Anyone who has ever made a purchase from a supplier or vendor on an online marketplace is aware that prices are always changing. And because of it, calculating out the cost of goods sold (COGS) and inventory costs can be challenging.
This is why understanding average inventory calculation is crucial. In order to smooth out value fluctuations, average inventory uses an accounting technique known as smoothing.
Average inventory is beneficial in many ways since it consistently and accurately provides data over a lengthy period of time. In many industries, from manufacturing to retail, inventory management is crucial. You can keep track of stock levels and manage inventory flow by calculating your average inventory.
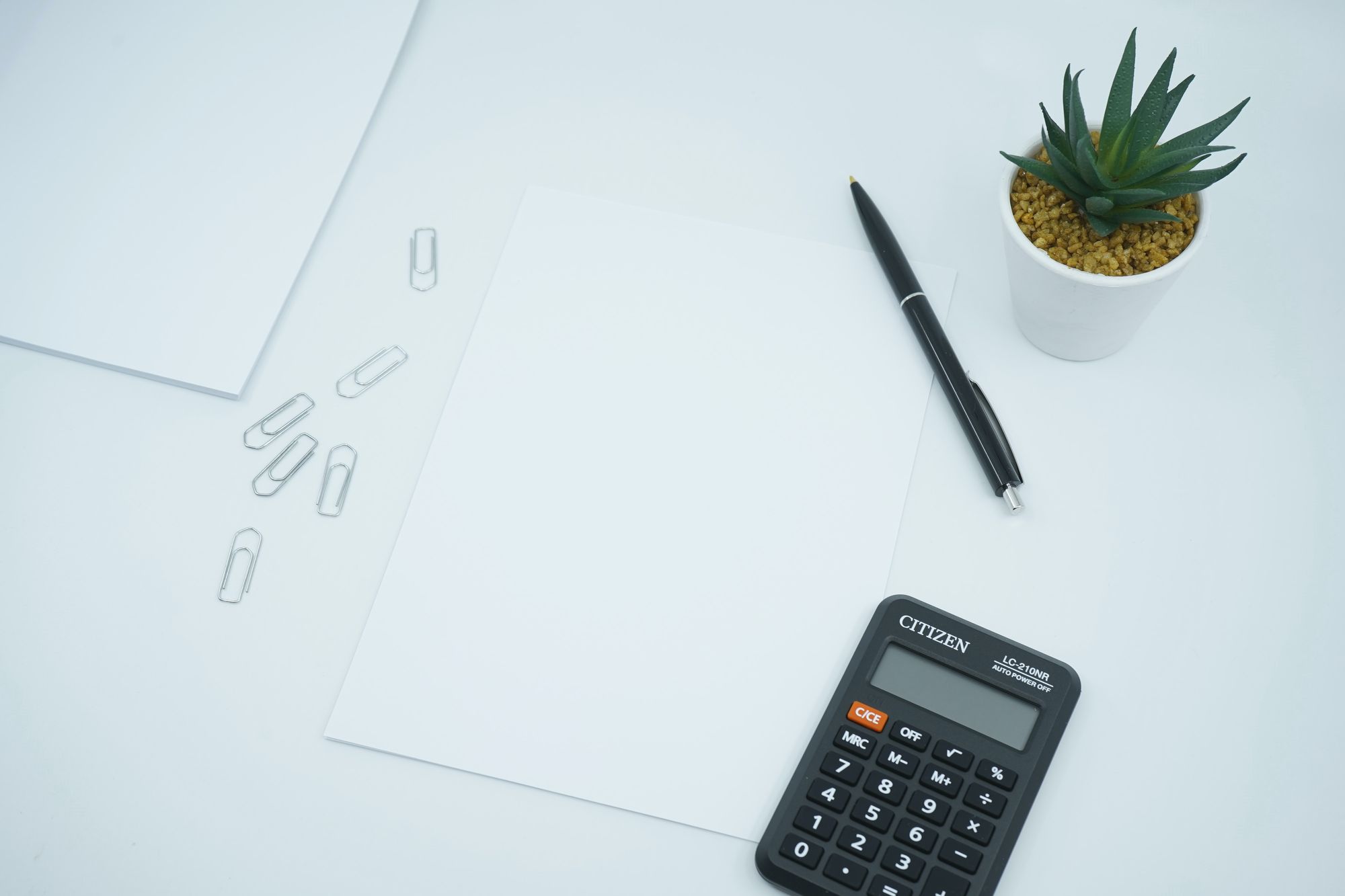
Missed sales prospects and empty store shelves might result from having insufficient goods on hand. A business grows and reflects its strengths in managing costs, sales, and client relationships by maintaining the ideal amount of inventory.
