Digital twins have emerged as a powerful new tool in the world of chemical manufacturing, offering companies unprecedented insight into their operations and the ability to optimize processes in real time.
By creating virtual models of physical assets and processes, companies can simulate a wide range of scenarios, test new ideas, and predict outcomes with a high degree of accuracy.
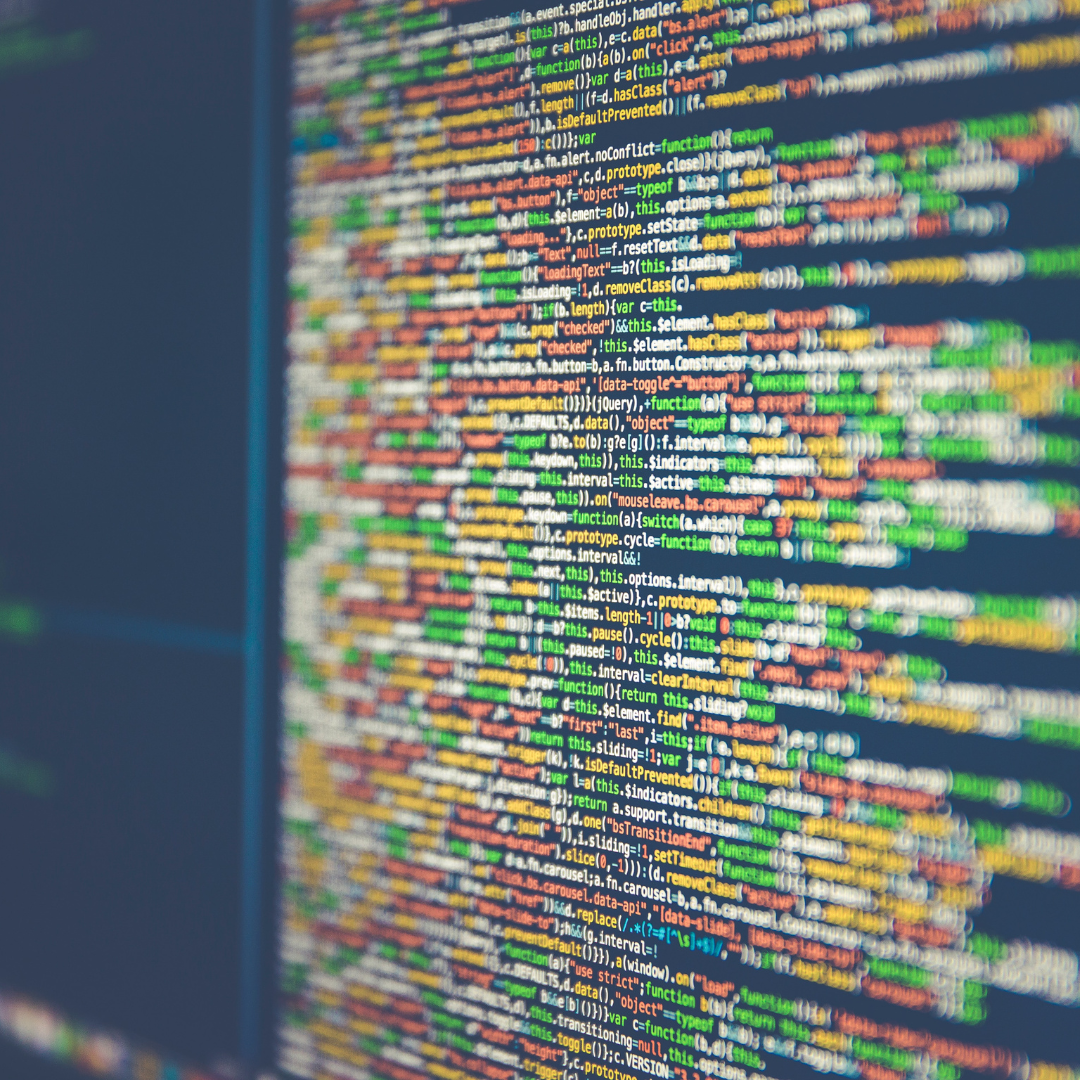
In this article, we will explore the role of digital twins in chemical manufacturing, including their benefits, applications, and the challenges companies may face when implementing them.
- What are Digital Twins?
- Types of Digital Twins
- How does a Digital Twin Work?
