How can you sort out the right plastic for your manufacturing process?
Selecting the right plastic can be confusing because there are a lot of factors to consider. The type of plastics you use, as well as the process you're using, will all play a role in how your plastic is used. Therefore, it is quite important to select the right plastic for your manufacturing process.
In today’s guide, we’ll cover all aspects related to selecting the right plastic for manufacturing process. Let’s take a look at the table of content below:
- Importance of Selecting the Right Plastic for Manufacturing
- Properties of Plastics that Affect Manufacturing
- Examples of Common Plastics and their Properties
- Common Plastic Manufacturing Processes
- Influence of Manufacturing Processes on Plastic Manufacturing
- Important Factor to Consider When Selecting Plastic for Manufacturing
- How Cost Can Influence Plastic Selection and Examples of Cost-Saving Measures
- Environmental Impact of Plastics and Examples of Environmentally Friendly Plastics and Practices
- Successful Plastic Selection
- Tips to Keep in Mind When Selecting the Right Plastic for your Manufacturing Process
- Wrapping Up
- How Deskera Can Assist You?
Importance of Selecting the Right Plastic for Manufacturing
Selecting the right plastic for manufacturing is essential for several reasons. Firstly, it ensures that the product will perform as intended and meet the necessary safety standards.
Secondly, it helps to reduce manufacturing costs and waste by minimizing the risk of product failure and the need for rework or replacement. Thirdly, selecting the right plastic can also reduce the environmental impact of the product by ensuring that it can be recycled or disposed of properly.
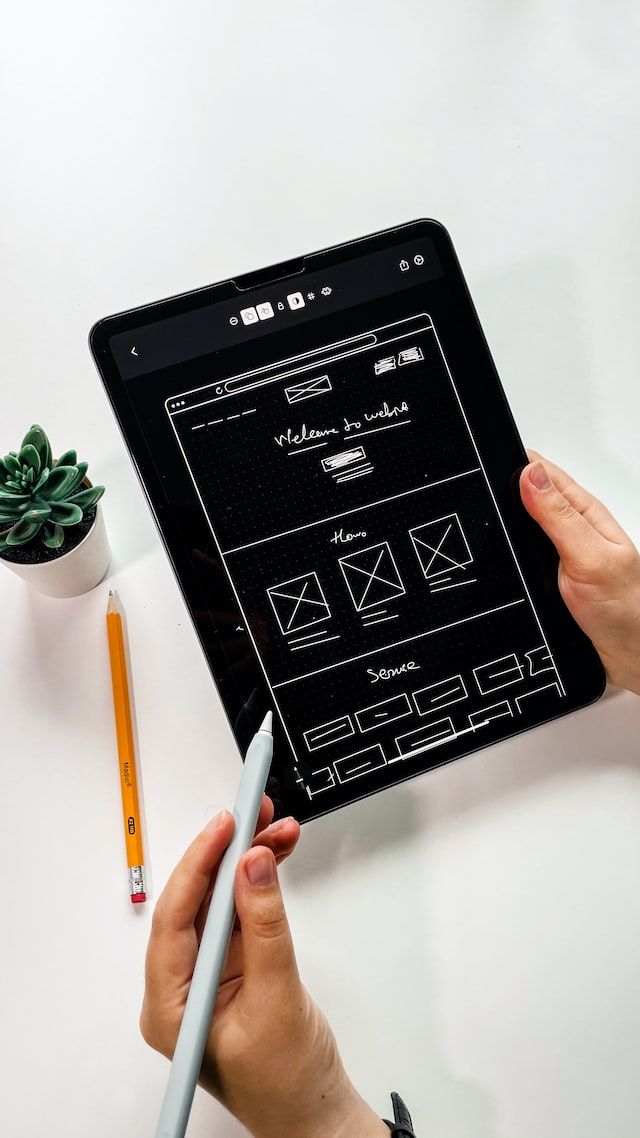
In addition to these benefits, selecting the right plastic for manufacturing can also improve the overall quality of the product, increase its lifespan, and enhance its appearance. By carefully considering the properties of plastics and the manufacturing processes used, manufacturers can create products that are stronger, more durable, and more aesthetically appealing.
Therefore, selecting the right plastic for manufacturing is crucial for achieving success in any manufacturing process. It can save time, money, and resources while ensuring that products are safe, reliable, and environmentally friendly.
Properties of Plastics that Affect Manufacturing
Plastics have a wide range of properties that can affect the manufacturing process. These properties include:
Melting Point:
The melting point of a plastic material determines the temperature at which it can be melted and molded. This property is important for determining the appropriate manufacturing process for a particular plastic.
Viscosity:
Viscosity is a measure of a plastic's resistance to flow. This property is important for injection molding and extrusion processes where the plastic needs to be melted and then pushed through a mold or die.
Hardness:
The hardness of a plastic material determines its ability to withstand wear and tear. This property is important for manufacturing products that need to be durable and long-lasting.
Flexibility:
The flexibility of a plastic material determines its ability to bend or stretch without breaking. This property is important for manufacturing products that need to be able to withstand some degree of deformation.
Chemical Resistance:
The chemical resistance of a plastic material determines its ability to resist damage from chemicals or solvents. This property is important for manufacturing products that will be used in environments where exposure to chemicals is likely.
UV Resistance:
The UV resistance of a plastic material determines its ability to resist damage from exposure to sunlight. This property is important for manufacturing products that will be used outdoors or in environments with high levels of sunlight.