To monitor changes and activity over time, calculating average inventory is a valuable accounting tool. A company's inventory status can frequently be seen via this lens rather than through the lens of a certain moment in time or accounting period.
This article defines average inventory, discusses how to calculate it analytically, and discusses uses of average inventory for businesses. Following are the topics covered:
- What Is Inventory?
- What Is Average Inventory?
- Average Inventory Formula and Calculations
- Importance of Average Inventory
- Benefits of Calculating Average Inventory
- Challenges With Average Inventory
- Conclusion
- Key Takeaways
What Is Inventory?
The term "inventory" refers to the quantity of goods on hand that are prepared for sale so that the business can make a profit or the quantity of raw materials on hand by the business that will be utilized to create the finished goods that will be sold off.
One of a company's most valuable assets is its inventory because it is one of the main sources of revenue generation and, consequently, a source of profits for the company's shareholders. There are three different categories of inventory: finished goods, work-in-progress, and raw materials. On the balance sheet of a company, it is listed as a current asset.
What Is Average Inventory?
The volume or value of an organization's average inventory is an estimate over a given period of time. Depending on when large shipments are received, when there is a buying spree or peak season that may significantly reduce the inventory, and other factors, inventory balances at the end of each month might vary greatly.
Such abrupt surges in either direction are evened out by an average inventory calculation, which provides a more consistent indicator of inventory readiness.
Businesses often tally their inventory towards the end of the month, but a significant end-of-month delivery of goods or a surge in outgoing stock could influence this total. A better picture of how much inventory is typically available is obtained by taking an average over two or more months.
Average Inventory Explained
Calculating average inventory involves averaging inventory items over two or more accounting periods.
- Add the inventory counts at the end of each month, then divide the total by the number of months to determine the average inventory throughout a year. Other periods of time's average inventory figures are calculated in a similar manner.
- Here is one comparative method using average inventory. Take your most recent fiscal year's sales and contrast it with the same period's typical inventory. This will demonstrate how much inventory you needed on average each month to meet and sustain that level of sales.
- The same experiment might be done for any given time frame, including the entire year, a quarter, or even a month.
- Since it enables them to better manage their total business in terms of sales, costs, and relationships with their suppliers, successful inventory management is a crucial focus for businesses.
- Average inventory is typically determined by employing the number of points required to better correctly reflect activities over a specific amount of time because two points may not always accurately indicate changes in inventory across different time periods.
Average Inventory Level
The quantity of products, not their dollar value, is what is meant by the average inventory level. It is simpler to calculate the average inventory level than the average inventory cost. You perform the identical calculations, but you don't give the goods a cost. Simply average their quantity.
4 Methods for Costing Inventory
The following are the four primary inventory costing techniques:
- FIFO (First in, first out)- When determining how much inventory was sold in a specific time frame, this method uses the inventory that was purchased initially.
- LIFO (Last in, first out)- When determining how much inventory was sold in a specific time frame, this method takes into account the most recent inventory transaction.
- Specific identification- Using this technique, you can pinpoint specific things that you've bought but haven't sold in order to calculate inventory expenses. For somewhat unique products, such as vehicles and houses, specific identification is a technique that works well.
