Plastic manufacturing has become an essential part of many different industries, from packaging and construction to automobiles and medical equipment. On the other hand, because of increased costs for labor, raw materials, energy, and waste management, manufacturers today confront considerable challenges.
As consumers become more environmentally conscious, manufacturers are coming under more and more pressure to adopt sustainable practices. Therefore, reducing the cost of plastic manufacturing has become a crucial factor for companies looking to remain competitive while improving their environmental impact.
This article will discuss various strategies that companies can implement to reduce costs in plastic manufacturing. Let’s take a look at the table of content:
- Importance of Reducing Costs of Plastic Manufacturing
- Ways to Reduce Cost of Plastic Manufacturing
- Wrapping Up
- How Deskera Can Assist You?
Let's get started!
Importance of Reducing Costs of Plastic Manufacturing
Reducing the costs of plastic manufacturing is crucial for several reasons:
Affordability: Plastics are widely used in many industries, from packaging to consumer goods to automotive and aerospace industries. Reducing the costs of plastic manufacturing can make these products more affordable and accessible to consumers.
Environmental sustainability: The cost of manufacturing plastics can impact the environment in several ways, such as through greenhouse gas emissions, water usage, and waste generation. By reducing the costs of plastic manufacturing, companies can invest in sustainable manufacturing processes and materials that have less of an impact on the environment.
Innovation: Lower costs can encourage innovation in plastic manufacturing, including the development of new materials and technologies. This can lead to the creation of new products and applications that may not have been feasible with higher costs.
Competitiveness: Reducing the costs of plastic manufacturing can help companies remain competitive in the global marketplace. This can be especially important for small and medium-sized enterprises that may struggle to compete with larger companies.
Overall, reducing the costs of plastic manufacturing can have significant benefits for businesses, consumers, and the environment.
Ways to Reduce Cost of Plastic Manufacturing
Following, we've discussed some crucial ways to reduce cost of plastic manufacturing. Let's discuss:
1. Material Selection
Plastic manufacturing involves the production of plastic products through various processes, including injection molding, extrusion, and blow molding. Material selection plays a critical role in determining the final cost of manufacturing these products. In this response, we will discuss in detail some ways to cut costs with material selection in plastic manufacturing.
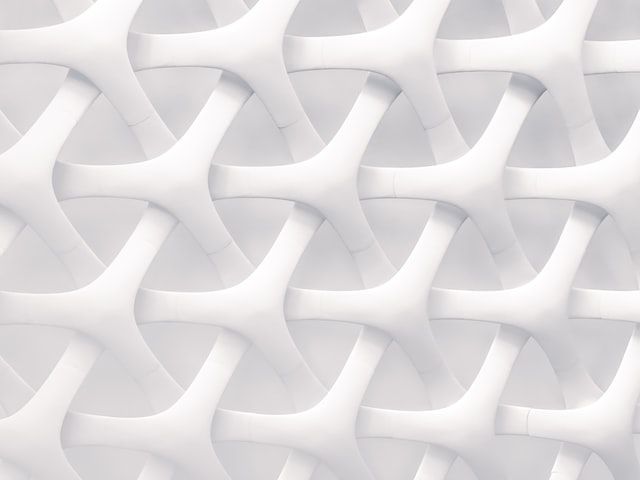
Use Recycled Materials: One effective way to cut costs in plastic manufacturing is by using recycled materials. Recycled materials are usually cheaper than virgin materials, and they also have a lower environmental impact. By incorporating recycled materials into the manufacturing process, manufacturers can reduce the cost of production and also appeal to eco-conscious consumers.
Choose the Right Material: It is essential to select the right material for the product being manufactured. This involves considering factors such as the product's end-use, durability, and strength requirements. By selecting the right material, manufacturers can avoid over-engineering and wasting money on expensive materials that are not necessary.
Optimize Part Design: Part design plays a significant role in the overall cost of manufacturing plastic products. Design optimization involves reducing the amount of material used while maintaining the desired strength and durability. This can be achieved through techniques such as thinning walls, reducing unnecessary features, and designing for efficient material flow.
Use Cost-effective Materials: Some materials are more expensive than others and using them unnecessarily can increase the cost of production. By selecting cost-effective materials that meet the product's requirements, manufacturers can significantly reduce costs. For example, high-density polyethylene (HDPE) is cheaper than polycarbonate (PC) but may be suitable for some products.
Consider Long-term Costs: When selecting materials for plastic manufacturing, it is essential to consider long-term costs. This involves looking at factors such as maintenance, repair, and replacement costs. By selecting materials that require less maintenance, last longer, and are easier to repair, manufacturers can reduce long-term costs significantly.
