Outsourcing furniture production has become a common practice for many companies looking to reduce costs and increase efficiency. By outsourcing, companies can take advantage of lower labor costs and gain access to skilled workers in other countries, which can lead to significant savings.
According to a report by Grand View Research, the global furniture market size was valued at USD 582.2 billion in 2020, and it is expected to grow at a CAGR of 5.4% from 2021 to 2028.
However, outsourcing also has its downsides. Quality control issues, communication barriers, intellectual property concerns, lack of control over the production process, and ethical considerations are just a few of the challenges that can arise when outsourcing.
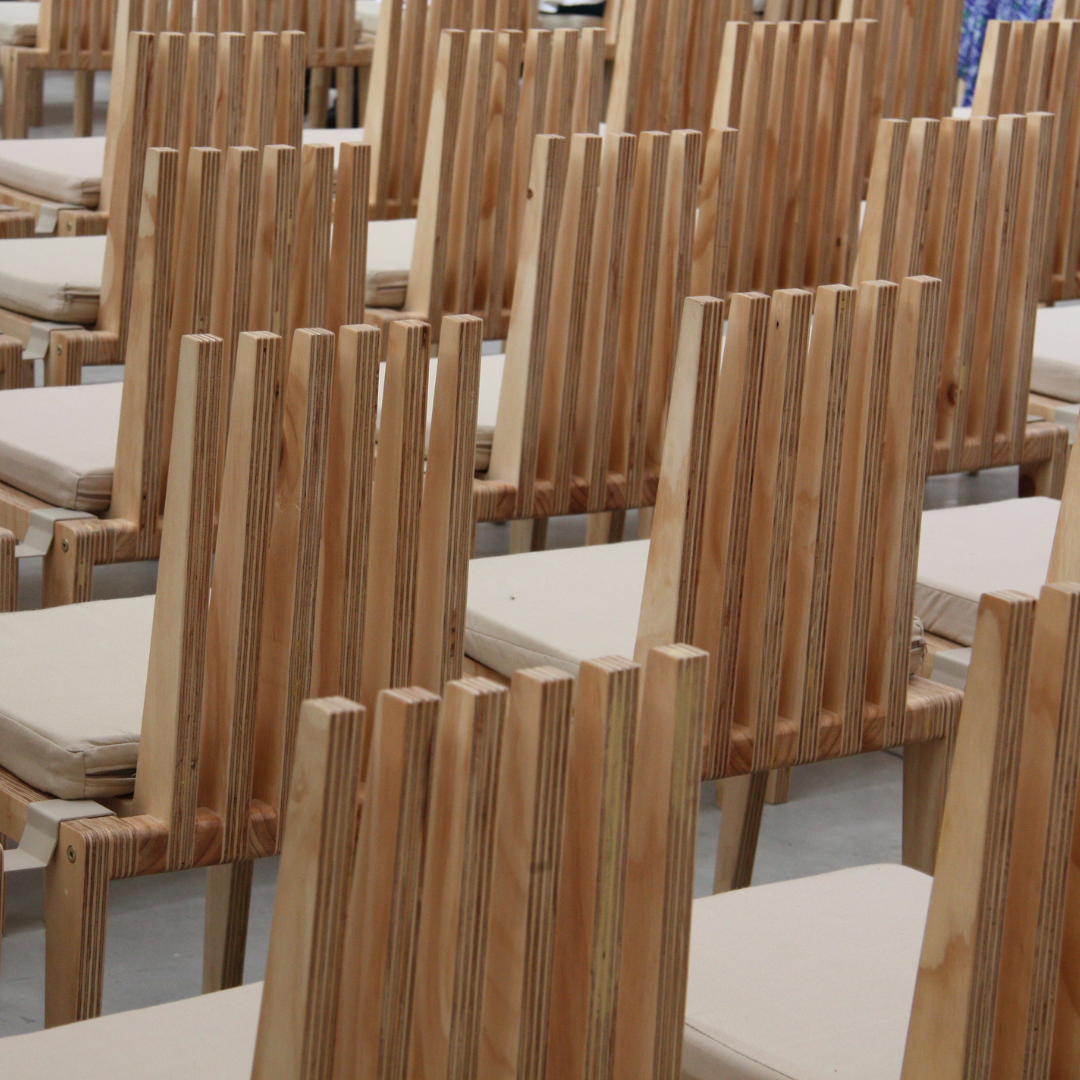
In this article, we will explore the pros and cons of outsourcing furniture production. We will examine the benefits of outsourcing, such as lower production costs, access to skilled labor, increased efficiency, and the ability to focus on core competencies. We will also discuss the drawbacks of outsourcing, including the potential for quality control issues, communication barriers, and ethical concerns.
