Managing furniture manufacturing budget could be a daunting task, especially when you are unsure of where your money needs to be invested. Moreover, tracking your expenses and making informed decisions about your budget can help you achieve financial stability and reach your organizational financial goals.
In this article, we will discuss practical tips for tracking expenses, identifying areas of overspending or underspending, and making informed decisions about reallocating resources. By following these steps, you can take control of your finances and achieve financial success.
Let’s take a look at the table of content:
- Importance of Managing Manufacturing Budget for Furniture Businesses
- Determine your Budget
- Prioritize your Spending
- Streamline your Processes
- Investing in Automation and Technology
- Monitoring and Adjusting your Budget
- Frequently Asked Questions (FAQs) Associated with Furniture Manufacturing Budget
- Wrapping Up
- How Deskera Can Assist You?
Let's get started!
Importance of Managing Manufacturing Budget for Furniture Businesses
Managing manufacturing budget effectively is crucial for the success of furniture businesses for several reasons:
Maximizing profitability: By managing their manufacturing budget effectively, furniture businesses can reduce costs and increase efficiency, which can lead to higher profitability.
Ensuring financial stability: Effective budget management can help furniture businesses avoid overspending or underestimating costs, which can lead to financial instability and even bankruptcy.
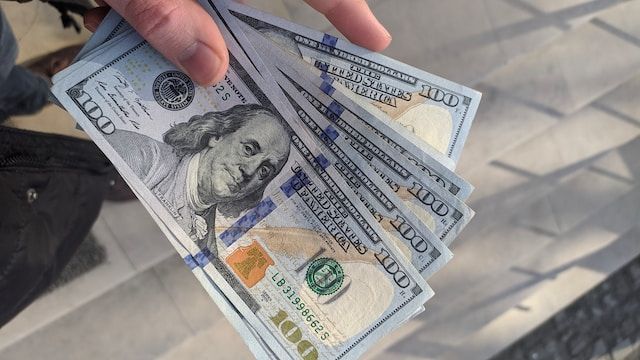
Enhancing competitiveness: Furniture businesses that manage their manufacturing budget effectively can offer more competitive prices and higher quality products, which can help them stand out in a crowded market.
Supporting growth: Proper budget management can provide furniture businesses with the financial resources necessary to invest in new technology, hire more staff, or expand their product lines, which can support growth and long-term success.
Improving customer satisfaction: Effective budget management can help furniture businesses ensure that they are producing high-quality products that meet customer expectations, which can lead to increased customer satisfaction and loyalty.
Overall, managing manufacturing budget effectively is essential for furniture businesses that want to succeed in a competitive and ever-changing market.
Determine your Budget
Determining a budget is a critical first step in managing manufacturing costs effectively for furniture businesses. Setting a realistic budget allows furniture manufacturers to allocate resources efficiently, reduce wastage, and maximize profitability.
A well-planned budget also enables furniture manufacturers to make informed decisions about investments, such as upgrading machinery or hiring new staff.
In this section, we will discuss some tips for calculating a budget for furniture manufacturing and factors to consider when setting a budget.
Importance of Setting a Realistic Budget based on your Company's Financial Situation
Setting a realistic budget based on a furniture company's financial situation is essential for several reasons:
Avoiding financial instability: A budget that is not based on a company's financial situation can lead to overspending or underestimating costs, which can result in financial instability or even bankruptcy.
Maximizing resources: A realistic budget helps furniture manufacturers allocate resources efficiently and effectively, allowing them to make the most of their available funds.
Supporting growth: A budget that is based on a company's financial situation can help furniture businesses identify areas where they can invest in new technology, hire new staff, or expand their product lines, which can support long-term growth and success.
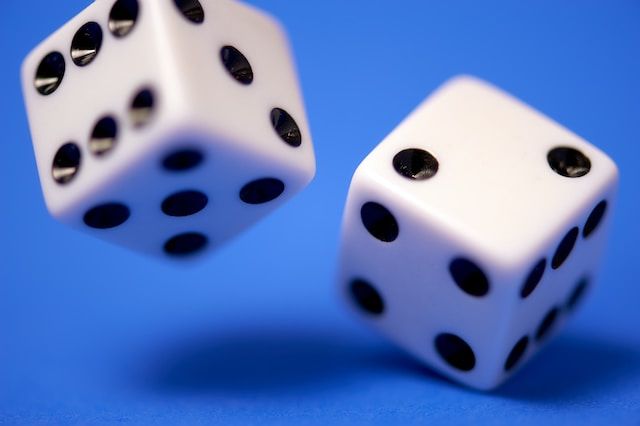
Managing risks: A realistic budget helps furniture manufacturers identify potential financial risks, such as unexpected expenses, and plan for them accordingly.
Overall, setting a realistic budget based on a furniture company's financial situation is crucial for financial stability, maximizing resources, supporting growth, and managing risks. By doing so, furniture manufacturers can make informed decisions about their business operations and investments, ultimately leading to increased profitability and success.
Tips for Calculating a Budget for Furniture Manufacturing
Here are some tips for calculating a budget for furniture manufacturing:
Review past financial statements: Reviewing past financial statements can help furniture manufacturers understand their revenue and expenses over a given period, which can provide insights into their cash flow and help in budget forecasting.
Consider industry benchmarks: Researching industry benchmarks for manufacturing costs and profitability can help furniture manufacturers set realistic goals for their budget and identify areas where they can improve.
Include all relevant costs: It's important to include all relevant costs when calculating a budget for furniture manufacturing, including direct costs such as materials and labor, as well as indirect costs such as overhead expenses and administrative costs.
Anticipate unexpected expenses: It's important to anticipate unexpected expenses, such as equipment repairs or increased material costs, when calculating a budget for furniture manufacturing. Building a cushion into the budget can help furniture manufacturers prepare for unforeseen costs and avoid financial instability.
Use forecasting techniques: Forecasting techniques, such as trend analysis or regression analysis, can help furniture manufacturers make informed decisions about their budget based on historical data.
Review and adjust regularly: It's important to review the budget regularly and adjust as necessary based on changing circumstances, such as changes in demand, production costs, or market conditions.
