In recent years, plastic manufacturing has been a topic of debate due to its potential harm to the environment. It is true that plastic can be incredibly damaging to the environment if it is not manufactured responsibly.
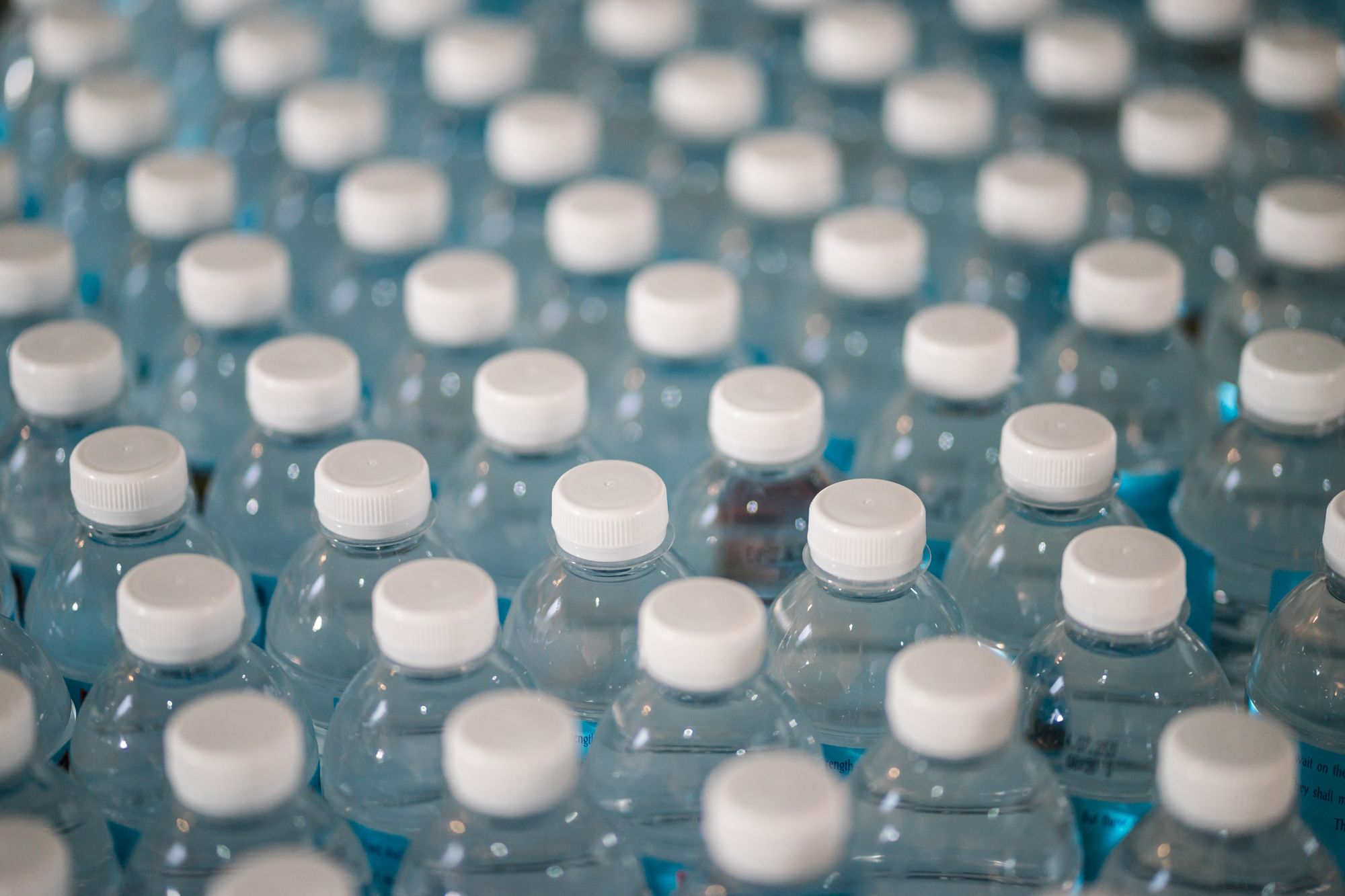
But it is also true that plastic can be produced in ways that have a positive impact on the environment. Responsible plastic manufacturing is a process that seeks to reduce the environmental impact of plastic production while providing products that are safe and durable.
This article covers the following:
- What Are the Latest Innovations in Plastic Manufacturing?
- Why Is Keeping Up with the Latest Innovations Important?
- How Can You Keep Up with the Latest Innovations?
- The Benefits of Keeping Up with Innovations in Plastic Manufacturing
- What Are the Challenges of Keeping Up with Innovations in Plastic Manufacturing?
