task: Job cards facilitate the tracking of time spent on each task by recording the start and end times of individual tasks. Production managers can document the precise time at which each task begins and ends, providing a clear timeline of task execution.
By tracking the start and end times, organizations can analyze and evaluate the efficiency and productivity of their production processes. This data can be utilized to identify bottlenecks, optimize workflow, and improve time management.
Time tracking on job cards also enables accurate estimation of project durations, assists in scheduling and resource allocation, and helps in identifying any potential delays or deviations from planned timelines.
Equipment, materials, and tools required: Job cards serve as a repository for capturing the equipment, materials, and tools required for each task or job. Production managers can list the specific resources needed to complete the task successfully. This includes identifying and documenting the necessary equipment, raw materials, components, or tools that are essential for the task execution.
By specifying the resource requirements on job cards, organizations can effectively manage their inventory and procurement processes. This ensures that the necessary resources are available when needed, minimizing delays and disruptions in the production process.
It also aids in cost estimation and budgeting, as job cards provide visibility into the resources required for each task, enabling organizations to allocate resources efficiently and avoid unnecessary expenses or shortages.
D. Quality standards and specifications
By documenting quality criteria and benchmarks, as well as establishing standards for measurements and inspections on job cards, organizations can effectively monitor and control the quality of their production processes. This enables them to meet customer expectations, achieve consistency in output, and continuously improve their quality performance.
1. Documented quality criteria and benchmarks: Job cards incorporate the documentation of quality criteria and benchmarks for each task or job. This includes outlining the specific quality standards and expectations that need to be met. By documenting these criteria and benchmarks on the job cards, production managers ensure that employees have clear visibility and understanding of the expected quality levels.
This information serves as a reference point for employees to perform their tasks in accordance with the established quality standards. It helps maintain consistency, uniformity, and customer satisfaction by ensuring that products or services meet or exceed the defined quality requirements.
Documented quality criteria and benchmarks enable organizations to track and measure the actual performance against the specified quality standards, facilitating continuous improvement and adherence to quality guidelines.
Standards for measurements and inspections: Job cards also incorporate standards for measurements and inspections to ensure quality control and assurance. They specify the methods, tools, and criteria for measuring and inspecting the quality attributes of the products or services being produced.
This includes detailing the specific measurements, tolerances, or specifications that need to be met during the production process. By establishing these standards on job cards, organizations ensure consistent and accurate measurements and inspections. It provides a standardized framework for evaluating the quality of the output and detecting any deviations or defects.
These standards help in identifying areas for improvement, taking corrective actions, and maintaining high-quality standards throughout the production process.
Benefits of Using Job Cards in Modern Production Management
The utilization of job cards in modern production management brings forth a multitude of benefits that enhance efficiency, accountability, and overall operational success. By exploring the advantages of using job cards, we can gain insights into how they contribute to improved productivity, streamlined decision-making, and effective resource allocation.
These benefits encompass enhanced traceability, increased productivity, streamlined decision-making, and improved coordination among teams. Understanding the advantages of incorporating job cards into production management processes underscores their significance in driving efficient operations and achieving optimal outcomes in today's dynamic business landscape.
A. Improved productivity and efficiency
By providing clear task assignments and deadlines, as well as preventing duplication and rework, job cards contribute to improved productivity and efficiency within modern production management. They enable employees to work more effectively, minimize errors, and optimize the utilization of resources, ultimately leading to streamlined operations and enhanced output.
Clear task assignments and deadlines: Job cards play a vital role in improving productivity and efficiency by providing clear task assignments and deadlines. Each job card specifies the tasks to be completed and assigns them to the appropriate personnel or teams. This clarity eliminates ambiguity and ensures that employees know their responsibilities and can focus on their assigned tasks.
Furthermore, job cards often include deadlines or target completion dates for each task, enabling employees to prioritize their work and manage their time effectively. Clear task assignments and deadlines minimize confusion, prevent tasks from being overlooked or delayed, and promote a sense of accountability among employees.
By providing a structured framework for task management, job cards facilitate efficient workflow and help teams meet their targets.
