Plastics are everywhere. From the packaging of our food and drink to the construction of our buildings and vehicles, plastics have become an essential part of modern life. But have you ever stopped to consider where these ubiquitous materials come from and how they are manufactured?
The history of plastics manufacturing is a fascinating tale of human ingenuity, from the early development of natural polymers like rubber and cellulose to the invention of synthetic materials like Bakelite and nylon. Along the way, plastics have revolutionized countless industries and transformed the way we live, work, and play.
However, the rise of plastics has also brought with it a host of environmental and health concerns and growing pressure to develop more sustainable manufacturing methods.
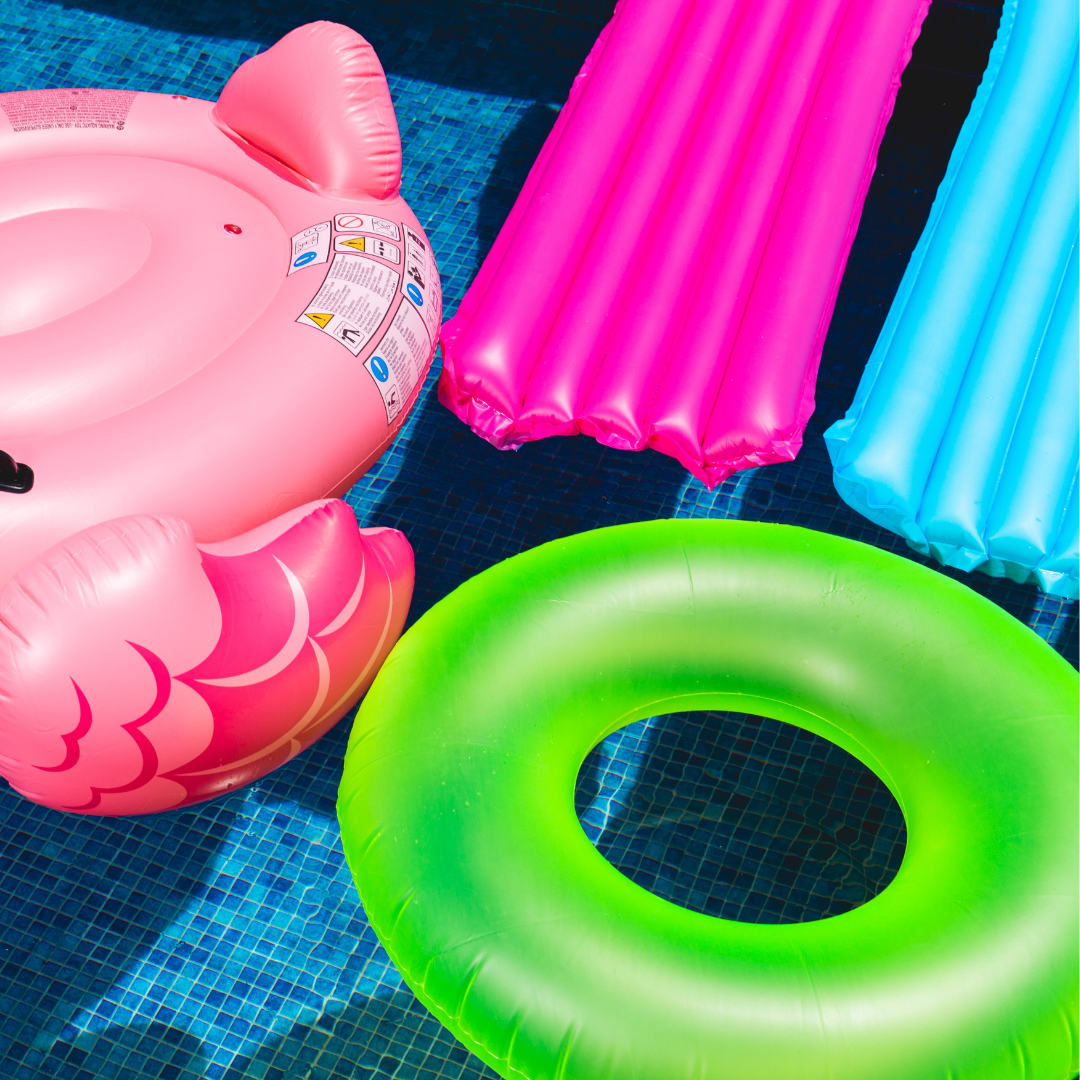
In this article, we'll take a deep dive into the history and future of plastics manufacturing, exploring the benefits and drawbacks of these versatile materials and considering what the future might hold for this essential industry.
- Plastics Manufacturing and its Importance in Modern Society
- History of Plastic Manufacturing
- Benefits and Drawbacks of Plastics Manufacturing
- Future of Plastic Manufacturing
- Latest Developments in Plastics Manufacturing
- What the Future of Plastics Manufacturing Might Look Like
- Need for ERP and MRP software for Plastic Manufacturing
- How can Deskera Help You?
- Key Takeaways
- Related Articles
Plastics Manufacturing and its Importance in Modern Society
Plastic manufacturing is essential to modern society, playing a vital role in countless industries and applications. From packaging and transportation to construction and healthcare, plastics are used to create a wide range of products that are essential to our daily lives.