- The Future of Plastic Manufacturing Innovations
- Examples of Innovations in Plastic Manufacturing
- What Are the Different Types of Plastic Manufacturing?
- What Are the Different Manufacturing Processes for Plastic?
- What Are the Different Types of Plastic Products?
What Are the Latest Innovations in Plastic Manufacturing?
In the past few decades, plastic manufacturing has made tremendous advances, offering more durable and cost-effective solutions for a variety of industrial and consumer applications.
From 3D printing to injection molding, plastic manufacturers are constantly innovating to meet the ever-evolving needs of the market. Here are some of the latest innovations in plastic manufacturing that are transforming the industry:
3D Printing
3D printing is a revolutionary technology that is transforming the way manufacturers make plastic components. Using a process called additive manufacturing, 3D printers layer thin layers of plastic filament to create complex shapes and parts with near-perfect precision.
This technology has enabled mass customization and rapid prototyping, allowing companies to quickly produce parts and products to meet their exact specifications.
Injection Molding
Injection molding is a process used to create parts from molten plastic material. The molten material is injected into a mold that is designed to create an exact replica of the desired shape. This technology is often used in large-scale production runs and offers a cost-effective solution for producing complex parts.
Vacuum Forming
Vacuum forming is a process used to shape plastic materials into desired shapes. A sheet of plastic material is heated and then placed over a mold. A vacuum is then used to draw the plastic material into the mold and create the desired shape. This process is often used for creating large parts or components with complex shapes.
Thermoforming
Thermoforming is a process used to create parts or components from a plastic sheet. The plastic sheet is heated and then placed over a mold. The mold is then used to shape the plastic material into the desired shape. This process is often used for creating large parts or components with complex shapes.
Extrusion
Extrusion is a process used to create parts or components from a plastic material. The plastic material is heated and then pushed through a die to create a continuous shape. This process is often used for creating complex shapes with intricate details.
These are just some of the latest innovations in plastic manufacturing. As the industry continues to evolve, more advanced processes and technologies will be developed to meet the ever-changing needs of the market. As a result, manufacturers will be able to create more precise parts with greater efficiency and better cost-effectiveness.
Why Is Keeping Up with the Latest Innovations Important?
Keeping up with the latest innovations in plastic manufacturing is essential for any company involved in the production of plastic components. The plastic industry is constantly evolving, and new technologies are being developed at a rapid rate.
As a result, it is important for companies to stay up-to-date with the latest innovations in order to remain competitive. One of the key reasons why it is important to keep up with the latest innovations in plastic manufacturing is to ensure that products are as efficient and cost-effective as possible.
By staying up-to-date with the latest developments in the industry, companies can ensure that their products are of the highest quality and that they are able to remain competitive in the market.
Additionally, keeping up-to-date with the latest innovations can help companies to reduce their costs and increase their profits. Furthermore, staying up-to-date with the latest innovations in plastic manufacturing can help companies to remain ahead of their competitors.
By staying ahead of the competition, companies can ensure that their products remain in demand and that they can continue to meet customer demands. Keeping up-to-date with the latest innovations in plastic manufacturing can also help companies to keep their production costs low, resulting in greater profits.
Another reason why it is important to keep up with the latest innovations in plastic manufacturing is to ensure that products are as safe and reliable as possible. By staying up-to-date with the latest developments in the industry, companies can ensure that their products are not only of the highest quality but that they are also safe for use.
Additionally, staying up-to-date with the latest innovations in plastic manufacturing can help companies to stay compliant with regulatory standards and ensure that their products meet all safety requirements.
Finally, staying up-to-date with the latest innovations in plastic manufacturing can help companies to remain environmentally friendly. By staying up-to-date with the latest developments in the industry, companies can ensure that their products are produced in an environmentally friendly manner, making them more attractive to consumers and helping to reduce their carbon footprint.
Overall, keeping up with the latest innovations in plastic manufacturing is essential for any company involved in the production of plastic components.
By staying up-to-date with the latest developments in the industry, companies can ensure that their products are of the highest quality, that they are cost-effective, that they remain ahead of their competitors, that they are safe and reliable, and that they are produced in an environmentally friendly manner. Keeping up with the latest innovations in plastic manufacturing is essential for any company involved in the industry.
How Can You Keep Up with the Latest Innovations?
In the world of plastic manufacturing, staying up-to-date with the latest innovations is essential. Knowing the newest technologies, materials, and processes can give you a competitive edge, help you produce better products, and even save you money. But how can you stay on top of the latest developments? Here are a few tips to help you stay in the know:
Read trade magazines and other publications.
