Plastic manufacturing is the process of creating plastic products from various raw materials, including polymers and additives. Polymers are long chains of repeating molecules that are the main building blocks of plastics. There are many different types of polymers, each with their own unique properties and uses.
Additives are chemical compounds that are added to polymers during the manufacturing process to enhance their properties or to make them easier to process. Additives can provide benefits such as increased durability, flexibility, or heat resistance, as well as improved color, texture, and appearance.
Some common types of additives used in plastic manufacturing include plasticizers, which increase flexibility; stabilizers, which prevent degradation from heat or light exposure; and colorants, which add color to the plastic. Other additives may be used to improve the processing of the plastic, such as lubricants, which reduce friction during molding, or blowing agents, which create air pockets to make the plastic more lightweight.
The process of plastic manufacturing typically involves melting the raw materials together and then shaping the resulting mixture into the desired form, such as through injection molding, extrusion, or blow molding. The use of polymers and additives allows for a wide range of plastic products to be created, from durable automotive parts to flexible packaging materials.
In this article, we will discuss more in details different types of polymers and additives used in plastic manufacturing:
- Manufacturing Processes for Plastic Products
- Polymers Used in Plastic Manufacturing
- Thermoplastics
- Polyethylene
- Polypropylene
- Polystyrene
- Thermosets
- Epoxy Resins
- Phenolic Resins
- Melamine Resins
- Additives Used in Plastic Manufacturing
- Stabilizers
- Plasticizers
- Fillers
- Pigments
- Flame retardants
- Fillers
- Talc
- Calcium Carbonate
- Glass Fibers
- Plasticizers
- Phthalates
- Adipates
- Citrates
- Stabilizers
- Antioxidants
- UV Stabilizers
- Heat Stabilizers
- Colorants
- Pigments
- Dyes
- Flame Retardants
- Halogenated Compounds
- Phosphorus Compounds
- Metal Oxides
- How can Deskera Help You?
- Conclusion
- Related Articles
Manufacturing Processes for Plastic Products
There are several different manufacturing processes that can be used to create plastic products. The choice of manufacturing process depends on the type of product being made, the properties required, and the production volume required. The most common manufacturing processes for plastic products include:
- Injection molding: This is the most commonly used manufacturing process for plastic products. It involves injecting molten plastic into a mold cavity and allowing it to cool and solidify. The mold is then opened, and the finished product is removed. Injection molding is used to produce a wide range of products, such as toys, automotive parts, and household items.
- Blow molding: This process is used to produce hollow plastic products, such as bottles, containers, and tanks. It involves blowing air into a molten plastic tube to form the desired shape, and then allowing it to cool and solidify.
- Extrusion: This process is used to produce products with a continuous shape, such as pipes, tubing, and sheeting. It involves forcing molten plastic through a die to form the desired shape, and then cooling and solidifying it.
- Rotational molding: This process is used to produce large, hollow plastic products, such as tanks, playground equipment, and kayaks. It involves placing a measured amount of plastic powder into a mold, which is then rotated on multiple axes to evenly distribute the plastic and create the desired shape. The mold is then cooled and the finished product is removed.
- Thermoforming: This process is used to produce products with a specific shape, such as trays, containers, and packaging. It involves heating a sheet of plastic until it becomes pliable, and then shaping it using a mold or vacuum-forming process. The plastic is then cooled and solidified, and the finished product is removed.
Each of these manufacturing processes has its own advantages and disadvantages, and the choice of process depends on the specific requirements of the product being made.
Polymers Used in Plastic Manufacturing
Polymers are large molecules composed of repeating units called monomers. They are the foundation of plastic and are used in a wide variety of applications, including packaging, automotive, construction, electronics, and medical devices. There are many types of polymers, each with its own unique properties and characteristics.
Polyethylene (PE):
Polyethylene is the most widely used polymer in the world. It is a thermoplastic polymer that is characterized by its high strength, durability, and resistance to impact and chemicals. It is commonly used in packaging, construction, and automotive applications. Polyethylene can be produced in different forms, including high-density polyethylene (HDPE) and low-density polyethylene (LDPE).
Polypropylene (PP):
Polypropylene is a thermoplastic polymer that is characterized by its high strength, durability, and resistance to chemicals and heat. It is commonly used in packaging, automotive, and medical applications. Polypropylene can be produced in different forms, including homopolymer and copolymer.
Polyvinyl Chloride (PVC):
Polyvinyl chloride is a thermoplastic polymer that is characterized by its high strength, durability, and resistance to chemicals and weathering. It is commonly used in construction, automotive, and medical applications. PVC can be produced in different forms, including rigid and flexible.
Polystyrene (PS):
Polystyrene is a thermoplastic polymer that is characterized by its high strength, durability, and resistance to impact and chemicals. It is commonly used in packaging, automotive, and construction applications. Polystyrene can be produced in different forms, including expandable polystyrene (EPS) and extruded polystyrene (XPS).