One of the key benefits of plastics is their versatility. They can be molded into any shape or form, and their properties can be tailored to suit specific needs. For example, plastics can be made lightweight, durable, and resistant to heat, chemicals, and UV radiation, making them ideal for use in everything from car parts to medical devices.
Another advantage of plastics is their low cost. Unlike many traditional materials like wood or metal, plastics can be produced on a large scale at a relatively low cost, making them an attractive option for many manufacturers.
However, the rise of plastics manufacturing has also brought with it a host of environmental and health concerns. Plastics are often non-biodegradable and can take hundreds of years to decompose, leading to significant amounts of plastic waste in landfills and oceans. In addition, some plastics contain harmful chemicals that can leach into food and water, posing potential health risks.
Despite these challenges, the plastics manufacturing industry continues to evolve and innovate, with new materials and manufacturing processes being developed to address these concerns. For example, biodegradable and compostable plastics are now being developed that can break down more quickly in the environment, and recycling programs are being implemented to reduce the amount of plastic waste.
In conclusion, plastics manufacturing is an essential part of modern society, providing countless benefits and opportunities for innovation. However, as we continue to rely on plastics daily, it is important to address the environmental and health challenges associated with these materials and work towards a more sustainable future.
History of Plastic Manufacturing
The history of plastics manufacturing is a story of human ingenuity and innovation. It began with the development of natural polymers like rubber and cellulose, which were used for a variety of applications, from waterproofing to clothing.
In the 19th century, scientists began experimenting with synthetic materials, leading to the invention of materials like Bakelite and nylon that transformed the manufacturing industry. Plastic manufacturing continued to evolve throughout the 20th century, with new materials and processes being developed to meet the growing demand for plastic products.
Today, plastics are used in a wide range of applications, from packaging and transportation to healthcare and construction. However, the rise of plastics has also brought with it a host of environmental and health concerns, leading to growing pressure to develop more sustainable manufacturing methods.
The history of plastics manufacturing is an important reminder of the power of human creativity and innovation and the need to balance progress with responsibility.
Origins Of Plastics and How They were First Developed
The origins of plastics can be traced back to natural materials that were used by ancient civilizations. For example, the Mesoamericans used rubber to make balls and waterproof fabrics, while the Egyptians used resins and waxes to create jewelry and figurines.
The first synthetic plastic was invented in the mid-19th century by Alexander Parkes, a British inventor. Parkes created a material he called Parkesine, which was made by dissolving cellulose in nitric acid and then shaping it into various forms.
Parkesine was exhibited at the 1862 Great International Exhibition in London, where it received a lot of attention and was praised for its potential to replace expensive materials like ivory and tortoiseshell.
However, Parkesine was not very successful commercially, as it was expensive to produce and had a tendency to crack and deform over time. It was not until the early 20th century that synthetic plastics became widely used, with the invention of materials like Bakelite and celluloid.
Bakelite, invented by Leo Baekeland in 1907, was a thermosetting plastic that was highly resistant to heat and electricity, making it ideal for use in electrical and mechanical applications. Celluloid, invented by John Wesley Hyatt in 1868, was a transparent, flexible material used for various applications, from photographic film to billiard balls.
Since then, the manufacturing of plastics has continued to evolve, with new materials and processes being developed to meet the growing demand for plastic products. Today, plastics are used in countless industries and applications, from food packaging to medical devices to automobile parts.
Despite their many advantages, the environmental and health concerns associated with plastics have led to a growing push for more sustainable manufacturing methods and materials.
How the Manufacturing Process has Evolved Over Time
The manufacturing process for plastics has evolved significantly over time, with new techniques and technologies being developed to improve efficiency, quality, and sustainability.
In the early days of plastics manufacturing, the process was largely manual and labor-intensive. Workers would mix the raw materials by hand, then heat and shape the material using molds and presses. This process was time-consuming and often produced inconsistent results.
In the 20th century, new manufacturing methods were developed that revolutionized the industry. Injection molding, for example, was invented in the 1930s and allowed for the rapid production of large quantities of identical parts. Extrusion, another common process, allowing for the continuous production of materials like plastic tubing and sheets.
In recent years, automation and computer technology advances have further transformed the plastics manufacturing process. Computer-aided design (CAD) and computer-aided manufacturing (CAM) software can now be used to design and simulate plastic products before they are produced, reducing the need for physical prototypes and streamlining the production process. Robotics and other automated systems are also increasingly being used to handle tasks like material handling, assembly, and quality control.
In addition to these technological advancements, there is also a growing emphasis on sustainable manufacturing methods and materials. For example, bio-based plastics are being developed that are made from renewable resources like cornstarch, and recycling programs are being implemented to reduce waste and conserve resources.
Overall, the manufacturing process for plastics has come a long way since the early days of manual labor and hand-mixing. Today, the industry is characterized by highly automated processes, advanced technologies, and a growing focus on sustainability.