Trade magazines, such as Plastics Technology and Modern Plastics, are great resources for staying current on the latest developments in plastic manufacturing. They often feature in-depth articles on the newest materials, processes, and technologies, as well as industry news, events, and trends.
Attend trade shows and conferences: Trade shows and conferences are great places to network and learn about the latest innovations in plastic manufacturing. At these events, you'll have the opportunity to see the newest products firsthand, as well as meet and talk with industry professionals.
Follow industry blogs and social media accounts.
Blogs and social media accounts related to plastic manufacturing are excellent sources for staying up-to-date on the latest developments. They often feature news and insights from industry experts, which can help you stay ahead of the curve.
Invest in research and development: Investing in research and development is a great way to stay on top of the latest innovations in plastic manufacturing. By investing in R&D, you'll be able to test and develop new materials, processes, and technologies, so you can stay ahead of the competition.
Partner with a trusted supplier: Partnering with a trusted supplier is another great way to stay current on the latest developments in plastic manufacturing. By partnering with a supplier, you'll be able to access their knowledge and resources, so you can stay up-to-date on the newest innovations.
By following these tips, you can ensure you stay on top of the latest innovations in plastic manufacturing. Keeping up with the latest developments is essential if you want to stay competitive and produce the best products. So, make sure to stay informed and be sure to invest in research and development to stay ahead of the curve.
The Benefits of Keeping Up with Innovations in Plastic Manufacturing
The world of plastic manufacturing is constantly evolving and transforming. With the rise of new technologies, materials, and processes, it's important for businesses to stay up to date with the latest innovations in the field.
Keeping up with the latest developments in plastic manufacturing offers numerous benefits, from improved product quality to cost savings. Here are some of the key benefits of staying current with the latest innovations in plastic manufacturing.
Improved Product Quality
By staying up to date on the latest innovations in plastic manufacturing, businesses can ensure that their products are of the highest quality. This can be critical for businesses that produce products that must meet certain standards, such as medical devices or automotive components.
Being aware of the latest innovations allows businesses to take advantage of improvements in plastic manufacturing technology and processes, leading to improved product quality.
Cost Savings
Staying up to date on the latest innovations in plastic manufacturing can lead to cost savings, as businesses can take advantage of new materials and processes that are more efficient and cost-effective. This can result in reduced costs associated with production, as well as improved profits.
Increased Efficiency
Keeping up with the latest innovations in plastic manufacturing can also lead to increased efficiency in production. By staying up to date on the latest developments, businesses can take advantage of improved processes that lead to faster production times and fewer wasted materials. This can translate into increased profits and a more efficient production process.
Enhanced Safety
By staying current with the latest innovations in plastic manufacturing, businesses can ensure that their products are produced in the safest way possible. This is especially important for companies producing products for the medical, automotive, and aerospace industries, where safety is critical.
Keeping up with the latest innovations in plastic manufacturing can be a critical component of a successful business. By staying current on the latest advancements, businesses can ensure that their products are of the highest quality, cost-effective, and produced in the safest manner possible.
Taking advantage of the latest innovations can lead to improved profits, increased efficiency, and enhanced safety, making it an invaluable investment for any business.
What Are the Challenges of Keeping Up with Innovations in Plastic Manufacturing?
The manufacturing industry is constantly evolving, with new technologies, materials, and techniques being developed every day. Plastic manufacturing is no different, as the industry is constantly pushing the boundaries of what’s possible with plastic.
Keeping up with the latest innovations in plastic manufacturing can be a challenge, however, as there are a wide variety of challenges that must be overcome. One of the biggest challenges of keeping up with the latest innovations in plastic manufacturing is cost.
Plastic manufacturing is an expensive process, and many of the new technologies and materials used can be expensive. Additionally, the cost of training employees to use the new technologies and materials can be prohibitive.
For smaller companies, it may be difficult to keep up with the latest innovations if they lack the resources to do so. Another challenge of keeping up with the latest innovations in plastic manufacturing is the need to stay up-to-date on the latest regulations.
Many countries and states have specific regulations and laws regarding the use of certain types of plastic, and it’s important to stay on top of these regulations in order to remain compliant.
Additionally, new regulations and technologies can be introduced on a regular basis, so it’s important to stay informed and ensure that your business is up-to-date. Finally, there is the challenge of staying ahead of the competition.
In the highly competitive plastic manufacturing industry, it’s important to stay ahead of the curve and be the first to adopt the latest innovations. This can be difficult to do, however, as other companies may be quicker to adopt new technologies and materials.
Keeping up with the competition can be a full-time job and require a lot of research and effort. Keeping up with the latest innovations in plastic manufacturing can be a challenge, but it’s also a necessary part of staying competitive in the industry. By overcoming the challenges mentioned above, businesses can remain ahead of the competition and ensure their products are of the highest quality.
