Accurate costing is the cornerstone of successful manufacturing operations, especially when it comes to finished goods. Calculating the true costs of finished products is a complex endeavor that requires meticulous consideration of various components, including direct materials, labor, and overhead expenses.
According to a study conducted by a leading manufacturing research firm, companies that leverage ERP systems for finished goods costing experience a 20% reduction in cost calculation errors. Additionally, research indicates that 78% of manufacturers cite improved decision-making as a result of implementing ERP for costing purposes.
These statistics highlight the significant impact ERP can have on accuracy and efficiency in the realm of finished goods costing, leading to better financial outcomes for manufacturers.
In the past, manufacturers often struggled with manual cost calculations, leading to inaccuracies, inefficiencies, and compromised decision-making. However, with the advent of Enterprise Resource Planning (ERP) systems, companies now have a powerful tool to navigate the intricate landscape of finished goods costing.
ERP systems have revolutionized the manufacturing industry by integrating key business processes and providing real-time visibility into operations. When it comes to costing, ERP plays a crucial role in streamlining the entire process, from tracking and allocating costs to generating insightful reports.
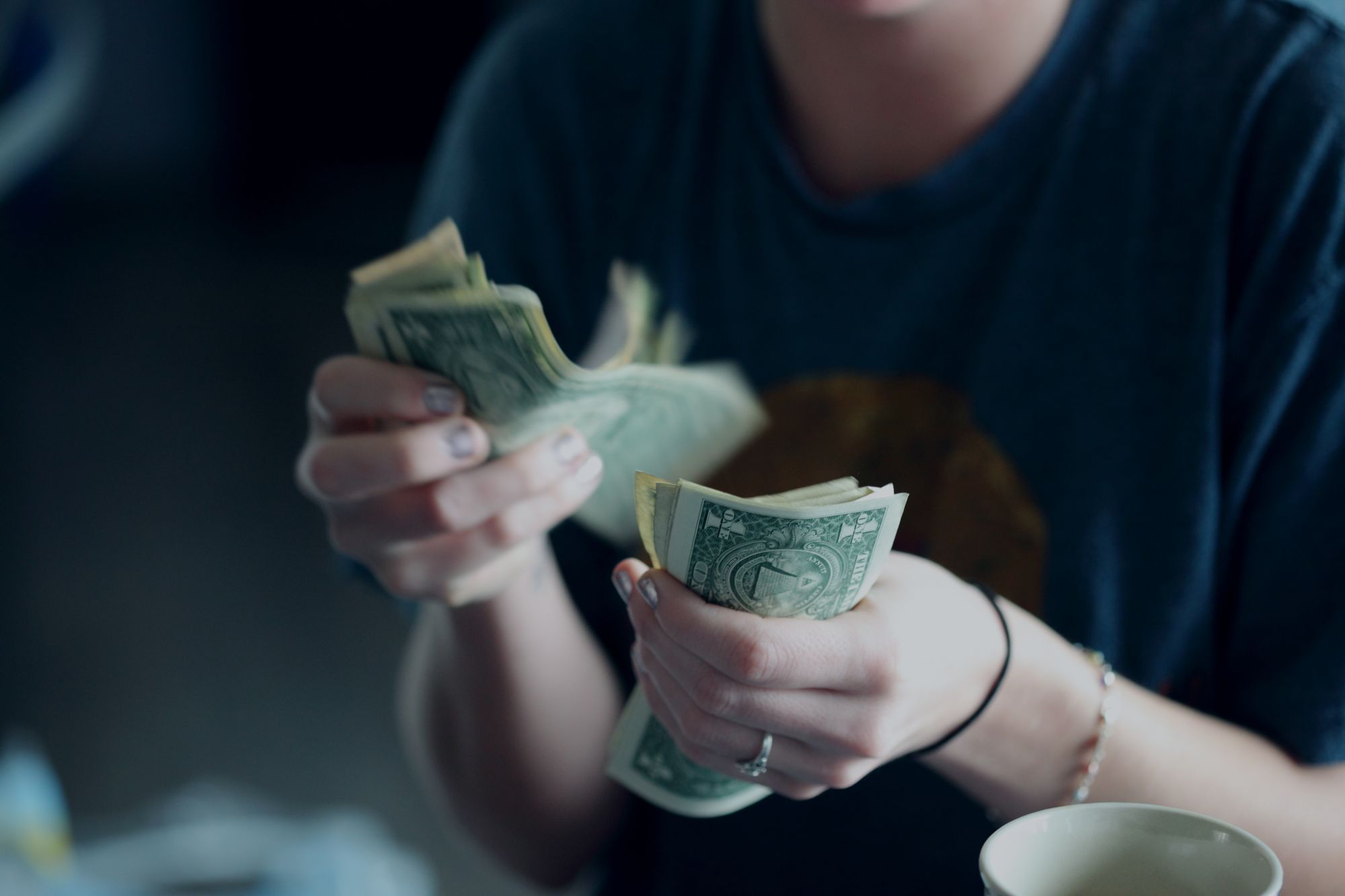
By automating these tasks, ERP systems significantly reduce errors, improve accuracy, and enable manufacturers to make informed decisions based on precise cost data.
In this article, we will delve into the complexities of finished goods costing and explore how ERP systems can effectively address these challenges. We will discuss the role of ERP in costing, implementation strategies, overcoming potential hurdles, best practices, and showcase a real-world case study.
Join us as we unravel the power of ERP in navigating the complexities of finished goods costing and unlock the potential for cost optimization and improved profitability in manufacturing operations.
- Importance of Accurate Costing for Finished Goods in Manufacturing
- The Role of Enterprise Resource Planning (ERP) Systems in Managing and Calculating Costs
- The Complexities Associated with Finished Goods Costing and How ERP Can Help Navigate Them
- Understanding Finished Goods Costing
- The Role of ERP in Finished Goods Costing
- Implementing ERP for Finished Goods Costing
- Overcoming Challenges with ERP in Finished Goods Costing
- Best Practices for Successful Finished Goods Costing with ERP
- Conclusion
- How can Deskera Help You?
- Key Takeaways
- Related Articles
Importance of Accurate Costing for Finished Goods in Manufacturing
Accurate costing plays a vital role in the realm of manufacturing, particularly when it comes to finished goods. It serves as the foundation for effective financial management and decision-making within a company. By precisely determining the costs associated with producing finished products, manufacturers can gain valuable insights into their profit margins, pricing strategies, and overall profitability.
Accurate costing allows manufacturers to understand the true expenses incurred throughout the production process, including direct materials, labor, and overhead costs. It enables them to evaluate the efficiency of their operations, identify areas for cost optimization, and make informed decisions about pricing, inventory management, and resource allocation.
Moreover, accurate costing helps manufacturers maintain competitiveness in the market. By understanding the precise costs of their finished goods, companies can set competitive prices that attract customers while still ensuring profitability. It also allows them to assess the impact of factors such as fluctuations in raw material prices or changes in production processes on the overall cost structure.
The Role Of Enterprise Resource Planning (ERP) Systems In Managing And Calculating Costs
Enterprise Resource Planning (ERP) systems play a pivotal role in managing and calculating costs in manufacturing. These comprehensive software solutions integrate various business functions, such as finance, procurement, inventory, production, and sales, into a centralized system. When it comes to costing, ERP systems offer several key functionalities that streamline and enhance the accuracy of cost management.