Major Milestones In The History Of Plastics Manufacturing, Key Inventions, And Developments
The history of plastics manufacturing is marked by many significant milestones, key inventions, and developments that have transformed the industry. Here are some of the major milestones in the history of plastics manufacturing:
- 1856: Alexander Parkes invented the first synthetic plastic, called Parkesine, made from cellulose treated with nitric acid.
- 1907: Leo Baekeland invents Bakelite, the first thermosetting plastic, which is highly heat-resistant and electrically insulating, and revolutionizes the electrical and mechanical industries.
- 1913: Polyvinyl chloride (PVC), a versatile and durable plastic, is invented.
- 1926: Polyethylene, a lightweight and flexible plastic used in packaging was invented by accident.
- 1933: Polypropylene, a versatile plastic with a high melting point and resistance to acids and solvents is invented.
- 1937: Nylon, a strong, lightweight, and durable synthetic fiber used in clothing, was invented.
- 1954: High-density polyethylene (HDPE), a stronger and more durable version of polyethylene, is developed.
- 1973: PET (polyethylene terephthalate), a highly recyclable and versatile plastic used in bottles and containers, was invented.
- 1980s: Biodegradable plastics, made from materials like starch, are developed.
- 1990s: Recycling programs and processes are developed to reduce waste and promote sustainability in the plastics industry.
These milestones and inventions have led to the widespread use of plastics in many different applications, from packaging and transportation to construction and healthcare. While plastics have brought many benefits to modern society, their production and disposal have also led to environmental and health concerns. As a result, there is growing interest in developing more sustainable and eco-friendly plastics and manufacturing processes.
Benefits and Drawbacks of Plastics Manufacturing
Plastics manufacturing has brought many benefits to modern society, but it also has its drawbacks. Here are some of the main benefits and drawbacks of plastics manufacturing:
Benefits:
- Versatility: Plastics can be molded into any shape and used in a wide range of applications, from packaging and transportation to construction and healthcare.
- Durability: Many types of plastics are strong and durable, making them ideal for use in products that need to withstand wear and tear, extreme temperatures, and other challenging conditions.
- Cost-effectiveness: Plastics are often cheaper to produce than other materials like metal or glass, making them an attractive option for manufacturers.
- Lightweight: Plastics are generally lightweight, which can reduce transportation costs and fuel consumption.
- Safety: Plastics can be designed to be safe for use in medical devices, food packaging, and other applications where hygiene and safety are critical.
Drawbacks:
- Environmental impact: Plastics can take hundreds of years to break down in the environment, leading to pollution and harm to wildlife.
- Health concerns: Some plastics contain chemicals that can harm human health, particularly if they are not disposed of properly.
- Limited recycling: While many types of plastics can be recycled, the process can be difficult and expensive, and not all plastics are recyclable.
- Non-renewable: Most plastics are made from non-renewable resources like oil and gas, which are finite and contribute to greenhouse gas emissions.
- Waste: Plastic manufacturing generates a significant amount of waste, from the production process itself to the disposal of plastic products at the end of their lifecycle.
Overall, while plastics manufacturing has brought many benefits to modern society, it is important to address the drawbacks and work towards more sustainable and eco-friendly practices. This includes developing new materials and recycling technologies, reducing plastic waste, and promoting responsible use and disposal of plastic products.
Future of Plastic Manufacturing
The future of plastics manufacturing is likely to be shaped by a number of factors, including environmental concerns, technological advancements, and changing consumer preferences. Here are some potential developments in the future of plastics manufacturing:
- Sustainable materials: There is growing interest in developing new types of plastics that are biodegradable, made from renewable resources, or easily recyclable. Researchers are exploring materials like algae, fungi, and even food waste as potential sources of bioplastics.
- Advanced recycling technologies: Recycling technologies are evolving to make it easier and more cost-effective to recycle different types of plastics. For example, chemical recycling processes can break down plastic waste into its component parts, which can then be used to create new plastic products.
- Digital manufacturing: Advanced digital manufacturing technologies like 3D printing could revolutionize the way that plastics are produced, allowing for more precise and efficient production and customization.
- Circular economy: The concept of a circular economy, in which waste is minimized and resources are kept in use for as long as possible, could significantly impact the future of plastics manufacturing. This could involve designing products with recycling and reuse in mind, and implementing closed-loop recycling systems that minimize waste and maximize resource efficiency.
- Consumer preferences: Changing consumer preferences, such as the growing demand for sustainable products and packaging, are likely to influence the future of plastics manufacturing. This could lead to an increased focus on sustainable materials and more eco-friendly production practices.
The future of plastics manufacturing is likely to be shaped by a combination of technological advancements, sustainability concerns, and changing consumer preferences. As the industry evolves, there will be opportunities to develop more sustainable and responsible approaches to plastics manufacturing and reduce the environmental impact of plastic production and waste.
Latest Developments in Plastics Manufacturing
Plastics manufacturing is a rapidly evolving industry, with new materials, technologies, and production methods emerging all the time. The latest developments in plastics manufacturing focus on creating more sustainable and eco-friendly materials and production processes, reducing waste, and improving efficiency.
These developments include biodegradable plastics, advanced recycling technologies, 3D printing, smart plastics, additive manufacturing, and recycling and reuse initiatives. By leveraging these latest developments, the industry is working to address some of its key challenges, such as plastic waste and pollution, resource depletion, and public perception.