By following these tips, furniture manufacturers can create a realistic and effective budget that supports their business goals and maximizes profitability.
Examples of Factors that Should be Considered When Setting a Budget
When setting a budget for furniture manufacturing, it's important to consider several factors, including:
Sales projections: Furniture manufacturers should consider their projected sales volume when setting a budget, as this will impact their revenue and profitability.
Production costs: Production costs, including direct costs such as materials and labor, as well as indirect costs such as overhead expenses, should be factored into the budget.
Market trends: Furniture manufacturers should consider market trends, such as changes in consumer demand or competition, when setting a budget. This can help them make informed decisions about investments and resource allocation. Learn about demand forecasting here.
Economic conditions: Economic conditions, such as inflation or interest rates, can impact production costs and revenue, and should be considered when setting a budget.
Investment goals: Furniture manufacturers should consider their investment goals, such as upgrading machinery or expanding their product lines, when setting a budget. This can help them allocate resources effectively and make informed decisions about future investments.
Cash flow: Cash flow should be considered when setting a budget, as furniture manufacturers need to ensure they have sufficient funds to cover expenses and support ongoing operations.
Seasonality: Seasonality can impact demand and revenue for furniture manufacturers, and should be factored into the budget.
By considering these factors when setting a budget for furniture manufacturing, businesses can create a realistic and effective budget that supports their goals and maximizes profitability.
Prioritize your Spending
Prioritizing spending is a critical step in managing a furniture manufacturing budget effectively. By identifying and allocating resources to high-priority expenses, furniture manufacturers can maximize their return on investment and ensure that their budget supports their business goals.
In this section, we will discuss some tips for prioritizing spending in a furniture manufacturing budget and factors to consider when determining spending priorities.
Importance of Prioritizing Spending to Maximize the Value of your Budget
Prioritizing spending is essential for maximizing the value of a furniture manufacturing budget in several ways:
Focusing on high-priority expenses: Prioritizing spending allows furniture manufacturers to focus on high-priority expenses that have the greatest impact on their business operations and profitability. This ensures that resources are allocated efficiently and effectively, and that the budget supports the company's goals.
Maximizing return on investment: Prioritizing spending helps furniture manufacturers invest in areas that offer the greatest return on investment, such as upgrading machinery or investing in research and development. This can lead to increased profitability and long-term success.
Managing cash flow: Prioritizing spending helps furniture manufacturers manage their cash flow by ensuring that they allocate funds to essential expenses first, such as payroll and materials costs. This helps avoid financial instability and ensures that the business can continue to operate smoothly.
Identifying areas for cost savings: Prioritizing spending helps furniture manufacturers identify areas where they can cut costs, such as reducing overhead expenses or renegotiating supplier contracts. This can help reduce expenses and increase profitability.
Overall, prioritizing spending is crucial for maximizing the value of a furniture manufacturing budget. By focusing on high-priority expenses, maximizing return on investment, managing cash flow, and identifying areas for cost savings, furniture manufacturers can ensure that their budget supports their business goals and leads to long-term success.
Tips for Determining Which Areas to Prioritize Spending On
Here are some tips for determining which areas to prioritize spending on in a furniture manufacturing budget:
Identify essential expenses: Start by identifying essential expenses that are necessary for the business to operate, such as rent, payroll, and materials costs. These should be given the highest priority in the budget.
Consider revenue-generating opportunities: Consider opportunities that can generate revenue for the business, such as investing in marketing or expanding product lines. These opportunities should be given high priority in the budget, as they can have a significant impact on profitability.
Evaluate current infrastructure and equipment: Evaluate the current state of the business's infrastructure and equipment, and prioritize investments that can improve efficiency and productivity. Upgrading machinery, for example, can increase production capacity and reduce labor costs in the long run.
Assess risk and compliance requirements: Consider any regulatory compliance requirements or potential risks, and prioritize spending on areas that can mitigate those risks. For example, investing in cybersecurity measures can help protect the business from potential data breaches.
Review historical data: Review historical financial data, such as revenue and expense reports, to identify areas where the business has had success or struggled in the past. Furthermore, use this information to prioritize spending on areas that have the potential to generate the most positive impact on the business.
By using these tips to determine which areas to prioritize spending on, furniture manufacturers can create a budget that supports their business goals and maximizes profitability.
Examples of Areas that Furniture Manufacturers Commonly Prioritize Spending On
Furniture manufacturers commonly prioritize spending on the following areas:
Materials and supplies: Furniture manufacturers require high-quality materials and supplies to create their products. Investing in high-quality materials can improve the quality and durability of the furniture, which can lead to increased customer satisfaction and repeat business.
Labor: Labor costs are a significant expense for furniture manufacturers, but investing in skilled labor can lead to increased efficiency and productivity, which can reduce costs in the long run.
Machinery and equipment: Investing in machinery and equipment, such as computer-aided design (CAD) software and automated production lines, can increase production capacity and reduce labor costs.
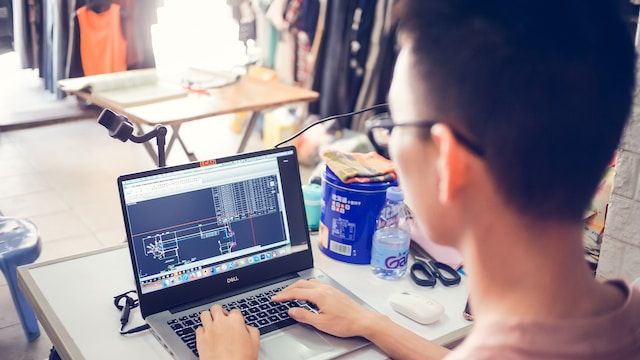
Research and development: Investing in research and development can help furniture manufacturers create innovative products that stand out in the market, and can also help improve the quality and durability of their existing products.
Marketing and advertising: Investing in marketing and advertising can help furniture manufacturers reach new customers and increase sales. This includes digital marketing, social media marketing, and traditional advertising methods.
