Wood manufacturing is a complex process that involves various stages of processing, from cutting to finishing. In the production of wood products, quality control is a crucial aspect that ensures that the end product meets the desired specifications. Quality control is the process of verifying that the final product meets the required standards, and it plays a crucial role in wood manufacturing.
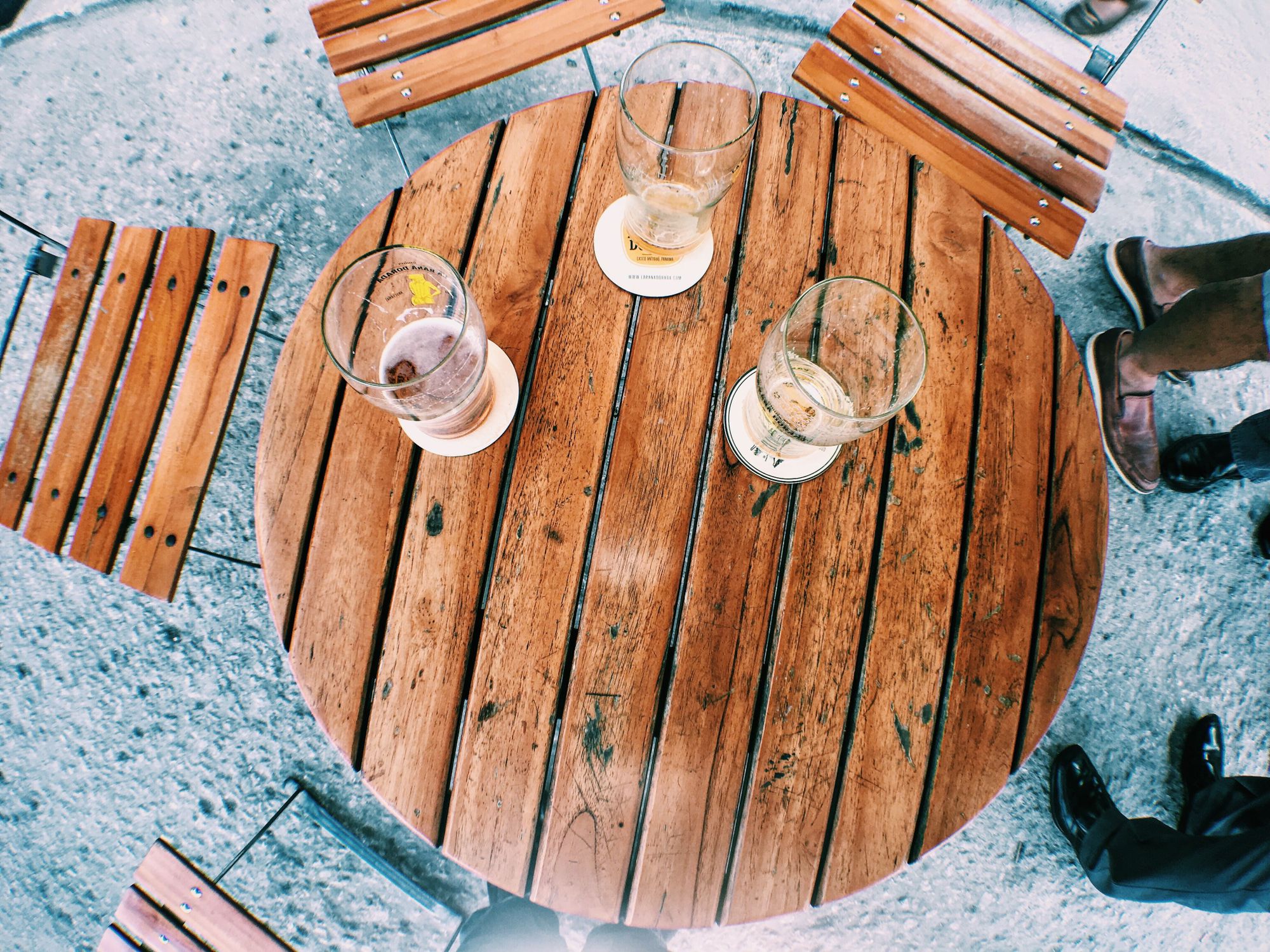
This article covers the following:
- The Importance of Quality Control in Wood Manufacturing
- Key Elements of Wood Manufacturing Quality Control
- Types of Defects in Wood Manufacturing and How to Prevent Them
- Tools and Techniques for Wood Manufacturing Quality Control
- Implementing a Quality Control Program in Your Wood Manufacturing Business
- Benefits of Implementing Quality Control in Wood Manufacturing
- Tips for Effective Wood Manufacturing Quality Control
- Common Challenges in Wood Manufacturing Quality Control and How to Overcome Them
- Quality Control Standards and Regulations for Wood Manufacturing
- Role of Training and Education in Wood Manufacturing Quality Control
- How Can Deskera Assist you?