As the industry continues to evolve, there will be opportunities to develop new and innovative approaches to plastics manufacturing that minimize environmental impact and promote sustainability.
Plastics manufacturing is an industry that is constantly evolving, with new developments in materials, processes, and applications emerging all the time. Here are some of the latest developments in plastics manufacturing:
- Biodegradable plastics: There is a growing interest in developing biodegradable plastics that can break down more quickly in the environment. This includes materials like plant-based plastics and biodegradable polymers.
- Recycling technologies: Advanced recycling technologies are being developed to make it easier and more cost-effective to recycle different types of plastics. This includes chemical recycling processes that can break down plastic waste into its component parts, which can then be used to create new plastic products.
- 3D printing: The use of 3D printing in plastics manufacturing is becoming more common, allowing for more precise and efficient production and customization.
- Smart plastics: Advances in materials science are leading to the development of "smart" plastics that can respond to changes in their environment. This includes materials that can change color, shape, or other properties in response to temperature, light, or other stimuli.
- Additive manufacturing: Additive manufacturing techniques like injection molding are being used to produce complex and customized plastic parts more efficiently.
- Recycling and reuse initiatives: There is an increasing focus on reducing plastic waste through recycling and reuse initiatives. For example, companies are developing closed-loop recycling systems that can capture and reuse plastic waste from their own manufacturing processes.
The latest developments in plastics manufacturing are focused on creating more sustainable and eco-friendly materials and production processes, as well as reducing waste and improving efficiency. As the industry continues to evolve, there will be opportunities to develop new and innovative approaches to plastics manufacturing that minimize environmental impact and promote sustainability.
Challenges Facing the Industry
The plastics manufacturing industry is facing a number of challenges, many of which are related to environmental concerns and sustainability. Here are some of the key challenges facing the industry:
- Plastic waste and pollution: Plastic waste and pollution are major environmental problems, with plastic waste ending up in landfills, oceans, and other natural habitats. The industry is facing pressure to reduce plastic waste and develop more sustainable and eco-friendly materials and production processes.
- Resource depletion: The production of plastics requires large amounts of natural resources, including oil and natural gas. With these resources becoming scarcer, the industry is facing pressure to develop more sustainable and resource-efficient production methods.
- Public perception: The plastics industry has a poor reputation among many consumers, who view plastic as environmentally damaging and wasteful. The industry is facing the challenge of changing public perception and promoting the benefits of plastic as a versatile and valuable material.
- Regulatory pressures: There is increasing regulatory pressure on the plastics industry to reduce its environmental impact, including through measures like extended producer responsibility (EPR) and plastic taxes.
- Technological limitations: While there have been many technological advancements in plastics manufacturing, there are still limitations in terms of the types of materials that can be produced, the efficiency of production processes, and the recyclability of different types of plastics.
The plastics manufacturing industry is facing significant challenges related to environmental sustainability, resource efficiency, public perception, and regulatory pressures.
To address these challenges, the industry will need to continue to innovate and develop new approaches to materials and production methods, while also working to promote the benefits of plastic and reduce its environmental impact.
What the Future of Plastics Manufacturing Might Look Like
The future of plastics manufacturing is likely to be shaped by a range of factors, including sustainability concerns, advances in materials science, and technological innovations. Here are some of the key trends that are likely to shape the future of the industry:
- Bioplastics: The use of bioplastics, which are made from renewable resources like plant-based materials, is likely to become more widespread as the industry seeks to reduce its reliance on fossil fuels.
- 3D printing: 3D printing is already being used to produce customized and complex plastic parts, and this technology is likely to become more widespread in the future, allowing for even greater precision and efficiency in production.
- Smart materials: Advances in materials science are leading to the development of "smart" plastics that can respond to changes in their environment. This includes materials that can change color, shape, or other properties in response to temperature, light, or other stimuli.
- Closed-loop recycling: The development of closed-loop recycling systems, where plastic waste from one manufacturing process is reused in another, is likely to become more common as the industry seeks to reduce waste and promote sustainability.
- Light weighting: The trend towards light weighting, or reducing the weight of plastic products, is likely to continue as companies seek to reduce material usage and improve fuel efficiency in transportation.
By leveraging new technologies and materials, and adopting more sustainable production processes, the industry will be better equipped to meet the challenges it faces and continue to provide valuable and versatile plastic products.
Need for ERP and MRP software for Plastic Manufacturing
The plastics manufacturing sector involves complex and diverse processes, which require efficient management of resources, production planning, inventory control, and quality assurance. This is where MRP (Material Requirements Planning) and ERP (Enterprise Resource Planning) software can be incredibly beneficial for the industry.
Here are some specific reasons why MRP and ERP software are needed in the plastics manufacturing sector:
- Resource Planning: MRP software helps in planning and managing the material requirements, production capacity, and scheduling of the production process. It enables the company to optimize resource utilization, reduce waste, and avoid overstocking or stockouts of raw materials and finished goods.
- Inventory Management: MRP and ERP software provide real-time visibility into inventory levels, demand forecasting, and order management. This helps in reducing inventory costs, improving order fulfillment, and avoiding stockouts.
