Order management is essential for any manufacturing enterprise. It allows businesses to control the flow of products through the manufacturing process and to meet customer expectations. When operational efficiency is maximized, it translates into improved customer service and increased profitability. Unfortunately, many companies struggle to implement an order management strategy that leads to operational excellence.
In a paper published by the Harvard Business Review, it was found that only 17 percent of U.S. manufacturing firms have achieved “high-performance” levels in terms of output, quality, and delivery on time. To improve these dismal numbers, companies must first understand how order management can support high performance.
There are several key elements that must be included in an effective order management strategy: visibility, timeliness, accuracy, and communication. By addressing each of these areas in a comprehensive manner, companies can achieve operational excellence and better serve their customers.
In today’s guide, we’ll discuss everything related to achieving operational excellence through an integrated order management strategy. Let’s take a look at the table of content below:
- What is Operational Excellence?
- Importance of Operational Excellence
- Crucial Aspects of Operational Excellence
- The Significance of Order Management
- Implementation of Different Methodologies
- Strategy to Achieve Operational Excellence through Integrated Order Management
- Right Process to Follow to Set Operational Excellence
- Important Benefits of Operational Excellence
- Major Industries that Can Benefit from Operational Excellence
- Important Examples of Operational Excellence
- Operational Excellence: KPIs and Metrics?
- Framework Operational Excellence
- Step-by-Step Implementation Plan for Operational Excellence
- Best and Important Practices for Operational Excellence
- Overcoming and Addressing Operational Excellence Challenges
- Frequently Asked Questions (FAQs) Associated with Operational Excellence through an Integrated Order Management
- Wrapping Up
- How Deskera Can Assist You?
Let's get started!
What is Operational Excellence?
Operational excellence refers to the relentless pursuit of efficiency, effectiveness, and continuous improvement in an organization's operations. It involves optimizing processes, eliminating waste, and maximizing productivity to achieve superior performance and deliver exceptional value to customers.
Importance of Operational Excellence
Operational excellence is crucial for organizations due to the following reasons:
Cost Efficiency: Operational excellence helps organizations streamline their processes, reduce waste, and optimize resource utilization. By eliminating unnecessary steps, minimizing errors, and improving productivity, operational excellence leads to cost savings and increased efficiency. This, in turn, improves profitability and provides a competitive advantage in the market.
Customer Satisfaction: Operational excellence enables organizations to consistently deliver high-quality products or services to customers. By improving processes and reducing errors, organizations can enhance customer satisfaction, meet or exceed customer expectations, and build long-term customer loyalty. Satisfied customers are more likely to become repeat customers and recommend the organization to others.
Competitive Advantage: Achieving operational excellence allows organizations to differentiate themselves from competitors. By optimizing processes, organizations can offer faster delivery, better quality, and improved customer service.
Furthermore, this enhances their market position and helps them gain a competitive edge in the industry. Operational excellence can also enable organizations to respond quickly to market changes and customer demands, staying ahead of the competition.
Innovation and Agility: Operational excellence fosters a culture of continuous improvement and innovation. By encouraging employees to identify inefficiencies, suggest improvements, and embrace change, organizations can drive innovation and adapt to evolving market conditions. This agility allows organizations to seize opportunities, respond to challenges, and stay relevant in a rapidly changing business environment.
Employee Engagement and Morale: Operational excellence initiatives involve employees at all levels of the organization. Engaging employees in process improvement activities enhances their sense of ownership, empowerment, and job satisfaction. When employees see their contributions leading to positive changes and improved outcomes, it boosts morale, motivation, and overall engagement within the organization.
Risk Mitigation: Operational excellence emphasizes robust processes, quality control, and risk management. By identifying and addressing process inefficiencies and weaknesses, organizations can reduce the likelihood of errors, defects, and operational risks. This leads to improved compliance, increased safety, and enhanced organizational resilience.
Scalability and Growth: Operational excellence provides a solid foundation for organizational scalability and growth. Efficient processes, optimized resource utilization, and standardized practices enable organizations to scale their operations without compromising quality or incurring excessive costs. This scalability allows organizations to expand their market reach, handle increased demand, and pursue growth opportunities.
Organizational Alignment: Operational excellence initiatives require cross-functional collaboration and alignment within the organization. By breaking down silos and fostering collaboration, organizations can improve communication, coordination, and overall alignment of goals and objectives. This alignment creates a unified organizational culture focused on delivering value to customers and driving continuous improvement.
In summary, operational excellence is important because it drives cost efficiency, customer satisfaction, competitive advantage, innovation, employee engagement, risk mitigation, scalability, and organizational alignment. By striving for operational excellence, organizations can optimize their performance, enhance their market position, and achieve sustainable success in today's dynamic business landscape.
Crucial Aspects of Operational Excellence
Following, we’ll discuss important key aspects of operational excellence including:
Process Optimization: Streamlining and improving processes across the organization to eliminate bottlenecks, reduce cycle times, and enhance efficiency. This involves identifying and eliminating non-value-added activities and implementing best practices.
Lean Principles: Embracing lean methodologies such as Lean Six Sigma to minimize waste, improve quality, and increase customer satisfaction. Lean principles focus on creating value, continuous improvement, and empowering employees to identify and eliminate inefficiencies.
Continuous Improvement: Encouraging a culture of continuous improvement at all levels of the organization. This involves regularly reviewing and enhancing processes, seeking feedback from employees and customers, and implementing changes to drive ongoing improvement.
Standardization and Consistency: Establishing standardized processes and practices across the organization to ensure consistency, reduce variability, and enhance quality. Standardization enables easier replication, scalability, and better control over operations.
Data-Driven Decision Making: Leveraging data and analytics to make informed decisions and drive operational improvements. This includes collecting and analyzing data to identify trends, insights, and areas for optimization.
Employee Engagement and Empowerment: Engaging and empowering employees to contribute to operational excellence. Encouraging a culture of ownership, collaboration, and innovation, where employees are empowered to identify and implement improvements.
Customer Focus: Aligning operational activities with customer needs and expectations. This involves understanding customer requirements, providing superior service, and continuously seeking ways to enhance the customer experience.
Supply Chain Optimization: Optimizing the end-to-end supply chain to improve efficiency, reduce costs, and enhance responsiveness. This includes effective inventory management, streamlined logistics, and strong supplier relationships.
The goal of operational excellence is to create a culture of continuous improvement, where every employee is engaged in seeking innovative ways to optimize operations, eliminate waste, and enhance overall performance. By achieving operational excellence, organizations can gain a competitive edge, improve profitability, and deliver superior value to customers.
The Significance of Order Management
Following, we've discussed the significance of order management. Let's learn:
A. Definition and Scope of Order Management:
Order management refers to the process of efficiently and effectively handling customer orders from the point of receipt to the final delivery. It involves managing and coordinating all activities related to order processing, fulfillment, and customer service. The scope of order management encompasses various stages, including order entry, order validation, inventory allocation, order tracking, shipping, and customer support.
B. Key Components of an Effective Order Management System:
Order Capture and Entry: A robust order management system should provide a seamless process for capturing and entering customer orders. This can be achieved through various channels such as online platforms, mobile applications, call centers, or in-person interactions.
Order Validation and Processing: Once an order is received, it is essential to validate its accuracy and feasibility. This involves verifying product availability, pricing, discounts, and customer information. The system should have automated checks to ensure that orders meet predefined criteria and business rules.
Inventory Management: An effective order management system integrates with inventory management systems to provide real-time visibility of available stock. This allows for accurate allocation of inventory to fulfill customer orders promptly. It helps prevent overselling or stockouts, leading to improved customer satisfaction.
Order Tracking and Status Updates: Customers expect visibility and transparency regarding their orders. An order management system should provide real-time tracking capabilities, allowing customers to monitor the status of their orders. Automated status updates and notifications keep customers informed about order progress, shipment details, and estimated delivery dates.
Integration with Logistics and Shipping: Seamless integration with logistics and shipping partners is vital for efficient order fulfillment. The order management system should facilitate automated communication and exchange of data with shipping carriers to generate shipping labels, track shipments, and manage returns or exchanges.
Customer Service and Support: Order management systems should have built-in features or integration with customer service tools to provide timely and effective support. This includes handling inquiries, addressing order-related issues, and facilitating returns or exchanges. Access to order history and customer information enables personalized customer service.
C. Link between Order Management and Operational Excellence:
Effective order management plays a significant role in achieving operational excellence. Here's how it contributes to operational excellence:
Improved Efficiency: An integrated order management system streamlines order processing, reducing manual effort and minimizing errors. Automated workflows and standardized processes enhance efficiency and productivity, allowing employees to focus on value-added tasks. This leads to faster order processing, reduced lead times, and increased throughput.
Enhanced Customer Experience: A well-executed order management process leads to a superior customer experience. The accurate order capture, prompt order confirmation, and proactive communication regarding order status create a positive impression and build customer trust. Timely and error-free order fulfillment increases customer satisfaction and loyalty.
Optimal Inventory Management: An effective order management system provides real-time visibility of inventory levels and demand patterns. This enables better inventory planning and optimization, minimizing stockouts and excess inventory. Improved inventory management leads to reduced carrying costs, improved cash flow, and efficient use of warehouse space.
Data-Driven Decision Making: An integrated order management system captures and stores valuable data related to customer orders, inventory, and fulfillment. This data can be analyzed to gain insights into customer behavior, demand patterns, and operational performance. Data-driven decision-making enables organizations to identify opportunities for process improvement, optimize inventory levels, and enhance overall operational efficiency.
Continuous Improvement: An order management system serves as a foundation for continuous improvement initiatives. By tracking and measuring key performance indicators (KPIs) related to order processing and fulfillment, organizations can identify areas for improvement and set targets for operational excellence. Regular analysis of KPIs enables organizations to implement process enhancements, eliminate bottlenecks, and drive continuous improvement in order management operations.
In conclusion, order management is a critical component of operational excellence. A well-designed and integrated order management system improves efficiency, enhances the customer experience, optimizes inventory management, supports data-driven decision-making, and facilitates continuous improvement. Organizations that prioritize order management and its link to operational excellence can gain a competitive advantage and drive sustainable growth.
Implementation of Different Methodologies
There are several methodologies and frameworks commonly used to implement operational excellence. Here are some of the key methodologies:
1. Shingo Model
The Shingo Model, also known as the Shingo Prize for Operational Excellence, is a framework that provides guidelines for achieving operational excellence and continuous improvement. Developed by the Shingo Institute, named after Japanese industrial engineer Shigeo Shingo, the model focuses on principles and behaviors that lead to operational excellence rather than just tools and techniques. It emphasizes the cultural and behavioral aspects of organizations in driving sustainable improvements.
The Shingo Model consists of ten guiding principles, categorized into four dimensions:
Cultural Enablers:
a. Respect for Every Individual: Promoting a culture of respect, empowerment, and engagement at all levels of the organization.
b. Lead with Humility: Encouraging leaders to serve as role models and foster a humble and learning-oriented culture.
Continuous Improvement:
a. Seek Perfection: Pursuing excellence through continuous improvement and eliminating waste.
b. Embrace Scientific Thinking: Encouraging evidence-based decision-making and problem-solving using data and experimentation.
Enterprise Alignment:
a. Focus on Process: Shifting the focus from individual tasks to end-to-end processes to achieve better flow and eliminate inefficiencies.
b. Assure Quality at the Source: Embedding quality checks and controls at each stage of the process to prevent defects and errors.
