Chemical processes and products are essential to modern life and play a crucial role in various industries such as pharmaceuticals, petrochemicals, and food. However, the improper handling or use of chemicals can lead to serious accidents, injuries, and even fatalities. Therefore, it is critical to ensure the safety of chemical processes and products to protect workers, the environment, and the public.
This article aims to discuss the different ways to ensure the safety of chemical processes and products. It will cover the following topics:
- Understanding the Hazards of Chemicals
- Conduct thorough Risk Assessments
- Implement Appropriate Safety Protocols and Controls
- Prevention Measures
- Emergency Response and Planning
- Regulations and Standards
- Train Employees and Provide Appropriate Safety Equipment
- Regularly Inspect and Maintain Equipment
- Store and Dispose of Chemicals Properly
- Monitor for Potential Hazards
- Continuous Improvement and Monitoring
- How can Deskera Help You?
- Conclusion
- Related Articles
Understanding the Hazards of Chemicals
The first step to ensuring the safety of chemical processes and products is to understand the hazards of chemicals. Chemicals can pose a variety of hazards, including:
- Toxicity: Chemicals can be toxic to humans, animals, and the environment. Exposure to toxic chemicals can cause acute or chronic health effects, such as respiratory problems, cancer, and reproductive issues.
- Flammability: Many chemicals are flammable and can ignite or explode when exposed to heat, sparks, or flames.
- Reactivity: Chemicals can react with other substances, leading to the release of energy, heat, or gases. Some reactions can be violent and cause explosions or fires.
- Corrosiveness: Chemicals can corrode or erode materials such as metals and concrete, causing damage to equipment and structures.
- Radioactivity: Some chemicals are radioactive and can emit ionizing radiation, which can cause health effects such as cancer and genetic mutations.
It is essential to identify the hazards of chemicals and assess their risks to determine the appropriate measures to ensure their safe handling and use.
Conduct thorough Risk Assessments
Conducting thorough risk assessments is an important step in ensuring the safety of chemical processes and products. Here are some key steps in conducting a risk assessment:
- Identify potential hazards: Start by identifying potential hazards that could arise during the chemical process or product development. This could include chemical reactions, fires, explosions, and exposure to hazardous substances.
- Evaluate the likelihood and severity of the hazard: Once you have identified potential hazards, evaluate the likelihood and severity of each hazard. Consider factors such as the quantity and concentration of the chemicals involved, the temperature and pressure of the process, and the potential for human error.
- Determine who is at risk: Identify who could be at risk of harm from each hazard. This could include workers involved in the process, nearby residents or communities, or the environment.
- Develop controls and mitigation measures: Based on the likelihood and severity of each hazard, develop controls and mitigation measures to minimize the risk of harm. This could include engineering controls, such as ventilation or containment systems, administrative controls such as training or procedural changes, or personal protective equipment.
- Document the risk assessment: Document the results of the risk assessment, including the hazards identified, the likelihood and severity of each hazard, and the controls and mitigation measures put in place to reduce the risk of harm.
- Review and update the risk assessment regularly: Regularly review and update the risk assessment to ensure it remains relevant and effective as conditions change, such as changes in chemicals used or modifications to the process.
Implement Appropriate Safety Protocols and Controls
Implementing appropriate safety protocols and controls is another important step in ensuring the safety of chemical processes and products. Here are some key steps to consider:
- Identify potential hazards: Start by identifying potential hazards that could arise during the chemical process or product development. This could include chemical reactions, fires, explosions, and exposure to hazardous substances.
- Evaluate the likelihood and severity of the hazard: Once you have identified potential hazards, evaluate the likelihood and severity of each hazard. Consider factors such as the quantity and concentration of the chemicals involved, the temperature and pressure of the process, and the potential for human error.
- Develop controls and mitigation measures: Based on the likelihood and severity of each hazard, develop controls and mitigation measures to minimize the risk of harm. This could include engineering controls, such as ventilation or containment systems, administrative controls such as training or procedural changes, or personal protective equipment.
- Implement the controls and mitigation measures: Once you have developed the controls and mitigation measures, implement them into the chemical process or product development. This may involve modifying equipment or procedures, or providing employees with appropriate personal protective equipment.
- Train employees: All employees involved in chemical processes or handling chemical products should receive appropriate training on safety protocols and procedures. This may include training on how to use personal protective equipment, how to respond to emergencies, and how to safely handle hazardous materials.
