Businesses can fulfill consumer orders more easily when they keep goods on hand. Inventory is often arranged by usage or priority by suppliers, such as cycle inventory, which is required for day-to-day business operations.
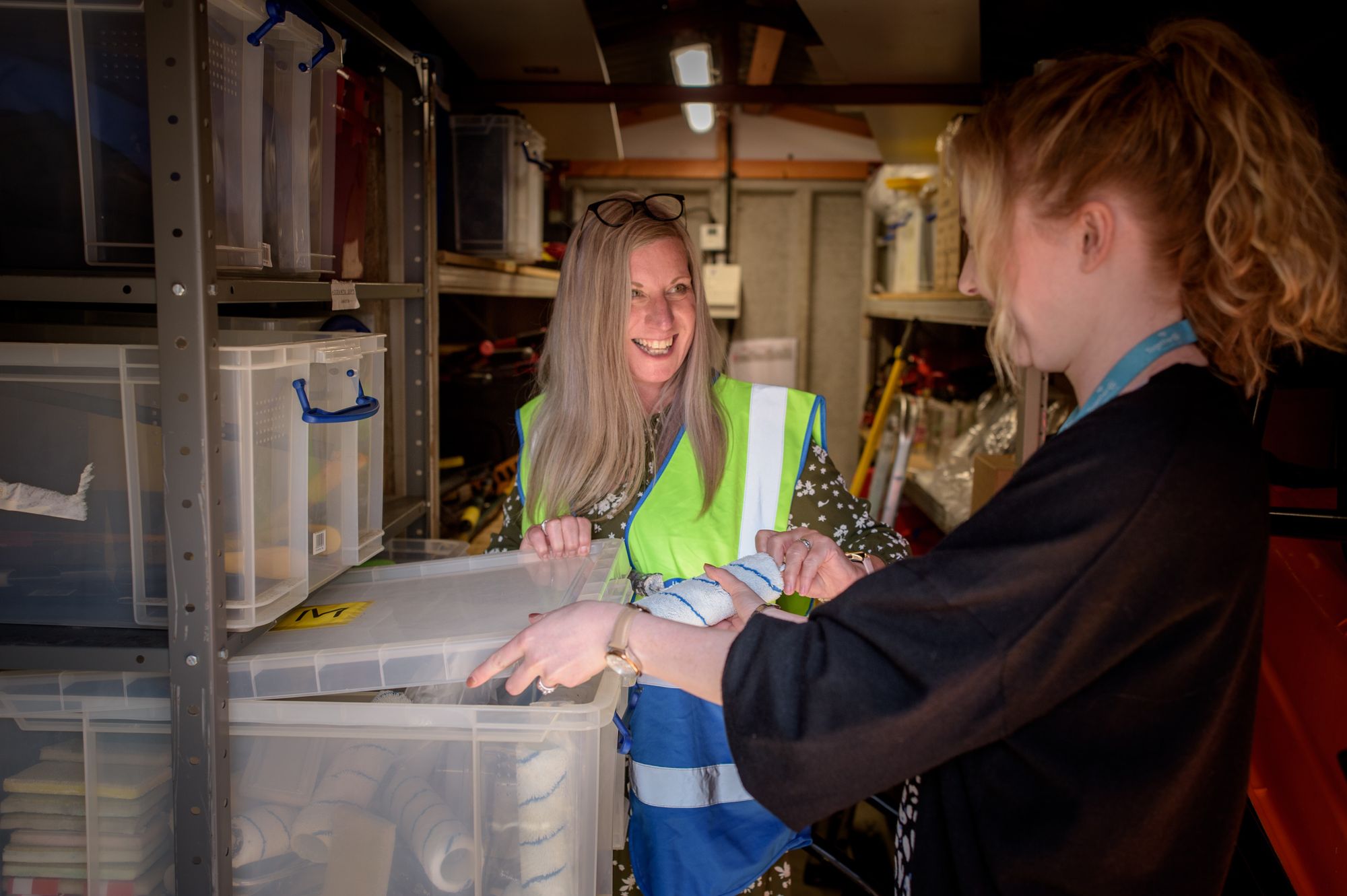
You may manage inventory to satisfy consumer expectations and better understand business needs by understanding cycle inventory. In this article, we define cycle inventory, discuss its significance, and discuss how maintaining proper cycle inventory affects how your company's inventory is organized.
This article covers the following:
- What is cycle inventory?
- How does cycle inventory work?
- What is the importance of cycle inventory?
- What are the factors that are important for cycle inventory?
- What are the benefits of cycle inventory?
- How to calculate cycle inventory?
- How to account for cycle inventory?
- Cycle inventory in supply chain inventory.
- How to manage cycle inventory?
- Tips to improve cycle inventory.
- How can Deskera assist you?
What is Cycle Inventory?
