Innovative plastic manufacturing is essential for the future of the industry. It can reduce waste, improve sustainability, and even create new products. Companies should invest in new technologies and processes to ensure that their manufacturing processes remain innovative and sustainable. By doing so, they can help to create a better future for plastic manufacturing.
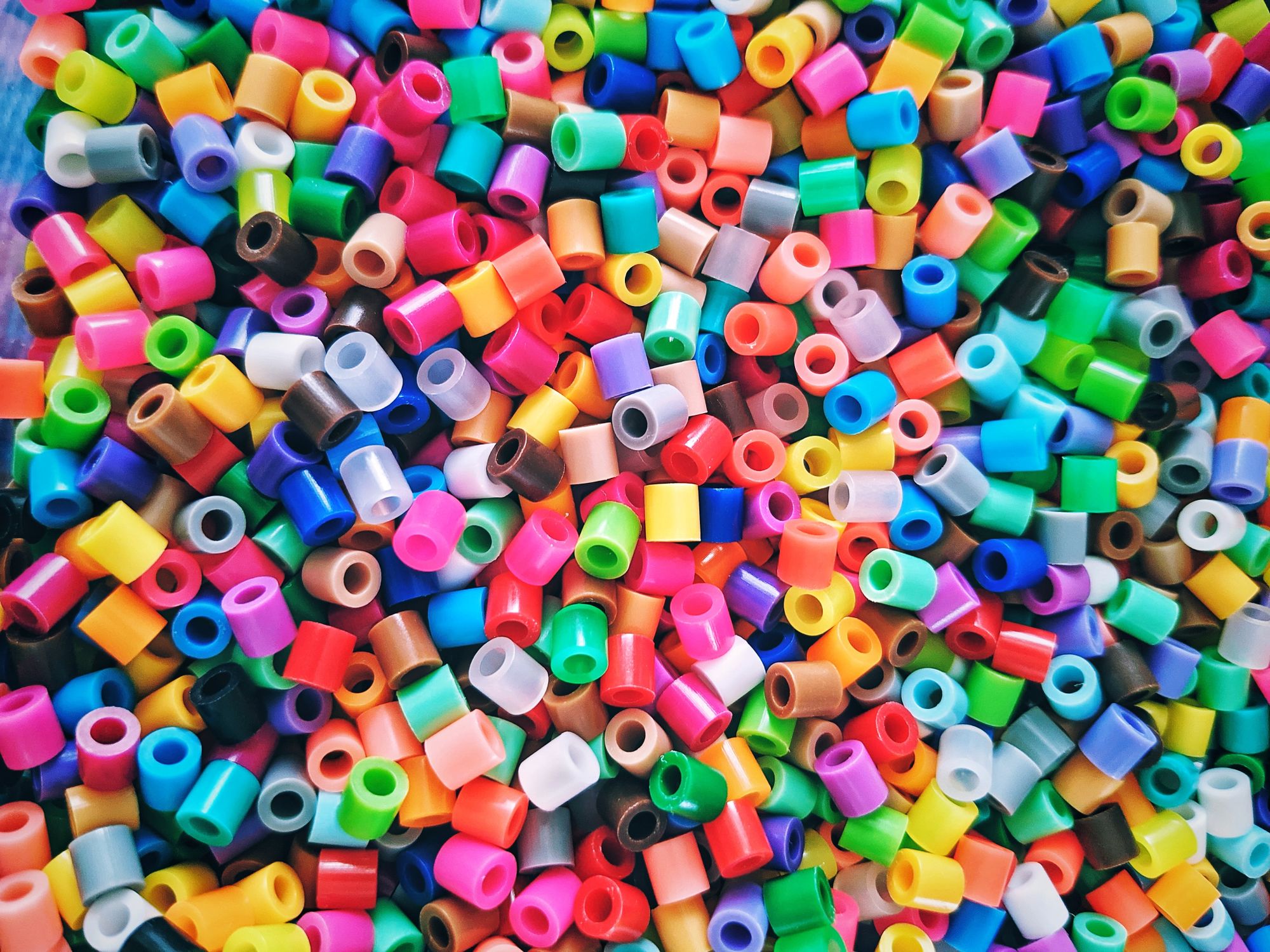
This article covers the following:
- Understanding Innovative Plastic Manufacturing
- Benefits of Innovative Plastic Manufacturing
- The Process of Innovative Plastic Manufacturing
- Different Types of Innovative Plastic Manufacturing
- Challenges of Innovative Plastic Manufacturing
- Safety Considerations for Innovative Plastic Manufacturing
- Innovative Plastic Manufacturing and the Environment
- Case Studies of Innovative Plastic Manufacturing
- The Future of Innovative Plastic Manufacturing
- How can Deskera assist you?