Polyethylene Terephthalate (PET):
Polyethylene terephthalate is a thermoplastic polymer that is characterized by its high strength, durability, and resistance to chemicals and impact. It is commonly used in packaging, beverage bottles, and textile applications. PET can be produced in different forms, including amorphous and crystalline.
Acrylonitrile Butadiene Styrene (ABS):
Acrylonitrile butadiene styrene is a thermoplastic polymer that is characterized by its high strength, toughness, and resistance to impact and chemicals. It is commonly used in automotive, electronic, and consumer goods applications.
Polyurethane (PU):
Polyurethane is a thermosetting polymer that is characterized by its high strength, durability, and resistance to impact and chemicals. It is commonly used in construction, automotive, and furniture applications. Polyurethane can be produced in different forms, including rigid and flexible.
Polycarbonate (PC):
Polycarbonate is a thermoplastic polymer that is characterized by its high strength, toughness, and resistance to impact and heat. It is commonly used in electronic, automotive, and medical applications. Polycarbonate can be produced in different forms, including amorphous and crystalline.
Polymers are the foundation of plastic and are used in a wide variety of applications. There are many types of polymers, each with its own unique properties and characteristics. The selection of the appropriate polymer is crucial to the success of any plastic manufacturing project. By understanding the properties and characteristics of different polymers, manufacturers can create plastic products that meet the specific needs and requirements of their customers.
Thermoplastics
Thermoplastics are a type of polymer that can be melted and re-molded multiple times without undergoing significant degradation in their properties. This property makes them an ideal choice for manufacturing plastic products that require repeated processing or reshaping. In addition, thermoplastics are lightweight, have good chemical resistance, and are easily recyclable, which makes them environmentally friendly.
Here are some examples of thermoplastics:
Polyethylene (PE):
Polyethylene is the most widely used thermoplastic in the world, and it is characterized by its high strength, durability, and resistance to impact and chemicals. It can be produced in different forms, including high-density polyethylene (HDPE) and low-density polyethylene (LDPE), each with their own unique properties and characteristics.
HDPE is a strong, tough, and lightweight material that is resistant to impact and chemicals. It is commonly used in applications that require a high degree of toughness, such as in water pipes, packaging, and automotive parts.
LDPE is a more flexible and softer material that is commonly used in applications that require a high degree of flexibility, such as in packaging films, squeeze bottles, and cable insulation.
Polypropylene (PP):
Polypropylene is a thermoplastic polymer that is characterized by its high strength, durability, and resistance to chemicals and heat. It can be produced in different forms, including homopolymer and copolymer, each with their own unique properties and characteristics.
Homopolymer is a strong, tough, and rigid material that is commonly used in applications that require high stiffness and strength, such as in automotive parts, toys, and packaging.
Copolymer is a more flexible and softer material that is commonly used in applications that require a high degree of flexibility, such as in food packaging, medical devices, and textiles.
Polystyrene (PS):
Polystyrene is a thermoplastic polymer that is characterized by its high strength, durability, and resistance to impact and chemicals. It can be produced in different forms, including expandable polystyrene (EPS) and extruded polystyrene (XPS), each with their own unique properties and characteristics.
EPS is a lightweight and rigid material that is commonly used in packaging, insulation, and disposable food containers.
XPS is a more dense and rigid material that is commonly used in applications that require high insulation properties, such as in construction and refrigeration.
Polyvinyl Chloride (PVC):
Polyvinyl chloride is a thermoplastic polymer that is characterized by its high strength, durability, and resistance to chemicals and weathering. It can be produced in different forms, including rigid and flexible, each with their own unique properties and characteristics.
Rigid PVC is a strong and stiff material that is commonly used in applications that require high impact resistance and strength, such as in construction, window frames, and pipes.
Flexible PVC is a more flexible and softer material that is commonly used in applications that require a high degree of flexibility, such as in medical devices, electrical cables, and inflatable products.
Polycarbonate (PC):
Polycarbonate is a thermoplastic polymer that is characterized by its high strength, toughness, and resistance to impact and heat. It is commonly used in applications that require high impact resistance and transparency, such as in electronic displays, automotive parts, and medical devices.
Thermoplastics are a versatile and widely used type of polymer that are characterized by their ability to be melted and re-molded multiple times without significant degradation in their properties. They are lightweight, have good chemical resistance, and are easily recyclable, making them an environmentally friendly choice for manufacturing plastic products. The selection of the appropriate thermoplastic is crucial to the success of any plastic manufacturing project.
Polyethylene
Polyethylene (PE) is a thermoplastic polymer that is widely used in various applications due to its excellent properties such as high strength, durability, and resistance to impact and chemicals. It is a member of the polyolefin family of polymers, which also includes polypropylene.
PE can be produced in different forms, including high-density polyethylene (HDPE), low-density polyethylene (LDPE), and linear low-density polyethylene (LLDPE). Each of these forms has its own unique properties and characteristics that make them suitable for different applications.