The Future of Plastic Manufacturing Innovations
The future of plastic manufacturing is looking brighter than ever. With advancements in technology, plastic manufacturing has come a long way in recent years. From 3D printing to injection molding, the possibilities of what can be created with plastic are seemingly endless.
In the coming years, we can expect to see continued advances in the way plastic is produced. 3D printing is making it easier than ever to create intricate and complex parts with precision.
Injection molding is also becoming more efficient, allowing companies to produce large quantities of plastic parts with high accuracy. It is also likely that we will see more advanced materials used in plastic manufacturing.
Bioplastics, for example, are made from renewable resources and are becoming increasingly popular.
These materials are not only more eco-friendly but also more resilient and lightweight than traditional plastics. In addition, the use of automation in plastic manufacturing is growing rapidly.
Robotics and other automation technologies can help companies increase efficiency and reduce costs. Automation can also help companies produce more consistent and high-quality parts.
Finally, the use of AI and machine learning in plastic manufacturing is also gaining momentum. By using AI to analyze data from production processes, manufacturers can gain insight into how to improve their operations.
This could ultimately lead to better products and more efficient processes. Overall, plastic manufacturing is on the rise and the future looks bright. As technology continues to improve, plastic manufacturing will become faster and more efficient, allowing companies to create more innovative products than ever before. With the right materials and the right technology, plastic manufacturing will continue to revolutionize the way we create goods.
Examples of Innovations in Plastic Manufacturing that Have Changed the Manufacturing Game
The plastics industry has come a long way in recent years, and manufacturers are continuously innovating to create new products and processes. From 3D printing to nanotechnology, the innovations in plastic manufacturing have been astounding. Here are just a few examples of the latest developments in this ever-evolving industry.
3D Printing
3D printing technology has revolutionized the plastics industry by allowing manufacturers to create complex parts and products with a higher degree of accuracy and precision.
With the help of 3D printing, companies can produce intricate parts and products with a much smaller environmental footprint. 3D printing also helps to reduce the cost of production and make plastic components more affordable.
Nanotechnology
Nanotechnology has been a major game-changer for the plastics industry. By utilizing nanomaterials, manufacturers can create stronger, more resilient plastics that can withstand extreme temperatures and harsh environments.
Nanoparticles also provide a higher degree of performance and durability, resulting in a longer product life. This technology has enabled manufacturers to create plastics that are lighter, more durable, and more cost-effective than ever before.
Recycled Plastics
As environmental awareness grows, so does the demand for recycled plastic products. Manufacturers are beginning to recognize the importance of reducing their environmental impact and are creating products made from recycled plastics. This not only helps to reduce waste and conserve resources, but it also helps manufacturers create cost-effective and sustainable plastic products.
Bio-based Plastics
Bio-based plastics are made from renewable resources, such as corn and sugarcane. These plastics are more sustainable than traditional plastic products, and they can be used to create a variety of products, from food packaging to medical devices.
In addition, bio-based plastics are often more cost-effective and require fewer hazardous chemicals in the manufacturing process. These are just a few of the many innovations in plastic manufacturing that are helping to shape the future of the plastics industry.
By leveraging the latest technologies, manufacturers can create cost-effective, sustainable, and high-performance plastics that can be used for a variety of applications. With the help of these technologies, the plastics industry is sure to continue to innovate for years to come.
What Are the Different Types of Plastic Manufacturing?
Plastic manufacturing has come a long way in the past decade. From the creation of new materials and processes to the development of more efficient production techniques, the plastic manufacturing industry has undergone significant growth.
But what exactly are the different types of plastic manufacturing out there? Here, we’ll take a look at some of the different types of plastic manufacturing and examine what each one does.
Injection Molding is one of the most common types of plastic manufacturing. This process involves the injection of molten plastic into a mold to create a desired shape. Injection molding is used to create a wide range of products, from small, intricate parts to large, complex items.
It’s a fast and efficient process that can be used to make a variety of products quickly and efficiently. Blow Molding is another type of plastic manufacturing that involves the creation of hollow plastic objects.
This process is often used for the production of large items and can be used to create items such as toys, bottles, and other hollow objects. Blow molding is a fast process and can be used to produce products in a variety of shapes and sizes.
Vacuum Forming is a type of plastic manufacturing where a plastic sheet is heated and then vacuum-sealed onto a mold. This process is used to create items like signs, packaging, and other products.
Vacuum forming is a cost-effective process that is often used to create items with intricate detail and shapes. Extrusion is a type of plastic manufacturing process where molten plastic is forced through a die to create a desired shape.
