Designing for paper manufacturing is a crucial aspect of product development that is often overlooked. It involves creating designs that are optimized for the paper manufacturing process, with the aim of improving efficiency, reducing costs, and minimizing waste.
The global paper and pulp market was valued at $390 billion in 2020 and is projected to reach $480 billion by 2026, growing at a CAGR of 3.4% during the forecast period.
In today's world where sustainability is becoming increasingly important, designing for paper manufacturing can also help reduce the environmental impact of the manufacturing process.
This complete guide to designing for paper manufacturing will provide a comprehensive overview of the key factors that need to be considered when designing for paper manufacturing.
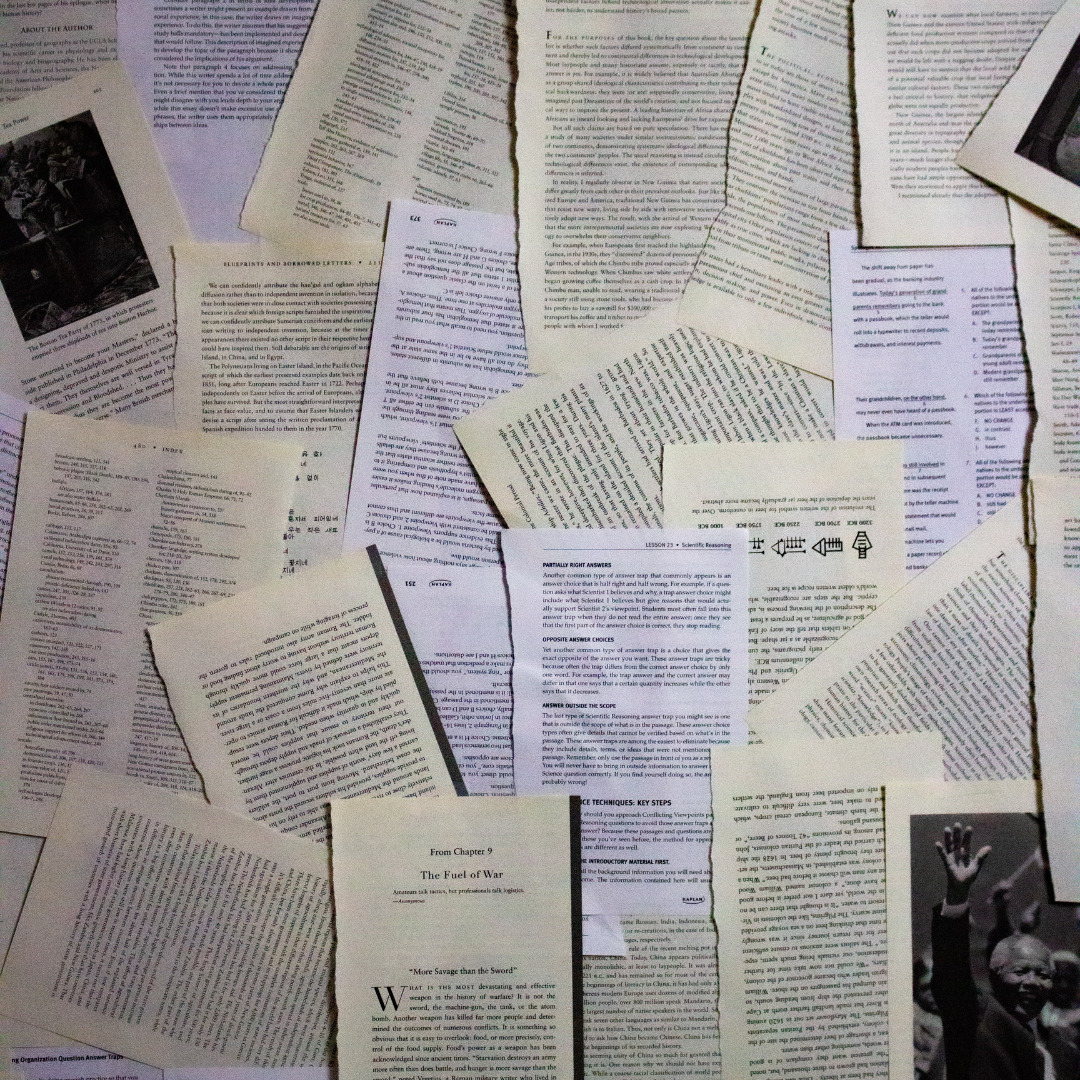
We will explore the paper manufacturing process, the different stages involved, and how the design of a product can affect the manufacturing process. We will also discuss the benefits of designing for paper manufacturing, including the economic benefits and the positive impact on the environment.