Results:
a. Create Constancy of Purpose: Aligning organizational goals and strategies with the purpose of creating value for customers.
b. Create Value for the Customer: Understanding customer needs and delivering products and services that meet or exceed their expectations.
c. Seek Systemic Thinking: Considering the interdependencies and interactions among various parts of the organization and the broader system.
The Shingo Model emphasizes the importance of embedding these principles into the culture and DNA of the organization. It encourages organizations to go beyond the superficial implementation of tools and techniques and focus on building a sustainable culture of continuous improvement.
To assess their progress toward operational excellence, organizations can apply for the Shingo Prize for Operational Excellence. The Shingo Institute evaluates applicants based on their adherence to the principles of the Shingo Model and recognizes organizations that demonstrate exceptional operational performance and a strong culture of continuous improvement.
The Shingo Model provides organizations with a comprehensive framework to guide their journey toward operational excellence. By focusing on principles and behaviors, it helps organizations create a culture of continuous improvement, employee empowerment, and customer-centricity, ultimately leading to improved operational performance and organizational success.
2. OKAPI Method
The Okapi methodology, developed by Iris Tsidon and Maya Gal. It further aims to support businesses in achieving operational excellence by identifying and addressing obstacles and challenges in the implementation process. It incorporates two foundational elements.
The Okapi methodology emphasizes the use of precise and quantifiable Key Performance Indicators (KPIs) to enhance the effectiveness of operational excellence initiatives. By setting clear and specific goals, organizations can measure their progress and outcomes more accurately.
The SMART criteria, which stands for Specific, Measurable, Achievable, Relevant, and Time-bound, are employed to develop SMART KPIs. Each KPI should be designed with the following characteristics:
Specific: The KPI should clearly define the desired outcome or target, leaving no room for ambiguity. It should address a specific aspect of operational excellence, such as cycle time reduction or defect rate improvement.
Measurable: The KPI should have quantifiable metrics or parameters that enable objective measurement. This allows organizations to track progress and assess the success of their operational excellence initiatives.
Achievable: The KPI should be attainable within the organization's capabilities and resources. It should stretch performance expectations without being unreasonably difficult to achieve, striking a balance between ambition and feasibility.
Relevant: The KPI should directly align with the organization's strategic objectives and operational excellence goals. It should be meaningful and relevant to the overall improvement efforts.
Time-bound: The KPI should have a specific timeframe or deadline for achieving the target. This provides a sense of urgency and helps organizations monitor progress within defined time intervals.
By adhering to the SMART criteria, organizations can develop KPIs that are precise, measurable, and aligned with their operational excellence objectives. This enables them to track performance accurately, make data-driven decisions, and continually improve their operational processes.
The use of SMART KPIs helps organizations set clear and measurable performance targets that are aligned with their strategic goals. These KPIs provide a framework for measuring progress, identifying areas for improvement, and evaluating the effectiveness of operational excellence initiatives.
Following, we've discussed the challenges that companies are facing in association with the Okapi methodology:
Disconnection: One common challenge organizations face is a disconnection between various departments or functions within the company. Silos can hinder effective communication, collaboration, and the sharing of information necessary for operational excellence. Overcoming disconnection requires breaking down barriers, fostering cross-functional collaboration, and establishing channels for transparent communication and knowledge sharing.
Absence of Progress: Many companies struggle with making tangible progress in their operational excellence initiatives. This can occur due to various reasons such as inadequate goal setting, insufficient implementation plans, or a lack of accountability. Overcoming this challenge involves setting clear and realistic goals, establishing action plans with measurable milestones, and regularly tracking and reviewing progress to ensure momentum and continuous improvement.
Inability to Change to Remain Competitive: In today's rapidly evolving business landscape, the inability to adapt and change can hinder an organization's competitiveness. Companies may face challenges in embracing new technologies, adopting innovative practices, or responding effectively to market dynamics. Addressing this challenge involves fostering a culture of agility, promoting a mindset of continuous learning and improvement, and creating mechanisms for monitoring and responding to industry changes.
Data Too Complex to Understand Quickly: Data complexity can pose a significant challenge when implementing operational excellence initiatives. Organizations may struggle with collecting, analyzing, and utilizing data effectively to drive decision-making and improvements. Overcoming this challenge requires investing in data management systems and tools, establishing data governance practices, and providing training and support to employees to enhance their data literacy and analytical skills.
Lack of Coherent Management Plan: Without a well-defined and coherent management plan, organizations may face difficulties in aligning their operational excellence efforts with their strategic objectives. This challenge can result in a lack of clarity, inconsistent execution, and disjointed initiatives. Addressing this challenge involves developing a comprehensive management plan that clearly articulates the objectives, actions, timelines, responsibilities, and measures for success. It should provide a roadmap for guiding and coordinating all operational excellence activities throughout the organization.
By addressing these common challenges, organizations can enhance their ability to implement operational excellence effectively. The Okapi methodology emphasizes identifying and proactively addressing these obstacles to foster a more successful and sustainable journey towards operational excellence.
Flawless Execution (FLEX)
Flawless Execution (FLEX) is a methodology developed by the Afterburner, Inc., a consulting and training firm founded by former U.S. military fighter pilots. FLEX aims to improve operational performance and execution by applying military-inspired principles and techniques in a business context. It focuses on aligning teams, maintaining situational awareness, and executing with discipline to achieve desired outcomes.
The FLEX methodology consists of six key steps:
- Plan: The first step in FLEX is to create a clear and concise plan that outlines the objectives, goals, and tasks required to achieve the desired outcome. The plan should identify potential risks, prioritize activities, and establish specific milestones.
- Brief: Once the plan is developed, it is essential to effectively communicate it to all team members. The brief ensures that everyone understands the plan, their roles, and responsibilities. It encourages open communication, addresses any concerns or questions, and fosters a shared understanding of the mission.
- Execute: During the execution phase, teams focus on accomplishing their assigned tasks while maintaining situational awareness. This involves maintaining clear communication, monitoring progress, adapting to changing circumstances, and making real-time decisions to stay on track.
- Debrief: After completing the execution phase, teams conduct a debrief to reflect on the outcomes, identify successes, and uncover areas for improvement. The debrief encourages honest feedback, facilitates learning, and captures lessons learned for future missions.
- Learn: The learn phase involves analyzing the insights gained from the debrief and applying them to improve future performance. It focuses on identifying patterns, best practices, and areas of improvement. The learn phase helps organizations continuously adapt and refine their approach to achieve higher levels of operational excellence.
- Adapt: The final step in FLEX is to adapt the plan based on the lessons learned and new information. This iterative approach allows organizations to adjust strategies, processes, and tactics to optimize performance and achieve better outcomes over time.
The FLEX methodology emphasizes the importance of disciplined execution, effective communication, and continuous improvement. It helps organizations enhance their operational performance by aligning teams, enhancing situational awareness, and fostering a culture of accountability and adaptability.
By adopting the principles of Flawless Execution, organizations can improve their ability to execute complex tasks, navigate uncertainty, and achieve their operational objectives more efficiently and effectively.
Kaizen
Kaizen, a Japanese term meaning "change for the better" or "continuous improvement," is a philosophy and methodology that focuses on making incremental and continuous improvements in all aspects of an organization. It originated in Japan and has been widely adopted in various industries worldwide. Kaizen emphasizes a bottom-up approach, involving every employee in the organization, from top management to front-line workers, in the pursuit of improvement.
Key principles and components of Kaizen include:
Continuous Improvement: Kaizen promotes the idea that no process, system, or method is ever perfect and that there is always room for improvement. It encourages organizations to continuously seek ways to eliminate waste, increase efficiency, and enhance quality.
Respect for People: Kaizen recognizes the value of every employee and encourages their active participation in the improvement process. It fosters a culture of respect, trust, and collaboration, where employees are empowered to contribute ideas and take ownership of their work.
PDCA Cycle: The Plan-Do-Check-Act (PDCA) cycle, also known as the Deming Cycle, is a fundamental tool used in Kaizen. It involves planning the improvement, implementing it on a small scale, checking the results, and acting on lessons learned to refine and standardize the improved process.
Gemba: Gemba, a Japanese term meaning "the actual place," refers to the principle of going to the source or the workplace to observe, gather data, and understand the current state. By directly engaging with the work environment, Kaizen practitioners gain firsthand insights, identify opportunities for improvement, and involve employees in problem-solving.
Standardization: Kaizen emphasizes the importance of establishing standardized work procedures and processes. Standardization provides a baseline for improvement, ensures consistency, and enables organizations to measure progress accurately.
Teamwork and Collaboration: Kaizen encourages cross-functional collaboration and teamwork. It recognizes that diverse perspectives and collective efforts lead to more effective problem-solving and sustainable improvements.
Kaizen Events: Kaizen events, also known as Kaizen blitz or Kaizen workshops, are structured improvement activities that bring together a cross-functional team for a focused period to address specific problems or opportunities. These events provide an intensive and collaborative environment for identifying and implementing improvements.
Kaizen can be applied at various levels within an organization, from small-scale improvements in individual processes to larger-scale initiatives that transform the entire organization's culture. It is a long-term approach that requires commitment, patience, and a mindset of continuous learning and improvement.
By embracing the principles of Kaizen, organizations can create a culture of continuous improvement, empower their employees, enhance operational efficiency, reduce waste, improve quality, and ultimately achieve sustainable success.
Six Sigma
Six Sigma is a data-driven methodology and quality management approach that aims to improve process performance, reduce defects, and enhance overall business outcomes. It was originally developed by Motorola in the 1980s and has since been widely adopted by organizations across various industries.
The core principles and components of Six Sigma include:
Focus on Customer Requirements: Six Sigma places a strong emphasis on understanding and meeting customer needs and expectations. The methodology aims to identify critical-to-quality (CTQ) characteristics that are most important to customers and align process improvements accordingly.
Data-Driven Decision Making: Six Sigma relies on the collection, analysis, and interpretation of data to drive decision-making. It utilizes statistical tools and techniques to measure process performance, identify root causes of defects or variations, and make informed improvements.
DMAIC Methodology: DMAIC stands for Define, Measure, Analyze, Improve, and Control, which is a structured problem-solving approach widely used in Six Sigma projects. Each phase has specific goals and activities:
- Define: Clearly define the problem, project goals, and customer requirements.
- Measure: Identify and collect relevant data to measure current process performance.
- Analyze: Analyze the data to identify root causes of defects or process variations.
- Improve: Develop and implement solutions to address the identified root causes and improve process performance.
- Control: Establish controls and monitoring mechanisms to sustain the improvements and prevent regression.
Roles and Certifications: Six Sigma projects typically involve a well-defined hierarchy of roles and certifications, including champions, project sponsors, Black Belts, Green Belts, and Yellow Belts. Each role has specific responsibilities in driving and supporting the Six Sigma initiatives within the organization.
Statistical Tools: Six Sigma employs a wide range of statistical tools and techniques to analyze and interpret data. These tools include process mapping, control charts, hypothesis testing, regression analysis, design of experiments (DOE), and many others. The selection and application of statistical tools depend on the nature of the problem and the data available.
Performance Metrics: Six Sigma uses performance metrics, such as defects per million opportunities (DPMO), process capability, and sigma levels, to assess process performance and measure improvement. These metrics provide a standardized way to quantify and compare the effectiveness of process improvements.