This process is used to make products like pipes, tubing, and rods. Extrusion is a highly efficient process that can be used to create a variety of shapes and sizes. These are just a few of the different types of plastic manufacturing that have been developed over the years.
Each type of plastic manufacturing has its own advantages and disadvantages and is best suited for certain applications. As technology continues to evolve, so too will the plastic manufacturing process. It’s important to keep up with the latest innovations in plastic manufacturing so that you can make the most of your production needs.
What Are the Different Manufacturing Processes for Plastic?
Plastic is a versatile material with a wide range of applications in different industries. As a result, manufacturing processes for plastic have become increasingly diverse, offering manufacturers a range of options to produce plastic products.
Injection molding is one of the most common manufacturing processes for plastic. It involves melting plastic pellets or powder and forcing it into a mold under pressure. Once the plastic has cooled and hardened, the mold is opened and the part is ejected.
Injection molding offers excellent dimensional accuracy and repeatability, and is ideal for producing high-volume components. Extrusion is another popular manufacturing process for plastic.
It involves forcing a heated thermoplastic through a die to form a continuous shape. The end result is a thin sheet or rod that can be cut to length and used for a variety of applications.
Extrusion is frequently used for manufacturing items such as pipes and tubing. Vacuum forming is a manufacturing process for plastics that involves heating a sheet of plastic and using a vacuum to pull it into a mold.
Vacuum forming is an economical way to produce plastic parts with complex shapes and dimensions, such as those used in packaging or signage. Rotational molding is a manufacturing process that involves rotating a mold while it is filled with a heated plastic.
The plastic is spread evenly over the mold, and once cooled it is ejected from the mold in the desired shape. Rotational molding is used for producing large, hollow parts, such as containers and toys.
Finally, blow molding is a manufacturing process for producing hollow plastic parts, such as bottles and other plastic containers. It involves melting a plastic tube and using air pressure to blow the melted plastic into a mold.
Blow molding is commonly used for producing large numbers of bottles and containers. These are just a few of the many manufacturing processes for plastic. Each process has its own advantages and disadvantages, so it is important to carefully consider the application and determine which process is best suited for the job. By keeping up with the latest innovations in plastic manufacturing, you can ensure that you are producing the highest quality parts.
What Are the Different Types of Plastic Products?
Plastics are everywhere in our lives. From the products we use every day to the packaging that protects our food, plastics are an integral part of modern life. But did you know that there are different types of plastics used in the production of these products? In this blog, we’ll take a look at the different types of plastic products and their uses.
Thermoplastic
These are the most common type of plastics used for everyday products and packaging. Thermoplastic polymers are lightweight, flexible, and can be easily molded into a variety of shapes.
Common products made from thermoplastics include plastic bottles, food containers, and plastic bags. Thermosetting Plastics: These plastics are more rigid and stronger than thermoplastic polymers.
They are heated to a high temperature, then hardened, and can’t be remolded once cooled. Common products made from thermosetting plastics include electrical components and auto parts.
Biodegradable Plastics
As the name suggests, biodegradable plastics are plastics that break down over time, making them a more sustainable option for packaging. Common products made from biodegradable plastics include plastic packaging and food containers.
Engineering Plastics
These plastics are used for more technical applications, such as in the electronics, automotive and medical industries. They are typically engineered to be tougher, have higher melting points, and be less prone to chemical attacks than other plastics.
Common products made from engineering plastics include electronic components and medical devices.
High-Performance Plastics
High-performance plastics are engineered for specific applications that require superior performance and strength. They are typically more expensive than traditional plastics, but are able to withstand extreme temperatures, high pressure and chemical attack.
Common products made from high performance plastics include aircraft components and medical implants.
Recycled Plastics
Recycled plastics are created by melting down and reforming discarded plastics. This reduces the amount of plastic waste that is sent to landfills, and is a more sustainable option for production.
Common products made from recycled plastics include plastic containers and packaging. As you can see, there are many different types of plastic products and each has its own unique properties and uses. By understanding the different types of plastics, you can make more informed decisions when selecting the right material for your application.
How Can Deskera Assist You?
As a manufacturer, you must keep track of your inventory stock. The condition of your inventory has a direct impact on production planning. It also has a direct impact on people and machinery use and capacity utilization.