Understanding Innovative Plastic Manufacturing
The use of plastics in manufacturing has revolutionized the way we make products for an array of industries. Plastics offer unique advantages over traditional materials such as metals, wood, and ceramics, including extremely light weight, durability, and flexibility.
Manufacturers are constantly innovating with plastic materials in order to create new, more efficient products. Innovative plastic manufacturing is a process that involves the use of advanced technologies and materials to create unique products with specific characteristics or requirements.
By utilizing a variety of plastic materials, manufacturers can create products that meet the needs of their customers while also providing efficient and economic solutions. In order to understand the process of innovative plastic manufacturing, it is important to understand the various technologies and materials involved.
One of the most important innovations in plastic manufacturing is thermoplastic injection molding. This process is used to produce a variety of plastic products, from medical devices to consumer electronics.
Injection molding is a highly precise and efficient process that involves injecting molten plastic into a mold to create a product. This process is often used for complex parts with intricate details, as it allows for precise control of the product’s shape, size, and other characteristics.
Another important technology in plastic manufacturing is extrusion. This process involves forcing melted plastic through a die in order to form a product. This process is often used to create products with complex shapes, such as tubing and pipe.
Extrusion is also used to create products with a variety of surface finishes, such as smooth or textured. In addition to the technologies and processes used in plastic manufacturing, the materials used are also important.
Plastics can be manufactured from a variety of materials, including polyethylene, polypropylene, polycarbonate, and more. Each of these materials has its own unique properties, such as strength, flexibility, and chemical resistance.
Manufacturers must consider the properties of the material they are using and how it will affect the performance of the product they are creating. Innovative plastic manufacturing is a complex process that requires knowledge of the various technologies and materials involved.
By understanding the different processes and materials used in plastic manufacturing, manufacturers can create products that are both efficient and cost-effective. In addition, this knowledge can help to ensure that the products created are of the highest quality and meet the needs of their customers.
Benefits of Innovative Plastic Manufacturing
Over the past few decades, plastic manufacturing has become increasingly popular due to its versatility, cost-effectiveness, and durability. It’s used for a wide variety of applications, from packaging to construction materials, and it’s estimated that nearly 8 million metric tons of plastic are produced annually.
But with the rise of environmental concerns, many manufacturers are turning to innovative plastic manufacturing techniques to reduce their environmental impact. Innovative plastic manufacturing is a process that uses new materials and techniques to reduce waste and energy consumption during production.
By using innovative techniques such as 3D printing, injection molding, and extrusion, manufacturers can produce plastic products with greater efficiency and accuracy. This not only reduces costs but also decreases the amount of energy and resources needed to produce the same quantity of plastic products.
Innovative plastic manufacturing also has a number of other benefits. For example, the use of 3D printing and injection molding allows manufacturers to produce plastic products with more intricate designs, which can be used to create unique and eye-catching products.
Additionally, 3D printing and injection molding allow for a greater degree of customization, so manufacturers can create products that are tailored to their customer’s specific needs.
Innovative plastic manufacturing techniques also offer a number of environmental benefits. For example, 3D printing and injection molding use significantly less energy and resources than traditional methods, and they can reduce the amount of plastic waste that is produced.
Additionally, 3D printing and injection molding can produce plastic parts and products with a higher degree of accuracy and precision than traditional methods, reducing the amount of scrap and waste produced during production.
Overall, innovative plastic manufacturing is an important step in the evolution of the plastic industry. By using more efficient and accurate production methods, manufacturers can reduce their environmental impact, create unique and eye-catching products, and reduce costs.
With the continued advancement of plastic manufacturing technologies, manufacturers will be able to create even more innovative solutions to meet the needs of their customers.
The Process of Innovative Plastic Manufacturing
The process of innovative plastic manufacturing is an ever-changing field that is constantly evolving. With new technologies and materials, it is possible to produce products of higher quality and durability than ever before.
In order to stay ahead of the competition and create products that stand out, companies must continually innovate and develop new processes and techniques. In this blog post, we'll discuss the process of innovative plastic manufacturing and how it can help your business.
First and foremost, manufacturers must have a comprehensive understanding of the material they're working with. This includes knowing its physical properties, such as its melting point, tensile strength, and chemical composition.
By having a thorough understanding of the material, manufacturers can then consider the best methods for forming, molding, and extruding the plastic into the desired shape and size.
Once the material is understood, the next step is to select the appropriate machinery and tools for the job. This includes selecting the right size and type of injection molding machines, extruders, and other tools.
It's important to select the machines that are best suited for the job and that can handle the product's requirements. The plastic manufacturing process also involves the use of various chemicals and additives.
These are used to shape and form the plastic into the desired shape and size. They can also be used to add colors and textures to the plastic. In some cases, these chemicals and additives may need to be specially formulated for the product in order to achieve the desired results.