- Regularly review and update safety protocols: Regularly review and update the safety protocols and controls to ensure they remain effective and relevant. This may involve conducting periodic audits or inspections of the process to identify any potential issues.
By implementing appropriate safety protocols and controls, you can minimize the risk of harm to employees, nearby communities, and the environment.
Prevention Measures
Prevention measures are the primary means of ensuring the safety of chemical processes and products. Prevention measures aim to eliminate or minimize the hazards of chemicals and prevent accidents and incidents. There are several prevention measures that can be used, including:
- Engineering controls: Engineering controls are physical barriers or systems that prevent or minimize exposure to hazardous chemicals. Examples of engineering controls include ventilation systems, enclosures, and interlocks.
- Administrative controls: Administrative controls are policies, procedures, and practices that reduce exposure to hazardous chemicals. Examples of administrative controls include training, job rotation, and work procedures.
- Personal protective equipment (PPE): PPE is equipment worn by workers to protect them from hazardous chemicals. Examples of PPE include respirators, gloves, and protective clothing.
- Chemical substitution: Chemical substitution involves replacing hazardous chemicals with less hazardous alternatives. For example, replacing a toxic solvent with a non-toxic solvent or using a less reactive chemical.
- Hazard communication: Hazard communication involves informing workers and others about the hazards of chemicals and the appropriate control measures. This includes labeling of containers, Safety Data Sheets (SDS), and training on the safe handling and use of chemicals.
Prevention measures should be implemented based on the results of the risk assessment to ensure that they are appropriate and effective in mitigating the identified risks.
Emergency Response and Planning
Despite the implementation of prevention measures, accidents and incidents can still occur. Therefore, it is important to have an emergency response and planning in place to ensure a rapid and effective response to minimize the consequences of an incident.
Emergency response planning involves developing procedures for responding to an incident, such as fire, spill, or release of hazardous chemicals. It includes identifying potential hazards, developing response procedures, and conducting regular training and drills.
Emergency response planning should involve collaboration between different stakeholders, including employees, emergency responders, regulatory agencies, and the community. It should also consider the potential impact of an incident on the environment and public health.
Regulations and Standards
Regulations and standards play a critical role in ensuring the safety of chemical processes and products. Regulations are legally binding rules that set requirements for the safe handling and use of chemicals. Standards are voluntary guidelines that provide recommendations for best practices.
Regulations and standards are developed by government agencies and industry organizations to protect workers, the environment, and the public from the hazards of chemicals. They provide a minimum level of safety requirements that must be followed by companies and organizations that handle and use chemicals.
Examples of regulations and standards that govern the safety of chemical processes and products include:
- Occupational Safety and Health Administration (OSHA): OSHA is a federal agency that sets safety and health standards for workers in the United States. OSHA has specific standards for handling hazardous chemicals, such as the Hazard Communication Standard (HCS) and the Process Safety Management (PSM) Standard.
- Environmental Protection Agency (EPA): EPA is a federal agency that regulates the use and disposal of hazardous chemicals to protect the environment. EPA has specific regulations, such as the Resource Conservation and Recovery Act (RCRA) and the Clean Air Act, that govern the handling and disposal of hazardous chemicals.
- International Organization for Standardization (ISO): ISO is an international organization that develops voluntary standards for best practices in various industries, including the handling and use of chemicals. ISO has specific standards, such as ISO 14001 and ISO 45001, that provide guidelines for environmental and occupational health and safety management.
Compliance with regulations and standards is critical in ensuring the safety of chemical processes and products. Companies and organizations should regularly review and update their compliance efforts to ensure that they meet the latest requirements.
Train Employees and Provide Appropriate Safety Equipment
Training employees and providing appropriate safety equipment is critical in ensuring the safety of chemical processes and products. Here are some key steps to consider:
- Identify the appropriate safety equipment: Based on the hazards identified in the risk assessment, identify the appropriate safety equipment needed to protect employees. This may include personal protective equipment such as gloves, goggles, respirators, and protective clothing.
- Provide the necessary safety equipment: Once you have identified the appropriate safety equipment, provide it to employees and ensure that it is used properly. This may involve providing multiple sizes to ensure a proper fit, and ensuring that employees know how to use and maintain the equipment.
- Train employees on safety protocols: All employees involved in chemical processes or handling chemical products should receive appropriate training on safety protocols and procedures. This may include training on how to use personal protective equipment, how to respond to emergencies, and how to safely handle hazardous materials.
- Conduct regular safety drills: Conduct regular safety drills to ensure that employees are prepared in case of an emergency. This may involve simulating a chemical spill or other hazardous situation and practicing appropriate responses.