Training and development: Providing training and development opportunities to employees can improve their skills and knowledge, which can increase productivity and reduce turnover.
Regulatory compliance: Investing in regulatory compliance measures, such as ensuring compliance with environmental regulations, can help furniture manufacturers avoid fines and legal issues.
By prioritizing spending on these areas, furniture manufacturers can create a budget that supports their business goals and maximizes profitability.
Streamline your Processes
Streamlining processes is an essential aspect of managing a furniture manufacturing budget effectively. By optimizing workflows and minimizing waste, furniture manufacturers can reduce costs, increase productivity, and improve product quality.
In this section, we will discuss some tips for streamlining processes in a furniture manufacturing business, and the benefits of doing so.
Benefits of Streamlining Manufacturing Processes
There are several benefits to streamlining manufacturing processes in a furniture manufacturing business, including:
Reducing costs: By identifying inefficiencies and minimizing waste, furniture manufacturers can reduce costs associated with materials, labor, and overhead expenses.
Increasing efficiency: Streamlining processes can help furniture manufacturers improve productivity, reduce cycle times, and increase output, which can lead to greater profitability.
Improving product quality: Streamlining processes can help furniture manufacturers identify and address quality issues, resulting in improved product quality and customer satisfaction.
Enhancing customer service: By streamlining processes, furniture manufacturers can improve their ability to meet customer needs, resulting in greater customer satisfaction and repeat business.
Improving employee morale: Streamlining processes can also improve employee morale by reducing frustration associated with inefficient workflows, resulting in a more engaged and productive workforce.
Overall, streamlining processes is an essential aspect of managing a furniture manufacturing budget effectively, and can lead to significant improvements in cost reduction, efficiency, product quality, customer service, and employee morale.
Tips for Identifying Inefficiencies in your Manufacturing Process
Here are some tips for identifying inefficiencies in a furniture manufacturing process:
Map out your current process: Start by mapping out the current process from start to finish. This will help you identify areas where work is duplicated, delayed, or not necessary.
Analyze data: Analyze data from past production runs to identify bottlenecks and other inefficiencies. This could include analyzing manufacturing cycle times, scrap rates, and material usage.
Identify unnecessary steps: Look for steps in the process that are not necessary or can be combined with other steps. This could include eliminating redundant quality checks or consolidating workstations.
Involve employees: Involve employees in the process of identifying inefficiencies. They may have valuable insights and ideas for improving workflows and reducing waste.
Implement continuous improvement practices: Adopt a continuous improvement mindset and regularly review and evaluate the manufacturing process to identify areas for improvement.
By using these tips, furniture manufacturers can identify inefficiencies in their manufacturing process and implement changes to streamline workflows, reduce waste, and improve efficiency.
Examples of Strategies for Streamlining Furniture Manufacturing Processes
Here are some strategies for streamlining furniture manufacturing processes:
Lean manufacturing: Lean manufacturing is a methodology that emphasizes the elimination of waste and the continuous improvement of processes. Furniture manufacturers can implement lean manufacturing techniques, such as value stream mapping, to identify and eliminate waste in their manufacturing process.
Automation: Automation can help furniture manufacturers streamline their manufacturing process by reducing the need for manual labor, increasing productivity, and reducing cycle times. Examples of automation in furniture manufacturing include CNC machines, robotic arms, and automated assembly lines.
Standardization: Standardizing processes, such as assembly procedures or quality control checks, can help reduce variability and errors in the manufacturing process. This can lead to improved product quality and increased efficiency.
Just-in-time (JIT) manufacturing: JIT manufacturing is a strategy that involves producing goods only when they are needed, reducing the amount of inventory and waste in the manufacturing process. Furniture manufacturers can implement JIT manufacturing by forecasting demand and adjusting production accordingly.
Cross-training employees: Cross-training employees on multiple tasks and workstations can help reduce bottlenecks in the manufacturing process and increase efficiency. This also allows for greater flexibility in staffing and scheduling.
By implementing these strategies, furniture manufacturers can streamline their manufacturing process, reduce costs, and improve efficiency, resulting in increased profitability and customer satisfaction.
Investing in Automation and Technology
Investing in automation and technology for furniture manufacturing can be a smart decision for companies looking to increase efficiency, reduce labor costs, and improve product quality.
With the advancement of technology, there are numerous opportunities to automate various processes in furniture manufacturing, such as cutting, sanding, drilling, and finishing.
Furthermore, the budget required for investing in automation and technology will depend on various factors such as the size of the operation, the type of technology being considered, and the specific needs of the company.
Costs Associated with Investing in Automation and Technology for Furniture Manufacturing
Some of the costs associated with investing in automation and technology for furniture manufacturing can include:
Equipment costs: This includes the cost of purchasing or leasing the machines, tools, and equipment required for automation.
Installation costs: Depending on the type of technology being implemented, installation costs may include setting up the equipment, rewiring the factory floor, and other related expenses.
Training costs: Workers will need to be trained on how to use the new technology and equipment, which may require additional costs.
Maintenance costs: Automation and technology require regular maintenance and repairs to ensure that they continue to operate efficiently.
Integration costs: Integrating the new technology with existing systems and processes may require additional costs.
In conclusion, investing in automation and technology for furniture manufacturing can be a significant investment, but it can provide numerous benefits in the long run, including increased productivity, improved product quality, and reduced labor costs. Companies should carefully evaluate their needs and budget before deciding on the most appropriate technology and equipment for their operation.
Tips for Selecting the Right Equipment and Integrating it into your Manufacturing Process
Following, we’ve discussed some tips for selecting the right equipment and integrating it into your furniture manufacturing process:
Define Your Equipment Needs: Before investing in new equipment, it's important to define your specific needs. Identify areas of your manufacturing process that could benefit from automation or equipment upgrades, and determine the specific functions you need the equipment to perform.
Research Your Options: Research various equipment options and manufacturers to determine which ones offer the best fit for your needs. Look for equipment that has a proven track record in the industry and offers the features you require.
Consider Your Budget: Determine how much you can afford to invest in new equipment, taking into account the potential return on investment. Consider the cost of installation, training, and maintenance when evaluating different options.