HDPE is a strong, tough, and lightweight material that is resistant to impact and chemicals. It is commonly used in applications that require a high degree of toughness, such as in water pipes, packaging, and automotive parts. HDPE is also widely used in the manufacturing of plastic bottles for milk, juice, water, and other liquids, as it is lightweight, shatterproof, and does not affect the taste or odor of the contents.
LDPE is a more flexible and softer material than HDPE. It is commonly used in applications that require a high degree of flexibility, such as in packaging films, squeeze bottles, and cable insulation. LDPE is also used in the manufacturing of plastic bags and wrap, as it is easy to seal and provides good protection against moisture and dust.
LLDPE is a form of polyethylene that has a higher tensile strength and puncture resistance than LDPE. It is commonly used in applications that require high strength and flexibility, such as in food packaging, industrial liners, and agricultural films. LLDPE is also used in the manufacturing of stretch wrap, as it provides good cling and elongation properties.
PE is a popular material for manufacturing plastic products due to its low cost, easy processing, and excellent properties. It is also considered to be a relatively environmentally friendly material, as it is recyclable and can be reused in the production of new products. However, it is important to note that PE is not biodegradable and can cause environmental issues if not properly disposed of.
Polyethylene is a widely used thermoplastic polymer that is popular in the manufacturing of various products due to its excellent properties such as high strength, durability, and resistance to impact and chemicals. The selection of the appropriate form of polyethylene is crucial to the success of any plastic manufacturing project.
Polypropylene
Polypropylene (PP) is a versatile thermoplastic polymer that is widely used in the manufacturing of a variety of products due to its excellent combination of mechanical, physical, and chemical properties. It is a member of the polyolefin family of polymers, which also includes polyethylene.
PP is a strong, tough, and lightweight material that is resistant to impact, heat, chemicals, and UV radiation. It is also highly resistant to fatigue and has a high melting point, making it suitable for use in applications that require high performance and durability.
PP can be produced in different forms, including homopolymer and copolymer. Homopolymer PP is a high-molecular-weight polymer that is produced by the polymerization of propylene. It is the most commonly used form of PP and has a high degree of stiffness, strength, and heat resistance. Copolymer PP, on the other hand, is produced by the polymerization of propylene and a comonomer such as ethylene or butene. It has a lower melting point than homopolymer PP and is more flexible and impact-resistant.
PP is widely used in the manufacturing of a variety of products such as packaging, automotive parts, textiles, medical devices, and consumer goods. In the packaging industry, PP is used in the manufacturing of food packaging, beverage containers, and cosmetic packaging due to its excellent barrier properties, good clarity, and ability to be easily molded into various shapes. In the automotive industry, PP is used in the manufacturing of interior parts such as dashboards, door panels, and instrument panels due to its lightweight, high strength, and resistance to heat and chemicals. In the medical industry, PP is used in the manufacturing of medical devices such as syringes, IV bags, and surgical instruments due to its biocompatibility and resistance to chemicals and radiation.
PP is a popular material for plastic manufacturing due to its low cost, easy processing, and excellent properties. It is also considered to be a relatively environmentally friendly material, as it is recyclable and can be reused in the production of new products. However, like polyethylene, PP is not biodegradable and can cause environmental issues if not properly disposed of.
In conclusion, polypropylene is a versatile thermoplastic polymer that is widely used in the manufacturing of a variety of products due to its excellent combination of mechanical, physical, and chemical properties. The selection of the appropriate form of PP is crucial to the success of any plastic manufacturing project.
Polystyrene
Polystyrene (PS) is a versatile thermoplastic polymer that is widely used in the manufacturing of a variety of products due to its excellent combination of mechanical, physical, and chemical properties. It is a member of the vinyl polymer family of polymers, which also includes polyvinyl chloride (PVC) and polyvinyl acetate (PVA).
PS can be produced in different forms, including crystal, high-impact, and expandable. Crystal PS is a transparent and rigid material that is commonly used in the manufacturing of food packaging, CD cases, and laboratory equipment. High-impact PS is a modified form of crystal PS that has a higher degree of toughness and impact resistance. It is commonly used in the manufacturing of products such as toys, appliance housings, and electronics casings. Expandable PS, also known as EPS or Styrofoam, is a lightweight material that is widely used in the manufacturing of insulation, packaging, and disposable products.
PS has excellent properties such as high stiffness, good dimensional stability, and low thermal conductivity. It is also highly resistant to moisture, chemicals, and UV radiation. However, PS is brittle and has poor impact resistance, which limits its use in applications that require high toughness and durability.
PS is a popular material for manufacturing plastic products due to its low cost, ease of processing, and excellent properties. However, it is important to note that PS is not biodegradable and can cause environmental issues if not properly disposed of. EPS, in particular, is a concern due to its non-biodegradable nature and the fact that it can easily become litter and cause harm to wildlife.