The next step in the process is the development of a prototype. This is a physical representation of the product that can be tested and evaluated before the final product is released.
Once the prototype is approved, the company can then move on to the production phase. During production, the plastic is typically melted and then molded or extruded into the desired shape and size.
Finally, the product is put through a series of tests to ensure that it meets all of the required standards. This may include testing for wear and tear, strength, and other factors.
If the product passes all of these tests, it is ready to be released to the public. Innovative plastic manufacturing is an exciting and ever-evolving field. By understanding the process and selecting the right materials, tools, and chemicals, manufacturers can create products that are both durable and attractive. With the right combination of innovation and quality, manufacturers can ensure that their products stand out from the competition.
How to Differentiate Plastics with Innovative Manufacturing?
Making plastics is a highly involved process and it requires lots of creativity and innovation to differentiate your products from the competition. As a plastics manufacturer, you must look for ways to make your plastics unique, regardless of the product you’re producing. Here are some tips on how to differentiate your plastics with innovative manufacturing processes:
Use the Latest Technologies
Invest in the latest technologies to make sure that your plastics are of the highest quality. Use 3D printing, advanced injection molding techniques, and advanced polymer-based materials to create custom designs and intricate shapes.
Utilize Sustainable Manufacturing Practices
Invest in sustainable manufacturing practices to reduce your environmental impact. Invest in renewable energy sources, use recycled materials, and create biodegradable plastics.
Develop Customized Solutions
Create customized solutions to meet the needs of your customers. Develop bespoke products and tailor them to each customer’s exact needs, ensuring that you stand out from the competition.
Create Novel Material
Create novel materials by combining different types of plastics. Develop new, innovative materials that offer superior performance or look more attractive.
Incorporate Branding
Incorporate branding into the manufacturing process to make your products stand out from the competition. Branding can be applied to the finished product, or to the actual manufacturing process.
Utilize Automation
Utilize automation to reduce costs and improve efficiency. Automated processes can help you produce high-quality products faster and with fewer resources. By implementing these strategies, you can ensure that your plastics stand out from the competition with innovative manufacturing processes.
Invest in the latest technologies, create customized solutions, develop novel materials, incorporate branding, and utilize automation to make sure that your products are top-notch. By doing so, you will be able to differentiate your plastics and ensure that your customers are getting the best products possible.
Different Types of Innovative Plastic Manufacturing
Plastic manufacturing is a rapidly growing industry that’s constantly evolving. Thanks to new technologies and innovative processes, manufacturers are now able to produce a wide range of products that are strong, lightweight, and cost-effective.
But there’s more to plastic manufacturing than just the material itself. Different types of innovative manufacturing processes can give plastic products even more impressive features. Here’s a closer look at the different types of innovative plastic manufacturing methods:
Injection Molding
Injection molding is a process in which molten plastic is injected into a mold, where it cools and takes the shape of the mold. This is one of the most common methods of plastic manufacturing, and it’s ideal for producing complex parts with tight tolerances. It’s also fast, efficient, and cost-effective.
Blow Molding
Blow molding is a method of plastic manufacturing that involves extruding molten plastic into a tube, which is then closed and sealed. This tube is then inserted into a mold, and air pressure is used to blow the plastic into the shape of the mold. This process is usually used to create hollow objects like bottles and containers.
Extrusion
Extrusion is a process in which plastic is melted and forced through a die. This creates a continuous piece of plastic with a uniform cross-section. Extrusion is often used to create plastic tubing, pipes, and sheets.
Rotational Molding
Rotational molding is a process in which a mold is filled with plastic powder and rotated on two axes. Heat is then applied, causing the powder to melt and adhere to the walls of the mold. This process is often used to create parts with complex shapes and hollow cavities.
Thermoforming
Thermoforming is a process in which a sheet of plastic is heated until it’s malleable and then formed into a specific shape using a vacuum. This method is often used to create parts with intricate details.
Vacuum Forming
Vacuum forming is similar to thermoforming, but instead of using a vacuum to shape the plastic, it’s formed using negative pressure. This allows manufacturers to create parts with very precise dimensions.
These are just a few of the innovative plastic manufacturing processes that are available. By taking advantage of these methods, manufacturers are able to create products that are stronger, more lightweight, and more cost-effective than ever before.
Challenges of Innovative Plastic Manufacturing
Plastic manufacturing is an important industry that has revolutionized the way we make and use products. From medical devices to consumer goods, plastic is ubiquitous in our lives.
But plastic manufacturing is also facing many challenges that must be addressed in order to ensure its continued success. One of the biggest challenges of innovative plastic manufacturing is the need for new materials that meet the demands of an ever-changing market.
As consumer preferences and industry standards evolve, manufacturers must find ways to create new and improved products that are both cost-effective and environmentally friendly.