Get Input from Your Team: Involve your team in the decision-making process to get their input on what equipment will be most useful and how it will fit into your existing processes. This can also help to ensure buy-in and adoption of the new equipment.
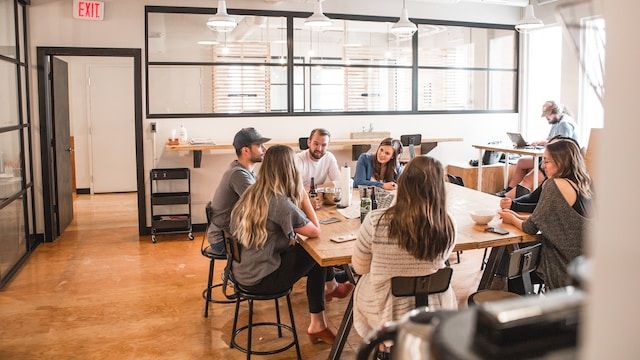
Plan for Integration: Plan how you will integrate the new equipment into your manufacturing process. Consider factors such as floor space, electrical and ventilation requirements, and how the new equipment will impact other parts of your production line.
Provide Adequate Training: Provide your team with proper training on how to use the new equipment. This will help to ensure it's used effectively and can also reduce the risk of accidents or damage.
Monitor and Evaluate Performance: Monitor the performance of your new equipment and evaluate how it's impacting your manufacturing process. This will help you identify any issues or opportunities for improvement, and make adjustments as needed.
By following these tips, you can select the right equipment for your furniture manufacturing process and integrate it effectively to improve efficiency, reduce costs, and increase productivity.
Monitoring and Adjusting your Budget
Monitoring and adjusting your budget are a critical process that helps you stay on track financially and achieve your financial goals. A budget is a plan that outlines your income and expenses over a specific period, typically a month or a year.
Monitoring and adjusting your budget involve regularly reviewing your actual income and expenses and making changes to ensure that you are meeting your financial objectives.
Monitoring your Budget Regularly and Making Adjustments as Needed
Monitoring your budget regularly and making adjustments as needed is crucial for several reasons:
Helps you stay on track: By monitoring your budget regularly, you can stay on track financially and ensure that you are not overspending. This will help you avoid debt and financial troubles in the future.
Enables you to identify areas of overspending: Regular monitoring of your budget will help you identify areas where you are overspending. This will allow you to make adjustments and cut back on expenses, which can help you save money.
Helps you achieve your financial goals: Monitoring your budget regularly and making adjustments as needed can help you achieve your financial goals. By tracking your progress, you can ensure that you are on track to achieving your goals and make changes if necessary.
Enables you to plan for unexpected expenses: Regular monitoring of your budget will help you plan for unexpected expenses such as medical emergencies, car repairs, or home repairs. This will help you avoid financial stress and ensure that you have enough savings to cover these expenses.
Enables you to adjust to changes in income: Your income may fluctuate from time to time, and regular monitoring of your budget will help you adjust to these changes. By making necessary adjustments, you can ensure that you are not overspending or underspending.
In conclusion, monitoring your budget regularly and making adjustments as needed is essential for maintaining financial stability and achieving your financial goals. By doing so, you can avoid overspending, identify areas for improvement, and plan for unexpected expenses, among other benefits.
Guidance to Make Informed Decisions About Reallocating Resources
Tracking expenses, identifying areas of overspending or underspending, and making informed decisions about reallocating resources can be achieved through the following steps:
Categorize your expenses: Start by categorizing your expenses into different categories such as housing, utilities, transportation, food, entertainment, and other expenses. This will help you understand where your money is going and identify areas where you may be overspending or underspending.
Track your expenses: Keep track of your expenses by recording them in a budgeting app or spreadsheet. Make sure to include all your expenses, including small purchases like coffee or snacks.
Analyze your expenses: Once you have tracked your expenses for a few weeks or months, analyze your spending habits. Furthermore, identify areas where you may be overspending or underspending. Look for patterns or trends in your spending.
Make informed decisions: Based on your analysis, make informed decisions about reallocating resources. If you are overspending in one category, consider cutting back on expenses in that category. If you are underspending in another category, consider allocating more resources to that category.
Set realistic goals: Set realistic goals for your budget based on your income and expenses. Make sure your goals are achievable and in line with your financial objectives.
Review and adjust regularly: Regularly review and adjust your budget as needed. This will help you stay on track financially and ensure that you are meeting your financial goals.
In conclusion, tracking expenses, identifying areas of overspending or underspending, and making informed decisions about reallocating resources is crucial for maintaining financial stability and achieving your financial goals. By categorizing your expenses, tracking your spending, analyzing your habits, setting realistic goals, and regularly reviewing and adjusting your budget, you can make the most of your resources and avoid overspending or underspending.
Frequently Asked Questions (FAQs) Associated with Furniture Manufacturing Budget
Following we've discussed some important frequently asked questions (FAQs) associated with furniture manufacturing budget. Let's learn:
Que 1: What are some common budgeting mistakes that furniture manufacturers make?
Ans: Some common budgeting mistakes that furniture manufacturers make include not accounting for all expenses, not regularly reviewing and adjusting budgets, and not setting realistic financial goals.
Que 2: How can furniture manufacturers reduce costs without sacrificing quality?
Ans: Furniture manufacturers can reduce costs without sacrificing quality by sourcing materials and supplies from cost-effective suppliers, streamlining production processes, optimizing inventory management, and investing in technology and automation.
Que 3: How can furniture manufacturers determine their ideal production volume?
Ans: Furniture manufacturers can determine their ideal production volume by analyzing historical sales data, forecasting future demand, and considering factors such as market trends and competition.
Que 4: What is the role of benchmarking in furniture manufacturing budgeting?
Ans: Benchmarking can help furniture manufacturers evaluate their financial performance against industry standards and identify areas for improvement. By benchmarking key performance metrics (KPIs) such as profitability and efficiency, manufacturers can set realistic goals and track progress towards achieving them.
Que 5: How can furniture manufacturers monitor and control expenses?
