According to a survey conducted by Industry Week, 70% of manufacturing companies stated that the most significant challenge they face is improving productivity and scheduling accuracy. This suggests that accurate shop floor scheduling is crucial to manufacturing productivity.
Managing a shop floor can be a challenging task, and efficient scheduling is key to maximizing productivity and profitability. However, it's not always easy to know where to start when it comes to improving your scheduling practices.
That's why we've put together a list of 10 ways to help you streamline your shop floor scheduling and get the most out of your operations.
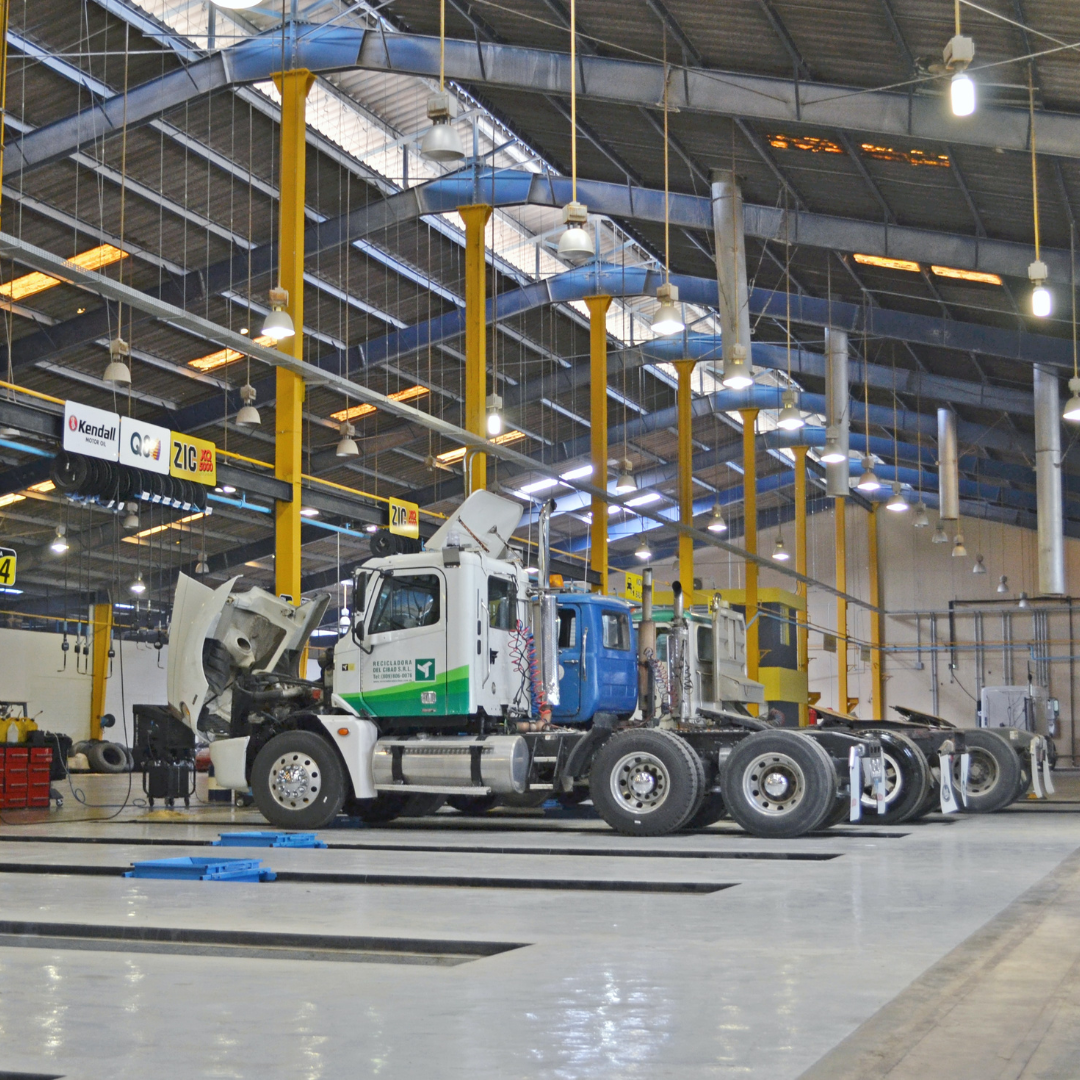
Whether you're looking to reduce downtime, increase throughput, or improve overall efficiency, these tips will provide you with actionable strategies to optimize your scheduling and take your shop floor to the next level.