This requires research, development, and testing of new polymers and materials, which can be a costly and time-consuming process. Another challenge is meeting the demands of sustainability.
As people become increasingly conscious of their environmental footprint, manufacturers must find ways to reduce the amount of plastic they use and the waste they produce.
This includes finding ways to recycle more plastic and reduce the amount of plastic that ends up in landfills. Finally, manufacturers must also stay ahead of trends and keep up with the latest technology.
Innovations in 3D printing, precision machining, and data-driven design can help manufacturers create more efficient and effective products. These investments can be costly, but they are essential for staying competitive in an ever-evolving market. Innovative plastic manufacturing is a complex process that requires a significant investment of resources.
But by addressing these challenges, manufacturers can create better products, reduce their environmental impact, and stay ahead of the competition. With the right strategies in place, plastic manufacturing can remain a viable and profitable industry for years to come.
Safety Considerations for Innovative Plastic Manufacturing
Plastic manufacturing is one of the most innovative, cost-effective, and versatile processes in the modern industrial world. However, the production of plastic products can be dangerous and hazardous to both workers and the environment. Here are five safety considerations that should be taken into consideration when manufacturing plastic products:
Adequate Ventilation
Proper ventilation is essential to reduce the risk of hazardous fumes and airborne particles. Proper ventilation should include adequate air intake, exhaust systems, and filters to remove hazardous materials.
Protective Equipment
Workers should be provided with personal protective equipment (PPE) such as safety glasses, face shields, respirators, and protective clothing.
Process Controls: Temperature, pressure, and other process parameters should be carefully monitored and controlled to reduce the risk of accidents and improper product formation.
Quality Controls
Quality controls should be implemented to ensure that the plastic products manufactured meet the required safety standards.
Training
All workers should be trained on the safe and proper use of plastic manufacturing equipment. By following these safety considerations, manufacturers can ensure a safe and efficient production process.
Additionally, manufacturers should ensure that all employees are aware of the safety protocols and that they are regularly monitored and updated. This will help to reduce the risk of accidents and ensure that the plastic products manufactured meet the highest standards.
Innovative Plastic Manufacturing and the Environment
Plastic is a popular material used in a variety of industries. It is relatively inexpensive, lightweight, and durable, making it an ideal material for many applications. However, plastic has a dark side when it comes to its environmental impact.
The production and disposal of plastic contribute to air and water pollution, as well as landfill waste. Fortunately, innovative plastic manufacturing processes are being developed to reduce the environmental footprint of this ubiquitous material.
One of the most promising advancements in plastic manufacturing is the use of recycled materials. Plastics can be recycled and reused in many ways, from creating new packaging materials to creating new products.
By using recycled materials, the amount of plastic that is sent to landfills is reduced, and the resources needed to create new plastics from scratch are also reduced. Another way to reduce the environmental impact of plastic production is to use biodegradable plastics.
Biodegradable plastics are made from natural materials like corn starch, vegetable oil, and other organic materials. These biodegradable plastics break down much faster than traditional plastics, reducing the amount of plastic waste that ends up in landfills.
Innovative technologies are also being developed to make plastic production more efficient and sustainable. One example is the use of 3D printing technology to create plastic components.
3D printing uses very little energy and results in little to no waste. This technology is being used to create medical devices, automotive parts, and other everyday objects. Finally, new methods of manufacturing plastic are being developed that are more energy-efficient and less wasteful.
For example, some plastic manufacturers are now using more efficient injection molding machines. These machines produce plastic parts with less energy and fewer emissions, resulting in a smaller environmental footprint.
Innovative plastic manufacturing processes are helping to reduce the environmental impact of plastic production. By using recycled materials, biodegradable plastics, 3D printing technology, and more efficient injection molding machines, plastic manufacturers can produce plastic products that are more sustainable and environmentally friendly. As these technologies continue to improve, plastic production can become a more sustainable industry.
Case Studies of Innovative Plastic Manufacturing
In recent years, plastic manufacturing has come a long way. From being a material used mainly for packaging, it has become a versatile material that can be used in various industries ranging from automotive to medical to consumer goods and many more. In this blog, we will be taking a look at some of the most innovative case studies of plastic manufacturing.
Automotive Industry
One of the most innovative plastic manufacturing case studies is the use of plastic injection molding in the automotive industry. This type of technology is used to create parts for cars, vans, trucks, and even buses.
Through their use of plastic injection molding, automakers are able to create intricate parts that are lightweight, durable, and cost-effective. This type of technology has enabled automakers to create parts that meet strict safety regulations, while also being able to reduce the weight of the car, resulting in improved fuel efficiency.
Medical Industry
Plastic manufacturing has also revolutionized the medical industry. Through the use of plastic injection molding, medical device manufacturers are able to create intricate parts for medical devices such as artificial limbs, implants, and denture appliances.