Ans: Furniture manufacturers can monitor and control expenses by creating a comprehensive budget, regularly reviewing and adjusting it, implementing cost-saving measures, and using financial reporting tools to track and analyze expenses.
Wrapping Up
In conclusion, making the most of your furniture manufacturing budget requires careful planning, efficient processes, and strategic investments.
By assessing your manufacturing needs, creating a realistic budget, maximizing efficiency, investing in technology and automation, and monitoring your budget regularly, you can optimize your operations and stay competitive in the industry.
Selecting the right equipment and integrating it effectively into your manufacturing process is a key part of this equation. By following the tips outlined in this article, you can make informed decisions about which equipment to invest in and how to integrate it successfully.
Ultimately, prioritizing budgeting and efficiency in your furniture manufacturing operations can help you achieve long-term success and profitability.
How Deskera Can Assist You?
Deskera's integrated financial planning tools allow investors to better plan their investments and track their progress. It can help investors make decisions faster and more accurately.
Deskera Books enables you to manage your accounts and finances more effectively. Maintain sound accounting practices by automating accounting operations such as billing, invoicing, and payment processing.
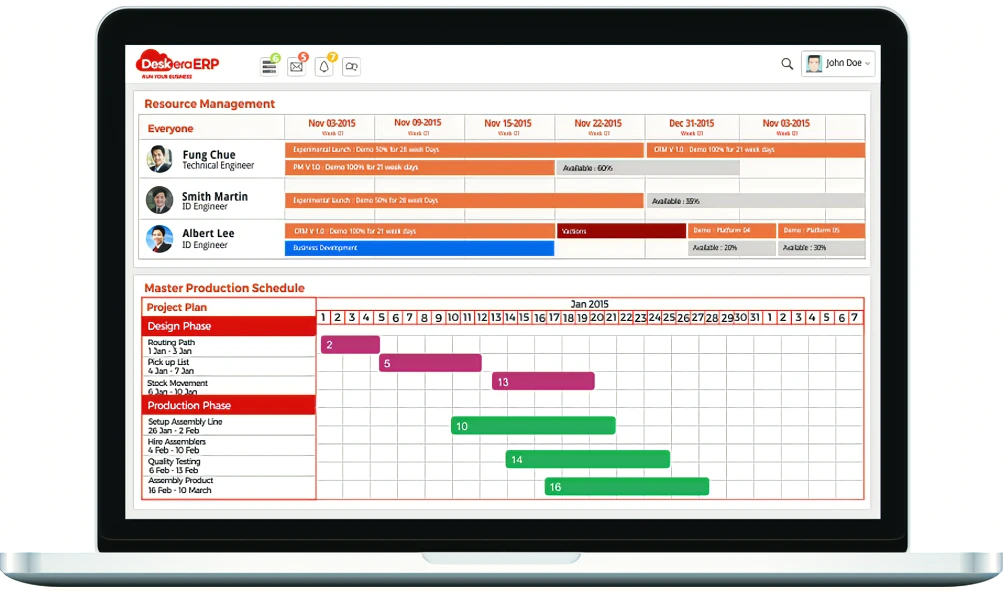
Deskera CRM is a strong solution that manages your sales and assists you in closing agreements quickly. It not only allows you to do critical duties such as lead generation via email, but it also provides you with a comprehensive view of your sales funnel.
Deskera People is a simple tool for taking control of your human resource management functions. The technology not only speeds up payroll processing but also allows you to manage all other activities such as overtime, benefits, bonuses, training programs, and much more. This is your chance to grow your business, increase earnings, and improve the efficiency of the entire production process.
Final Takeaways
We've arrived at the last section of this guide. Let's have a look at some of the most important points to remember:
- Determining a budget is a critical first step in managing manufacturing costs effectively for furniture businesses. Setting a realistic budget allows furniture manufacturers to allocate resources efficiently, reduce wastage, and maximize profitability.
- It's important to anticipate unexpected expenses, such as equipment repairs or increased material costs, when calculating a budget for furniture manufacturing. Building a cushion into the budget can help furniture manufacturers prepare for unforeseen costs and avoid financial instability.
- Prioritizing spending allows furniture manufacturers to focus on high-priority expenses that have the greatest impact on their business operations and profitability. This ensures that resources are allocated efficiently and effectively, and that the budget supports the company's goals.
- Consider opportunities that can generate revenue for the business, such as investing in marketing or expanding product lines. These opportunities should be given high priority in the budget, as they can have a significant impact on profitability.
- Automation can help furniture manufacturers streamline their manufacturing process by reducing the need for manual labor, increasing productivity, and reducing cycle times. Examples of automation in furniture manufacturing include CNC machines, robotic arms, and automated assembly lines.
- Monitor the performance of your new equipment and evaluate how it's impacting your manufacturing process. This will help you identify any issues or opportunities for improvement, and make adjustments as needed.