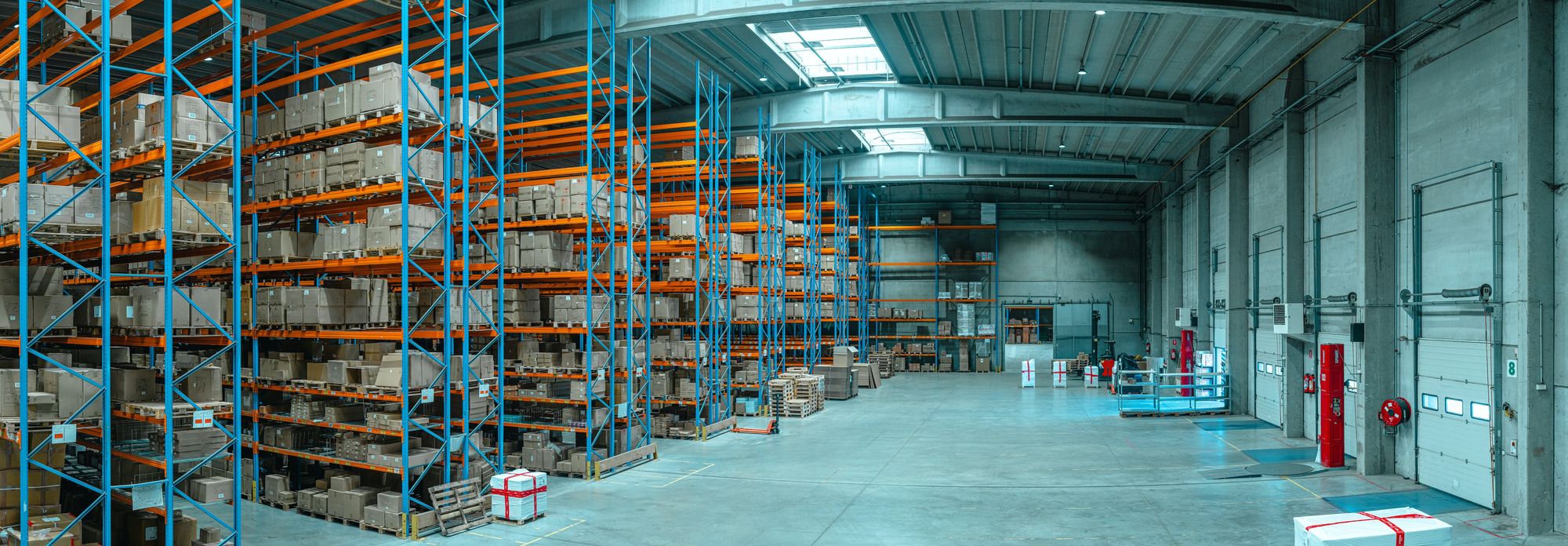
Cycle inventory refers to the goods, supplies, or raw materials that a business keeps on hand to meet its minimum production requirements. Due to the continuous "cycling" of the inventory during normal business operations, cycle inventory is essential to the company's operations.
Effective cycle inventory management enables the company to continue producing high-quality items and meet client needs.
How does Cycle Inventory Work?
Managing cycle stock inventory gets simpler once you detect recurring sales trends and have access to past data to look back on. If done correctly, firms may be confident that the relevant products are readily available in the proper quantities and are efficiently refilled.
The quantity of cycle stock required when a business is first starting out can be challenging to forecast. To determine the right amount to carry, it could be helpful to speak with similar companies or industry professionals.
When calculating the optimal amount of cycle stock, take into consideration important marketing campaigns, seasonality, and pertinent trends. Businesses may create more accurate and detailed demand projections once they have some data to work with.
They will gain insight into how sales change over the course of a year, which SKUs sell quickly or slowly, and other useful data. As many solutions contain a demand planning engine that considers historical data, trends, seasonality, and other criteria to estimate future sales, inventory management software often plays a significant part in this situation.
For each product the business sells, this software may determine the anticipated amount of cycle stock required to cover a specific time period. The most important thing is to have enough cycle stock to endure until the facility receives the next purchase order (whether a manufacturing plant, warehouse or store).
Typically, businesses employ the intervals between order receipts or between production cycles (in industrial environments) as the time frame used to determine cycle stock. By the time the next replenishment order arrives, the company's cycle stock should ideally have been mostly sold.
What is the Importance of Cycle Inventory?
Cycle inventory is crucial since it offers the resources a company requires for everyday operations. The organization, administration, and tracking of cycle inventory can make or break a corporation's production efforts.