- Weighted average- With the weighted average costing method, comparable units receive the same unit price. When product units are so identical that applying the same price is quick and easy, this is the easiest situation to handle.
Average Inventory Formula and Calculations
By averaging the inventory at the start and end of the accounting period, the average inventory formula determines the average value of inventory at a specific moment in time. It aids management in comprehending the inventory that the company must maintain in order to conduct business on a daily basis.
Since a sudden drawdown in inventory or a big supply of inventory might affect ending inventory, average takes care of such surges by calculating the average value of both beginning and ending inventory.
Average Inventory = (current inventory + previous inventory) / number of periods
Average inventory is frequently calculated over a single month as follows:
Average Inventory = (Beginning Inventory + Ending Inventory) / 2
Given that it involves calculating the average of the beginning and ending inventories, the formula above is one of the easiest ways to calculate the average inventory, which is used to reduce the impact of sudden spikes or reductions in the ending inventory.
- Inventory is what drives a company's ability to create sales and, ultimately, profit, and managing inventory cost-effectively aids the company in maximizing its profits.
- It serves as a comparison tool and aids in the analysis of the entire revenue produced by the company in light of inventory usage.
- Long-term inventory holding costs the company money in the form of labour and storage fees. It also exposes the company to the danger of the inventory rotting, going out of date, etc.
Average Inventory Example
For example, if the cost of inventory was $183,000, $274,000, and $105,000 at the end of July, August, and September, respectively, the average inventory for the fourth quarter would be the total of all three divided by the number of months.
What is Day Sales Inventory?
The cost of goods (COG) multiplied by the time period, in this case a year, equals the average inventory divided by the COG. Therefore,
Day Sales Inventory = Average inventory/COG*365
Any business's profit increases as the DSI falls; the lower the DSI, the higher the profits. Because there are numerous sectors operating today and each one employs a range of manufacturing and sales methods, DSI varies from one firm to the next.
Although a lower DSI is often preferred, industry-specific factors will affect this as well. To get a sense of performance, compare your DSI to those of similar businesses.
What Is Inventory Turnover Ratio?
The inventory turnover ratio can be used to determine how long it takes from the moment inventory is purchased until it is sold to customers. Additionally, it reveals whether you're storing too much stock.
- A greater turnover ratio indicates that you are moving more items and replacing your inventory. But if you don't have enough inventory on hand to meet demand, it might also be a sign of lost revenue.
- To evaluate your performance, compare your company's ratios to those of similar businesses.
- Finding the average inventory and the cost of goods sold (COGS), a measurement of how much it costs to make your goods, including materials and labor, is the first step in calculating the inventory turnover ratio.
Typically, it appears on your income statement. Then follow this formula:
Inventory turnover ratio = Cost of goods sold / average inventory
Moving Average Inventory
Businesses that use the perpetual inventory method of accounting maintain an ongoing, real-time inventory record. By monitoring sales and inventory depletion or replenishment, computerised point-of-sale systems and inventory management software instantly reflect changes in inventory.
Businesses that employ the perpetual inventory approach can compare inventory averages over various time periods by using a moving average inventory. In order to enable a more realistic comparison of the eras, moving average inventory adapts pricing to the current market standard.
Moving average inventory solutions- For real-time records of inventory movement, several firms use a perpetual inventory valuation approach.
With computerized point-of-sale (POS) systems and inventory management software, you can use this valuation method to track inventory movements in real time and reflect changes in inventory right away. The perpetual inventory method is used by manufacturers to compare inventory averages throughout time.
Who Should Calculate Average Inventory?
The inventory manager, who may also be in charge of stocktaking, is typically the one who calculates average inventory for larger businesses. A lot of smaller companies, however, lack the funding to hire an inventory manager.
- Managing this process manually is completely acceptable for a business owner to do, but as the company expands, this becomes less viable.
- Instead of using a spreadsheet or pen and paper, we would always advise business owners to compute average inventory using a dependable inventory management program.