- Quality Control: The plastics manufacturing industry demands a high level of quality control due to the diverse applications of plastics in different industries. MRP and ERP software provide quality control tools and help in tracking and monitoring product quality at every stage of the manufacturing process.
- Regulatory Compliance: The plastics manufacturing sector is subject to stringent regulatory compliance requirements. MRP and ERP software provide tracking and monitoring tools for regulatory compliance, thereby reducing the risk of non-compliance and associated penalties.
- Improved Efficiency: MRP and ERP software help in automating and streamlining many of the routine and repetitive tasks, which frees up resources and improves overall efficiency.
In summary, MRP and ERP software provide a comprehensive solution for managing the complex operations of the plastics manufacturing sector. It helps in improving resource planning, inventory management, quality control, regulatory compliance, and overall efficiency, thereby increasing profitability and competitiveness.
How can Deskera Help You?
Deskera ERP and MRP systems help you to keep your business units organized. The system's primary functions are as follows:
- Keep track of your raw materials and final items inventories
- Control production schedules and routings
- Keep a bill of materials
- Produce thorough reports
- Make your own dashboards
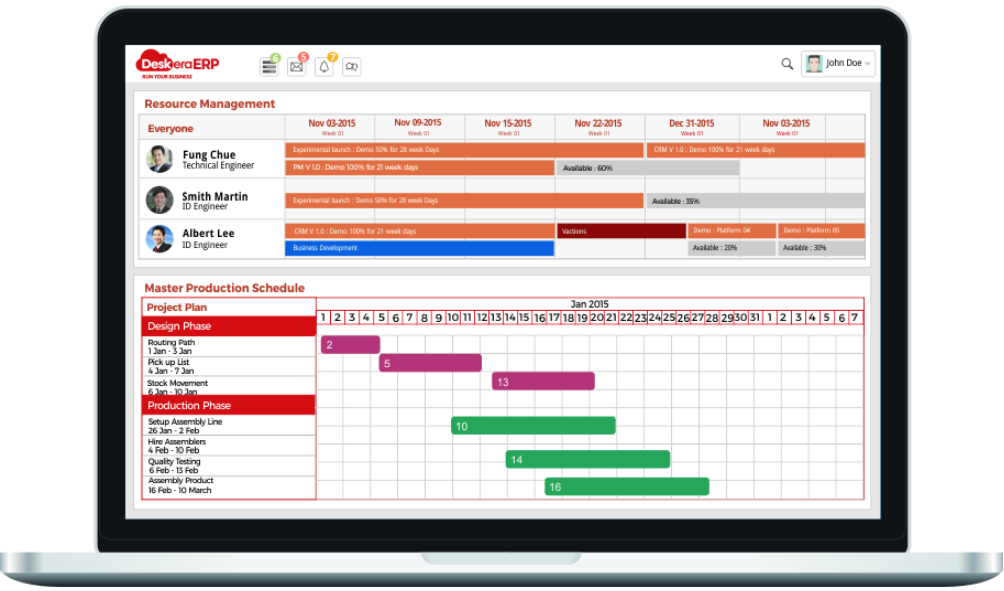
Deskera's integrated financial planning tools enable investors to better plan and track their investments. It can assist investors in making faster and more accurate decisions.
Deskera Books allows you to better manage your accounts and finances. Maintain good accounting practices by automating tasks like billing, invoicing, and payment processing.
Deskera CRM is a powerful solution that manages your sales and helps you close deals quickly. It not only enables you to perform critical tasks like lead generation via email, but it also gives you a comprehensive view of your sales funnel.
Deskera People is a straightforward tool for centralizing your human resource management functions.
Key Takeaways
- Plastics were first developed in the mid-19th century and have since become one of the most ubiquitous materials in modern society.
- The early years of plastics manufacturing were characterized by experimentation with different materials and production methods.
- The 20th century saw the development of many new types of plastics, including polyethylene, PVC, and polystyrene, which revolutionized the manufacturing industry.
- Plastics have many benefits, including durability, versatility, and low cost, but also have drawbacks, such as environmental impact and resource depletion.
- The plastics manufacturing industry is facing significant challenges related to sustainability, including plastic waste and pollution, resource depletion, and regulatory pressures.
- The industry has responded to these challenges with innovations in materials science, recycling technology, and production processes.
- Bioplastics, 3D printing, smart materials, and closed-loop recycling are all likely to become more widespread in the future.
- The development of new materials and production methods is likely to lead to more sustainable and eco-friendly plastics in the future.
- The industry is also likely to face continued pressure from regulators, consumers, and other stakeholders to reduce its environmental impact.
- The public perception of plastics is changing, with many consumers seeking out alternatives to traditional plastics and demanding more sustainable and eco-friendly materials.
- Plastics will continue to play an important role in modern society, but the industry will need to adapt to changing demands and find ways to reduce its environmental impact.
- By leveraging new technologies and adopting more sustainable practices, the plastics manufacturing industry can help to create a more sustainable and eco-friendly future.