Work with Suppliers: Working closely with material suppliers can help manufacturers cut costs in plastic manufacturing. Suppliers can provide valuable insights into the best materials to use for specific products and offer cost-effective alternatives. Additionally, partnering with suppliers can lead to better pricing and improved supply chain efficiency.
All in all, cutting costs with material selection in plastic manufacturing requires a careful balance between selecting the right material, optimizing part design, and considering long-term costs. By incorporating recycled materials, choosing cost-effective materials, and working with suppliers, manufacturers can significantly reduce the cost of production while maintaining product quality.
2. Raw Material Procurement
Reducing costs in raw material procurement for plastic manufacturing can be achieved through the following strategies:
Bulk purchasing: One of the most effective ways to reduce the cost of raw materials in plastic manufacturing is by purchasing them in bulk. This approach allows for greater negotiating power with suppliers and can result in lower prices per unit.
Supplier consolidation: Reducing the number of suppliers can lead to better prices and terms for raw materials procurement. This can also simplify the supply chain management process, reducing administrative costs and errors.
Material substitution: Finding alternative raw materials that are less expensive can help reduce costs. However, it is important to ensure that any substitutions maintain product quality and performance standards.
Lean manufacturing: Implementing lean manufacturing principles can help reduce waste and improve efficiency in the production process, which can ultimately lead to lower costs.
Supply chain optimization: Optimizing the supply chain through better inventory management, logistics planning, and demand forecasting can help reduce costs associated with raw material procurement.
Negotiating with suppliers: Negotiating with suppliers for better prices and terms can help reduce costs in the procurement of raw materials.
By implementing these strategies, companies can effectively reduce costs associated with raw material procurement in plastic manufacturing, resulting in a more cost-effective and sustainable production process.
3. Efficient Production Processes
Reducing costs in plastic manufacturing for efficient production processes can be achieved through the following strategies:
Automation: Automating production processes can help reduce labor costs and improve efficiency. This can include the use of robots and other automated machinery to streamline production and reduce errors.
Process optimization: Analyzing production processes and identifying areas for improvement can help reduce waste, reduce downtime, and improve efficiency. This can include using techniques like lean manufacturing and Six Sigma to streamline production processes.
Energy efficiency: Improving energy efficiency can reduce the cost of production. This can include using energy-efficient machinery and equipment, implementing energy-saving measures like lighting and HVAC controls, and using renewable energy sources like solar or wind power.
Maintenance and repair: Proper maintenance and repair of machinery and equipment can help prevent breakdowns and improve efficiency. This can include regular inspections, preventative maintenance, and timely repairs.
Continuous improvement: Implementing a continuous improvement program can help identify opportunities for cost reduction and efficiency improvements on an ongoing basis. This can include regular reviews of production processes, feedback from employees, and customer feedback.
Supply chain management: Effective supply chain management can help reduce costs associated with raw material procurement, logistics, and inventory management. This can include supplier consolidation, just-in-time inventory management, and demand forecasting.
By implementing these strategies, companies can reduce costs associated with plastic manufacturing and improve efficiency, resulting in a more cost-effective and sustainable production process.
4. Recycling and Reuse
Reducing costs in plastic manufacturing for recycling and reuse can be achieved through the following strategies:
Closed-loop systems: Implementing closed-loop systems can reduce costs associated with the procurement of new raw materials. Closed-loop systems involve recycling and reusing materials within the production process, reducing waste and the need for new materials.
Material recovery facilities: Implementing material recovery facilities can help recover materials that would otherwise be wasted. This can include recycling scrap plastic or reprocessing plastic waste into new products.
Product design: Designing products for ease of disassembly and recycling can reduce costs associated with material recovery. This can include using materials that are easier to recycle or designing products with fewer parts.
Circular supply chain: Implementing a circular supply chain can reduce costs associated with the procurement of new materials. This involves collaborating with suppliers, customers, and other stakeholders to reduce waste and maximize the reuse and recycling of materials.
Regulatory compliance: Compliance with regulations and standards related to recycling and reuse can reduce costs associated with fines or penalties. This can include compliance with recycling quotas or environmental regulations.
Technology innovation: Investing in technology innovation can help reduce costs associated with recycling and reuse. This can include investing in new recycling technologies or developing new products made from recycled materials.
By implementing these strategies, companies can reduce costs associated with plastic manufacturing for recycling and reuse, resulting in a more sustainable and cost-effective production process.