Here’s what we shall take away from this post:
- What is the Shop Floor?
- What is Shop Floor Scheduling?
- 10 Ways You can Improve Shop Floor Scheduling
- Conclusion
- How can Deskera Help You?
- Key Takeaways
- Related Articles
What is the Shop Floor?
The shop floor refers to the physical space in a manufacturing plant or factory where production activities occur. It is where raw materials and components are transformed into finished products using various tools, machinery, and equipment.
The shop floor is where workers and operators carry out various production activities, such as assembly, machining, welding, painting, and quality control. It is typically a busy and dynamic environment, where multiple processes and activities are taking place simultaneously.
In addition to production activities, the shop floor may also include areas for storing raw materials and finished products, as well as equipment maintenance and repair. Overall, the shop floor is a crucial part of the manufacturing process, as it is where the actual production takes place and where products are created.
What is the Shop Floor Scheduling?
Shop floor scheduling is the process of planning and managing the production activities that take place on the shop floor in a manufacturing plant or factory. It involves creating a schedule of tasks and activities that need to be completed in order to produce finished products, and assigning resources, such as equipment, materials, and personnel, to those tasks.
Shop floor scheduling takes into account factors such as production capacity, resource availability, and production lead times in order to create a feasible and efficient schedule. It is important to ensure that the production schedule is balanced and that all resources are being used effectively, while also ensuring that customer demands are met and inventory levels are managed effectively.
Effective shop floor scheduling is essential to ensure that production processes are executed efficiently, on time, and within budget. It helps to optimize the use of resources, reduce downtime and waste, and improve productivity.
It is typically carried out using specialized software that enables manufacturers to create, manage, and adjust production schedules as needed.
Let’s look at some of the top ways in which you can improve shop floor scheduling.
10 Ways you can Improve Shop Floor Scheduling
Here are ten ways to improve shop floor scheduling:
1. Use a Scheduling Software
Scheduling software can greatly improve shop floor scheduling by automating and optimizing the scheduling process. This type of software can take into account a wide range of variables, such as machine availability, material availability, employee availability, and order priorities. Knowledge about these factors assists in creating an optimized production schedule.
By automating this process, the software can save valuable time and reduce the risk of human error, leading to more accurate and efficient scheduling. Furthermore, it is crucial to understand the appropriate time to start production. A scheduling software can be a great help in such a scenario.
It can also provide real-time updates, allowing shop floor managers to make adjustments to the schedule as needed to avoid bottlenecks, minimize downtime, and ensure on-time delivery of customer orders.
Additionally, this type of software can help managers track key metrics such as production cycle and lead times, allowing them to identify areas where improvements can be made to further optimize the schedule.
2. Analyze Production Data
Analyzing production data can result in providing valuable insights into the performance of the manufacturing process. Managers can identify patterns and trends in production, which can be used to optimize the shop floor schedule.
For example, production data may reveal that certain products require longer setup times or are prone to frequent timeouts. This can be taken into account when creating the schedule.
Additionally, analyzing production data can help managers to identify areas where improvements can be made, such as reducing cycle times, increasing throughput, or improving quality. This information can be used to adjust the schedule to optimize resource allocation, reduce lead times, and improve on-time delivery of customer orders.
3. Develop a Clear Production Plan
Establish a clear production plan that outlines the necessary resources, staffing, and timing required for each job. This action provides a framework for efficient resource allocation and effective scheduling.
