If you have been in business for a while, you may have an inventory problem. The constant stress of excess inventory can toll a small business owner's confidence and bank account.
Trying to figure out how much you need to order to keep your shelves stocked can be a headache. But the easiest way to solve this problem is by using the ending inventory formula.
The formula will help you determine how much to order to not overstock and lose money on inventory. It gives you the ability to decide whether or not you require additional inventory.
Here is an overview of the key points covered in the article:
1) What is an Ending Inventory Formula?
2) What is the significance of the Ending Inventory Formula?
3) How to calculate the Ending Inventory Formula?
4) Steps to calculate the Ending Inventory Formula
5) What are the factors that affect the Ending Inventory Formula?
6) Why should you calculate the Ending Inventory Formula?
What is an Ending Inventory Formula?
Ending inventory is the total value of all physical goods that are on hand at the end of an accounting period. The company must have purchased these goods during earlier periods, but they need not have been sold by the company yet.
Goods that are on hand but are not being used by the company (such as supplies or raw materials) are not considered part of the ending inventory. Goods held for sale to customers, whether or not those sales were recorded in previous periods, are typically included in the ending list.
The ending inventory figure is recorded under assets on a company's balance sheet. The value of this asset reflects the current cost of goods held for sale in future periods. This figure can fluctuate from period to period, depending on sales levels and changes in pricing policies during those periods.
The end-of-month inventory formula is a mathematical equation that involves various factors that affect the amount of inventory that needs to be ordered to maintain the correct stock level throughout the month. The formula calculates the percentage increase or decrease in demand and translates this into several units.
What is the significance of the Ending Inventory Formula?
To make a profit, wholesale and retail business owners need to sell their products for more than the item cost. The business owner will start with the inventory costs, subtract that number from their selling price, and that is what they need to sell at.
For example, if you bought an apple at $1 and sold it for $1.50, you made 50 cents profit. If you bought an apple at $1 and sold it for $0.50, you lost 50 cents.
Inventory costs are expressed in a company's accounting records as ledger accounts or book values. These values are based upon the original price of the items purchased but only reflect the amount paid for inventory at the time of purchase--it does not reflect any markups or additional costs.
The physical inventory count is done to determine the correct book value for each item in a company's inventory. A company must have an accurate physical count of all its inventory items to do this.
How to calculate the Ending Inventory Formula?
Ending inventory is finding the trend between beginning Inventory and ending inventory. Ending inventory is the current value of your goods while beginning inventory is the previous value of goods.
Trying to find a formula to calculate this? It's simple.
End inventory = Beginning Inventory + Purchases - Sales
But what if you want to predict the future stock based on other factors, like monthly sales or total profit? Try one of these formulas:
Ending inventory = Beginning Inventory + Monthly Sales/12-Month Average Monthly Sales + Profit/12-Month Average Profit
If you're trying to minimize your end inventory, you might use a formula like this:
Ending inventory = Beginning Inventory + Monthly Sales/2 × Average Monthly Sales - Profit/2 × Average Profit
The key here is to look for opportunities to minimize your ending inventory without sacrificing sales. Working backward from your end goal, these formulas can help you make intelligent decisions about when and how much to order or whether it's worth spending a bit extra to reduce your ending inventory by 10%.
Steps to calculate Ending Inventory Formula
Ending inventory is a calculation used to foresee changes in stock levels, allowing you to order new products before exhausting your current inventory. In the retail sector, it is often used in conjunction with reorder points – a stock level at which you should place an order to bring your stock levels back up to optimal levels.
Tally the cost of all items in stock (including the cost of all items on order). Subtract any returns (or discounts), and add markups from markdown costs. This gives you the total cost of goods available for sale.
Add 10% to this figure for safety, as no business can create 100% efficient processes.
Divide the result by your average daily sales over a set period (usually one month, three months, or one year). This will tell you how many days' worth of stock you have left.
Ending inventory can be calculated for any period but is most commonly done monthly in retail stores and restaurants. For a business that sells goods, it is essential to track the ending inventory because it represents goods that have been produced and are waiting to be sold.
An important factor in calculating ending inventory involves the cost of goods sold (COGS), which is calculated by taking sales less any discounts or trade allowances and adding any input costs incurred while producing the goods.
The opening inventory + purchases – ending inventory = COGS
This formula can be applied to determine COGS which helps calculate gross profit margin, which will help determine if a company needs additional capital or if they should begin production of different goods.