In conclusion, polystyrene is a versatile thermoplastic polymer that is widely used in the manufacturing of a variety of products due to its excellent combination of mechanical, physical, and chemical properties. The selection of the appropriate form of PS is crucial to the success of any plastic manufacturing project. However, it is important to be mindful of the environmental impact of PS and to properly dispose of it to minimize harm to the environment.
Thermosets
Thermosets are a class of polymers that, unlike thermoplastics, cannot be melted and reshaped once they have been cured. Once a thermoset polymer has been molded and cured, it retains its shape and properties permanently, making it a highly durable and reliable material.
The curing process of thermosets involves a chemical reaction, often through the use of heat, pressure, or a catalyst, that causes the polymer chains to cross-link and form a rigid, three-dimensional network structure. This network structure gives thermosets their excellent mechanical, thermal, and chemical resistance properties, making them ideal for high-performance applications that require durability and stability.
There are several types of thermosets, including epoxy, phenolic, melamine, and unsaturated polyester resins. Each type of thermoset has unique properties that make it suitable for specific applications.
Epoxy resins are a type of thermoset that are widely used in the manufacturing of adhesives, coatings, and composites due to their excellent mechanical, thermal, and chemical resistance properties. They are also highly resistant to moisture and have excellent bonding strength, making them ideal for use in high-stress environments.
Phenolic resins are a type of thermoset that are commonly used in the manufacturing of electrical components, molded parts, and adhesives due to their excellent mechanical, electrical, and fire-resistant properties. They are also highly resistant to chemicals and have a low coefficient of thermal expansion, making them ideal for use in high-temperature applications.
Melamine resins are a type of thermoset that are commonly used in the manufacturing of dinnerware, countertops, and laminates due to their excellent heat resistance, durability, and resistance to stains and scratches.
Unsaturated polyester resins are a type of thermoset that are commonly used in the manufacturing of composites, boat hulls, and piping systems due to their excellent mechanical and chemical resistance properties. They are also highly resistant to corrosion and have good dimensional stability.
Thermosets are a popular material for high-performance applications due to their excellent properties and durability. However, the curing process of thermosets can be challenging and requires careful attention to temperature and curing time to achieve the desired properties. Additionally, once a thermoset is cured, it cannot be melted and reshaped, making it difficult to recycle.
In conclusion, thermosets are a class of polymers that are highly durable and reliable due to their rigid, three-dimensional network structure. They have excellent mechanical, thermal, and chemical resistance properties, making them ideal for high-performance applications that require durability and stability. However, the curing process of thermosets can be challenging, and they cannot be recycled or reshaped once cured.
Epoxy Resins
Epoxy resins are a type of thermosetting polymer that are widely used in the manufacturing of adhesives, coatings, and composites due to their excellent mechanical, thermal, and chemical resistance properties. They are formed by the reaction between epichlorohydrin and bisphenol A, resulting in a rigid, cross-linked structure.
Epoxy resins have several advantages over other types of thermosetting polymers. They have excellent adhesion properties, making them ideal for use as adhesives and coatings. They are also highly resistant to moisture, chemicals, and temperature, making them suitable for use in harsh environments. Additionally, epoxy resins have good electrical insulation properties and can be used in the manufacturing of electrical components.
Epoxy resins are used in a variety of applications, including construction, aerospace, automotive, and electronics. In construction, epoxy resins are used as adhesives for bonding concrete, wood, and metal. In aerospace, they are used in the manufacturing of composite materials for aircraft structures. In automotive, they are used as adhesives for bonding body panels and in the manufacturing of carbon fiber reinforced plastic (CFRP) components. In electronics, they are used in the manufacturing of printed circuit boards (PCBs) and encapsulation of electronic components.
One of the most significant advantages of epoxy resins is their ability to be customized to meet specific application requirements. The curing process of epoxy resins can be adjusted to achieve different properties, such as flexibility, hardness, and impact resistance. Epoxy resins can also be modified with additives, such as fillers and pigments, to improve their properties and appearance.
However, epoxy resins also have some limitations. They are brittle and can crack under high impact or stress. Additionally, they are not UV-resistant and can degrade when exposed to sunlight, which limits their use in outdoor applications.
In conclusion, epoxy resins are a versatile and widely used type of thermosetting polymer due to their excellent mechanical, thermal, and chemical resistance properties. They have several advantages over other types of thermosetting polymers, including their adhesion properties, resistance to moisture and temperature, and electrical insulation properties. Epoxy resins can be customized to meet specific application requirements and can be modified with additives to improve their properties and appearance. However, they also have some limitations, such as their brittleness and lack of UV resistance.
Phenolic Resins
Phenolic resins are a type of thermosetting polymer that are widely used in the manufacturing of adhesives, coatings, and composites due to their excellent mechanical and thermal properties. They are formed by the reaction between phenol and formaldehyde, resulting in a rigid, cross-linked structure.
Phenolic resins have several advantages over other types of thermosetting polymers. They have excellent heat resistance properties and can withstand temperatures up to 150°C without degrading. They also have excellent mechanical properties, including high stiffness and strength, making them suitable for use in structural applications. Additionally, phenolic resins have good electrical insulation properties and can be used in the manufacturing of electrical components.