A clear production plan outlines the necessary resources, staffing, and timing required for each job, which can be used to create a realistic and efficient schedule that takes into account the available resources.
By developing a clear production plan, managers can identify the critical path for each job and ensure that the necessary resources are available when needed. This can help to minimize delays, which can lead to improved productivity and on-time delivery of customer orders.
Additionally, a clear production plan can help to prioritize production activities, ensuring that high-demand products are given priority over less critical jobs. This can help to maximize profits and improve customer satisfaction by ensuring that orders are delivered on time.
4. Identify the Shop Floor Scheduling Variables
Shop floor variables can include machine availability, material availability, employee availability, order priorities, and other factors that can impact the production process. Identifying these variables can help in better shop floor scheduling by providing a more accurate understanding of the factors that affect production.
- With this technique, managers can create a more detailed and accurate schedule that takes into account the available resources and potential disruptions.
For example, if a particular machine is prone to breakdowns, the schedule can be adjusted to ensure that it is available when needed, and that backup resources are available in case of a breakdown.
- Also, it can help managers to prioritize production activities based on order priorities and demand. This can help to ensure that high-priority orders are given priority over less critical jobs, and that resources are allocated accordingly to maximize efficiency and productivity.
By taking into account the available resources, potential disruptions, and order priorities, managers can create a more accurate and efficient schedule that optimizes resource allocation and maximizes productivity.
5. Consider Demand Planning
Demand planning is a process of estimating future demand for products or services to ensure that the necessary resources are available to meet customer needs. It involves analyzing historical data, market trends, and customer behavior to predict future demand accurately.
It can help in better shop floor scheduling by providing a more accurate forecast of the demand for products. Thus, enabling manufacturers to plan their production schedules accordingly.
By knowing what products are in high demand and when, manufacturers can optimize their production processes, and minimize waste. This information allows them to plan their resources, such as labor, equipment, and materials, and schedule their production lines accordingly.
Demand planning also enables manufacturers to respond quickly to changes in demand, allowing them to adjust their production schedules in real-time to meet changing customer needs.
With accurate demand planning, manufacturers can increase their efficiency and reduce manufacturing costs, resulting in a more streamlined and profitable shop floor scheduling process.
6. Eliminate Manual Work and Spreadsheets
Spreadsheets and manual work can be prone to mistakes, and when it comes to scheduling, even a small error can have significant consequences. Eliminating spreadsheets and manual work can help in better shop floor scheduling by reducing errors, improving accuracy, and saving time.
By using automated software or tools to manage the scheduling process, manufacturers can eliminate the risk of human error and ensure that the schedules are accurate and up-to-date.
This paves the way for optimizing their production processes and minimize downtime. Also, you can reduce waste, resulting in increased efficiency and productivity.
Automated scheduling tools can also provide real-time updates and notifications, allowing manufacturers to respond quickly to changes in demand or unexpected events.
When manual work is eliminated, manufacturers can focus their resources on more value-added tasks, such as analyzing production data and making strategic decisions, rather than spending time on administrative tasks like data entry and manual scheduling.
Overall, eliminating spreadsheets and manual work can help manufacturers to optimize their shop floor scheduling. It results in the following:
- improve accuracy and efficiency
- respond quickly to changes in demand
- more streamlined and profitable production process
7. Schedule Maintenance Activities
Regular maintenance activities can help to identify and address potential issues before they result in more significant problems, reducing the risk of equipment failure and unplanned downtime.
Schedule maintenance activities can help in better shop floor scheduling by reducing the risk of equipment breakdowns, and improving overall equipment effectiveness (OEE).
Here are the points that regular maintenance can assist with:
- With this procedure in place, manufacturers can ensure that maintenance is performed at a time that minimizes disruption to the production process. This helps to maintain productivity and minimize the impact on delivery schedules.
- Regular maintenance also helps to extend the lifespan of equipment, reducing the need for costly repairs or replacements. This can result in significant cost savings over time and increase the overall efficiency of the shop floor.