5. Energy Efficiency
Reducing costs in plastic manufacturing for energy efficiency can be achieved through the following strategies:
Equipment efficiency: Using energy-efficient machinery and equipment can reduce energy costs and improve efficiency. This can include replacing older equipment with newer, more energy-efficient models.
Lighting and HVAC controls: Installing energy-efficient lighting and HVAC controls can help reduce energy costs associated with heating, ventilation, and air conditioning. This can include installing programmable thermostats and occupancy sensors to reduce energy usage in areas that are not in use.
Renewable energy sources: Investing in renewable energy sources like solar or wind power can help reduce energy costs associated with electricity usage. This can include installing solar panels or wind turbines to generate electricity on-site.
Energy management systems: Implementing energy management systems can help reduce energy costs associated with production processes. This can include real-time monitoring of energy usage and the implementation of energy-saving measures like peak load management.
Employee engagement: Engaging employees in energy-saving initiatives can help reduce energy costs. This can include training employees on energy-saving measures, providing incentives for energy savings, and encouraging employees to identify and report energy-saving opportunities.
Continuous improvement: Implementing a continuous improvement program can help identify opportunities for energy efficiency improvements on an ongoing basis. This can include regular reviews of energy usage, feedback from employees, and customer feedback.
By implementing these strategies, companies can reduce costs associated with plastic manufacturing for energy efficiency, resulting in a more sustainable and cost-effective production process.
6. Labor Costs
Reducing costs in plastic manufacturing for labor costs can be achieved through the following strategies:
Automation: Automating production processes can reduce the need for labor and help improve efficiency. This can include the use of robots and other automated machinery to streamline production and reduce errors.
Cross-training: Cross-training employees in multiple areas can help reduce labor costs by enabling the company to be more flexible with its workforce. This can help reduce downtime and improve efficiency.
Outsourcing: Outsourcing certain functions can help reduce labor costs associated with those functions. This can include outsourcing functions like packaging or assembly to specialized contractors.
Shift scheduling: Optimizing shift scheduling can help reduce labor costs. This can include adjusting shift schedules to match production demand and avoiding overtime pay whenever possible.
Employee engagement: Engaging employees in continuous improvement initiatives can help reduce labor costs by enabling them to identify and implement process improvements. This can include providing incentives for employee ideas and feedback.
Training and development: Investing in employee training and development can help reduce labor costs associated with turnover and absenteeism. This can include providing training on production processes and safety procedures, as well as offering opportunities for career development and advancement.
By implementing these strategies, companies can reduce costs associated with plastic manufacturing for labor costs, resulting in a more cost-effective and sustainable production process.
7. Quality Control
Reducing costs in plastic manufacturing for quality control can be achieved through the following strategies:
Statistical process control: Implementing statistical process control can help identify quality issues early in the production process, reducing the need for rework and improving efficiency.
Automation: Automating quality control processes can help improve efficiency and reduce labor costs associated with manual inspection. This can include the use of automated testing equipment and quality control software.
Supplier quality management: Implementing supplier quality management can help reduce costs associated with defects in raw materials or components. This can include implementing supplier audits and inspections, as well as providing supplier training on quality standards.
Employee training: Providing employee training on quality standards and procedures can help reduce costs associated with quality issues and rework. This can include providing training on inspection techniques and quality control procedures.
Continuous improvement: Implementing a continuous improvement program can help identify opportunities for quality improvement on an ongoing basis. This can include regular reviews of quality data and feedback from employees and customers.
Root cause analysis: Implementing root cause analysis can help identify the underlying causes of quality issues, enabling the company to implement targeted solutions to prevent future issues.
By implementing these strategies, companies can reduce costs associated with plastic manufacturing for quality control, resulting in a more cost-effective and sustainable production process.
8. Supply Chain Optimization
Reducing costs in plastic manufacturing for supply chain optimization can be achieved through the following strategies:
Inventory management: Implementing effective inventory management practices can help reduce costs associated with inventory holding and storage. This can include using just-in-time (JIT) inventory management and implementing inventory tracking systems.
Supplier management: Implementing effective supplier management practices can help reduce costs associated with raw material procurement. This can include negotiating better pricing and terms with suppliers, implementing supplier performance monitoring, and supplier collaboration.
Transportation optimization: Optimizing transportation can help reduce costs associated with transporting raw materials and finished goods. This can include optimizing transportation routes, using transportation optimization software, and consolidating shipments.
Demand forecasting: Implementing effective demand forecasting can help reduce costs associated with overproduction and underproduction. This can include using demand planning software and using customer demand data to make production decisions.