Transparency:
The transparency of a plastic material determines its ability to transmit light. This property is important for manufacturing products that need to be transparent or translucent.
Ultimately, understanding the properties of plastics is crucial for selecting the right material for a manufacturing process. Each property affects the performance and durability of the final product and should be carefully considered before making a decision.
Examples of Common Plastics and their Properties
There are many different types of plastics available, each with their own unique properties. Following, we've discussed some crucial examples of common plastics and their properties:
Polyethylene (PE): This plastic is known for its toughness, flexibility, and chemical resistance. It is commonly used in packaging, toys, and outdoor furniture.
Polypropylene (PP): This plastic is lightweight, flexible, and resistant to heat and chemicals. It is commonly used in packaging, automotive parts, and household appliances.
Polyvinyl Chloride (PVC): This plastic is known for its durability and resistance to moisture and chemicals. It is commonly used in construction materials, electrical cables, and medical devices.
Polystyrene (PS): This plastic is lightweight and rigid, making it a good choice for packaging materials and disposable cups and utensils.
Acrylonitrile Butadiene Styrene (ABS): This plastic is strong, rigid, and impact-resistant, making it a popular choice for automotive parts, toys, and electronic housings.
Polycarbonate (PC): This plastic is known for its high impact resistance and transparency, making it a good choice for safety glasses, automotive parts, and electronic housings.
Nylon (PA): This plastic is known for its strength and durability, making it a good choice for automotive parts, electrical components, and industrial applications.
These are just a few examples of common plastics and their properties. When selecting a plastic for manufacturing, it is important to consider the specific properties needed for the intended application.
Common Plastic Manufacturing Processes
There are several common plastic manufacturing processes used to create plastic products. Here is an overview of some of the most common processes:
Injection Molding: Injection molding is the most common plastic manufacturing process. It involves melting plastic pellets and injecting them into a mold to create a specific shape. Injection molding is used to create a wide range of products, from small toys to large automotive parts.
Extrusion: Extrusion is a process where plastic is melted and forced through a die to create a specific shape. This process is commonly used to create plastic pipes, tubing, and sheets.
Blow Molding: Blow molding is used to create hollow plastic products, such as bottles and containers. The process involves melting plastic and blowing air into it to create the desired shape.
Rotational Molding: Rotational molding is used to create large, hollow plastic products, such as tanks and playground equipment. The process involves melting plastic in a mold and rotating it slowly to evenly distribute the plastic and create the desired shape.
Thermoforming: Thermoforming is used to create thin plastic products, such as food packaging and disposable cups. The process involves heating plastic sheets and molding them into the desired shape.
Compression Molding: Compression molding is used to create large, high-strength plastic products, such as automotive parts and electrical components. The process involves placing plastic material in a mold and compressing it under heat and pressure.
Each plastic manufacturing process has its own unique advantages and disadvantages. The process used depends on the desired properties of the final product, the volume of production, and the cost of manufacturing.
Influence of Manufacturing Processes on Plastic Manufacturing
The choice of plastic material for a particular manufacturing process is influenced by several factors related to the process. Following, we’ve discussed some crucial ways that the manufacturing process can influence plastic selection:
- Molding Process: Different plastics have different melting points, flow properties, and viscosities. The manufacturing process used to create a product will determine the temperature and pressure needed to melt and mold the plastic. Some plastics, like polyethylene, are easily molded using low-pressure injection molding techniques, while others, like polycarbonate, require high-pressure injection molding.
- Part Geometry: The shape and complexity of the product being manufactured will also influence the choice of plastic material. Some plastics, like polystyrene, are better suited for creating products with simple shapes, while others, like nylon, can be molded into complex shapes and structures.
- Production Volume: The volume of production is another important factor to consider when selecting a plastic material. High-volume production runs may require a plastic that is more cost-effective or easier to process, while lower volume runs may allow for more specialized or higher-performance plastics.
- Cost: The cost of the plastic material is also a factor to consider. Some plastics, like polyethylene, are relatively inexpensive and widely available, while others, like polycarbonate, are more expensive due to their unique properties and production processes.
- Performance Requirements: The performance requirements of the final product will also influence plastic selection. For example, products that require high strength and durability may require a more rigid plastic like acrylonitrile butadiene styrene (ABS), while products that require flexibility may require a more pliable plastic like polypropylene.
Overall, the choice of plastic material for a particular manufacturing process is a balance between the desired properties of the final product, the constraints of the manufacturing process, and the cost of production.
Important Factor to Consider When Selecting Plastic for Manufacturing
Following, we’ve discussed some important factors to consider while selecting plastic for manufacturing. Also, we’ve discussed how each factor influences the choice of plastic. Let’s learn:
Physical Properties:
The physical properties of the plastic play a crucial role in determining the choice of plastic for manufacturing. The stiffness, strength, flexibility, and temperature resistance of the plastic must be matched with the intended use of the product.
For example, a product that requires high stiffness and strength, such as a car bumper, would require a plastic material like ABS, while a product that requires flexibility, such as a plastic bag, would require a material like polyethylene.
Chemical Properties:
The chemical properties of the plastic material are also an essential factor to consider. The resistance of the plastic to chemicals, UV radiation, and water is critical in determining the longevity of the product.
For example, a product that requires contact with chemicals, such as a chemical storage tank, would require a plastic material that is resistant to chemicals, such as polypropylene or PVC.