Finally, we will consider the future of outsourcing in the furniture industry and provide guidance for companies considering whether or not to outsource their furniture production.
- What Outsourcing Furniture Production Means
- Pros of Outsourcing Furniture Production
- Cons of Outsourcing Furniture Production
- How can MRP Systems Assist Furniture Production Process?
- How can Deskera Help You?
- Key Takeaways
- Related Articles
What Outsourcing Furniture Production Means
Outsourcing furniture production means that a company contracts with an external manufacturer or supplier to produce furniture products, rather than producing them in-house. In this arrangement, the external manufacturer or supplier is responsible for the entire production process, including sourcing of raw materials, manufacturing, quality control, and shipping.
Outsourcing is typically done to take advantage of lower labor costs in other countries, as well as to gain access to specialized skills and expertise that may not be available in-house.
For example, a furniture company based in the United States may outsource production to a manufacturer in China, where labor costs are lower and there are specialized skills in certain areas of furniture production.
Outsourcing furniture production can also allow companies to focus on their core competencies and reduce the amount of resources they need to allocate to non-core activities.
However, outsourcing can also bring challenges, such as quality control issues, communication barriers, intellectual property concerns, and ethical considerations, which need to be carefully managed by companies to ensure a successful outsourcing relationship.
Pros of Outsourcing Furniture Production
Outsourcing furniture production can bring a range of benefits to companies, including cost savings, increased efficiency, and access to specialized skills and expertise. In this section, we will explore the pros of outsourcing furniture production in more detail, including the potential for lower production costs, increased flexibility, improved quality, and the ability to focus on core competencies.
We will also provide examples of successful outsourcing relationships in the furniture industry and examine how companies can maximize the benefits of outsourcing while minimizing the risks.
Lower Labor Costs can Lead to Cheaper Furniture Prices for Consumers
One of the main advantages of outsourcing furniture production is that it can lead to lower labor costs in foreign countries, which in turn can result in cheaper furniture prices for consumers. This is because wages and other labor costs in some countries, such as China or Vietnam, may be significantly lower than in developed countries like the United States or Canada.
By outsourcing to a foreign manufacturer, a company can take advantage of these lower labor costs and potentially reduce the overall cost of production. This can enable the company to offer its products at a more competitive price point, which can attract more customers and increase sales.
Lower labor costs can also enable companies to invest in other areas of the business, such as research and development, marketing, or customer service. By reducing production costs through outsourcing, a company may be able to allocate more resources to these other areas, which can lead to further growth and success.
Access to Specialized Skills and Technology that may not be Available Domestically
By outsourcing to a foreign manufacturer, companies can gain access to specialized skills and technology that may not be available domestically.
For example, some countries may have a strong tradition of woodworking or furniture making, which can result in a higher level of expertise and experience in these areas. By outsourcing to a manufacturer in one of these countries, a company can tap into this expertise and potentially improve the quality of its products.
In addition, some countries may have access to certain technologies or manufacturing processes that are not widely available in other countries. By outsourcing to a manufacturer with these capabilities, a company can gain a competitive advantage and potentially create products that are more innovative or unique.
Overall, outsourcing furniture production can enable companies to leverage the expertise and technology of manufacturers in other countries, which can help to improve the quality and competitiveness of their products.
Allows Domestic Furniture Companies to Focus on other Aspects of their Business
By outsourcing the production of their furniture products, domestic furniture companies can free up resources and focus on other aspects of their business, such as marketing and design.
Outsourcing can allow companies to focus on their core competencies, such as designing innovative and high-quality furniture products, while leaving the production process to an external manufacturer. This can help companies to create a more efficient and streamlined business model, which can lead to increased productivity and profitability.