Collaboration and communication: Collaborating with suppliers and customers can help improve supply chain efficiency and reduce costs. This can include using collaborative planning, forecasting, and replenishment (CPFR) and improving communication between supply chain partners.
Continuous improvement: Implementing a continuous improvement program can help identify opportunities for supply chain optimization on an ongoing basis. This can include regular reviews of supply chain data and feedback from employees and customers.
By implementing these strategies, companies can reduce costs associated with plastic manufacturing for supply chain optimization, resulting in a more cost-effective and sustainable production process.
9. Pricing Strategy Against Competitors
To reduce costs in plastic manufacturing, it is important to consider the pricing strategy against competitors. Here are some strategies to consider:
Cost-plus pricing: This is a pricing strategy where you add a markup to the cost of production to determine the price of the product. This strategy helps ensure that you are covering your costs and making a profit, while still remaining competitive with your pricing.
Value-based pricing: This is a pricing strategy where you determine the price of the product based on the perceived value to the customer. This can be particularly effective if your product has unique features or benefits that differentiate it from competitors.
Penetration pricing: This is a pricing strategy where you set a low price for your product initially to gain market share and attract customers. This strategy can be effective if you are entering a new market or if you have a product that is not well-known.
Skimming pricing: This is a pricing strategy where you set a high price initially for your product to capture the high-end of the market before gradually lowering the price. This strategy can be effective if you have a product that is perceived as premium or high-end.
Competitive pricing: This is a pricing strategy where you set your prices based on the prices of your competitors. This strategy can be effective if you are in a highly competitive market and want to remain competitive with your pricing.
When deciding on a pricing strategy, it is important to consider the costs associated with your product, including raw materials, labor, and overhead costs. You should also consider the value of your product to the customer, as well as the prices of your competitors.
In addition to setting the right price for your product, it is also important to continuously monitor and adjust your pricing strategy based on market conditions and changes in costs. This can help ensure that you remain competitive while also maximizing profitability.
Wrapping Up
In conclusion, reducing the cost of plastic manufacturing requires a multifaceted approach that involves optimizing various aspects of the production process. By focusing on strategies such as raw material procurement, efficient production processes, recycling and reuse, energy efficiency, labor costs, quality control, and supply chain optimization, companies can reduce costs, increase efficiency, and improve sustainability.
Effective cost reduction strategies can include process automation, employee training, continuous improvement programs, and the use of data-driven decision-making. Companies must also consider pricing strategies and competitor analysis when reducing costs in plastic manufacturing.
Overall, the goal of reducing the cost of plastic manufacturing is to create a more efficient and sustainable production process that balances cost-effectiveness with quality and social responsibility. By implementing the right strategies and continually monitoring and adapting to changes in the market, companies can successfully reduce costs and improve their competitive position in the plastic manufacturing industry.
How Deskera Can Assist You?
Deskera's integrated financial planning tools allow investors to better plan their investments and track their progress. It can help investors make decisions faster and more accurately.
Deskera Books enables you to manage your accounts and finances more effectively. Maintain sound accounting practices by automating accounting operations such as billing, invoicing, and payment processing.
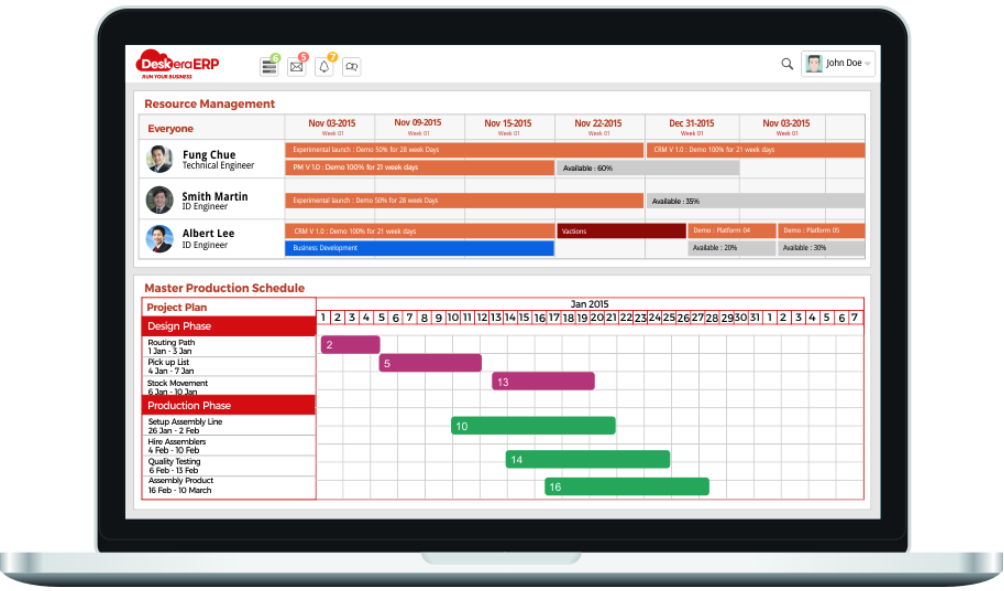
Deskera CRM is a strong solution that manages your sales and assists you in closing agreements quickly. It not only allows you to do critical duties such as lead generation via email, but it also provides you with a comprehensive view of your sales funnel.