Manufacturing Process:
The manufacturing process used to create the product must also be considered when selecting plastic for manufacturing. The plastic should be compatible with the manufacturing process, such as injection molding, extrusion, or blow molding. The process must be able to form the plastic into the desired shape and size without causing defects or material degradation.
Cost:
The cost of the plastic material must be considered to ensure the final product is cost-effective. Some plastics, like polyethylene, are relatively inexpensive and widely available, while others, like polycarbonate, are more expensive due to their unique properties and production processes.
Environmental Impact:
The environmental impact of the plastic material is also a crucial factor to consider. The plastic should be recyclable or biodegradable to reduce environmental impact. For example, products made from bioplastics, like polylactic acid (PLA), can help reduce the environmental impact of plastic waste.
Regulatory Compliance:
Depending on the industry and application, the plastic material may need to comply with certain regulations and standards. The plastic must meet safety and quality standards for its intended use. For example, food packaging plastics must be approved for contact with food.
Considering these factors when selecting plastic for manufacturing can ensure that the final product meets its intended use, is cost-effective, and is environmentally responsible.
How Cost Can Influence Plastic Selection and Examples of Cost-Saving Measures
The cost of plastic is an essential factor that influences the selection of the appropriate type of plastic for a particular application. The cost of plastic varies depending on the type, quantity, and quality of the plastic used. Therefore, it is necessary to balance the performance requirements with the cost of plastic to select the most cost-effective option.
Following, we've discussed some ways cost can influence plastic selection:
Material Cost: The cost of plastic is directly related to the type of polymer used. Some polymers like PVC, Polypropylene, and PE are less expensive, whereas others like Polycarbonate, ABS, and Acrylic are more costly. So, depending on the budget and performance requirements of a project, a cheaper plastic may be chosen over a more expensive option.
Processing Cost: The cost of processing can also affect plastic selection. Some plastics may require special processing methods or equipment that can increase the overall cost of production. For example, injection molding is a common method for producing plastic parts, but some plastics may require more complicated molds, which can increase the cost of production.
Maintenance Cost: The maintenance cost of equipment used in the production process also influences the choice of plastic. Some plastics may be more abrasive or corrosive, which can damage processing equipment more quickly. Choosing a plastic that is less abrasive or corrosive can help reduce the maintenance costs of the equipment.
Examples of cost-saving measures in plastic selection include:
Recycling: Using recycled plastic is an effective way to reduce costs while also being environmentally friendly. Many manufacturers are now using recycled plastic in their products to reduce the cost of production.
Material substitution: Material substitution involves replacing a more expensive plastic with a less expensive option that provides similar performance. For example, replacing polycarbonate with PETG can reduce the cost of production while still providing a similar level of durability and impact resistance.
Bulk purchasing: Bulk purchasing allows for larger quantities of plastic to be purchased at a lower price per unit. This strategy is beneficial for large-scale production runs where the cost of plastic is a significant factor.
Design optimization: Design optimization involves optimizing the design of a product to reduce the amount of plastic used without compromising performance. This approach reduces the overall cost of production while also being environmentally friendly.
Environmental Impact of Plastics and Examples of Environmentally Friendly Plastics and Practices
The importance of considering the environmental impact of plastics cannot be overstated. Plastics have become an integral part of our daily lives, but their production, use, and disposal have significant environmental consequences.
Plastics are a major contributor to the pollution of our oceans, landfills, and waterways, and they also contribute to the emission of greenhouse gases during production and disposal.
Here are some reasons why considering the environmental impact of plastics is important:
Pollution: Plastics can take hundreds of years to break down in the environment, which means they can accumulate in our oceans, landfills, and waterways. This pollution can harm wildlife, damage ecosystems, and contribute to climate change.
Resource depletion: Plastics are made from non-renewable resources, such as oil and gas. The production of plastics requires significant amounts of energy and natural resources, which can lead to resource depletion and contribute to climate change.
Health impacts: Some plastics contain harmful chemicals, such as phthalates and bisphenol A (BPA), which can leach into food and water and have negative health impacts.
Sustainable development: Considering the environmental impact of plastics is crucial for promoting sustainable development and reducing our carbon footprint.
Examples of environmentally friendly plastics and practices include:
Bioplastics: Bioplastics are made from renewable resources, such as corn starch, sugarcane, or potato starch, and they are biodegradable. These plastics have a lower carbon footprint than traditional plastics, and they can help reduce waste in landfills and oceans.
Recyclable plastics: Some plastics are designed to be recycled, which can help reduce the amount of plastic waste that ends up in landfills and oceans. Recycling also conserves resources and reduces greenhouse gas emissions.
Reduce, reuse, and recycle: The best way to reduce the environmental impact of plastics is to reduce our consumption of single-use plastics, reuse plastics where possible, and recycle plastics that cannot be reused. This involves making conscious decisions to purchase products with minimal packaging, use reusable containers instead of single-use plastics, and dispose of plastics responsibly.
Design for sustainability: Designing products with sustainability in mind can help reduce the environmental impact of plastics. This involves using minimal packaging, designing products to be easily recycled or composted, and using materials that are biodegradable and renewable.
By considering the environmental impact of plastics, we can make conscious decisions that reduce our impact on the environment and promote sustainable development.
Successful Plastic Selection
Successful plastic selection is crucial for the success of the manufacturing process. The choice of plastic can impact the performance, quality, and cost-effectiveness of the final product.
