Hazardous chemicals are widely used in the manufacturing process and can pose a potential threat to human health and the environment. Effective management of hazardous chemicals is essential to minimize risk and ensure compliance with regulations. This article discusses new strategies for managing hazardous chemicals in manufacturing, including identification, substitution, engineering controls, administrative controls, personal protective equipment, hazardous waste management, emergency planning and response, and continuous improvement.
Managing hazardous chemicals in the manufacturing process is crucial to ensure the safety of workers, the environment, and the public.
Here are some strategies that can be implemented to manage hazardous chemicals effectively:
- Hazard Communication Program
- Substitution
- Engineering Controls
- Administrative Controls
- Personal Protective Equipment (PPE)
- Hazardous Waste Management
- Emergency Planning and Response
- Continuous Improvement
- How can Deskera Help You?
- Key Takeaways
- Related Articles
Hazard Communication Program
A Hazard Communication Program (HCP) is a workplace program designed to protect employees from hazardous chemicals. The HCP is required by law in the United States under the Occupational Safety and Health Administration's (OSHA) Hazard Communication Standard (HCS) 29 CFR 1910.1200. The HCP includes a set of procedures, policies, and practices that identify and communicate the risks associated with hazardous chemicals to employees and other potentially affected parties.
The HCP typically includes the following elements:
- Hazard identification: This involves identifying and evaluating the hazardous chemicals present in the workplace. The employer must maintain a comprehensive inventory of all hazardous chemicals used, stored, or produced in the workplace.
- Labeling: The employer must ensure that all containers of hazardous chemicals are labeled with the appropriate hazard warning. The labeling must include the product name, manufacturer's name and address, and hazard warnings, such as "flammable" or "corrosive."
- Safety Data Sheets (SDS): The employer must maintain an SDS for each hazardous chemical in the workplace. The SDS provides detailed information about the chemical, including its properties, health effects, and safe handling procedures.
- Employee training: Employers must train employees on the hazards of the chemicals in the workplace, how to read labels and SDSs, and the safe handling and use of the chemicals.
- Hazard communication program review and evaluation: Employers must regularly review and update their HCP to ensure that it remains effective and up-to-date with new chemicals, processes, or regulations.
The Hazard Communication Program helps to protect employees from exposure to hazardous chemicals by ensuring that they have access to information about the risks associated with the chemicals and how to safely handle and use them. The program is a critical component of any workplace safety and health program and must be implemented in all workplaces that use hazardous chemicals.
Substitution
Substitution is a strategy for managing hazardous chemicals that involves replacing hazardous substances or processes with less hazardous alternatives. The goal of substitution is to eliminate or reduce the risks associated with the use of hazardous chemicals.
Substitution can take various forms, including:
- Chemical substitution: This involves replacing a hazardous chemical with a less hazardous alternative. For example, using a less toxic cleaning agent instead of a highly toxic one.
- Process substitution: This involves replacing a hazardous process with a safer one. For example, using water-based paints instead of solvent-based paints.
- Product substitution: This involves replacing a hazardous product with a safer one. For example, using lead-free solder instead of lead-based solder.
The benefits of substitution include:
- Reduced exposure to hazardous chemicals: By replacing hazardous chemicals with less hazardous alternatives, workers are less likely to be exposed to harmful substances.
- Improved worker safety and health: By reducing the risks associated with the use of hazardous chemicals, substitution can help to improve worker safety and health.
- Environmental benefits: Substitution can also have environmental benefits by reducing the release of hazardous substances into the environment.
- Compliance with regulations: Substitution can help employers comply with regulations related to hazardous chemicals and protect them from legal liabilities.
Substitution requires careful evaluation of the hazards associated with the chemicals or processes and identification of safer alternatives. It may require changes in equipment, work practices, or procedures. However, the benefits of substitution often outweigh the costs and can lead to long-term improvements in safety and health, as well as cost savings for the organization.
Engineering Controls
Engineering controls are physical or mechanical methods for managing hazardous chemicals that eliminate or reduce worker exposure to hazards. These controls can be implemented at different stages of the manufacturing process and are considered one of the most effective ways to control workplace hazards.
Examples of engineering controls for managing hazardous chemicals in the manufacturing process include:
- Enclosed systems: These are systems that are completely sealed or enclosed to prevent hazardous chemicals from escaping into the workplace. For example, enclosed spray booths for painting operations.