Related Articles
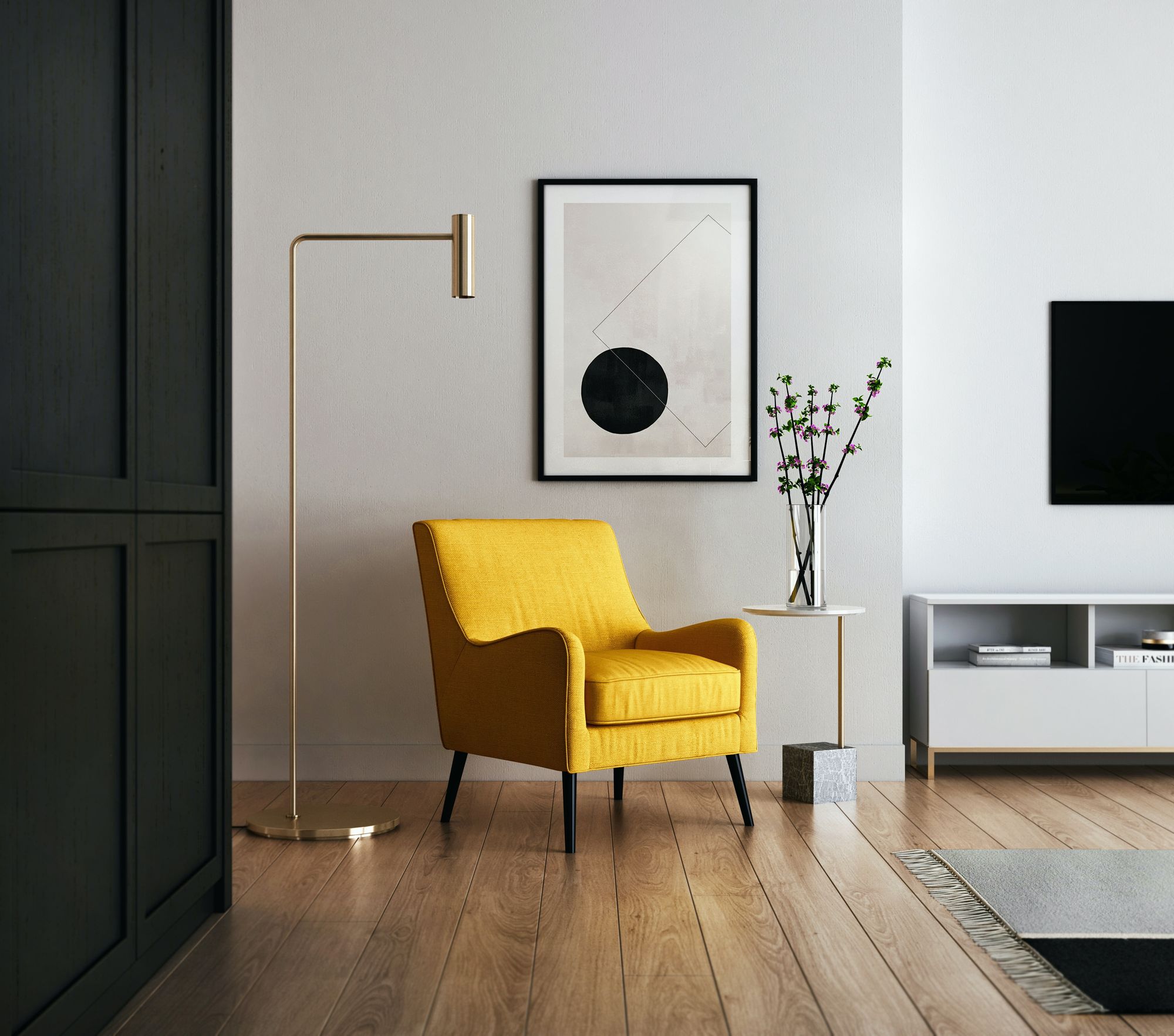