The Importance of Quality Control in Wood Manufacturing
Wood manufacturing is an essential industry that produces a wide range of products, including furniture, construction materials, paper, and many others. In any wood manufacturing process, quality control plays a critical role in ensuring that the finished product meets the desired standards of performance, safety, and aesthetic appeal.
In this blog, we will explore the importance of quality control in wood manufacturing and how it can help businesses produce high-quality wood products that meet the expectations of their customers.
Consistency in Product Quality
One of the most significant advantages of implementing quality control in wood manufacturing is ensuring that the product quality remains consistent. Quality control helps to identify defects and inconsistencies in the wood materials used in the manufacturing process, as well as any issues that arise during the production process.
By identifying these issues early on, manufacturers can take corrective action to maintain product quality and consistency throughout the manufacturing process.
Reduced Waste
Implementing quality control measures in wood manufacturing can also help reduce waste by ensuring that the wood products produced meet the required standards.
Poor quality products are often rejected by customers, leading to the wastage of resources and increasing production costs. Quality control can help to minimize this wastage by identifying defects early on in the production process, reducing the number of defective products produced.
Improved Customer Satisfaction
Customer satisfaction is an essential factor in any business, and wood manufacturing is no exception. Quality control helps to ensure that the wood products produced are of high quality and meet the customers' expectations. High-quality wood products not only look better, but they also perform better and have a longer lifespan, leading to greater customer satisfaction and loyalty.
Enhanced Safety
Quality control also plays a crucial role in ensuring that wood products meet safety standards. Wood products that do not meet safety standards can pose a risk to the users, leading to accidents and injuries.
By implementing quality control measures, manufacturers can ensure that their products meet the required safety standards, reducing the risk of accidents and injuries.
Compliance with Regulations
Wood manufacturing is subject to various regulations and standards, including environmental regulations, safety standards, and product quality standards. By implementing quality control measures, manufacturers can ensure that their products comply with these regulations, avoiding any legal or financial penalties associated with non-compliance.
In conclusion, quality control is an essential aspect of wood manufacturing that helps to ensure that the products produced are of high quality and meet the required standards.
By implementing quality control measures, manufacturers can reduce waste, improve customer satisfaction, enhance safety, and comply with regulations. These benefits can help businesses improve their bottom line, build their reputation, and stay competitive in the wood manufacturing industry.
Key Elements of Wood Manufacturing Quality Control
Wood, manufacturing quality control, is a critical aspect of the wood industry. It ensures that wood products are manufactured to meet the required specifications and standards.
Quality control is necessary to maintain the reputation of the manufacturer and to provide customers with products that are safe, durable, and of high quality. In this blog, we will discuss the key elements of wood manufacturing quality control.
Raw Material Inspection
The first key element of wood manufacturing quality control is raw material inspection. This involves checking the wood logs or boards for defects, such as cracks, knots, and insect damage. A raw material inspection ensures that the wood is of good quality and suitable for the manufacturing process.