By the end of this guide, readers will have a clear understanding of how to design for paper manufacturing and the importance of doing so.
- Understanding the Paper Manufacturing Process
- Designing for Paper Manufacturing
- Common Challenges in Paper Manufacturing Design
- Benefits of Designing for Paper Manufacturing
- Relevance of MRP and ERP Systems in Paper Manufacturing Process
- How can Deskera Help You?
- Key Takeaways
- Related Articles
Understanding the Paper Manufacturing Process
The paper manufacturing process involves several stages that are essential in the production of paper products. While the process can vary depending on the type of paper being produced, the following are the most common stages involved in the paper manufacturing process:
- Wood Preparation: This stage involves the preparation of the wood chips for processing. The wood chips are washed and screened to remove impurities before they are sent to the next stage.
- Pulp Making: The wood chips are processed in a pulping machine that removes the lignin and other impurities. The resulting pulp is then washed and screened to remove any remaining impurities.
- Bleaching: The pulp is then bleached to remove any remaining impurities and to achieve the desired brightness level.
- Paper Making: The pulp is then mixed with water and other additives to form a slurry. This slurry is then poured onto a moving screen, which allows the water to drain away, leaving a layer of fibers behind.
- Pressing: The fibers are then pressed to remove any remaining water and to consolidate the paper.
- Drying: The paper is then dried using heated rollers or hot air.
- Finishing: The dried paper is then cut into the desired size and shape, and any final touches such as coatings or laminations are added.
It is important to note that the design of a product can significantly impact the paper manufacturing process. For instance, a product that requires a particular size or shape of paper may require additional steps in the manufacturing process, which can increase the cost and time of production. Therefore, it is essential to consider the manufacturing process when designing a product to ensure that it can be efficiently and cost-effectively produced.
Designing for Paper Manufacturing
Designing for paper manufacturing involves creating product designs that are optimized for the paper manufacturing process. This means taking into consideration the materials, production methods, and the manufacturing process itself when designing a product. By doing so, designers can create products that can be efficiently and cost-effectively produced, reducing waste and minimizing the environmental impact of the manufacturing process.
When designing for paper manufacturing, several factors need to be considered. These include the following:
Materials
When designing for paper manufacturing, designers need to consider the materials used in the manufacturing process. The materials used can significantly impact the manufacturing process, as well as the quality and properties of the final paper product. Here are some materials that are important when designing for paper manufacturing:
- Wood chips: Wood chips are the primary raw material used in the paper manufacturing process. They are used to create pulp, which is then used to make paper products. Designers need to consider the type of wood chips used, as well as the quality and purity of the wood chips, as these can affect the quality and properties of the final paper product.
- Chemicals: Chemicals are used in the paper manufacturing process to remove impurities from the pulp and to achieve the desired properties of the final paper product. Designers need to consider the type and quality of chemicals used, as well as the amount of chemicals used, as these can affect the quality and environmental impact of the final paper product.
- Water: Water is a critical component in the paper manufacturing process. Designers need to consider the quality and quantity of water used, as well as the water treatment processes used, as these can affect the environmental impact of the paper manufacturing process.
- Additives: Additives are used in the paper manufacturing process to improve the quality and properties of the final paper product. These can include fillers, dyes, coatings, and other materials. Designers need to consider the type and quality of additives used, as well as the amount of additives used, as these can affect the quality and environmental impact of the final paper product.
By carefully considering the materials used in the paper manufacturing process, designers can create product designs that are optimized for paper manufacturing, reducing waste and improving the sustainability of the manufacturing process.
Production Methods
The production methods used in paper manufacturing can vary depending on the type of paper being produced. Here are some of the most common production methods used in paper manufacturing:
- Mechanical pulp: Mechanical pulp is produced by grinding wood chips against a rough surface, such as a stone or a metal plate. This process separates the fibers from the wood chips, creating a pulp that is suitable for making newsprint and other low-quality paper products.