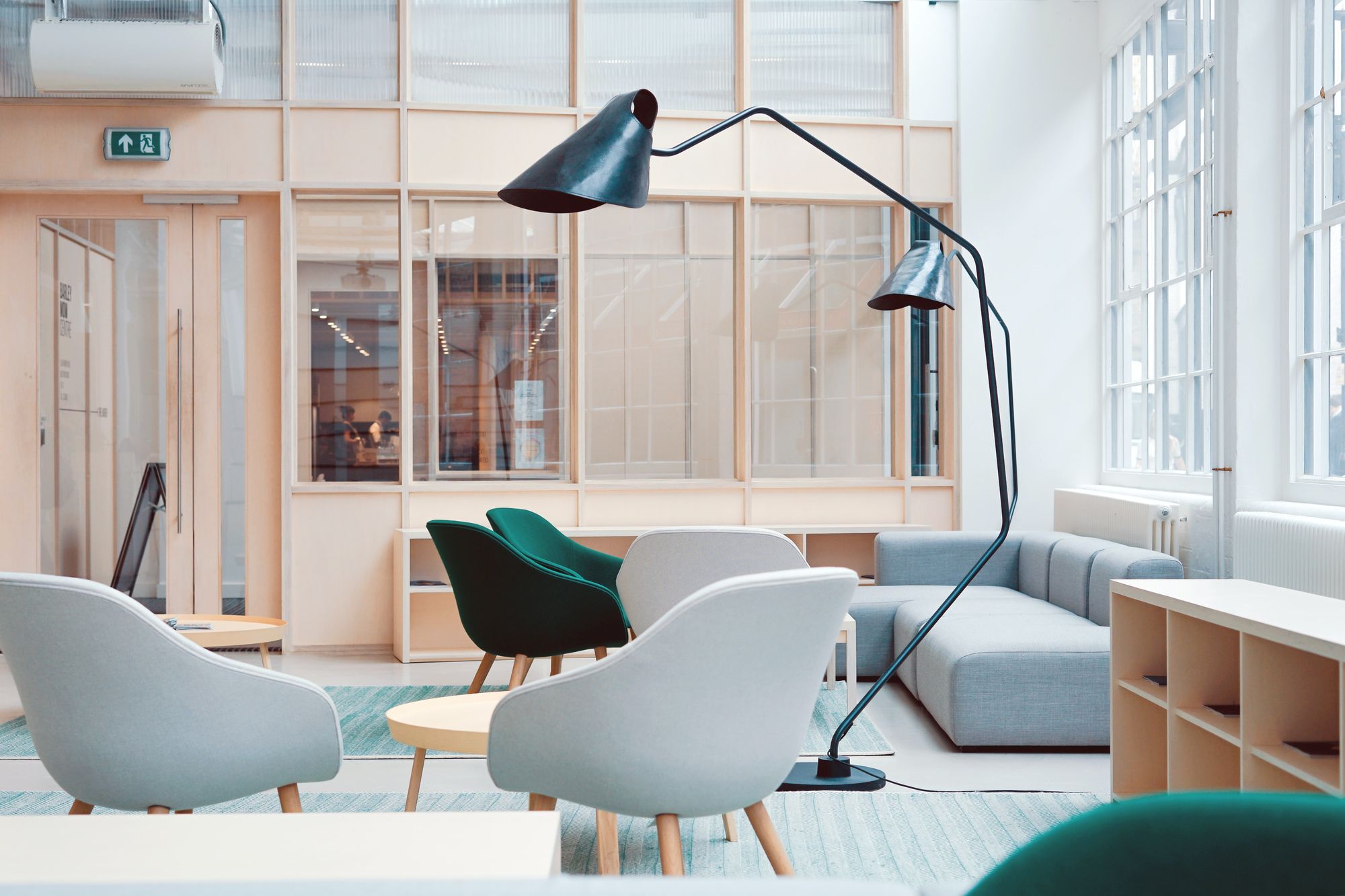
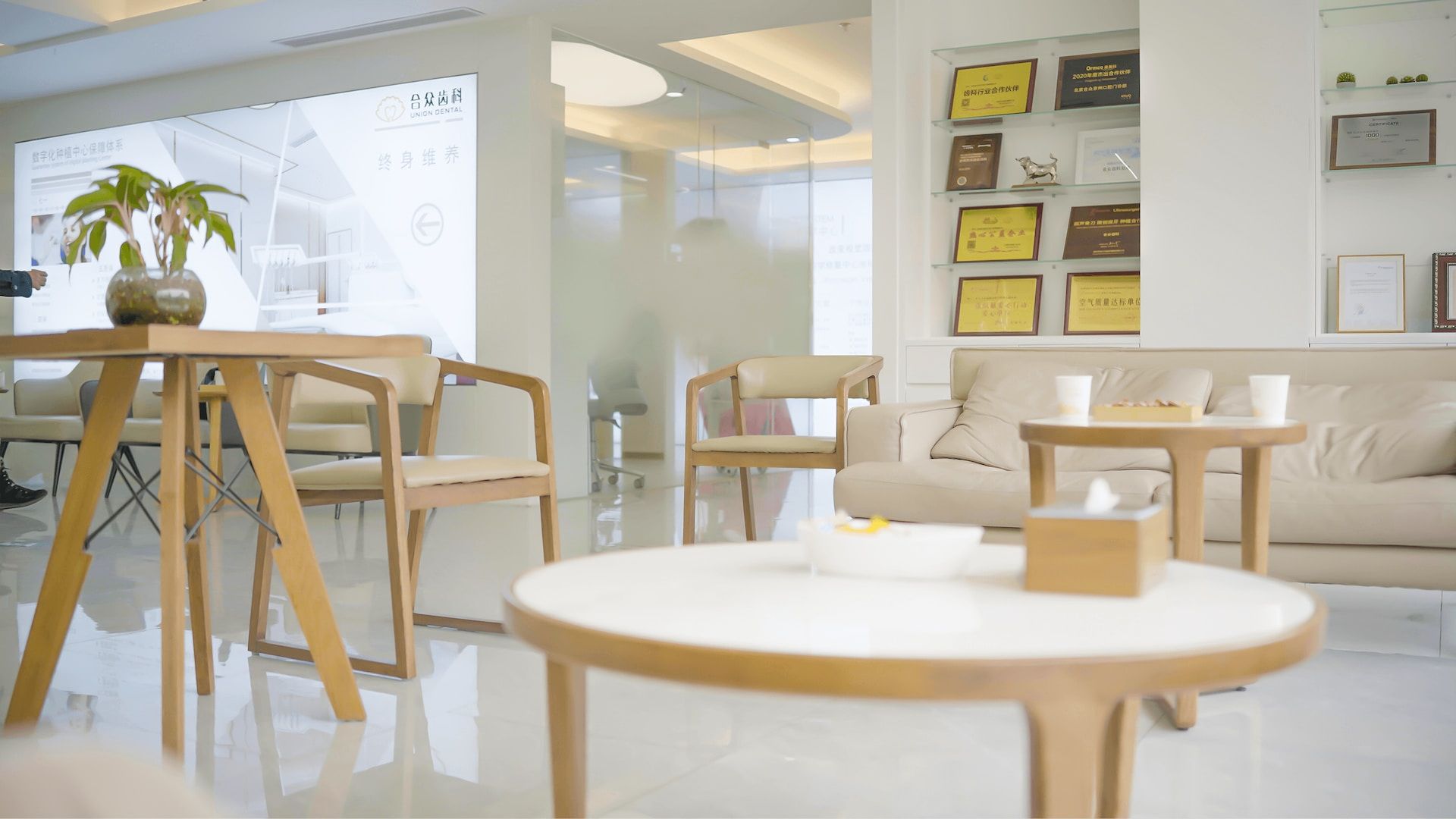