Moisture Content Control
Wood is a hygroscopic material, which means it absorbs and releases moisture depending on the surrounding environment. Moisture content control is crucial in wood manufacturing as it affects the quality of the final product.
Excess moisture can cause warping, cracking, and decay, while insufficient moisture can result in brittle wood. Therefore, wood manufacturers must control the moisture content of the wood throughout the manufacturing process.
Quality Control at Each Manufacturing Stage
Quality control should be performed at each manufacturing stage, from sawing and planing to sanding and finishing. The wood products should be checked for defects such as rough surfaces, improper sizing, and other issues that can affect the quality of the final product.
Equipment Maintenance
Equipment maintenance is a critical aspect of wood manufacturing quality control. Regular maintenance and calibration of equipment, such as saws and sanders, ensure that they are working correctly and producing products of consistent quality.
Testing and Certification
Wood manufacturers must conduct testing and certification to ensure that their products meet the required standards and specifications. Certification helps to build customer trust and ensures that the wood products are safe and durable.
Continuous Improvement
Continuous improvement is the final key element of wood manufacturing quality control. Wood manufacturers should continuously evaluate and improve their manufacturing processes to enhance the quality of their products.
This involves reviewing customer feedback, identifying areas of improvement, and implementing changes to improve the overall quality of the wood products. In conclusion, wood manufacturing quality control is a crucial aspect of the wood industry.
Raw material inspection, moisture content control, quality control at each manufacturing stage, equipment maintenance, testing and certification, and continuous improvement are the key elements of wood manufacturing quality control. By following these elements, wood manufacturers can ensure that their products are of high quality and meet the required standards and specifications.
Types of Defects in Wood Manufacturing and How to Prevent Them?
Wood is one of the most widely used materials in manufacturing. It is strong, durable, and versatile, making it ideal for a variety of applications. However, like any material, wood is not perfect, and defects can occur during the manufacturing process.
These defects can lead to weaker products and lower quality, which is why it is important to identify and prevent them. In this blog, we will explore the different types of defects in wood manufacturing and how to prevent them.
Types of Defects in Wood Manufacturing
Knots: Knots are areas in the wood where a branch grows. These can weaken the wood and cause it to split or break. Knots can also affect the appearance of the finished product, making it less attractive.
Checks and Splits: These are cracks that occur in the wood due to uneven drying or changes in moisture content. They can weaken the wood and reduce its strength.
Warping and Twisting: Warping and twisting occur when the wood is not dried or stored properly. This can lead to a finished product that is not flat or straight, making it less usable.
Grain Defects: Grain defects occur when the wood is cut improperly or when the growth rings are not aligned. This can result in a weaker product or one that is less attractive.
Decay and Insects: Decay, and insect damage can occur when the wood is not properly treated or stored. This can weaken the wood and make it less durable.
How to Prevent Defects in Wood Manufacturing?
Proper Drying: Proper drying is essential to prevent warping, twisting, and cracking in the wood. This can be achieved by storing the wood in a dry, well-ventilated area and monitoring its moisture content regularly.
Sorting and Grading: Sorting and grading the wood can help to identify defects and ensure that only high-quality wood is used in the manufacturing process.
Cutting and Milling: Proper cutting and milling techniques can help to prevent grain defects and ensure that the wood is cut to the correct dimensions.
Treating and Finishing: Treating the wood with preservatives can help to prevent decay and insect damage. Finishing the wood with a protective coating can also help to prevent defects and improve its appearance.
Quality Control: Regular quality control checks can help to identify defects and ensure that only high-quality products are being manufactured.
Defects in wood manufacturing can lead to weaker products and lower quality. By understanding the different types of defects and how to prevent them, manufacturers can produce high-quality wood products that are durable and attractive.
Proper drying, sorting and grading, cutting and milling, treating and finishing, and quality control are all essential to prevent defects in wood manufacturing.