Deskera People is a simple tool for taking control of your human resource management functions. The technology not only speeds up payroll processing but also allows you to manage all other activities such as overtime, benefits, bonuses, training programs, and much more. This is your chance to grow your business, increase earnings, and improve the efficiency of the entire production process.
Final Takeaways
We've arrived at the last section of this guide. Let's have a look at some of the most important points to remember:
- One effective way to cut costs in plastic manufacturing is by using recycled materials. Recycled materials are usually cheaper than virgin materials, and they also have a lower environmental impact. By incorporating recycled materials into the manufacturing process, manufacturers can reduce the cost of production and also appeal to eco-conscious consumers.
- When selecting materials for plastic manufacturing, it is essential to consider long-term costs. This involves looking at factors such as maintenance, repair, and replacement costs. By selecting materials that require less maintenance, last longer, and are easier to repair, manufacturers can reduce long-term costs significantly.
- Analyzing production processes and identifying areas for improvement can help reduce waste, reduce downtime, and improve efficiency. This can include using techniques like lean manufacturing and Six Sigma to streamline production processes.
- Implementing closed-loop systems can reduce costs associated with the procurement of new raw materials. Closed-loop systems involve recycling and reusing materials within the production process, reducing waste and the need for new materials.
- Engaging employees in energy-saving initiatives can help reduce energy costs. This can include training employees on energy-saving measures, providing incentives for energy savings, and encouraging employees to identify and report energy-saving opportunities.