- Ventilation systems: These systems are used to control the release of hazardous chemicals into the air by removing contaminated air and replacing it with clean air. Examples include local exhaust ventilation (LEV) systems, which capture hazardous emissions at the source and duct them to a ventilation system, or general dilution ventilation systems, which dilute the concentration of hazardous chemicals in the air.
- Automated processes: These processes eliminate the need for manual handling of hazardous chemicals, reducing the risk of exposure. For example, automated filling or mixing processes.
- Process isolation: This involves separating hazardous processes or equipment from workers by using barriers or remote control systems. For example, using a robot to perform hazardous tasks or operating equipment from a control room.
- Substitution of chemicals: Substitution of hazardous chemicals with less hazardous alternatives can also be considered an engineering control if it is achieved through modifications to the manufacturing process.
Engineering controls can be very effective in managing hazardous chemicals because they address the hazard at the source, making it unnecessary for workers to rely solely on personal protective equipment (PPE). However, the selection and implementation of engineering controls require careful evaluation of the hazards associated with the chemicals and processes and an understanding of the effectiveness and limitations of the control measures. Therefore, it is essential to involve safety professionals and engineers in selecting and implementing engineering controls to ensure their effectiveness.
Administrative Controls
Administrative controls are measures that aim to manage hazardous chemicals through changes in work procedures or practices. Administrative controls can be implemented in conjunction with engineering controls and personal protective equipment (PPE) further to reduce the risk of exposure to hazardous chemicals.
Examples of administrative controls for managing hazardous chemicals in the manufacturing process include:
- Work procedures: Developing and implementing standard operating procedures (SOPs) for the safe handling, use, storage, and disposal of hazardous chemicals can help to reduce the risk of exposure.
- Training: Providing workers with training on the hazards associated with the chemicals they work with, how to use them safely, and how to use PPE can help reduce the risk of exposure.
- Job rotation: Rotating workers through different jobs can help to reduce the duration of exposure to hazardous chemicals.
- Limiting exposure time: Limiting workers' exposure to hazardous chemicals can help reduce the risk of exposure.
- Signs and labels: Posting signs and labels in areas where hazardous chemicals are present can help remind workers of the hazards and the precautions they must take.
Administrative controls are often less effective than engineering controls or substitution, as they rely on worker compliance with procedures or practices. However, when implemented properly, administrative controls can be an effective way to reduce the risks associated with hazardous chemicals. It is important to regularly review and evaluate administrative controls to ensure their effectiveness and to make changes as needed to address new hazards or changes in work practices.
Personal Protective Equipment (PPE)
Personal protective equipment (PPE) is equipment worn by workers to protect against hazardous chemicals and other workplace hazards that cannot be completely eliminated through engineering or administrative controls. PPE can include a variety of items such as gloves, goggles, respirators, face shields, and protective clothing.
When selecting PPE for managing hazardous chemicals in the manufacturing process, the following factors should be considered:
- The type and concentration of the hazardous chemical(s) being used
- The duration of exposure
- The route of exposure (e.g., inhalation, skin contact, ingestion)
- The physical characteristics of the hazardous chemical(s) (e.g., corrosive, flammable)
- The work environment (e.g., temperature, humidity)
PPE should be selected based on the hazards present and the level of protection required. It is important to provide workers with appropriate training on the use and maintenance of PPE, including how to properly put on, take off, and dispose of PPE. PPE should also be regularly inspected, maintained, and replaced as needed to ensure it remains effective.
While PPE can be an important component of managing hazardous chemicals, it is generally considered a lower-level control measure compared to engineering and administrative controls. This is because PPE relies on the worker to use and maintain the equipment properly, and it does not eliminate the hazard at the source. Therefore, PPE should be used in conjunction with other control measures to provide the highest level of protection for workers.
Hazardous Waste Management
Hazardous waste is any waste that poses a potential threat to human health or the environment due to its chemical or physical properties. Hazardous waste is generated in the manufacturing process through a variety of activities such as cleaning, maintenance, and the use of hazardous chemicals. Hazardous waste management involves the safe handling, storage, transportation, and disposal of hazardous waste to prevent harm to human health and the environment.
Here are some strategies for managing hazardous waste in the manufacturing process:
- Identification: The first step in managing hazardous waste is to identify the waste generated in the manufacturing process. This can be achieved through a waste audit, where all waste streams are evaluated to determine if they are hazardous.