Tools and Techniques for Wood Manufacturing Quality Control
Wood manufacturing is an intricate process that involves numerous steps and stages. The end product is a thing of beauty, but it also needs to be durable and functional.
As such, it is imperative to have a robust quality control process in place to ensure that the final product meets the desired standards. In this blog, we will explore the tools and techniques used in wood manufacturing quality control.
Moisture meters
Wood is an organic material that absorbs and releases moisture depending on the environment. The ideal moisture content for wood used in furniture manufacturing is between 6% to 8%.
If the moisture content is too high or too low, it can cause warping, cracking, or splitting. Moisture meters are used to measure the moisture content in the wood and ensure it is within the acceptable range.
Calipers
Calipers are essential tools in wood manufacturing quality control. They are used to measure the thickness, width, and length of the wood. The measurements obtained are then compared with the required specifications to ensure that the wood is cut to the correct dimensions.
Microscopes
Microscopes are used to inspect the wood's surface for any defects or imperfections. They magnify the surface and allow inspectors to detect even the smallest of flaws. This is especially important when it comes to high-end furniture manufacturing, where the smallest blemish can ruin the overall look of the product.
Tensile strength testing machines
Tensile strength testing machines are used to test the strength of the wood. They exert force on the wood until it breaks, and the force required to break it is measured. This is important because the strength of the wood determines how much weight it can support and how durable it is.
Surface hardness testers
Surface hardness testers are used to determine the hardness of the wood's surface. This is important because the surface needs to be able to withstand wear and tear, and the harder the surface, the more durable it is.
Spectrophotometers
Spectrophotometers are used to measure the color of the wood. They are particularly useful when it comes to matching the color of different wood pieces or matching the wood to a specific color scheme.
- X-ray machines: X-ray machines are used to inspect the wood's internal structure. This is particularly useful in detecting defects that may not be visible to the naked eye, such as knots or insect damage.
- Ultrasonic machines: Ultrasonic machines are used to inspect the wood's internal structure for any defects. They use sound waves to detect any changes in the wood's density and can detect defects that may not be visible to the naked eye.
- Visual inspection: Visual inspection is perhaps the most important tool in wood manufacturing quality control. It involves a trained inspector examining the wood for any defects, such as cracks, knots, or warping. The inspector uses a combination of their expertise and the tools mentioned above to ensure that the wood meets the desired standards.
The tools and techniques used in wood manufacturing quality control are crucial in ensuring that the end product meets the desired standards. From moisture meters to visual inspection, each tool plays a vital role in detecting defects and ensuring that the wood is of the highest quality. As such, wood manufacturers should invest in these tools and techniques to ensure that their products are durable, functional, and aesthetically pleasing.
Implementing a Quality Control Program in Your Wood Manufacturing Business
As a wood manufacturing business owner, you know that quality control is essential for the success of your business. A quality control program is a systematic approach to ensuring that your products meet the desired level of quality, which ultimately improves customer satisfaction and increases your profits. In this blog, we will discuss the steps you can take to implement a quality control program in your wood manufacturing business.
Step 1: Set Quality Standards
The first step in implementing a quality control program is to set quality standards. This involves defining the quality criteria for your products and establishing acceptable tolerances.
Quality standards can include dimensions, strength, durability, finish, and any other relevant features that are important to your customers. Setting clear quality standards will help you to identify defects early and take corrective actions before the products reach your customers.
Step 2: Develop a Quality Control Plan
Once you have established quality standards, you need to develop a quality control plan that outlines the steps you will take to ensure that your products meet those standards. Your quality control plan should include the following:
- Inspection and testing procedures
- Sampling methods
- Acceptance criteria
- Training requirements for quality control personnel
- Corrective action procedures
Your quality control plan should be well-documented, and all employees should be trained on the procedures and their roles in the quality control process.