- Chemical pulp: Chemical pulp is produced by cooking wood chips with chemicals, such as sodium hydroxide and sodium sulfide. This process breaks down the lignin in the wood chips, allowing the fibers to separate and form a pulp that is suitable for making higher-quality paper products.
- Recycled pulp: Recycled pulp is produced by recycling paper products, such as newspapers and cardboard boxes. The paper products are first shredded and then mixed with water to create a pulp that can be used to make new paper products.
- Coated paper: Coated paper is produced by adding a coating to the paper surface. The coating can be made from various materials, such as clay or latex, and it can improve the quality and properties of the final paper product.
- Tissue paper: Tissue paper is produced using a special process that involves stretching and thinning the paper fibers. This process creates a soft and absorbent paper product that is suitable for use as facial tissue, toilet paper, and other similar products.
When designing for paper manufacturing, designers need to consider the production methods used for the paper product they are designing. This can impact the design requirements, such as the size and shape of the paper, the type of paper used, and the coatings or additives required.
By considering the production methods used, designers can create product designs that are optimized for paper manufacturing, reducing waste and improving the efficiency of the manufacturing process.
Manufacturing Process
The design of a product can significantly impact the manufacturing process. Therefore, designers need to consider the manufacturing process when designing a product. For instance, they need to ensure that the product can be efficiently produced without requiring additional steps that can increase the cost and time of production.
Designing for paper manufacturing can provide several benefits, including cost savings, increased efficiency, and improved sustainability. By creating designs that are optimized for paper manufacturing, designers can reduce waste, improve the environmental impact of the manufacturing process, and create products that are cost-effective and efficient to produce.
Common Challenges in Paper Manufacturing Design
Designing for paper manufacturing comes with its own set of challenges. Here are some of the common challenges faced in paper manufacturing design:
- Fiber quality: The quality of the fiber used in paper manufacturing can significantly impact the quality of the final paper product. Poor quality fibers can result in weak or low-quality paper products. Therefore, designers need to consider the quality of the fiber when designing a product.
- Process variability: The paper manufacturing process can be complex and involves multiple steps, which can result in process variability. Variability in the process can impact the quality and properties of the final paper product. Therefore, designers need to consider the process variability when designing a product to ensure that it can be consistently produced.
- Environmental impact: Paper manufacturing can have a significant environmental impact, such as deforestation, water pollution, and greenhouse gas emissions. Designers need to consider the environmental impact of the manufacturing process when designing a product and strive to create designs that are environmentally sustainable.
- Production efficiency: Paper manufacturing can be a labor-intensive and time-consuming process. Therefore, designers need to consider the production efficiency when designing a product. They need to create designs that can be efficiently and cost-effectively produced, reducing waste and improving the efficiency of the manufacturing process.
- Cost: Paper manufacturing can be expensive, with raw materials, chemicals, and energy costs being significant contributors. Designers need to consider the cost of the materials and the production process when designing a product, ensuring that the design is cost-effective and can be produced at a reasonable cost.
By addressing these challenges, designers can create product designs that are optimized for paper manufacturing, reducing waste, improving the efficiency of the manufacturing process, and producing high-quality paper products.
Benefits of Designing for Paper Manufacturing
Designing for paper manufacturing can provide numerous benefits, including:
- Improved product quality: By designing for paper manufacturing, designers can ensure that the final paper product meets the desired quality and performance standards. This can result in a better end-user experience and increased customer satisfaction.
- Reduced waste: Designing for paper manufacturing can help reduce waste by optimizing the design of the product to minimize the amount of material used and reduce production inefficiencies. This can also help reduce manufacturing costs and improve the overall sustainability of the manufacturing process.
- Increased production efficiency: Designing for paper manufacturing can help streamline the production process by optimizing the design for efficient manufacturing. This can result in faster production times, reduced downtime, and increased production capacity.
- Environmental sustainability: By designing for paper manufacturing, designers can create products that are environmentally sustainable by reducing waste, minimizing the use of natural resources, and optimizing the manufacturing process. This can help reduce the environmental impact of the manufacturing process and improve the overall sustainability of the product.
