Global plastic production reached 368 million metric tons in 2019 and is projected to double by 2040. (Source: PlasticsEurope, "Plastics - the Facts 2020")
The global bioplastics market is expected to reach USD 19.93 billion by 2027, growing at a CAGR of 15.3% from 2020 to 2027. (Source: Grand View Research, "Bioplastics Market Size, Share & Trends Analysis Report By Type, By Application, By Region And Segment Forecasts, 2020 - 2027")
The global market for recycled plastic is expected to reach USD 72.6 billion by 2026, growing at a CAGR of 5.8% from 2020 to 2026. (Source: MarketsandMarkets, "Recycled Plastics Market by Source, Type, End-Use Industry And Region - Global Forecast to 2026")
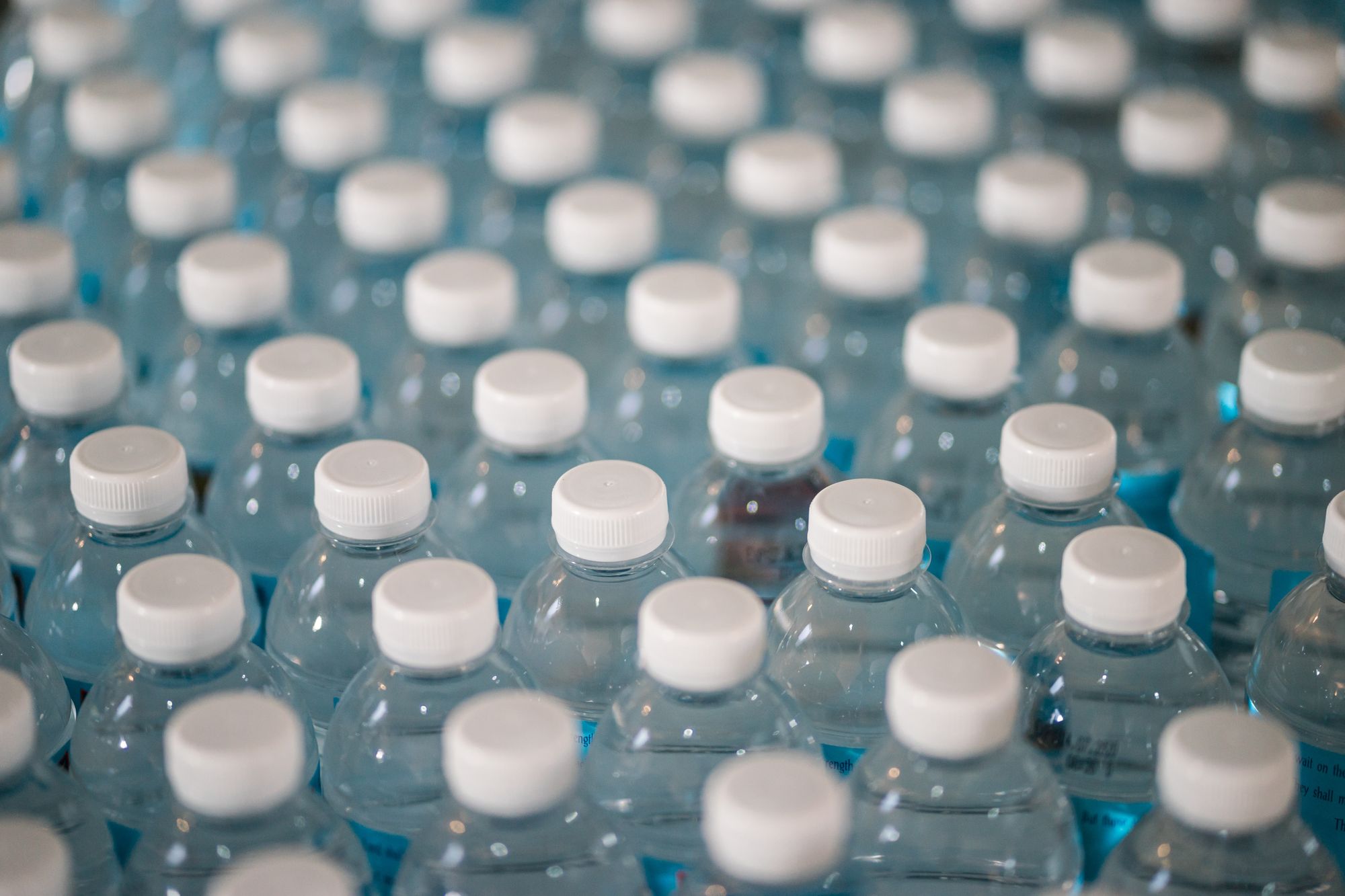
These statistics highlight how plastics are one of the most widely used materials in the world, playing an essential role in our everyday lives. From packaging and building materials to consumer products and medical devices, plastics are found in a vast range of applications. But have you ever wondered how plastics are made?
The process of manufacturing plastic is a complex and multi-step process that involves several techniques, technologies, and materials. This process has evolved over time due to technological advancements and growing concerns about sustainability.
In this context, it is essential to understand the plastic manufacturing process and the various factors that influence it.
This article will help you with that by covering the following topics:
- What is the Plastic Manufacturing Process?
- Plastic Manufacturing Process: How Plastic is Made?
- Challenges Associated with Plastic Manufacturing Process
- Opportunities Associated with Plastic Manufacturing Process
- Areas of Improvement in the Plastic Manufacturing Process
- How have Technological Advancements Affected the Plastic Manufacturing Process?
- Role of Automation in the Plastic Manufacturing Process
- Ensuring Sustainability in Plastic Manufacturing Process
- New Trends in Plastic Manufacturing Process
- FAQs related to Plastic Manufacturing Process
- How can Deskera Help with the Plastic Manufacturing Process?
- Key Takeaways
- Related Articles
What is the Plastic Manufacturing Process?
Plastic manufacturing is a process of converting raw materials into useful plastic products. The process involves several stages, each with its own unique procedures and techniques.
Below is a detailed discussion of the plastic manufacturing process.
- Material Preparation: The first step in plastic manufacturing is material preparation. The raw materials used in plastic manufacturing are petrochemicals, such as ethylene and propylene. The raw materials must be cleaned and processed before they can be used to make plastic. This process involves the separation of impurities and refining of the raw materials.
- Polymerization: Once the raw materials are prepared, they are subjected to polymerization, which is the process of converting small molecules into long-chain polymers. Polymerization is achieved by heating the raw materials in the presence of a catalyst, which helps to link the molecules together into chains. The resulting material is a resin that is used as a base for making plastic.
- Additives: After polymerization, additives are mixed with the resin to give the plastic its desired properties. Additives can include colorants, stabilizers, plasticizers, and other materials that modify the plastic's physical and chemical properties.
- Molding: Molding is the process of shaping the plastic into the desired form. There are several molding techniques, including injection molding, blow molding, and thermoforming. Injection molding involves injecting the molten plastic into a mold, where it cools and solidifies. Blow molding uses air pressure to shape the molten plastic into a hollow form. Thermoforming involves heating the plastic sheet until it is pliable and then shaping it over a mold.
- Finishing: The final stage of plastic manufacturing is finishing. This involves removing any excess material from the molded product and adding any final touches, such as labeling or packaging. The finished products are then ready for distribution.
The plastic manufacturing process is a complex and technical process that requires a high degree of precision and expertise. Quality control is essential at every stage of the process to ensure that the final product meets the required standards.