One of the primary roles of ERP in managing costs is providing real-time visibility into financial data. By capturing and consolidating data from different departments and processes, ERP systems enable manufacturers to track costs throughout the entire value chain. This visibility allows for better cost control and identification of cost drivers.
ERP systems also facilitate cost allocation by automating the process. With predefined rules and algorithms, these systems accurately allocate costs to finished goods based on factors such as labor hours, material usage, and overhead rates. This automation minimizes manual errors and ensures consistency in cost calculations.
Moreover, ERP systems enable robust cost reporting and analysis. They generate detailed reports and dashboards that provide insights into various cost components, such as direct material costs, labor costs, and overhead expenses. These reports aid in identifying cost variances, analyzing profitability, and making informed decisions regarding pricing, product mix, and cost-saving measures.
Additionally, ERP systems integrate with other essential business functions, such as procurement and inventory management, to optimize costs further. By streamlining procurement processes, managing vendor relationships, and optimizing inventory levels, ERP systems help reduce material costs and eliminate waste.
In summary, ERP systems serve as powerful tools for managing and calculating costs in manufacturing. They provide real-time visibility, automate cost allocation, generate comprehensive reports, and integrate with other business functions to optimize cost management. By leveraging ERP systems, manufacturers can enhance accuracy, efficiency, and decision-making when it comes to managing costs associated with finished goods.
The Complexities Associated With Finished Goods Costing And How Erp Can Help Navigate Them
Finished goods costing poses several complexities for manufacturers, but Enterprise Resource Planning (ERP) systems offer effective solutions to navigate these challenges.
Here are some key complexities associated with finished goods costing and how ERP can help:
Multi-layered Cost Components: Finished goods costs comprise various components, including direct materials, labor, and overhead. Calculating and tracking these components manually can be time-consuming and prone to errors. ERP systems streamline the process by automating cost calculations and integrating data from different departments, ensuring accurate and consistent costing.
Cost Allocation: Allocating costs to finished goods accurately can be challenging, especially when there are multiple products sharing common resources or overhead expenses. ERP systems provide predefined allocation methods and rules, enabling manufacturers to allocate costs based on predetermined factors such as labor hours or machine usage. This ensures fair and accurate cost allocation across different products.
Real-time Cost Updates: Manufacturing operations are dynamic, with cost fluctuations occurring due to factors like changing raw material prices or labor rates. ERP systems provide real-time updates on costs, allowing manufacturers to adapt pricing strategies and make informed decisions promptly. By capturing cost data at each stage of production, ERP systems enable better cost tracking and visibility.
Integration with Other Functions: Finished goods costing is closely tied to other business functions such as procurement, inventory management, and sales. ERP systems integrate these functions, enabling seamless data exchange and providing a holistic view of costs. This integration ensures that cost calculations consider factors like material prices, inventory levels, and customer demand, leading to more accurate costing and improved decision-making.
Complex Manufacturing Processes: Manufacturing processes can be intricate, involving multiple stages, subcontracting, and routing variations. ERP systems offer process mapping and customization capabilities to align with specific manufacturing workflows. This enables manufacturers to capture costs at each process step, handle subcontracting costs, and track costs accurately despite process complexities.
Understanding Finished Goods Costing
Understanding the intricacies of finished goods costing is crucial for manufacturers seeking accurate financial insights and effective decision-making. In this section, we will delve into the concept of finished goods costing, exploring its significance in manufacturing and the factors involved in determining the true costs of finished products.
Definition of finished goods costing and its significance in manufacturing
Finished goods costing refers to the process of calculating and determining the total cost associated with producing a finished product in manufacturing. It encompasses the evaluation of direct material costs, direct labor costs, and overhead costs incurred during the production of the final goods.
The significance of accurate finished goods costing in manufacturing cannot be overstated. It serves as a critical foundation for financial management and decision-making within a company. Here are some key reasons why finished goods costing is essential:
Pricing and Profitability: Accurate costing allows manufacturers to establish competitive pricing strategies while ensuring profitability. Understanding the true costs of finished goods enables companies to set prices that cover expenses and generate desired profit margins, striking a balance between attracting customers and sustaining financial health.
Cost Optimization: Through thorough costing analysis, manufacturers can identify cost drivers and inefficiencies within the production process. This knowledge empowers them to implement cost-saving measures, optimize resource allocation, and improve operational efficiency. By identifying areas for improvement, companies can reduce costs and enhance overall profitability.
Decision-Making: Accurate costing data provides crucial insights for effective decision-making in various aspects of manufacturing. It helps manufacturers evaluate the feasibility of new product lines, assess the impact of changes in production processes, and make informed decisions about inventory management, pricing strategies, and resource allocation.
Performance Evaluation: Finished goods costing plays a vital role in evaluating the performance of different products or product lines. By comparing actual costs with expected costs, manufacturers can identify variances, analyze profitability, and make informed decisions about product mix, investment prioritization, and overall business strategy.
Regulatory Compliance and Financial Reporting: Accurate costing is essential for regulatory compliance and financial reporting requirements. It ensures that manufacturing companies have a clear understanding of their cost structures, enabling them to meet financial reporting standards and fulfill tax obligations accurately.
Factors involved in finished goods costing
Finished goods costing involves considering various factors that contribute to the overall cost of producing a finished product in manufacturing. Here are the key factors typically involved in finished goods costing:
Direct Materials: Direct materials refer to the tangible components that directly become part of the finished product. These include raw materials, components, and any other materials required for production. The cost of direct materials is a significant factor in finished goods costing, as it directly impacts the overall cost of production.
Direct Labor: Direct labor costs encompass the wages or salaries paid to the workers directly involved in the manufacturing process. This includes the labor required for assembling, manufacturing, or producing the finished goods. Tracking and allocating direct labor costs accurately are crucial in determining the total cost of producing finished goods.
Overhead Costs: Overhead costs are the indirect expenses incurred during the production process, which are not directly attributable to specific products or labor. They include expenses such as factory rent, utilities, equipment maintenance, depreciation, and administrative costs. Allocating overhead costs appropriately to finished goods ensures a fair distribution of expenses and provides a comprehensive picture of the total cost.
Indirect Materials: Indirect materials are materials used in the production process but are not directly incorporated into the finished product. These materials support the manufacturing process, such as lubricants, cleaning supplies, or tools. While they do not form part of the finished goods, their costs contribute to the overall cost structure.
Indirect Labor: Indirect labor costs encompass the wages or salaries of employees who support the production process but are not directly involved in manufacturing the finished goods. This includes supervisors, quality control personnel, maintenance staff, and other support roles. Indirect labor costs should be allocated appropriately to accurately reflect the total cost of production.
Other Costs: There may be additional factors specific to each manufacturing process that impact finished goods costing. These can include costs related to equipment or machinery usage, packaging materials, shipping, or any other expenses directly associated with producing the finished goods.
Properly considering and accounting for these factors is essential in accurate finished goods costing. Manufacturers need to track and allocate costs associated with direct materials, direct labor, overhead costs, indirect materials, indirect labor, and other relevant expenses to gain a comprehensive understanding of the true costs of their finished products.
The challenges manufacturers face when calculating accurate costs manually
Manufacturers encounter several challenges when attempting to calculate accurate costs manually. Relying on manual cost calculations can lead to inefficiencies, errors, and a lack of real-time insights. Here are the key challenges faced by manufacturers in manually calculating accurate costs:
Time-Consuming: Manual cost calculations are often time-consuming and labor-intensive. Manufacturers must collect data from various sources, compile it, and perform complex calculations manually. This process can be tedious and prone to errors, especially when dealing with large volumes of data or complex manufacturing processes.