Following, we’ve discussed some examples of successful plastic selection and how the chosen plastic influenced the success of the manufacturing process:
Automotive Parts: Many automotive parts are made from plastic, such as bumpers, dashboards, and door panels. Polycarbonate (PC) is a popular choice for these parts because it is lightweight, durable, and impact-resistant. The use of PC has helped reduce the weight of vehicles, improve fuel efficiency, and enhance safety.
Medical Devices: Medical devices require materials that are biocompatible, non-toxic, and easy to sterilize. Polytetrafluoroethylene (PTFE) is a commonly used plastic for medical devices because it is inert and can withstand high temperatures. The use of PTFE has helped improve the safety and effectiveness of medical devices.
Packaging: Packaging plays a crucial role in protecting and preserving products during shipping and storage. Polyethylene terephthalate (PET) is a popular choice for packaging because it is lightweight, transparent, and has good barrier properties. The use of PET has helped reduce the amount of packaging required and improved the shelf life of products.
Consumer Goods: Consumer goods, such as electronics, toys, and household appliances, require materials that are durable, lightweight, and aesthetically pleasing. Acrylonitrile butadiene styrene (ABS) is a commonly used plastic for these applications because it is strong, impact-resistant, and can be easily molded into complex shapes. The use of ABS has helped improve the durability and functionality of consumer goods.
In each of these examples, the choice of plastic influenced the success of the manufacturing process. The selected plastic provided the required properties, such as strength, durability, and aesthetic appeal, while also being cost-effective and easy to process.
The use of the appropriate plastic helped improve the quality and performance of the final product, reduce the weight and cost of production, and enhance safety and functionality.
Tips to Keep in Mind When Selecting the Right Plastic for your Manufacturing Process
Following, we’ve discussed some tips to keep in mind when selecting plastic for your manufacturing process:
Identify the Required Properties:
The first step in selecting plastic is to identify the properties required for your application, such as strength, durability, flexibility, and chemical resistance. This will help narrow down the options and ensure that the selected plastic meets the performance requirements.
Consider the Processing Requirements:
Plastic selection should also consider the processing requirements, such as molding, extrusion, or casting. Some plastics are more difficult to process than others, which can impact the cost and time required for production.
Evaluate the Cost-Effectiveness:
Cost is an important consideration when selecting plastic, as it can impact the overall cost of production. It is important to consider the cost of the plastic itself, as well as any additional costs associated with processing, tooling, and production.
Assess the Environmental Impact:
The environmental impact of plastics should also be considered when selecting plastic. It is important to choose plastics that are recyclable or biodegradable, and that have a lower carbon footprint than traditional plastics.
Consult with a Plastic Expert:
It can be helpful to consult with a plastic expert or a plastic supplier when selecting plastic for your manufacturing process. They can provide guidance on the best plastic for your application, as well as advice on processing and production.
By keeping these tips in mind, you can ensure that the plastic selected for your manufacturing process meets your performance requirements, is cost-effective, and has a lower environmental impact.
Wrapping Up
In conclusion, plastic selection plays a critical role in the success of the manufacturing process.
The choice of plastic can impact the performance, quality, and cost-effectiveness of the final product. Factors such as strength, durability, aesthetics, and cost must be considered when selecting the appropriate plastic for each application.
Additionally, it is important to consider the environmental impact of plastics and strive towards using more environmentally friendly plastics and practices. By making conscious decisions and selecting the appropriate plastic, we can improve the functionality, durability, and sustainability of products, while also reducing our impact on the environment.
How Deskera Can Assist You?
Deskera's integrated financial planning tools allow investors to better plan their investments and track their progress. It can help investors make decisions faster and more accurately.
Deskera Books enables you to manage your accounts and finances more effectively. Maintain sound accounting practices by automating accounting operations such as billing, invoicing, and payment processing.
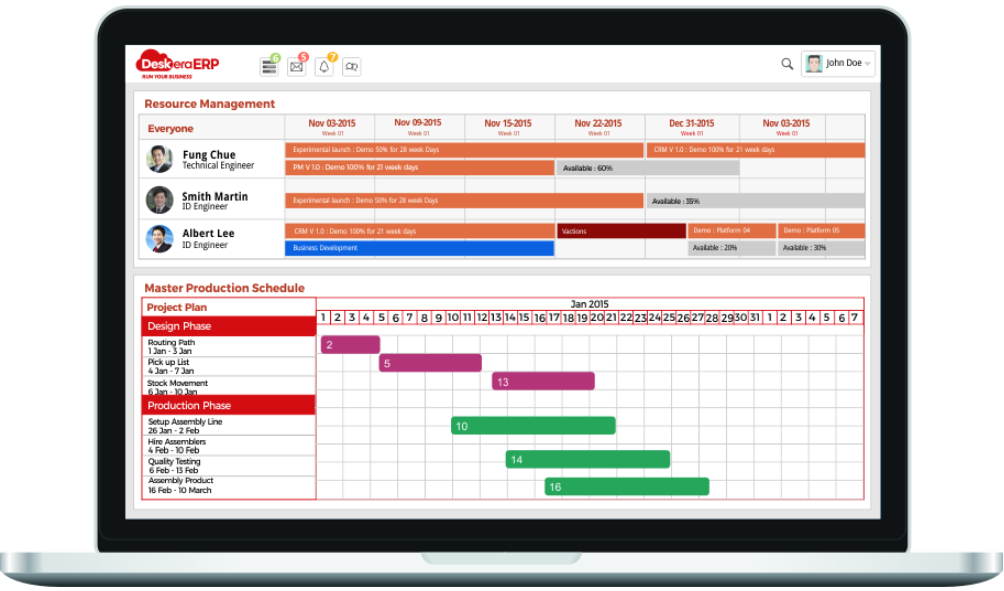
Deskera CRM is a strong solution that manages your sales and assists you in closing agreements quickly. It not only allows you to do critical duties such as lead generation via email, but it also provides you with a comprehensive view of your sales funnel.