Phenolic resins are used in a variety of applications, including construction, automotive, and aerospace. In construction, phenolic resins are used as adhesives for bonding wood and laminates. In automotive, they are used in the manufacturing of brake pads, clutch facings, and insulation materials. In aerospace, they are used in the manufacturing of composites for aircraft structures.
One of the most significant advantages of phenolic resins is their fire resistance properties. They are classified as self-extinguishing materials and can withstand fire and high temperatures without igniting or releasing toxic gases. This makes phenolic resins ideal for use in applications where fire safety is a concern.
Phenolic resins can also be customized to meet specific application requirements. The curing process of phenolic resins can be adjusted to achieve different properties, such as flexibility and impact resistance. They can also be modified with additives, such as fillers and pigments, to improve their properties and appearance.
However, phenolic resins also have some limitations. They are brittle and can crack under high impact or stress. Additionally, they are not UV-resistant and can degrade when exposed to sunlight, which limits their use in outdoor applications.
In conclusion, phenolic resins are a versatile and widely used type of thermosetting polymer due to their excellent mechanical and thermal properties. They have several advantages over other types of thermosetting polymers, including their heat resistance properties, mechanical properties, and fire resistance properties. Phenolic resins can be customized to meet specific application requirements and can be modified with additives to improve their properties and appearance. However, they also have some limitations, such as their brittleness and lack of UV resistance.
Melamine Resins
Melamine resins are a type of thermosetting polymer that are widely used in the manufacturing of laminates, coatings, and adhesives. They are formed by the reaction between melamine and formaldehyde, resulting in a hard and durable cross-linked structure.
Melamine resins have several advantages over other types of thermosetting polymers. They have excellent heat resistance properties and can withstand temperatures up to 180°C without degrading. They also have excellent chemical resistance properties, making them suitable for use in harsh chemical environments. Additionally, melamine resins have good electrical insulation properties and can be used in the manufacturing of electrical components.
Melamine resins are used in a variety of applications, including furniture, flooring, and food packaging. In furniture, melamine resins are used as laminates for surfaces such as countertops and cabinets. In flooring, they are used as a wear-resistant layer on top of the flooring material. In food packaging, they are used as coatings to prevent contamination and spoilage.
One of the most significant advantages of melamine resins is their durability and scratch resistance properties. They are highly resistant to scratches and abrasions, making them ideal for use in applications that require high durability and wear resistance.
Melamine resins can also be customized to meet specific application requirements. The curing process of melamine resins can be adjusted to achieve different properties, such as flexibility and impact resistance. They can also be modified with additives, such as fillers and pigments, to improve their properties and appearance.
However, melamine resins also have some limitations. They are brittle and can crack under high impact or stress. Additionally, they can release formaldehyde and other volatile organic compounds (VOCs) during the curing process, which can be harmful to human health and the environment. This has led to the development of low-formaldehyde melamine resins, which release lower levels of VOCs during curing.
Melamine resins are a durable and widely used type of thermosetting polymer due to their excellent heat and chemical resistance properties, as well as their scratch resistance properties. They can be customized to meet specific application requirements and can be modified with additives to improve their properties and appearance. However, they also have some limitations, such as their brittleness and potential to release formaldehyde and other VOCs during the curing process.
Lets us discuss the role of Additives in Plastic manufacturing:
Additives Used in Plastic Manufacturing
Additives are substances that are added to polymers during the manufacturing process to enhance their properties, improve processing, or impart new properties. There are various types of additives used in plastic manufacturing, including stabilizers, plasticizers, fillers, pigments, and flame retardants.
Stabilizers
Stabilizers are additives that prevent the degradation of polymers due to heat, light, or oxygen exposure. They help to maintain the mechanical properties and appearance of the plastic over time. Common stabilizers include antioxidants, UV stabilizers, and heat stabilizers.
Antioxidants prevent the oxidation of the polymer by scavenging free radicals. UV stabilizers absorb or scatter UV radiation, protecting the plastic from degradation due to sunlight exposure. Heat stabilizers prevent thermal degradation of the polymer by reacting with unstable intermediates and preventing further breakdown.
Plasticizers
Plasticizers are additives that improve the flexibility and processability of the polymer. They reduce the glass transition temperature (Tg) of the polymer, making it softer and more pliable. Common plasticizers include phthalates, adipates, and citrates.
Plasticizers are commonly used in PVC (polyvinyl chloride) manufacturing to make it more flexible and less brittle. They are also used in other applications, such as coatings, adhesives, and sealants.
Fillers
Fillers are additives that are used to improve the mechanical properties of the polymer, such as strength, stiffness, and impact resistance. They can also reduce the cost of the polymer by replacing some of the more expensive polymer with a less expensive filler material.
Common fillers include calcium carbonate, talc, glass fibers, and carbon black. They are commonly used in thermoplastic manufacturing, such as in automotive parts, construction materials, and consumer goods.