- The calculation of average inventory can be made extremely simple, automatic, and less prone to errors with the use of inventory management software.
For instance, barcodes and barcode scanners can be used to automate the process of stock counting. Every time you scan an item, the details about that item are recorded in your database so that whenever you need to calculate average inventory, you can quickly access all the information you need. This is especially helpful for companies who have a lot of inventory or for companies that have a lot of store-fronts, warehouses, or storage facilities.
Calculating Beginning Inventory in Your Business
You won't have any prior accounting periods to look to if you're beginning a new business.
You'll have to estimate your beginning inventory from start in this situation. This is how:
- Establish what each item in your inventory is worth.
- Total up the cost of every item in your inventory.
- Subtract the overall expense from the quantity of items in your inventory.
You will then know what your average cost per item is.
After that, you can use this figure to determine how much your initial inventory is worth.
- It's crucial to maintain track of your initial inventory if you run a firm that uses inventory.
- This can help you have a better understanding of your overall inventory expenses and enable you to choose your stock with greater knowledge.
- You must figure out the beginning inventory if you don't have the ending inventory from the prior accounting period.
- For the current accounting period, you must be aware of the ending inventory and cost of goods sold.
The following formula should be used to determine COGS:
COGS = Beginning Inventory + Purchases – Ending Inventory
To determine the beginning inventory, put the cost of goods sold into the following formula once you have it:
Beginning inventory = COGS – Purchases + Ending Inventory
Calculating Ending Inventory in Your Business
You must be aware of the beginning inventory, purchases, and sales for the period in order to calculate ending inventory. The equation is:
Ending inventory = Beginning Inventory + Purchases – Sales
How Do You Calculate Average Inventory in EOQ?
In order to help you strike a balance between keeping inventory on hand and placing orders, the economic order quantity (EOQ) is a tipping point in your inventory management.
You must know the annual demand for your product in order to calculate this amount. You should also be aware of the costs associated with placing a single order and maintaining a single unit for a whole year.
Once you have those figures, you can use a formula to determine your EOQ, or reorder quantity. This is how the complete formula is written:
EOQ = Square Root of [(2 x (Cost of One Order x Demand) / Cost of Holding One Unit for a Year]
Divide your EOQ by 2 to get the average inventory from your EOQ. Why? Essentially, the average amount of inventory you have should be around half of your EOQ, or the amount you're reordering, which brings us back to a major assumption the math makes.
The formula is as follows:
Average Inventory = EOQ/2
Therefore, you may use this formula to determine how much inventory you ought to have on hand if you're already figuring out your EOQ.
Formula is Effective for Multiple Inventory Systems
This formula is adaptable, as was previously noted. So this inventory statistic can be used with either perpetual or periodic inventory systems.
- Inventory management software refreshes your records in real-time when you use perpetual inventory.
- The only time your records are updated under a periodic inventory system is at the conclusion of each accounting period.
- The information required to determine your average is already available if you use a perpetual inventory system.
- Finding your beginning and ending inventory values for a certain time period is the first step. The average inventory formula is then applied to those figures.
- A periodic method does not provide you with a real-time inventory count of your available items.
The items you have on hand must be physically counted at the conclusion of each accounting period. After that, you may use those figures to enter into the method above to get your average.
Importance of Average Inventory
- Your inventory will change over time. A sizable delivery could arrive towards the end of the month. Or perhaps you're stocking up for a particular bargain.
- Your line of work can also be seasonal, such as selling frozen yogurt in the summer or Christmas décor in the winter.
- You won't always have a clear view of your inventory if you only consider one moment in time.
- You need to have a solid grasp of the big picture while negotiating with suppliers and making smart judgments regarding how much stock to acquire.
How much inventory will you require to fund the bottom line and support the sales? The typical inventory can be useful by providing you with the overview for a specific time.
Understanding how quickly you can convert inventory into sales depends on your typical inventory as well. This is accomplished using the days' sales of inventory (DSI) and the inventory turnover ratio.