Avoidance of duplication and rework: Job cards contribute to improved productivity and efficiency by helping to avoid duplication of work and unnecessary rework. When tasks and requirements are clearly documented on job cards, employees can easily access the information they need to perform their tasks accurately.
This prevents duplication of efforts, as employees can see what tasks have already been assigned and completed by others. Additionally, job cards often include detailed instructions and guidelines, reducing the likelihood of errors or mistakes that would require rework.
By promoting a systematic approach to task execution, job cards help minimize wastage, optimize resources, and ensure that work is done right the first time. This reduces overall production time and increases efficiency, leading to improved productivity.
B. Enhanced traceability and accountability
By enabling easy identification of responsible individuals and facilitating auditing and analysis of performance metrics, job cards enhance traceability and accountability within modern production management. They provide a clear record of task ownership and performance, empowering organizations to monitor progress, make data-driven decisions, and promote a culture of accountability and improvement.
Easy identification of responsible individuals: Job cards facilitate enhanced traceability and accountability by providing easy identification of responsible individuals for each task or job. With clear task assignments documented on job cards, it becomes evident who is accountable for the completion of specific tasks.
This promotes transparency and clarity within the production management system, ensuring that there is no ambiguity regarding task ownership. By clearly identifying responsible individuals, job cards enable efficient communication, coordination, and collaboration among team members.
It becomes easier to track progress, address any delays or issues, and ensure that tasks are completed within the designated timeframe. Enhanced traceability through job cards enhances accountability and encourages a sense of ownership among employees, fostering a culture of responsibility and commitment.
Auditing and analysis of performance metrics: Job cards provide a valuable source of data for auditing and analyzing performance metrics within the production management system. By recording essential information such as task details, timelines, and resource utilization, job cards enable organizations to evaluate performance against set benchmarks.
This data can be used to conduct performance audits, comparing actual results with expected outcomes. Job cards also facilitate the analysis of key performance indicators (KPIs) related to productivity, efficiency, and quality. By analyzing the data captured on job cards, organizations can identify areas for improvement, track trends, and make informed decisions to optimize processes and resource allocation.
The availability of comprehensive performance metrics through job cards enables organizations to drive continuous improvement, enhance productivity, and ensure accountability throughout the production management process.
C. Streamlined decision-making and problem-solving
By providing access to historical data for analysis and decision support, as well as aiding in identifying bottlenecks and areas for improvement, job cards streamline decision-making and problem-solving within modern production management. They enable organizations to leverage past performance data to make informed decisions, optimize processes, and address operational challenges effectively.
Access to historical data for analysis and decision support: Job cards provide access to valuable historical data that can be utilized for analysis and decision support. As job cards capture detailed information about tasks, timelines, resource utilization, and quality metrics, they serve as a repository of historical data related to production processes.
By analyzing this data, production managers can gain insights into past performance, trends, and patterns. This historical data enables informed decision-making, as it provides a basis for evaluating the effectiveness of past strategies, identifying successful approaches, and determining areas that require improvement.
Access to historical data through job cards helps organizations make data-driven decisions, optimize resource allocation, and implement process enhancements to drive productivity and efficiency.
Identifying bottlenecks and areas for improvement: Job cards play a crucial role in identifying bottlenecks and areas for improvement within the production management system. By reviewing the data recorded on job cards, production managers can identify tasks or processes that consistently face delays, resource constraints, or quality issues.
This information helps pinpoint bottlenecks and areas where operational improvements can be made. Job cards also provide insights into task dependencies, allowing managers to understand how one task affects the overall workflow and identify potential areas for optimization. By analyzing job card data, organizations can streamline processes, eliminate inefficiencies, and implement targeted improvements to enhance productivity and overall performance.
Job cards serve as valuable tools in problem-solving by providing a detailed overview of the production process, enabling a systematic approach to identifying and resolving issues.
Challenges and Considerations in Implementing Job Cards
While job cards offer numerous benefits in modern production management, their successful implementation can face certain challenges and considerations. Understanding these challenges is essential to ensure a smooth integration of job cards into the production management system.
This section delves into the potential hurdles organizations may encounter when implementing job cards. It examines factors such as resistance to change, employee training, integration with existing systems, and data synchronization.