Data Accuracy and Integrity: Manual data entry increases the likelihood of errors, such as transposed numbers or misplaced decimals. Even a small mistake can have significant repercussions on cost calculations, potentially leading to inaccurate costing and misleading financial insights. Maintaining data accuracy and integrity throughout the manual calculation process can be challenging.
Complexity of Cost Components: Cost calculations involve considering multiple cost components, including direct materials, direct labor, and overhead expenses. Manually tracking and allocating costs for each component can be complex, particularly when dealing with factors such as shared resources, variable costs, or complex manufacturing processes. This complexity increases the chances of errors and inconsistencies in cost calculations.
Lack of Real-Time Insights: Manual cost calculations often lack real-time visibility into costs and financial data. This can lead to delays in obtaining accurate cost information and hinder timely decision-making. Manufacturers may rely on outdated cost data, making it challenging to respond swiftly to changing market conditions, pricing strategies, or cost optimization opportunities.
Difficulty in Cost Allocation: Allocating costs accurately to specific products, processes, or departments can be challenging manually, particularly when there are shared resources or complex allocation methodologies. Manufacturers may struggle to determine the appropriate allocation bases and ensure fairness in distributing costs, leading to inaccuracies in cost calculations.
Limited Cost Analysis: Manual cost calculations may provide limited capabilities for in-depth cost analysis and scenario modeling. Manufacturers may find it difficult to perform cost variance analysis, conduct "what-if" analyses, or evaluate the impact of changes in cost drivers. This limitation hampers the ability to identify cost-saving opportunities, optimize operations, and make informed strategic decisions.
The Role of ERP in Finished Goods Costing
In the realm of finished goods costing, Enterprise Resource Planning (ERP) systems play a pivotal role in streamlining and enhancing cost management processes. This section explores the crucial role that ERP systems fulfill in optimizing finished goods costing. By automating calculations, providing real-time visibility, facilitating cost allocation, and enabling comprehensive analysis, ERP systems empower manufacturers to navigate the complexities of cost management, make informed decisions, and drive profitability.
An overview of ERP systems and their purpose in manufacturing
ERP systems, or Enterprise Resource Planning systems, are comprehensive software solutions designed to integrate and manage various aspects of a company's operations. In the context of manufacturing, ERP systems serve a crucial purpose in streamlining and optimizing processes across different functional areas.
The primary purpose of an ERP system in manufacturing is to centralize and automate core business functions such as finance, procurement, inventory management, production planning, sales, and customer relationship management. By consolidating these functions into a unified platform, ERP systems provide a single source of truth and enable seamless data flow and communication between departments.
ERP systems offer a range of features and modules tailored to the specific needs of manufacturing companies. These modules can include production planning and scheduling, material resource planning (MRP), shop floor control, quality management, demand forecasting, and supply chain management.
The key benefits of ERP systems in manufacturing are improved operational efficiency, enhanced decision-making, increased visibility, and better resource utilization. By automating and integrating processes, ERP systems reduce manual errors, streamline workflows, and optimize resource allocation. They provide real-time data and analytics, enabling manufacturers to make informed decisions and respond quickly to market changes.
Furthermore, ERP systems facilitate collaboration and communication within and across departments, enhancing coordination and efficiency. They also support compliance with regulatory requirements and enable accurate financial reporting.
Specific functionalities of ERP related to costing, including cost tracking, allocation, and reporting
ERP systems offer specific functionalities related to costing that are instrumental in accurate cost tracking, allocation, and reporting. Here are the key functionalities:
Cost Tracking: ERP systems provide real-time cost tracking capabilities throughout the production process. By capturing and consolidating data from various sources, such as material purchases, labor hours, and overhead expenses, ERP systems enable manufacturers to monitor costs at each stage of production. This real-time visibility ensures accurate and up-to-date cost information.
Cost Allocation: ERP systems offer advanced functionalities for cost allocation. They provide predefined rules and algorithms for allocating costs to specific products or processes based on various factors such as labor hours, machine usage, or specific allocation bases. This automated allocation ensures fair and accurate distribution of costs and supports more precise cost calculations for finished goods.
Cost Reporting: ERP systems generate comprehensive cost reports and analysis, enabling manufacturers to gain insights into various cost components. These reports provide detailed information on direct material costs, direct labor costs, overhead expenses, and cost variances. With customizable reporting capabilities, manufacturers can analyze costs from different perspectives, identify cost-saving opportunities, and evaluate profitability.
Costing Methods: ERP systems support different costing methods, such as standard costing, actual costing, or activity-based costing. Manufacturers can define and apply the appropriate costing method within the ERP system based on their specific requirements. This flexibility allows for accurate and consistent costing practices aligned with industry standards.
Integration with Other Modules: ERP systems integrate costing functionalities with other modules such as procurement, inventory management, and sales. This integration ensures that cost calculations consider factors like material prices, inventory levels, and customer demand. It facilitates a holistic view of costs, enabling manufacturers to optimize procurement, manage inventory efficiently, and make informed pricing decisions.
Cost Variance Analysis: ERP systems enable cost variance analysis, comparing actual costs with standard or budgeted costs. By identifying variances, manufacturers can investigate the underlying causes, analyze deviations from expected costs, and take corrective actions as necessary. This analysis helps improve cost control, identify inefficiencies, and enhance overall financial performance.
How ERP streamlines the costing process, reducing errors and providing real-time insights
ERP systems streamline the costing process in manufacturing by automating manual tasks, reducing errors, and providing real-time insights.
Here's how ERP streamlines the costing process:
Automated Data Integration: ERP systems integrate data from various departments and sources, such as procurement, production, and inventory. Instead of manually collecting and entering data, ERP systems automatically capture and consolidate relevant cost-related information. This automation eliminates the need for manual data entry, reducing errors and ensuring data consistency.
Real-Time Data Capture: ERP systems capture cost-related data in real-time as transactions occur throughout the production process. Whether it's material purchases, labor hours, or overhead expenses, the system records and updates the cost data instantly. This real-time data capture provides accurate and up-to-date cost information, enabling manufacturers to make timely decisions and respond quickly to changes.
Centralized Database: ERP systems store all cost-related data in a centralized database, accessible to authorized users across the organization. This centralization ensures data integrity and eliminates the need for multiple spreadsheets or disparate systems. Users can access the latest cost information from a single source, reducing data duplication and inconsistencies.
Automated Cost Calculations: ERP systems automate cost calculations based on predefined formulas and rules. By incorporating direct material costs, direct labor costs, and overhead expenses, ERP systems accurately calculate the total cost of producing finished goods. This automation eliminates manual calculations, reducing the risk of errors and ensuring consistency in cost calculations.
Cost Allocation and Tracking: ERP systems provide robust functionalities for cost allocation. They allocate costs to specific products, processes, or departments based on predefined allocation rules and methodologies. Manufacturers can track costs throughout the production process, monitor cost variances, and have granular visibility into cost breakdowns at different levels.
Real-Time Insights and Reporting: With ERP systems, manufacturers have real-time insights into cost-related data. The system generates comprehensive reports and dashboards that provide detailed cost analysis, cost variances, and profitability insights. Manufacturers can access these reports instantly, enabling informed decision-making based on accurate and up-to-date cost information.