Pigments
Pigments are additives that are added to the polymer to impart color or opacity. They can also improve the weatherability of the polymer by absorbing UV radiation and preventing degradation due to sunlight exposure.
Common pigments include titanium dioxide, iron oxide, and carbon black. They are commonly used in consumer goods, such as toys, packaging, and housewares.
Flame retardants
Flame retardants are additives that are added to the polymer to reduce its flammability and prevent the spread of fire. They work by either releasing water or gases to dilute the flammable gases, or by forming a char layer that acts as a barrier to prevent the spread of fire.
Common flame retardants include brominated compounds, phosphorus-based compounds, and inorganic compounds. They are commonly used in applications that require high fire safety, such as electronics, construction materials, and transportation.
Additives play an essential role in plastic manufacturing by improving the properties, processing, and appearance of the polymer. Stabilizers, plasticizers, fillers, pigments, and flame retardants are some of the most commonly used additives in plastic manufacturing. By carefully selecting and using additives, manufacturers can tailor the properties of the plastic to meet specific application requirements.
Fillers
Fillers are additives that are added to the polymer to improve its mechanical properties and reduce the cost of the plastic. Fillers can be organic or inorganic and are typically added in small amounts. Some common fillers used in plastic manufacturing include talc, calcium carbonate, and glass fibers.
Talc
Talc is a natural mineral that is commonly used as a filler in plastic manufacturing. It is added to the polymer to improve its stiffness and reduce shrinkage during molding. Talc is also used to improve the plastic's resistance to heat and chemicals.
Calcium Carbonate
Calcium carbonate is an inorganic filler that is commonly used in plastic manufacturing. It is added to the polymer to improve its stiffness, impact resistance, and heat resistance. Calcium carbonate is also used to reduce the cost of the plastic.
Glass Fibers
Glass fibers are inorganic fillers that are commonly used in plastic manufacturing. They are added to the polymer to improve its strength, stiffness, and impact resistance. Glass fibers are also used to reduce the weight of the plastic.
Plasticizers
Plasticizers are additives that are added to the polymer to improve its flexibility and reduce its brittleness. Plasticizers are typically added to thermoplastic polymers and can be organic or inorganic. Some common plasticizers used in plastic manufacturing include phthalates, adipates, and citrates.
Phthalates
Phthalates are organic plasticizers that are commonly used in plastic manufacturing. They are added to the polymer to improve its flexibility and reduce its brittleness. Phthalates are also used to improve the plastic's resistance to heat and chemicals.
Adipates
Adipates are organic plasticizers that are commonly used in plastic manufacturing. They are added to the polymer to improve its flexibility and reduce its brittleness. Adipates are also used to improve the plastic's resistance to heat and chemicals.
Citrates
Citrates are organic plasticizers that are commonly used in plastic manufacturing. They are added to the polymer to improve its flexibility and reduce its brittleness. Citrates are also used to improve the plastic's resistance to heat and chemicals.
Stabilizers
Stabilizers are additives that are added to the polymer to improve its resistance to degradation and extend its lifespan. Stabilizers can be used to protect the plastic from UV radiation, heat, and chemicals. Some common stabilizers used in plastic manufacturing include antioxidants, UV stabilizers, and heat stabilizers.
Antioxidants
Antioxidants are additives that are added to the polymer to protect it from oxidation and degradation. Antioxidants can be added to thermoplastic and thermoset polymers and are typically added in small amounts. Antioxidants are also used to improve the plastic's resistance to heat and chemicals.
UV Stabilizers
UV stabilizers are additives that are added to the polymer to protect it from UV radiation. UV stabilizers are typically added to thermoplastic polymers and can be organic or inorganic. UV stabilizers are also used to improve the plastic's resistance to heat and chemicals.
Heat Stabilizers
Heat stabilizers are additives that are added to the polymer to protect it from thermal degradation. Heat stabilizers are typically added to thermoplastic polymers and can be organic or inorganic. Heat stabilizers are also used to improve the plastic's resistance to heat and chemicals.
Colorants
Colorants are additives that are added to the polymer to give it a specific color. Colorants can be organic or inorganic and are typically added in small amounts. Some common colorants used in plastic manufacturing include pigments and dyes.
Pigments
Pigments are inorganic color ants that are commonly used in plastic manufacturing. They are added to the polymer to give it a specific color and can be opaque or transparent. Pigments are also used to improve the plastic's resistance to UV radiation and heat.
Dyes
Dyes are organic colorants that are commonly used in plastic manufacturing. They are added to the polymer to give it a specific color and are typically transparent. Dyes are also used to improve the plastic's resistance to UV radiation and heat.
Flame Retardants
Flame retardants are additives that are added to the polymer to reduce its flammability and improve its resistance to fire. Flame retardants can be organic or inorganic and are typically added in small amounts. Some common flame retardants used in plastic manufacturing include halogenated compounds, phosphorus compounds, and metal oxides.