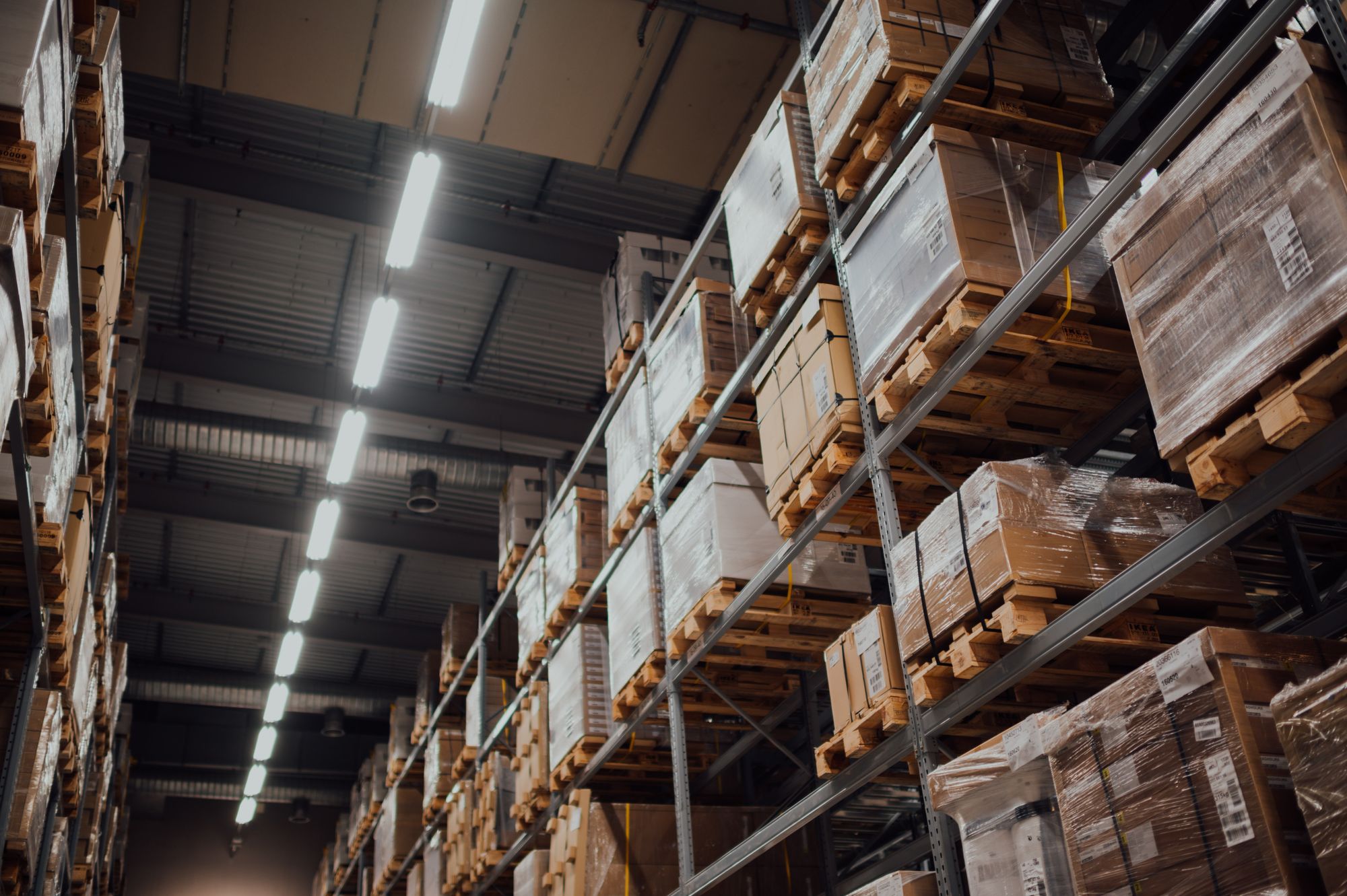
Because of the constant cycling of inventory, the business must replace the inventory it utilizes. Businesses that operate on a business-to-business or direct-to-consumer basis track and manage cycle inventory. Modern inventory software is used by many businesses to improve accuracy, scalability, and information organization.
What are the Factors that Impact Cycle Inventory?
Here are some of the factors that impact cycle inventory:
Demand for the Product
Cycle inventory can be significantly impacted by the demand for the company's products, since more demand may result in more frequent cycling and better management and organization.
The business may retain less inventory on hand and spend less money on production when demand is weaker. For instance, if a bakery maintains flour in its warehouse for bread loaves, it needs a specific quantity of flour to fill usual orders. By monitoring this cycle inventory, the business can effectively adapt to changes in demand and make sure that the bakers have adequate flour for each batch of bread.
Costing of Orders
The cost of acquiring cycle inventory also influences how much the business stores in storage and how readily available it is. Costs associated with an order include those related to tracking, storing, and bringing in freight.
The cycle inventory price for the company may rise if delivery expenses such as gasoline and driver salaries are greater. For instance, if the same bakery needs cane sugar for its bread and fuel prices rise sharply, the business may see an increase in the cost of its orders. The facility that processes raw sugar or the shipper may decide to raise pricing as a result of the growing cost of fuel.
Lead Time of Product
The lead time is the interval between when a business places an order and when the ordered goods actually arrive. In order to meet its basic demands, the corporation must plan further in advance due to longer lead periods.
Lower lead times give the business more time between orders and could help it avoid paying more for expedited shipping. To meet its needs, the bakery, for instance, could need to order its cycle inventory of flour up to a month in advance if there is a scarcity. Although costs could be greater, the organization might locate a superior supplier close by.
Holding Costs
Any monetary expenses incurred in order to store the company's goods are referred to as holding charges. This can include property costs for warehousing space, insurance to secure stored products, labor wages, and material handling costs for transporting materials into and out of warehouses or production locations.