The ultimate goal of Six Sigma is to achieve a state of near-perfect process performance, where the defect rate is significantly reduced, and processes operate within tight tolerances. By reducing process variations and defects, organizations can improve customer satisfaction, reduce costs, enhance productivity, and drive overall business success.
It's important to note that Six Sigma is a rigorous and systematic approach that requires dedicated training, expertise, and organizational commitment to implementation. Organizations often have dedicated Six Sigma teams or specialists who lead improvement projects and facilitate the adoption of Six Sigma principles throughout the organization.
Lean Manufacturing
Lean manufacturing, often referred to as just "Lean," is a systematic approach to process improvement and waste reduction that originated from the Toyota Production System (TPS). It focuses on maximizing value for customers while minimizing waste, thereby improving overall operational efficiency and productivity. Lean principles and practices have been widely adopted across various industries worldwide.
The key principles and components of Lean manufacturing include:
Value: Lean starts by understanding the value from the customer's perspective. It involves identifying the specific products, features, or services that customers are willing to pay for. This helps eliminate activities that do not add value and focus resources on the critical aspects that meet customer needs.
Value Stream Mapping: Value stream mapping is a visual tool used to analyze and document the flow of materials, information, and activities involved in delivering a product or service. It helps identify and eliminate non-value-added activities (waste) and streamline the overall process flow.
Waste Reduction: Lean aims to minimize or eliminate various forms of waste, known as "Muda." The seven common types of waste identified in Lean are:
- Transportation: Unnecessary movement or transportation of materials or goods.
- Inventory: Excess inventory that ties up resources and increases costs.
- Motion: Unnecessary movement of people or equipment during production.
- Waiting: Idle time and delays in the process.
- Overproduction: Producing more than what is required by the customer.
- Overprocessing: Performing unnecessary or excessive steps in the process.
- Defects: Rework, scrap, or defects that require additional effort and resources to correct.
Just-in-Time (JIT): JIT is a Lean concept that aims to produce and deliver products or services at the exact time and quantity required by the customer, minimizing inventory and associated costs. It involves synchronizing production with demand, reducing lead times, and establishing a smooth flow of materials.
Continuous Flow: Lean promotes the concept of a continuous flow of work, where products or services move seamlessly through the production process without interruption or delays. This eliminates waiting time, reduces batch sizes, and improves overall productivity and efficiency.
Pull Systems: Lean uses pull systems to regulate products based on customer demand. Instead of pushing products through the production process based on forecasts, a pull system responds to actual customer demand, minimizing overproduction and excess inventory.
Continuous Improvement (Kaizen): Lean emphasizes a culture of continuous improvement, encouraging employees at all levels to identify and implement small, incremental improvements in their work processes. Kaizen events and daily improvement practices are used to engage employees and sustain a mindset of ongoing improvement.
Respect for People: Lean recognizes the value of every employee and emphasizes creating a supportive and respectful work environment. It encourages employee engagement, involvement in problem-solving, and the empowerment of workers to contribute to process improvement.
By adopting Lean manufacturing principles and practices, organizations can achieve higher levels of efficiency, reduce costs, improve quality, shorten lead times, enhance customer satisfaction, and create a culture of continuous improvement. Lean principles can be applied not only in manufacturing but also in service industries, healthcare, and other operational contexts.
Strategy to Achieve Operational Excellence through Integrated Order Management
Achieving operational excellence is a continuous journey that requires a strategic approach and ongoing commitment from an organization. Here are several key steps and strategies to help achieve operational excellence:
Define Clear Objectives: Start by clearly defining the objectives and outcomes you want to achieve through operational excellence. These objectives should align with your overall business strategy and focus on areas such as efficiency, quality, customer satisfaction, cost reduction, and innovation.
Develop a Comprehensive Strategy: Create a comprehensive strategy that outlines how you will achieve operational excellence. This strategy should include specific initiatives, action plans, and performance metrics that will drive improvement across different areas of your organization.
Embrace a Continuous Improvement Culture: Foster a culture of continuous improvement within your organization. Encourage all employees to actively participate in identifying process inefficiencies, suggesting improvements, and implementing changes. Emphasize the importance of learning from mistakes and using feedback to drive ongoing improvement.
Implement Lean Principles: Adopt Lean principles, such as value stream mapping, waste reduction, just-in-time production, and continuous flow, to streamline processes, eliminate waste, and improve overall efficiency. Use Lean tools and techniques, such as 5S, Kaizen events, and visual management, to facilitate improvement efforts.
Implement Six Sigma Methodology: Incorporate Six Sigma methodology to reduce process variations, defects, and errors. Use statistical tools and data-driven approaches to identify root causes of problems, improve process capability, and enhance overall quality and performance.
Foster Collaboration and Cross-Functional Teams: Break down silos and encourage collaboration among different departments and teams. Establish cross-functional teams to work on specific improvement projects, leveraging diverse perspectives and expertise to drive innovation and problem-solving.
Invest in Technology and Automation: Identify opportunities to leverage technology and automation to streamline processes, reduce manual errors, and improve productivity. Implement digital solutions, such as enterprise resource planning (ERP) systems, robotic process automation (RPA), and data analytics tools, to enhance data visibility, decision-making, and operational efficiency.
Focus on Employee Engagement and Development: Invest in employee training and development programs to enhance skills, knowledge, and capabilities. Empower employees to take ownership of their work, provide them with the necessary resources and tools to succeed, and recognize and reward their contributions to operational excellence.
Measure and Monitor Performance: Establish key performance indicators (KPIs) that align with your operational excellence objectives and regularly track and monitor progress. Use data-driven insights to identify trends, opportunities, and areas for improvement. Implement performance dashboards or scorecards to provide real-time visibility into performance and foster accountability.
Engage Leadership and Stakeholder Support: Ensure that leadership is actively involved and supportive of operational excellence initiatives. Leaders should set a clear vision, communicate expectations, provide resources, and lead by example. Engage stakeholders across the organization to gain their support, input, and feedback throughout the journey.
Continuously Learn and Adapt: Embrace a mindset of continuous learning and adaptation. Encourage experimentation, learn from failures, and use insights gained to refine strategies and approaches. Stay informed about emerging trends, best practices, and industry benchmarks to continuously challenge the status quo and drive improvement.
Remember that achieving operational excellence is an ongoing process that requires sustained effort, collaboration, and a commitment to continuous improvement. It requires a holistic approach that combines people, processes, technology, and a culture of excellence. By implementing these strategies and embracing a mindset of continuous improvement, organizations can enhance their operational performance, achieve better outcomes, and stay ahead in a competitive business environment.
Right Process to Follow to Set Operational Excellence
Setting operational excellence goals requires careful planning and consideration of organizational objectives and priorities. Here are the steps to set operational excellence goals:
Understand Organizational Objectives: Begin by understanding the overall strategic objectives of the organization. These may include improving profitability, increasing market share, enhancing customer satisfaction, reducing costs, or achieving regulatory compliance. Align the operational excellence goals with these broader organizational goals to ensure coherence and relevance.
Identify Key Performance Areas: Identify the key areas of your operations that have a significant impact on achieving the organizational objectives. These areas can vary depending on your industry and business model. Examples may include product quality, process efficiency, supply chain management, customer service, employee productivity, or safety and compliance.
Analyze Current Performance: Evaluate your current performance in each key area. Use key performance indicators (KPIs) and relevant metrics to assess performance levels, identify gaps, and understand areas for improvement. This analysis will help prioritize the operational excellence goals and focus on areas that require the most attention.
Set Specific and Measurable Goals: Ensure that your operational excellence goals are specific, measurable, achievable, relevant, and time-bound (SMART). Avoid setting vague or generic goals. Instead, make them concrete and quantifiable. For example, rather than stating a goal to "improve customer service," set a specific target, such as "reduce average customer response time by 20% within six months."
Involve Stakeholders: Engage key stakeholders, including employees, managers, and subject matter experts, in the goal-setting process. Seek their input and perspective to ensure that the goals are realistic, aligned with their needs, and feasible given available resources. Involving stakeholders also fosters ownership, commitment, and collaboration in achieving operational excellence goals.
Prioritize Goals: Assess the urgency and impact of each operational excellence goal and prioritize them accordingly. Consider the resources, time, and effort required to achieve each goal. It may be necessary to sequence the goals and tackle them in a phased approach based on their importance and interdependencies.
Break Down Goals into Actionable Steps: Once the operational excellence goals are defined, break them down into actionable steps or initiatives. Create a roadmap or action plan outlining the specific tasks, responsibilities, timelines, and milestones for each initiative. Assign accountability for each task to ensure progress and implementation.
Establish Monitoring and Measurement Mechanisms: Define the metrics and measurement systems to track progress toward the operational excellence goals. Establish regular monitoring and reporting processes to assess performance, identify deviations, and take corrective actions as needed. Use data and analytics to provide insights into performance trends, identify areas for improvement, and drive decision-making.
Communicate and Engage: Clearly communicate the operational excellence goals, initiatives, and progress to all relevant stakeholders. Promote transparency, provide updates, and celebrate achievements to maintain engagement and momentum. Furthermore, engage employees through effective communication channels, training programs, and recognition to ensure their commitment and involvement in achieving the goals.
Continuously Review and Adjust: Regularly review the progress of the operational excellence goals and adjust the strategies or initiatives as needed. Analyze the results, learn from successes and failures, and refine the goals based on feedback and changing business conditions. Continuous improvement and flexibility are essential to adapt and drive ongoing operational excellence.
By following these steps, organizations can effectively set operational excellence goals that are aligned with their strategic objectives, measurable, and capable of driving continuous improvement in their operations.
Important Benefits of Operational Excellence
Operational excellence offers several core benefits to organizations, encompassing various aspects of their operations and overall performance. Let's delve into the key benefits in detail:
Cost Reduction and Efficiency: Operational excellence focuses on eliminating waste, streamlining processes, and optimizing resource utilization. By identifying and eliminating non-value-added activities, organizations can reduce costs, enhance productivity, and improve operational efficiency. This leads to higher profitability and a competitive advantage in the market.
Improved Quality and Customer Satisfaction: Operational excellence emphasizes quality management and continuous improvement. By implementing robust quality control measures, organizations can reduce defects, errors, and customer complaints. Consistently delivering high-quality products or services enhances customer satisfaction, fosters loyalty, and generates positive word-of-mouth, leading to business growth.
Enhanced Operational Performance: Operational excellence drives improvements in key operational metrics such as cycle time, lead time, and throughput. By identifying and addressing bottlenecks, process inefficiencies, and constraints, organizations can achieve smoother operations, faster delivery, and increased productivity. This enhances overall operational performance and the ability to meet customer demand effectively.
Agility and Adaptability: Operational excellence promotes a culture of continuous improvement and agility. Organizations that embrace operational excellence are more adaptable to changing market conditions, customer demands, and industry disruptions. They can quickly respond to challenges, seize opportunities, and make informed decisions based on data and insights. This flexibility allows organizations to stay ahead of the competition and drive innovation.
Risk Mitigation and Compliance: Operational excellence emphasizes risk management and compliance. By implementing standardized processes, robust controls, and monitoring mechanisms, organizations can identify and mitigate operational risks. This includes risks related to safety, security, regulatory compliance, and data integrity. By proactively managing risks, organizations safeguard their reputation, protect stakeholders, and ensure business continuity.