Halogenated Compounds
Halogenated compounds are organic flame retardants that are commonly used in plastic manufacturing. They are added to the polymer to reduce its flammability and improve its resistance to fire. Halogenated compounds are also used to improve the plastic's resistance to heat.
Phosphorus Compounds
Phosphorus compounds are organic and inorganic flame retardants that are commonly used in plastic manufacturing. They are added to the polymer to reduce its flammability and improve its resistance to fire. Phosphorus compounds are also used to improve the plastic's resistance to heat.
Metal Oxides
Metal oxides are inorganic flame retardants that are commonly used in plastic manufacturing. They are added to the polymer to reduce its flammability and improve its resistance to fire. Metal oxides are also used to improve the plastic's resistance to heat.
How can Deskera Help You?
Deskera's integrated financial planning tools allow investors to better plan their investments and track their progress. It can help investors make decisions faster and more accurately.
Deskera Books can assist you in automating your accounting and mitigating business risks. Deskera makes it easier to create invoices by automating many other procedures, reducing your team's administrative workload.
Deskera also offers a suite of integrated applications to help businesses manage their financials, inventory, and operations. Furthermore, other business aspects such as HR (Deskera People), CRM (Deskera CRM), and ERP are provided by Deskera. These could be crucial and can help short sellers keep track of their businesses and make better decisions.
Conclusion