This type of technology has allowed medical device manufacturers to create parts that are both lightweight and durable, while also being able to create parts that are extremely precise and accurate.
This type of technology has enabled medical device manufacturers to create parts that meet exact specifications and are able to perform at the highest level.
Consumer Goods
Plastic manufacturing has also been used to create a variety of consumer goods. Through the use of plastic injection molding, manufacturers are able to create intricate parts for toys, sporting goods, kitchenware, and even mobile phones.
This type of technology has enabled manufacturers to create parts that are both lightweight and durable, while also being able to create parts that are extremely precise and accurate.
This type of technology has enabled manufacturers to create parts that meet the highest standards in terms of performance and quality. These are just some of the many case studies of plastic manufacturing that showcase its innovative capabilities.
From the automotive industry to the medical industry to consumer goods, plastic manufacturing has revolutionized the way we produce products. Through its use of precision and accuracy, plastic manufacturing has enabled manufacturers to create parts that are both lightweight and durable while also being able to create parts that meet exact specifications and are able to perform at the highest level.
By taking a look at these case studies, it is evident that plastic manufacturing has revolutionized the way we produce products and has enabled manufacturers to create parts that are both lightweight and durable while also being able to create parts that meet exact specifications and are able to perform at the highest level.
The Future of Innovative Plastic Manufacturing
The plastics industry has been in existence for centuries, but the last few decades have seen an incredible surge in the use of plastic products. This is largely due to the fact that plastic is incredibly versatile, durable, and cost-effective.
It is also incredibly easy to mold into virtually any shape, making it a great option for manufacturers of all kinds. As technology continues to advance, plastic manufacturers are finding new and innovative ways to use plastic to create products that are both useful and aesthetically pleasing.
As the world continues to become more focused on sustainability, the plastics industry has had to adapt to meet the demand for more environmentally friendly products. Fortunately, plastic manufacturers are rising to the challenge.
In recent years, there have been tremendous advancements in the development of bioplastics, which are made from renewable plant-based materials such as corn and sugarcane.
These materials are not only more sustainable than traditional plastics, they are also stronger and more durable. This is just one of the many ways that the plastics industry is working to become more eco-friendly.
In addition to bioplastics, plastic manufacturers are also turning to 3D printing technology to create complex and intricate designs. 3D printing allows manufacturers to create products with intricate detail that would otherwise be impossible to achieve.
This technology is being used to create everything from medical devices to toys and even jewelry. This is just one way that plastic manufacturers are adapting to the changing needs of consumers.
The future of innovative plastic manufacturing looks to be bright. As technology continues to advance and sustainability becomes more of a priority, manufacturers will continue to find new and innovative ways to use plastic.
From bioplastics to 3D printing, the possibilities are almost endless. As long as manufacturers continue to innovate and create new uses for plastic, the possibilities are endless. So, if you’re looking for a material that can help you create something unique and useful, plastic is definitely the way to go.
Resources for Learning More About Innovative Plastic Manufacturing
Innovative plastic manufacturing is an ever-evolving field of technology, with new processes and materials being developed all the time. As a result, there is a plethora of resources available for those looking to learn more about this area.
Whether you're a manufacturing expert or a curious bystander, these resources will help you stay informed about the latest developments in plastic manufacturing. First and foremost, online resources are a great way to get up-to-date information on the plastic manufacturing industry.
Sites such as PlasticsToday.com provide useful articles, videos, and other resources related to the industry. Additionally, the Plastics Industry Association offers an online library that provides resources such as industry news, regulations, and more.
For those interested in gaining a deeper understanding of plastic manufacturing, academic journals are a great place to start. Journals such as Plastics Engineering and Plastics Technology provide research-based articles on the latest trends and developments in the field. Additionally, conferences and seminars provide great opportunities to learn from industry experts.
For those looking for hands-on experience, there are a number of educational programs and certifications available. Many universities offer courses and degrees in plastic engineering and manufacturing, and some specialized schools and technical institutes offer diplomas in plastic fabrication and injection molding.
Additionally, there are numerous certifications available from organizations such as the American Mold Builders Association and the Society of Plastics Engineers. Finally, many manufacturers offer free educational materials and resources on their websites.
Companies such as Dow, DuPont, and BASF provide detailed technical information and resources on the plastic manufacturing process and materials. Additionally, these companies often host webinars and other events to educate the public on the latest developments in the industry.
In conclusion, there are numerous resources available for those looking to learn more about innovative plastic manufacturing. From online resources and academic journals to educational programs and certifications, to manufacturer materials, there is plenty of information out there to help you stay informed and up-to-date.
How Can Deskera Assist You?
As a manufacturer, you must keep track of your inventory stock. The condition of your inventory has a direct impact on production planning. It also has a direct impact on people and machinery use and capacity utilization.