- Segregation: Once hazardous waste has been identified, it should be segregated from non-hazardous waste to prevent contamination. This can be achieved through the use of color-coded bins or containers.
- Storage: Hazardous waste should be stored in appropriate containers that are compatible with the waste and can prevent leaks or spills. The storage area should be labeled with appropriate signage and secured to prevent unauthorized access.
- Transportation: When hazardous waste needs to be transported off-site, it should be done by licensed and trained professionals who are equipped to handle hazardous waste safely.
- Disposal: Hazardous waste should be disposed of in a manner that minimizes harm to human health and the environment. This can include incineration, landfills, or recycling.
- Record Keeping: Manufacturers should maintain accurate records of the types and quantities of hazardous waste generated and the disposal methods used. This can help manufacturers to identify areas for improvement and ensure compliance with regulations.
Effective hazardous waste management requires a comprehensive approach that involves the cooperation of all employees, appropriate training, and the implementation of appropriate procedures and protocols. Manufacturers should regularly review and update their hazardous waste management practices to ensure they remain effective and comply with changing regulations.
Emergency Planning and Response
Emergency planning and response is an important aspect of managing hazardous chemicals in the manufacturing process. Accidents, spills, and other unexpected events can occur despite best efforts to prevent them, and it is important to have plans in place to respond quickly and effectively to minimize harm to human health and the environment.
Here are some strategies for emergency planning and response:
- Emergency plan: Manufacturers should develop and maintain an emergency plan that outlines procedures for responding to accidents and spills involving hazardous chemicals. The plan should include emergency contact information, evacuation procedures, and spill response protocols.
- Training: All employees should receive appropriate training on the emergency plan, including how to identify and respond to hazardous chemical spills and other emergencies.
- Equipment and supplies: Manufacturers should have appropriate equipment and supplies on hand to respond to hazardous chemical spills, such as spill kits, absorbents, and personal protective equipment.
- Communication: Effective communication is key during an emergency. Manufacturers should establish procedures for communicating with employees, emergency responders, and regulatory agencies during an emergency.
- Mock drills: Regularly conducting mock drills can help to identify areas for improvement in the emergency plan and ensure that employees are prepared to respond effectively in an actual emergency.
- Post-incident analysis: After an emergency, it is important to conduct a post-incident analysis to identify what went well and areas for improvement. This can help to refine the emergency plan and improve preparedness for future emergencies.
Effective emergency planning and response requires ongoing evaluation and improvement. Manufacturers should regularly review and update their emergency plans and procedures to ensure they remain effective and comply with changing regulations.
Continuous Improvement
Continuous improvement is an ongoing effort to improve processes and systems in order to achieve better results, reduce waste, and increase efficiency. In managing hazardous chemicals in the manufacturing process, continuous improvement can help identify areas for improvement in the management of hazardous chemicals, reduce the risk of accidents and spills, and improve overall safety and compliance.
Here are some strategies for continuous improvement in the management of hazardous chemicals:
- Regular evaluation: Manufacturers should regularly evaluate their processes and systems for managing hazardous chemicals to identify areas for improvement. This can include conducting regular audits and risk assessments.
- Employee involvement: Employees can provide valuable insights and suggestions for improving the management of hazardous chemicals. Manufacturers should encourage employee involvement in the continuous improvement process.
- Benchmarking: Benchmarking can help manufacturers to compare their processes and systems for managing hazardous chemicals to industry standards and best practices, and identify areas for improvement.
- Technology: Advances in technology can provide new tools and solutions for managing hazardous chemicals more effectively. Manufacturers should stay up-to-date with new technologies and evaluate their potential to improve the management of hazardous chemicals.
- Metrics: Manufacturers should establish metrics to measure the effectiveness of their processes and systems for managing hazardous chemicals. This can include metrics such as the number of spills, compliance with regulations, and employee training.
- Collaboration: Collaboration with other manufacturers, regulatory agencies, and industry organizations can provide valuable insights and resources for improving the management of hazardous chemicals.
Continuous improvement in the management of hazardous chemicals requires a commitment to ongoing evaluation, collaboration, and innovation. Manufacturers should regularly review and update their processes and systems to ensure they remain effective and comply with changing regulations.
How can Deskera Help You?
Deskera's integrated financial planning tools allow investors to better plan their investments and track their progress. It can help investors make decisions faster and more accurately.