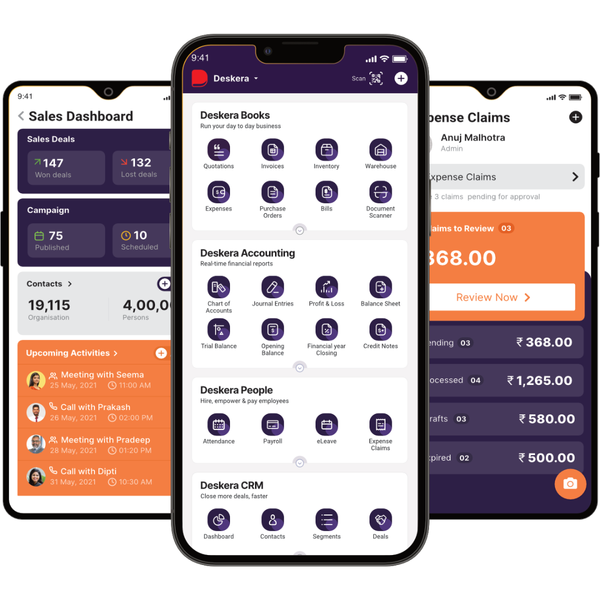
Deskera MRP is the one tool that lets you do all of the above. With Deskera, you can:
- Control production schedules
- Compile a Bill of Materials
- Produce thorough reports
- Make your dashboard
Deskera ERP is a complete solution that allows you to manage suppliers and track supply chain activity in real time. It also allows you to streamline a range of other company functions.
Deskera Books allows you to manage your accounts and finances better. It helps maintain good accounting standards by automating billing, invoicing, and payment processing tasks.