Low holding costs for cycle inventory can assist the company in producing its goods more affordably and frequently more quickly. For instance, if the bakery uses an industrial cooler to store its eggs, the cost of maintaining the cooler is included in its holding expenses. By slashing the lead time between egg orders and batch production of baked goods, the corporation may lower the costs associated with keeping eggs.
Costing of the Products
Cycle inventory is also impacted by the end product's pricing because it may necessitate the use of alternative materials or increased production due to price changes and demand. In general, businesses increase product prices in reaction to rising consumer demand or the cost of raw materials and production.
For instance, the bakery might increase the price of its baked goods if the cost of raw cane sugar increases by 15% as a result of scarcity. This enables the business to pay for its essential costs while still turning a profit on the finished product.
What are the Benefits of Cycle Inventory?
Here are some of the benefits of cycle invetory that you must not miss out on:
Fewer Sales
Forecasts reduce the likelihood that particular supplies may run out. The system will notice if swimsuits in a few sizes started flying off the shelves last spring and boost the order size for those specific items.
Business leaders will become dissatisfied when they find the demand is there but the supply isn't, and they're losing out on revenue, even though under-ordering may initially save them some money.
Reduced Carrying Costs
Forecasts stop you from holding too much inventory, just as they stop you from not having enough things on hand. Keeping the ideal quantity prevents unduly high inventory carrying costs, which are the expense of having products sitting in a store or warehouse.
Safety Stock
Companies that order insufficient inventory usually burn through it, defeating the purpose of holding safety stock in the first place. Safety stock should be kept in reserve for significant interruptions, such as a supplier closing due to a natural disaster or an unusually high demand for a certain item. Forecasts ensure that your safety stock is just that safety stock and not just cycle inventory under another name.
No Oversights
Leading forecasting systems employ algorithms and consider a lot of data when generating projections. By doing the arithmetic and crunching the figures yourself, it's challenging to duplicate that. A new trend you haven't yet observed or something from a year ago that you forgot about might be taken into account by forecasting software.
More Buying Confidence
Confidence is a significant purchase. When you buy more inventory of various goods, you can be a lot more assured if you know what you already have. You won't have to be concerned about buying too much or too little. You'll be able to develop clear plans of action that let you make decisions with assurance.
Decreased Downtime
If you don’t understand your inventory systems or the amount of inventory you have, you’re likely to experience downtime. Without a doubt, this will cost you money. Downtime always costs a lot of money. By staying on top of your inventory, you’ll eliminate downtime and become a more reliable warehouse.
How to Calculate Cycle Inventory?
To calculate the cycle inventory, businesses use a specific formula to calculate how many units the company needs to order at once to maintain production and cost efficiency. Before the company uses this formula, it calculates numbers for several factors, including:
- Annual sales or demand
- Reordering costs
- Cost per unit
- Storage costs
Once you calculate these items, you can use this formula to calculate the number of units to order at once:
Cycle inventory = √[(2 x D x S) / (C x I)]
In this formula:
- D = annual demand for the product
- S = fixed cost per unit
- C = unit cost
- I = storage cost per unit
Accounting for Cycle Inventory
Cycle stock is crucial to accounting since it generates cash, and adding more of this inventory to meet demand has an impact on cash flow. A company's balance sheet will also list any inventory it has as an asset.
Companies have a few options for calculating the costs of goods sold (COGS) for inventories. Because prices change, the inventory costing technique selected may have an impact on COGS and, as a result, gross profit.
The most common and GAAP-accepted costing techniques are as follows:
First In, First Out (FIFO): The cost of inventory is determined by the earliest products that have been bought and the amount paid for them. Therefore, if a customer wants 50 goods, the corporation will calculate the cost based on the items it bought for $20 each two months prior (COGS = $1,000).
Last In, First Out (LIFO): Based on the most recent purchases and the price made for them, the cost of inventory is calculated. If someone orders 50 things, the business will calculate the cost based on the $25 per item cost from two weeks ago (COGS = $1,250).
The Weighted Average Cost (WAC) method merely averages the costs of all sold items. The weighted average price for those 50 goods, using the same example, would be $22.50 (COGS = $1,125).
Cycle Inventory in Supply Chain Inventory
A significant portion of your overall supply chain management strategy is cycle stock (SCM). Sending orders to the appropriate suppliers at the appropriate times and making adjustments based on how rapidly you're selling through products are necessary to maintain the ideal amount of inventory on hand.
It is difficult to find the most economical way to ensure that everything goes according to plan, which explains why firms have invested more in SCM in recent years.
Likewise, if the prediction predicts that sales of a particular category of goods will triple this summer as a result of constant growth over the previous year and a consistent summer demand surge, that could have an effect on downstream supply chain partners.
Do you currently receive volume discounts from your delivery couriers if they are able to manage that volume? You might need to look for a different courier if the charges are too expensive or they don't have the capacity.
How to Manage Cycle Stock Inventory?
Managing cycle stock inventory gets simpler once you detect recurring sales trends and have access to past data to look back on. If done correctly, firms may be confident that the relevant products are readily available in the proper quantities and are efficiently refilled.