In recent years, there has been a growing focus on sustainability and reducing the environmental impact of plastic manufacturing, leading to the development of new materials and production methods that aim to minimize waste and energy consumption.
Plastic Manufacturing Process: How Plastic is Made?
Plastic is a synthetic polymer made from organic materials such as petroleum and natural gas. The manufacturing process for plastic involves several steps, including:
Polymerization
Polymerization is a process that is used to create long chains of polymers from smaller molecules called monomers in plastic manufacturing. In this process, the monomers are chemically bonded together to create a polymer, which can be shaped and molded into various forms.
There are different methods of polymerization used in plastic manufacturing, depending on the type of polymer being produced and the desired properties of the final product.
There are different types of polymerization processes used in plastic manufacturing, including:
- Addition polymerization: This process involves the combination of monomers without the elimination of any byproducts. For example, polyethylene is created through the addition polymerization of ethylene molecules.
- Condensation polymerization: This process involves the combination of two or more different monomers with the elimination of a small molecule, such as water. For example, nylon is created through the condensation polymerization of a diamine and a dicarboxylic acid.
- Ring-opening polymerization: This process involves the opening of cyclic monomers to create linear polymers. For example, polycaprolactone is created through the ring-opening polymerization of caprolactone.
- Free radical polymerization: This method involves the use of free radicals to initiate the polymerization reaction. The free radicals are generated through the use of initiators, which can be heat, light, or chemical compounds. This method is commonly used to produce polymers such as polyvinyl chloride and polyacrylonitrile.
- Ionic polymerization: In this method, the polymerization reaction is initiated through the use of an ionic initiator, which generates a charged species that can react with the monomers to form a polymer. This method is commonly used to produce polystyrene and polyvinyl acetate.
Polymerization is a critical step in plastic manufacturing, as it determines the properties and characteristics of the resulting polymer. The type of polymerization used will depend on the desired properties of the plastic and the intended use of the final product.
Extrusion
Extrusion is a common manufacturing process used in plastic manufacturing. In this process, a material is melted and then forced through a die to create a continuous shape with a fixed cross-section. The process is used to create a wide range of plastic products, including pipes, tubes, sheets, films, and profiles.
The extrusion process involves several steps:
- Material preparation: The raw plastic material is first prepared by blending and drying the resin pellets to remove any moisture.
- Feeding: The prepared material is then fed into the extruder through a hopper. An extruder is a machine that heats and melts plastic material.
- Melting and mixing: Inside the extruder, the plastic material is heated and mixed using a screw mechanism. The heat and pressure cause the material to melt and become homogeneous.
- Shaping: The molten plastic is then forced through a die, which gives it the desired shape. The die can have a simple or complex shape, depending on the final product.
- Cooling: The extruded plastic is then cooled using a water bath or air cooling system. This solidifies the plastic and ensures it retains the desired shape.
- Cutting and finishing: The extruded plastic is then cut to the desired length and undergoes any finishing processes, such as polishing or coating.
Extrusion is a versatile process that can be used to produce a wide range of plastic products of different shapes and sizes. It is a cost-effective and efficient manufacturing method that can produce high volumes of products with consistent quality.
Injection Molding
Injection molding is a popular manufacturing process used in the production of plastic products. In this process, plastic material is melted and then injected into a mold under high pressure. Once the plastic cools and solidifies, it is removed from the mold, resulting in a finished product.
The injection molding process involves several steps:
- Material preparation: The plastic resin pellets are first dried and then melted in the injection molding machine.
- Injection: The melted plastic is injected into a mold cavity under high pressure. The mold is typically made of two halves that fit together to create the desired shape of the product.
- Cooling: The plastic material is allowed to cool and solidify inside the mold.
- Ejection: Once the plastic has solidified, the mold is opened, and the finished product is ejected from the mold.
- Finishing: The product may undergo additional finishing processes, such as trimming excess plastic or applying a coating.
Injection molding is used to produce a wide range of products, from small and intricate parts to larger objects such as car parts and household appliances.
The process allows for high levels of precision and consistency in the final product. It is a highly automated process that can produce large volumes of products quickly and efficiently. Injection molding is used extensively in the plastic manufacturing industry due to its versatility and cost-effectiveness.
Blow Molding
Blow molding is a manufacturing process used in plastic manufacturing to produce hollow plastic parts, such as bottles, containers, and tanks. The process involves melting plastic resin and forming it into a hollow tube or parison, which is then inflated using compressed air to take the shape of a mold.
The blow molding process involves several steps:
- Material preparation: The plastic resin pellets are first dried and then melted in an extruder.
- Forming the parison: The molten plastic is extruded through a die to form a tube-like shape called a parison.
- Molding: The parison is then placed into a mold, which is typically made up of two halves. The mold is closed around the parison, and compressed air is blown into the parison, causing it to expand and take the shape of the mold.
- Cooling: The plastic is then allowed to cool and solidify inside the mold.
- Ejection: Once the plastic has solidified, the mold is opened, and the finished product is ejected from the mold.
Blow molding is used to produce a wide range of products with varying shapes and sizes. It is a highly automated process that can produce large volumes of products quickly and efficiently. There are three main types of blow molding processes: extrusion blow molding, injection blow molding, and stretch blow molding.
Extrusion blow molding is the most common method used to produce large quantities of bottles, while injection blow molding is used for smaller, more precise products. Stretch blow molding is used for producing PET bottles, jars, and containers.
Thermoforming
Thermoforming is a plastic manufacturing process that involves heating a plastic sheet until it is pliable and then forming it into a specific shape using a mold. The process is used to produce a wide range of products, including packaging, trays, containers, and automotive parts.
The thermoforming process involves several steps:
- Material preparation: The plastic sheet is prepared by heating it to a specific temperature. The plastic sheet can be made from a variety of materials, such as polystyrene, polypropylene, and PET.
- Forming: The heated plastic sheet is then placed into a mold, which can be made of aluminum or other materials. The mold is designed to create the desired shape of the final product.
- Cooling: The formed plastic is then allowed to cool and solidify inside the mold.
- Trimming: The finished product is then trimmed to remove any excess plastic and to create a clean edge.
Thermoforming is a versatile process that can produce large or small quantities of products at a relatively low cost. The process is efficient and can produce products quickly, making it a popular choice for many plastic manufacturers.
Additionally, thermoforming is a sustainable process because it generates less waste than other manufacturing methods, and the plastic sheets used in the process can be recycled.
Compression Molding
Compression molding is a plastic manufacturing technique used to create complex shapes and parts with tight tolerances. The process involves compressing preheated plastic material in a mold cavity, where it is then cooled and solidified. Compression molding is a popular method used to create thermosetting plastic products that are strong, durable, and resistant to heat and chemicals.
The process begins by placing a pre-measured amount of plastic material, typically in the form of a preform, into a heated mold cavity. The mold is then closed, and pressure is applied to the material, forcing it to flow and take the shape of the mold. The mold is held under pressure until the plastic material cools and solidifies, which may take several minutes.
Compression molding can be used to create a wide range of products, including automotive parts, electrical components, and household appliances. The process is particularly suitable for creating parts with intricate designs, high strength, and good dimensional stability. The main advantage of compression molding is its ability to produce large parts with consistent quality and high precision, making it a popular choice for mass production.