By addressing these challenges and considerations, organizations can overcome barriers and optimize the adoption and utilization of job cards, leading to more efficient and effective production management practices.
A. Resistance to change and adoption
One of the key challenges in implementing job cards in modern production management is the resistance to change and adoption from employees. Introducing a new system or process can disrupt established routines and workflows, leading to resistance or reluctance among employees to embrace job cards.
Some common reasons for resistance include fear of the unknown, concerns about increased workload or additional responsibilities, and skepticism about the benefits of implementing job cards.
To address resistance to change and encourage adoption of job cards, organizations can take the following steps:
Communicate the purpose and benefits: It is crucial to clearly communicate the reasons behind implementing job cards and the potential benefits they offer. This helps employees understand the value and purpose of the system, dispelling misconceptions and addressing concerns. Emphasize how job cards can streamline work, improve productivity, and enhance overall efficiency.
Provide training and support: Proper training and support are essential to help employees adapt to the new system. Offer comprehensive training programs that familiarize employees with job cards, including their purpose, components, and how to use them effectively. Provide ongoing support, such as documentation, FAQs, or dedicated support channels, to address any questions or challenges that arise during the transition period.
Foster employee involvement and ownership: Involve employees in the implementation process by seeking their input, feedback, and suggestions. This helps create a sense of ownership and inclusion, making employees feel valued and invested in the success of the job card system. Encourage them to provide insights on how job cards can be tailored to their specific roles and responsibilities.
Lead by example: Leadership plays a crucial role in driving change. Leaders should actively embrace and promote the use of job cards to set an example for employees. When employees see their managers and supervisors embracing the change, it can help overcome resistance and encourage wider adoption throughout the organization.
Monitor and evaluate progress: Regularly monitor the progress of job card implementation and evaluate its impact on productivity and efficiency. Collect feedback from employees and address any concerns or challenges that arise. This iterative approach allows for continuous improvement and refinement of the job card system based on real-world experiences and employee feedback.
By addressing resistance to change and adoption, organizations can overcome employee reluctance and successfully implement job cards in their production management processes. Effective communication, training, employee involvement, and leadership support are key factors in fostering a culture of acceptance and maximizing the benefits of job card implementation.
B. Integration with existing systems and technologies
Another significant challenge in implementing job cards in modern production management is the integration with existing systems and technologies. Organizations may already have established software, databases, or other tools in place to manage their production processes. Integrating job cards seamlessly with these existing systems can be complex and require careful planning and coordination.
Here are some considerations to address the integration challenge:
Compatibility and interoperability: Ensure that the job card system is compatible with existing software and technologies used in the organization. Assess the compatibility of data formats, APIs, and interfaces to facilitate smooth integration. If necessary, consult with IT experts or vendors to ensure compatibility and interoperability between systems.
Data synchronization: Establish mechanisms for data synchronization between the job card system and other existing systems. This ensures that information is consistently updated and shared across platforms, avoiding discrepancies or data duplication. Automate data synchronization processes where possible to minimize manual effort and improve accuracy.
Training and familiarity: Provide training and support to employees on how to use the integrated system effectively. Familiarize them with any new features or functionalities resulting from the integration. Ensure that employees understand how to navigate between different systems and leverage the integrated data to enhance their productivity and decision-making.
Testing and validation: Conduct thorough testing and validation before fully implementing the integrated job card system. Test data flows, data accuracy, and system performance to ensure smooth operation and identify any potential issues or bottlenecks. Address any concerns or anomalies that arise during the testing phase.
Scalability and future growth: Consider the scalability of the integrated system to accommodate future growth and evolving needs. Anticipate changes in production processes or technologies and ensure that the job card system can adapt and integrate seamlessly with future systems or upgrades.
Collaboration with IT department: Collaborate closely with the IT department or relevant stakeholders to ensure a smooth integration process. Involve IT experts early on to assess technical feasibility, provide guidance, and support the integration efforts.
By addressing the integration challenge, organizations can effectively incorporate job cards into their existing systems and technologies. Seamless integration allows for efficient data exchange, streamlined workflows, and improved overall production management processes. Collaboration, compatibility, and proactive planning are essential in overcoming integration challenges and maximizing the benefits of the integrated job card system.