Deskera People is a simple tool for taking control of your human resource management functions. The technology not only speeds up payroll processing but also allows you to manage all other activities such as overtime, benefits, bonuses, training programs, and much more. This is your chance to grow your business, increase earnings, and improve the efficiency of the entire production process.
Final Takeaways
We've arrived at the last section of this guide. Let's have a look at some of the most important points to remember:
- Selecting the right plastic for manufacturing can also improve the overall quality of the product, increase its lifespan, and enhance its appearance. By carefully considering the properties of plastics and the manufacturing processes used, manufacturers can create products that are stronger, more durable, and more aesthetically appealing.
- Injection molding is the most common plastic manufacturing process. It involves melting plastic pellets and injecting them into a mold to create a specific shape. Injection molding is used to create a wide range of products, from small toys to large automotive parts.
- Different plastics have different melting points, flow properties, and viscosities. The manufacturing process used to create a product will determine the temperature and pressure needed to melt and mold the plastic. Some plastics, like polyethylene, are easily molded using low-pressure injection molding techniques, while others, like polycarbonate, require high-pressure injection molding.
- The physical properties of the plastic play a crucial role in determining the choice of plastic for manufacturing. The stiffness, strength, flexibility, and temperature resistance of the plastic must be matched with the intended use of the product.
- The cost of processing can also affect plastic selection. Some plastics may require special processing methods or equipment that can increase the overall cost of production. For example, injection molding is a common method for producing plastic parts, but some plastics may require more complicated molds, which can increase the cost of production.