Rotational Molding
Rotational molding is a plastic manufacturing technique used to create large, hollow plastic parts such as tanks, containers, and playground equipment. The process involves rotating a mold around two perpendicular axes while plastic material is added to the mold and heated until it forms a solid layer. Rotational molding is a cost-effective method used to create complex shapes with consistent wall thickness and excellent durability.
The process starts with adding measured amounts of plastic material, usually in the form of a powder or liquid, into a hollow mold. The mold is then heated and rotated around two perpendicular axes while the plastic material melts and coats the entire inner surface of the mold. The rotation continues until the plastic material has fully melted and forms a solid layer of the desired thickness. The mold is then cooled and opened to remove the finished product.
Rotational molding is particularly suitable for creating large, hollow parts that cannot be easily made with other molding techniques. The process can also produce parts with consistent wall thickness and excellent durability, making it ideal for creating products such as water tanks, playground equipment, and large storage containers.
The main advantage of rotational molding is that it can produce complex shapes with no seams or joints, which reduces the risk of leakage and improves the structural integrity of the final product. Additionally, the low tooling cost and short setup time make it a cost-effective method for producing small to medium volumes of parts.
3D Printing
3D printing, also known as additive manufacturing, is a plastic manufacturing technique that allows for the creation of three-dimensional objects from digital models. The process involves adding successive layers of molten plastic material to build up the final product layer by layer. 3D printing has revolutionized plastic manufacturing, offering a high degree of design flexibility, fast turnaround times, and reduced waste.
The 3D printing process starts with a digital model, which is created using computer-aided design (CAD) software or 3D scanning. The digital model is then sliced into thin layers, and the 3D printer begins printing the object layer by layer. The printer deposits melted plastic material onto a build platform or onto a previously printed layer, creating a three-dimensional object.
3D printing offers several benefits for plastic manufacturing. First, it allows for the creation of complex shapes and geometries that are difficult or impossible to produce with traditional manufacturing methods. Second, it offers faster turnaround times and reduced tooling costs compared to traditional manufacturing methods. Third, it reduces material waste since only the required amount of material is used to produce the object.
3D printing is used in a wide range of industries, including aerospace, automotive, medical, and consumer goods. It is commonly used for prototyping, small-scale production, and custom-made parts. As technology continues to evolve and become more sophisticated, it has the potential to transform the entire plastic manufacturing industry.
Finishing
Finishing is a process in plastic manufacturing that involves applying additional treatments or modifications to the surface of a plastic product to improve its appearance or performance. Finishing processes can vary depending on the type of plastic product being produced and its intended use.
Some common finishing processes in plastic manufacturing include:
- Trimming: Trimming is the process of removing any excess material or flash from the finished product. This process is typically performed after the product has been formed using processes such as injection molding, blow molding, or thermoforming.
- Painting or coating: Painting or coating is a process that can be used to enhance the appearance of a plastic product or to provide additional protection from the environment. Products can be painted using a variety of methods, including spray painting, dip coating, or electrostatic coating.
- Printing: Printing is a process used to apply graphics, logos, or other designs to a plastic product. This can be achieved using techniques such as screen printing, digital printing, or pad printing.
- Surface treatment: Surface treatment is a process used to modify the surface properties of a plastic product. For example, a surface treatment can be used to make a plastic product more resistant to scratching or to improve its adhesion properties.
- Assembly: Assembly is a process used to join multiple plastic components together to create a finished product. This can be achieved using techniques such as welding, adhesives, or mechanical fasteners.
Finishing is an important part of plastic manufacturing because it can improve the functionality, durability, and aesthetics of a plastic product. By applying the appropriate finishing process, manufacturers can create plastic products that meet specific design and performance requirements.
Quality Control
Quality control is a critical aspect of plastic manufacturing to ensure that the final products meet the required standards and specifications. Here are some of the quality control measures commonly used in plastic manufacturing:
- Raw material inspection: Quality control starts with inspecting the raw materials used in plastic production, such as polymers, additives, fillers, and colorants, to ensure that they meet the required standards and specifications.
- Process monitoring: Quality control involves monitoring the various processes involved in plastic manufacturing, such as polymerization, compounding, extrusion, injection molding, and blow molding, to detect any deviations from the required parameters.
- Testing: Quality control includes testing the plastic products to ensure that they meet the required specifications, such as tensile strength, elongation, impact resistance, and color consistency.
- Inspection: Quality control involves inspecting the plastic products visually to check for any defects, such as cracks, warping, or uneven surfaces.
- Statistical process control: Quality control may use statistical process control methods to track and analyze the manufacturing process to identify and correct any deviations from the required standards.
- Employee training: Quality control may involve training employees on the importance of quality control and the specific procedures to follow to ensure that the plastic products meet the required specifications.
Overall, quality control is an essential aspect of plastic manufacturing, and it requires a comprehensive approach to ensure that the final products are of high quality and meet the required standards.
What must be kept in mind is that quality control should be implemented at every stage of plastic manufacturing to ensure that the final product meets the required standards and specifications.
Waiting until the end of the manufacturing process to implement quality control can be costly and time-consuming. Detecting defects at the end of the process can lead to the need for significant rework or even scrapping of the entire production run. This can result in delays, additional costs, and reduced customer satisfaction.
Therefore, quality control should be implemented throughout the entire manufacturing process. This includes monitoring the raw materials used in production, monitoring the various processes involved in plastic manufacturing, testing the plastic products during and after production, and inspecting the final product before it is shipped to customers.
By implementing quality control at every stage of the manufacturing process, defects can be detected and corrected early, reducing the likelihood of costly rework and ensuring that the final product meets the required quality standards.
Challenges Associated with Plastic Manufacturing Process
While plastics have many advantages and are widely used, there are also significant challenges associated with how they are made. Some of the main challenges include the following:
- Environmental impact: The production of plastics is associated with a significant environmental impact, including greenhouse gas emissions, water pollution, and land use.
- Energy consumption: The production of plastics is energy-intensive, with large amounts of energy required to extract and refine the raw materials and manufacture the final products.
- Waste generation: Plastics is a major source of waste, and the disposal of plastic waste is a significant environmental problem, with plastic pollution causing harm to wildlife and ecosystems.
- Non-renewable resources: Many plastics are made from non-renewable resources such as petroleum, which are finite and contribute to climate change.
- Health concerns: Some types of plastics contain chemicals that are harmful to human health, including endocrine disruptors and carcinogens.
- Supply chain challenges: The production of plastics involves complex supply chains that can be vulnerable to disruptions and issues such as price volatility and geopolitical risks.
- Consumer behavior: Consumers often use plastics in ways that are not sustainable, such as single-use plastic products that are not recycled or disposed of properly.
In conclusion, the challenges associated with how plastics are made are significant and require ongoing efforts to address. Addressing these challenges will require innovative solutions that reduce the environmental impact of plastic production, promote sustainability, and encourage responsible consumer behavior.
Opportunities Associated with Plastic Manufacturing Process
Despite the challenges associated with how plastics are made, there are also significant opportunities for innovation and growth in the industry. Some of the main opportunities include:
- Development of sustainable materials: The increasing focus on sustainability and environmental responsibility is driving demand for new, sustainable materials that can replace traditional plastics.
- Advancements in recycling technology: Innovations in recycling technology are creating opportunities to recover and reuse plastic waste, reducing the environmental impact of plastic production.
- Digitalization: Digital technologies such as artificial intelligence and the internet of things are creating new opportunities for efficiency and quality improvements in plastic manufacturing.
- Development of smart plastics: Smart plastics that can sense and respond to their environment are opening up new possibilities for applications in areas such as healthcare and transportation.