What are the factors that affect the Ending Inventory Formula?
Ending inventory is known in other terminology as ending goods, goods available for sale, and sales. An essential tool in all inventory management systems, ending inventory is necessary to determine net income and gross profit. Ending inventory can be calculated using the following formula:
Ending inventory = Beginning Inventory + Purchases - Sales
The following are the factors that affect the Ending Inventory Formula:
- Beginning Inventory - The number of goods or products a company or business has at the beginning of a period, such as an accounting cycle. This figure is found on the balance sheet in the asset section of long-term assets
- Purchases - The total cost of goods a company purchases during an accounting period such as a fiscal year or quarter. This figure is found on the income statement under expenses and includes both direct and indirect costs
- Sales - The amount of money collected from selling products or services during an accounting period. Sales are recorded on the income statement and do not include returns, allowances, discounts, or other deductions
Why should you calculate the Ending Inventory Formula?
One of the most challenging parts of forecasting is determining how much inventory you need for the future. There are so many variables involved in calculating the correct amount of inventory that it can be a real headache.
Trying to add up all your sales from now until the end of time can be overwhelming and time-consuming, but it doesn't have to be that way. A simple formula for ending inventory can help you figure out how much stock you will need at each stage of your business.
Establishing a formula for inventory tracking is an essential business practice that you need to get right. In the wrong hands, inventory tracking can be confusing and time-consuming. The best way to avoid this scenario is by setting up a simple inventory formula that is easy to understand and use. It is also essential to create an inventory formula that accurately reflects your business's needs.
The formula described below will provide the framework to effectively and efficiently track your inventory.
There are many times when you need to know how many units to order. You may be rolling over products as part of a continuous supply, or you may have a stock out of product. Whatever the reason, you must have a method in place to help you determine how much to order.
Ending inventory formula refers to a simple calculation used to ascertain the amount of a product that should remain in stock. There are several ways to calculate the ending inventory formula, and the one that works best depends on your specific situation.
How can Deskera help Improve Your Lead Time?
As a business owner, you can invest in Inventory and Accounting management tools like Deskera to help you manage and track your business cycle. A successful business needs an efficient operational cycle process that meets its specific needs. Deskera is an all-in-one software that can help you keep track of drop shipping, inventory and help you digitalize your business with the right tactics and management.
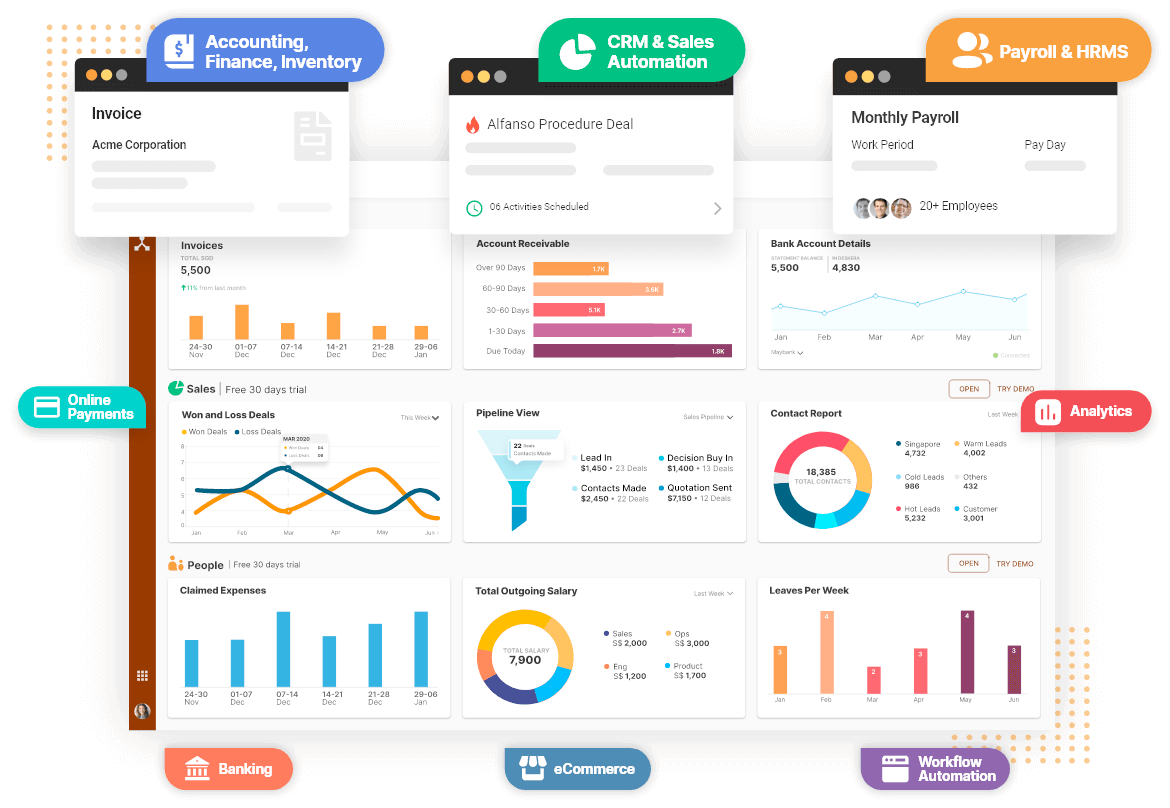
Deskera Books will make accounting faster, more efficient, and real-time. Deskera books will also ensure that your business follows the RITE framework of accounting, which will save it money. You can have access to Deskera's ready-made Profit and Loss Statement, Balance Sheet, and other financial reports instantly.