- Benefits of Digital Twins in Chemical Manufacturing
- Applications of Digital Twins in Chemical Manufacturing
- Challenges in Implementing Digital Twins
- Future Outlook
- Conclusion
- How can Deskera Help You?
- Key Takeaways
- Related Articles
What are Digital Twins?
Digital twins are virtual representations of physical assets, processes, and systems that are designed to simulate and predict real-world performance. Essentially, they are advanced digital models that are linked to real-world data, enabling companies to monitor, analyze, and optimize the performance of their physical assets in real time.
Digital twins use a wide range of technologies, including sensors, internet of things (IoT) devices, machine learning, and artificial intelligence (AI), to collect and process data from physical assets and generate insights that can be used to optimize performance.
By creating a digital twin, companies can run simulations, test new ideas, and predict outcomes with high accuracy, without the need for expensive and time-consuming physical testing.
One of the key benefits of digital twins is their ability to provide companies with real-time data and insights that can be used to improve performance, reduce downtime, and increase efficiency.
For example, in chemical manufacturing, digital twins can be used to simulate chemical processes, predict equipment failures, and optimize production schedules. Thereby, leading to increased safety, reduced costs, and improved product quality.
Digital twins can be applied to a wide range of industries, from manufacturing and energy to healthcare and transportation. They can be used to simulate everything from buildings and bridges to planes and cars and can help companies identify potential issues before they occur, leading to increased safety and reduced manufacturing costs.
Types of Digital Twins
A digital twin is a virtual representation of a physical system, process, or asset. There are different types of digital twins, depending on the level of detail, purpose, and complexity of the virtual model. Here are some of the most common types of digital twins:
- Physics-based digital twin: This type of digital twin is based on the physical properties, behavior, and interactions of the real-world system or asset. It uses mathematical models and simulations to replicate the physical system in a virtual environment, allowing for accurate predictions and analysis.
- Data-driven digital twin: This type of digital twin is based on data collected from sensors, IoT devices, and other sources. It uses machine learning algorithms and statistical models to analyze and interpret the data, identify patterns and trends, and predict future performance.
- Hybrid digital twin: This type of digital twin combines both physics-based and data-driven approaches to create a more comprehensive and accurate virtual model. It can provide a deeper understanding of the physical system by integrating real-time data with simulation models.
- Process digital twin: This type of digital twin models a specific process or workflow, such as a production line, supply chain, or customer journey. It can help identify bottlenecks, inefficiencies, and opportunities for improvement.
- System digital twin: This type of digital twin models a complex system or network of interconnected components, such as a smart city, a transportation system, or a power grid. It can help optimize the performance of the system, predict and prevent failures, and improve resource allocation.
- Product digital twin: This type of digital twin models a specific product, such as a car, a plane, or a building. It can be used for product design, testing, and optimization, as well as for maintenance and repair.
These are just some examples of the different types of digital twins that exist. Each type of digital twin has its own unique characteristics, benefits, and applications.
How does a Digital Twin Work?
A digital twin is a virtual replica of a physical system, process, or asset. It works by collecting data from sensors, IoT devices, and other sources, and using this data to create a model of the real-world system. The digital twin can then be used for analysis, optimization, and simulation, allowing for better understanding and control of the physical system.
Here's a basic overview of how a digital twin works:
Data Collection
The first step in creating a digital twin is to collect data from the physical system. This can include data from sensors, IoT devices, and other sources, such as production records, maintenance logs, and energy consumption data.
Data Processing
The collected data is then processed and analyzed to create a model of the physical system. This can involve using machine learning algorithms, statistical models, or other techniques to identify patterns and trends in the data.
Model Creation
Using the processed data, a model of the physical system is created. This model can be a simple representation of the system or a highly detailed replica that includes every component and interaction.
Simulation
Once the model is created, it can be used to simulate the behavior of the physical system under different conditions. This can include testing the impact of changes to the system, such as new equipment, processes, or layouts.
Analysis
The digital twin can be used to analyze the performance of the physical system and identify opportunities for optimization and improvement. This can include identifying inefficiencies, reducing downtime, and improving product quality.
Control
Finally, the digital twin can be used to control the physical system in a real-time model to make adjustments and optimize performance. This can involve using machine learning algorithms to automatically adjust system parameters or using a human operator to make manual adjustments.
Overall, a digital twin works by creating a virtual replica of a physical system, allowing for better understanding, control, and optimization of the system.