Employee Engagement and Empowerment: Operational excellence engages employees at all levels and empowers them to contribute to process improvements. Employees are encouraged to identify inefficiencies, suggest solutions, and take ownership of their work. This fosters a culture of engagement, collaboration, and continuous learning. Engaged employees are more motivated, productive, and committed to the organization's success.
Strategic Alignment and Focus: Operational excellence aligns organizational goals and activities with strategic objectives. It helps organizations prioritize initiatives that create value, aligning resources and efforts towards strategic outcomes. By focusing on the most critical areas and continuously monitoring performance, organizations ensure that their operations are aligned with their overall business strategy.
Innovation and Competitive Advantage: Operational excellence cultivates a culture of innovation and experimentation. Organizations that encourage continuous improvement and creative problem-solving are more likely to drive innovation and generate new ideas. This enables them to introduce new products, services, or business models that differentiate them from competitors and provide a competitive advantage in the market.
In conclusion, operational excellence delivers core benefits such as cost reduction, improved quality, enhanced operational performance, agility, risk mitigation, employee engagement, strategic alignment, and innovation. By embracing operational excellence, organizations can optimize their operations, enhance customer satisfaction, drive growth, and achieve sustainable success in a rapidly evolving business landscape.
Major Industries that Can Benefit from Operational Excellence
Operational excellence is a concept that can benefit organizations across various industries. While the specific implementation may vary based on industry-specific requirements, the fundamental principles and practices of operational excellence can be applied universally. Here are some industries that can benefit from operational excellence:
Manufacturing: Manufacturing industries, such as automotive, electronics, consumer goods, and pharmaceuticals, can significantly benefit from operational excellence. By optimizing production processes, reducing waste, improving quality control, and enhancing supply chain management, manufacturers can achieve cost savings, increased productivity, faster time-to-market, and improved customer satisfaction.
Healthcare: The healthcare industry can benefit from operational excellence to improve patient care, operational efficiency, and cost-effectiveness. By streamlining processes, reducing wait times, eliminating errors, and optimizing resource utilization, healthcare organizations can enhance patient outcomes, increase patient satisfaction, and improve financial performance.
Retail and E-commerce: Operational excellence is vital for the retail and e-commerce sectors, where customer satisfaction and efficient order fulfillment are crucial. By implementing efficient inventory management, optimizing distribution networks, improving supply chain coordination, and enhancing customer service, retailers can deliver a seamless shopping experience, reduce costs, and increase customer loyalty.
Financial Services: Banks, insurance companies, and other financial institutions can benefit from operational excellence to enhance operational efficiency, risk management, and customer experience. By optimizing processes such as loan approvals, account openings, claims processing, and fraud detection, financial organizations can improve customer satisfaction, reduce operational risks, and drive cost savings.
Logistics and Transportation: Operational excellence is critical for logistics and transportation companies to ensure smooth operations, timely deliveries, and efficient fleet management. By optimizing route planning, improving warehouse management operations, enhancing load optimization, and utilizing real-time data for decision-making, logistics companies can reduce costs, improve delivery times, and enhance overall service quality.
Hospitality and Tourism: The hospitality and tourism industry can benefit from operational excellence to enhance guest experiences, optimize service delivery, and improve operational efficiency. By implementing efficient booking systems, streamlining check-in/check-out processes, enhancing housekeeping operations, and providing personalized services, hospitality businesses can achieve higher guest satisfaction, increase repeat business, and maximize revenue.
Energy and Utilities: Operational excellence is crucial for the energy and utilities sector to improve asset performance, optimize energy generation and distribution, and ensure regulatory compliance. By implementing predictive maintenance strategies, optimizing energy usage, improving outage management, and enhancing customer service, energy, and utility companies can reduce costs, improve reliability, and meet sustainability goals.
Technology and Software: Operational excellence is relevant to the technology and software industry, where efficient development processes, product quality, and customer satisfaction are key. By implementing agile methodologies, continuous integration and delivery practices, quality assurance processes, and efficient customer support systems, technology companies can accelerate product development cycles, enhance product quality, and improve customer retention.
In summary, operational excellence can benefit organizations across industries by improving operational efficiency, reducing costs, enhancing customer satisfaction, and driving overall business performance. By embracing operational excellence principles and tailoring them to their specific industry, organizations can achieve sustainable success and a competitive edge in their respective markets.
Important Examples of Operational Excellence
Following, we’ve discussed some examples of operational excellence initiatives and practices implemented by organizations across different industries:
Toyota Production System (TPS): Toyota is widely recognized for its operational excellence practices through the implementation of the Toyota Production System. TPS focuses on eliminating waste, continuous improvement, and empowering employees. It includes concepts such as Just-in-Time production, Kanban systems, standardized work, and Kaizen (continuous improvement).
Lean Manufacturing at Nike: Nike has implemented Lean Manufacturing principles to improve its operational efficiency and reduce waste. They have streamlined their production processes, reduced lead times, and implemented pull systems to match production with customer demand. Nike's Lean initiatives have resulted in improved inventory management, reduced costs, and enhanced customer satisfaction.
Six Sigma at General Electric: General Electric (GE) has widely adopted the Six Sigma methodology to achieve operational excellence. Through Six Sigma projects, GE focuses on reducing defects and process variations, enhancing quality, and improving customer satisfaction. GE uses statistical tools and data-driven analysis to identify and address the root causes of problems and drive continuous improvement.
Amazon's Fulfillment Centers: Amazon has built its operational excellence by leveraging advanced technology, automation, and data-driven decision-making. Their fulfillment centers are highly optimized to ensure efficient order processing, fast delivery, and accurate inventory management. Amazon uses sophisticated algorithms, robotics, and real-time data analytics to optimize warehouse operations and enhance the customer experience.
Continuous Improvement at Toyota Motor Manufacturing: Toyota's manufacturing plants worldwide implement a culture of continuous improvement through employee involvement and problem-solving. They encourage employees to identify and address process inefficiencies and quality issues through daily improvement activities. Toyota's focus on continuous improvement has resulted in enhanced productivity, quality, and customer satisfaction.
Operational Excellence in Healthcare: Healthcare organizations strive for operational excellence to improve patient outcomes, reduce costs, and enhance efficiency. For example, the Virginia Mason Medical Center in Seattle implemented the Virginia Mason Production System (VMPS), which applies Lean principles to healthcare processes. VMPS has led to improved patient flow, reduced waiting times, and increased staff efficiency.
Operational Excellence in Airlines: Airlines, such as Southwest Airlines, have achieved operational excellence through efficient operations and customer-centric practices. Southwest Airlines focuses on quick turnaround times, streamlined processes, and a low-cost business model. Their operational excellence initiatives have resulted in high customer satisfaction, on-time performance, and cost-effective operations.
Operational Excellence in Banking: Banks often implement operational excellence initiatives to improve customer service, reduce processing time, and minimize errors. For instance, ING Bank in the Netherlands implemented Lean practices to streamline their mortgage approval process, resulting in faster processing times and improved customer experience.
These examples highlight how organizations across various industries have achieved operational excellence by adopting different methodologies, such as Lean, Six Sigma, and continuous improvement. The specific practices implemented may vary, but the underlying principles remain focused on eliminating waste, improving efficiency, enhancing quality, and delivering value to customers.
Operational Excellence: KPIs and Metrics?
Operational excellence key performance indicators (KPIs) and metrics are measurements used to assess and track the performance of various operational processes and activities within an organization. These indicators provide valuable insights into the effectiveness, efficiency, and quality of operations, helping organizations identify areas for improvement and measure progress toward operational excellence. Here are some common operational excellence KPIs and metrics:
Overall Equipment Effectiveness (OEE): OEE is a metric that measures the efficiency of equipment utilization. It combines three factors: availability (the percentage of time the equipment is available for production), performance (the actual production rate compared to the maximum potential rate), and quality (the percentage of defect-free output). OEE helps identify equipment downtime, performance losses, and quality issues.
Cycle Time: Cycle time measures the time required to complete a specific process or task. It helps assess process efficiency and identify bottlenecks or delays. By monitoring cycle time, organizations can identify opportunities for improvement, reduce lead times, and enhance overall operational efficiency.
First-Time Right (FTR) Rate: The FTR rate measures the percentage of products or services that meet customer requirements and quality standards on the first attempt, without the need for rework, revisions, or corrections. A higher FTR rate indicates better quality control, reduces waste, and improves customer satisfaction.
Customer Satisfaction Score (CSAT): CSAT measures customer satisfaction levels based on surveys or feedback. It captures the customer's perception of product quality, service delivery, responsiveness, and overall experience. Monitoring CSAT helps organizations identify areas of improvement, enhance customer loyalty, and build long-term relationships.
On-Time Delivery (OTD): OTD measures the percentage of products or services delivered to customers within the agreed-upon timeframe. It reflects the organization's ability to meet customer expectations, fulfill orders promptly, and manage logistics effectively. High OTD rates indicate reliable delivery performance and customer service.
Defect Rate: The defect rate measures the percentage of products or services that have quality defects or do not meet specified standards. It helps identify areas of quality improvement, production issues, or process inefficiencies. By reducing the defect rate, organizations can enhance product quality, customer satisfaction, and operational efficiency.
Employee Productivity: Employee productivity metrics assess the efficiency and effectiveness of employees in delivering outputs. These metrics can include units produced per hour, sales revenue per employee, or customer service tickets resolved per employee. Monitoring employee productivity helps optimize workforce utilization, identify training needs, and drive performance improvement.
Process Efficiency: Process efficiency metrics assess the effectiveness and efficiency of specific processes or workflows. Examples include the number of process steps, the time taken to complete a process, or the number of handoffs between departments. By tracking process efficiency, organizations can identify waste, streamline workflows, and optimize resource allocation.
Cost of Quality (CoQ): CoQ measures the total cost incurred due to quality-related issues, including prevention, appraisal, and failure costs. It helps identify the financial impact of poor quality, assess the effectiveness of quality management practices, and make informed decisions regarding process improvements and investments in quality initiatives.
Employee Engagement and Retention: Employee engagement and retention metrics assess the satisfaction, motivation, and commitment levels of employees within the organization. These metrics can include employee satisfaction surveys, turnover rates, or employee net promoter scores. Monitoring employee engagement and retention helps organizations understand the impact of their operational practices on employee morale and loyalty.
It's important for organizations to select operational excellence KPIs and metrics that align with their strategic objectives, industry-specific requirements, and desired outcomes. These indicators should be regularly monitored, analyzed, and used to drive continuous improvement and operational excellence throughout the organization.
Framework Operational Excellence
Following, we've discussed framework operational excellence. Let's learn:
DMAIC Framework
The DMAIC framework is a widely used and recognized methodology within the field of operational excellence. It stands for Define, Measure, Analyze, Improve, and Control, and provides a structured approach for problem-solving and process improvement. Let's explore each phase of the DMAIC framework in detail:
Define: In the Define phase, the focus is on clearly defining the problem or opportunity for improvement. This involves understanding the process or area that needs improvement, defining project goals, and identifying customer requirements and expectations. Key activities include creating a project charter, forming a cross-functional team, and defining project scope and objectives.
Measure: The Measure phase involves gathering data and measuring the current performance of the process or area under study. This includes identifying relevant process metrics, collecting data using appropriate measurement techniques, and establishing a baseline performance. The aim is to obtain a clear understanding of the process performance, including any variations or defects.