Related Articles
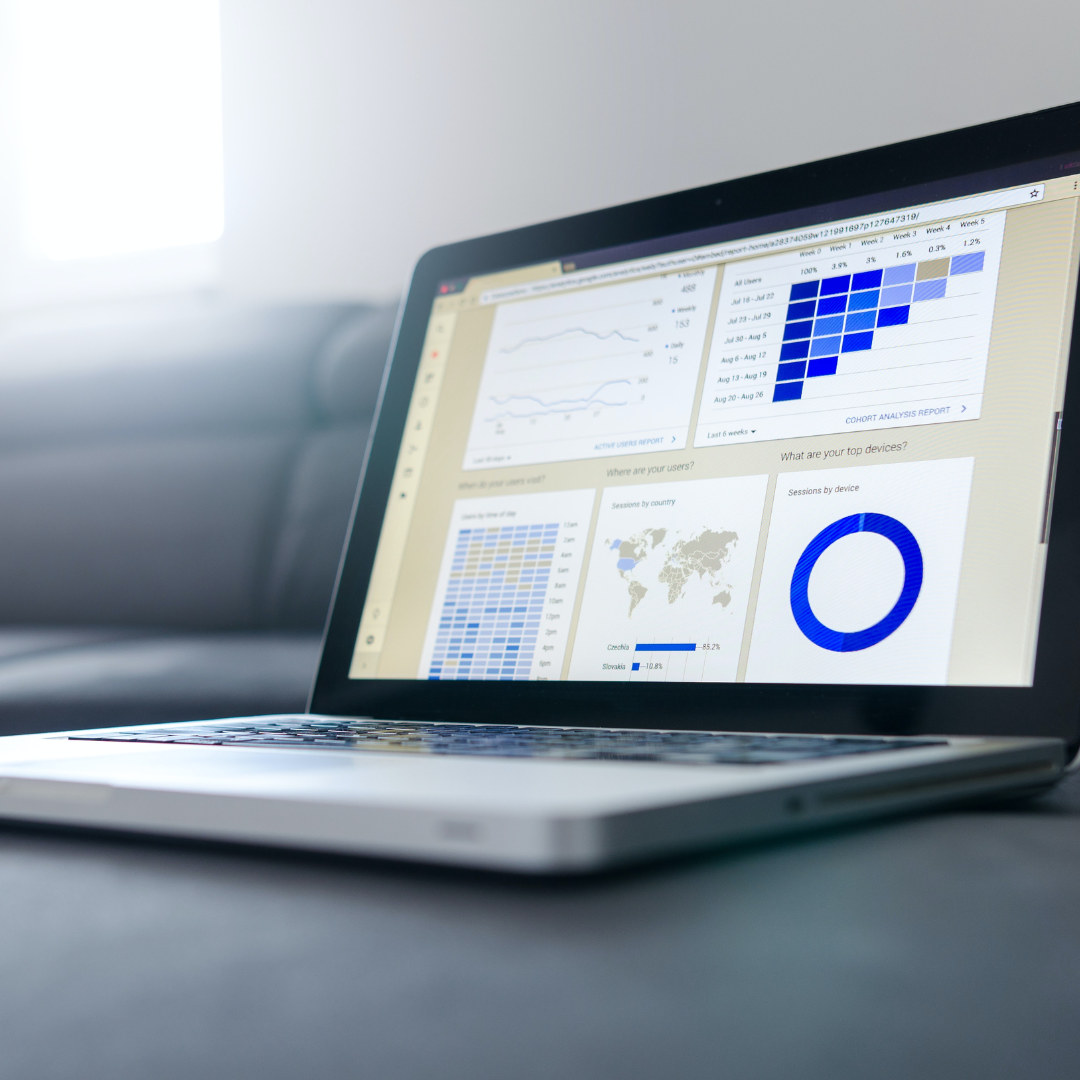