Benefits of Digital Twins in Chemical Manufacturing
Digital twins offer a range of benefits in the context of chemical manufacturing. Some of the key benefits include:
- Improved process efficiency: By creating a virtual model of a chemical process, companies can identify inefficiencies and bottlenecks in real-time and make adjustments to optimize performance. This can lead to increased efficiency, reduced waste, and improved throughput.
- Increased safety: Digital twins can be used to simulate and test chemical processes in a safe, controlled environment. This can help identify potential safety risks and hazards before they occur, leading to increased safety and reduced risk of accidents.
- Reduced downtime and maintenance costs: Digital twins can be used to predict equipment failures and maintenance needs, allowing companies to schedule maintenance and repairs in advance. This can reduce downtime and maintenance costs and prevent unexpected disruptions to production.
- Improved product quality: Digital twins can be used to optimize chemical processes and identify potential issues that could affect product quality. By identifying and addressing these issues in real time, companies can improve product quality and reduce the risk of product defects.
- Faster time to market: Digital twins can be used to test and optimize chemical processes before they are implemented in the real world. This can reduce the time and cost of product development and accelerate time to market.
Applications of Digital Twins in Chemical Manufacturing
Digital twins have a wide range of applications in chemical manufacturing. Here are some of the most common applications:
- Process optimization: Digital twins can be used to optimize chemical processes, identify inefficiencies, and improve overall performance. By creating a virtual model of a chemical process and simulating different scenarios, companies can identify the most efficient way to produce a product while minimizing waste and reducing costs.
- Equipment monitoring and maintenance: Digital twins can be used to monitor equipment in real-time and predict when maintenance is required. By identifying potential equipment failures in advance, companies can reduce downtime, prevent unexpected disruptions to production, and extend the lifespan of their equipment.
- Quality control: Digital twins can be used to monitor and optimize product quality. By simulating different scenarios and analyzing data in real-time, companies can identify potential issues that could affect product quality and take corrective action before they occur.
- Safety analysis: Digital twins can be used to simulate and test chemical processes in a safe, controlled environment. By identifying potential safety risks and hazards before they occur, companies can improve safety and reduce the risk of accidents.
- Supply chain optimization: Digital twins can be used to optimize the supply chain, identify potential bottlenecks, and improve overall efficiency. By creating a virtual model of the supply chain, companies can identify areas for improvement and implement changes to reduce costs and improve delivery times.
Industrial Application of Digital Twins
This section lists some industries that rely on digital twins for their effective operations:
Healthcare and Medical Services Sector
Patients receiving healthcare services, like products, can be profiled using digital twins. The same sensor-generated data system can be used to track a wide range of health indicators and generate key insights. Thus, the healthcare sector utilizes the concept of digital twins for the overall betterment of services.
Automobile Industry
Cars are many different types of complex, co-existing systems, and digital twins are widely used in the auto design and automobile industry to improve vehicle performance and increase production efficiency.
Power-generation equipment
The use of digital twins is extremely advantageous for large engines, such as jet engines, locomotive engines, and power-generation turbines, particularly for assisting in determining timeframes for routine maintenance. In other words, we can summarize that digital twins play a significant role in energy sector.
Challenges in Implementing Digital Twins in Chemical Manufacturing
Implementing digital twins in chemical manufacturing can present a number of challenges. Here are some of the most common challenges:
- Data integration: Creating an accurate digital twin requires a large amount of data from a variety of sources. Integrating this data can be a complex and time-consuming process, and ensuring the data is accurate and up-to-date can be a challenge.
- Cost: Implementing a digital twin can require significant investment in hardware, software, and personnel. This can be a significant barrier to adoption, especially for smaller companies.
- Cybersecurity: As with any digital system, there is a risk of cyber-attacks and data breaches. Ensuring the security of a digital twin and the data it contains is essential, but can be a complex and ongoing challenge.
- Complexity: Digital twins can be complex systems with many interdependent variables. Ensuring the accuracy and reliability of the digital twin can be a challenge, and any errors or inaccuracies can have significant impacts on the real-world process.
- Integration with existing systems: Integrating a digital twin with existing process control systems and other software can be a challenge. Ensuring that the digital twin is compatible with existing systems and does not disrupt ongoing operations is essential.