- In addition, scheduling maintenance activities can help to identify opportunities for process improvements and optimization. By analyzing maintenance data and identifying trends, manufacturers can make data-driven decisions that improve overall equipment effectiveness and reduce waste.
By ensuring that equipment is in good working order, manufacturers can optimize their production processes, improve efficiency, and ultimately increase profitability.
8. Capacity-Loading Scheduling
Capacity-loading scheduling helps optimize the use of available resources and ensuring that the production process runs efficiently. It involves analyzing the available capacity of equipment, labor, and materials and scheduling production to make the most effective use of those resources.
By analyzing the available capacity, manufacturers can ensure that their production schedules are balanced and avoid overloading specific resources, such as equipment or personnel, while other resources remain underutilized. This helps to minimize bottlenecks.
Capacity-loading scheduling can also help to identify potential constraints or limitations in the production process, such as equipment that is reaching the end of its lifespan or personnel with specific skills that are in short supply. By identifying these constraints in advance, manufacturers can plan for the future and make strategic decisions that optimize their production processes.
Production should be scheduled according to what is feasible, and there are two ways to do this in capacity-loading scheduling: Forward and Backward Scheduling
- Forward scheduling: Determining the earliest possible time to complete a customer's order; or
- Backward scheduling: Calculating the production start date based on available resources and material from the due date.
9. Implement Lean Manufacturing
Lean manufacturing is an approach to production that focuses on eliminating waste and optimizing the value stream, or the sequence of steps required to create a product or service.
By implementing lean manufacturing principles, manufacturers can streamline their production processes, reducing the time required to complete each step and increasing the overall efficiency of the shop floor.
This helps to reduce lead times and increase throughput, resulting in a more efficient production process.
Lean manufacturing also helps to reduce waste by identifying and eliminating unnecessary steps in the production process. This can include anything from excess inventory to unnecessary movements or transportation of materials. By reducing waste, manufacturers can save time, reduce costs, and improve overall efficiency.
10. Real-time Production Tracking
By tracking production in real-time, manufacturers can monitor progress, identify obstacles, and optimize processes to avoid unnecessary snags. The process aims at improve overall productivity and reducing lead times, ultimately resulting in a more efficient production process.
Real-time production tracking can also provide valuable insights into equipment performance and maintenance needs. By monitoring equipment in real-time, manufacturers can identify potential issues before they result in breakdowns. This helps to minimize the impact on delivery schedules.
In addition, real-time production tracking can help to identify opportunities for process improvements and optimization. By analyzing production data and identifying trends, manufacturers can make data-driven decisions that improve overall equipment effectiveness, and increase profitability.
Conclusion
Shop floor scheduling is essential in manufacturing as it plays a critical role in ensuring that production processes are optimized and resources are used effectively. The primary goal of shop floor scheduling is to balance the available resources, including labor, equipment, and materials, with the demand for products.
In conclusion, effective shop floor scheduling can help manufacturers to meet customer demands and ensure that they can fulfill orders within the required timeframe. By creating production schedules that are balanced and realistic, manufacturers can avoid overloading specific resources, such as equipment or personnel, and ensure that all resources are being used effectively.
Therefore, adopting techniques and methods that can help to optimize and improve shop floor scheduling is vital to manufacturing sector.
How can Deskera Help You?
Deskera MRP is the only tool that allows you to do everything listed above. Deskera allows you to track raw materials and finished goods inventory.