In addition, outsourcing can enable companies to be more flexible and responsive to changing market conditions. For example, if demand for a particular product increases, an outsourced manufacturer can ramp up production more quickly than an in-house production team. This can allow companies to take advantage of new opportunities and respond more quickly to changes in consumer demand.
Overall, outsourcing furniture production can enable domestic furniture companies to focus on their core competencies and improve their overall business model, which can lead to increased competitiveness and profitability.
Provides Job Opportunities in Foreign Countries where Labor is in Demand
By outsourcing to foreign manufacturers, domestic furniture companies can create job opportunities in countries where labor is in demand.
For example, some developing countries may have high levels of unemployment or underemployment, and outsourcing can provide opportunities for workers to gain employment and improve their standard of living. In addition, outsourcing can help to stimulate economic growth and development in these countries, which can have positive ripple effects throughout the local economy.
However, it's worth noting that outsourcing can also have negative impacts on domestic labor markets, particularly if jobs are being moved overseas to take advantage of lower wages. This can lead to job losses and reduced wages for domestic workers, which can have negative social and economic consequences.
Overall, while outsourcing can create job opportunities in foreign countries, it's important for companies to consider the potential impacts on both domestic and foreign labor markets and ensure that they are operating in a socially responsible and sustainable manner.
Cons of Outsourcing Furniture Production
While outsourcing furniture production has its advantages, there are also several potential drawbacks that companies should consider before deciding to outsource. In this section, we will explore some of the cons of outsourcing furniture production.
Ethical Concerns Surrounding Working Conditions and Wages in Foreign Countries
One of the most significant cons of outsourcing furniture production is the ethical concerns surrounding working conditions and wages in foreign countries. While outsourcing can create job opportunities in developing countries, there have been numerous reports of workers being exploited and forced to work in unsafe and unfair conditions.
In some cases, foreign manufacturers may pay workers low wages and subject them to long working hours, poor working conditions, and inadequate health and safety standards. This can lead to negative impacts on the workers' health and wellbeing, and can also have broader social and economic impacts.
Furthermore, there have been reports of child labor and other forms of exploitation in some countries where furniture production is outsourced. This can raise serious ethical concerns for companies and consumers, and can damage a company's reputation and brand image.
Overall, ethical concerns surrounding working conditions and wages in foreign countries are a significant con of outsourcing furniture production. Companies must carefully consider the potential ethical implications of outsourcing and ensure that they are working with reputable manufacturers that prioritize the well-being and fair treatment of their workers.
Quality Control Issues, such as Language Barriers and Cultural Differences
Another potential con of outsourcing furniture production is quality control issues, such as language barriers and cultural differences. When outsourcing production to foreign countries, there can be differences in language, culture, and business practices that can lead to miscommunications and misunderstandings.
For example, furniture manufacturers may not understand the specific quality standards or design requirements of the domestic furniture company, which can lead to products that do not meet the expected quality standards. Additionally, language barriers can make it difficult to communicate about design changes, production issues, or other important matters, which can lead to delays or mistakes in the production process.
Cultural differences can also be a challenge when outsourcing furniture production. Different cultures may have different approaches to business and production, and this can lead to misunderstandings and differences in expectations. This can result in products that do not meet the desired specifications or quality standards.
To mitigate these quality control issues, it's important for companies to establish clear communication channels and expectations with their foreign manufacturers.
This may involve hiring translators or interpreters to help facilitate communication, or investing in training and development programs to help foreign manufacturers understand the specific quality standards and requirements of the domestic furniture company.
Increased Shipping Costs and Longer Lead Times
Another potential con of outsourcing furniture production is the increased shipping costs and longer lead times associated with importing furniture from foreign countries. When outsourcing production to overseas manufacturers, furniture companies will need to factor in the cost of shipping the furniture back to their home country, which can be a significant expense.
In addition, shipping furniture over long distances can also lead to longer lead times, which can delay the delivery of products to customers. This can be a particular challenge for companies that require quick turnaround times or need to respond quickly to changes in customer demand.
Moreover, shipping furniture over long distances can also increase the carbon footprint of the furniture industry, as it requires more fuel and energy to transport products across the globe. This can be a concern for companies that are committed to sustainability and reducing their environmental impact.