- Customization and personalization: The use of 3D printing and other additive manufacturing technologies is creating new opportunities for the customization and personalization of plastic products.
- Development of bioplastics: The development of bioplastics, which are made from renewable resources and can biodegrade, is creating new opportunities for environmentally friendly plastic production.
- Advancements in materials science: Advances in materials science are leading to the development of new plastics with improved properties, such as increased strength, durability, and resistance to heat and chemicals.
- Development of circular economy models: The adoption of circular economy models that prioritize the reuse and recycling of materials is creating new opportunities for sustainable plastic production.
In conclusion, the challenges associated with how plastics are made are significant, but there are also many opportunities for innovation and growth in the industry. By embracing sustainable practices and new technologies, the plastic industry can continue to evolve and meet the changing needs of consumers and the environment.
Areas of Improvement in the Plastic Manufacturing Process
There are several areas of improvement in plastic manufacturing processes that can help address the challenges associated with plastic production and promote sustainability. Some of the main areas of improvement include:
- Raw materials: Using renewable raw materials such as plant-based feedstocks and waste materials can help reduce reliance on non-renewable resources and decrease the environmental impact of plastic production.
- Energy efficiency: Implementing energy-efficient processes and equipment can reduce energy consumption and greenhouse gas emissions during plastic production.
- Waste reduction: Reducing waste generation and promoting circular economy models that prioritize the reuse and recycling of plastics can help reduce the environmental impact of plastic production.
- Green chemistry: Adopting green chemistry principles and practices can help reduce the use of hazardous chemicals and promote safer and more sustainable plastic production.
- Sustainable design: Designing products with end-of-life considerations in mind can promote circularity and reduce the environmental impact of plastic products.
- Supply chain transparency: Improving supply chain transparency and traceability can help identify and address sustainability issues throughout the plastic production process.
- Collaboration: Collaboration among stakeholders, including plastic manufacturers, governments, NGOs, and consumers, can help drive progress toward sustainable plastic production.
In conclusion, there are several areas of improvement in plastic manufacturing processes that can help address the environmental impact of plastic production and promote sustainability. By adopting sustainable practices and embracing new technologies, the plastic industry can continue to evolve and meet the changing needs of consumers and the environment.
How has Technological Advancements Affected Plastic Manufacturing Process?
Technological advancements have led to significant changes in how plastics are made. The following are some of the changes that have occurred in plastic manufacturing due to technological advancements:
- 3D Printing: The development of 3D printing technology has revolutionized the way plastics are made. With 3D printing, it is possible to create complex plastic shapes and designs that were previously impossible to manufacture using traditional methods. This technology has led to the development of customized and low-volume production of plastic products.
- Bioplastics: The use of bioplastics, which are made from renewable resources such as corn starch, has become more popular in recent years. Technological advancements have made it possible to produce bioplastics that are strong and durable enough to be used in various applications, including packaging and consumer goods.
- Recycling: Technological advancements have led to the development of more efficient recycling methods for plastic. Recycling facilities now use advanced technologies to sort and process plastics, allowing for a higher percentage of plastics to be recycled into new products.
- Nanotechnology: Nanotechnology is being used in the development of new types of plastics with unique properties. For example, nanotechnology can be used to create plastics that are more resistant to UV light, making them ideal for outdoor applications.
- Lightweighting: Technological advancements have enabled manufacturers to create plastic products that are lighter in weight while maintaining their strength and durability. This has led to the development of lighter and more fuel-efficient vehicles and packaging materials.
- Automation: Automation has led to improved production efficiency and quality control in plastic manufacturing. Robotics and other automated systems can perform repetitive tasks with high precision, reducing the risk of errors and improving the overall quality of the products.
In conclusion, technological advancements have had a significant impact on the plastic manufacturing industry, leading to the development of new materials, production methods, and recycling technologies. These advancements have enabled manufacturers to produce stronger, lighter, and more sustainable plastic products while reducing waste and energy consumption.
Role of Automation in the Plastic Manufacturing Process
Automation plays a significant role in the plastic manufacturing process, providing several benefits, including:
- Increased production efficiency: Automation can streamline the manufacturing process, reducing the time required to complete tasks and increasing production efficiency. This will help in reducing manufacturing lead times and manufacturing costs, while leading to an increase in net revenue and net profit ratio.
- Improved quality control: Automated systems can perform tasks with a high degree of precision, improving the consistency and quality of products. This will help in improving customer retention and customer loyalty.
- Reduced labor costs: Automation can reduce labor costs by replacing manual labor with automated systems, reducing the need for human workers. This will improve your cash flow, and increase the ratio of operating income to operating expenses.
- Enhanced safety: Automated systems can perform tasks that are dangerous or hazardous to human workers, improving workplace safety, which will help in retaining top talents as well as better management of workplace stress.
- Increased production capacity: Automation can increase production capacity by allowing manufacturers to produce more products in a shorter amount of time.
- Data collection and analysis: Automated systems can collect data on production processes, allowing manufacturers to analyze and optimize their manufacturing processes for improved efficiency and quality.
Some examples of automation in plastic manufacturing include:
- Injection molding machines: Injection molding machines use automated systems to inject molten plastic into molds, allowing for high-volume production of plastic parts.
- Robotics: Robotics can be used for a range of tasks in plastic manufacturing, including material handling, assembly, and packaging.
- Automated inspection systems: Automated inspection systems can perform quality control checks on plastic products, identifying defects and ensuring consistency and quality.
- Material handling systems: Automated material handling systems can transport raw materials and finished products throughout the manufacturing process, reducing the need for human workers.
In conclusion, automation plays a critical role in the plastic manufacturing process, providing benefits such as increased production efficiency, improved quality control, reduced labor costs, enhanced safety, increased production capacity, and data collection and analysis.
By embracing automation, manufacturers can optimize their production processes, reduce costs, and improve the quality and consistency of their products.
Ensuring Sustainability in Plastic Manufacturing Process
Ensuring sustainability in plastic manufacturing is an important goal for the industry. There are several ways that sustainability is ensured in how plastics are made.
- Reducing Raw Material Use: One way to ensure sustainability is to reduce the number of raw materials used in plastic production. This can be achieved through the use of lightweight and thin-wall molding techniques, which reduce the amount of plastic needed to create a product.
- Recycling: Recycling is another important aspect of sustainability in plastic manufacturing. Many plastic products are recyclable, and recycling facilities can turn them into new products, reducing the amount of plastic waste that ends up in landfills and oceans.
- Bioplastics: The use of bioplastics, which are made from renewable resources such as corn starch, can also promote sustainability. Bioplastics can be composted, reducing the amount of plastic waste that ends up in landfills.
- Energy Efficiency: Manufacturers can also promote sustainability by improving energy efficiency in their production processes. This can be achieved through the use of energy-efficient equipment, process improvements, and the use of renewable energy sources.
- Life Cycle Assessment: Life cycle assessment (LCA) is a tool used to assess the environmental impact of a product throughout its entire life cycle, from raw material extraction to disposal. By conducting an LCA, manufacturers can identify areas where improvements can be made to promote sustainability.
- Sustainability Certifications: There are several sustainability certifications available for plastic products, such as the Cradle to Cradle certification and the Sustainable Forestry Initiative. These certifications provide a way for manufacturers to demonstrate their commitment to sustainability to customers and stakeholders.