The quantity of cycle stock required when a business is first starting out can be challenging to forecast. To determine the right amount to carry, it could be helpful to speak with similar companies or industry professionals.
When calculating the optimal amount of cycle stock, take into consideration important marketing campaigns, seasonality, and pertinent trends. Businesses may create more accurate and detailed demand projections once they have some data to work with.
They will gain insight into how sales change over the course of a year, which SKUs sell quickly or slowly, and other useful data. As many solutions contain a demand planning engine that considers historical data, trends, seasonality, and other criteria to estimate future sales, inventory management software often plays a significant part in this situation.
For each product the business sells, this software may determine the anticipated amount of cycle stock required to cover a specific time period. The most important thing is to have enough cycle stock to endure until the facility receives the next purchase order (whether a manufacturing plant, warehouse or store).
The time period used by businesses to calculate cycle stock is often the interval between receiving orders or, in manufacturing settings, the interval between production runs. By the time the next replenishment order arrives, the company's cycle stock should ideally have been mostly sold.
How to Improve Cycle Inventory?
Here is how you can improve cycle inventory:
Keep an Account
You can account for inventory and ascertain the company's inventory demands with the use of good inventory records. Maintain accurate records and account for any extra inventory by keeping thorough records.
Easy Inventory Management with Inventory Software
Inventory management human labor can be decreased with the aid of inventory software. For a more effective management strategy, take into account inventory software.
Active Calculations
Prices and vendor rates are subject to fluctuate depending on the market, demand, and supply. Make periodic calculations to identify the most economical inventory ordering strategies.
Stay in Touch with your Vendors
You may learn more about the supply chain and stay up to date on changes in price or material availability by communicating often with vendors and suppliers. This can make it easier and quicker for you to account for changes in supply networks.
Simplify Cycle Inventory with Inventory Software
Manually calculating the optimal size for replenishment orders and the amount of cycle stock your company presently has is not only time-consuming and labor-intensive but also prone to error.
Companies require a strong solution like Deskera’s inventory management system to effectively track inventory levels by SKU and across locations. The software may show cycle stock and safety stock separately from total inventory data.
In order to prompt reorders and avoid stockouts, it can also notify users when the amount of an item's on-hand inventory exceeds a predetermined level. Additionally, to predict future demand for various items, Deskera’s demand planning solution has access to a wide range of algorithms.
It takes into account several data sets to forecast future sales and decide how much merchandise companies should order to refill cycle stock, assisting them in maintaining the proper inventory balance.
Cycle stock has a direct impact on your business's capacity for revenue and profit. You may maintain the ideal level of inventory on hand by using software to monitor your inventory and enhance sales projections. This enables businesses to save money while giving more clients a good experience.
How can Deskera Assist You?
Remember discussing best-in-class inventory software? There is no way you can find anything as well-equipped as the Deskera inventory software. Deskera inventory software allows you to closely monitor the manufacturing process.
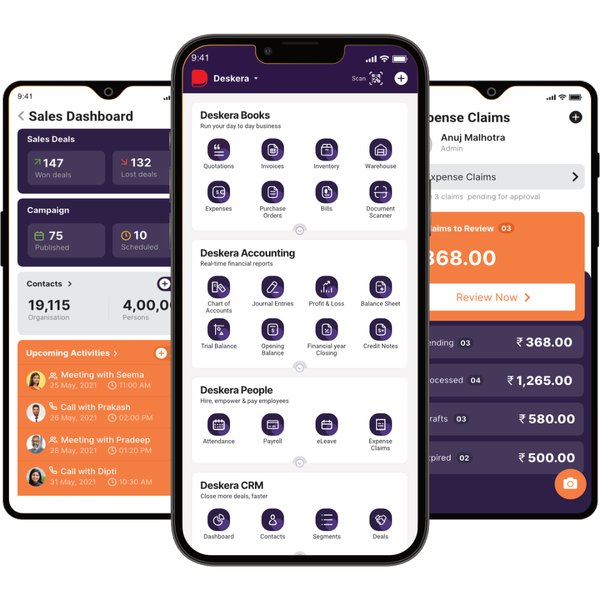
Key Takeaways
- Cycle inventory refers to the goods, supplies, or raw materials that a business keeps on hand to meet its minimum production requirements.
- Managing cycle stock inventory gets simpler once you detect recurring sales trends and have access to past data to look back on.
- Cycle inventory is crucial since it offers the resources a company requires for everyday operations.
- Cycle inventory can be significantly impacted by the demand for the company's products.
- Inventory management human labor can be decreased with the aid of inventory software.
- The cycle inventory price for the company may rise if delivery expenses such as gasoline and driver salaries are greater.