The following are some crucial areas where an ERP or MRP (Material Requirements Planning) system can be helpful in:
- Monitor carrying costs
- Control production
- Evaluate work-in-progress costs
These solutions allow you to quickly view your manufacturing and material expenses. This simplifies your selling price computation in the end.
Relevance and Usage
Understanding purchase patterns and sales trends through inventory analysis enables management to better plan inventory to prevent stock-outs and the associated costs, which can put a burden on the business's budget. Further. It aids in the calculation of several beneficial ratios, including:
Inventory Turnover Ratio- The inventory turnover ratio is a useful indicator of how successfully your company can sell its goods and can be applied to stock management. For instance, if your inventory turnover ratio is poor, it's possible that your company is buying too much inventory or that there has been a breakdown in communication between the departments of sales and purchasing.
Determine how frequently you had to replenish over a specific period by calculating your inventory turnover ratio by dividing the average inventory by the cost of the inventory sold:
Inventory turnover rate = Cost of goods sold / Average inventory
Average Inventory Period- Inventory Turnover Ratio is another crucial ratio that management can use to gauge how quickly products are sold.
Average Inventory Period = (Number of Days in Period/Inventory Turnover Ratio)
- Inventory Turnover Ratio is another crucial ratio that management can use to gauge how quickly products are sold.
- The average number of days it takes a business to sell off all of its current inventory is known as the average inventory period.
- The average inventory period is a measure of how effectively a business can turn its stock into sales.
- A corporation with a lower AIP is more productive.
- AIP is typically computed over one-year intervals.
- Only compare the average inventory period to companies in similar industries.
- DSI requires two variables: Number of days in period and Inventory turnover.
Sales Support Calculations- In order to calculate the amount of inventory required to maintain a specific sales level, average inventory can be compared to revenues produced from income statements.
- These comparisons can be made between two or more accounting periods or even year-to-date.
- Finding the average number of units sold to earn a certain amount of sales income by comparing sales to average inventory figures.
- In order to ensure that enough completed goods or raw materials are accessible to fulfil orders, average inventory is a crucial component of sales planning.
However, it shouldn't be too high to increase warehousing and other related costs. But in order to account for shifting corporate, economic, and environmental changes—as was recently illustrated by the most recent pandemic—both inventory measures and inventory planning must be done on a frequent basis. The average inventory is only one of the inventory management's tools.
Benefits of Calculating Average Inventory
Comparison between Average Inventories
Average inventory can assist you understand the firm. Compare the average inventory totals for each quarter. The company can determine which quarter performs better and the precise cause of the fluctuation by doing a comparison analysis. You may also comprehend the things that were damaged, returned, or lost in transit.
Analyze the workings of the business
Inventory is essential to every organization. Now, inventory can take on any form, and it affects even the service sector.
- To determine which inventory performed better and which period performed better for their business, the companies calculate the average inventory several times throughout the operational year and compare the results.
- They can then refill their inventory appropriately and make the required preparations for the upcoming year.
- Due to rising demand, you might receive a sizeable delivery one month. Alternatively, perhaps you deal in seasonal products like ice cream in the summer and Christmas decorations in the winter.
- Because inventory levels change frequently in scenarios like this, viewing at one moment in time won't provide you a true picture of your inventory.
- The ability to identify trends and forecast future sales is another benefit of examining your average inventory. For instance, it may be a hint that you need to change your ordering procedure if you notice that your average inventory is gradually rising over time.
Resource capacity planning
If your average inventory is dropping, that can mean you're not placing enough orders to keep up with demand, which will result in a decline in overall sales volume.
- You can plan your resource capacity, such as storage space and manpower, by taking a look at your typical inventory.
- You can make plans based on your usual inventory levels if you are aware of them. For instance, you can rent a bigger storage container or hire extra staff to help handle everything if you need to keep more product during the holiday season.
In short, looking at your average inventory rather than just your present inventory might help you get a better sense of what your company needs. You can use it to identify patterns and improve your staffing and storage selections.