Workflow Automation: ERP systems automate workflows related to costing processes, such as approvals, cost adjustments, or budget updates. This automation streamlines the process, reduces manual intervention, and ensures consistent and auditable cost management practices.
Implementing ERP for Finished Goods Costing
Key steps involved in implementing an ERP system for finished goods costing
Implementing an ERP system for finished goods costing involves a systematic approach to ensure a successful integration of the software into the manufacturing process. Here are the key steps involved in implementing ERP for finished goods costing:
Needs Assessment: Begin by conducting a thorough needs assessment to understand the specific requirements and challenges related to finished goods costing in your manufacturing organization. Identify pain points, desired functionalities, and goals to be achieved with the ERP implementation.
Vendor Selection: Research and evaluate ERP vendors that specialize in manufacturing and offer robust costing capabilities. Consider factors such as the vendor's industry experience, system functionality, scalability, implementation support, and pricing. Request demonstrations and gather feedback from reference clients to make an informed decision.
Project Planning: Develop a comprehensive project plan that outlines the timeline, resources, and milestones for the ERP implementation. Define roles and responsibilities, establish communication channels, and allocate necessary resources for the project. Consider engaging an experienced project manager to oversee the implementation process.
Data Preparation and Migration: Prepare and clean existing data for migration to the ERP system. Identify data sources, extract relevant information, and ensure data accuracy and integrity. Develop a migration strategy and execute the data transfer process, keeping in mind the requirements of finished goods costing.
Configuration and Customization: Work closely with the ERP vendor to configure and customize the system according to your organization's specific costing requirements. This includes setting up cost elements, allocation methods, cost centers, and cost calculation formulas within the ERP system. Align the system with your organization's costing practices and industry standards.
User Training: Provide comprehensive training to users who will be using the ERP system for finished goods costing. Train employees on the system's functionalities, data input procedures, cost tracking, allocation processes, and reporting capabilities. Conduct hands-on workshops and offer ongoing support to ensure users are proficient in utilizing the system effectively.
Testing and Quality Assurance: Conduct rigorous testing to ensure the ERP system performs as expected. Test various scenarios, data inputs, cost calculations, and reporting functionalities to validate accuracy and reliability. Address any identified issues or discrepancies, and ensure the system meets the defined requirements.
Go-Live and Continuous Improvement: Once testing is complete, launch the ERP system for finished goods costing in a controlled manner. Monitor the system's performance, gather feedback from users, and address any post-implementation issues promptly. Continuously evaluate and improve processes, leveraging the capabilities of the ERP system to enhance cost management practices.
Ongoing Support and Maintenance: Establish a support mechanism to address user queries, system issues, and provide ongoing maintenance and updates. Regularly review and optimize the system's performance, incorporating feedback and making necessary adjustments to maximize the benefits of the ERP system for finished goods costing.
Importance of data integration and accuracy when setting up ERP for cost calculations
Data integration and accuracy play a crucial role when setting up an ERP system for cost calculations in a manufacturing organization. These factors are of utmost importance for ensuring the reliability and effectiveness of the costing process.
Data integration is essential because it allows for the consolidation of relevant cost data from different departments and sources into a centralized ERP system. This integration enables a comprehensive view of costs throughout the manufacturing process.
By integrating data from procurement, production, labor, and overheads, manufacturers gain a holistic understanding of the various components that contribute to the overall cost of finished goods. This comprehensive visibility is vital for accurate cost calculations and better decision-making.
Accurate data is the foundation of reliable cost calculations. When setting up an ERP system, it is crucial to ensure that the data being integrated is accurate, complete, and consistent. Inaccuracies or errors in the data can have a cascading effect on cost calculations, leading to incorrect financial reports and misguided decision-making.
By ensuring data accuracy, manufacturers can have confidence in the cost calculations performed by the ERP system, allowing them to make informed decisions based on reliable cost data.
Timely decision-making is another key aspect influenced by data integration and accuracy. With accurate and up-to-date cost data integrated into the ERP system, manufacturers can quickly assess the profitability of products, identify cost-saving opportunities, and make informed decisions to optimize resources and improve overall financial performance.
Timely access to accurate cost information enables manufacturers to respond swiftly to market changes, adjust pricing strategies, and identify areas for cost reduction or process improvement.
Effective cost control relies on accurate and integrated data. When cost data is accurate and integrated within the ERP system, manufacturers can track costs at various stages of production, identify cost variances, and take corrective actions promptly. This level of cost control helps in identifying inefficiencies or areas where costs can be reduced.
Furthermore, accurate data integration is essential for reliable reporting capabilities within the ERP system. By integrating accurate cost data, manufacturers can generate comprehensive cost reports, cost breakdowns, and cost variance analysis.
These reports provide valuable insights into cost trends, cost drivers, and help in identifying areas for improvement. Reliable reporting enables manufacturers to evaluate cost-saving initiatives, monitor performance against budgeted costs, and make data-driven decisions to optimize costs.
Lastly, data integration and accuracy ensure seamless integration and data flow between the ERP system and other enterprise systems, such as inventory management, procurement, and financial systems. When data is accurately integrated, it eliminates manual data entry, reduces errors, and ensures data consistency across different systems. This seamless integration enables efficient data exchange and improves overall operational efficiency.
In summary, data integration and accuracy are vital when setting up an ERP system for cost calculations in manufacturing. They provide comprehensive cost visibility, accurate cost calculations, timely decision-making, effective cost control, reliable reporting, and seamless system integration. By prioritizing data integrity during the setup phase, manufacturers can leverage the full potential of the ERP system and achieve accurate and meaningful cost calculations for improved financial management.
Exploring the customization options available in ERP systems to align with specific manufacturing processes and costing methodologies
ERP systems offer a range of customization options that allow manufacturers to align the software with their specific manufacturing processes and costing methodologies. These customization options ensure that the ERP system caters to the unique requirements of each organization.
Here are some key customization options available in ERP systems for manufacturing:
Cost Element Configuration: ERP systems allow customization of cost elements to reflect the specific components that contribute to the cost of finished goods. Manufacturers can define and configure cost elements such as direct materials, direct labor, and overhead costs based on their costing methodologies. This customization ensures that the cost elements accurately represent the cost structure of the organization.
Cost Allocation Methods: ERP systems provide flexibility in defining cost allocation methods. Manufacturers can customize the system to allocate costs based on specific criteria such as labor hours, machine usage, production volume, or any other relevant factors. This customization allows for accurate and consistent allocation of costs to products or cost centers.
Cost Center Setup: ERP systems allow customization of cost centers to align with the organization's structure and manufacturing processes. Manufacturers can define cost centers based on departments, production lines, or any other relevant divisions within the organization. This customization enables better tracking and analysis of costs at the desired level of granularity.
Cost Calculation Formulas: ERP systems offer customization options for defining cost calculation formulas. Manufacturers can set up formulas that consider different cost drivers and variables specific to their manufacturing processes. This customization allows for accurate calculation of costs based on the organization's unique cost allocation and calculation methodologies.
Reporting and Analytics: ERP systems provide customization options for reporting and analytics capabilities. Manufacturers can tailor reports to display the desired cost metrics, performance indicators, and other relevant information based on their specific requirements. Customized reports help in gaining insights into cost trends, variances, and performance against targets, enabling better decision-making.
Workflow and Approval Processes: ERP systems allow customization of workflow and approval processes related to costing. Manufacturers can define customized workflows to ensure that cost-related transactions and approvals follow the organization's specific processes and hierarchies. This customization helps in maintaining control over cost-related activities and ensures compliance with internal policies and procedures.