In conclusion, sustainability in plastic manufacturing can be achieved through various methods, including reducing raw material use, recycling, using bioplastics, improving energy efficiency, conducting life cycle assessments, and obtaining sustainability certifications.
By incorporating these methods into their production processes, manufacturers can promote sustainability and reduce their environmental impact.
New Trends in Plastic Manufacturing Process
There are several new trends in how plastics are made that are shaping the future of the industry. These trends include:
- Biodegradable plastics: Manufacturers are increasingly focusing on developing biodegradable plastics that can break down naturally in the environment, reducing their impact on ecosystems.
- Plant-based plastics: There is a growing trend towards using plant-based materials to create plastics, as they are renewable and more environmentally friendly than traditional petroleum-based plastics.
- Recycling technologies: Innovations in recycling technologies are making it easier to recycle and reuse plastics, reducing waste and promoting sustainability.
- Advanced materials: Advances in materials science are leading to the development of new plastics with improved properties, such as increased strength, durability, and resistance to heat and chemicals.
- Smart plastics: Smart plastics are materials that can sense and respond to changes in their environment, opening up new possibilities for applications such as medical devices and sensors.
- Advanced Composites: Advanced composites are materials made from a combination of plastic and other materials, such as carbon fiber or fiberglass. These materials are lightweight, strong, and durable, making them ideal for use in the aerospace, automotive, and construction industries.
- 3D printing: Additive manufacturing or 3D printing is being increasingly used in plastic manufacturing, allowing for the creation of complex designs and customized products.
- Digitalization: Digital technologies such as artificial intelligence and the internet of things are being used to improve the efficiency and quality of plastic production processes.
- Closed-loop systems: Some manufacturers are adopting closed-loop systems in which plastics are recycled and reused within the same production process, reducing waste and increasing efficiency.
- Sustainable packaging: With the rise of e-commerce, there is a growing demand for sustainable packaging materials that can protect products during shipping while reducing waste and environmental impact.
- Lifecycle assessments: Lifecycle assessments are being used to evaluate the environmental impact of plastic production and help manufacturers identify areas where they can improve sustainability.
FAQs related to Plastic Manufacturing Process
- What is plastic manufacturing?
Plastic manufacturing is the process of producing plastic products from raw materials.
- What are the raw materials used in plastic manufacturing?
The most commonly used raw materials in plastic manufacturing are petrochemicals, such as ethylene and propylene.
- What are the different processes used in plastic manufacturing?
There are several processes used in plastic manufacturing, including injection molding, blow molding, extrusion, and thermoforming.
- What is injection molding in plastic manufacturing?
Injection molding is a process in which melted plastic is injected into a mold and then cooled to create a solid plastic product.
- What is blow molding in plastic manufacturing?
Blow molding is a process in which air is used to blow melted plastic into a mold to create a hollow plastic product.
- What is extrusion in plastic manufacturing?
Extrusion is a process in which melted plastic is forced through a die to create a continuous shape.
- What is thermoforming in plastic manufacturing?
Thermoforming is a process in which plastic sheets are heated and formed into specific shapes.
- What are the steps in the plastic manufacturing process?
The plastic manufacturing process typically involves material preparation, melting and shaping, cooling, and finishing.
- What are the safety considerations in plastic manufacturing?
Safety considerations in plastic manufacturing include proper use of equipment, handling of chemicals, and adherence to safety protocols.
- How is quality control maintained in plastic manufacturing?
Quality control in plastic manufacturing is maintained through inspections, testing, and adherence to industry standards.
- What are some common plastic products made through manufacturing?
Common plastic products made through manufacturing include packaging, bottles, toys, automotive parts, and consumer goods.
- What is the impact of plastic manufacturing on the environment?
Plastic manufacturing can contribute to environmental pollution through greenhouse gas emissions, waste generation, and littering.
- How can plastic manufacturing be made more sustainable?
Plastic manufacturing can be made more sustainable through the use of renewable materials, improved recycling processes, and a reduction in energy consumption.
- What is the role of automation in plastic manufacturing?
Automation in plastic manufacturing can improve efficiency, reduce errors, and increase productivity.
- What are some emerging technologies in plastic manufacturing?
Emerging technologies in plastic manufacturing include biodegradable plastics, 3D printing, and advanced recycling methods.
- How are plastic manufacturers addressing concerns about waste and pollution?
Plastic manufacturers are developing new materials, exploring sustainable production methods, and supporting recycling efforts.
- What is the economic impact of plastic manufacturing?
Plastic manufacturing has a significant economic impact, providing jobs and contributing to global trade.
- How can consumers make a difference in plastic manufacturing?
Consumers can make a difference in plastic manufacturing by reducing their use of single-use plastics, recycling properly, and supporting companies with sustainable practices.
- What is the future of plastic manufacturing?
The future of plastic manufacturing will likely focus on sustainability, innovation, and reducing environmental impact.
- How is plastic manufacturing regulated?
Plastic manufacturing is regulated through various national and international regulations and standards, such as those set by the Environmental Protection Agency and the International Organization for Standardization.
How can Deskera Help with the Plastic Manufacturing Process?
Deskera MRP is a business software solution that offers a range of tools to help manage various aspects of the manufacturing process, including plastic manufacturing. Deskera can help with the plastic manufacturing process in the following ways:
- Inventory management: Deskera can help manage inventory levels of raw materials and finished products, ensuring that manufacturers have the necessary materials and products on hand to meet production demands.
- Production planning and scheduling: Deskera can help manufacturers plan and schedule production processes, optimizing production efficiency and reducing waste.
- Quality control: Deskera can help ensure quality control measures are in place throughout the production process, ensuring that finished products meet quality standards and reduce the risk of defects.
- Supply chain management: Deskera can help manage supply chain processes, including procurement, shipping, and logistics, ensuring that materials and products are delivered on time and at the best possible price.
- Compliance management: Deskera can help manage compliance requirements for plastic manufacturing, including environmental regulations and safety standards.
- Financial management: Deskera can help manage financial aspects of the plastic manufacturing process, including tracking costs, expenses, and revenues and generating financial reports.
Key Takeaways
Plastic manufacturing is a process of converting raw materials into useful plastic products. The process involves several stages, each with its own unique procedures and techniques. These stages are:
- Polymerization
- Extrusion
- Injection molding
- Blow molding
- Thermoforming
- Compression molding
- Rotational molding
- 3D printing
- Finishing
The challenges associated with plastic manufacturing processes are:
- Environmental impact
- Energy consumption
- Waste generation
- Non-renewable resources
- Health concerns
- Supply chain challenges
- Consumer behavior
The opportunities associated with plastic manufacturing processes are:
- Development of sustainable materials
- Advancements in recycling technology
- Digitalization
- Development of smart plastics
- Customization and personalization
- Development of bioplastics
- Advancements in materials science
- Development of circular economy models
New trends in the plastic manufacturing process are:
- Biodegradable plastics
- Plant-based plastics
- Recycling technologies
- Advanced materials
- Smart plastics
- Advanced Composites
- 3D printing
- Digitalization
- Closed-loop systems
- Sustainable packaging
- Lifecycle assessments
Technological advancements have played a crucial role in improving the plastic manufacturing process, leading to increased efficiency, consistency, and quality. Automation has become an essential tool for plastic manufacturing, allowing for increased precision and reducing labor costs.
Environmental challenges, such as waste generation and pollution, are associated with plastic manufacturing, and sustainable practices should be embraced. Sustainability is a growing concern in the plastic manufacturing industry, leading to the development of eco-friendly alternatives such as bioplastics.