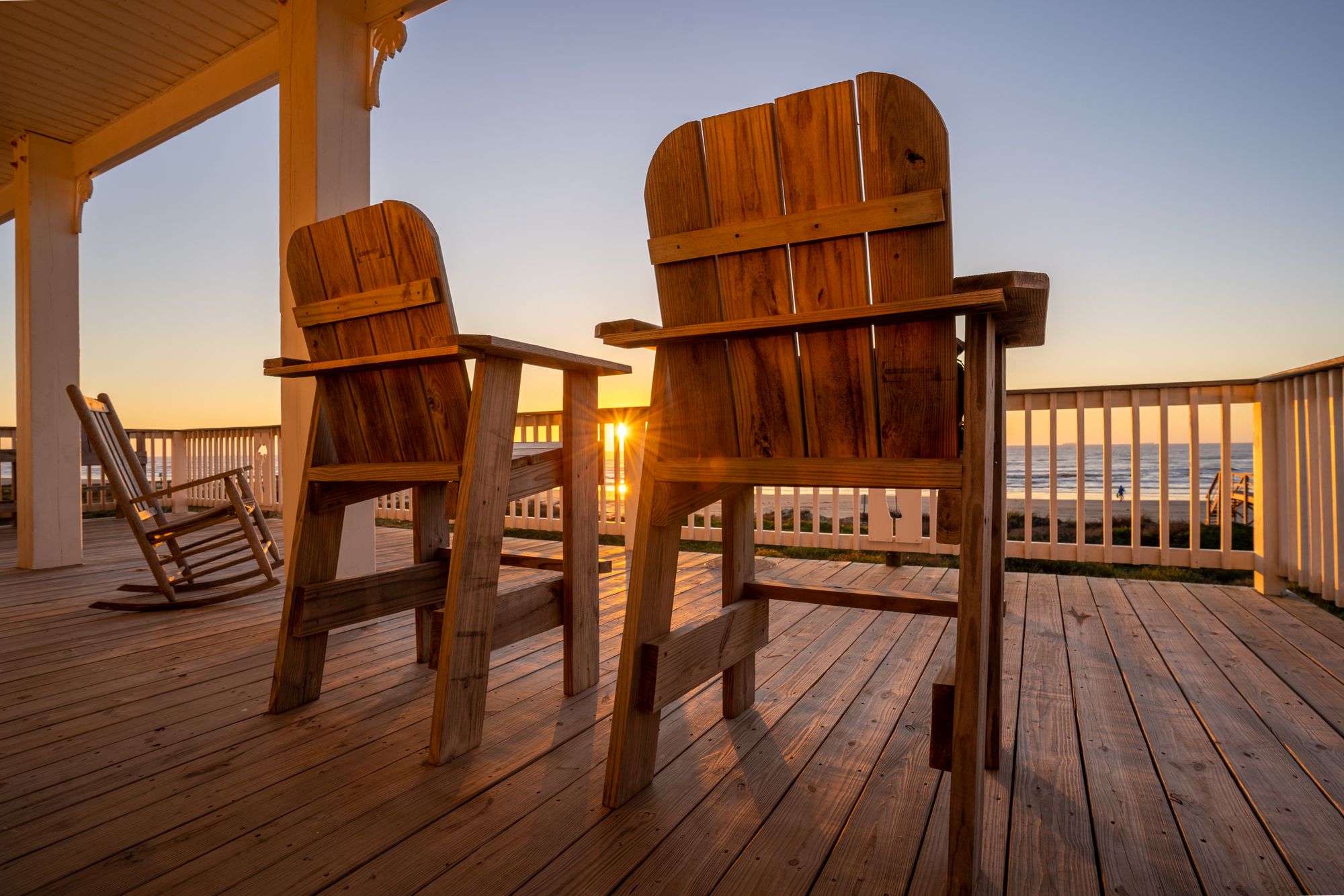
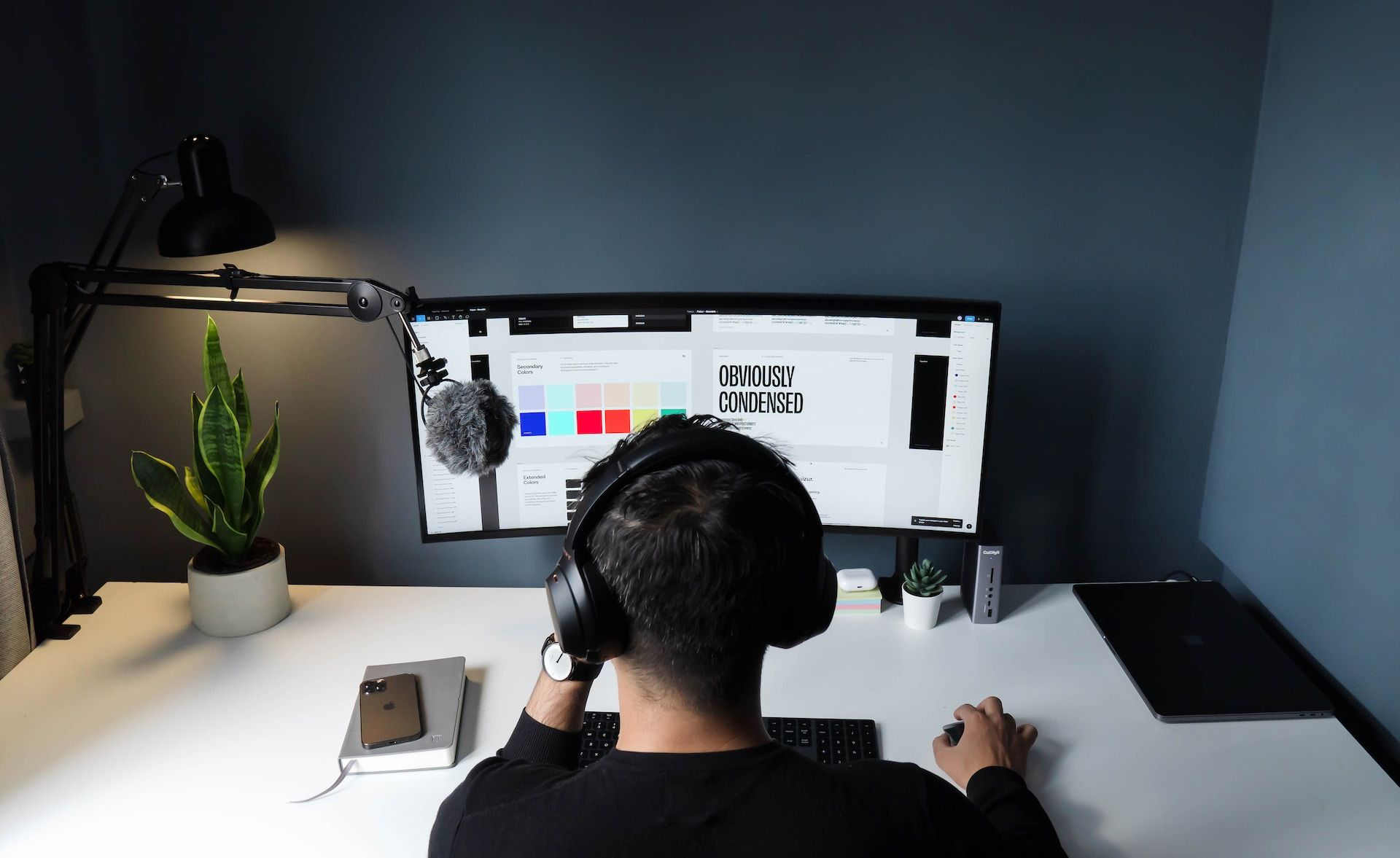