Analyze: In the Analyze phase, the collected data is analyzed to identify root causes and factors contributing to the problem or performance gaps. Various analysis tools and techniques, such as Pareto charts, cause-and-effect diagrams, and statistical analysis, are used to identify patterns, trends, and potential sources of variation. The goal is to gain insights into the underlying causes and drivers of the problem.
Improve: The Improve phase focuses on developing and implementing solutions to address the identified root causes and improve the process performance. This involves brainstorming and evaluating potential solutions, designing and testing improvement strategies, and implementing the selected solutions. Iterative testing and piloting may be conducted to validate the effectiveness of the improvements before full-scale implementation.
Control: The Control phase aims to sustain the improvements achieved and prevent the recurrence of the problem. It involves implementing control measures, developing standard operating procedures (SOPs), establishing monitoring systems, and defining key control metrics. Additionally, the phase includes developing a plan for ongoing measurement and monitoring to ensure the sustained success of the improvements.
Throughout the DMAIC framework, cross-functional collaboration, data-driven decision-making, and a structured problem-solving approach are emphasized. The framework follows a logical progression, ensuring that the root causes are identified, effective solutions are implemented, and the improvements are sustained over time.
The DMAIC framework is commonly associated with the Six Sigma methodology, which aims to reduce process variation and defects to achieve operational excellence. However, the DMAIC framework can be applied in various operational improvement initiatives, regardless of whether they are specifically labeled as Six Sigma projects.
By following the DMAIC framework, organizations can systematically identify and address process inefficiencies, reduce defects, improve customer satisfaction, and drive continuous improvement in their operations.
Step-by-Step Implementation Plan for Operational Excellence
Implementing operational excellence requires careful planning and execution to ensure successful adoption and sustainable results. Here is a step-by-step implementation plan:
Establish a Clear Vision: Clearly define your vision for operational excellence and communicate it throughout the organization. Ensure that all stakeholders understand the purpose, benefits, and expected outcomes of the initiative. Align the vision with the organization's strategic objectives to ensure coherence and support.
Create a Cross-Functional Team: Form a dedicated team with representatives from different departments and levels within the organization. This team will be responsible for driving the operational excellence initiative, coordinating activities, and facilitating communication across the organization. Ensure the team has the necessary skills and authority to implement changes effectively.
Assess Current State: Conduct a thorough assessment of your organization's current operations, processes, and performance. Identify strengths, weaknesses, and areas for improvement. This assessment can include process mapping, value stream analysis, performance metrics review, and feedback from employees and customers. Use this information to prioritize improvement opportunities.
Set Specific Goals and Metrics: Based on the assessment, set specific, measurable, achievable, relevant, and time-bound (SMART) goals for operational excellence. Define key performance indicators (KPIs) and metrics that align with your goals. These goals and metrics should be focused on areas such as quality, efficiency, customer satisfaction, cost reduction, and employee engagement.
Develop an Improvement Plan: Create a detailed plan outlining the actions required to achieve the operational excellence goals. Break down the plan into specific projects, initiatives, and tasks. Assign responsibilities, set timelines, and allocate resources accordingly. Prioritize the initiatives based on their impact and feasibility, and ensure they align with the overall vision.
Implement Continuous Improvement Practices: Embed a culture of continuous improvement within the organization. Encourage employees at all levels to identify and contribute ideas for improvement. Implement practices such as Kaizen events, suggestion systems, and process review sessions to promote a proactive and collaborative approach to problem-solving. Foster a learning environment that embraces experimentation, learning from failures, and sharing of best practices.
Provide Training and Support: Invest in training programs to enhance the skills and capabilities of employees at all levels. Provide training on lean principles, problem-solving methodologies, quality management techniques, and other relevant areas. Offer coaching and support to help employees embrace new practices and adopt a continuous improvement mindset. Develop a system for recognizing and rewarding employees' contributions to operational excellence.
Communicate and Engage: Regularly communicate the progress and achievements of the operational excellence initiative to all stakeholders. Share success stories, provide updates on key metrics, and celebrate milestones. Maintain open channels of communication to address concerns, provide feedback, and gather suggestions from employees. Engage employees by involving them in improvement projects, empowering them to make decisions, and recognizing their contributions.
Monitor and Measure Progress: Establish a system to monitor and measure the progress of your operational excellence initiative. Continuously track key metrics, review performance against goals, and analyze trends and patterns. Use this data to identify areas of success, areas that require additional attention, and potential adjustments to the improvement plan. Regularly report on progress to senior leadership and the broader organization.
Sustain and Evolve: Operational excellence is an ongoing journey, not a one-time project. Continuously review, refine, and evolve your practices to ensure sustainability. Foster a culture that embraces change and adapts to new challenges and opportunities. Regularly assess the effectiveness of your initiatives, learn from experiences, and update your improvement plan to keep pace with evolving business needs and industry trends.
By following this implementation plan, organizations can lay a strong foundation for operational excellence and drive continuous improvement across their operations. The plan ensures alignment with organizational objectives, engagement of employees, and a systematic approach to achieving and sustaining excellence in performance.
Best and Important Practices for Operational Excellence
To achieve operational excellence, organizations can implement several best practices that have proven effective in driving improvement and sustainable success. Here are some key operational excellence best practices:
Define Clear Goals and Objectives: Establish clear and measurable goals aligned with the organization's strategic objectives. Ensure that these goals are communicated throughout the organization and that employees understand their roles in achieving them. Clear goals provide a sense of direction and focus for improvement efforts.
Foster a Culture of Continuous Improvement: Create a culture that values and encourages continuous improvement. Empower employees at all levels to identify and implement process enhancements. Promote a mindset of learning, experimentation, and innovation. Provide the necessary training and resources to support employees in their improvement efforts.
Standardize Processes: Document and standardize key processes to ensure consistency and efficiency. Clearly define process steps, roles, responsibilities, and performance expectations. Standardization reduces variability, eliminates waste, and enables easier replication of best practices across the organization.
Implement Lean Principles: Adopt lean principles, such as waste reduction, value stream mapping, and continuous flow. Identify and eliminate non-value-added activities and bottlenecks in processes. Streamline workflows to minimize wait times, excess inventory, and unnecessary movement. Lean principles focus on maximizing customer value while minimizing waste and lead time.
Engage and Empower Employees: Engage employees by involving them in improvement initiatives and decision-making processes. Encourage ownership and accountability for results. Provide opportunities for training and skill development. Recognize and reward employees for their contributions to operational excellence. Engaged employees are more motivated, productive, and committed to driving improvements.
Use Data-Driven Decision Making: Collect and analyze relevant data to make informed decisions. Use key performance indicators (KPIs) to measure process performance and identify areas for improvement. Implement data management systems and tools to capture, store, and analyze data effectively. Data-driven decision-making reduces guesswork and enables targeted improvements.
Implement Effective Change Management: Successful operational excellence initiatives require effective change management practices. Proactively communicate the need for change, the benefits, and the expected outcomes. Involve employees in the change process and address their concerns. Provide training and support to help employees adapt to new processes and ways of working.
Foster Collaboration and Cross-Functional Teams: Break down silos and foster collaboration across departments and functions. Establish cross-functional teams to tackle complex improvement projects. Encourage knowledge sharing, teamwork, and information exchange. Collaboration facilitates a holistic view of processes and enables more effective problem-solving.
Focus on Customer Value: Place the customer at the center of operational excellence efforts. Understand customer needs and expectations. Continuously seek feedback to identify areas for improvement. Design processes and deliver products and services that provide value to customers. Customer-centricity drives customer satisfaction, loyalty, and business growth.
Continuously Monitor and Improve: Establish a system for monitoring and measuring key metrics and performance indicators. Regularly review progress against goals and make data-driven adjustments. Conduct periodic process audits and reviews to identify opportunities for further improvement. Operational excellence is an ongoing journey that requires a commitment to continuous monitoring and refinement.
By implementing these best practices, organizations can create a culture of excellence, drive efficiency and effectiveness, and achieve sustained operational improvements. It is important to adapt these practices to the specific needs and context of the organization, continuously learn from experiences, and evolve the approach over time.
Overcoming and Addressing Operational Excellence Challenges
While pursuing operational excellence, organizations may encounter various challenges that can impede progress. However, with proper strategies and approaches, these challenges can be overcome. Here are some common operational excellence challenges and ways to address them:
Resistance to Change: Resistance to change is a common challenge when implementing operational excellence initiatives. Employees may be reluctant to embrace new processes or ways of working.
Moreover, to overcome this challenge, it is important to foster open communication and create a culture that values and supports change. Involve employees early in the process, address their concerns, provide training and support, and demonstrate the benefits of the changes. Encourage and reward employees for their contributions to change and highlight success stories to inspire others.
Lack of Leadership Support: Operational excellence initiatives require strong leadership support to be successful. Lack of commitment or involvement from leaders can hinder progress. To address this challenge, it is crucial to engage senior leadership early on and gain their buy-in.
Clearly communicate the strategic importance of operational excellence and its alignment with organizational goals. Provide leaders with the necessary resources and training to lead and support the initiative effectively. Regularly update leaders on progress and involve them in decision-making processes.
Siloed Thinking and Lack of Collaboration: Siloed thinking and lack of collaboration between departments or functions can hinder operational excellence efforts. To overcome this challenge, foster a culture of collaboration and break down silos. Encourage cross-functional teams and communication. Promote knowledge sharing and create platforms for employees to collaborate and share best practices. Emphasize the importance of working together to achieve common goals.
Inadequate Resources and Skills: Insufficient resources, both financial and human, can pose a challenge to operational excellence implementation. A lack of necessary skills and expertise can also hinder progress. To address this challenge, conduct a thorough resource assessment and ensure adequate allocation of resources for the initiative.
Furthermore, invest in training and development programs to enhance employees' skills and capabilities. Consider partnering with external experts or consultants to fill skill gaps and provide guidance.
Lack of Metrics and Performance Tracking: Without proper metrics and performance tracking systems, it becomes difficult to measure progress and identify areas for improvement. To overcome this challenge, establish key performance indicators (KPIs) and develop robust performance tracking mechanisms.
Furthermore, implement data management systems and tools to capture and analyze relevant data. Regularly review performance against targets and use the data to drive decision-making and improvement efforts.
Sustaining Continuous Improvement: Sustaining the momentum of continuous improvement can be a challenge over time. After initial successes, organizations may face complacency or a lack of focus on ongoing improvement.
To address this challenge, establish a culture of continuous learning and improvement. Encourage employees to seek out opportunities for improvement and provide channels for submitting ideas. Celebrate achievements and recognize employees' contributions to sustaining operational excellence. Regularly communicate the importance of continuous improvement and reinforce its value throughout the organization.
Lack of Clear Communication: Communication challenges can arise when implementing operational excellence initiatives. It is essential to effectively communicate the goals, progress, and expected outcomes of the initiative.
To address this challenge, develop a comprehensive communication plan that includes regular updates, town hall meetings, newsletters, and other channels of communication. Furthermore, ensure that the messaging is clear, consistent, and targeted to various stakeholder groups. Encourage two-way communication and provide opportunities for feedback and input.
By addressing these challenges proactively and implementing appropriate strategies, organizations can overcome obstacles on the path to operational excellence. It is important to recognize that challenges may vary depending on the organization's context, and a tailored approach is necessary to navigate them successfully.
Frequently Asked Questions (FAQs) Associated with Operational Excellence through an Integrated Order Management
Following, we’ve discussed important operational excellence through integrated order management. Let’s learn:
Que 1: What is the role of technology in an integrated order management strategy?