Related Articles:
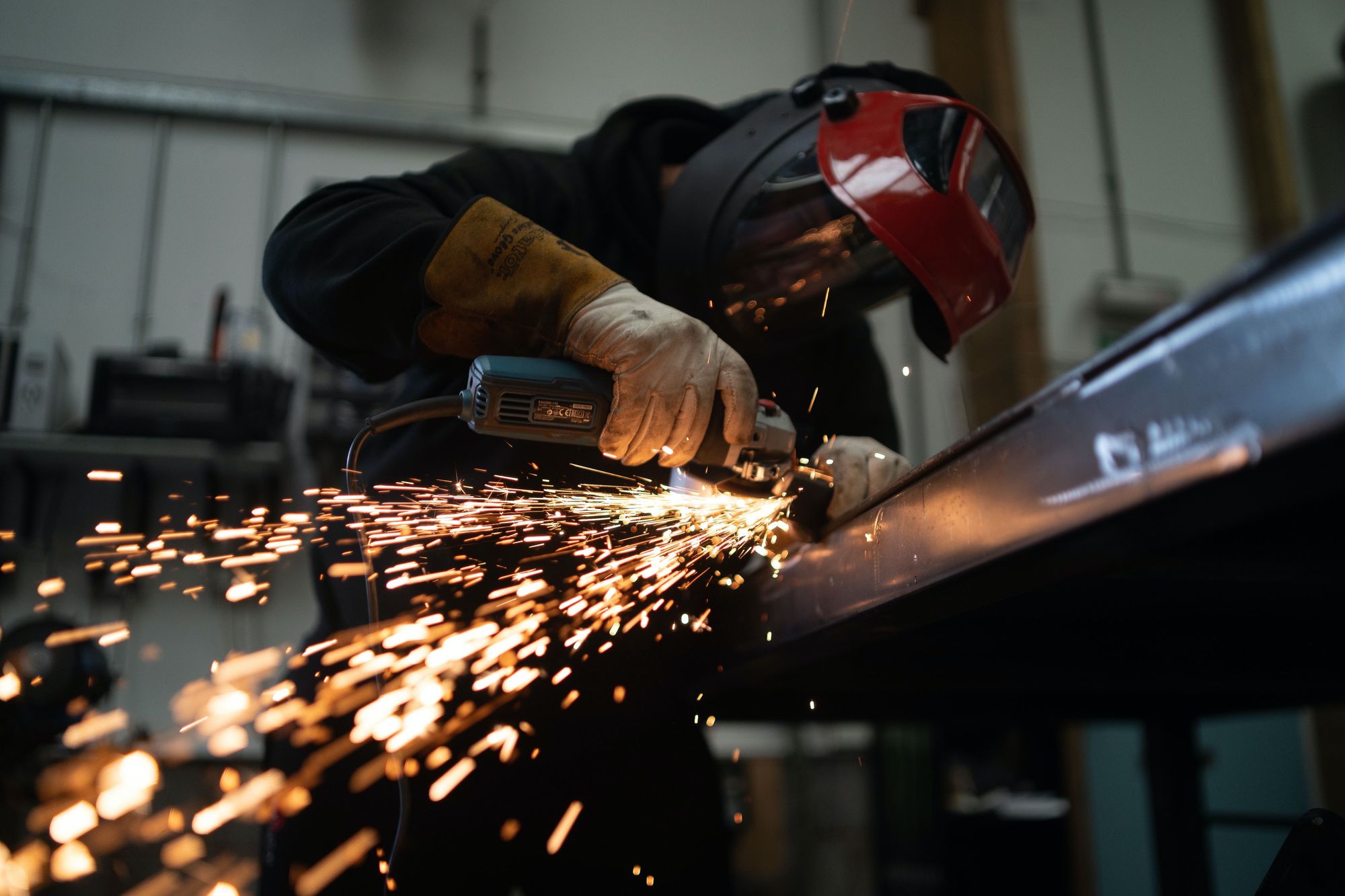