- Cost savings: Designing for paper manufacturing can help reduce the cost of manufacturing by optimizing the design for efficient production and reducing waste. This can result in cost savings for both the manufacturer and the end-user.
By considering the manufacturing process when designing a product, designers can create products that are optimized for paper manufacturing, resulting in high-quality, cost-effective, and sustainable products.
Relevance of MRP and ERP Systems in Paper Manufacturing Process
MRP (Material Requirements Planning) and ERP (Enterprise Resource Planning) systems play a critical role in the paper manufacturing process. Here's why:
- Material planning: MRP systems are designed to manage and plan material requirements, including raw materials, chemicals, and energy, for the production process. In paper manufacturing, MRP systems can help optimize the use of resources by forecasting demand and determining the required inventory levels.
- Production scheduling: MRP and ERP systems can help schedule and manage the production process, ensuring that the production is completed on time, and the materials are available for production.
- Cost management: MRP and ERP systems can help manage costs by providing real-time visibility into material usage, labor, and overhead costs. This can help manufacturers optimize their cost structures and improve profitability.
- Quality control: ERP systems can help monitor and manage quality control processes, ensuring that the final paper product meets the required quality standards.
- Environmental sustainability: MRP and ERP systems can help manage the environmental impact of the manufacturing process by tracking and reporting on energy and resource usage. This can help manufacturers optimize their resource usage and minimize waste.
- Supply chain management: ERP systems can help manage the supply chain, including supplier relationships, inventory management, and logistics. This can help manufacturers optimize their supply chain and ensure that materials are available when needed.
How can Deskera Help You?
Deskera ERP and MRP systems help you to keep your business units organized. The system's primary functions are as follows:
- Keep track of your raw materials and final items inventories
- Control production schedules and routings
- Keep a bill of materials
- Produce thorough reports
- Make your own dashboards
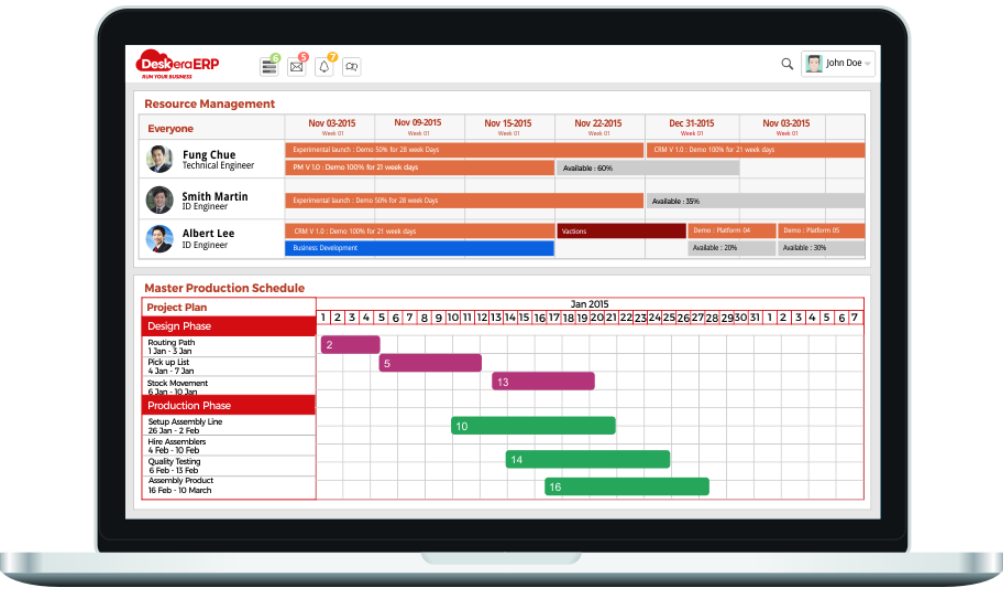
Deskera's integrated financial planning tools enable investors to better plan and track their investments. It can assist investors in making faster and more accurate decisions.
Deskera Books allows you to better manage your accounts and finances. Maintain good accounting practices by automating tasks like billing, invoicing, and payment processing.
Deskera CRM is a powerful solution that manages your sales and helps you close deals quickly. It not only enables you to perform critical tasks like lead generation via email, but it also gives you a comprehensive view of your sales funnel.