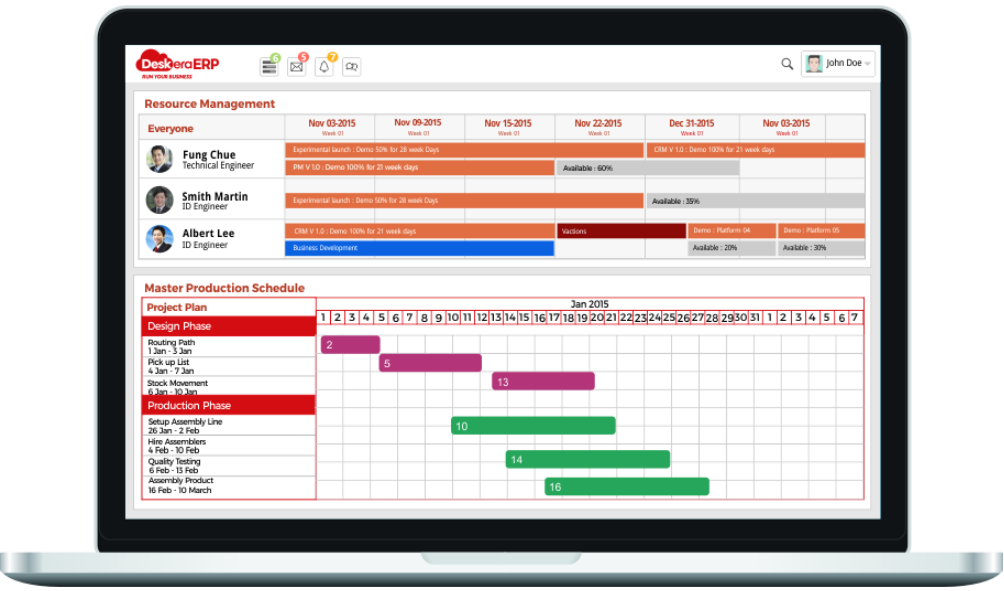
Deskera ERP and MRP system can help you:
- Produce detailed reports
- Make your own dashboards
- Maintain a bill of materials
- Improve resource allocation
Deskera's modules are appropriate for companies of all sizes, from small start-ups to large corporations. It provides businesses with a simple, unified platform for more effective and efficient management of their operations.