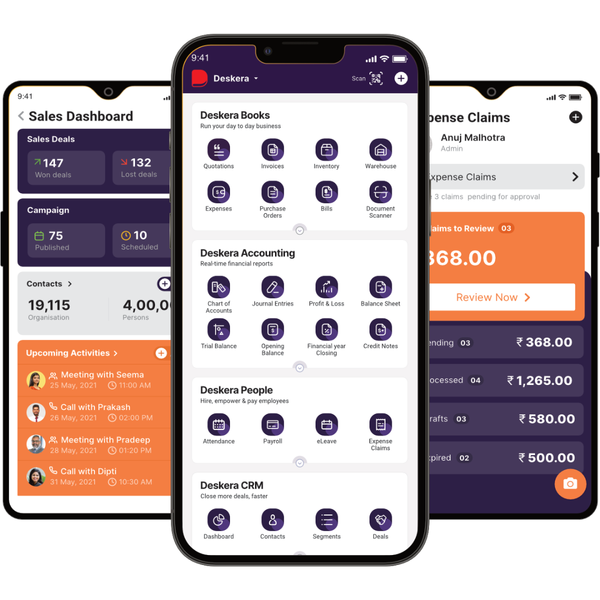
Deskera MRP is the one tool that lets you do all of the above. With Deskera, you can:
- Control production schedules
- Compile a Bill of Materials
- Produce thorough reports
- Make your dashboard
Deskera ERP is a complete solution that allows you to manage suppliers and track supply chain activity in real time. It also allows you to streamline a range of other company functions.
Deskera Books allows you to manage your accounts and finances better. It helps maintain good accounting standards by automating billing, invoicing, and payment processing tasks.