Deskera can help with your inventory management, customer relationship management, HR, attendance, and payroll management all on one platform.
Through Deskera CRM, the sales pipeline can also be designed, customized, and monitored. It will again give real-time feedback for the functions carried out and those forgotten. Email campaigns can also be automated through deskera.
Tasks like Invoice generation, invoice reminders, and integration of functions, inventory, tax calculations, and payments due and receivable can also be brought together in one place.
Deskera is hence your go-to solution for all your business financial reports and more. It will become your guide, mentor, and assistant to help you avoid mistakes and save you money.
Wrapping Up
The Ending Inventory Formula is an integral part of your inventory management system. This formula tells you how much inventory you need to order from suppliers, and it can be calculated in different ways depending on what you want to know.
Key Takeaways
- Knowing how much is ending is essential if you want to get the most out of your inventory. Calculating the Ending Inventory Formula will help you make better decisions regarding your inventory and can save you a lot of money in the long run.
- Treating your inventory as part of your "cash" will allow you to make more informed decisions about what products are worth carrying and which ones should be left on the shelf.
- There are some great benefits to calculating your Ending Inventory Formula, including:
– Saving money by knowing when to replenish inventory
– Better understanding of which items are most profitable
– Making better decisions about when to stock certain items or run special promotions
At Deskera, we know that the art of inventory management is more than just the process of how you manage your inventory. It also involves learning how, when, and where to buy it. One of the most common ways to keep track of your inventory is by using an inventory system, but you can also use a formula to calculate your ending inventory.
Related Articles
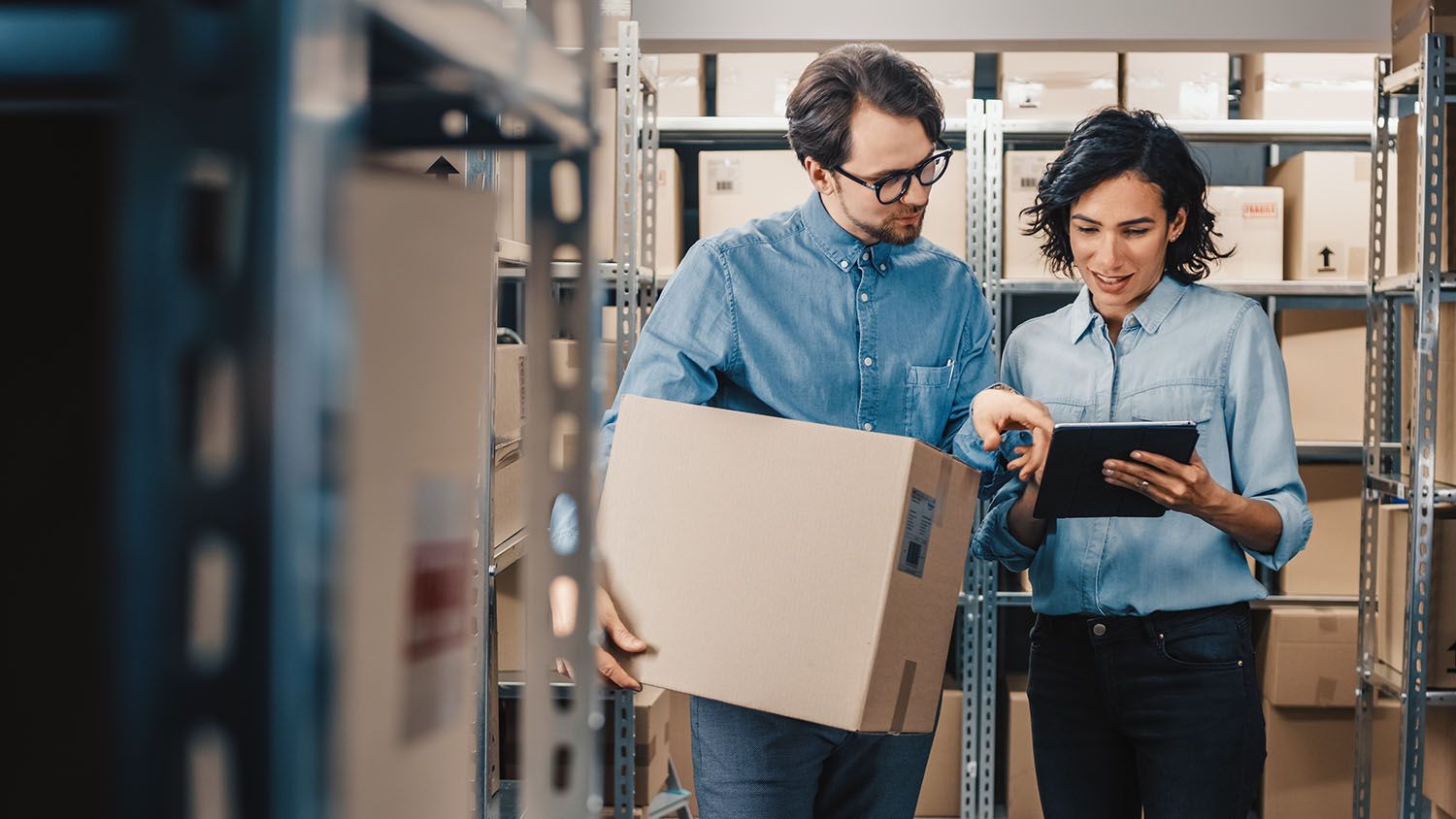
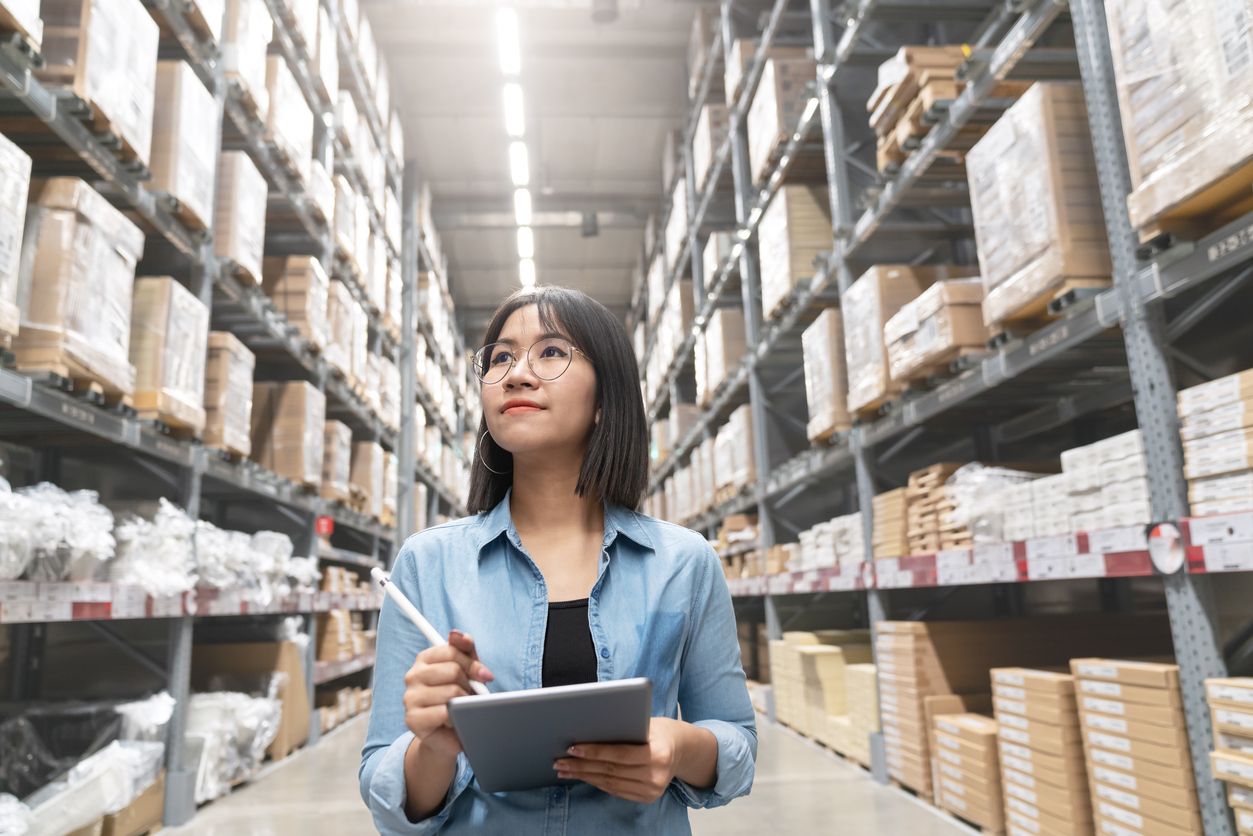
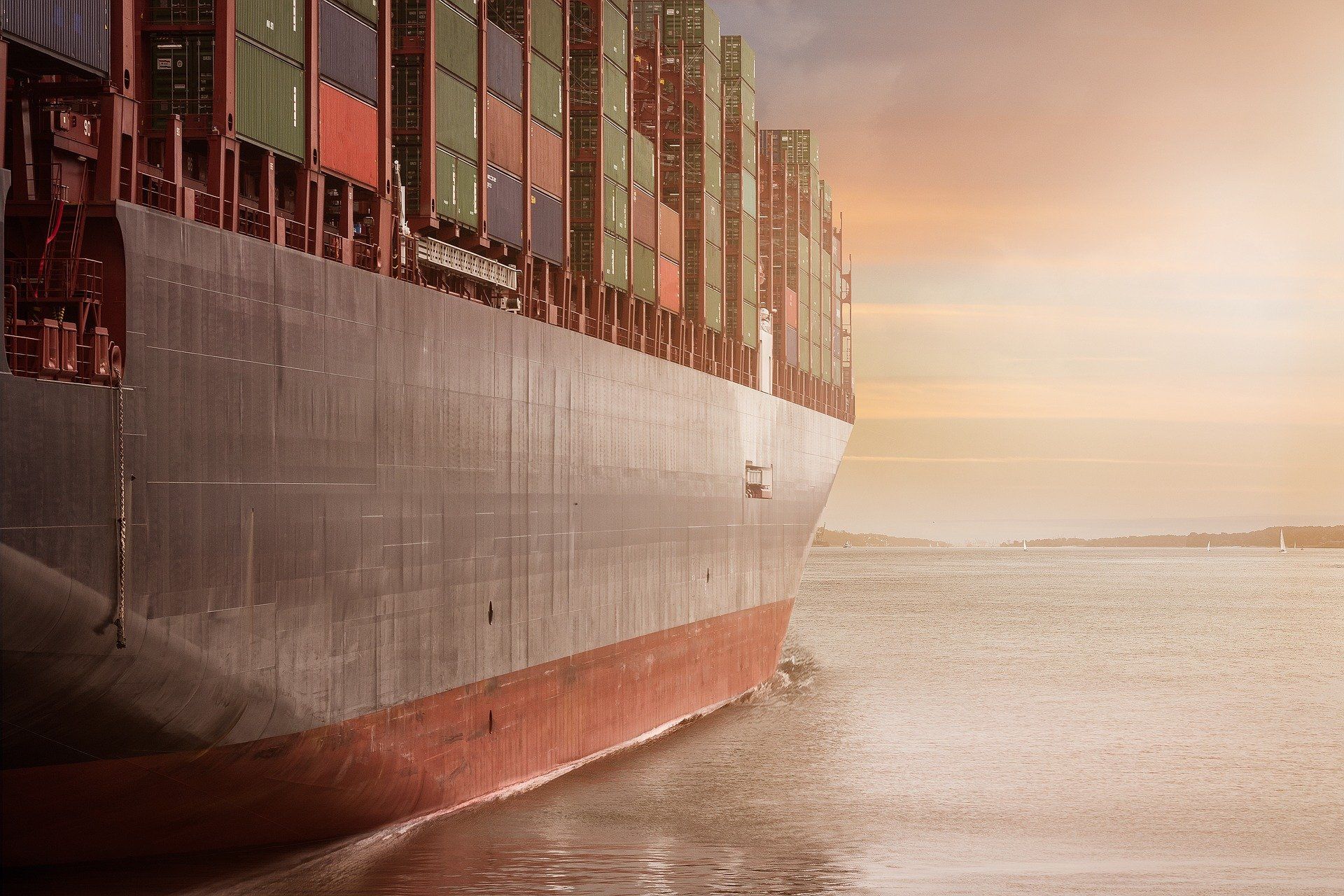
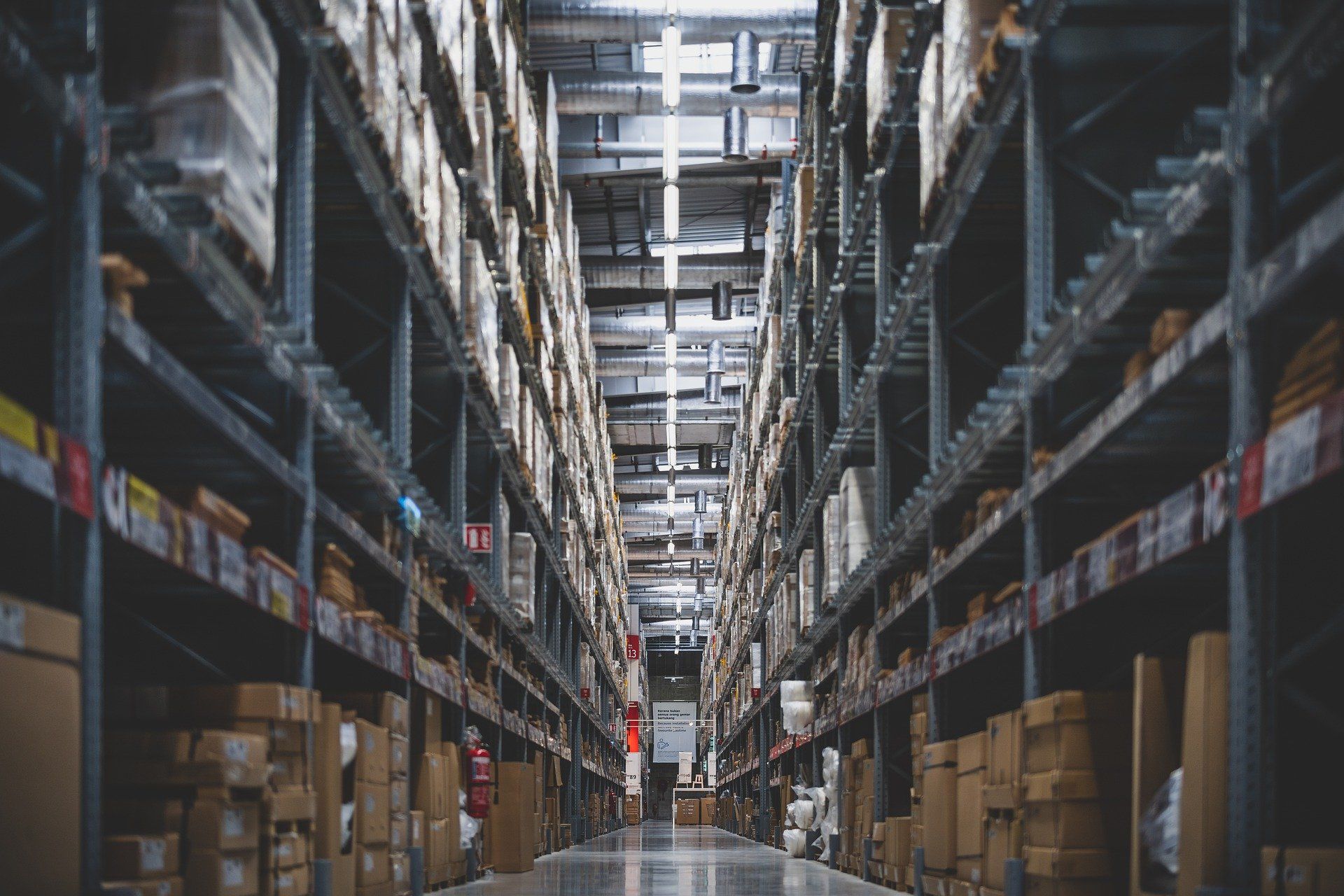