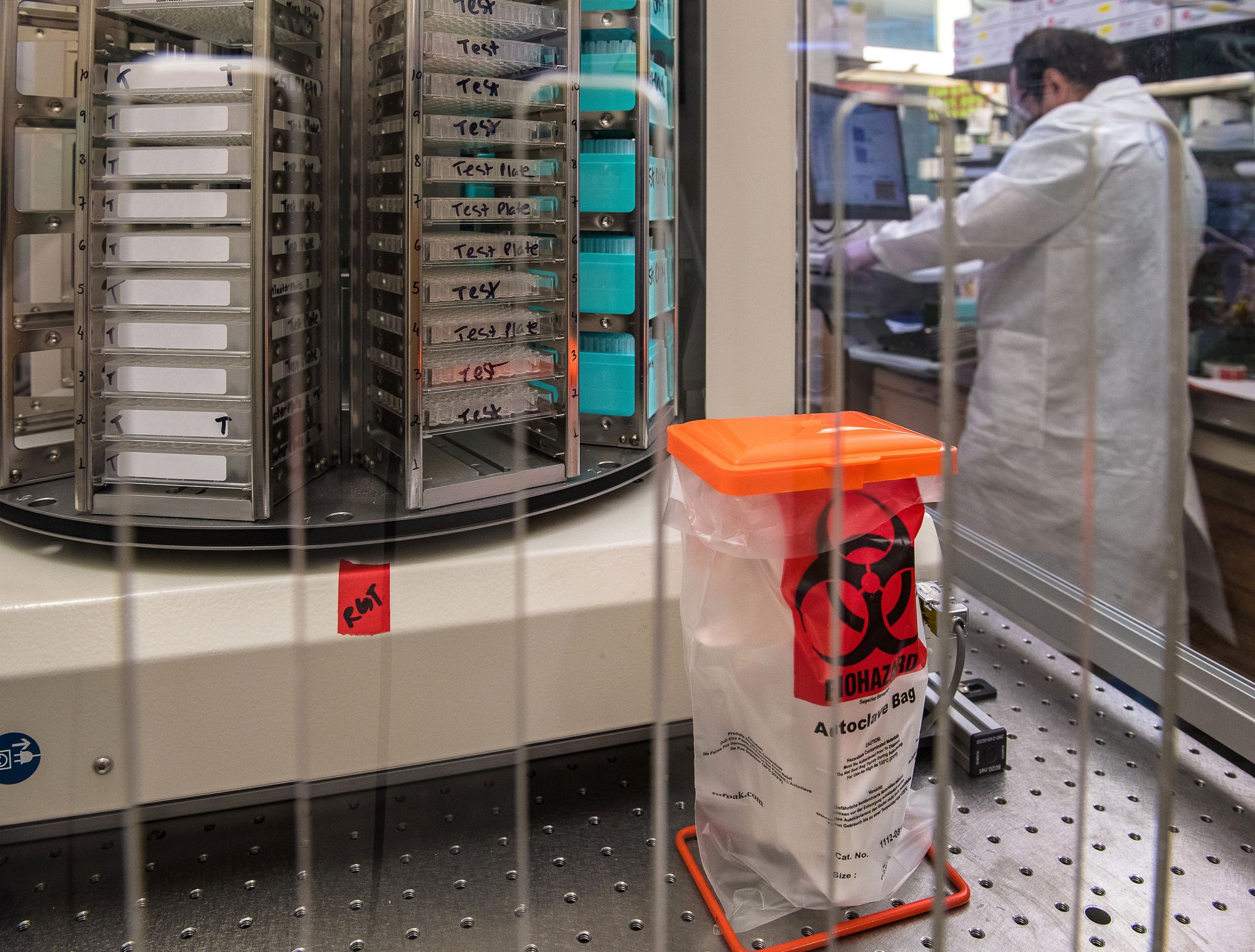
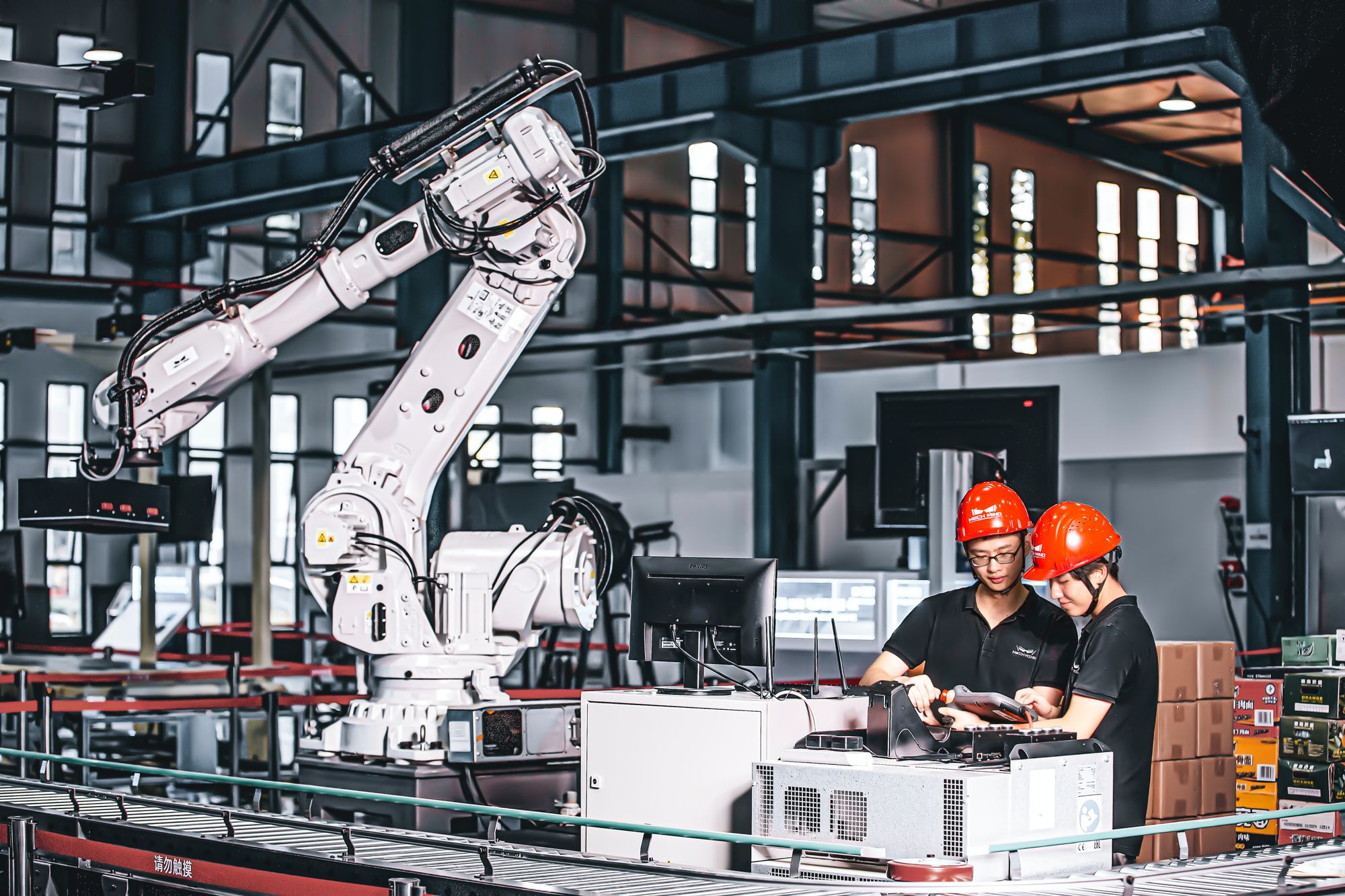