Integration with Third-Party Systems: ERP systems can be customized to integrate with other third-party systems such as inventory management, supply chain management, or business intelligence tools. This customization enables seamless data exchange and provides a unified view of information across different systems, enhancing overall operational efficiency and decision-making.
It is important to note that customization should be approached with caution to avoid excessive complexity and potential challenges in system maintenance and upgrades. Organizations should carefully assess their customization needs, considering the balance between customization and standard system functionality.
Overcoming Challenges with ERP in Finished Goods Costing
Implementing an ERP system for finished goods costing brings numerous benefits, but it is not without its challenges. In this section, we will explore the common obstacles manufacturers may face when utilizing ERP for finished goods costing and discuss effective strategies to overcome them. By understanding these challenges and implementing appropriate solutions, organizations can maximize the potential of their ERP system, streamline cost calculations, and gain accurate insights into their manufacturing costs.
Identifying potential challenges or limitations in utilizing ERP for finished goods costing
Utilizing an ERP system for finished goods costing can bring significant advantages, but it is important to be aware of potential challenges or limitations that organizations may face. Here are some common challenges that can arise when using ERP for finished goods costing:
Complex Implementation: Implementing an ERP system for finished goods costing can be a complex process. It requires thorough planning, data migration, system configuration, and user training. Organizations may encounter challenges in aligning the ERP system with their unique costing methodologies, integrating data from various sources, and ensuring data accuracy during the implementation phase.
Data Accuracy and Integration: Accurate and integrated data is crucial for reliable cost calculations. However, organizations may face challenges in ensuring data accuracy, consistency, and completeness. Integrating data from multiple departments, systems, and sources can be a complex task, and discrepancies in data can lead to inaccurate cost calculations and unreliable financial reports.
Customization and Flexibility: While ERP systems offer customization options, there may be limitations in terms of the level of customization required by specific costing methodologies or unique business processes. Organizations may find that the ERP system does not fully align with their desired cost allocation methods, cost element structures, or reporting requirements. Limited flexibility can pose challenges in adapting the ERP system to meet specific needs.
User Adoption and Training: ERP systems require users to input data accurately, follow defined costing processes, and utilize the system effectively. However, organizations may face challenges in user adoption and training. Employees may be resistant to change, find the system complex to navigate, or lack sufficient training to utilize the ERP system for finished goods costing optimally. Insufficient user adoption can hinder the accuracy and effectiveness of cost calculations.
Integration with External Systems: Manufacturers often need to integrate the ERP system with other external systems such as suppliers' systems, customer relationship management (CRM) systems, or e-commerce platforms. Challenges can arise in ensuring seamless data exchange, maintaining data integrity, and synchronizing information across different systems. Incomplete integration can result in discrepancies between cost data in the ERP system and other systems.
Ongoing Maintenance and Support: ERP systems require ongoing maintenance, updates, and technical support. Organizations may encounter challenges in ensuring system stability, addressing software bugs, and keeping up with evolving technology. Lack of ongoing maintenance and support can affect the performance and reliability of the ERP system for finished goods costing.
While these challenges exist, organizations can overcome them by adopting effective strategies. These include conducting thorough data analysis and cleansing, involving key stakeholders during the implementation process, providing comprehensive user training, leveraging available customization options to align the ERP system with specific costing methodologies, and establishing regular maintenance and support processes.
Strategies to overcome these challenges, such as data validation, user training, and continuous system monitoring
To overcome the challenges associated with utilizing ERP for finished goods costing, organizations can implement several strategies. Here are some effective approaches:
Data Validation and Cleansing: Conduct a thorough analysis of the data to identify inconsistencies, inaccuracies, and gaps. Implement data validation processes to ensure data accuracy and integrity. Regularly cleanse and update the data to maintain its quality. Establish data validation checks and procedures to catch errors early on and ensure reliable cost calculations.
User Training and Education: Provide comprehensive user training to employees who will be using the ERP system for finished goods costing. Train them on system functionalities, data input requirements, and cost calculation processes. Encourage user adoption by emphasizing the benefits of accurate cost calculations and providing ongoing support and resources for continuous learning.
Change Management and Stakeholder Engagement: Involve key stakeholders from various departments in the implementation process. Engage them in defining costing methodologies, configuring the ERP system, and aligning it with business processes. Implement change management strategies to address resistance and ensure smooth adoption of the ERP system. Regular communication and collaboration with stakeholders can help overcome challenges and drive successful implementation.
Customization and System Configuration: Leverage the customization options available in the ERP system to align it with specific costing methodologies. Configure the system to accommodate unique cost allocation methods, cost element structures, and reporting requirements. Work closely with ERP vendors or consultants to optimize the system's configuration and ensure it meets the organization's specific needs.
Continuous System Monitoring and Maintenance: Implement regular system monitoring and maintenance practices to ensure system stability and performance. Establish processes for bug tracking, system updates, and patches. Conduct periodic system audits to identify any issues or areas for improvement. Maintain a dedicated support team or engage with the ERP vendor to provide ongoing technical assistance and address any system-related challenges promptly.
Integration and Data Exchange: Pay attention to the integration points between the ERP system and other external systems. Establish robust integration processes and data exchange protocols to ensure seamless information flow. Test and validate data integrity during integration to avoid discrepancies between the ERP system and external systems. Regularly monitor and reconcile data between systems to maintain accuracy and consistency.
Continuous Improvement and Optimization: Treat the implementation of ERP for finished goods costing as an iterative process. Continuously review and evaluate the system's performance, cost calculation accuracy, and user feedback. Identify areas for improvement and optimization, and implement necessary changes to enhance the system's effectiveness over time. Encourage feedback from users and leverage their insights to drive continuous improvement.
Benefits of using ERP for cost calculations, such as improved accuracy, efficiency, and decision-making
Utilizing an ERP system for cost calculations in manufacturing brings a wide range of benefits that contribute to improved accuracy, efficiency, and decision-making. Here are some key advantages:
Enhanced Cost Accuracy: ERP systems provide robust functionality for capturing and analyzing cost data at various stages of the manufacturing process. By integrating data from multiple sources, such as procurement, production, labor, and overheads, ERP systems enable more accurate cost calculations. This accuracy helps organizations gain a precise understanding of the cost components associated with finished goods, leading to more reliable financial reporting and cost analysis.
Streamlined Cost Calculation Process: ERP systems automate and streamline the cost calculation process, eliminating manual and error-prone methods. With predefined cost allocation methods, cost centers, and calculation formulas, ERP systems can efficiently allocate and calculate costs based on defined parameters. This automation reduces the time and effort required for cost calculations and ensures consistency and standardization across the organization.
Real-time Cost Visibility: ERP systems provide real-time visibility into cost data, allowing manufacturers to access up-to-date information on costs associated with finished goods. This real-time visibility enables timely decision-making and the ability to respond quickly to cost-related issues or market changes. Organizations can monitor costs, track cost variances, and identify cost-saving opportunities more effectively, leading to improved cost control and profitability.
Improved Decision-Making: ERP systems offer comprehensive reporting and analytics capabilities, enabling organizations to generate meaningful insights into their manufacturing costs. With accurate and reliable cost data available through the ERP system, decision-makers can make informed choices about pricing strategies, product profitability, resource allocation, and cost-saving initiatives. This data-driven decision-making leads to more effective utilization of resources and improved overall financial performance.