Step 3: Implement the Quality Control Program
With quality standards and a quality control plan in place, it's time to implement the program. This involves establishing a quality control team, which can include a quality control manager, inspectors, and testers. The team should be responsible for inspecting and testing products at various stages of production to ensure that they meet the established quality standards. The team should also document any defects found and take corrective actions as necessary.
Step 4: Monitor and Evaluate the Quality Control Program
To ensure that your quality control program is effective, you need to monitor and evaluate its performance regularly. This involves analyzing quality control data to identify any trends or patterns in defects, as well as conducting regular audits of the program to ensure that it is being followed correctly. Based on the results of these evaluations, you can make any necessary adjustments to the program to improve its effectiveness.
Step 5: Continuously Improve the Quality Control Program
Finally, a quality control program is never complete. You should continuously review and improve the program to ensure that it remains effective and meets the changing needs of your customers and your business. This can involve updating quality standards, revising inspection and testing procedures, or providing additional training to your quality control team.
In conclusion, implementing a quality control program is crucial for any wood manufacturing business. By setting quality standards, developing a quality control plan, implementing the program, monitoring and evaluating its performance, and continuously improving the program, you can ensure that your products meet the desired level of quality and improve customer satisfaction, ultimately leading to increased profits for your business.
Benefits of Implementing Quality Control in Wood Manufacturing
Wood manufacturing involves several processes, including sawing, planning, sanding, and finishing, among others. Quality control is a critical component of the wood manufacturing process that ensures that the final product meets the necessary standards.
Quality control is the systematic process of inspecting, testing, and assessing products to ensure that they meet the required specifications. Implementing quality control in wood manufacturing has numerous benefits, and this article will delve into some of them.
Consistency and Uniformity
Implementing quality control in wood manufacturing ensures that products are consistent and uniform. Quality control ensures that products meet the required specifications, and this results in products that are consistent in terms of size, shape, and quality. Uniformity in products makes it easier for customers to identify the product, and it also ensures that products fit perfectly, reducing the risk of wastage.
Reduced Waste
Quality control in wood manufacturing helps to reduce waste. Waste can occur due to manufacturing errors, which result in defective products. Quality control ensures that products are manufactured according to the required specifications, reducing the risk of producing defective products. This, in turn, reduces the amount of waste produced, saving costs on raw materials and reducing the environmental impact of the manufacturing process.
Improved Product Quality
Quality control ensures that the products manufactured meet the necessary standards, resulting in high-quality products. High-quality products are more durable, last longer, and are more aesthetically pleasing. Improved product quality can help to build a positive reputation for the business, leading to increased sales and customer satisfaction.
Increased Customer Satisfaction
Quality control in wood manufacturing results in high-quality products that meet the customer's needs and expectations. Customers are more likely to be satisfied with products that meet their requirements, resulting in increased customer loyalty and repeat business. This can help to build a positive reputation for the business and attract new customers.
Compliance with Regulations
Quality control in wood manufacturing ensures that products comply with regulatory requirements. Compliance with regulations is essential for businesses to avoid legal penalties, which can be costly.
Quality control ensures that products are manufactured according to the required standards, reducing the risk of legal penalties and ensuring that the business operates within the law.
Improved Efficiency
Quality control in wood manufacturing improves efficiency by identifying and correcting manufacturing errors before they result in defective products. This results in a streamlined manufacturing process, reducing the time and cost of manufacturing products. Improved efficiency can help businesses to compete effectively in the market, resulting in increased sales and profits.
In conclusion, quality control is a critical component of wood manufacturing that ensures that products meet the necessary standards. Implementing quality control in wood manufacturing has numerous benefits, including consistency and uniformity, reduced waste, improved product quality, increased customer satisfaction, compliance with regulations, and improved efficiency. These benefits can help businesses to build a positive reputation, increase sales and profits, and operate effectively in the market.