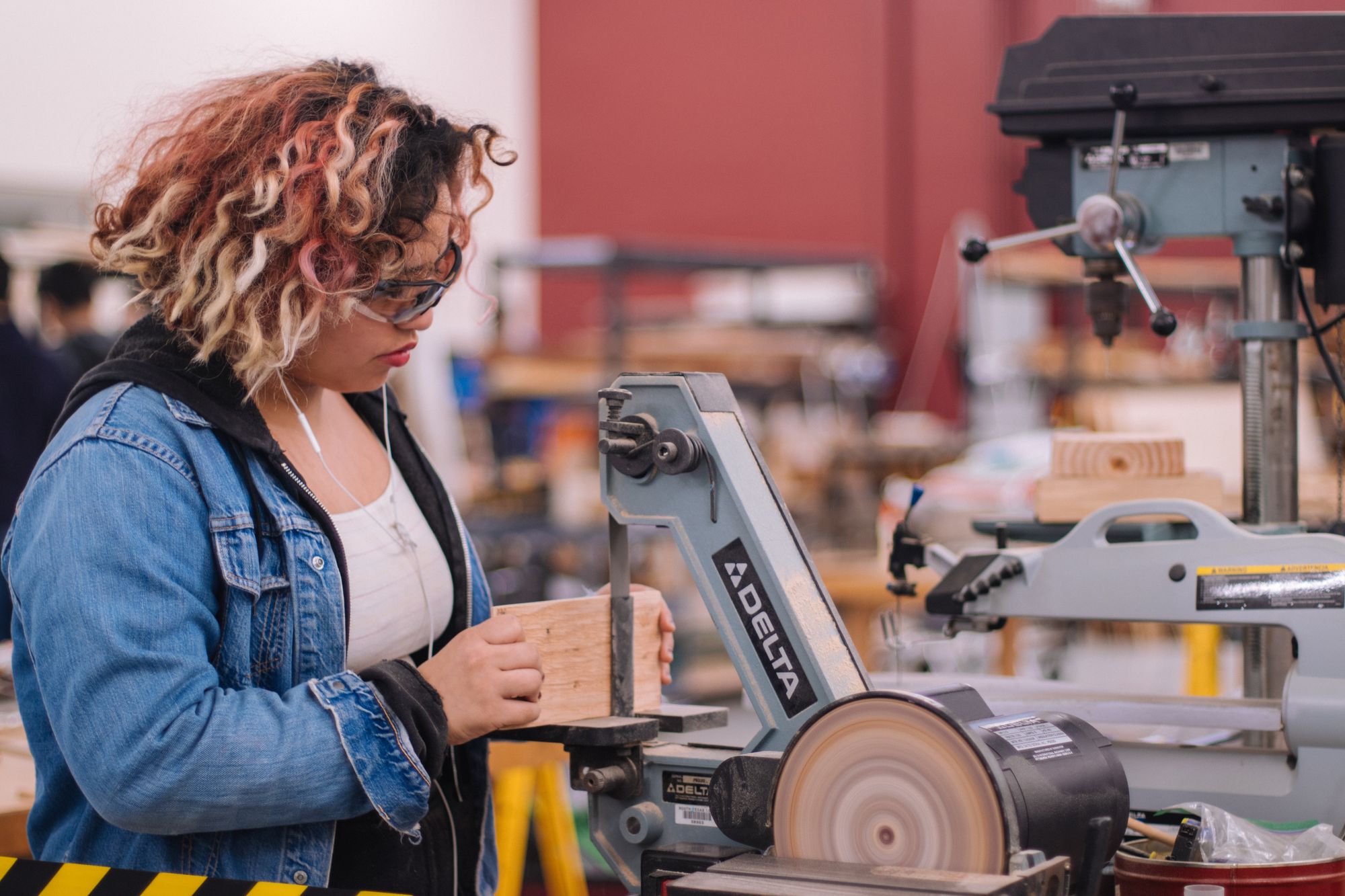