Integration and Data Consistency: ERP systems integrate data from various departments and systems, ensuring data consistency and eliminating the need for manual data entry or reconciliation. This integration eliminates data silos and provides a unified view of cost information. The availability of consistent and integrated data across the organization enhances collaboration, enables better coordination between departments, and facilitates a more accurate analysis of costs at different levels, such as product, project, or customer.
Efficient Resource Management: ERP systems help optimize resource management by providing insights into resource utilization, labor costs, and production efficiencies. Manufacturers can identify bottlenecks, inefficiencies, or areas for improvement in the production process, leading to enhanced resource utilization and cost optimization. By tracking and analyzing resource-related costs, ERP systems assist in making informed decisions to optimize resource allocation and improve overall operational efficiency.
Compliance and Audit Readiness: ERP systems provide a structured and auditable framework for cost calculations and financial reporting. With predefined cost allocation methods, standardized processes, and accurate data, organizations can ensure compliance with regulatory requirements and financial standards. The transparency and traceability of cost data within the ERP system facilitate audits and ensure readiness for financial inspections.
Best Practices for Successful Finished Goods Costing with ERP
To ensure successful finished goods costing with ERP, it is essential for organizations to follow best practices that optimize the use of the system and maximize its benefits. In this section, we will explore key best practices that can help organizations effectively leverage ERP for cost calculations, streamline processes, enhance accuracy, and make informed decisions.
Best practices to optimize finished goods costing using ERP systems
Optimizing finished goods costing using ERP systems requires implementing a set of best practices that enhance accuracy, efficiency, and decision-making. Here are some key practices to consider:
Define Clear Costing Methodologies: Establish clear and consistent costing methodologies within the ERP system. Define cost elements, cost allocation methods, and calculation formulas that align with your organization's specific requirements. This clarity ensures accurate cost calculations and facilitates meaningful analysis of cost data.
Ensure Data Accuracy and Integration: Maintain high-quality data by regularly validating, cleansing, and integrating data from various sources. Establish data governance practices to ensure data accuracy, consistency, and completeness. Implement data integration mechanisms to synchronize data between ERP modules and external systems, ensuring a holistic view of cost-related information.
Regularly Monitor and Review Cost Data: Continuously monitor cost data within the ERP system to identify any discrepancies, outliers, or inconsistencies. Conduct periodic cost reviews to validate cost calculations, track cost trends, and identify opportunities for improvement. Regularly reconcile cost data with financial records to ensure accuracy and reliability.
Leverage Customization for Cost Visibility: Customize ERP dashboards and reports to provide relevant and actionable cost information to different stakeholders. Tailor reports to display key cost metrics, variances, and performance indicators that align with specific user roles and responsibilities. This customization enhances cost visibility and facilitates informed decision-making.
Implement Strong Internal Controls: Establish robust internal controls within the ERP system to ensure data integrity, prevent unauthorized access, and mitigate the risk of errors or fraud. Define user access permissions based on job roles and responsibilities. Implement approval workflows and segregation of duties to maintain control over cost-related transactions and processes.
Provide Ongoing User Training and Support: Continuously invest in user training and provide ongoing support to employees using the ERP system for cost calculations. Ensure users are proficient in utilizing the system's cost calculation functionalities, entering accurate data, and interpreting cost reports. Encourage user feedback and address any usability issues or challenges promptly.
Foster Collaboration and Communication: Promote cross-functional collaboration and communication between departments involved in cost calculations. Establish regular meetings or forums to discuss cost-related topics, share insights, and align on cost management strategies. Encourage collaboration between finance, operations, and procurement teams to ensure accurate and up-to-date cost data.
Stay Up-to-Date with System Upgrades: Keep the ERP system up-to-date by regularly applying system upgrades, patches, and enhancements provided by the ERP vendor. Stay informed about new features or functionalities that can improve cost calculation processes or enhance data analysis capabilities. Engage with the ERP vendor or consultants to leverage their expertise and guidance for system optimization.
Continuously Improve and Adapt: Foster a culture of continuous improvement by regularly evaluating and optimizing the finished goods costing processes within the ERP system. Seek feedback from users, identify areas for enhancement, and implement changes to streamline workflows, automate repetitive tasks, and improve the accuracy and efficiency of cost calculations.
Importance of standardized processes, data integrity, and regular system maintenance
Standardized processes, data integrity, and regular system maintenance are vital components for successful finished goods costing with ERP systems. Let's explore the importance of each of these elements:
Standardized Processes: Standardized processes ensure consistency and uniformity in cost calculations across the organization. By establishing clear and defined methodologies for cost allocation, data entry, and reporting, organizations can minimize errors and discrepancies in cost calculations. Standardized processes also facilitate better comparability and analysis of cost data, enabling effective decision-making and accurate financial reporting.
Data Integrity: Data integrity is crucial for reliable cost calculations. Accurate and reliable data ensures the integrity of cost information within the ERP system. It eliminates inconsistencies, inaccuracies, and duplications that can distort cost calculations and compromise the validity of financial reports. Maintaining data integrity involves implementing data validation checks, ensuring data accuracy during data entry, and regularly reviewing and cleansing data to address any discrepancies or anomalies.
Regular System Maintenance: Regular system maintenance is essential to keep the ERP system running smoothly and effectively. It involves activities such as applying system updates, bug fixes, and security patches provided by the ERP vendor. By keeping the system up-to-date, organizations can benefit from improved system performance, enhanced security, and access to new features or functionalities that can enhance cost calculations and data analysis.
Regular system maintenance also includes periodic system audits, performance optimization, and addressing any technical issues or system errors promptly. This proactive approach ensures the stability, reliability, and efficiency of the ERP system, minimizing downtime and disruptions in cost calculations.
Standardized processes, data integrity, and regular system maintenance work together to create a robust foundation for accurate and reliable finished goods costing. They provide organizations with the confidence that cost calculations are based on consistent methodologies, accurate data, and a well-maintained system. This foundation enables organizations to make informed decisions, effectively manage costs, and maintain financial transparency. Moreover, it enhances the trust in the cost information generated by the ERP system, both internally and externally, which is crucial for compliance, audits, and stakeholder confidence.
By prioritizing standardized processes, data integrity, and regular system maintenance, organizations can maximize the benefits of their ERP system for finished goods costing. They can achieve greater accuracy in cost calculations, improve cost management practices, and make informed decisions based on reliable cost information.
Tips for leveraging ERP reporting capabilities to gain insights into cost variances, profitability, and pricing decisions
Leveraging ERP reporting capabilities is crucial for gaining insights into cost variances, profitability, and pricing decisions. Here are some tips to effectively utilize ERP reporting functionalities for these purposes:
Cost Variance Analysis: Utilize ERP reports to analyze cost variances between planned and actual costs. Compare budgeted costs with actual costs at various stages of the production process. Identify the key cost drivers and investigate significant deviations from expected costs. This analysis helps identify areas of cost overruns or savings, enabling organizations to take corrective actions and improve cost control.
Profitability Analysis: Leverage ERP reports to analyze the profitability of finished goods. Generate profitability reports that provide a comprehensive view of costs, revenues, and margins associated with different products, product lines, or customer segments. Identify the most profitable products or customer segments and analyze the factors contributing to profitability. This analysis helps optimize pricing strategies, product mix, and resource allocation for maximizing overall profitability.