- Encourage a culture of safety: Encourage employees to report any safety concerns or incidents, and create a culture where safety is a top priority. This may involve regular safety meetings and open communication channels between employees and management.
By training employees and providing appropriate safety equipment, you can minimize the risk of harm to employees and create a safer working environment.
Regularly Inspect and Maintain Equipment
Regularly inspecting and maintaining equipment is another important step in ensuring the safety of chemical processes and products. Here are some key steps to consider:
- Develop an inspection and maintenance schedule: Develop a schedule for regular inspections and maintenance of all equipment used in chemical processes or product development. This may involve scheduling weekly, monthly, or quarterly inspections, depending on the type of equipment and the level of risk involved.
- Conduct regular inspections: During inspections, check for signs of wear and tear, corrosion, leaks, or other damage to equipment that could pose a safety risk. Pay particular attention to high-risk areas such as piping systems, pressure vessels, and storage tanks.
- Address any issues promptly: If any issues are identified during inspections, address them promptly to minimize the risk of harm. This may involve repairing or replacing damaged equipment, tightening loose bolts, or replacing worn or damaged gaskets.
- Perform regular maintenance: Regular maintenance should also be performed to keep equipment in good working order. This may involve cleaning, lubricating, and replacing parts as necessary.
- Keep detailed records: Keep detailed records of all inspections and maintenance performed on equipment. This can help to identify patterns of wear and tear, and to schedule future maintenance or replacement of equipment as needed.
By regularly inspecting and maintaining equipment, you can minimize the risk of equipment failure or malfunction, which could lead to serious safety hazards such as fires, explosions, or toxic releases.
Store and Dispose of Chemicals Properly
Storing and disposing of chemicals properly is a critical aspect of ensuring the safety of chemical processes and products. Here are some key steps to consider:
- Follow regulatory requirements: Be aware of regulatory requirements for the storage and disposal of chemicals, and ensure that your organization complies with all relevant laws and regulations. This may involve obtaining permits, keeping records of chemical use and disposal, and reporting any spills or releases.
- Store chemicals in appropriate containers: Store chemicals in appropriate containers that are designed for the specific type of chemical being stored. This may involve using containers made of a certain type of material, such as glass or plastic, and ensuring that containers are clearly labeled with the contents and any associated hazards.
- Store chemicals in appropriate locations: Store chemicals in appropriate locations that are designed for the specific type of chemical being stored. This may involve using designated storage areas that are fire-resistant, well-ventilated, and equipped with appropriate safety equipment such as fire suppression systems.
- Train employees on proper handling and disposal: All employees involved in chemical processes or handling chemical products should receive appropriate training on proper handling and disposal procedures. This may include training on how to handle chemicals safely, how to store chemicals properly, and how to dispose of chemicals safely and legally.
- Dispose of chemicals safely and responsibly: Dispose of chemicals safely and responsibly in accordance with regulatory requirements. This may involve using a licensed waste disposal company or other authorized facility, and following all applicable procedures for handling and transporting hazardous materials.
By storing and disposing of chemicals properly, you can minimize the risk of accidental spills, releases, or exposure to hazardous substances, which can have serious health and environmental consequences.
Monitor for Potential Hazards
Monitoring for potential hazards is an essential step in ensuring the safety of chemical processes and products. Here are some key steps to consider:
- Establish a monitoring program: Establish a monitoring program that includes regular inspections and testing of chemical processes, equipment, and products to identify potential hazards.
- Conduct regular inspections: Conduct regular inspections of all areas where chemicals are used or stored, including equipment, storage areas, and workspaces. Look for signs of corrosion, leaks, spills, or other hazards.
- Test for potential hazards: Test for potential hazards such as toxic gases, flammable liquids, or other hazardous substances that could pose a risk to employees or the environment. This may involve using monitoring equipment such as gas detectors, radiation monitors, or other testing devices.
- Analyze test results: Analyze test results to identify any potential hazards and take appropriate action to minimize risks. This may involve adjusting processes, modifying equipment, or changing work procedures.
- Regularly review and update monitoring program: Regularly review and update the monitoring program to ensure that it remains effective and up-to-date with changing regulations or industry standards.
By monitoring for potential hazards, you can identify and address potential safety risks before they become a problem. This can help to prevent accidents, injuries, or environmental damage, and promote a safer workplace for employees.