Deskera Books is a software that automates accounting and invoice generation.
Deskera CRM excels at customer relationship management.
Deskera ERP provides exceptional enterprise resource planning at a low cost.
Deskera People is a straightforward payroll automation software. The tool streamlines payroll processing from hiring, onboarding, and managing employee benefits and bonuses to leave and attendance management.
Key Takeaways
- There are various ways to improve shop floor scheduling and optimize production processes.
- By implementing demand planning, eliminating spreadsheets and manual work, scheduling maintenance activities, and using capacity-loading scheduling, manufacturers can ensure that their resources are being used effectively, reduce waste, and increase productivity.
- Furthermore, implementing lean manufacturing, using real-time production tracking, and investing in automation and robotics can help to further optimize shop floor scheduling and increase efficiency.
- By making data-driven decisions and focusing on continuous improvement, manufacturers can streamline their production processes, reduce lead times, and ultimately increase profitability.
Related Articles
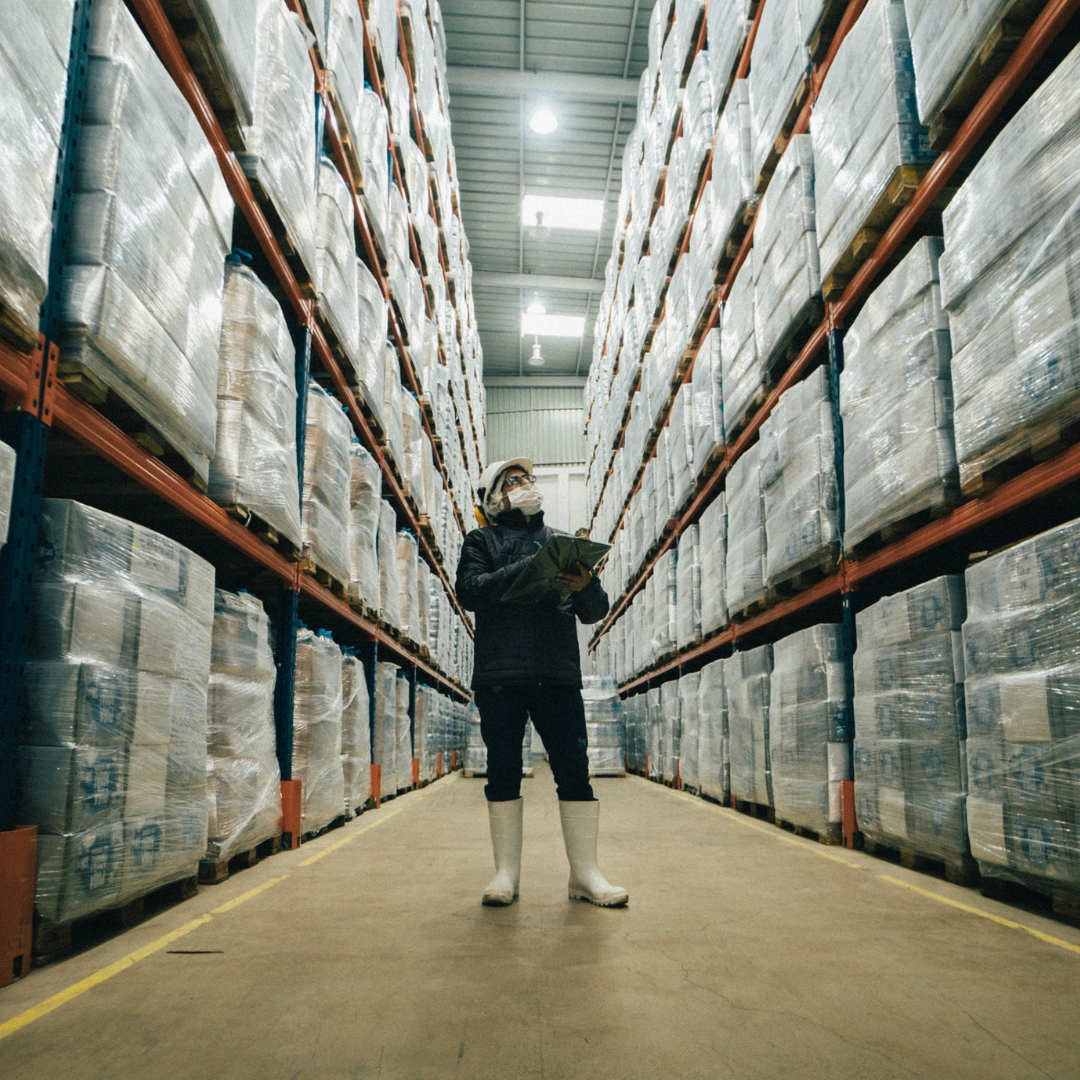
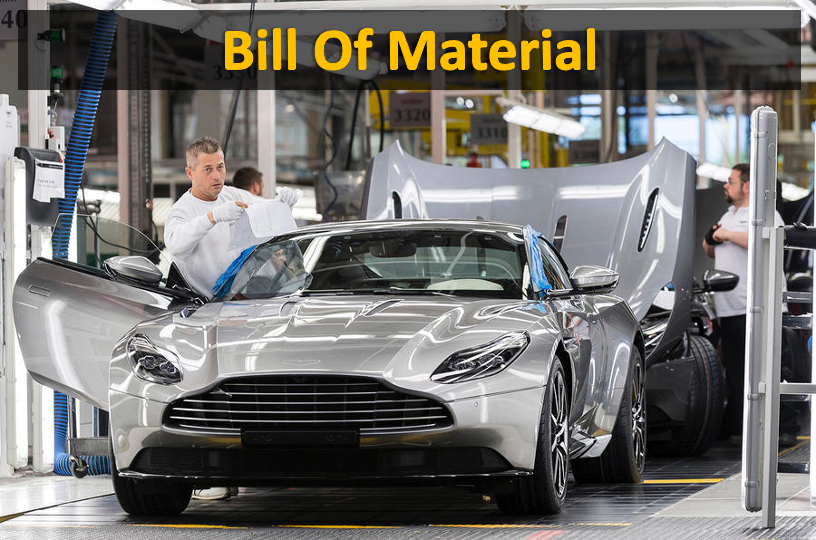
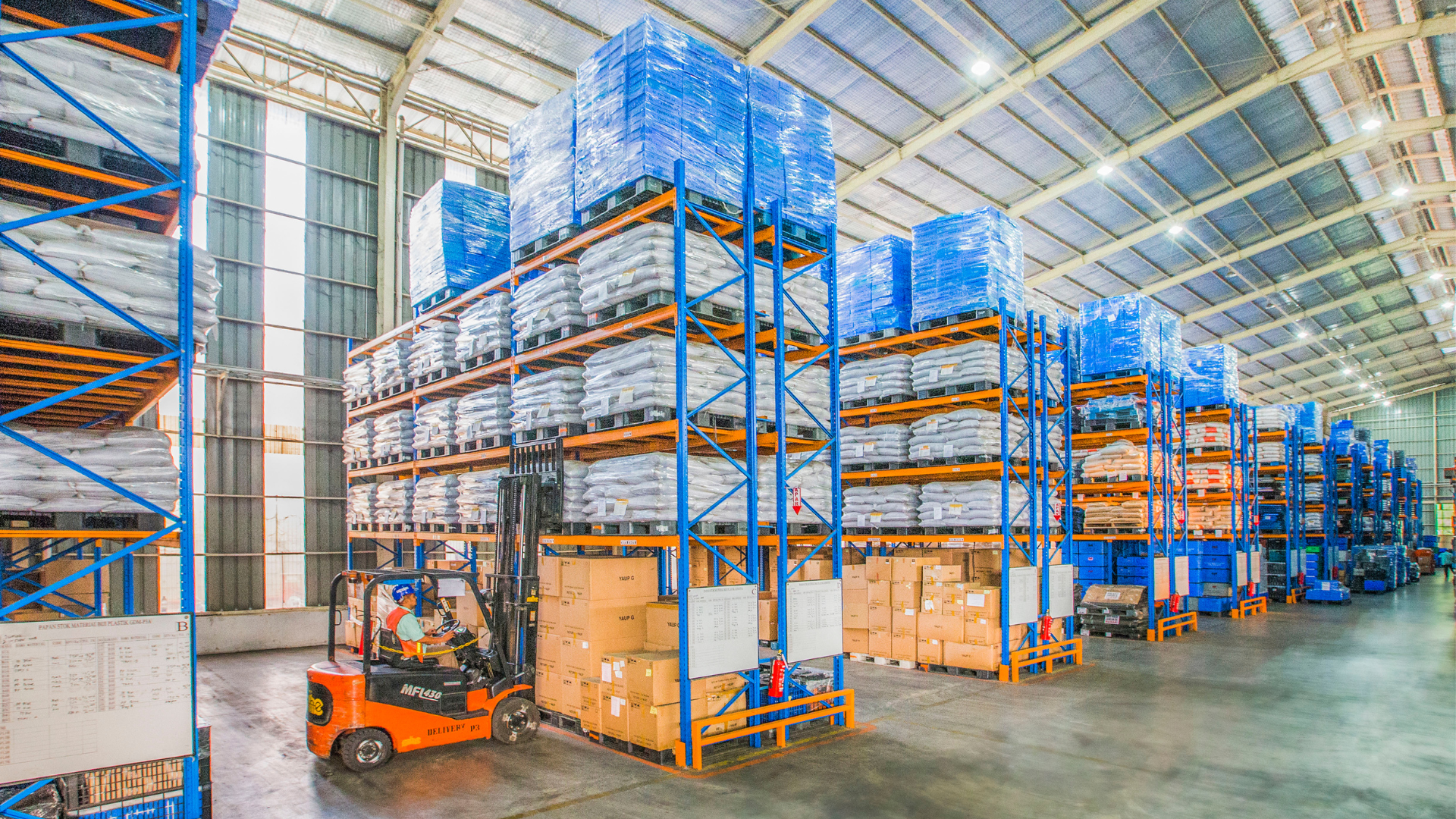
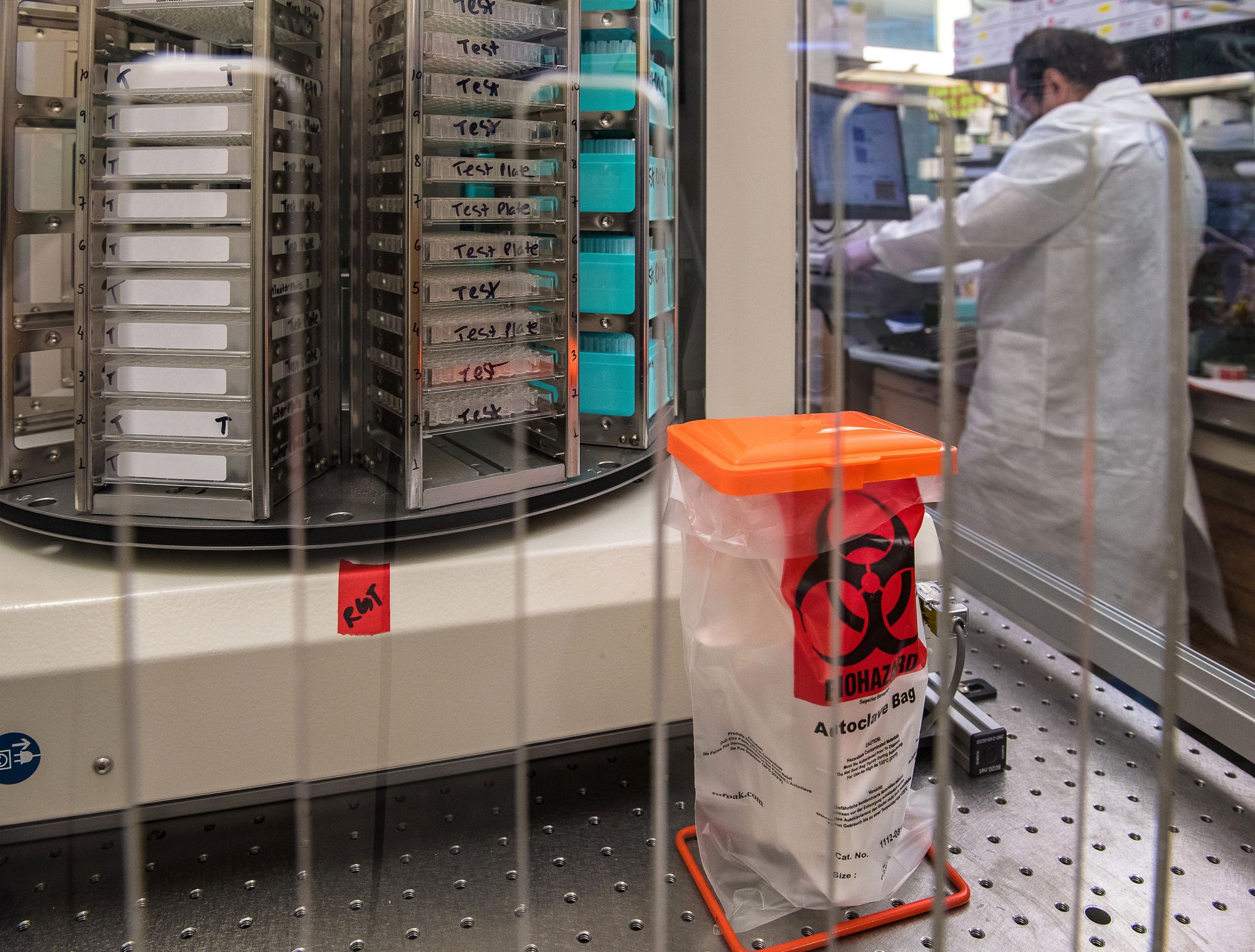