Pros of Inventory Formula
It's time to step back and consider the broader picture now that you understand how to use this formula. Although this formula is useful, it is not flawless.
Here are a few of the advantages.
Required for different numbers- As you'll see in the section below, you need this number to calculate other ratios, such as those that reveal how frequently you sell your complete inventory.
Flexibility- This method can be used to determine your average inventory for any particular time period. This formula might help you determine your average monthly or quarterly inventory.
Useful for planning- You can make sure you have the necessary quantity of units on hand to satisfy that demand if you are aware of your average inventory.
Challenges With Average Inventory
It is possible to get the average inventory period by dividing total sales by average inventory, but utilizing cost of goods sold is probably more accurate. It is essential to utilize the same calculation approach for both methods in order to do a "apples-to-apples" comparison of this measure between different businesses.
In particular industries, this rate may occasionally vary throughout various business cycles and exhibit some seasonality. For instance, during the holidays, retailers could face shorter inventory times and longer inventory periods during the summer. As a result, it's crucial to determine the average inventory period using a time-frame appropriate for the specific business sector.
Average inventory has a few downsides, although being helpful for inventory management:
Errors brought on by seasonal variations.
Inventory balances and average inventory are skewed if a company generates a significant share of its sales within a single season. Inventory balances typically peak unusually high immediately before a seasonal sales boom and plummet abnormally low following.
The quota element.
The month's end inventory balances will have a significant impact on the sales quotas and will encourage meeting those quotas. Therefore, when they are significantly below the typical inventory standards, the month-end inventory levels may also decline.
Errors occur when balances are estimated.
Up to a point, using estimated inventory balances could seem sufficient. It is not as accurate as employing actual counts of inventories, which are more accurate.
Inventory management accuracy can result in better reports, more accurate forecasts, and more profitability.
Different business settings
The industry in which your company operates, the health of the economy, what your competitors are doing, and more are factors that must be taken into account while making this assessment. When considering average inventory to guide any business decisions, businesses should consider all of these factors.
When a business has to correlate inventory with revenue, average inventory is still helpful despite these difficulties. Revenue is shown on income statements both monthly and annually. Your accountant can then determine how much capital was committed to meet the needed level of sales by comparing the year-to-date revenue on the income statement to the average inventory balance.
Issues With Using an Average Inventory Formula
The average inventory formula for valuing inventory has some drawbacks.
First, the calculation makes the assumption that all of the available inventory is sold evenly over the course of the year. Contrary to popular belief, some goods may sell more fast than others. If not taken into consideration appropriately, this could result in an incorrect inventory valuation.
Another issue is that the typical inventory model only takes the cost of products sold into account. It disregards other crucial elements like:
- Shrinkage
- Storage costs
- Insurance
- Manufacturing overhead
This may cause the real cost of inventories to be underestimated.
And lastly, price variations over time are not taken into account by the average inventory formula.
- The valuation of the inventory will change if prices increase or decrease. This is why it's crucial to monitor price changes and modify the formula as necessary.
- A typical inventory formula is nevertheless a useful tool for valuing items despite these difficulties.
- By taking into consideration these elements, you can obtain a more precise view of your actual inventory costs.
It's incomplete.
Although this method is straightforward to calculate, it could not provide you with a complete view of your inventory. For instance, seasonal sales can have a significant impact on your inventory levels since you'll have a significant rise in inventory as you prepare for them and after, you'll (ideally) be almost out of goods to sell.
A significant price differential between your products will also make it difficult to determine whether one expensive item or a number of cheaper ones are having an impact on your inventory since you're working with averages rather than precise quantities.
Can’t estimate potential changes
This equation explains what happened in the past and might assist you in making plans for the future. However, it is unable to estimate changes in your inventory levels or future trends.
Do You Require the Average Inventory for Each SKU?
While having the average inventory for every item on your shelves would be fantastic, it's generally not realistic, especially as your company expands. Concentrate on the products that are most in-demand and popular since you can't afford to run out of them.