Deskera MRP can help with the plastic manufacturing process by providing a comprehensive business software solution that addresses the various aspects of manufacturing, including inventory management, production planning, quality control, supply chain management, compliance management, and financial management.
With Deskera, manufacturers can optimize their production processes, reduce waste, and ensure compliance with regulations, ultimately improving their efficiency and profitability.
Related Articles
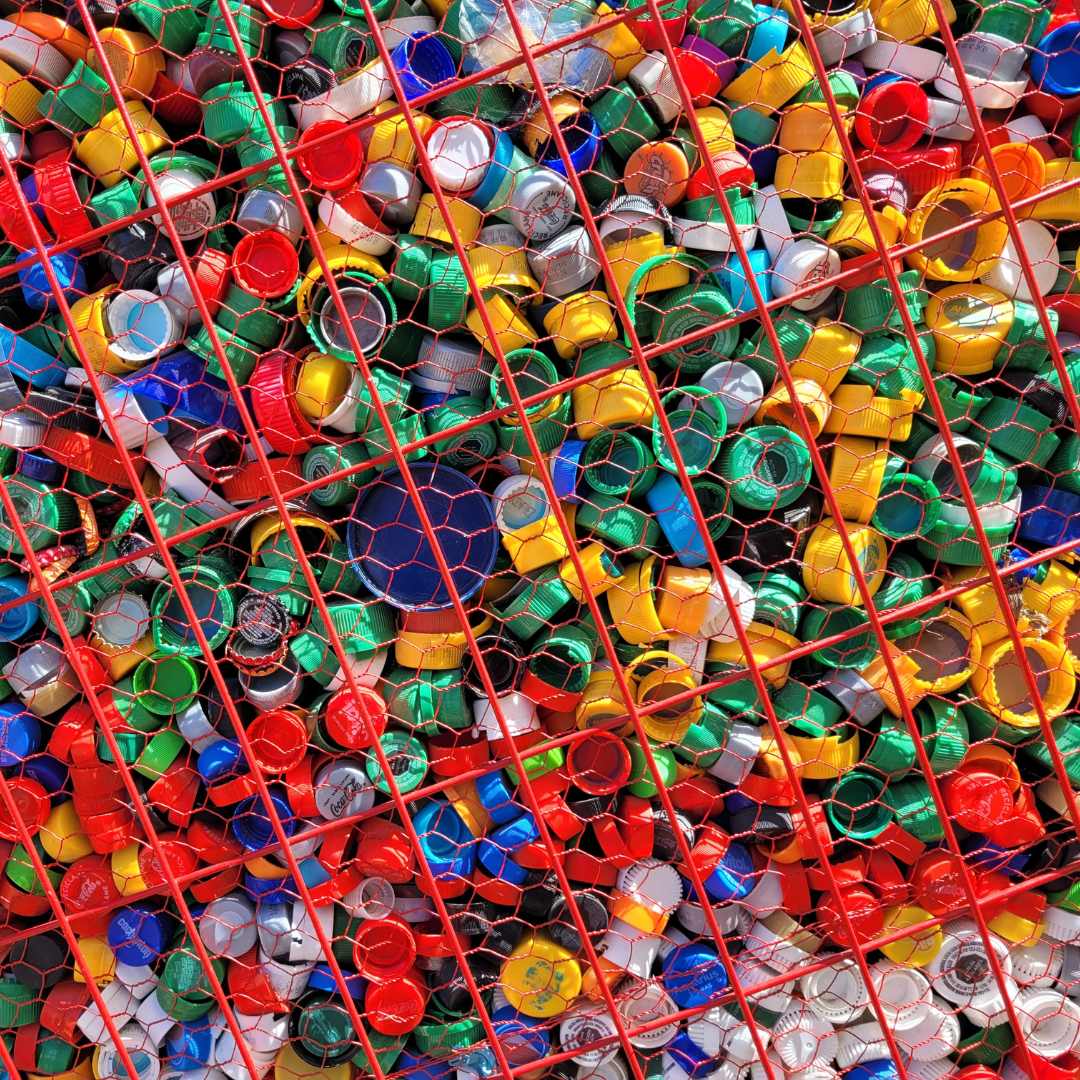
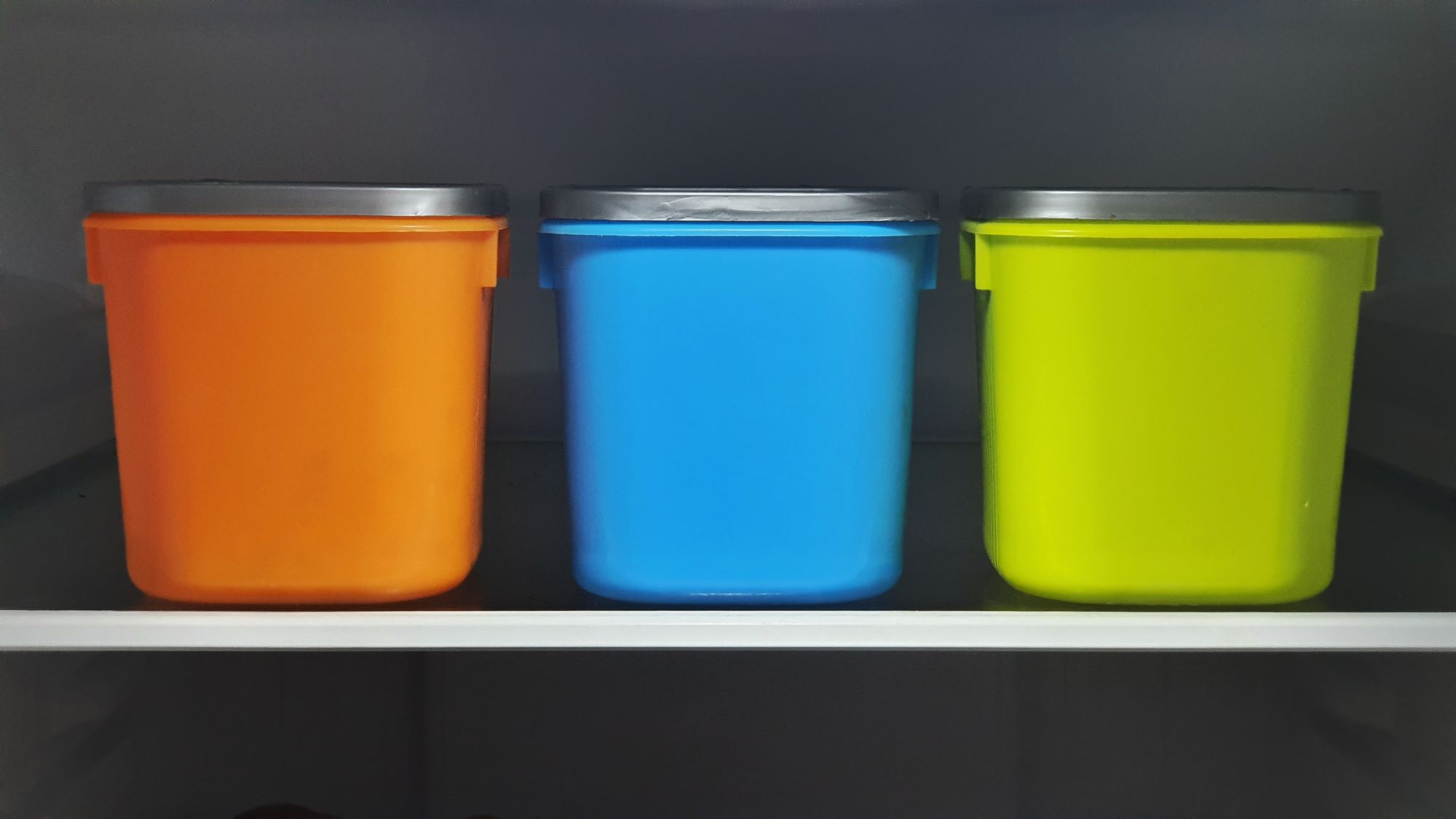
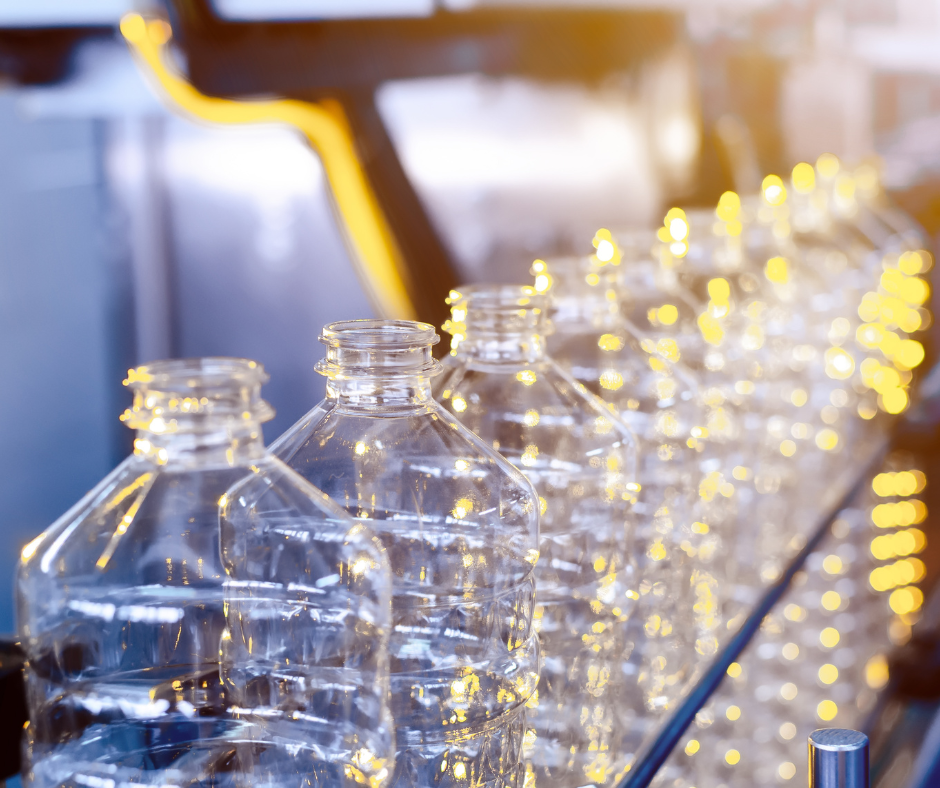
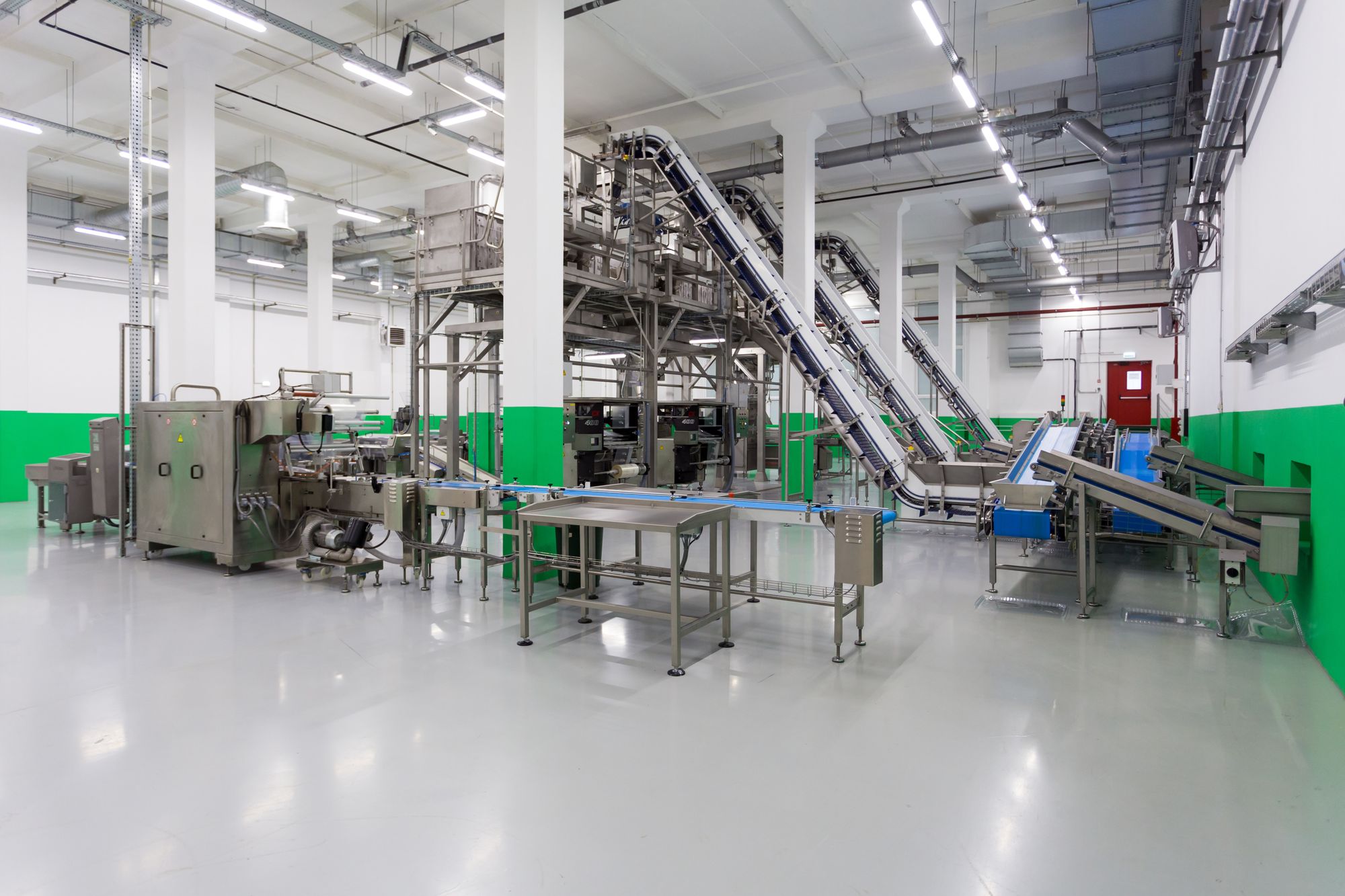
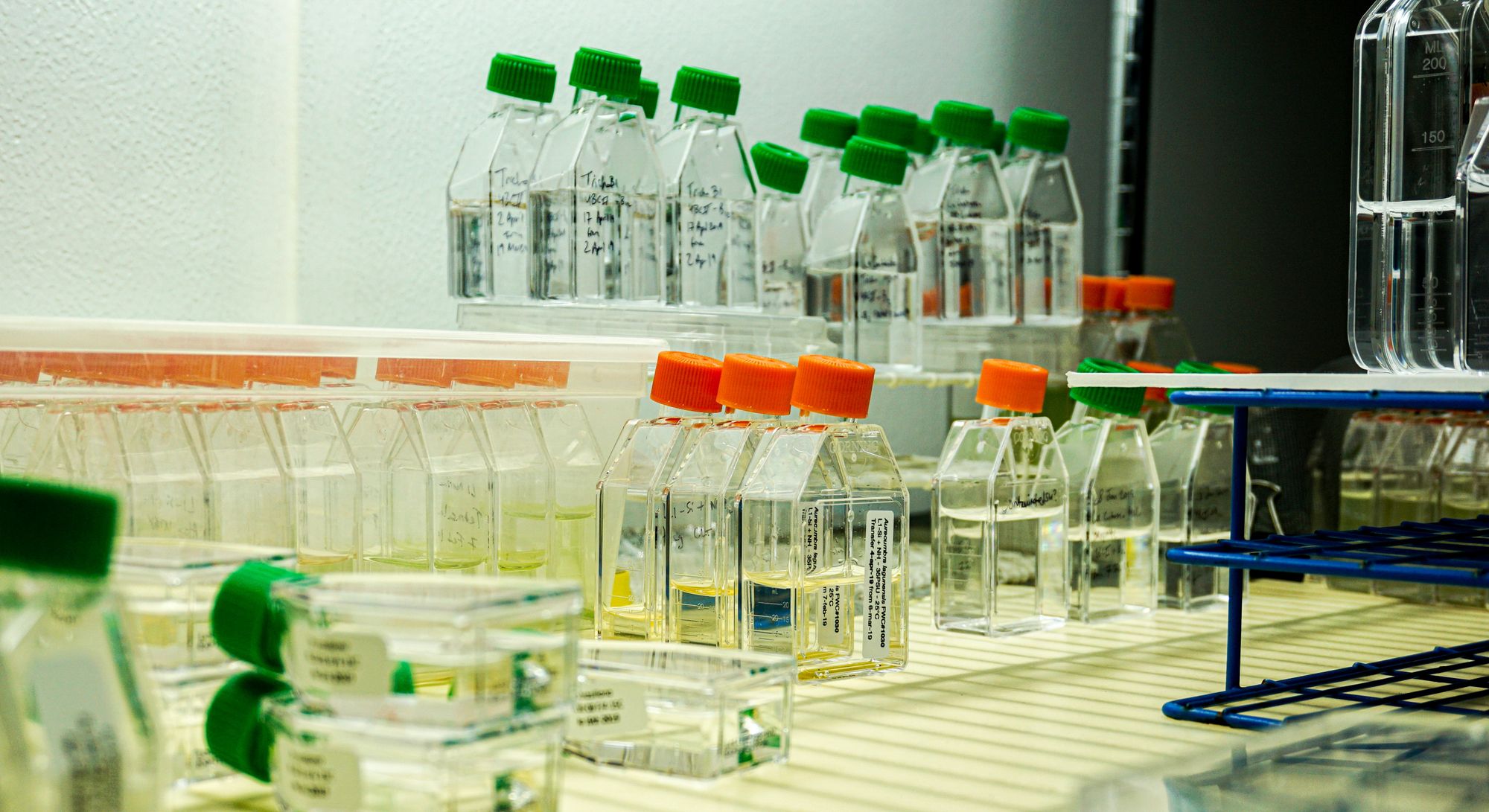
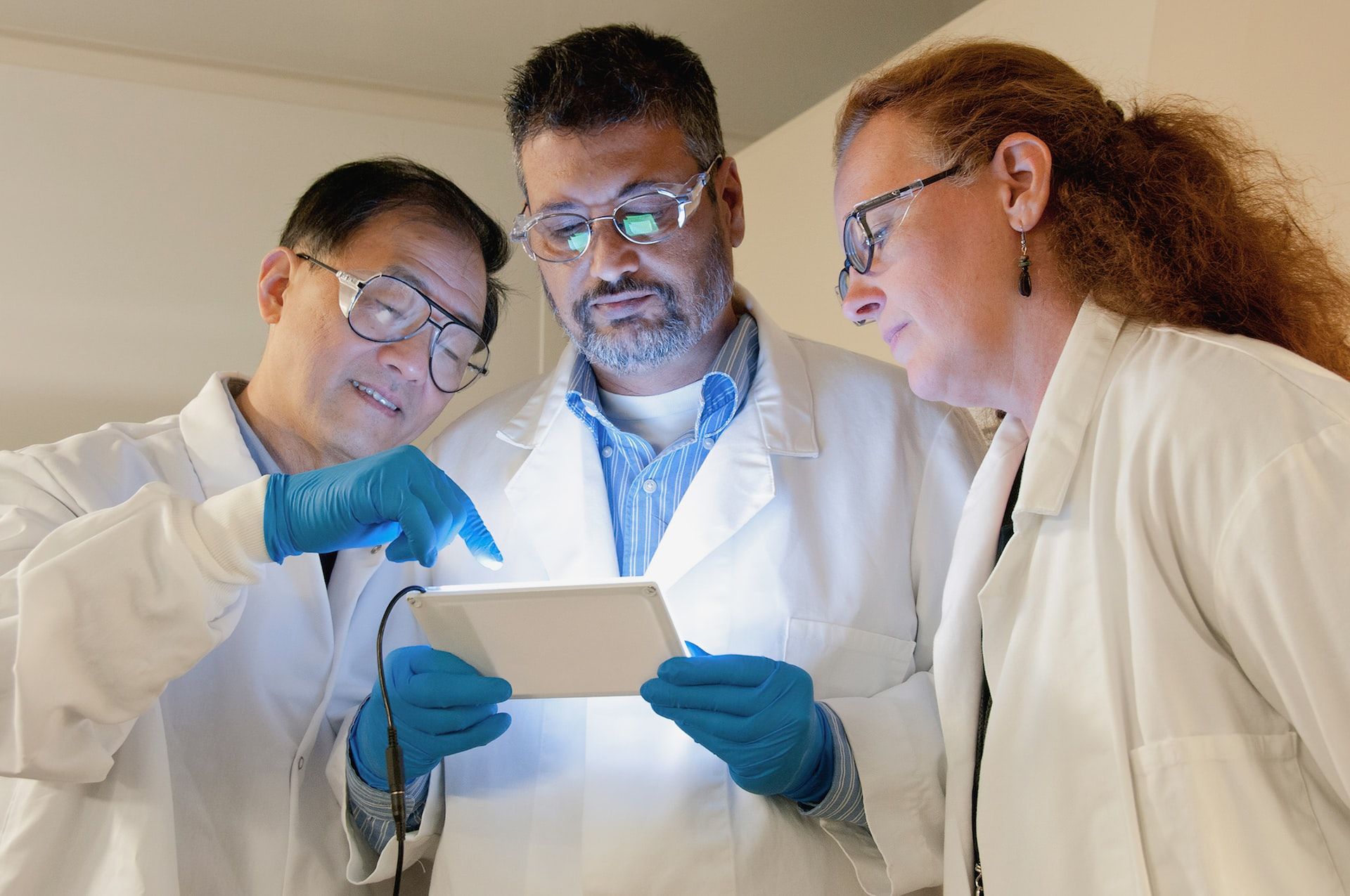