Technology plays a crucial role in an integrated order management strategy, enabling organizations to streamline and automate their order management processes. Here are key ways technology supports an integrated order management strategy:
Order Processing Automation: Technology automates order processing tasks, reducing manual effort and minimizing errors. Orders received through various channels (e.g., online platforms, mobile apps, call centers) can be automatically captured, validated, and entered into the system. This automation improves order accuracy, speeds up processing times, and eliminates the need for manual data entry.
Inventory Management and Real-time Visibility: Technology enables real-time visibility into inventory levels and availability. Integrated order management systems can be connected to inventory management systems, providing up-to-date information on stock levels. This ensures accurate inventory allocation and prevents overselling or stockouts. With real-time visibility, organizations can efficiently manage inventory across multiple locations and make informed decisions on replenishment and fulfillment.
Order Tracking and Shipment Visibility: Technology allows customers to track their orders and provides them with real-time updates on the status and location of their shipments. Order management systems integrated with logistics partners enable automated tracking and delivery notifications. This enhances customer satisfaction, reduces inquiries, and improves the overall transparency of the order fulfillment process.
Customer Relationship Management (CRM) Integration: Integrating order management with CRM systems provides a comprehensive view of customer information and order history. This integration enables personalized customer service, as representatives have access to order details, preferences, and previous interactions. It allows for efficient handling of inquiries, order modifications, and returns/exchanges, leading to improved customer satisfaction and loyalty.
Reporting and Analytics: Technology facilitates the collection and analysis of order management data, supporting data-driven decision-making and performance measurement. Advanced reporting and analytics tools provide insights into order volume, fulfillment cycle times, customer behavior, and other key metrics. These insights help identify bottlenecks, areas for improvement, and trends, enabling organizations to optimize their order management processes and drive operational excellence.
Integration with Supply Chain Partners: Technology enables seamless integration with external partners, such as suppliers, manufacturers, and logistics providers. Integration with suppliers allows for automated order placement and procurement, improving supply chain efficiency. Integration with logistics providers enables streamlined shipping, label generation, and tracking, enhancing the end-to-end order fulfillment process.
Scalability and Adaptability: Technology provides the scalability and adaptability needed to support growing order volumes and changing business requirements. Cloud-based order management systems offer flexibility, allowing organizations to scale their operations and accommodate fluctuations in demand. They can easily add new sales channels, integrate with new systems, and expand their order management capabilities as the business evolves.
Workflow Automation and Alerts: Technology enables workflow automation by defining rules and triggers for order management processes. It automates tasks such as order validation, invoicing, and notifications, reducing manual intervention and ensuring consistent execution. Alerts and notifications can be set up to notify stakeholders about specific events or exceptions, enabling timely action and resolution.
In summary, technology is a key enabler of an integrated order management strategy. It automates processes, provides real-time visibility, enhances customer experience, supports data-driven decision-making, facilitates integration with supply chain partners, and offers scalability and adaptability. By leveraging technology effectively, organizations can achieve operational excellence, improve efficiency, and deliver a superior order management experience to their customers.
Que 2: How can an integrated order management strategy improve customer satisfaction?
An integrated order management strategy can significantly improve customer satisfaction by streamlining and enhancing the entire order fulfillment process. Here are several ways an integrated order management strategy can achieve this:
Order Accuracy and Timeliness: An integrated order management system ensures accurate and timely order processing. It eliminates manual errors by automating order capture, validation, and entry. This reduces the chances of incorrect orders or delays in processing. Customers receive the right products and services promptly, leading to increased satisfaction and trust in the organization.
Real-time Order Tracking: With an integrated order management strategy, customers gain real-time visibility into the status of their orders. They can track their orders online, view estimated delivery dates, and receive proactive updates on any changes or delays. This transparency empowers customers, reduces anxiety, and enhances their overall experience.
Seamless Multi-channel Experience: An integrated order management system allows customers to place orders through multiple channels, such as online platforms, mobile apps, or in-person interactions. Regardless of the channel used, the order management system ensures a consistent experience by capturing and processing orders uniformly. Customers can switch between channels seamlessly, modify orders, or access order history, contributing to convenience and satisfaction.
Personalized Customer Service: Integration with customer relationship management (CRM) systems enables personalized customer service. Representatives have access to order details, preferences, and previous interactions, allowing them to provide tailored support. When customers contact customer service for inquiries or issues, representatives can quickly retrieve order information, resolve concerns efficiently, and offer personalized assistance, leaving customers satisfied with the level of support received.
Efficient Returns and Exchanges: An integrated order management strategy streamlines the returns and exchanges process. Customers can initiate returns or exchanges online or through customer service channels. The system facilitates seamless handling of these requests, generating return labels, managing inventory updates, and processing refunds or replacements promptly. The ease and efficiency of the returns process contribute to customer satisfaction and loyalty.
Consistent Communication: An integrated order management system enables consistent and proactive communication with customers throughout the order fulfillment journey.
Furthermore, automated order confirmation emails, status updates, and shipping notifications keep customers informed about their orders. This reduces uncertainty, manages expectations, and demonstrates the organization's commitment to excellent customer service.
Order History and Preferences: Integrated order management systems maintain a comprehensive order history for each customer. This allows customers to access their past orders, review purchase details, and make informed decisions. By understanding customer preferences and order history, organizations can provide personalized recommendations, promotions, or special offers, further enhancing the customer experience.
Continuous Improvement: An integrated order management strategy enables organizations to continuously improve their processes based on customer feedback and data analysis. By monitoring key performance indicators (KPIs) related to order fulfillment, organizations can identify areas for enhancement, such as reducing order processing times, improving packaging, or enhancing delivery options. This commitment to continuous improvement demonstrates responsiveness to customer needs and fosters long-term satisfaction.
In conclusion, an integrated order management strategy plays a vital role in improving customer satisfaction. It ensures order accuracy, provides real-time tracking, offers a seamless multi-channel experience, enables personalized customer service, streamlines return and exchanges, maintains consistent communication, facilitates access to order history, and drives continuous improvement. By focusing on customer-centric order management processes, organizations can exceed customer expectations, build loyalty, and differentiate themselves in the marketplace.
Que 3: How does data analytics contribute to operational excellence in order management?
Data analytics plays a critical role in driving operational excellence in order management. By leveraging data analytics, organizations can gain valuable insights into their order management processes, identify areas for improvement, make data-driven decisions, and optimize overall operational performance. Here are several ways data analytics contributes to operational excellence in order management:
Performance Measurement and Monitoring: Data analytics allows organizations to measure and monitor key performance indicators (KPIs) related to order management. By tracking metrics such as order processing time, order accuracy, on-time delivery, and customer satisfaction, organizations can assess their performance and identify areas that require attention. Regular monitoring of KPIs provides visibility into operational performance, helps identify bottlenecks or inefficiencies, and enables organizations to take proactive measures for improvement.
Root Cause Analysis: Data analytics helps uncover the root causes of operational challenges or issues in order management. By analyzing data related to order processing, fulfillment, and customer feedback, organizations can identify patterns, trends, and potential causes of delays, errors, or customer dissatisfaction. This insight allows organizations to address underlying issues, implement corrective actions, and prevent similar problems from occurring in the future.
Demand Forecasting and Planning: Data analytics enables organizations to forecast and plan demand accurately. By analyzing historical order data, customer behavior, market trends, and external factors, organizations can predict future demand patterns. This helps in optimizing inventory levels, ensuring sufficient stock availability, and minimizing stockouts or overstock situations. Accurate demand forecasting allows organizations to align their supply chain processes, reduce lead times, and enhance operational efficiency.
Process Optimization and Automation: Data analytics provides insights into process inefficiencies and areas of improvement in order management. By analyzing order data, organizations can identify process bottlenecks, repetitive manual tasks, and potential automation opportunities.
Furthermore, this helps streamline processes, eliminate manual errors, reduce processing times, and improve overall efficiency. Data analytics enables organizations to make informed decisions about process optimization initiatives, invest in automation technologies, and drive continuous improvement.
Customer Insights and Personalization: Data analytics helps organizations understand customer behavior, preferences, and buying patterns. By analyzing customer data, order history, and interactions, organizations can gain insights into customer segments, their needs, and preferences.
Furthermore, this knowledge allows organizations to personalize the order management process, and offer tailored recommendations, promotions, or targeted marketing campaigns. By providing a personalized experience, organizations can enhance customer satisfaction, and loyalty, and drive repeat business.
Supplier Performance Evaluation: Data analytics enables organizations to evaluate the performance of suppliers and external partners involved in order management. By analyzing data related to supplier lead times, order fulfillment accuracy, and quality, organizations can assess supplier performance objectively. This insight helps in supplier selection, contract negotiations, and ongoing supplier management. Data analytics enables organizations to identify underperforming suppliers, initiate corrective actions, and improve overall supply chain collaboration.
Continuous Improvement Initiatives: Data analytics provides a foundation for continuous improvement initiatives in order management. By analyzing historical data, organizations can identify trends, patterns, and anomalies that can be used to drive process enhancements and operational efficiencies. Data-driven insights allow organizations to set improvement goals, track progress, and implement data-backed strategies to achieve operational excellence.
In summary, data analytics plays a crucial role in achieving operational excellence in order management. It provides insights into performance metrics, enables root cause analysis, supports demand forecasting and planning, drives process optimization and automation, facilitates customer insights and personalization, aids in supplier performance evaluation, and fuels continuous improvement initiatives. By leveraging data analytics effectively, organizations can optimize their order management processes, enhance operational efficiency, and deliver superior customer experiences.
Wrapping Up
In conclusion, achieving operational excellence through an integrated order management strategy is a key driver for organizational success. By implementing effective order management practices, businesses can enhance operational efficiency, improve customer satisfaction, and gain a competitive edge in the marketplace. Throughout this article, we explored the various aspects of operational excellence and its link to order management.
We discussed the definition and scope of order management, highlighting its significance in ensuring smooth and efficient order fulfillment. We identified the key components of an effective order management system, including order capture, processing, fulfillment, and post-order activities. We also emphasized the crucial link between order management and operational excellence, as seamless and well-executed order processes directly contribute to overall operational performance.
Furthermore, we explored different methodologies and frameworks that organizations can adopt to achieve operational excellence in order management. These include the Shingo Model, OKAPI Method, DMAIC Framework, Kaizen, Six Sigma, Lean Manufacturing, and Flawless Execution (FLEX). Each approach brings its unique set of principles, tools, and practices to optimize order management processes and drive continuous improvement.
We also discussed the significance of setting operational excellence goals, identifying key performance indicators (KPIs), and implementing an operational excellence implementation plan. These elements provide a structured approach to aligning organizational objectives, measuring performance, and implementing strategies to achieve operational excellence.
Moreover, we highlighted the role of technology in an integrated order management strategy, emphasizing how automation, data analytics, and advanced software systems can enhance operational efficiency, accuracy, and customer satisfaction. We explored how technology enables real-time monitoring, data-driven decision-making, process optimization, and improved communication throughout the order management lifecycle.
Additionally, we discussed the importance of customer satisfaction in the context of integrated order management. We explored how an integrated order management strategy can improve customer satisfaction through order accuracy, real-time tracking, seamless multi-channel experiences, personalized customer service, efficient returns and exchanges, consistent communication, access to order history, and continuous improvement initiatives.