- Skilled personnel: Creating and maintaining a digital twin requires a team of skilled personnel with expertise in data analytics, software development, and chemical engineering. Finding and retaining this talent can be a challenge, especially in regions with a shortage of qualified personnel.
Overall, implementing a digital twin in chemical manufacturing can be a complex and challenging process, but the benefits can be significant in terms of process optimization, safety, and product lifecycle. Companies must carefully consider these challenges and develop a comprehensive plan for implementing a digital twin that addresses these challenges to ensure a successful implementation.
Future Outlook
The future outlook for digital twins in chemical manufacturing is positive, as technology is expected to play an increasingly important role in the industry in the years to come. Here are some of the key trends and developments that are expected to shape the future of digital twins in chemical manufacturing:
- Greater integration: Digital twins are expected to become increasingly integrated with other technologies, such as artificial intelligence and machine learning. This integration will enable even greater levels of optimization and automation in chemical manufacturing processes.
- Increased use in research and development: Digital twins are expected to be used more extensively in the research and development of new chemicals and materials. By simulating the behavior of new products in a digital twin, researchers can test their properties and performance before producing physical prototypes.
- Expansion of use cases: As the technology becomes more widely adopted, digital twins are expected to be used in a wider range of use cases beyond process optimization. For example, they may be used for predictive maintenance, supply chain optimization, and safety analysis.
- Improved accuracy: Advances in data analytics and modeling are expected to lead to even more accurate digital twins. This will enable better prediction of process behavior and more precise optimization of operations.
- Increased adoption: As the benefits of digital twins become more widely recognized, it is expected that adoption will continue to increase across the chemical manufacturing industry. This will be driven by a combination of factors, including cost savings, increased efficiency, and improved product quality.
Conclusion
In conclusion, digital twins offer a promising solution to enhance the efficiency, safety, and sustainability of chemical manufacturing. By creating a digital replica of physical assets, digital twins provide real-time data analytics and predictive insights that enable manufacturers to optimize their operations, reduce downtime, and improve product quality.
Additionally, digital twins enable manufacturers to simulate and test different scenarios and potential outcomes, thereby reducing risks and costs associated with physical experimentation.
With the increasing adoption of Industry 4.0 technologies and the ongoing digital transformation of the chemical manufacturing industry, digital twins are set to play an even greater role in shaping the future of this critical sector.
How can Deskera Help You?
Deskera's integrated financial planning tools allow investors to better plan their investments and track their progress. It can help investors make decisions faster and more accurately.
Deskera MRP allows you to monitor the manufacturing process in real time. From the bill of materials to the production planning features, the solution helps you stay on top of your game and maintain your company's competitive edge.
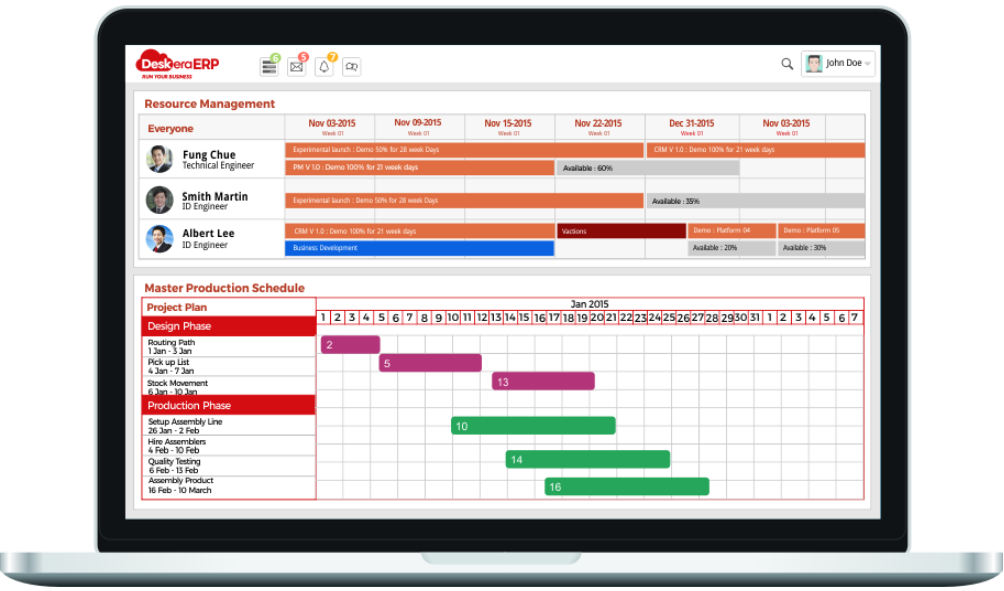
Deskera Books can assist you in automating your accounting and mitigating business risks. Deskera makes it easier to create invoices by automating many other procedures, reducing your team's administrative workload.