To mitigate these challenges, companies may need to consider alternative shipping methods or explore local sourcing options. For example, some companies may choose to source materials and components locally and only outsource certain aspects of production, such as assembly or finishing. This can help to reduce shipping costs and lead times while still taking advantage of the benefits of outsourcing.
Domestic Job Loss and Impact on the Economy
When companies outsource production to foreign countries, they may be displacing domestic workers who would have otherwise been employed in the furniture industry.
This can have negative effects on the domestic economy, as workers may struggle to find new employment opportunities or may be forced to accept lower-paying jobs in other industries. This can result in lower consumer spending and reduced economic growth, as workers have less disposable income to spend on goods and services.
Furthermore, outsourcing furniture production can also lead to a loss of industry expertise and knowledge within the domestic furniture industry. When production is outsourced, companies may lose valuable skills and knowledge related to design, manufacturing, and production processes.
This can make it more difficult for companies to innovate and compete in the global marketplace, potentially leading to further economic impacts.
To address these concerns, some companies may choose to keep production within their home country or explore alternative ways of supporting domestic job growth. For example, companies may invest in training and development programs to help workers transition into new industries, or may seek to collaborate with local suppliers and manufacturers to support domestic supply chains.
How can MRP Systems Assist Furniture Production Process?
MRP (Material Requirements Planning) systems can assist the furniture production process in several ways. These systems are designed to help manufacturers manage and plan their production operations more efficiently, by providing real-time visibility into inventory levels, production schedules, and resource availability. Here are some of the ways that MRP systems can assist furniture production:
Streamline Production Planning: MRP systems can help manufacturers to plan their production schedules more effectively, by providing real-time information on inventory levels and production requirements. This can help to reduce the risk of stockouts or overproduction, and ensure that production schedules are optimized for maximum efficiency.
Manage Inventory Levels: MRP systems can also help manufacturers to manage their inventory levels more effectively, by providing real-time visibility into stock levels and usage rates. This can help to reduce the risk of stockouts or excess inventory, and ensure that manufacturers have the right materials and components on hand to support production.
Improve Resource Utilization: MRP systems can also help manufacturers to optimize their use of resources, such as labor and equipment. By providing real-time visibility into resource availability and production schedules, MRP systems can help to ensure that resources are allocated effectively, and that production processes are optimized for maximum efficiency.
Enhance Collaboration: MRP systems can also enhance collaboration between different departments and stakeholders within the production process. By providing real-time visibility into production schedules and resource availability, MRP systems can help to ensure that everyone is working towards the same goals, and that production processes are aligned for maximum efficiency.
Overall, MRP systems can help furniture manufacturers to improve their production efficiency, reduce costs, and enhance collaboration across the organization. By leveraging these systems, manufacturers can gain a competitive edge in the global marketplace, and meet the evolving demands of consumers more effectively.
How can Deskera Help You?
Deskera ERP and MRP systems help you to keep your business units organized. The system's primary functions are as follows:
- Keep track of your raw materials and final items inventories
- Control production schedules and routings
- Keep a bill of materials
- Produce thorough reports
- Make your own dashboards
Deskera's integrated financial planning tools enable investors to better plan and track their investments. It can assist investors in making faster and more accurate decisions.
Deskera Books allows you to better manage your accounts and finances. Maintain good accounting practices by automating tasks like billing, invoicing, and payment processing.
Deskera CRM is a powerful solution that manages your sales and helps you close deals quickly. It not only enables you to perform critical tasks like lead generation via email, but it also gives you a comprehensive view of your sales funnel.
Deskera People is a straightforward tool for centralizing your human resource management functions.
Key Takeaways
- Pros of outsourcing furniture production include lower labor costs, access to specialized skills and technology, and the ability for domestic companies to focus on other aspects of their business, such as marketing and design.
- Outsourcing can also provide job opportunities in foreign countries where labor is in demand, which can help support economic growth and development.
- However, there are also several cons to outsourcing furniture production, including ethical concerns surrounding working conditions and wages in foreign countries, quality control issues, increased shipping costs, and longer lead times.