Lastly, we recognized the challenges organizations may face in achieving operational excellence and provided insights into overcoming these challenges. By addressing issues such as process disconnection, lack of progress, inability to change, complex data, and the absence of a coherent management plan, organizations can proactively navigate obstacles and drive operational excellence in order management.
In conclusion, achieving operational excellence through an integrated order management strategy requires a holistic approach that encompasses people, processes, technology, and a customer-centric mindset.
By adopting best practices, leveraging data analytics, and continuously improving order management processes, organizations can optimize efficiency, enhance customer satisfaction, and position themselves for long-term success in a competitive marketplace.
Operational excellence in order management is a journey of continuous improvement, and organizations that embrace it are poised to thrive in today's dynamic business landscape.
How Deskera Can Assist You?
Deskera ERP and MRP systems help you to keep your business units organized. The system's key features of demand forecasting with Deskera include as follows:
- Establish Demand Forecasting Process
- Automate Data Collection
- Monitor Market Trends
- Analyze Historical Data
- Estimate Future Demand
- Adjust Production Levels
- Manage Supply Chain...and much more!
- Deskera's integrated financial planning tools enable investors to better plan and track their investments. It can assist investors in making faster and more accurate decisions.
- Deskera CRM is a powerful solution that manages your sales and helps you close deals quickly. It not only enables you to perform critical tasks like lead generation via email, but it also gives you a comprehensive view of your sales funnel.
- Deskera Books allows you to better manage your accounts and finances. Maintain good accounting practices by automating tasks like billing, invoicing, and payment processing.
- Deskera People is a straightforward tool for centralizing your human resource management functions.
Final Takeaways
We've arrived at the last section of this guide. Let's have a look at some of the most important points to remember:
- Operational excellence refers to the relentless pursuit of efficiency, effectiveness, and continuous improvement in an organization's operations. It involves optimizing processes, eliminating waste, and maximizing productivity to achieve superior performance and deliver exceptional value to customers.