Deskera Books can assist you in automating your accounting and mitigating business risks. Deskera makes it easier to create invoices by automating many other procedures, reducing your team's administrative workload.
Deskera also offers a suite of integrated applications to help businesses manage their financials, inventory, and operations. Furthermore, other business aspects such as HR (Deskera People), CRM (Deskera CRM), and ERP are provided by Deskera. These could be crucial and can help short sellers keep track of their businesses and make better decisions.
Key Takeaways
Here are some key points to summarize managing hazardous chemicals in the manufacturing process:
- Hazardous chemicals pose potential threats to human health and the environment.
- Effective management of hazardous chemicals requires a comprehensive approach that includes identification, substitution, engineering controls, administrative controls, personal protective equipment, and hazardous waste management.
- Emergency planning and response is important to minimize harm in case of accidents or spills involving hazardous chemicals.
- Continuous improvement is an ongoing effort to improve processes and systems to achieve better results, reduce waste, and increase efficiency in managing hazardous chemicals.
- Manufacturers should regularly evaluate and update their processes and systems for managing hazardous chemicals to ensure they remain effective and comply with changing regulations.
- Employee involvement, benchmarking, technology, metrics, and collaboration can all be valuable strategies for improving the management of hazardous chemicals in the manufacturing process.
Related Articles
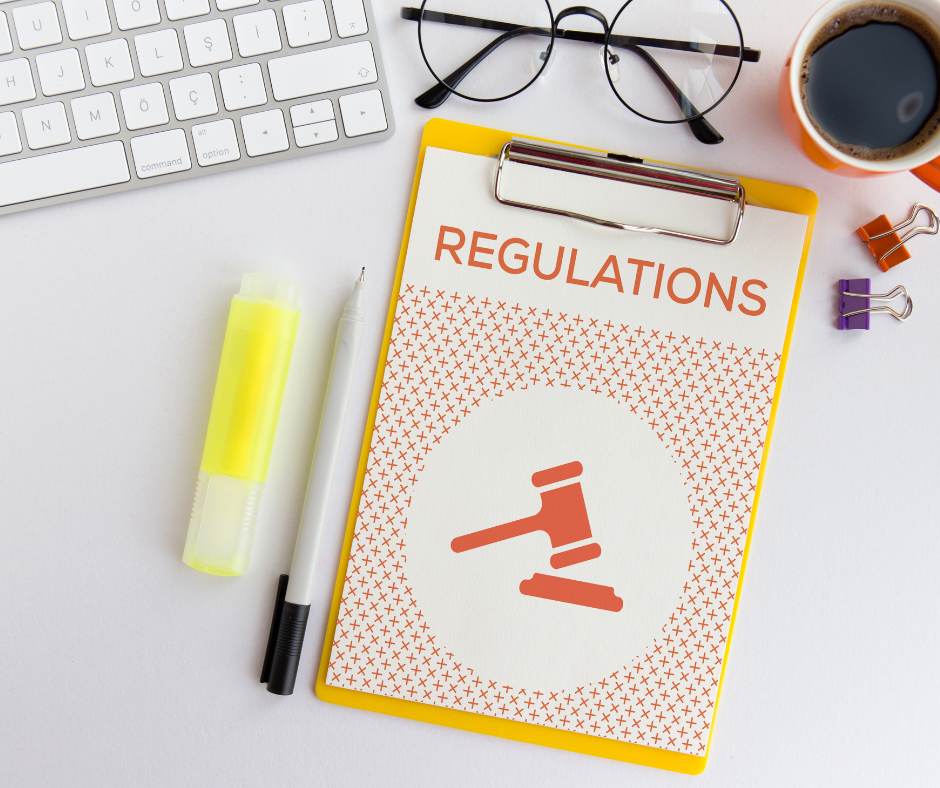
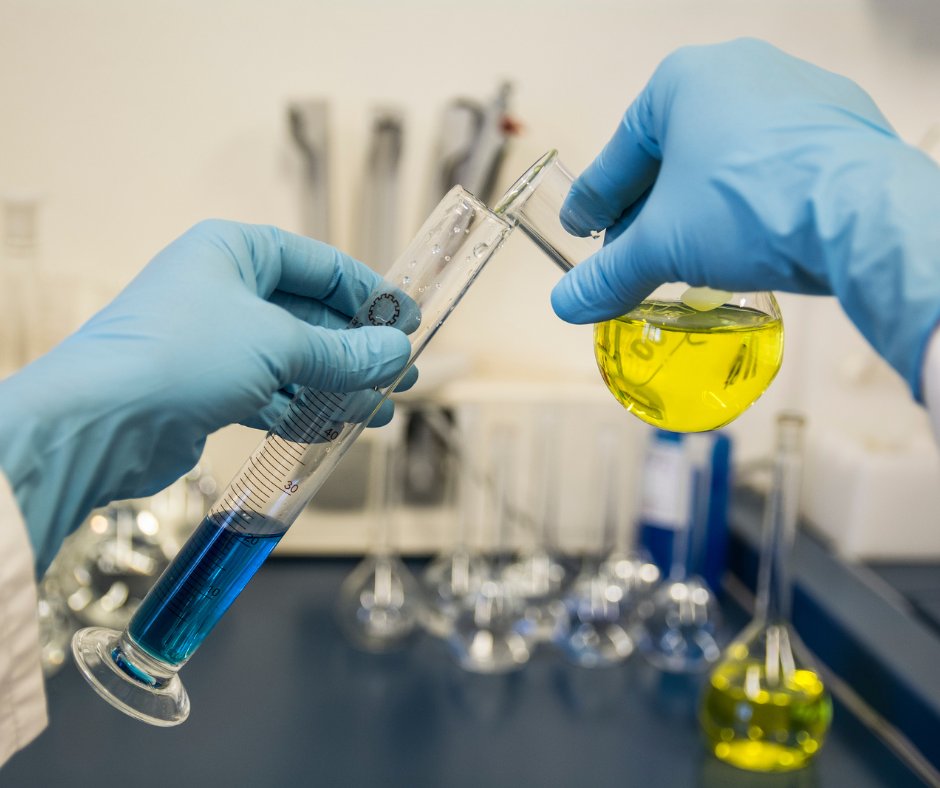
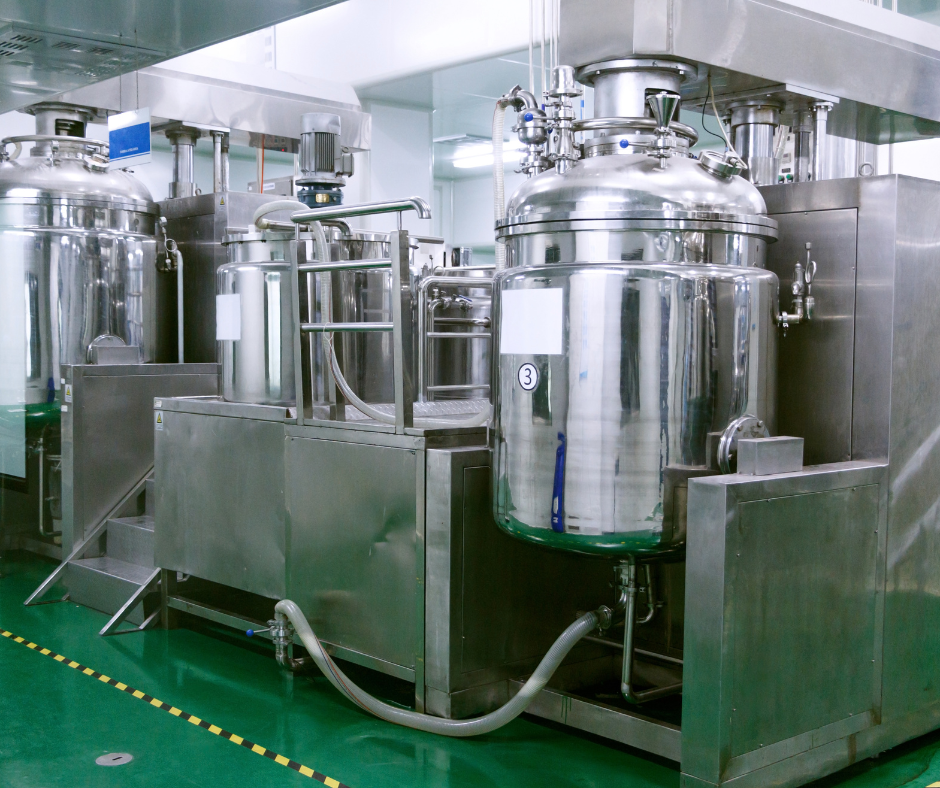