Pricing Decisions: Utilize ERP reports to evaluate the impact of pricing decisions on profitability. Analyze the relationship between pricing, costs, and sales volumes to identify the optimal pricing strategies. Generate pricing sensitivity analysis reports to understand how changes in pricing affect revenue, margin, and market competitiveness. Leverage historical sales and cost data to simulate different pricing scenarios and assess their impact on profitability.
Drill-Down Capabilities: Take advantage of the drill-down capabilities of ERP reports to gain deeper insights into cost variances, profitability, and pricing decisions. Drill down from summary-level reports to detailed transaction-level data to investigate the underlying causes of cost fluctuations. Analyze cost components, such as material costs, labor costs, and overheads, to identify specific areas for improvement or cost-saving opportunities.
Comparative Analysis: Utilize comparative reports to benchmark costs and profitability across different time periods, product lines, or business units. Compare cost trends, variances, and profitability metrics to identify areas of improvement or areas where costs are out of line with industry benchmarks. This analysis helps identify areas for cost optimization and supports data-driven decision-making.
Visualization and Dashboarding: Leverage ERP reporting tools to create visual dashboards and interactive reports for cost variance analysis, profitability analysis, and pricing decisions. Visual representations, such as charts, graphs, and heatmaps, provide a quick and intuitive understanding of cost patterns, trends, and outliers. Interactive dashboards allow users to dynamically explore data, filter information, and drill down into specific areas of interest.
Scheduled and Automated Reporting: Set up scheduled and automated reports within the ERP system to ensure timely and consistent access to cost variance, profitability, and pricing information. Establish a reporting cadence that aligns with decision-making cycles and provides stakeholders with up-to-date insights. Automating report generation and distribution saves time and ensures that decision-makers have access to relevant information when needed.
Conclusion
Implementing an ERP system for finished goods costing provides significant benefits for organizations. It streamlines and automates the cost calculation process, improves accuracy, enhances decision-making, and enables real-time visibility into cost data. By leveraging ERP's functionalities, such as cost tracking, allocation, and reporting, organizations can gain valuable insights into cost variances, profitability, and pricing decisions.
Standardizing processes, ensuring data integrity, and conducting regular system maintenance are crucial for maximizing the effectiveness of ERP systems in finished goods costing. By following best practices and overcoming potential challenges, organizations can optimize cost calculations, improve efficiency, and make informed decisions based on reliable cost information.
In conclusion, ERP systems play a pivotal role in navigating the complexities of finished goods costing. By embracing ERP, organizations can optimize their cost calculations, gain valuable insights, and stay competitive in an increasingly complex manufacturing landscape. The integration of ERP systems enables organizations to effectively manage costs, improve decision-making, and drive sustainable growth in the ever-evolving manufacturing industry.
How can Deskera Help You?
Deskera ERP and MRP systems help you to keep your business units organized. The system's primary functions are as follows:
- Keep track of your raw materials and final items inventories
- Control production schedules and routings
- Keep a bill of materials
- Produce thorough reports
- Make your own dashboards
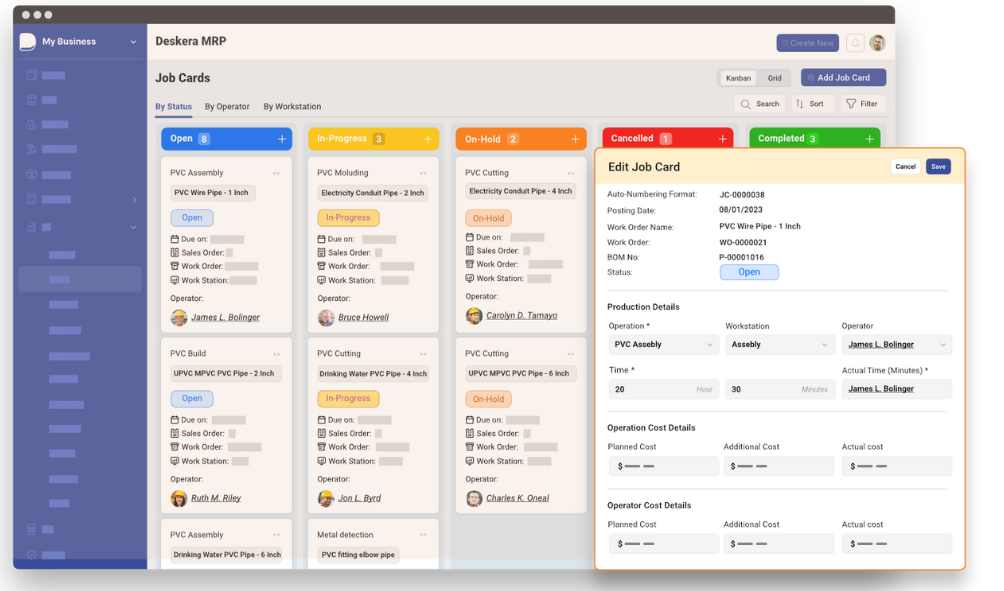
Deskera's integrated financial planning tools enable investors to better plan and track their investments. It can assist investors in making faster and more accurate decisions.
Deskera Books allows you to better manage your accounts and finances. Maintain good accounting practices by automating tasks like billing, invoicing, and payment processing.
Deskera CRM is a powerful solution that manages your sales and helps you close deals quickly. It not only enables you to perform critical tasks like lead generation via email, but it also gives you a comprehensive view of your sales funnel.
Deskera People is a straightforward tool for centralizing your human resource management functions.
Key Takeaways
- Finished goods costing is crucial in manufacturing as it enables organizations to accurately determine the cost of their products and make informed pricing and profitability decisions.
- Enterprise Resource Planning (ERP) systems play a significant role in managing and calculating costs in the manufacturing industry. They offer robust functionalities for cost tracking, allocation, reporting, and analysis.
- Factors involved in finished goods costing include direct materials, direct labor, and overhead costs. ERP systems provide the tools to efficiently track and allocate these costs, ensuring accuracy and consistency.
- Manual cost calculations pose challenges such as errors, time-consuming processes, and lack of real-time visibility. Implementing ERP systems automates the costing process, reduces errors, and provides real-time insights into cost data.
- ERP systems streamline the costing process by automating calculations, consolidating data, and providing standardized processes. This improves efficiency, accuracy, and overall cost management.
- Implementing ERP for finished goods costing involves selecting the right system, customizing it to align with specific manufacturing processes, and integrating and migrating data from various sources.
- Data integration and accuracy are crucial when setting up ERP for cost calculations. Organizations must ensure that data from different sources is properly integrated, validated, and cleansed to maintain data integrity.
- Customization options in ERP systems allow organizations to align the system with their specific manufacturing processes and costing methodologies. This ensures accurate and relevant cost calculations.
- Challenges in utilizing ERP for finished goods costing can be overcome through data validation, user training, continuous system monitoring, and promptly addressing technical issues.
- Leveraging ERP reporting capabilities provides valuable insights into cost variances, profitability, and pricing decisions. It allows for cost variance analysis, profitability analysis, drill-down capabilities, comparative analysis, and visualization through dashboards.