- Order management refers to the process of efficiently and effectively handling customer orders from the point of receipt to the final delivery. It involves managing and coordinating all activities related to order processing, fulfillment, and customer service. The scope of order management encompasses various stages, including order entry, order validation, inventory allocation, order tracking, shipping, and customer support.
- An effective order management system provides real-time visibility of inventory levels and demand patterns. This enables better inventory planning and optimization, minimizing stockouts and excess inventory. Improved inventory management leads to reduced carrying costs, improved cash flow, and efficient use of warehouse space.
- The Shingo Model provides organizations with a comprehensive framework to guide their journey towards operational excellence. By focusing on principles and behaviors, it helps organizations create a culture of continuous improvement, employee empowerment, and customer-centricity, ultimately leading to improved operational performance and organizational success.
- Flawless Execution (FLEX) is a methodology developed by the Afterburner, Inc., a consulting and training firm founded by former U.S. military fighter pilots. FLEX aims to improve operational performance and execution by applying military-inspired principles and techniques in a business context.
- Establish key performance indicators (KPIs) that align with your operational excellence objectives and regularly track and monitor progress. Use data-driven insights to identify trends, opportunities, and areas for improvement. Implement performance dashboards or scorecards to provide real-time visibility into performance and foster accountability.
- Ensure that your operational excellence goals are specific, measurable, achievable, relevant, and time-bound (SMART). Avoid setting vague or generic goals. Instead, make them concrete and quantifiable. For example, rather than stating a goal to "improve customer service," set a specific target, such as "reduce average customer response time by 20% within six months."
- Operational excellence drives improvements in key operational metrics such as cycle time, lead time, and throughput. By identifying and addressing bottlenecks, process inefficiencies, and constraints, organizations can achieve smoother operations, faster delivery, and increased productivity. This enhances overall operational performance and the ability to meet customer demand effectively.
Related Articles
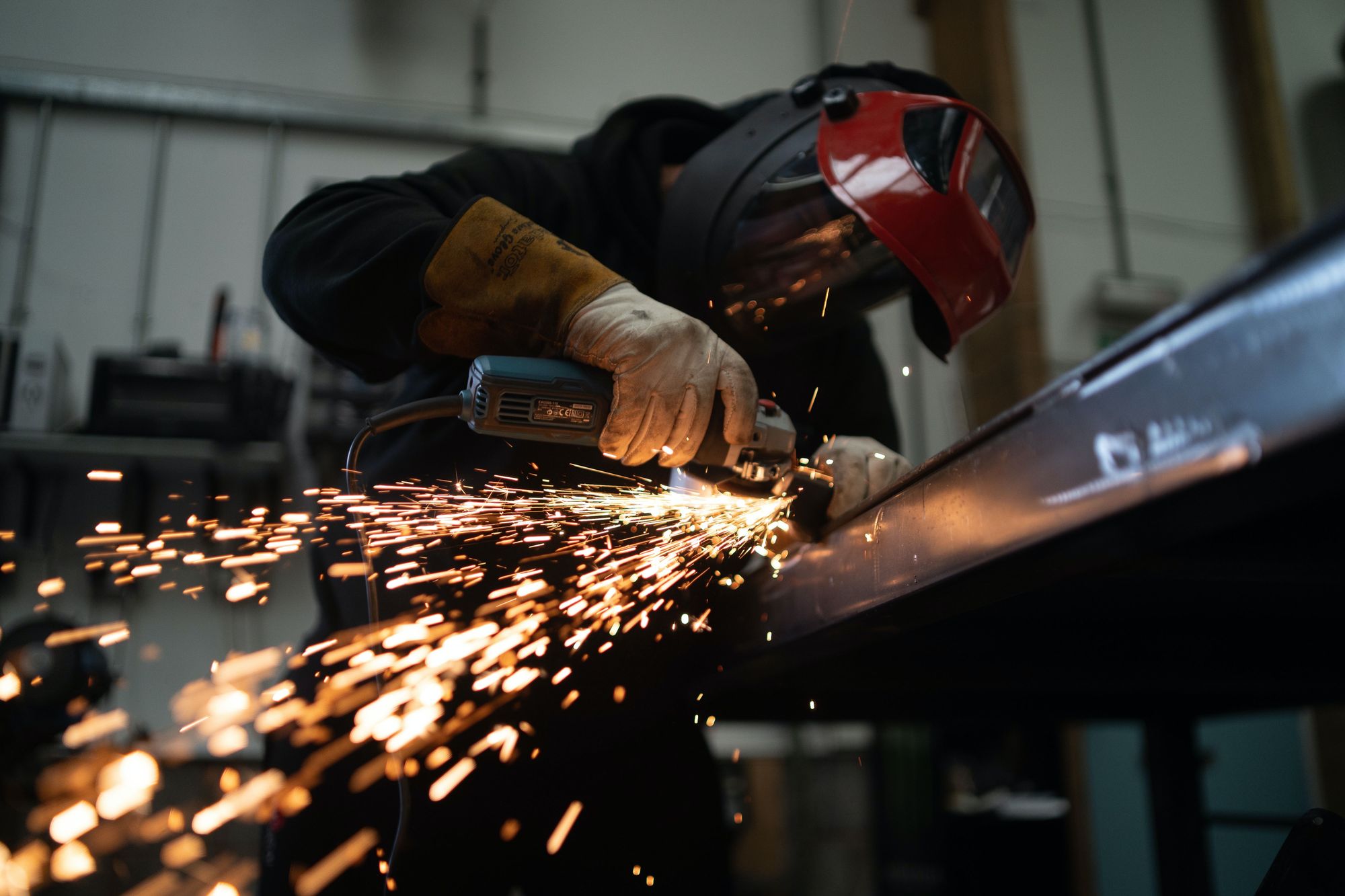
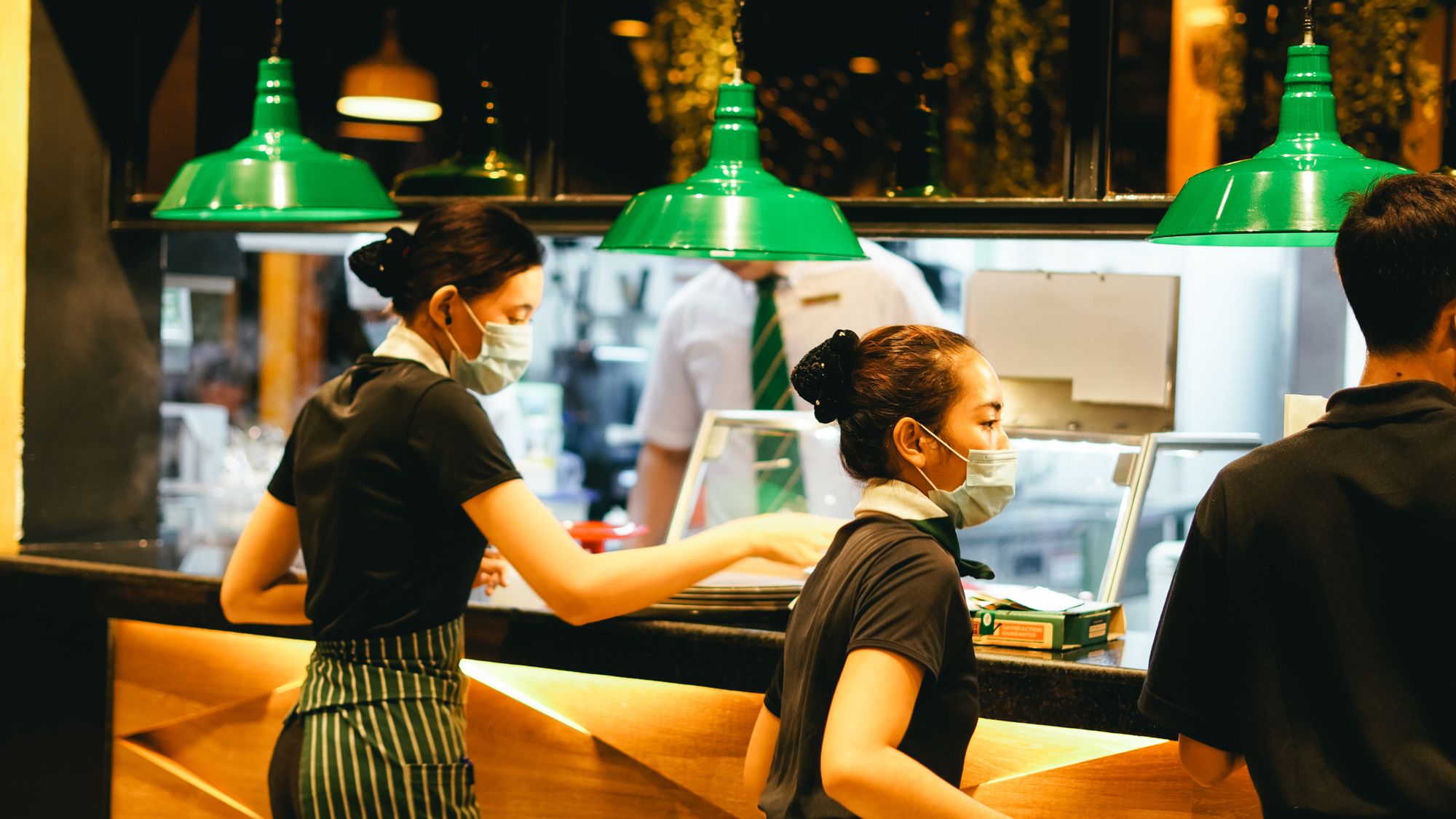
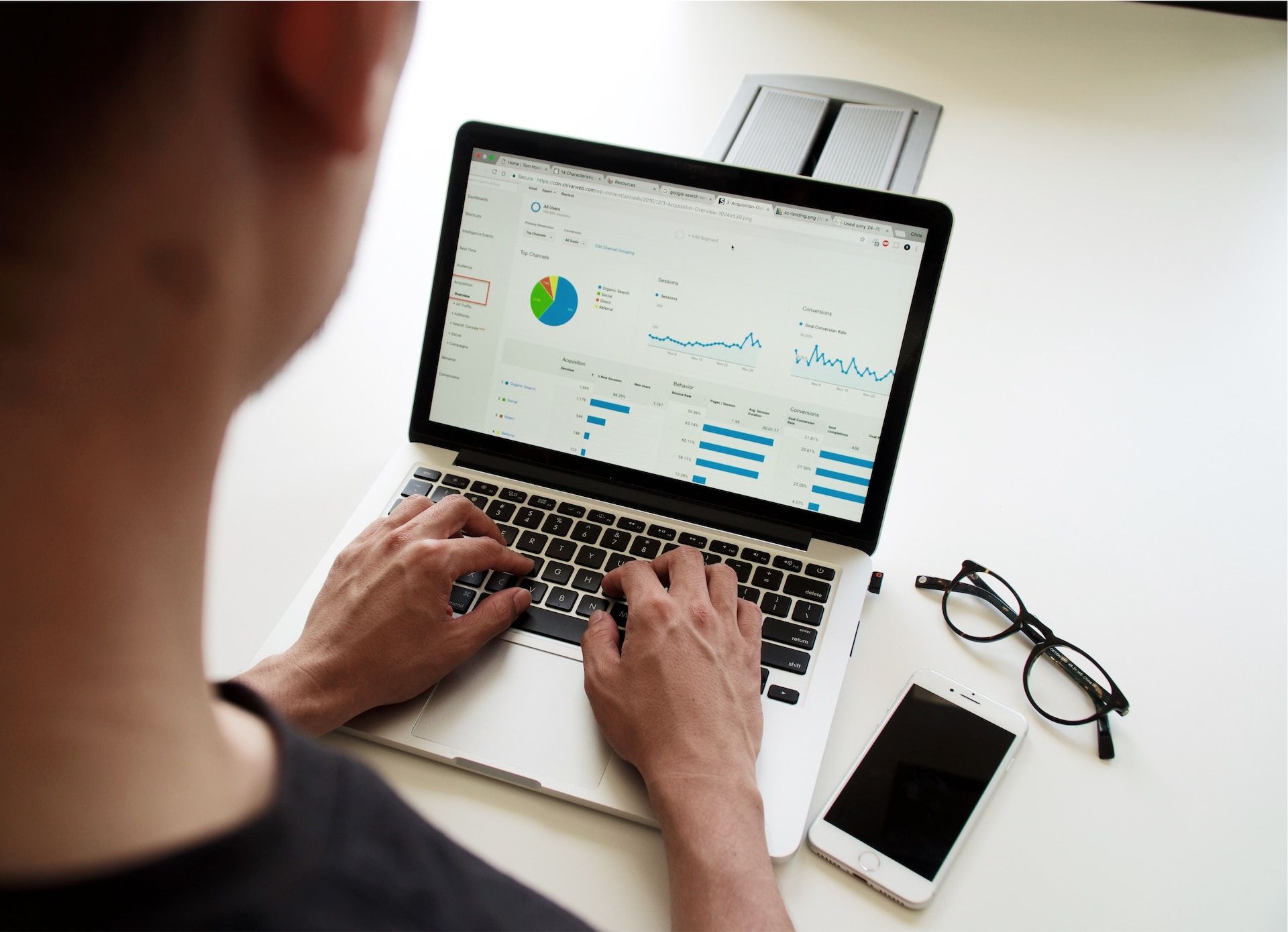
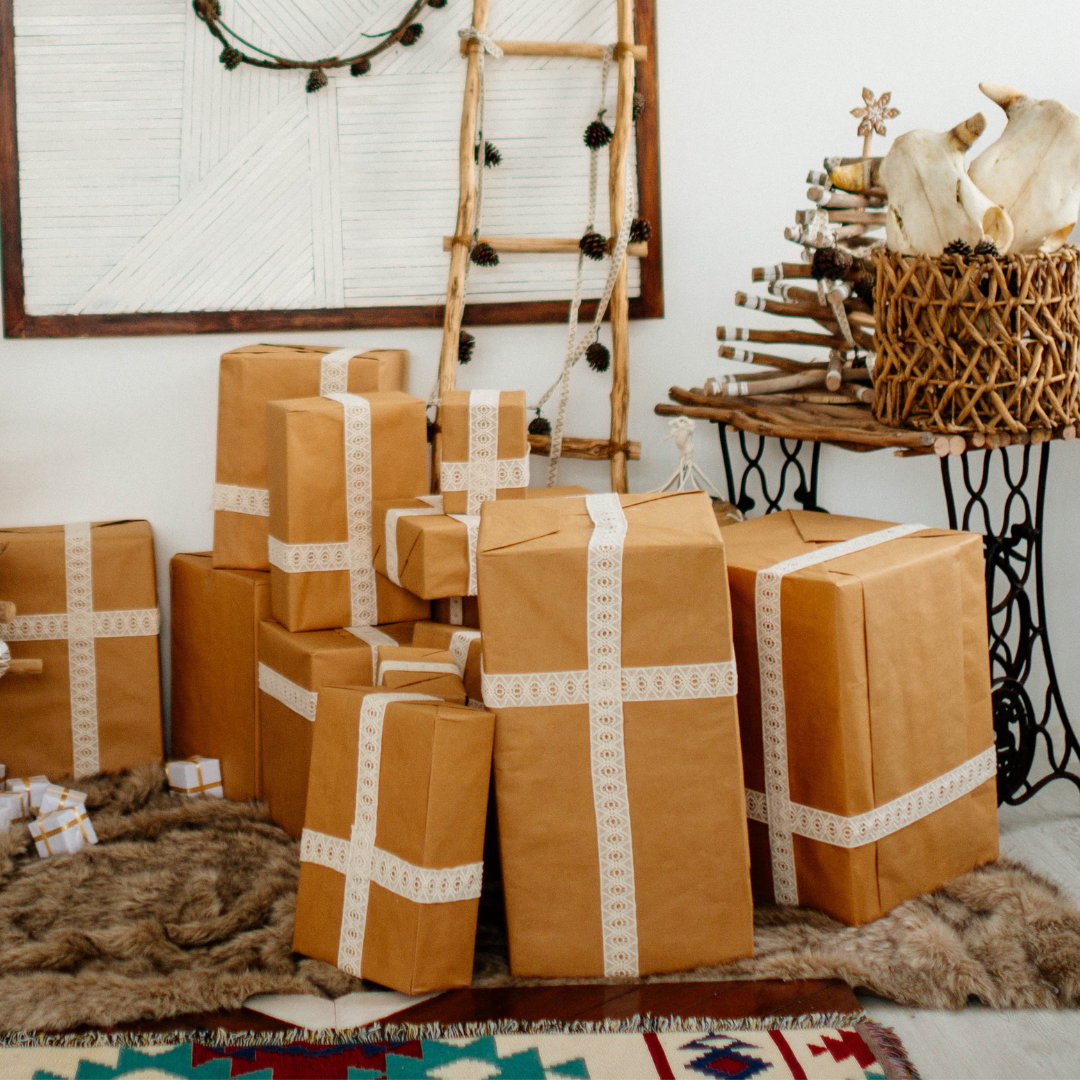
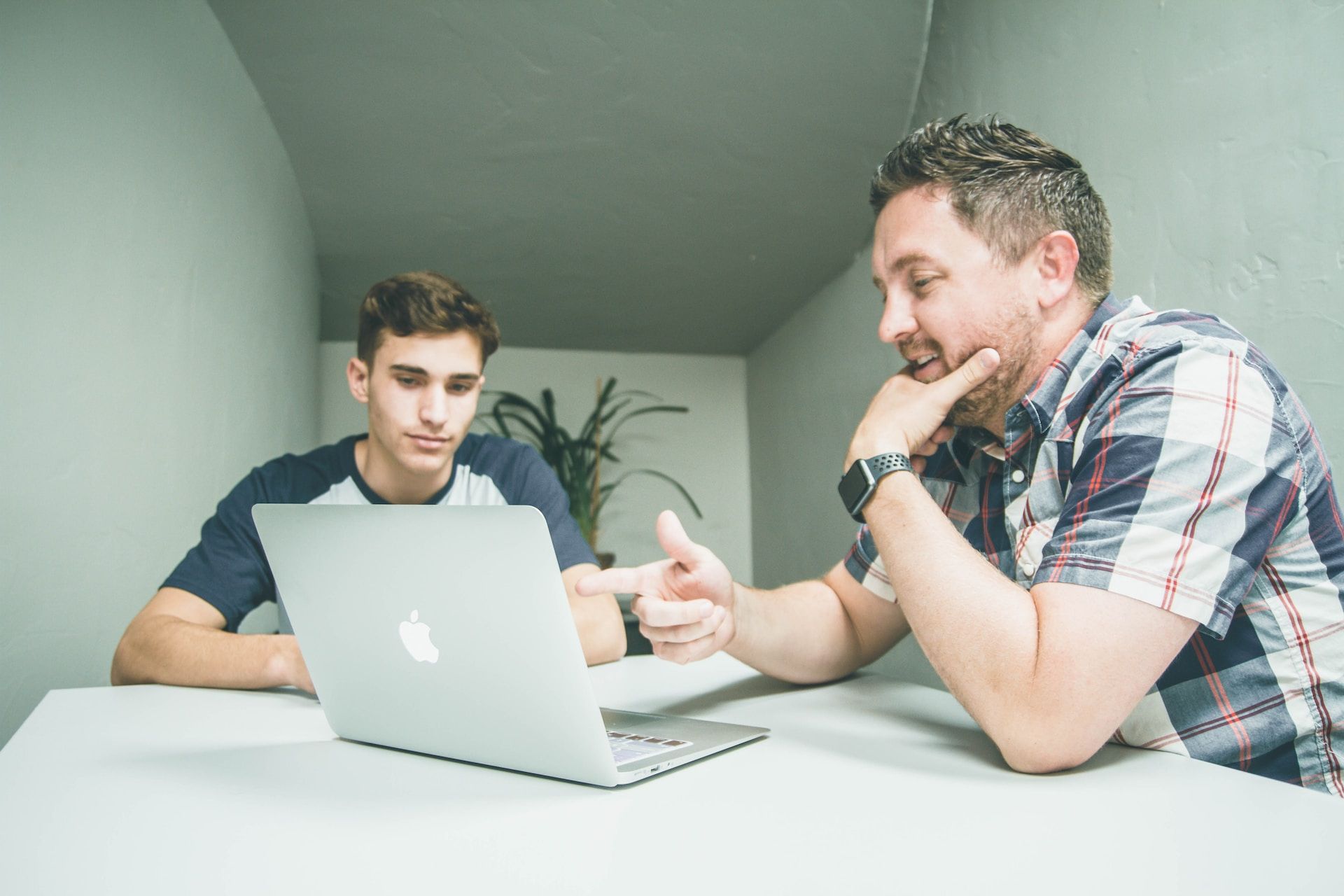