Here are the main points covered in the article:
- Polymers are large molecules made up of repeating units called monomers.
- Different types of polymers have different properties and applications.
- Additives are substances added to polymers to enhance their properties and make them easier to process.
- Additives can improve properties such as strength, flexibility, color, and UV resistance.
- Common additives include plasticizers, antioxidants, and stabilizers.
- Plastic manufacturing processes include injection molding, blow molding, extrusion, rotational molding, and thermoforming.
- The choice of manufacturing process depends on the specific requirements of the product being made.
- Understanding the properties and functions of different polymers and additives is essential for creating high-quality plastic products.
- Combining different polymers and additives allows for the creation of plastic products with a wide range of properties and applications.
Polymers and additives play a vital role in plastic manufacturing. Polymers are the foundation of plastic and determine its physical and chemical properties. Additives are used to improve the plastic's mechanical properties, flexibility, stability, color, and resistance to heat, chemicals, and fire. The selection of the appropriate polymers and additives is crucial to the success of any plastic manufacturing project. By understanding the properties and functions of polymers and additives, manufacturers can create plastic products that meet the specific needs and requirements of their customers.
Related Articles
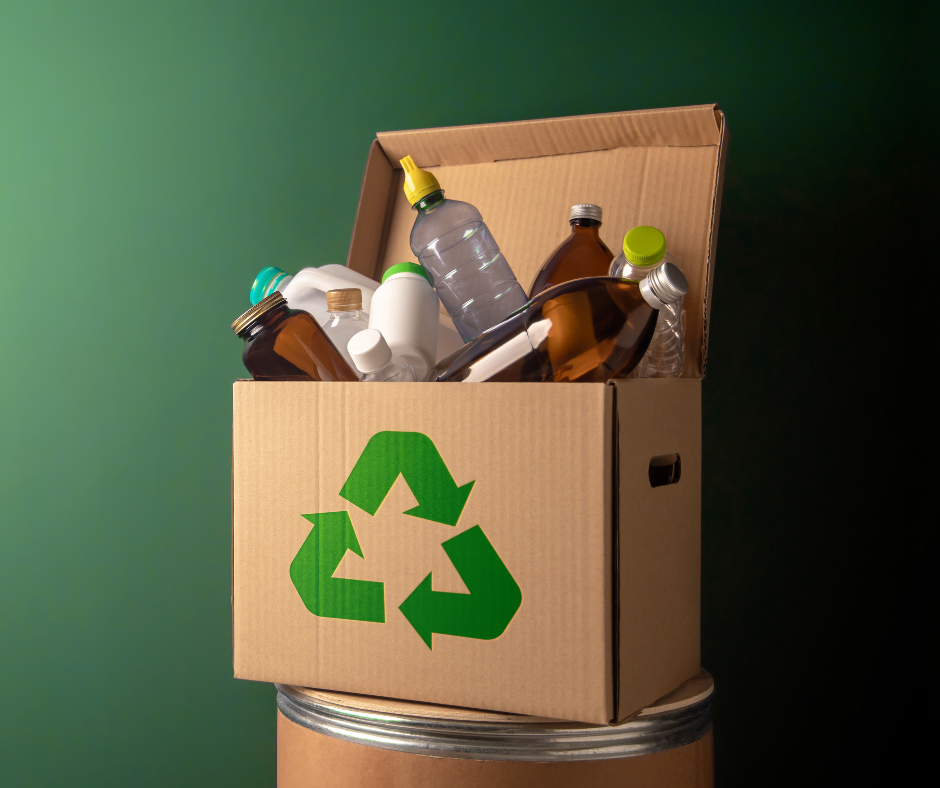
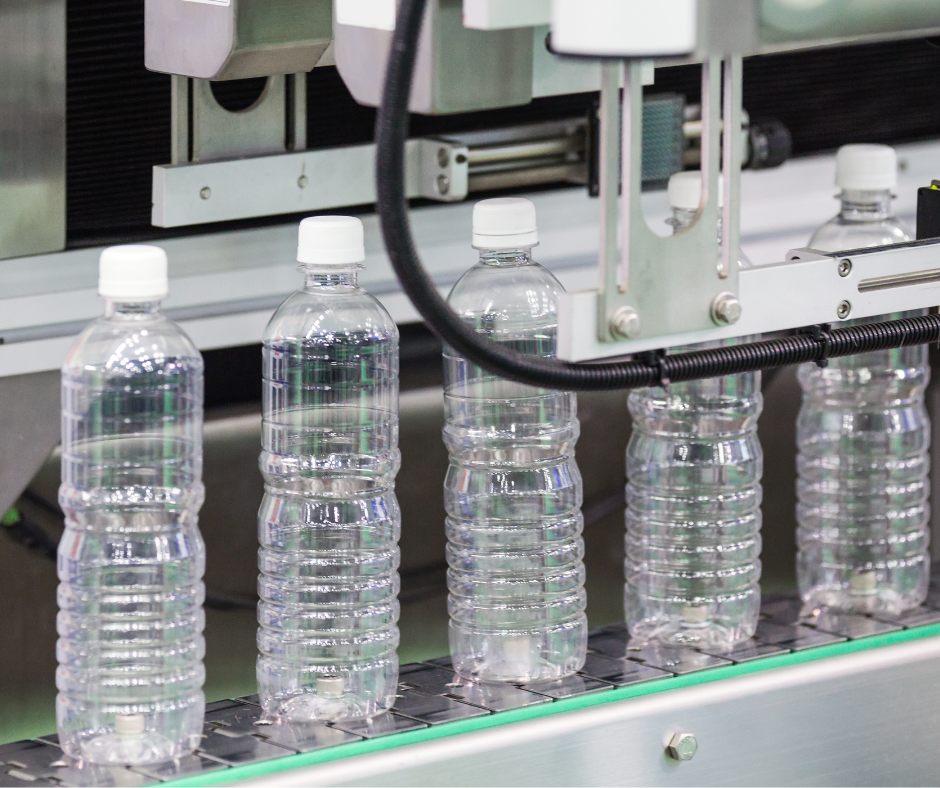
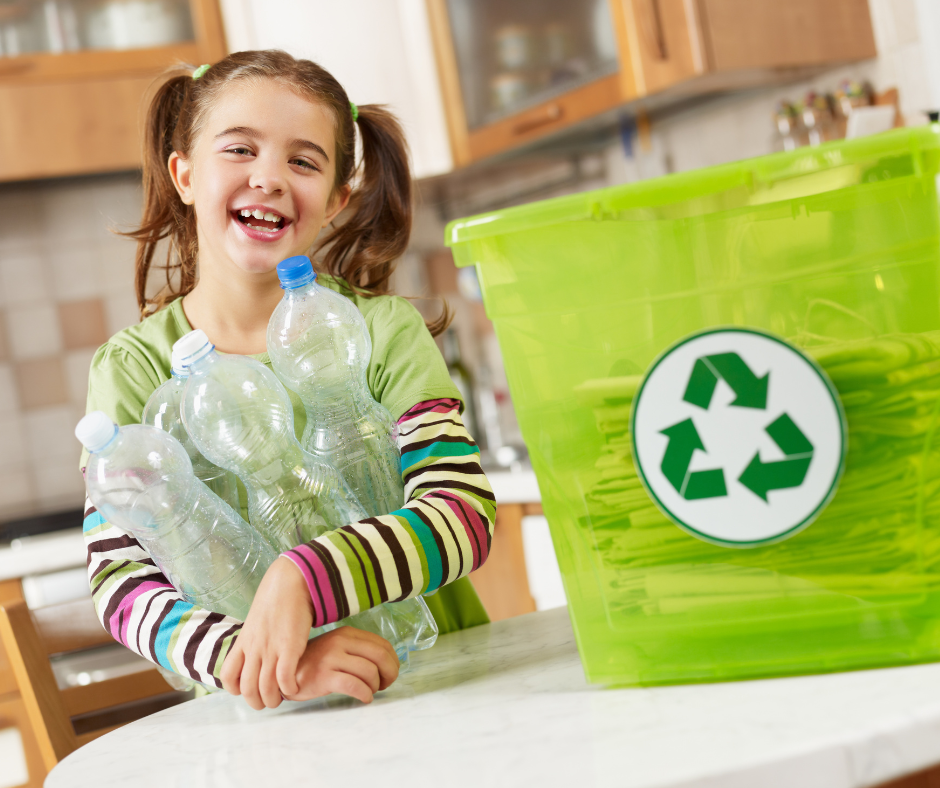