Examine your product line to determine which things, in terms of average inventory, lead time, and ROI, you truly need to track. You can prevent running out of popular products that keep consumers coming back and increase your earnings by concentrating just on these essential things.
How can Deskera Help You?
As a manufacturer, you must keep track of your inventory stock. The condition of your inventory has a direct impact on production planning, people and machinery use, and capacity utilization.
Deskera MRP is the one tool that lets you do all of the above. With Deskera, you can:
- Control production schedules
- Compile a Bill of Materials
- Produce thorough reports
- Make your own dashboard.
Deskera ERP is a complete solution that allows you to manage suppliers, track supply chain activity in real time, and streamline a range of other company functions.
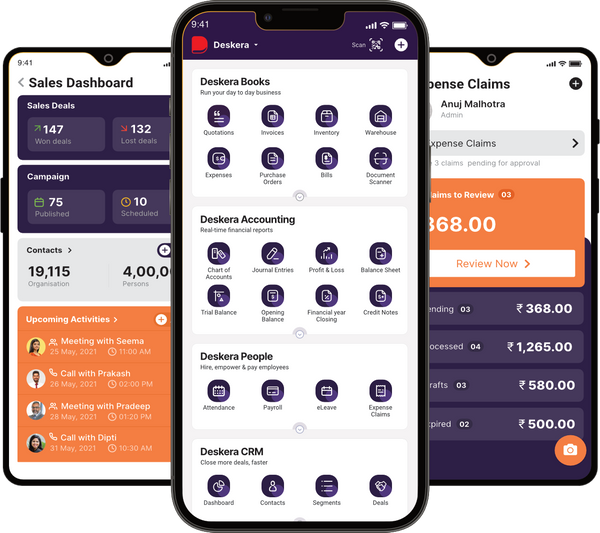
Deskera Books allows you to manage your accounts and finances better. It helps maintain good accounting standards by automating billing, invoicing, and payment processing tasks.
Deskera CRM is a powerful tool that organizes your sales and helps you close deals rapidly. It enables you to perform crucial tasks like lead generation via email and gives you a comprehensive view of your sales funnel.
Deskera People is a straightforward application for centralizing your human resource management activities. Not only does the technology expedite payroll processing, but it also helps you to handle all other operations such as overtime, benefits, bonuses, training programs, and much more.
Conclusion
Inventory helps in determining the amount of inventory investment needed to support a particular level of sales for the company. It is used to calculate how much inventory a company typically keeps on hand over a longer period of time.
The inventory level provided at the start of the measurement period and the conclusion of the measurement period are simply averaged. It is important because the Balance Sheet only shows the situation as of one specific date, whereas the Income Statement spans a period of time.
It makes sense to use Average when contrasting a company's inventory level with its sales level.
You should be able to conduct more accurate inventory operations with ease after you are aware of the average inventory formula. Your company's inventory is what makes it run and allows you to bring in money and make a profit.
You may maximise your revenues by managing your inventory profitably. It serves as a tool for comparison and aids in the analysis of the total revenue made by your company. Because knowing the calculations can have an effect on your company's bottom line, the work to compute the formula is worthwhile.
And it's easy as pie to use this formula! With the help of the method in this article, you will soon be tracking your inventory like an expert.
Key Takeaways
- It is the average inventory value over a specific period of time. The median value produced from the same data may or may not be identical to that value.
- Finding the average inventory and the cost of goods sold (COGS), which is a measurement of how much it costs to make your items including materials and labor, is the first step in calculating the inventory turnover ratio.
- As with inventory turnover ratio, lower DSI is often preferred, but industry-specific requirements may vary. To get a sense of performance, benchmark your DSI against similar businesses.
- The average quantity or value of your inventory over two or more accounting periods is known as average inventory.
- Comparing average inventory to other data points in a meaningful way is possible. By comparing average inventory to total sales volume over the same time period, for instance, one may monitor inventory losses caused by theft, damage, and shrinkage.