Continuous Improvement and Monitoring
Continuous improvement and monitoring are essential to ensure that the measures implemented to ensure the safety of chemical processes and products remain effective. This involves regularly reviewing and updating risk assessments, prevention measures, emergency response plans, and compliance efforts.
Continuous improvement and monitoring should involve collaboration between different stakeholders, including workers, management, regulatory agencies, and the community. It should also consider the latest scientific and technological developments.
How can Deskera Help You?
Deskera's integrated financial planning tools allow investors to better plan their investments and track their progress. It can help investors make decisions faster and more accurately.
Deskera Books can assist you in automating your accounting and mitigating business risks. Deskera makes it easier to create invoices by automating many other procedures, reducing your team's administrative workload.
Deskera also offers a suite of integrated applications to help businesses manage their financials, inventory, and operations. Furthermore, other business aspects such as HR (Deskera People), CRM (Deskera CRM), and ERP are provided by Deskera. These could be crucial and can help short sellers keep track of their businesses and make better decisions.
Conclusion
Ensuring the safety of chemical processes and products requires a comprehensive approach that includes risk assessments, safety protocols and controls, employee training, equipment inspections and maintenance, proper storage and disposal of chemicals, and monitoring for potential hazards. By implementing these measures, organizations can minimize the risk of accidents, injuries, and environmental damage, and promote a safer workplace for employees. It is important to regularly review and update safety procedures and protocols to ensure they remain effective and up-to-date with changing regulations and industry standards. By prioritizing safety, organizations can build a culture of safety and responsibility, and protect both their employees and the environment.
Related Articles
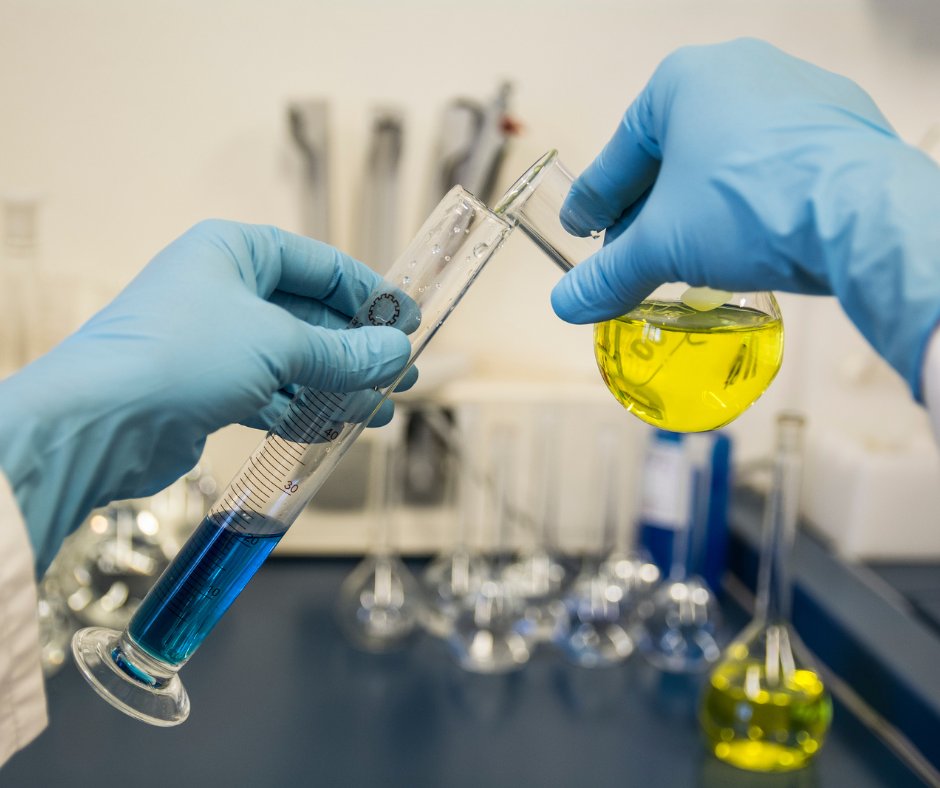
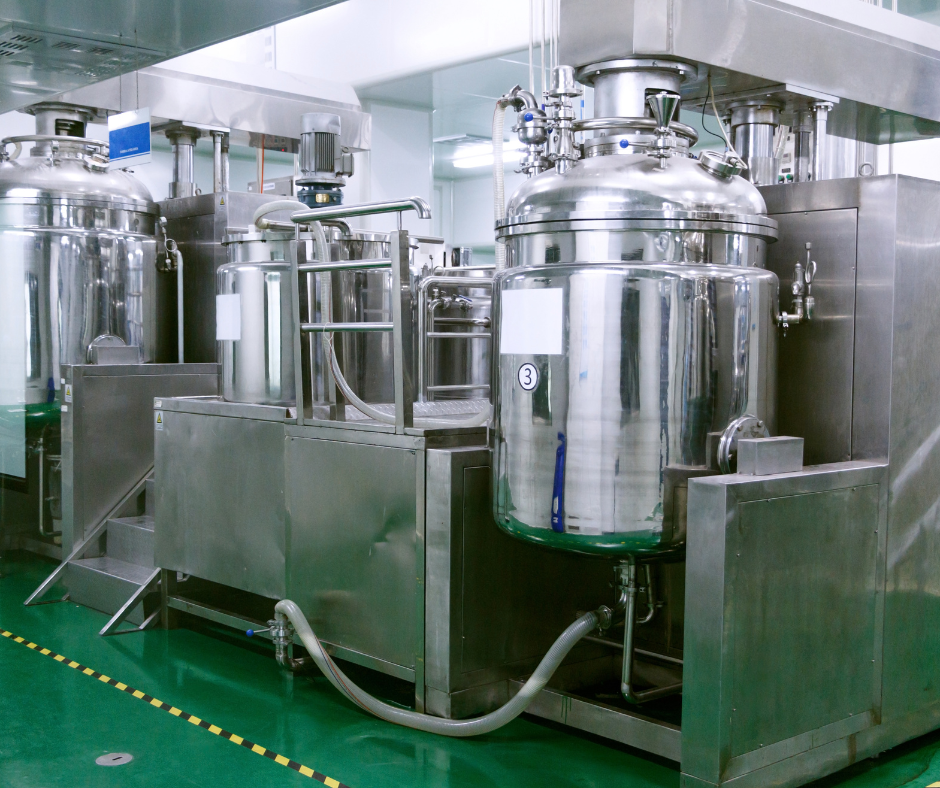
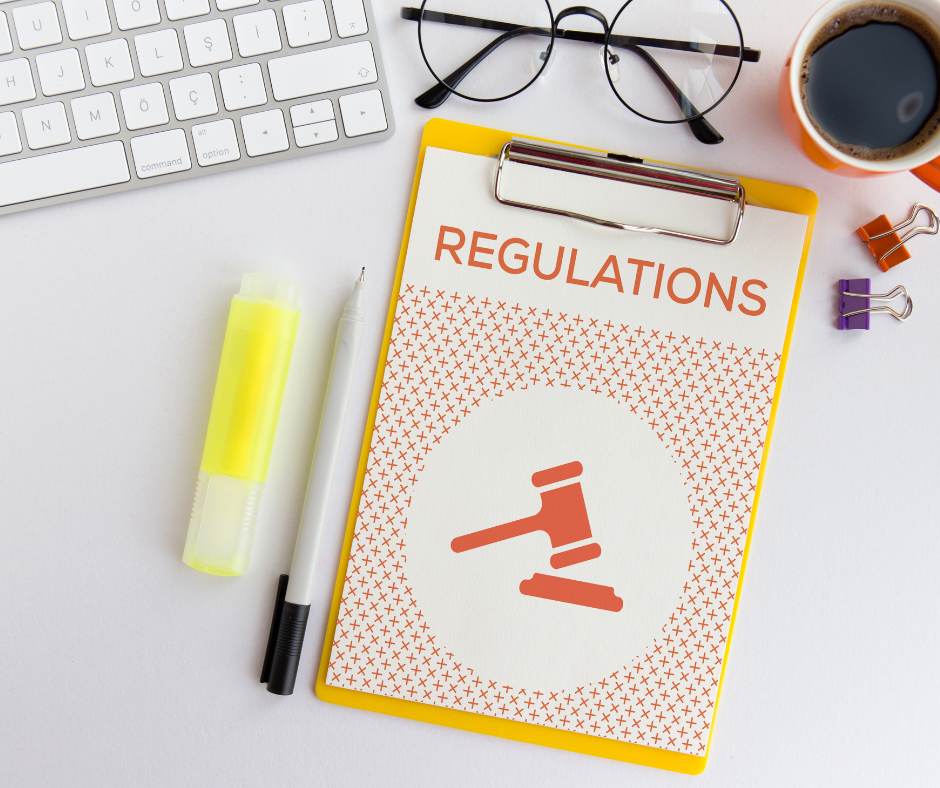