Conclusion
In conclusion, job cards play a significant role in modern production management by providing a structured framework for tracking, coordinating, and documenting work activities. They offer numerous benefits, including improved productivity and efficiency, enhanced traceability and accountability, streamlined decision-making, and effective resource allocation.
Job cards facilitate clear task assignments, deadlines, and instructions, enabling smooth workflow management and minimizing duplication or rework. They also contribute to improved traceability and accountability by easily identifying responsible individuals and providing valuable data for analysis and decision support. Furthermore, job cards help identify bottlenecks and areas for improvement, promoting continuous enhancement of production processes.
However, implementing job cards can present challenges, such as resistance to change and adoption from employees, and integration with existing systems and technologies. These challenges can be overcome through effective communication, training, employee involvement, leadership support, and careful planning for integration.
Overall, job cards serve as valuable tools in modern production management, facilitating efficient coordination, effective communication, and streamlined processes. By embracing job cards and addressing the challenges in their implementation, organizations can optimize productivity, improve quality control, and achieve operational success in today's dynamic business environment.
How can Deskera Help You?
Deskera ERP and MRP systems help you to keep your business units organized. The system's primary functions are as follows:
- Keep track of your raw materials and final items inventories
- Control production schedules and routings
- Keep a bill of materials
- Produce thorough reports
- Make your own dashboards
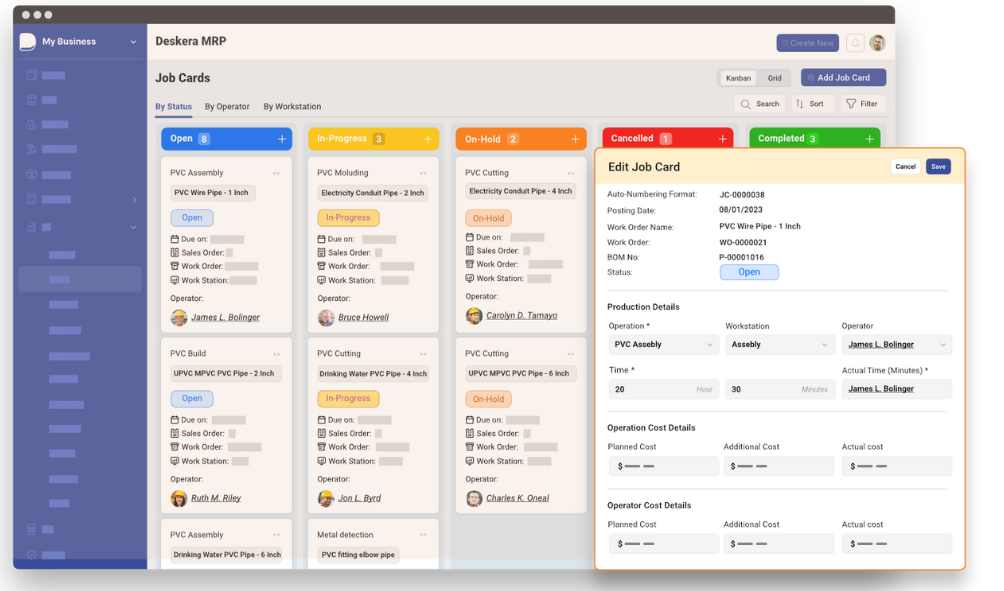
Deskera's integrated financial planning tools enable investors to better plan and track their investments. It can assist investors in making faster and more accurate decisions.
Deskera Books allows you to better manage your accounts and finances. Maintain good accounting practices by automating tasks like billing, invoicing, and payment processing.
Deskera CRM is a powerful solution that manages your sales and helps you close deals quickly. It not only enables you to perform critical tasks like lead generation via email, but it also gives you a comprehensive view of your sales funnel.
Deskera People is a straightforward tool for centralizing your human resource management functions.
Key Takeaways
- Job cards provide a structured framework for tracking, coordinating, and documenting work activities in production management.
- Clear task assignments and deadlines on job cards improve productivity and ensure efficient workflow management.