- The best way to reduce the environmental impact of plastics is to reduce our consumption of single-use plastics, reuse plastics where possible, and recycle plastics that cannot be reused. This involves making conscious decisions to purchase products with minimal packaging, use reusable containers instead of single-use plastics, and dispose of plastics responsibly.
- The environmental impact of plastics should also be considered when selecting plastic. It is important to choose plastics that are recyclable or biodegradable, and that have a lower carbon footprint than traditional plastics.
Related Articles
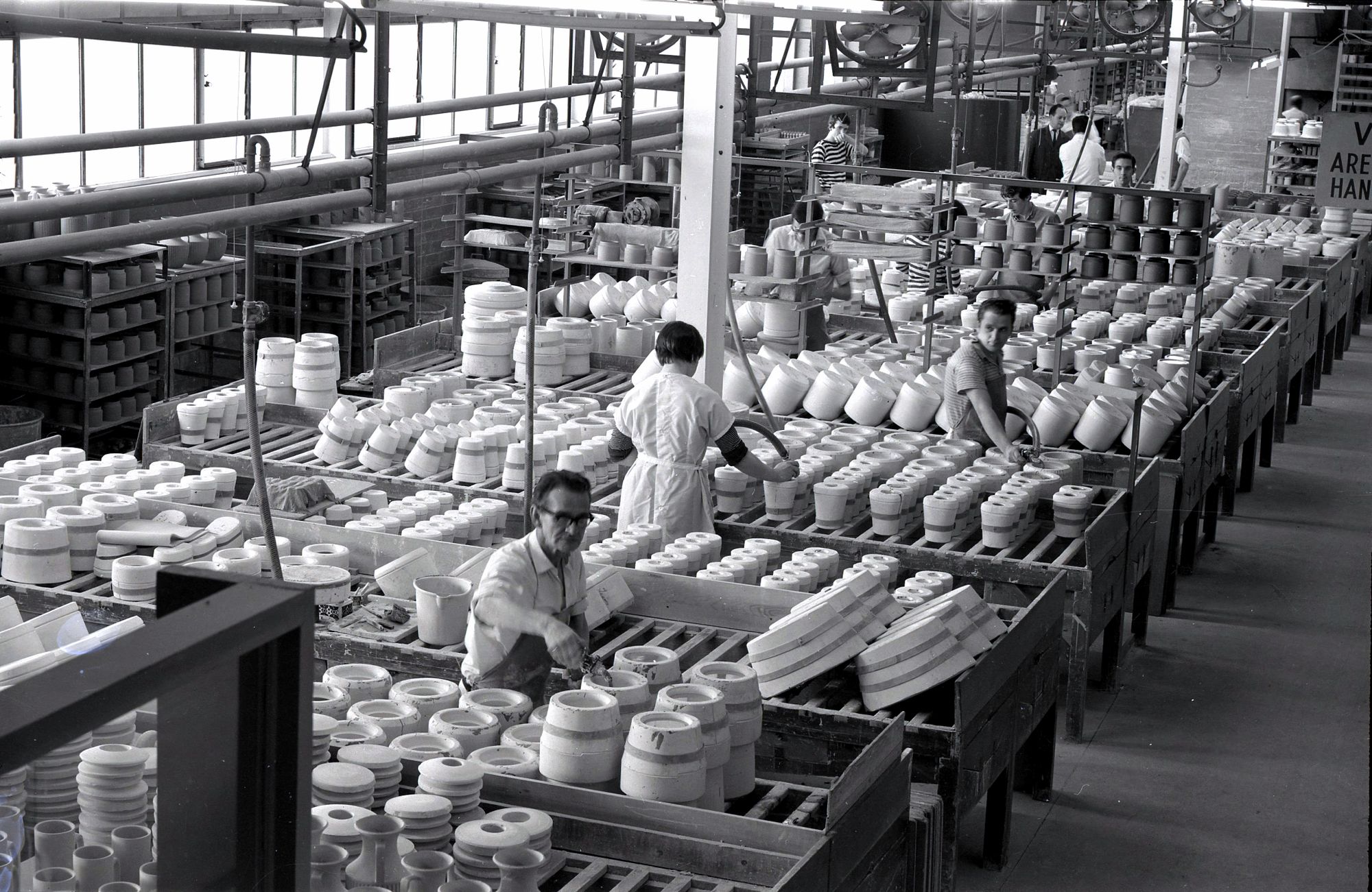
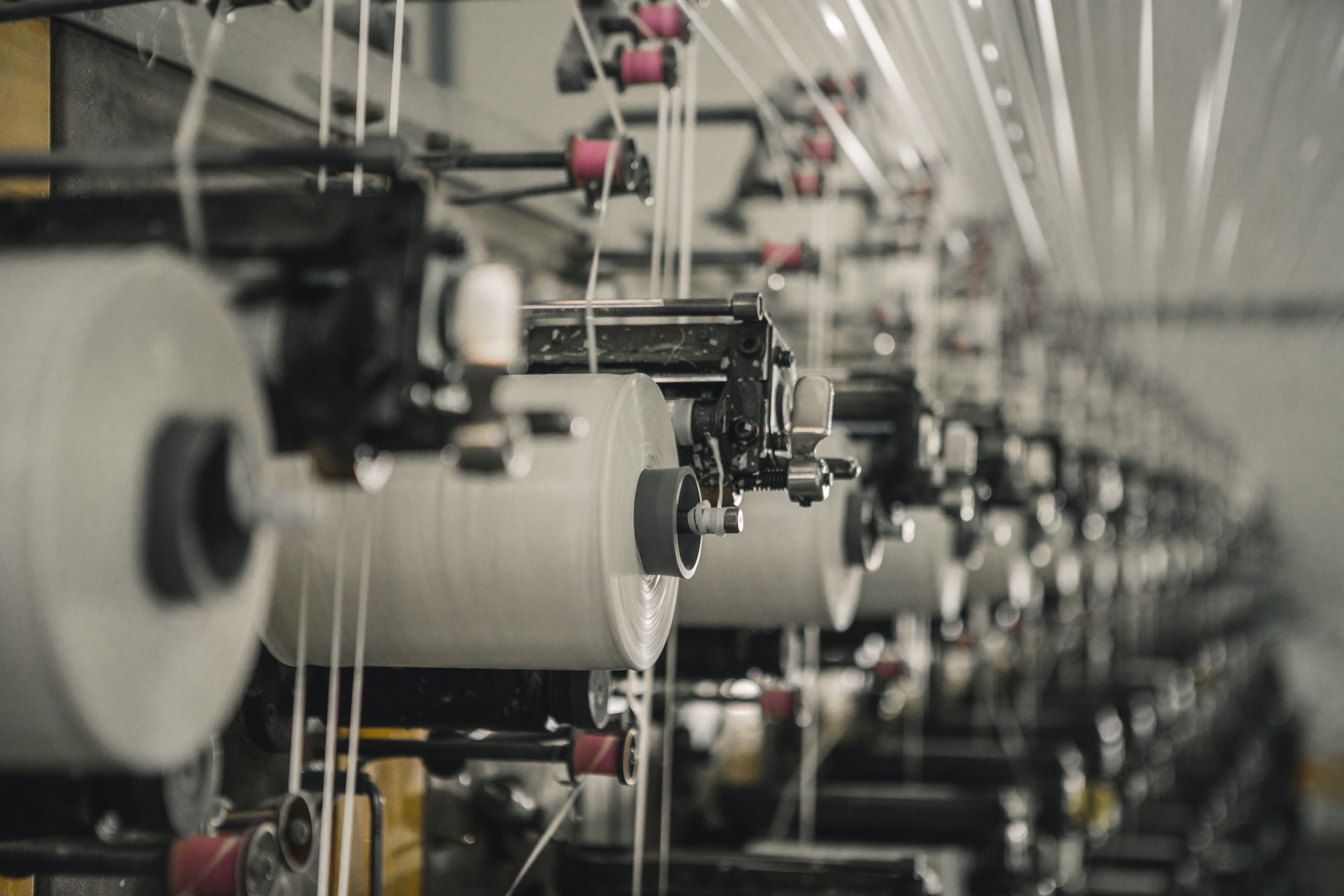
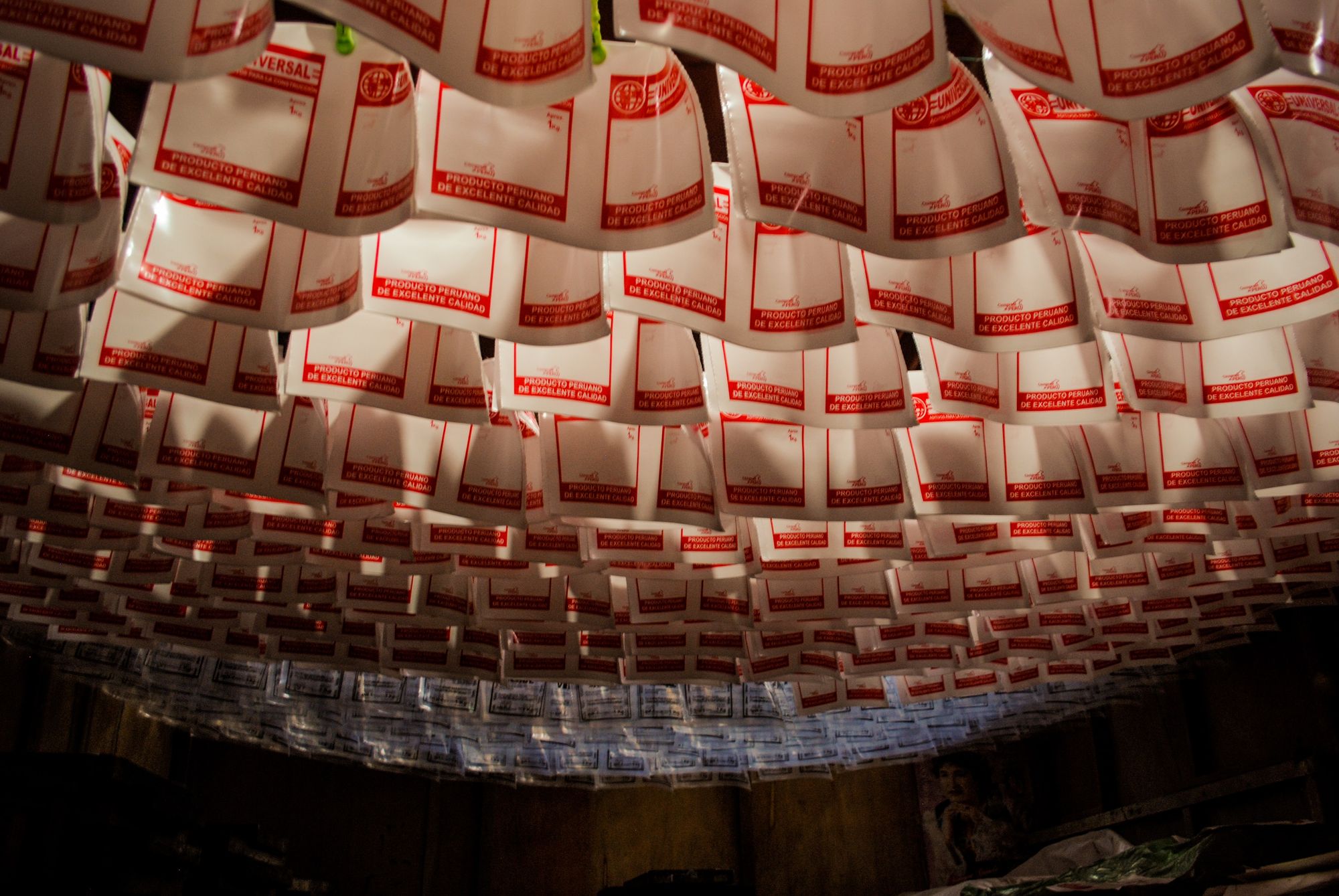
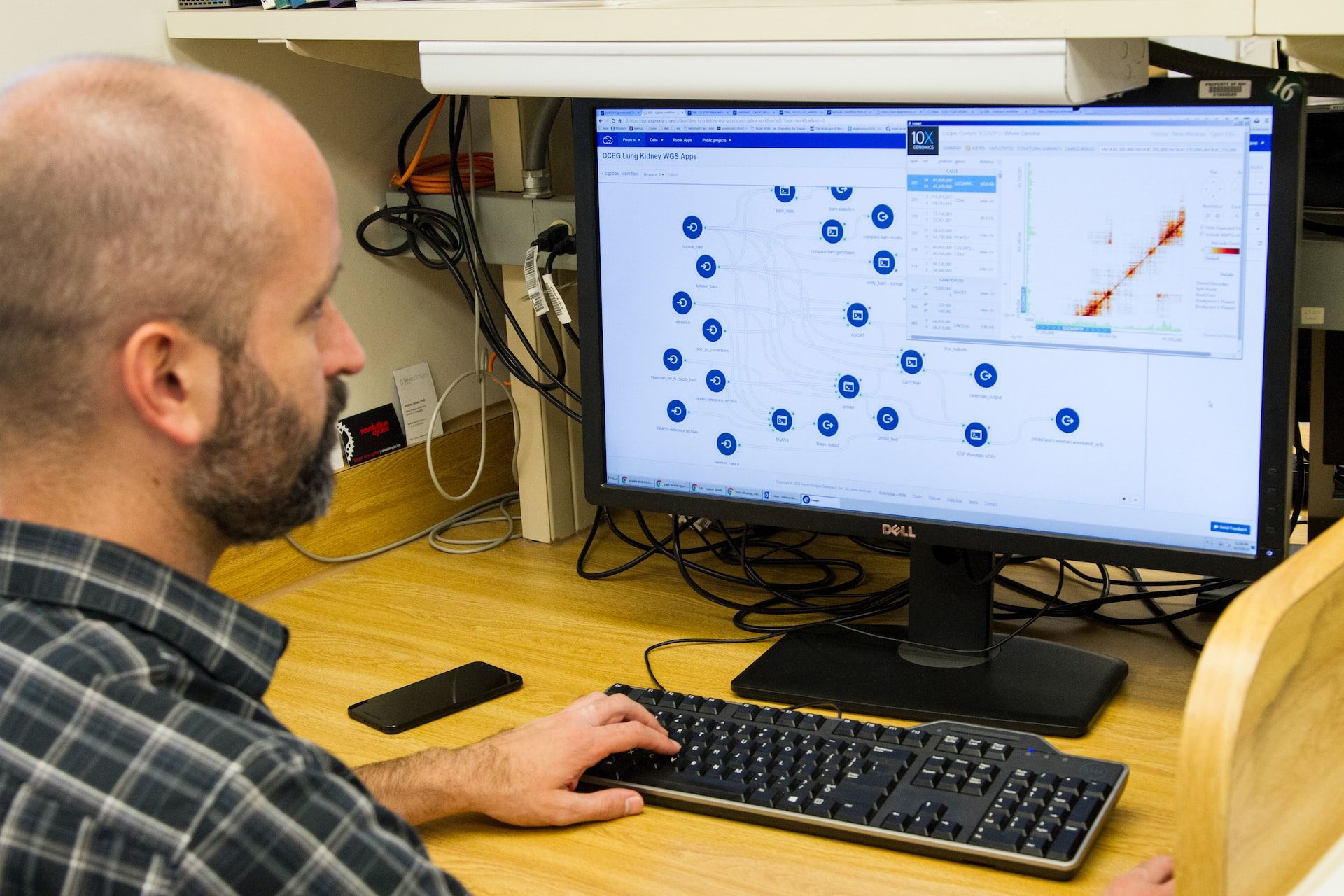
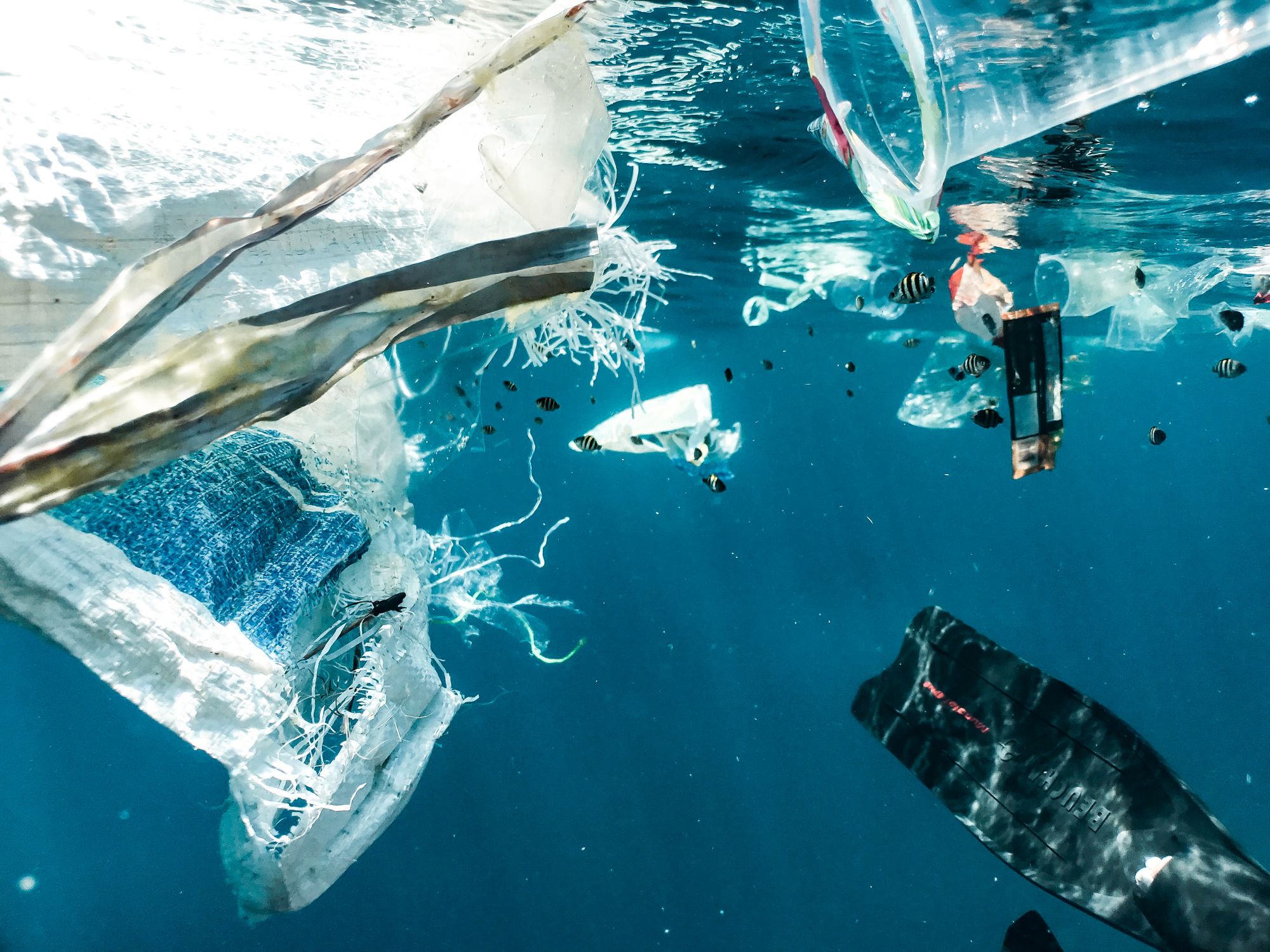