Deskera also offers a suite of integrated applications to help businesses manage their financials, inventory, and operations. Furthermore, other business aspects such as HR (Deskera People), CRM (Deskera CRM), and Deskera ERP are provided by Deskera. These could be crucial and can help short sellers keep track of their businesses and make better decisions.
Key Takeaways
- Digital twins are virtual representations of physical assets, processes, and systems that are designed to simulate and predict real-world performance.
- Essentially, they are advanced digital models that are linked to real-world data, enabling companies to monitor, analyze, and optimize the performance of their physical assets in real time.
- Better safety, increased efficiency, and product quality are some of the benefits of utilizing digital twins in chemical manufacturing.
- It finds application in quality control, process optimization, and equipment monitoring.
- Data integration, cost, cybersecurity, and the requirement of skilled personnel are some of the challenges in implementing digital twins.
Related Articles
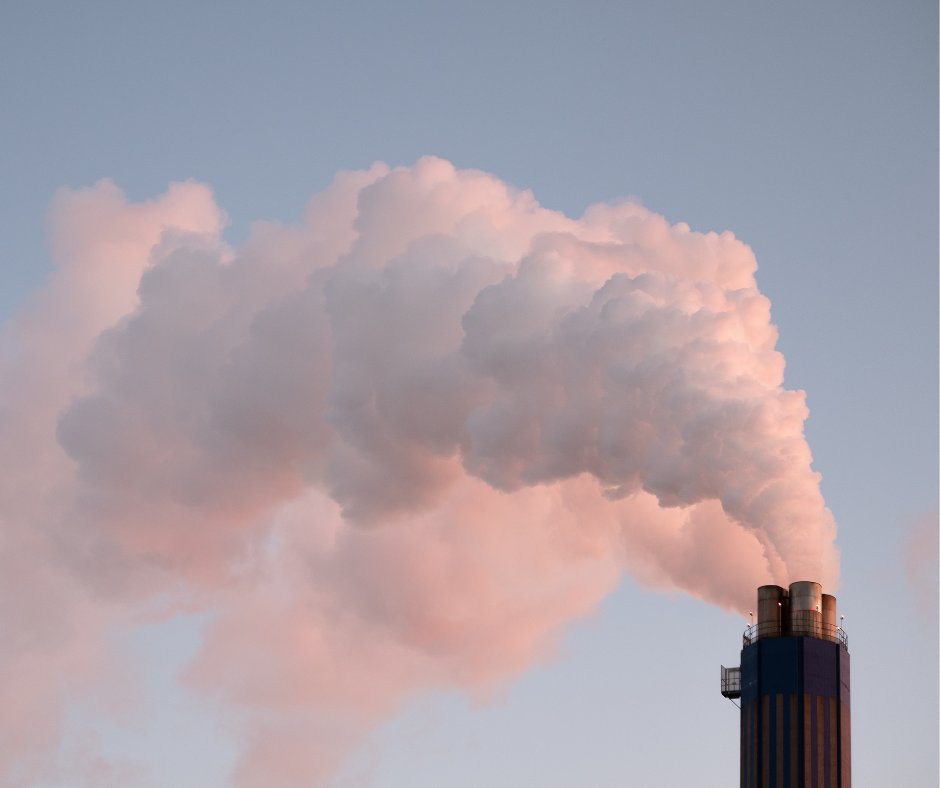
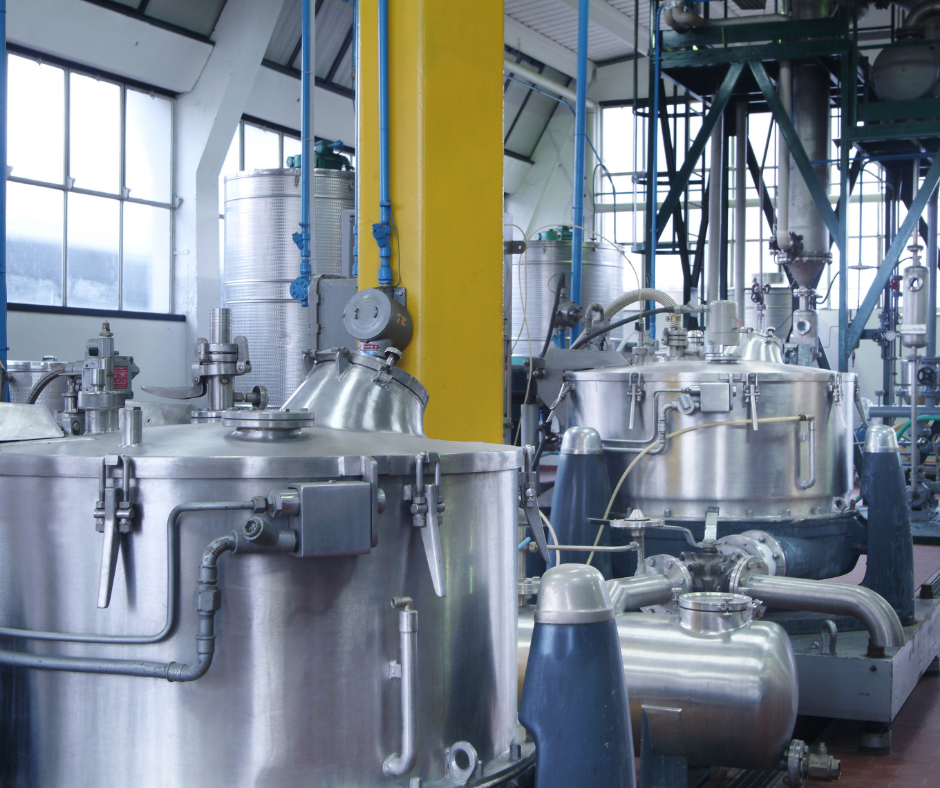
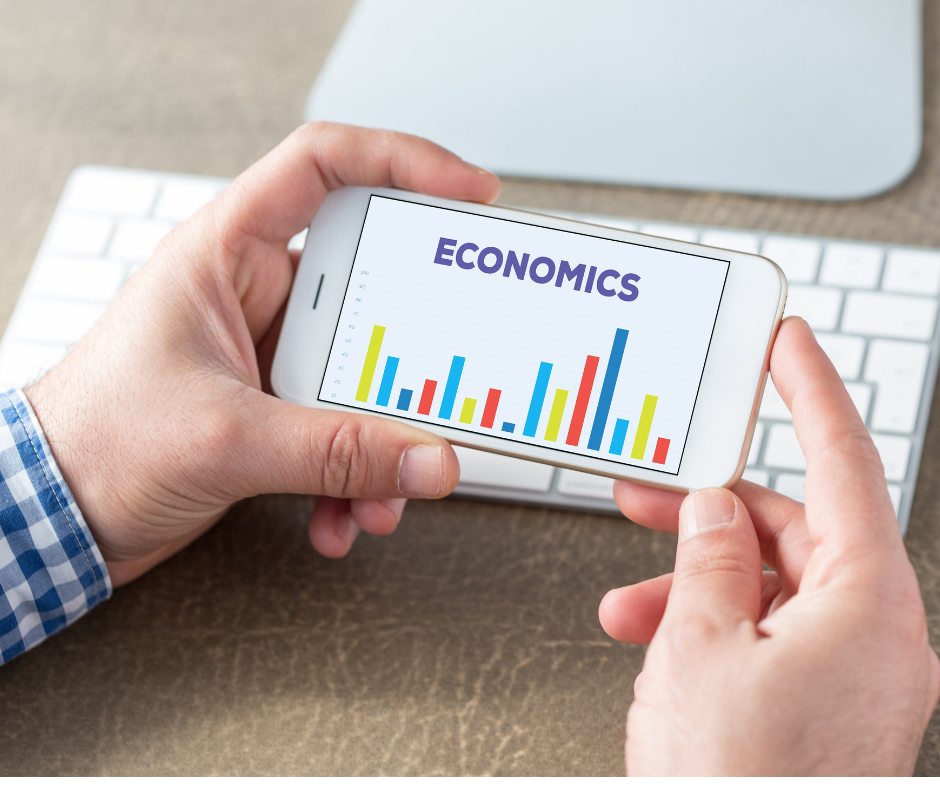