Deskera CRM is a powerful tool that organizes your sales and helps you close deals rapidly. It enables you to perform crucial tasks like lead generation via email and gives you a comprehensive view of your sales funnel.
Deskera People is a straightforward application for centralizing your human resource management activities. Not only does the technology expedite payroll processing, but it also helps you to handle all other operations such as overtime, benefits, bonuses, training programs, and much more.
Key Takeaways:
- 3D printing is a revolutionary technology that is transforming the way manufacturers make plastic components.
- The plastic industry is constantly evolving, and new technologies are being developed at a rapid rate.
- Many countries and states have specific regulations and laws regarding the use of certain types of plastic, and it’s important to stay on top of these regulations in order to remain compliant.
- Injection molding is one of the most common manufacturing processes for plastic.
- Each type of plastic manufacturing has its own advantages and disadvantages and is best suited for certain applications. As technology continues to evolve, so too will the plastic manufacturing process.
Related Articles:
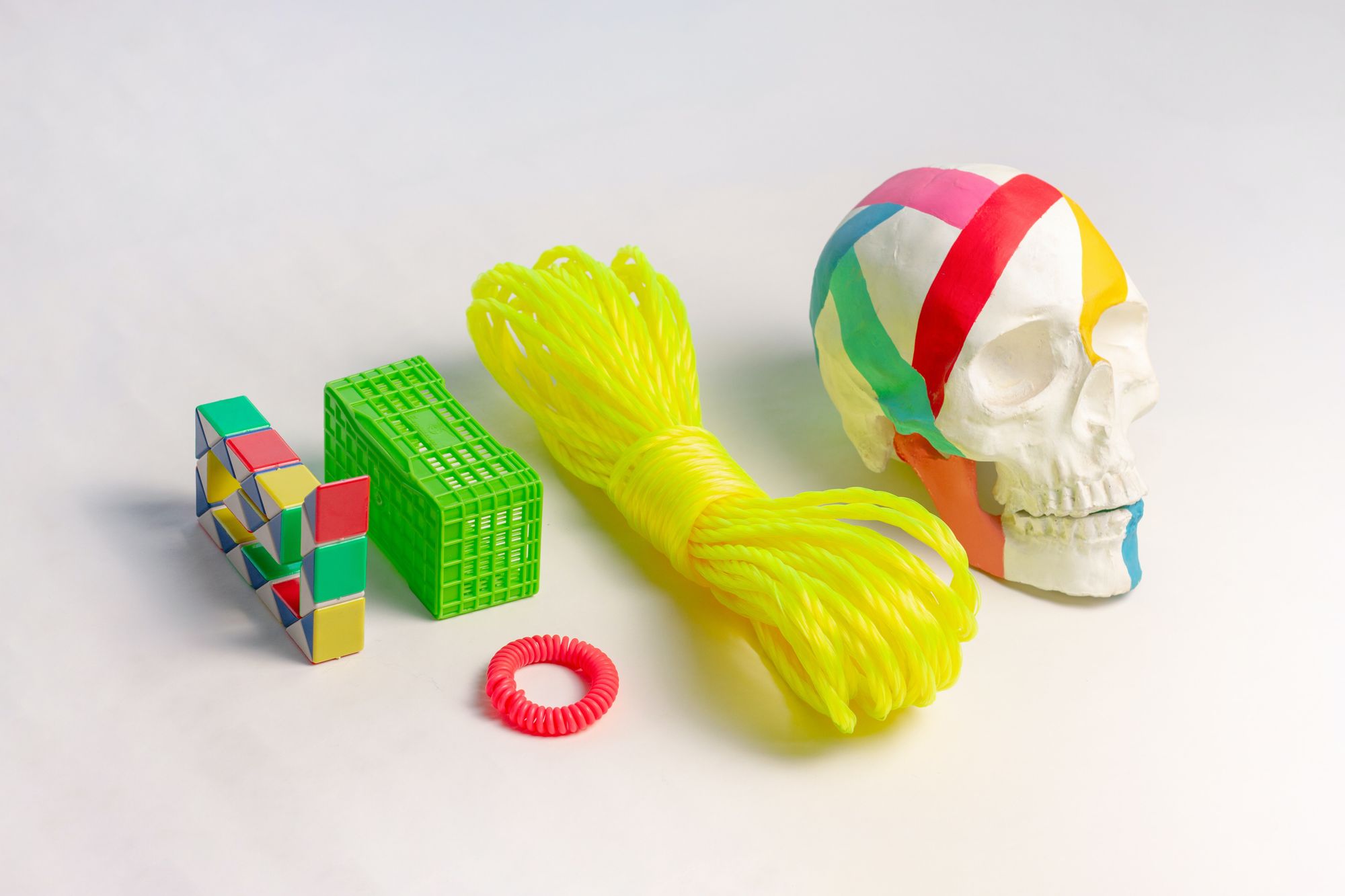
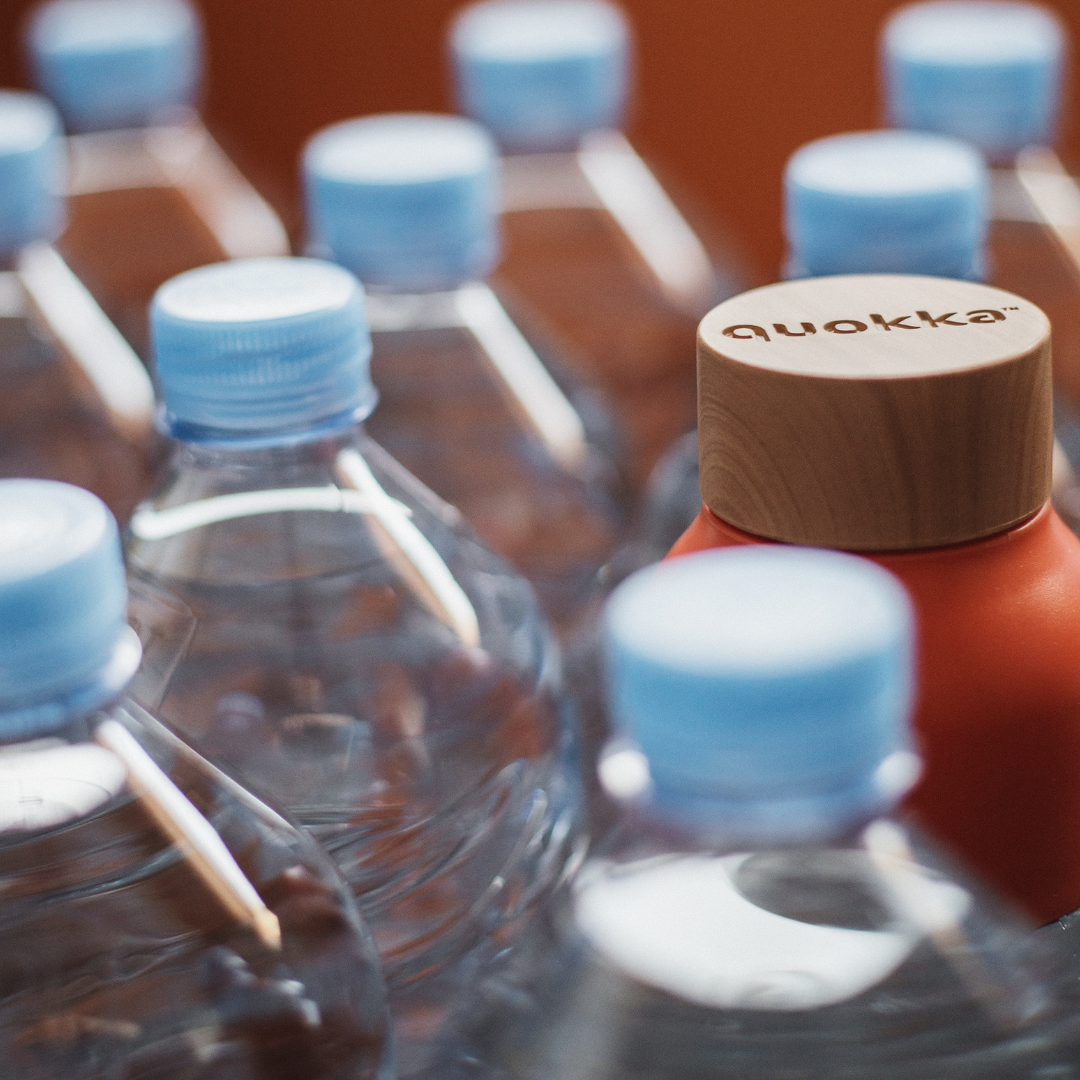
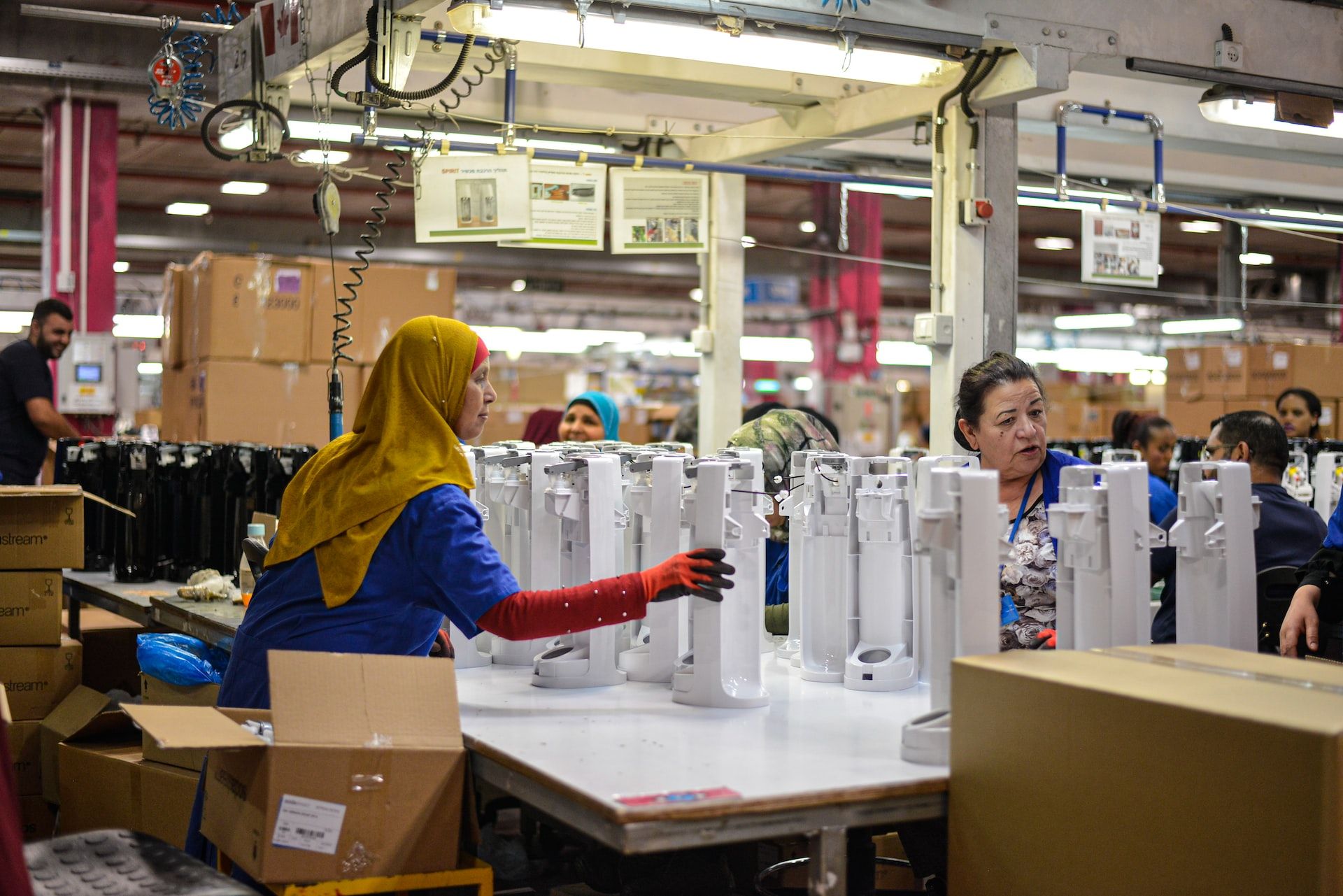