Tips for Effective Wood Manufacturing Quality Control
Wood manufacturing is a complex process that requires careful attention to detail at every stage of production. Quality control is an essential part of this process, ensuring that every product leaving the factory meets the highest standards of quality and consistency.
In this blog, we'll share some tips for effective wood manufacturing quality control that can help you streamline your processes, reduce waste, and deliver exceptional products to your customers.
Develop a Quality Control Plan
The first step in effective quality control is to develop a plan that outlines your quality goals, procedures, and metrics. This plan should identify the key stages in your production process where quality checks will be performed and the specific criteria that will be used to measure quality at each stage. You should also identify the people responsible for conducting quality checks and define the corrective actions that will be taken if any quality issues are identified.
Use High-Quality Raw Materials
The quality of your finished products is directly linked to the quality of the raw materials you use. To ensure consistent quality, you should source your raw materials from reputable suppliers who can provide you with consistent quality products. You should also implement a system for inspecting raw materials when they arrive at your factory to ensure they meet your quality standards.
Monitor Your Production Processes
Monitoring your production processes is essential for effective quality control. You should use a combination of manual and automated monitoring systems to detect any deviations from your quality standards in real time.
This could include visual inspections, testing for physical properties such as moisture content, and using sensors to monitor critical parameters such as temperature and humidity.
Train Your Workforce
Your workforce is a critical component of your quality control system. You should invest in training programs to ensure that your employees understand the importance of quality and are equipped with the skills and knowledge needed to detect and address quality issues. Regular refresher training sessions can also help to reinforce the importance of quality throughout your organization.
Use Statistical Process Control (SPC)
Statistical Process Control (SPC) is a powerful tool for monitoring and controlling quality in manufacturing. SPC uses statistical methods to analyze data from your production processes and identify any trends or patterns that indicate potential quality issues. By using SPC, you can quickly identify and address quality issues before they become significant problems.
Implement a Continuous Improvement Process
Continuous improvement is essential for maintaining and improving the quality of your products over time. You should regularly review your quality control processes and metrics to identify areas for improvement. This could involve implementing new technologies, updating your procedures, or adjusting your metrics to better reflect your quality goals.
Regularly Communicate with Your Customers
Your customers are the ultimate judge of your product quality, so it's essential to regularly communicate with them about their satisfaction levels. You should gather feedback from your customers through surveys or direct communication and use this feedback to identify areas for improvement in your quality control processes.
Effective quality control is essential for delivering high-quality wood products that meet the needs of your customers. By following these tips, you can establish a robust quality control system that ensures consistent quality throughout your production process.
Remember to regularly review your quality control processes and metrics to identify areas for improvement and implement a continuous improvement process to maintain and improve your quality over time.
Common Challenges in Wood Manufacturing Quality Control and How to Overcome Them?
Wood manufacturing is a complex process that requires meticulous quality control measures to ensure that the end product meets the required standards. Quality control is an essential part of the manufacturing process that involves inspecting, testing, and verifying the product to ensure it meets the necessary requirements.
Despite the numerous quality control measures put in place, there are common challenges that manufacturers face. In this blog, we will discuss these challenges and provide solutions on how to overcome them.
Wood Quality Variation
Wood quality variation is a common challenge that manufacturers face. The quality of the wood used in the manufacturing process can vary depending on factors such as age, moisture content, species, and geographic location. These variations can affect the final product's strength, durability, and appearance, leading to quality issues.
To overcome this challenge, manufacturers need to implement strict quality control measures when sourcing wood. This can include using certified suppliers and conducting on-site inspections to ensure the wood meets the required standards.
Additionally, manufacturers can also implement a system to track the wood's source and quality, allowing them to make informed decisions when selecting wood for specific products.
Inconsistent Product Dimensions
Inconsistent product dimensions can result from variations in the manufacturing process. This can lead to products that are not uniform in size, shape, or thickness, making them difficult to use in specific applications.
To overcome this challenge, manufacturers can implement process control measures such as regular equipment maintenance, operator training, and process monitoring to ensure consistency in the manufacturing process.