Deskera People is a straightforward tool for centralizing your human resource management functions.
Key Takeaways
- Designing for paper manufacturing involves considering the manufacturing process when designing a product to optimize its production.
- The paper manufacturing process involves several stages, including pulping, bleaching, papermaking, and finishing.
- Paper manufacturers use different production methods, such as batch, continuous, and hybrid, to produce paper products.
- Designers face common challenges in paper manufacturing, such as designing for efficiency, reducing waste, and ensuring quality control.
- Materials required for designing for paper manufacturing include pulp, chemicals, and energy.
- Designing for paper manufacturing provides benefits such as improved product quality, reduced waste, increased production efficiency, environmental sustainability, and cost savings.
- MRP and ERP systems are critical in the paper manufacturing process as they help manage material requirements, production scheduling, cost management, quality control, environmental sustainability, and supply chain management.
- Designing for sustainability in paper manufacturing is crucial to reduce the environmental impact of the manufacturing process.
- Collaboration between designers, engineers, and paper manufacturers can lead to better-designed products that meet manufacturing requirements and result in high-quality, cost-effective, and sustainable products.
- By considering the manufacturing process when designing a product, designers can create products that are optimized for paper manufacturing, resulting in better efficiency, cost savings, and a more sustainable manufacturing process.
Related Articles
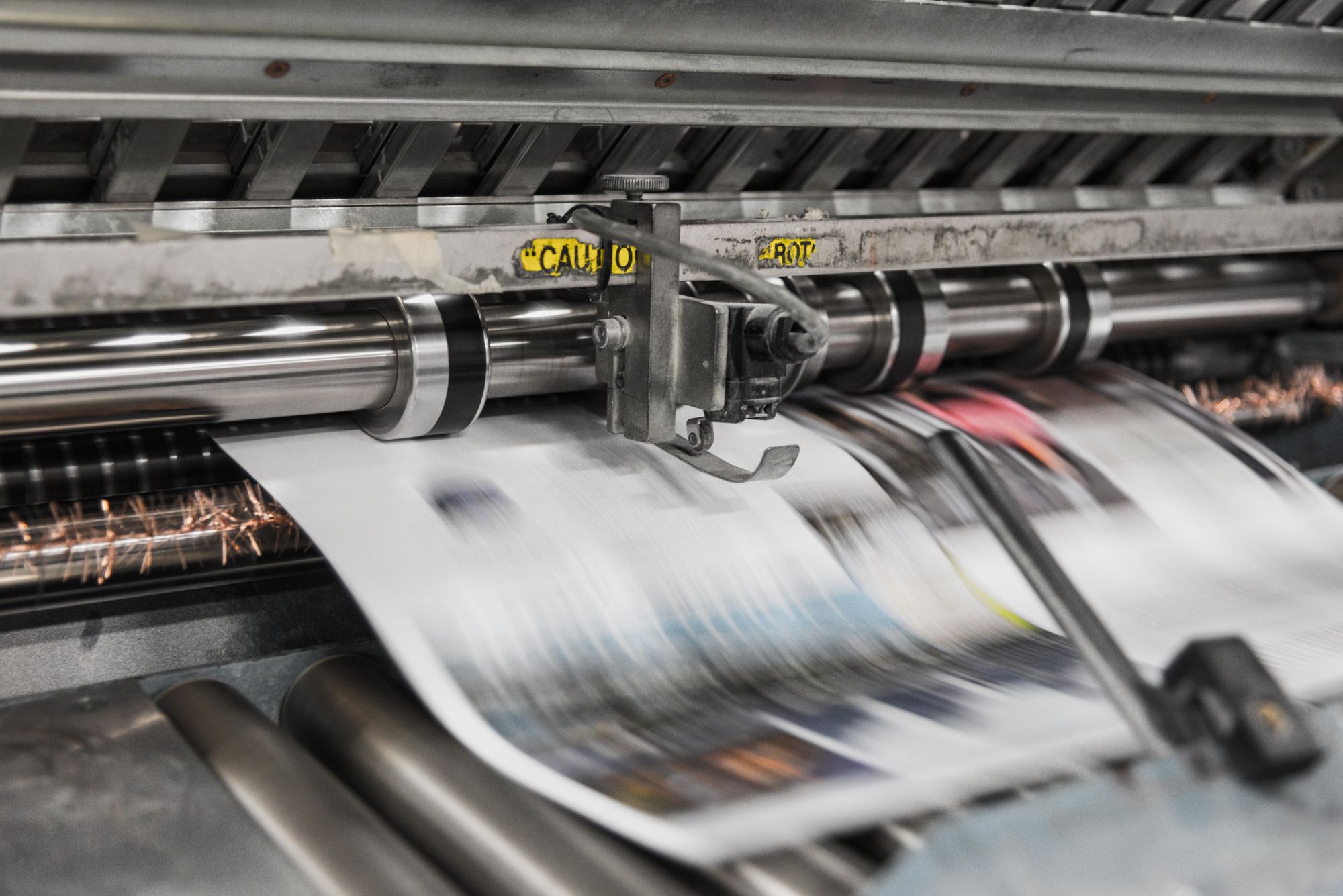
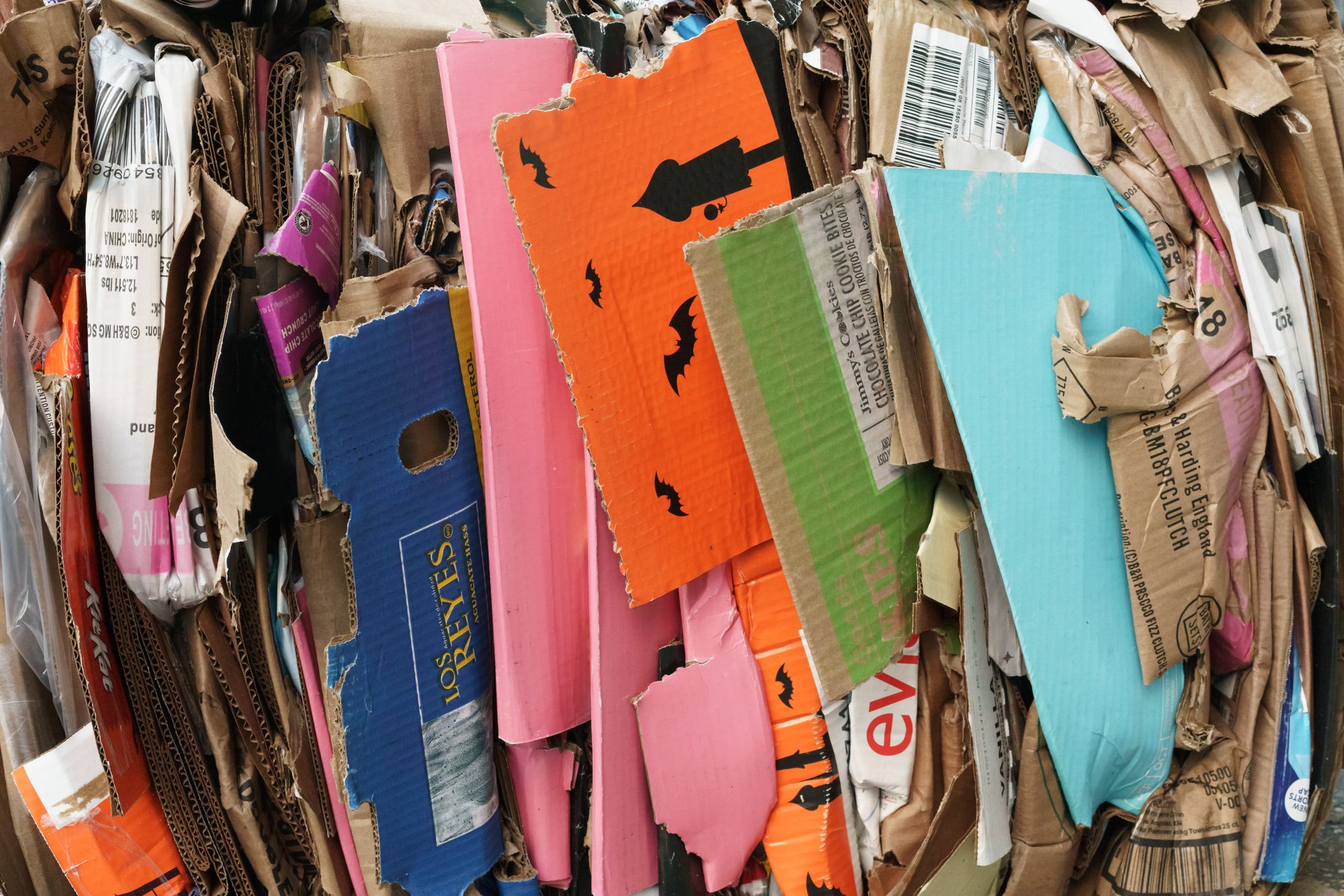
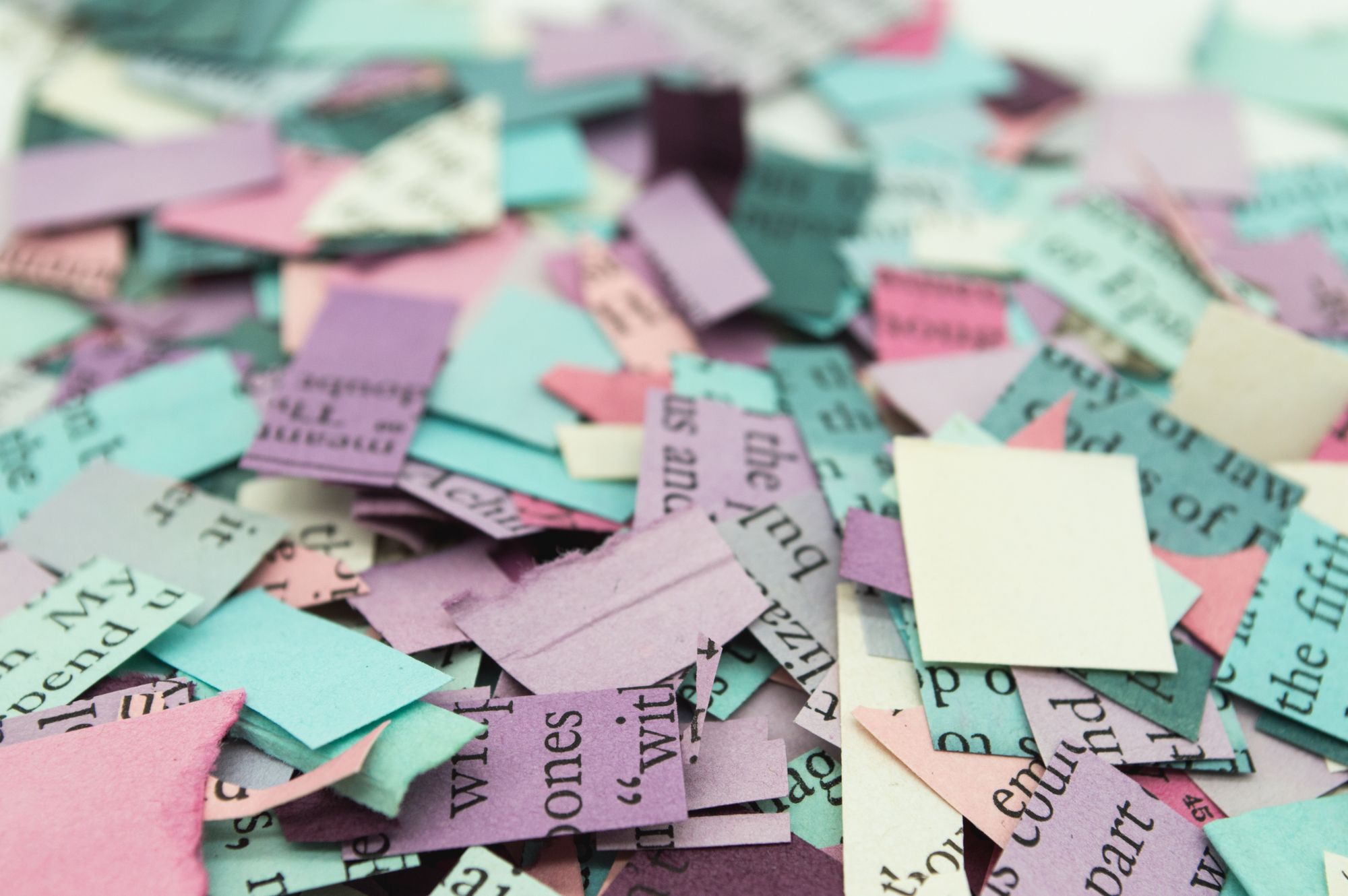
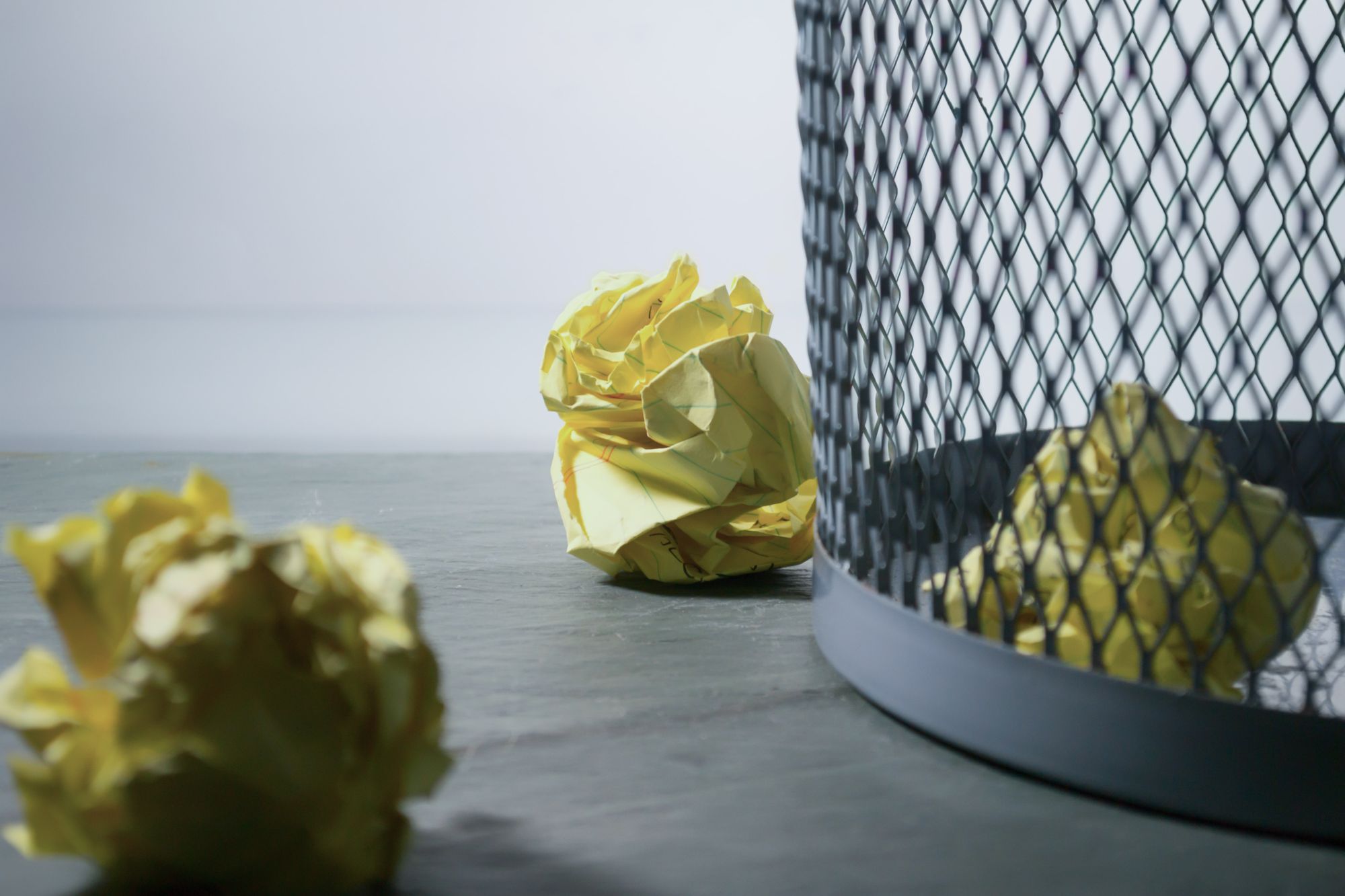