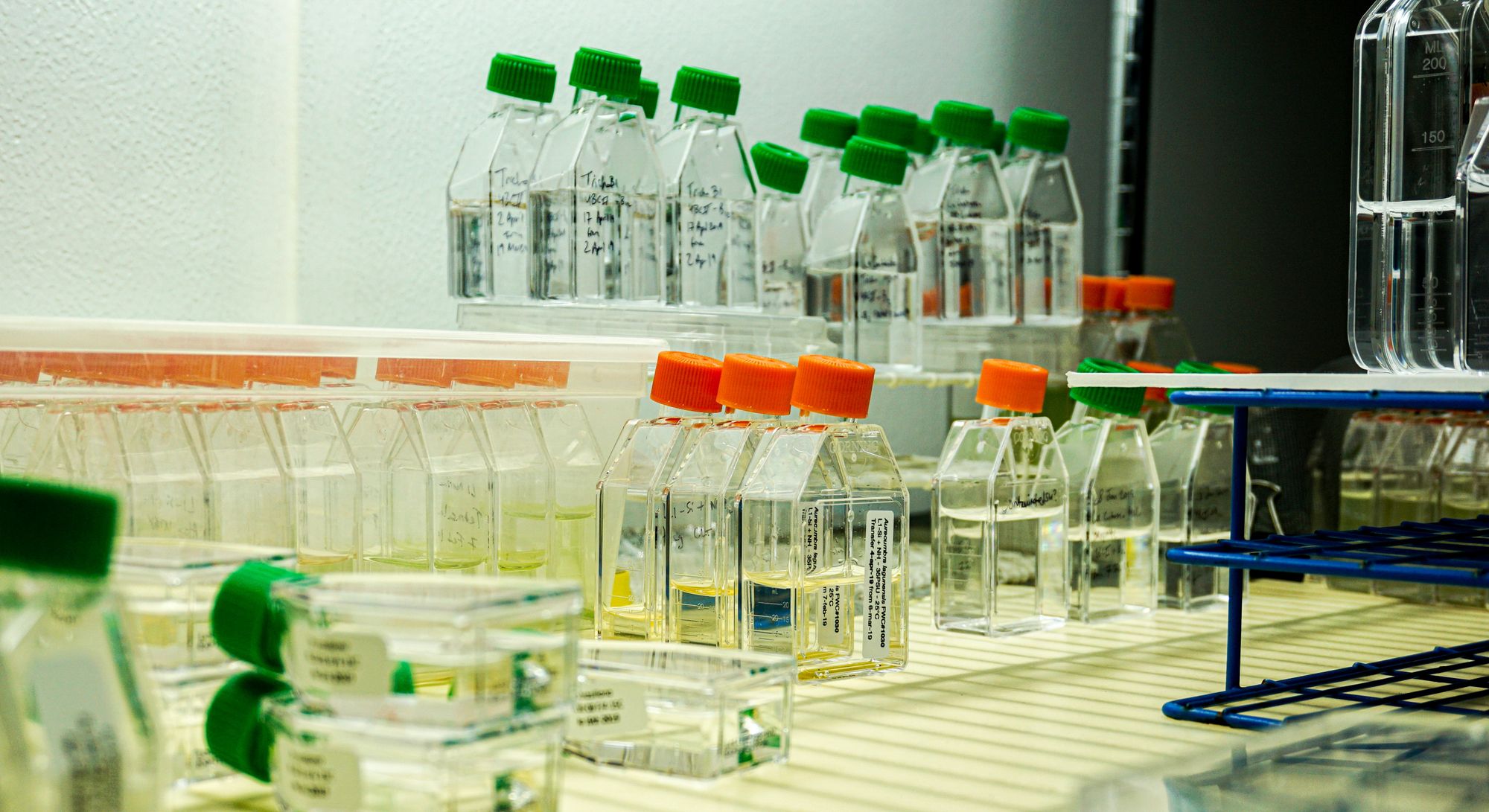
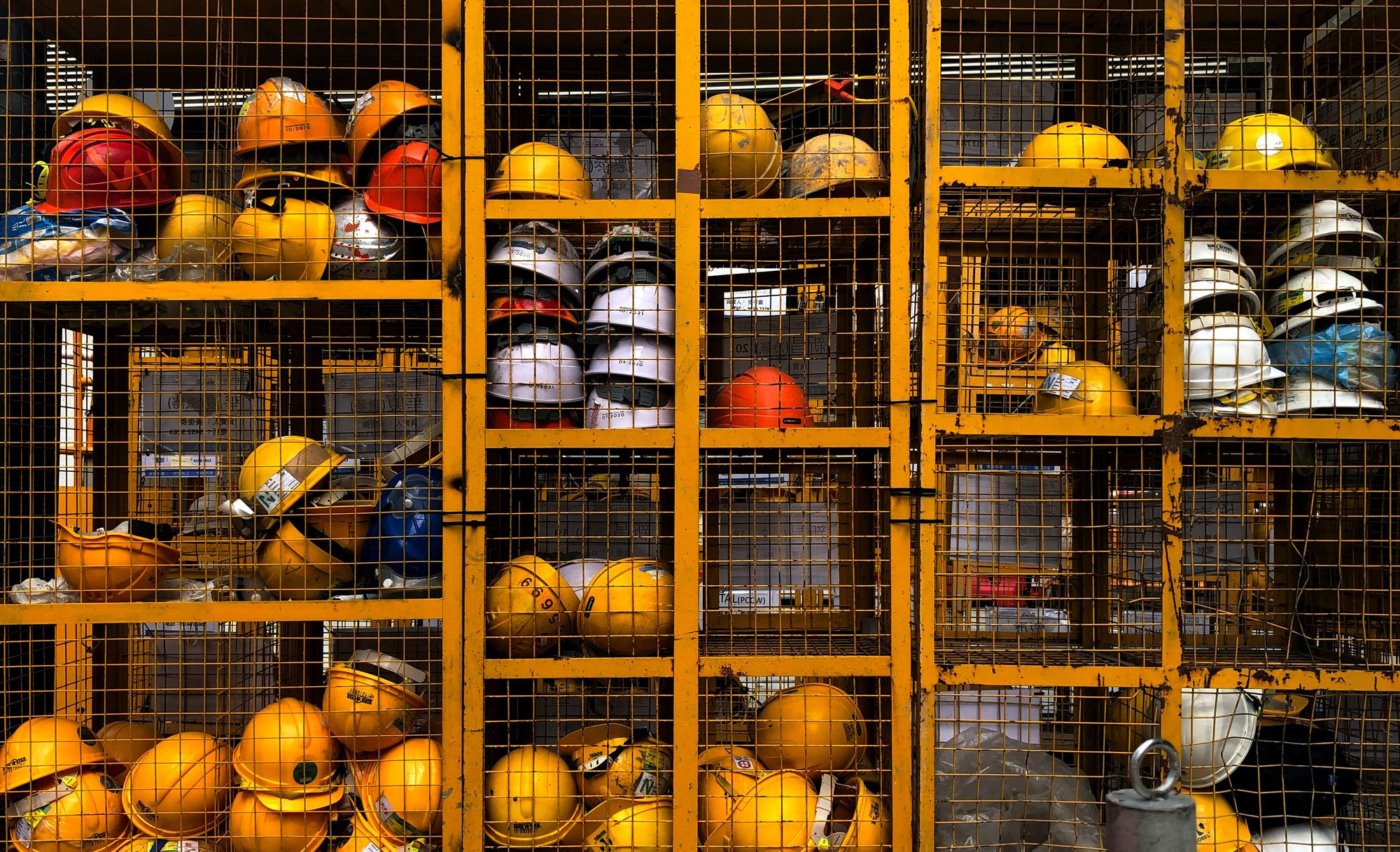