- Job cards help prevent duplication of work and unnecessary rework, leading to enhanced efficiency and minimized wastage.
- By documenting quality criteria and benchmarks, job cards facilitate adherence to quality standards and improve overall product or service quality.
- Job cards enable easy identification of responsible individuals, promoting traceability and accountability within the production process.
- Access to historical data on job cards supports analysis and decision-making, enabling organizations to make informed choices based on past performance.
- Job cards aid in identifying bottlenecks and areas for improvement, allowing for targeted enhancements to increase productivity and efficiency.
- Resistance to change and adoption is a common challenge when implementing job cards, which can be overcome through effective communication, training, and involvement of employees.
- Integrating job cards with existing systems and technologies requires careful planning, compatibility assessment, and collaboration with IT departments.
- Successful implementation of job cards in production management leads to improved productivity, streamlined decision-making, enhanced traceability, and optimized resource allocation, ultimately contributing to operational success.
Related Articles
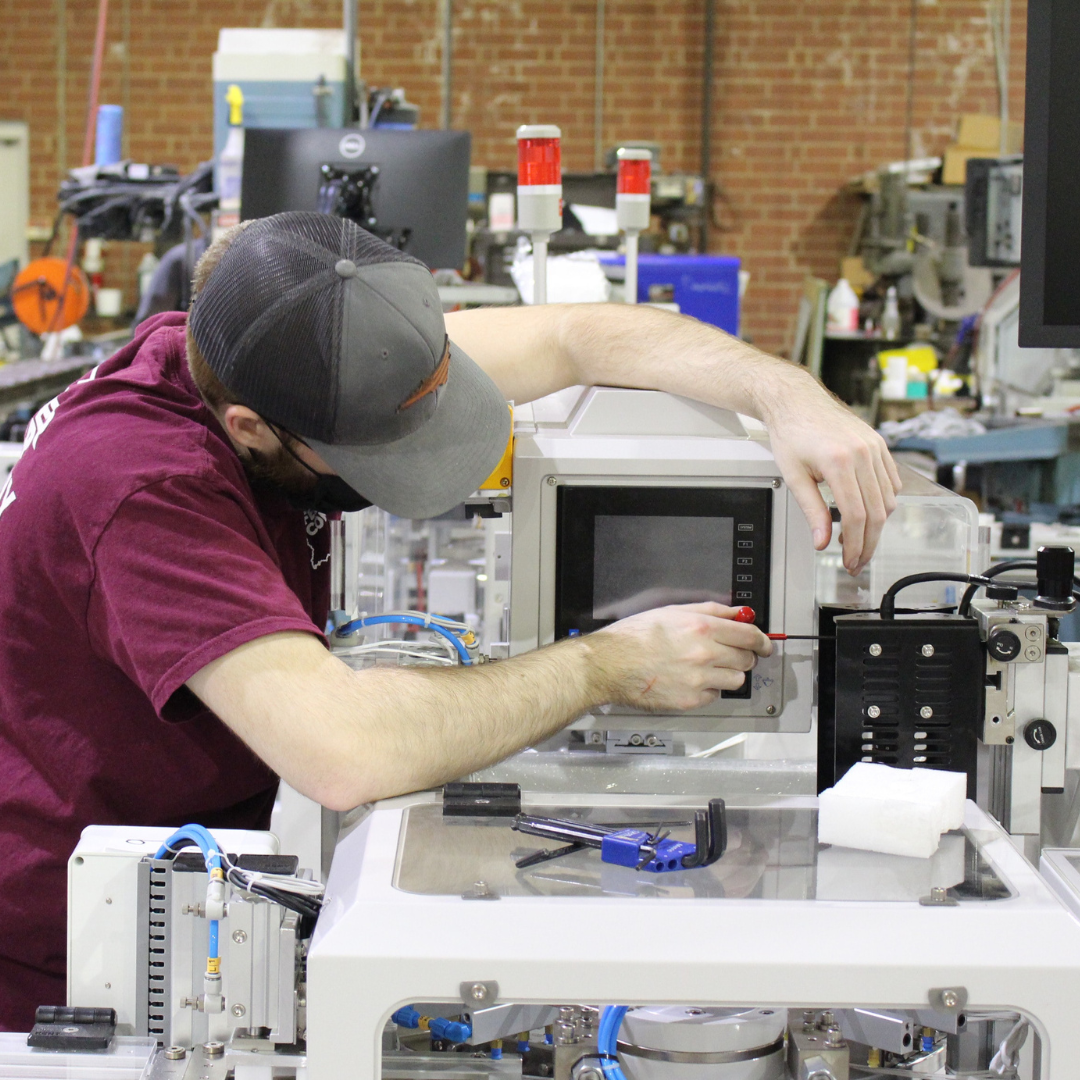
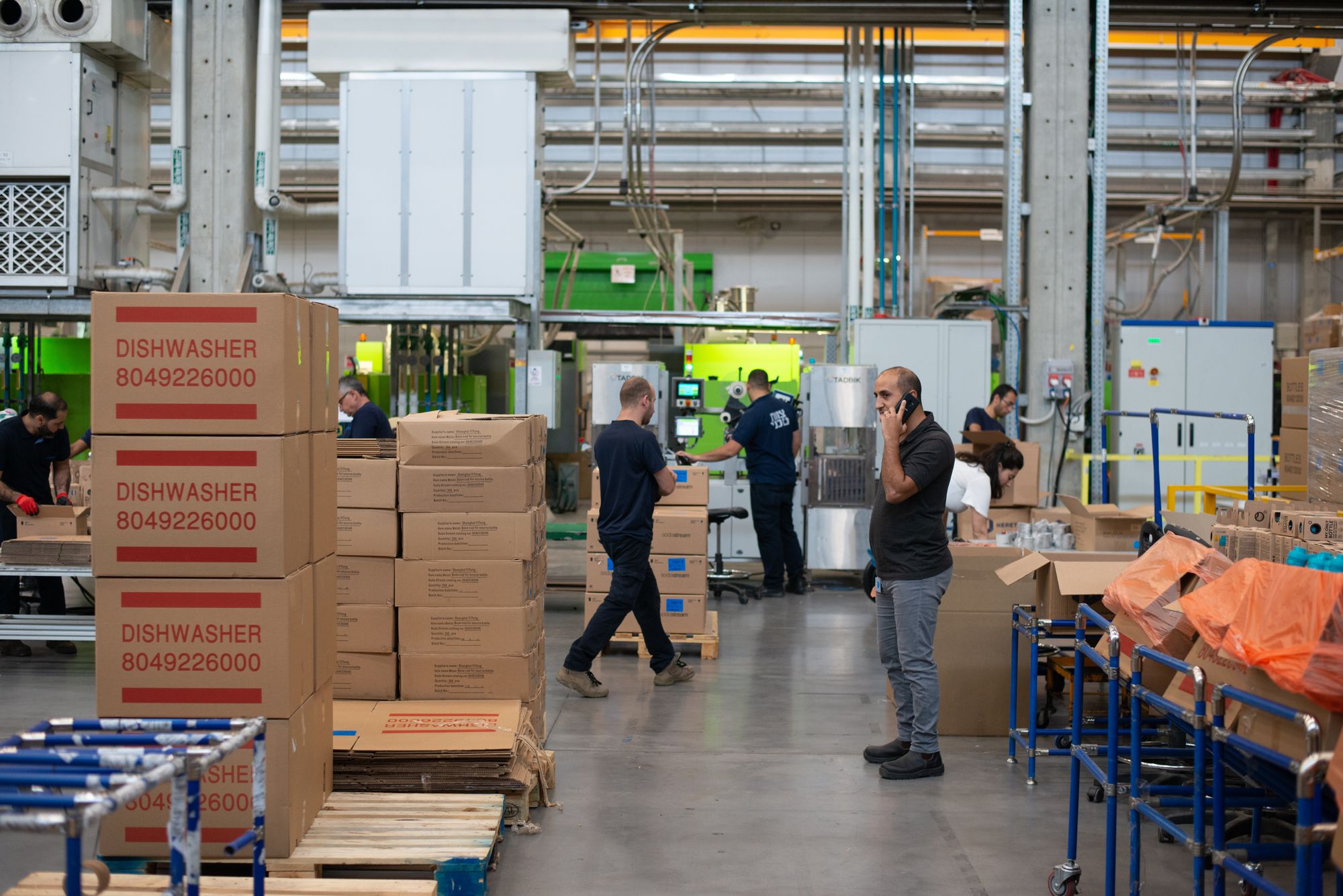
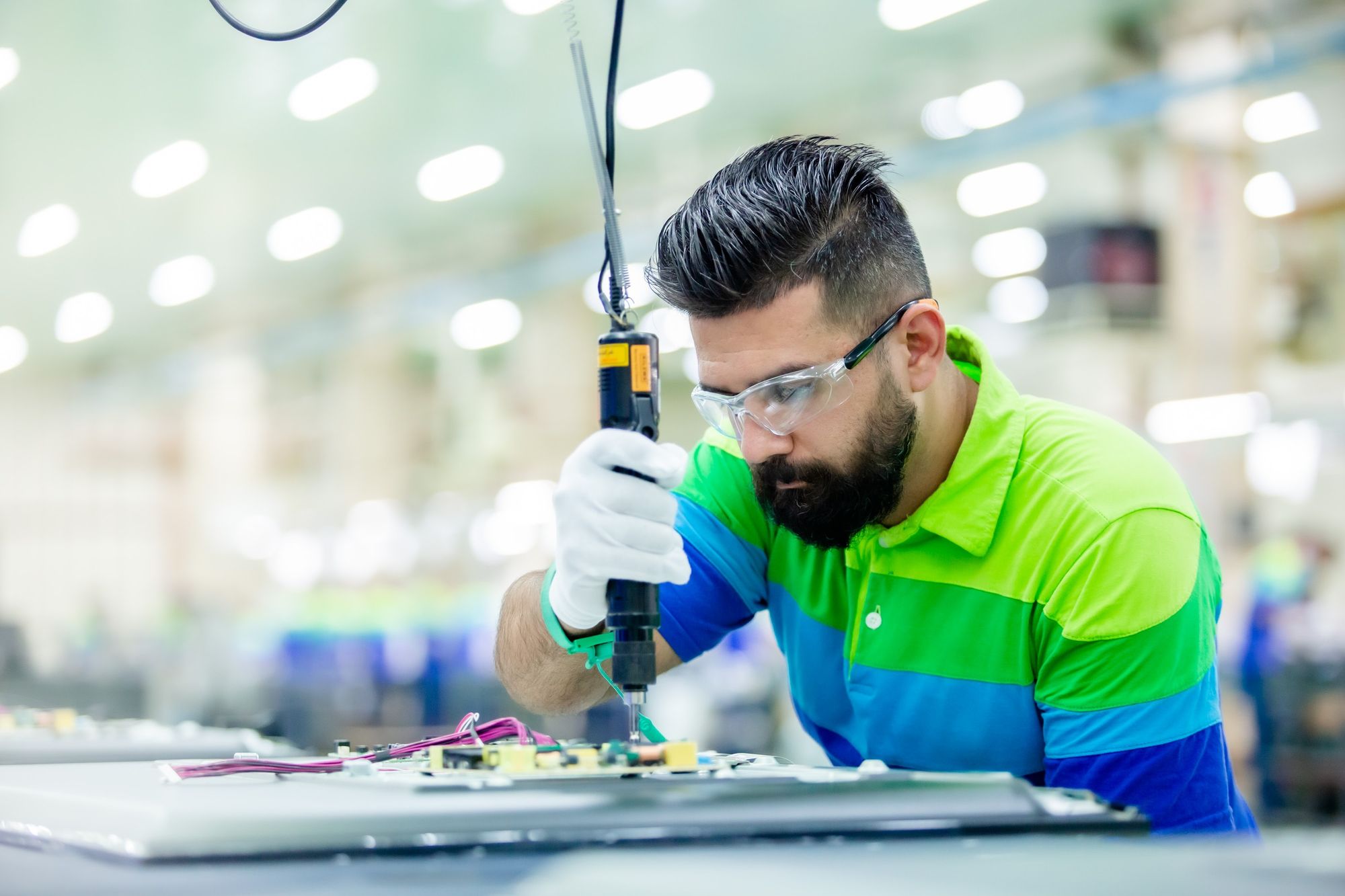
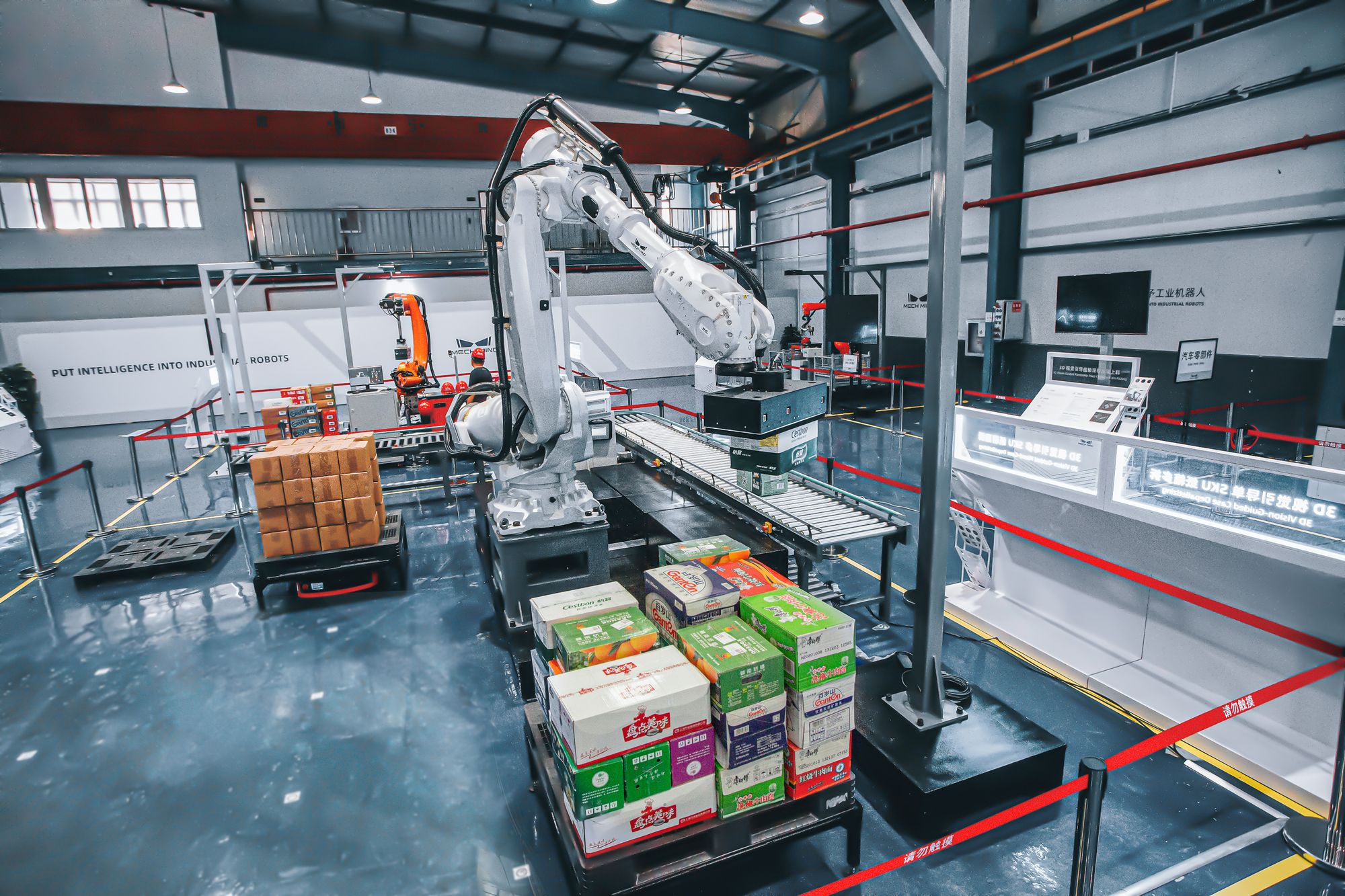