- Another major con of outsourcing furniture production is the potential impact on domestic job loss and the wider economy, as companies may be displacing domestic workers who would have otherwise been employed in the furniture industry.
- To address these concerns, some companies may choose to keep production within their home country or explore alternative ways of supporting domestic job growth.
- MRP systems can assist the furniture production process by streamlining production planning, managing inventory levels, improving resource utilization, and enhancing collaboration.
- Furniture companies should carefully weigh the pros and cons of outsourcing before making a decision, taking into account factors such as cost, quality, lead time, and ethical considerations.
- Ultimately, the decision to outsource furniture production should be based on a thorough analysis of the company's needs and goals, as well as an understanding of the potential risks and benefits associated with outsourcing.
Related Articles
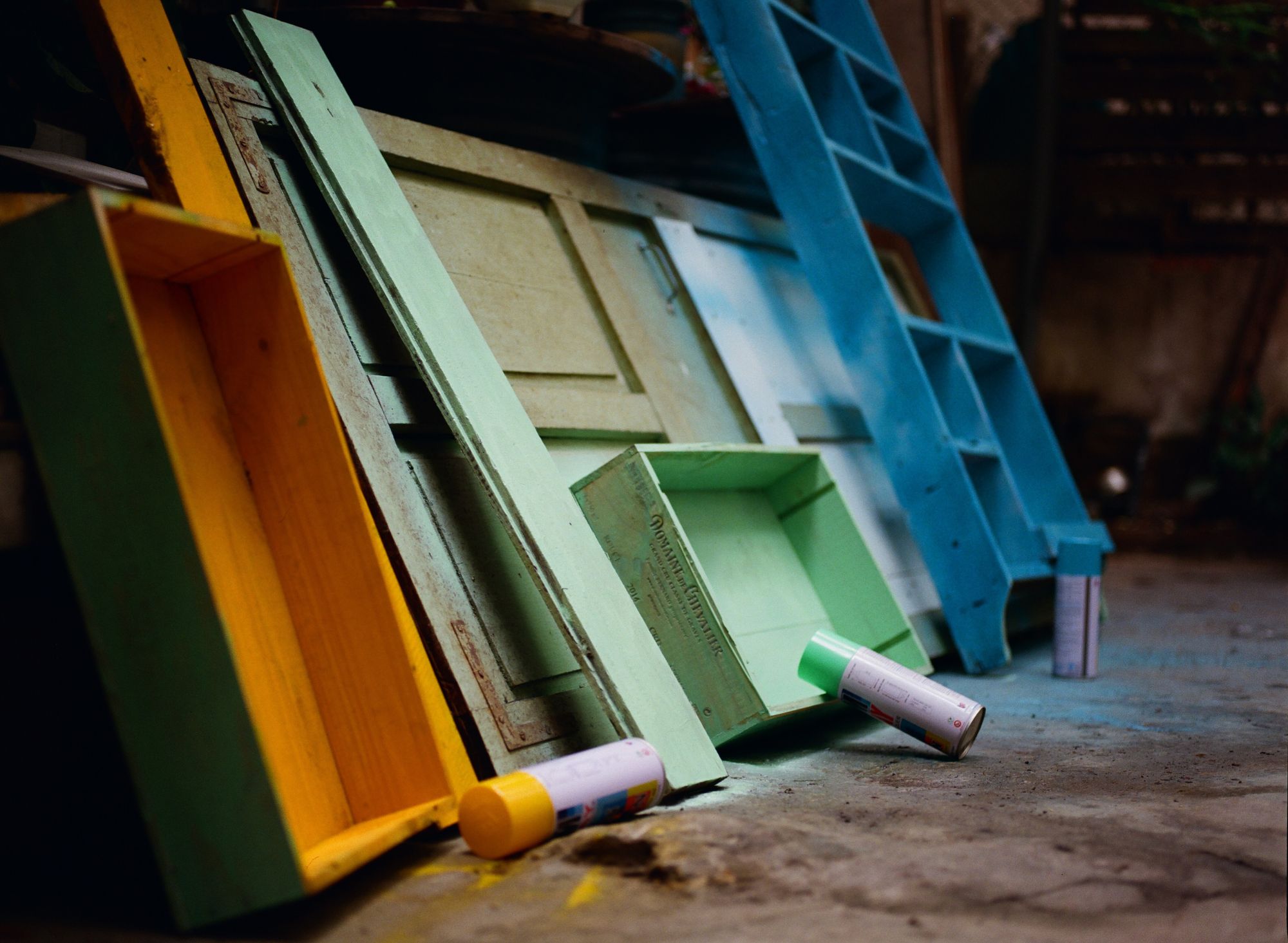
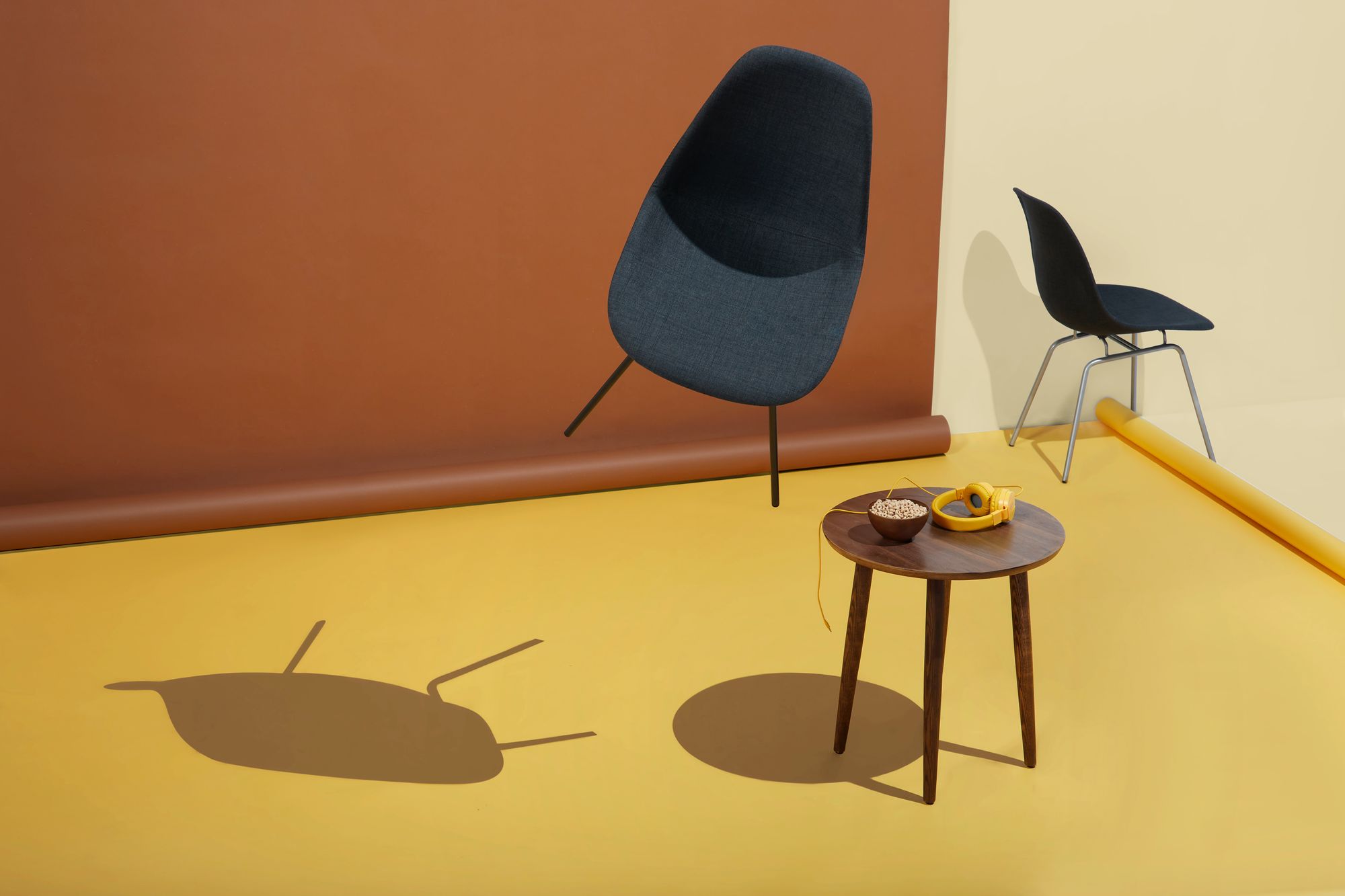
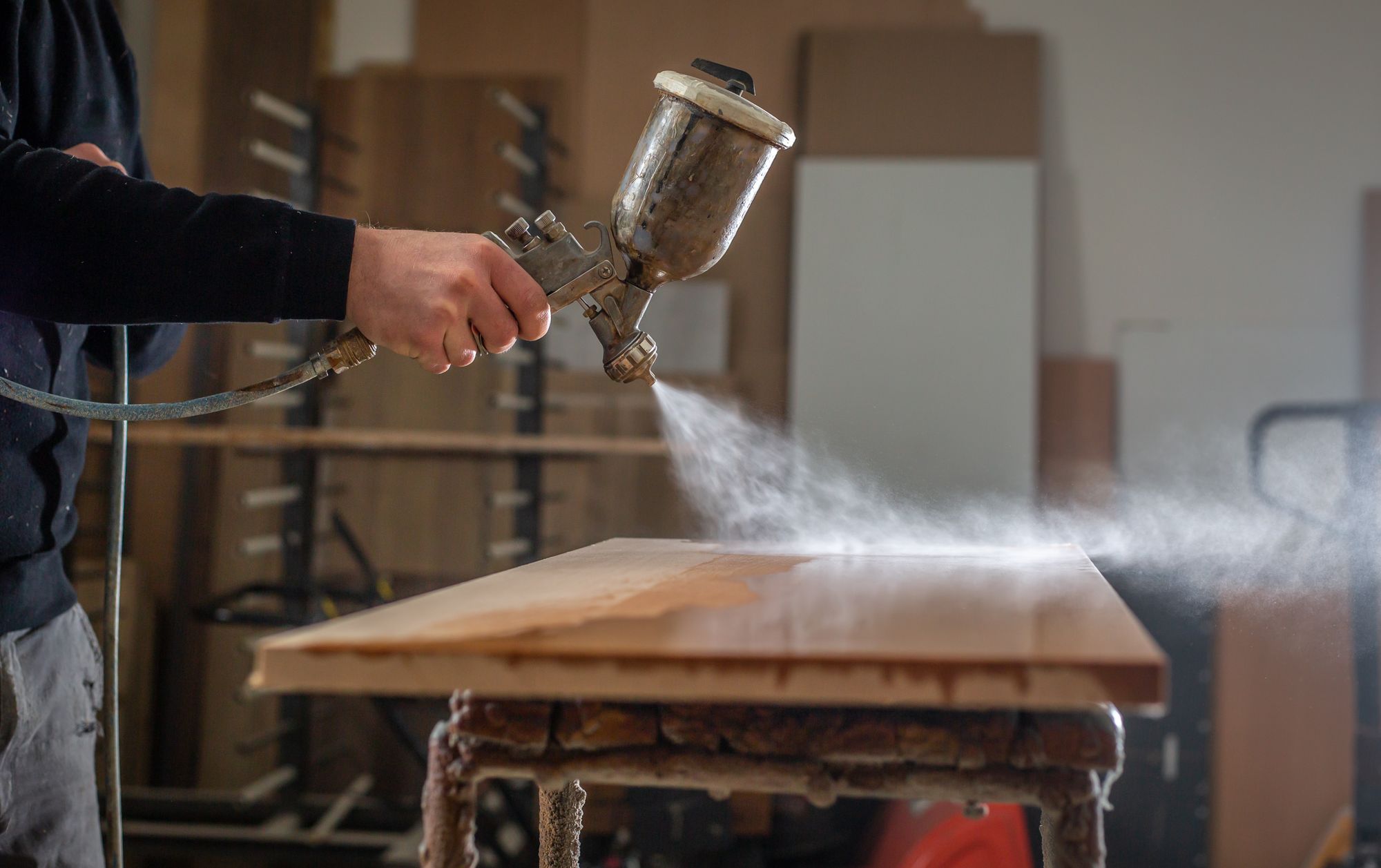