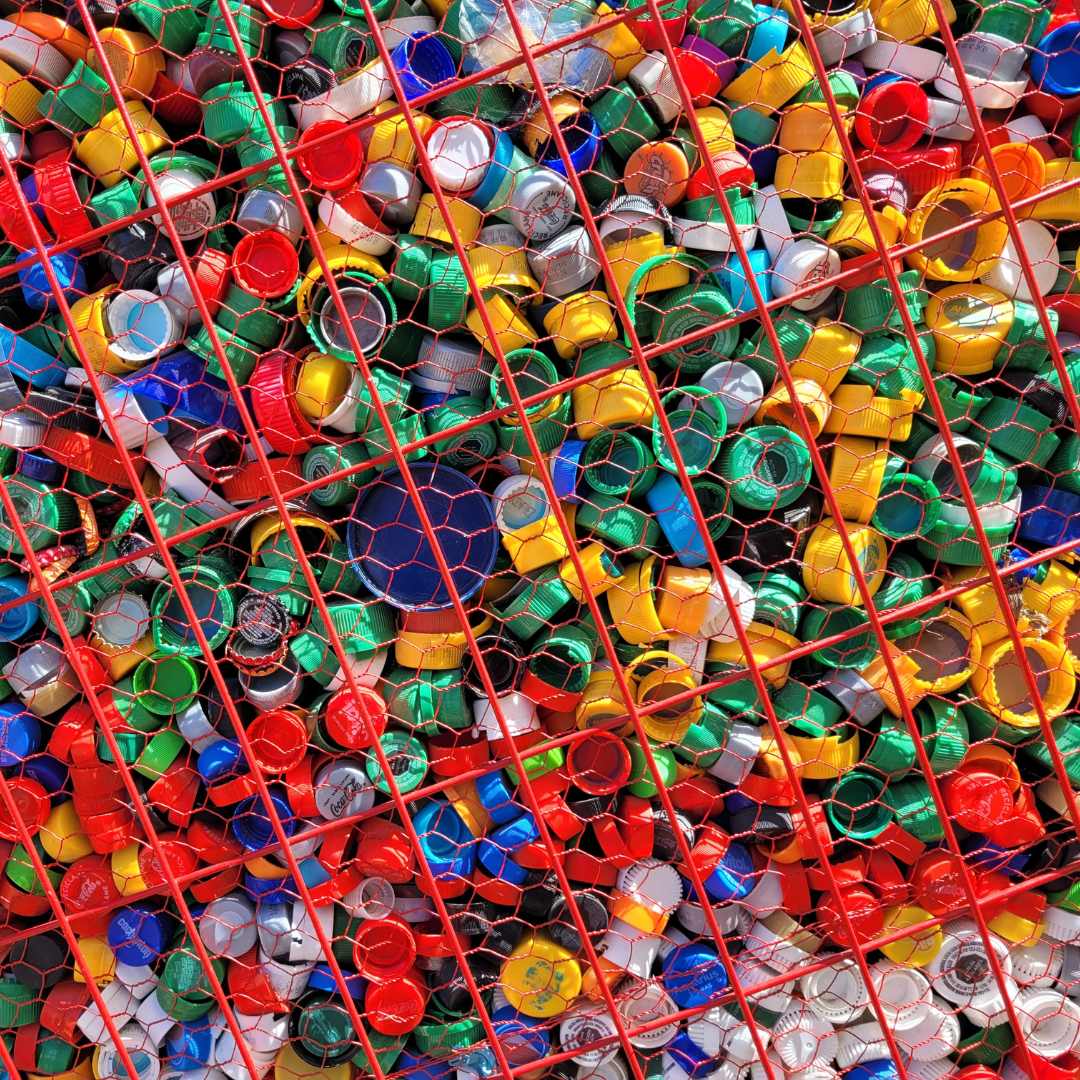