Related Articles
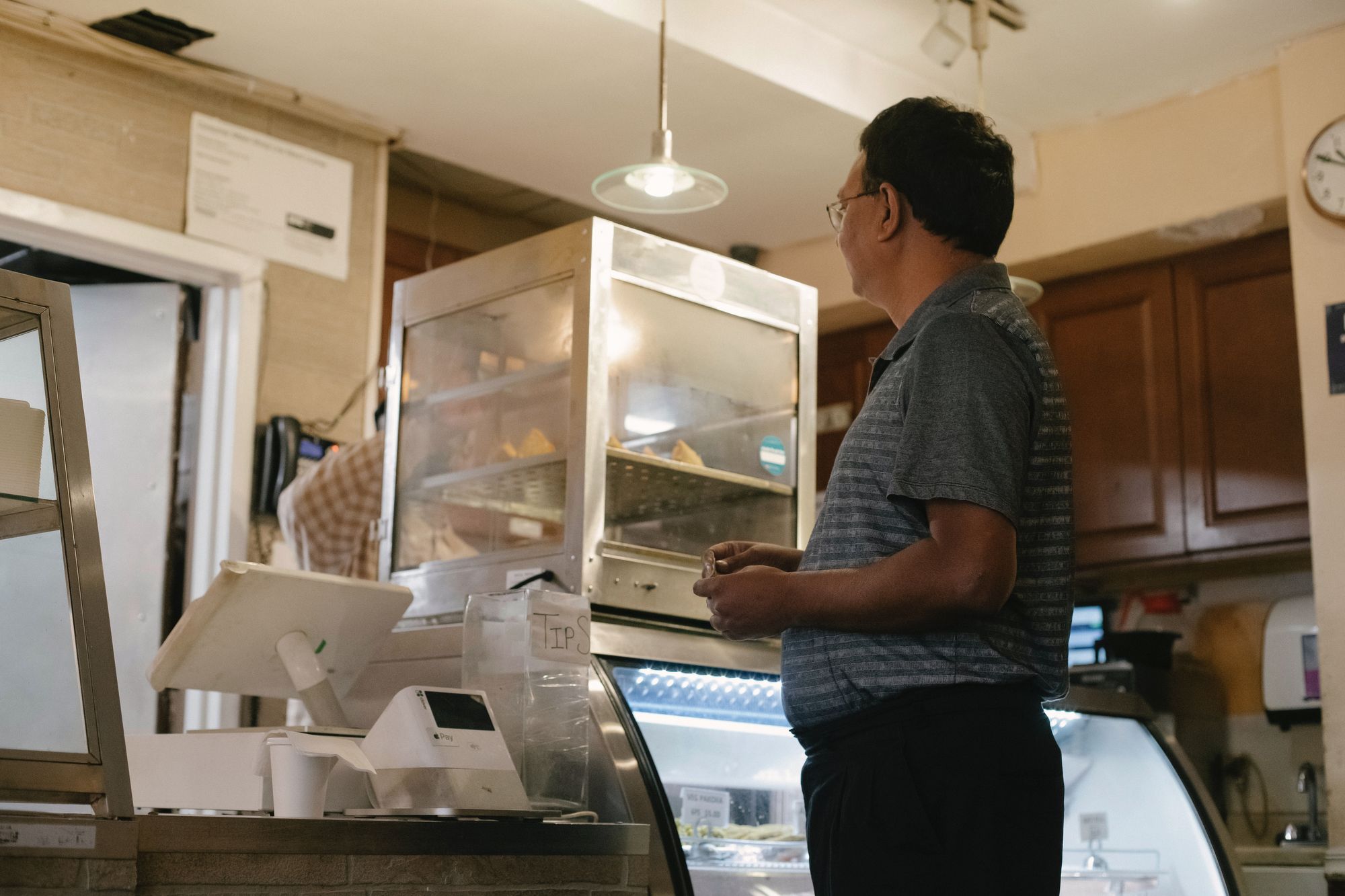
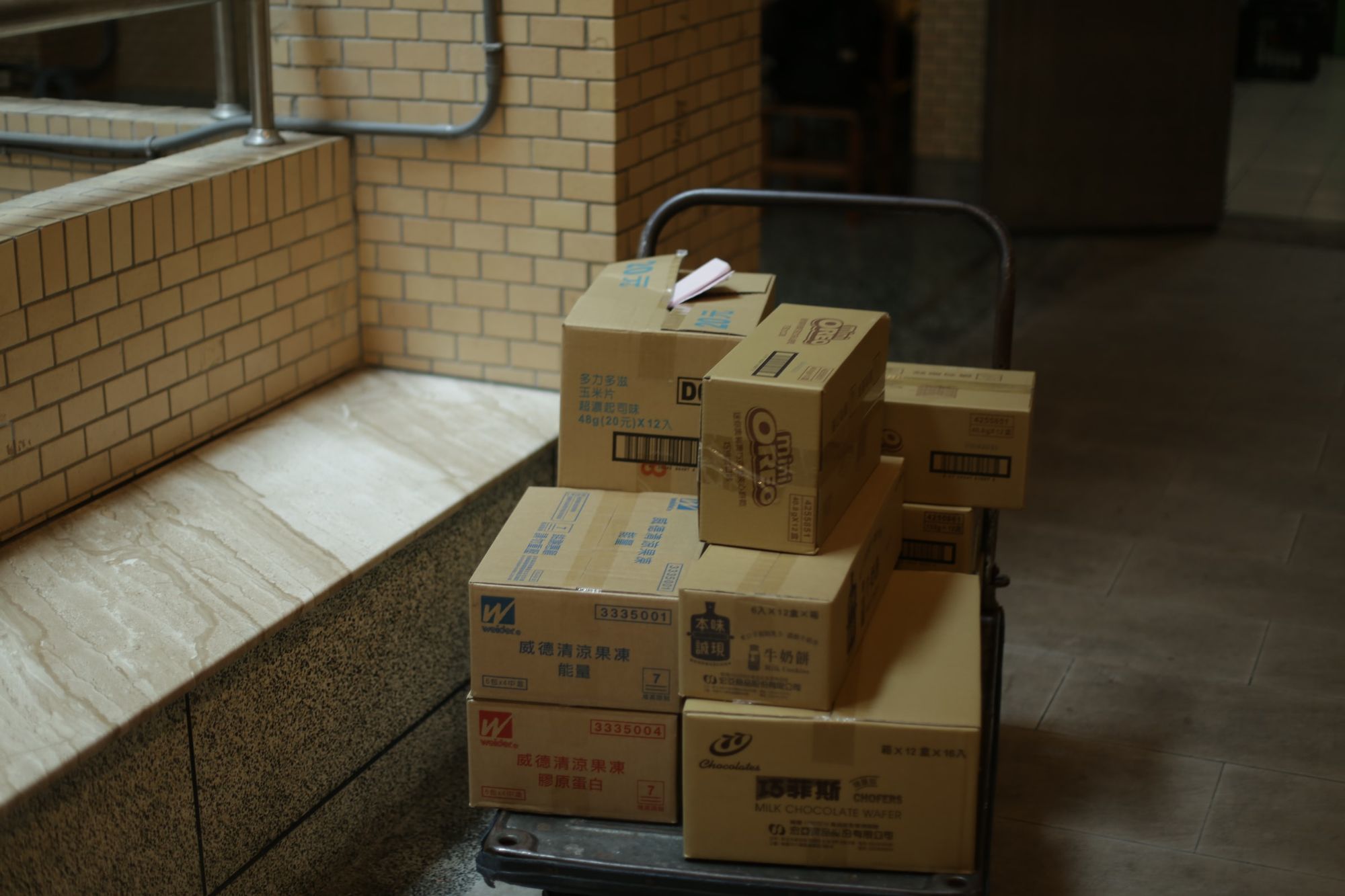