Deskera CRM is a powerful tool that organizes your sales and helps you close deals rapidly. It enables you to perform crucial tasks like lead generation via email and gives you a comprehensive view of your sales funnel.
Deskera People is a straightforward application for centralizing your human resource management activities. Not only does the technology expedite payroll processing, but it also helps you to handle all other operations such as overtime, benefits, bonuses, training programs, and much more.
Key Takeaways:
- The use of plastics in manufacturing has revolutionized the way we make products for an array of industries.
- Plastic manufacturing is an important industry that has revolutionized the way we make and use products. From medical devices to consumer goods, plastic is ubiquitous in our lives.
- The production and disposal of plastic contribute to air and water pollution, as well as landfill waste.
- One of the most innovative plastic manufacturing case studies is the use of plastic injection molding in the automotive industry.
- As the world continues to become more focused on sustainability, the plastics industry has had to adapt to meet the demand for more environmentally friendly products.
Related Articles:
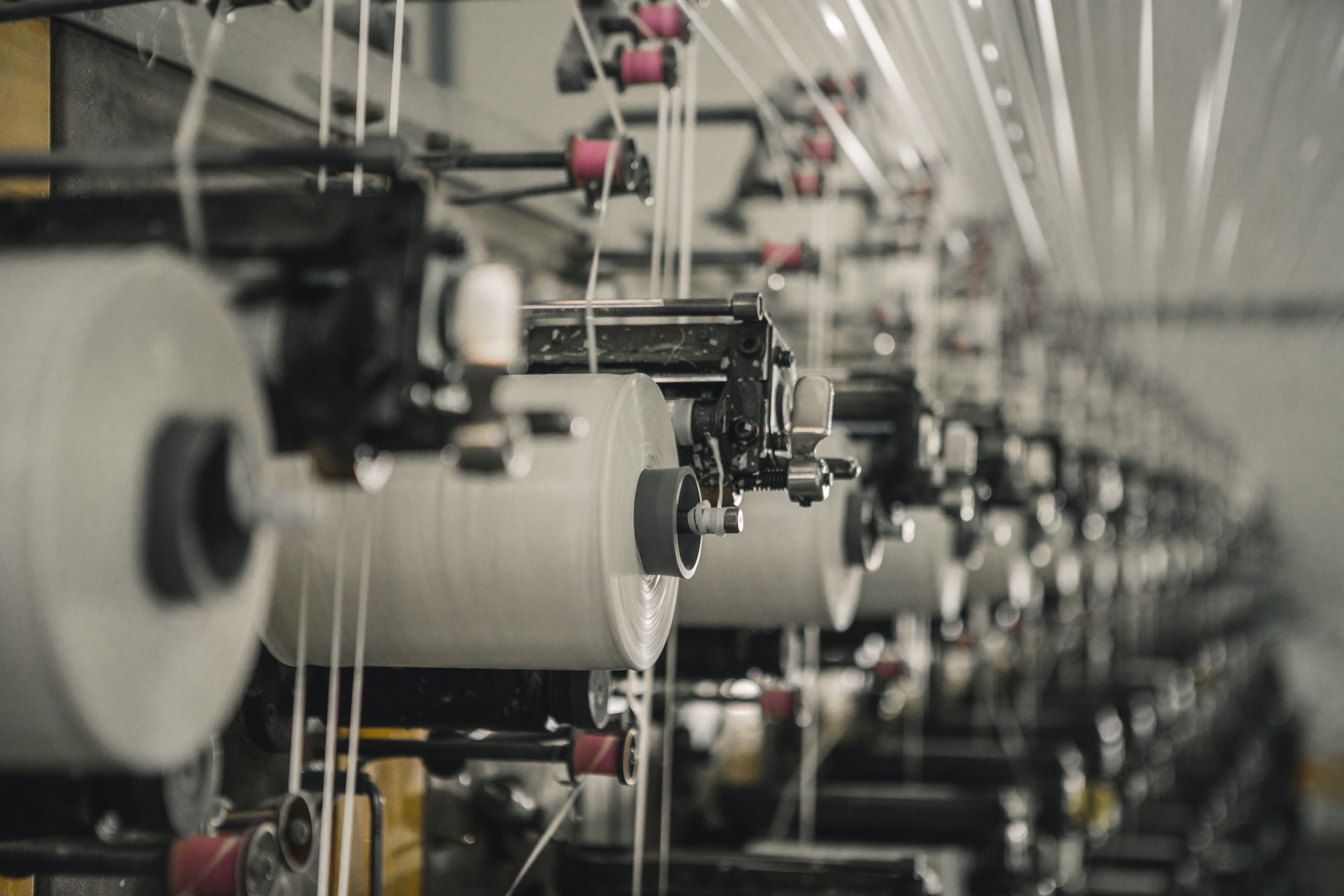
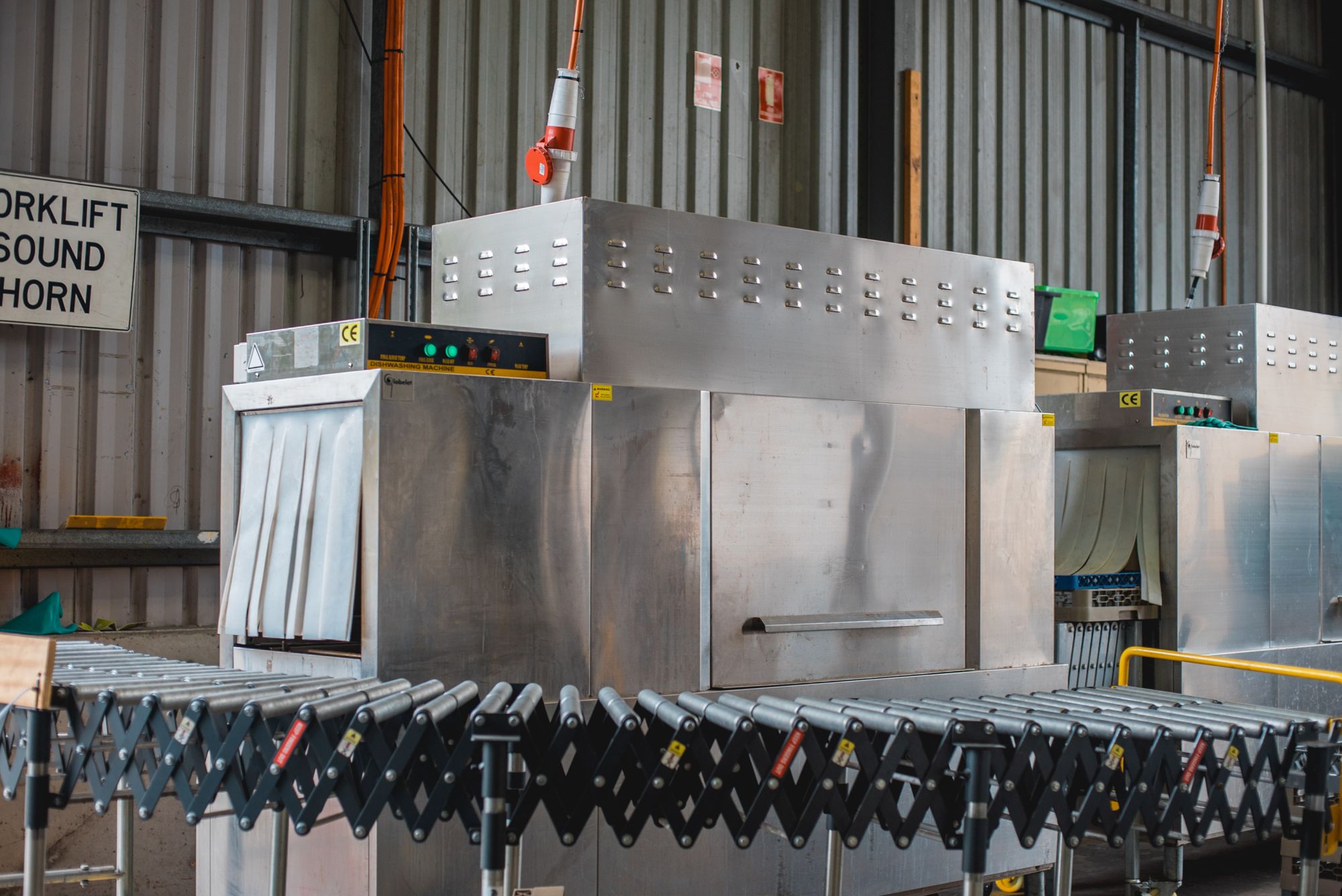
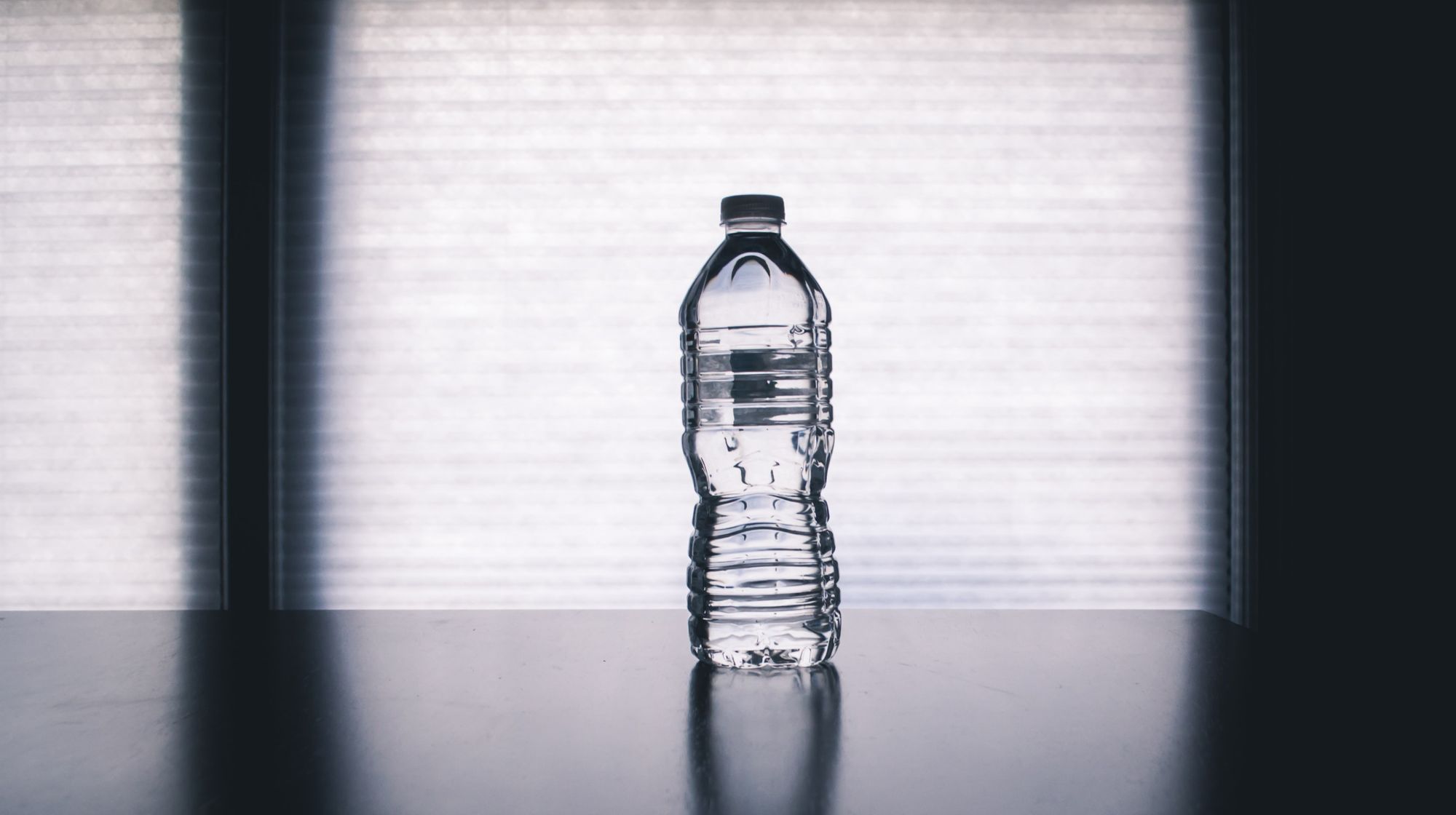