- Training and development: Investing in employee training and development can help reduce labor costs associated with turnover and absenteeism. This can include providing training on production processes and safety procedures, as well as offering opportunities for career development and advancement.
- Supplier management: Implementing effective supplier management practices can help reduce costs associated with raw material procurement. This can include negotiating better pricing and terms with suppliers, implementing supplier performance monitoring, and supplier collaboration.
Related Articles
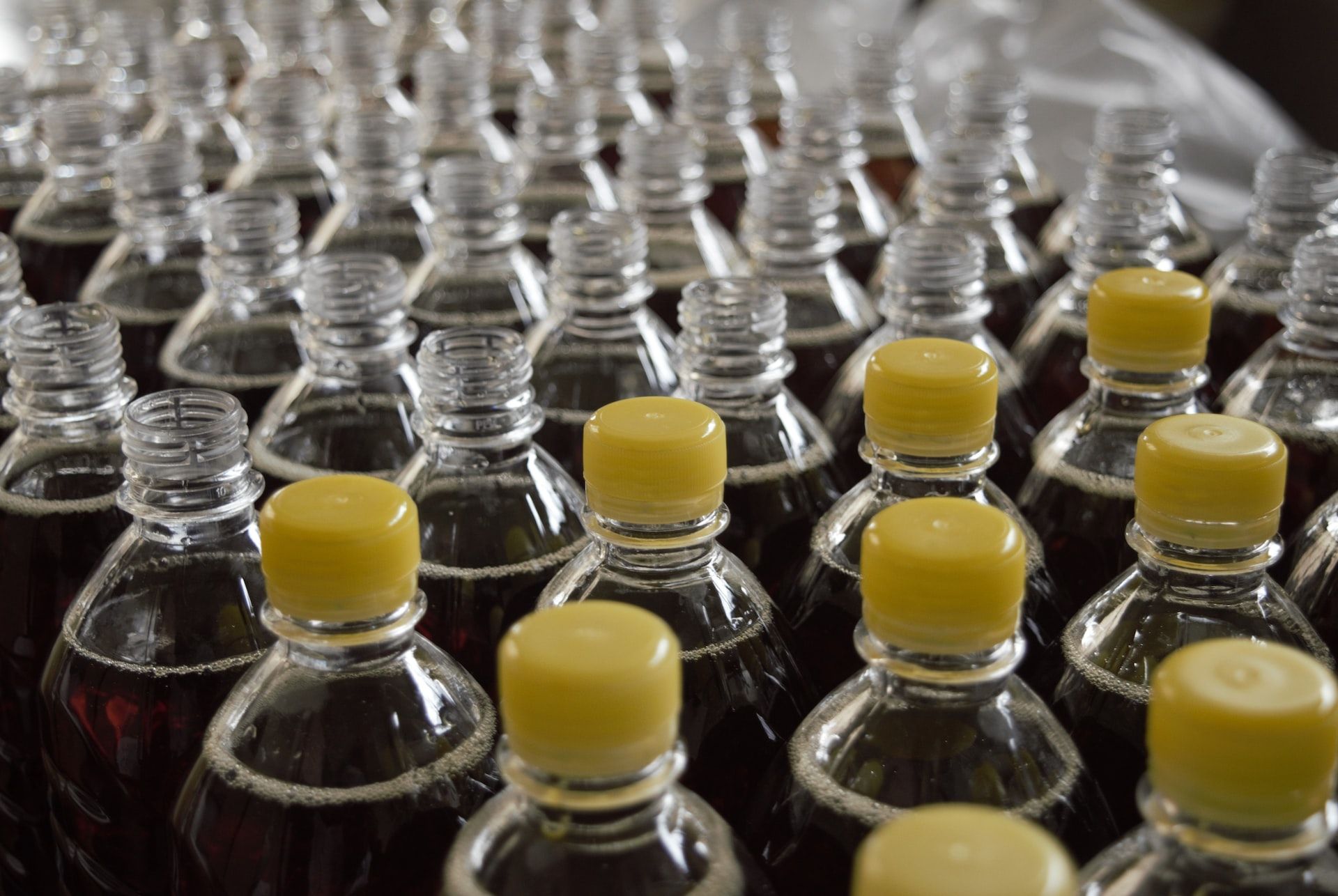
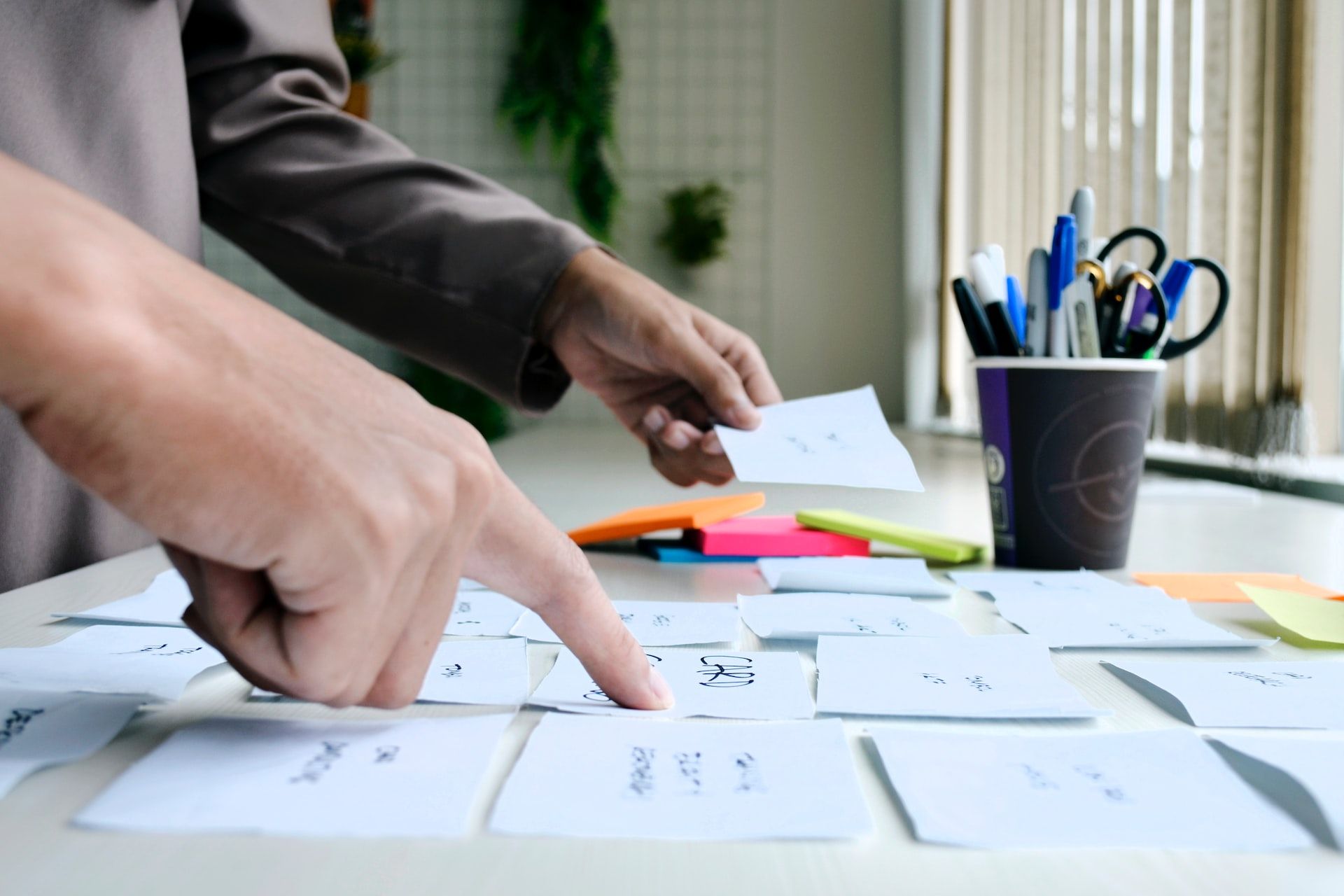
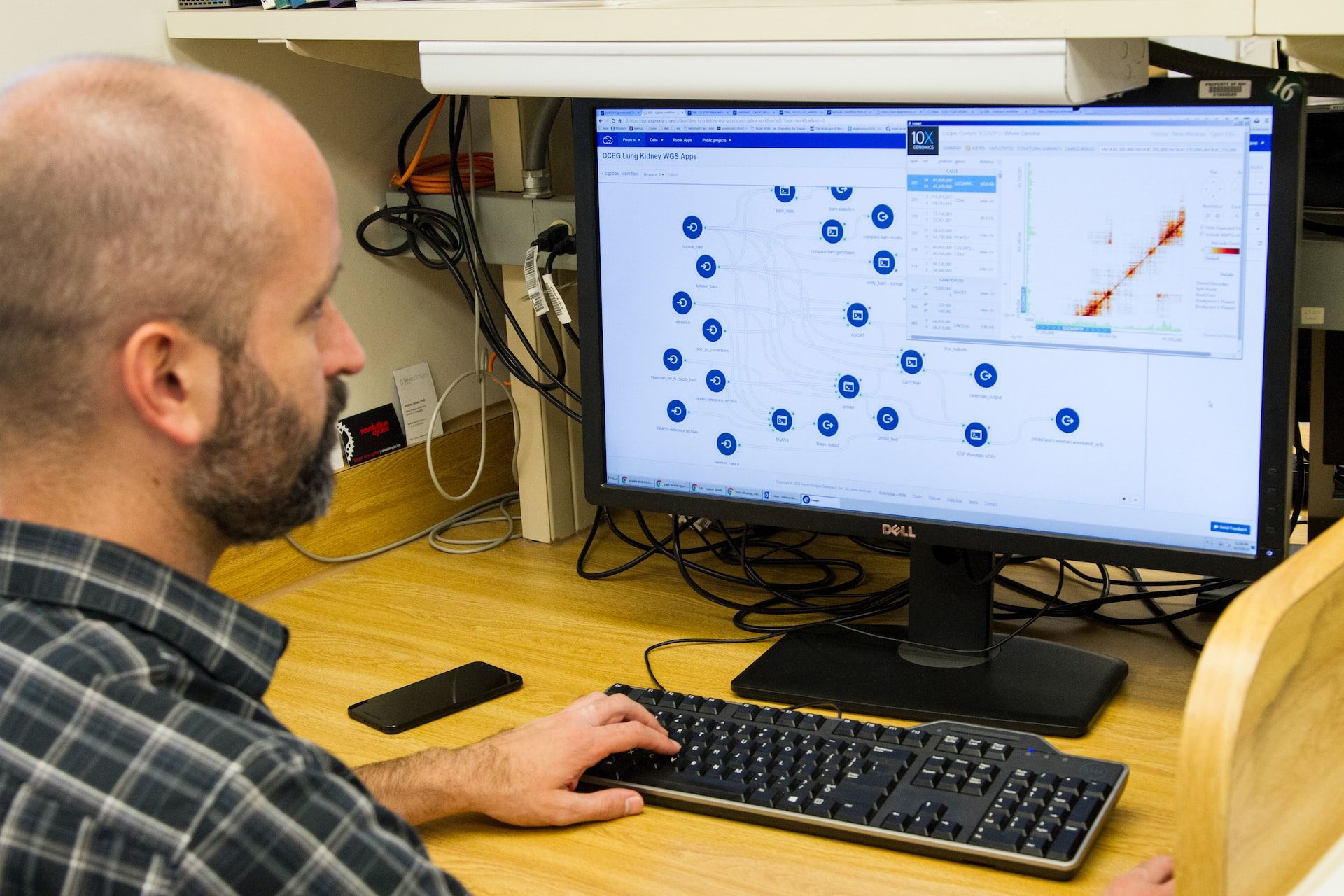

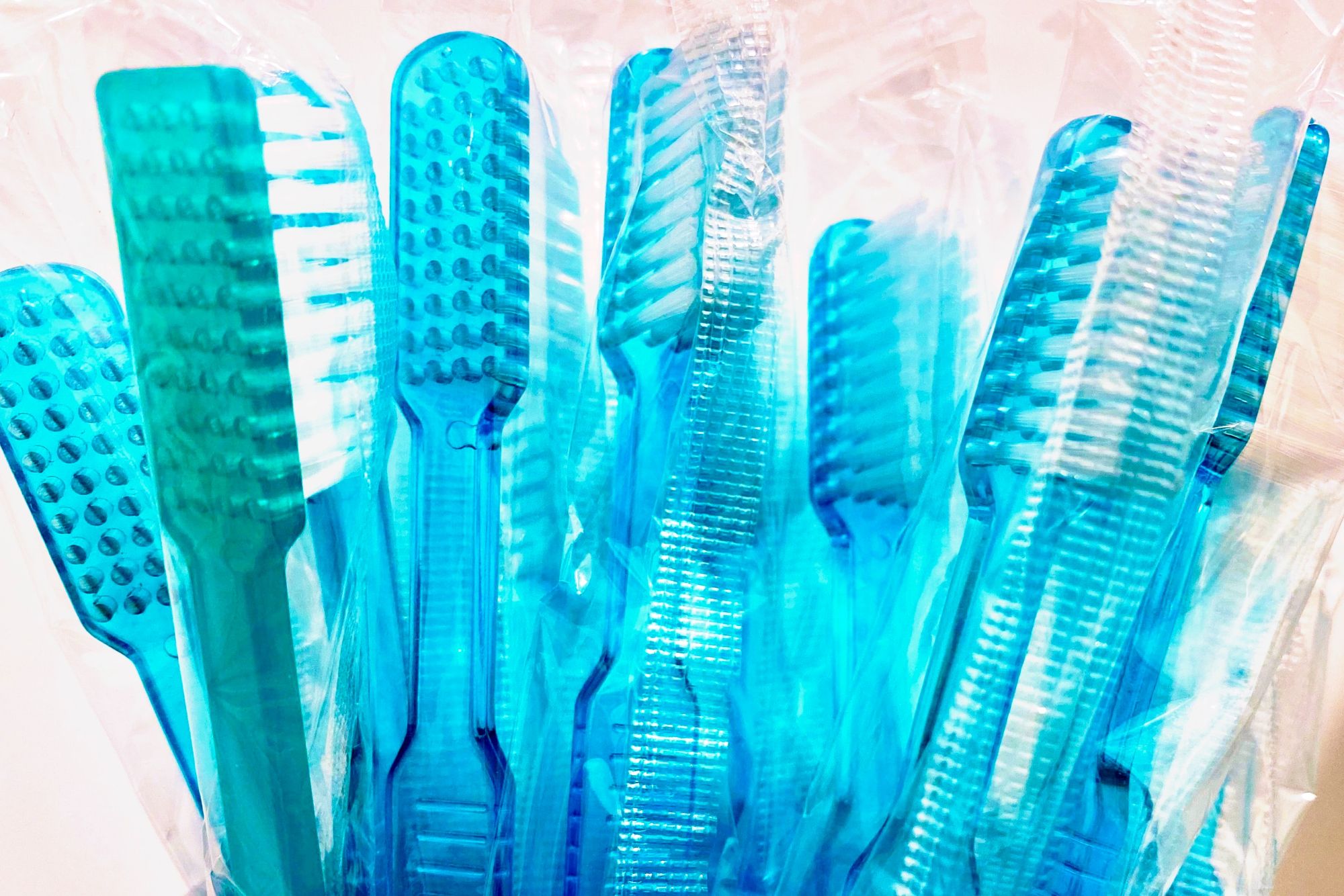