Related Articles

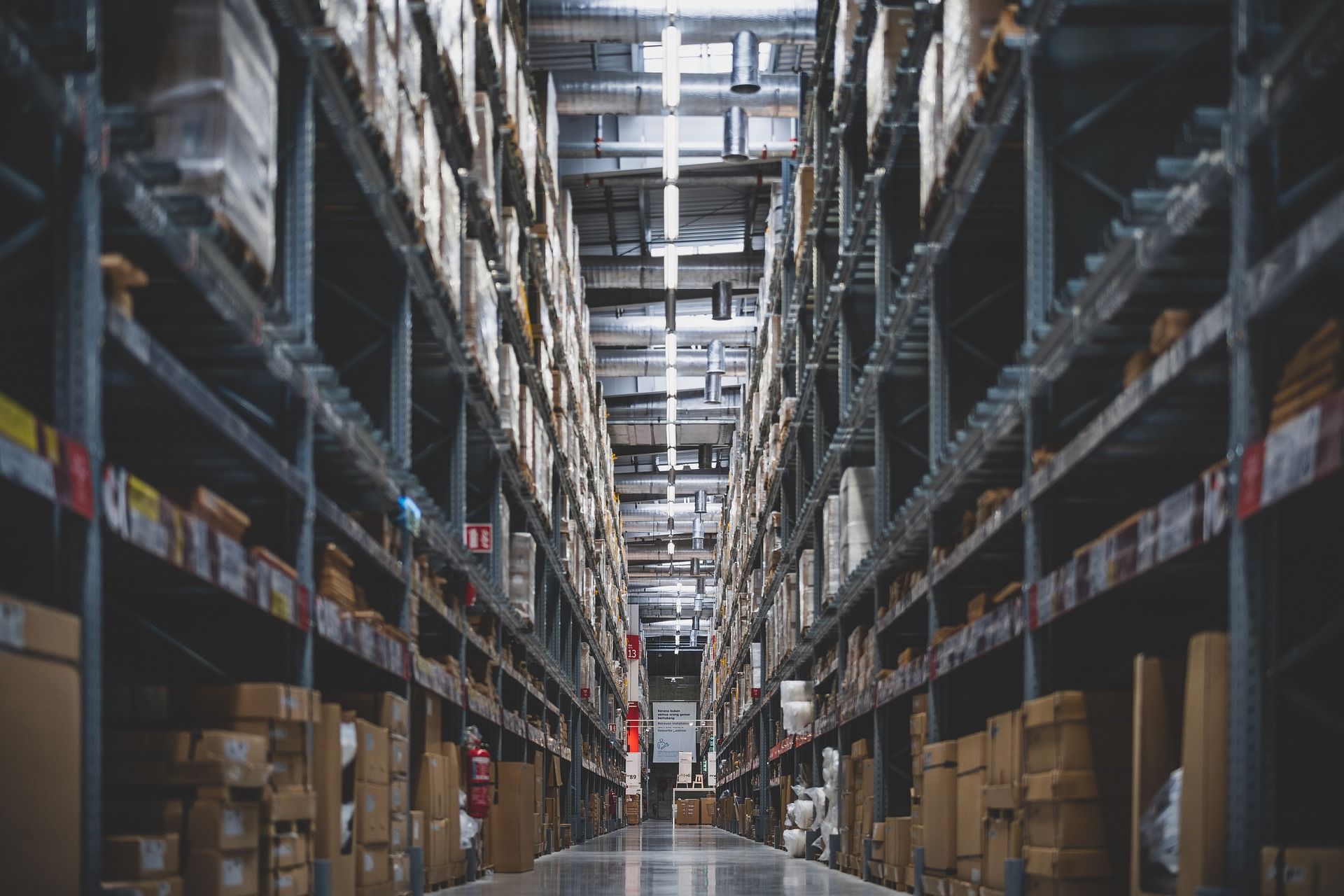