Additionally, implementing quality control procedures such as inspection and testing can help identify and correct any inconsistencies in the final product.
Contamination
Contamination is a significant challenge in wood manufacturing that can lead to quality issues. Contaminants such as dirt, oil, and other foreign materials can affect the final product's appearance, strength, and durability.
To overcome this challenge, manufacturers need to implement a robust cleaning and maintenance program for all equipment and work surfaces. Additionally, they should implement a system for inspecting and testing raw materials to identify and eliminate any potential contaminants.
Production Waste
Production waste can significantly impact a manufacturer's bottom line. It can result from a variety of factors, such as material waste, process inefficiencies, and quality issues.
To overcome this challenge, manufacturers need to implement lean manufacturing principles such as process optimization, waste reduction, and continuous improvement. By identifying and eliminating waste in the manufacturing process, manufacturers can reduce costs, increase productivity, and improve product quality.
Human Error
Human error is a common challenge in wood manufacturing that can result from a lack of training, poor communication, or inadequate process controls. This can lead to quality issues, production delays, and increased costs.
To overcome this challenge, manufacturers should prioritize training and communication to ensure all employees understand their roles and responsibilities in the manufacturing process. Additionally, implementing process controls such as checklists and standard operating procedures can help reduce the risk of human error.
Quality control is an essential aspect of wood manufacturing that ensures the end product meets the required standards. However, several challenges can affect the quality of the final product, including wood quality variation, inconsistent product dimensions, contamination, production waste, and human error.
Manufacturers can overcome these challenges by implementing robust quality control measures, lean manufacturing principles, and prioritizing employee training and communication. By addressing these challenges, manufacturers can improve product quality, reduce costs, and increase productivity.
Quality Control Standards and Regulations for Wood Manufacturing
Quality control standards and regulations play a crucial role in ensuring that the wood products manufactured meet the expected quality standards. The wood industry has grown rapidly over the years, and the demand for quality wood products has increased. In this blog, we will discuss the quality control standards and regulations for wood manufacturing.
Quality Control Standards
Quality control is the process of ensuring that the products manufactured meet the desired quality standards. The following are the quality control standards for wood manufacturing:
American Wood Protection Association (AWPA)
The AWPA is a non-profit organization that develops and maintains standards for wood products. The standards include the use of preservatives, coatings, and other treatments to enhance the durability of wood products.
International Organization for Standardization (ISO)
The ISO is an international organization that develops and publishes standards for various products and services. The ISO 9001:2015 standard is the most widely recognized quality management system (QMS) standard in the world.
The standard provides guidelines for the implementation of a QMS, including the use of a quality manual, procedures, and records to ensure that the products manufactured meet the desired quality standards.
Forest Stewardship Council (FSC)
The FSC is an international organization that promotes responsible forest management. The organization develops and maintains standards for responsible forest management and chain-of-custody certification. The FSC certification ensures that the wood used in the manufacturing of products is sourced from responsibly managed forests.
Sustainable Forestry Initiative (SFI)
The SFI is a non-profit organization that promotes sustainable forestry practices. The organization develops and maintains standards for sustainable forest management, including the use of responsible forestry practices, such as reforestation and the protection of wildlife habitats.
Regulations
Regulations are laws and guidelines that govern the manufacturing of wood products. The following are the regulations for wood manufacturing:
Occupational Safety and Health Administration (OSHA)
OSHA is a federal agency that sets safety and health standards for workplaces in the United States. The agency sets regulations for the use of machinery, tools, and equipment to ensure that the workers are safe while working.
Environmental Protection Agency (EPA)
The EPA is a federal agency that sets regulations for the protection of the environment. The agency sets regulations for the use of chemicals and other substances in the manufacturing process to ensure that the environment is protected.
Consumer Product Safety Commission (CPSC)
The CPSC is a federal agency that sets regulations for consumer products. The agency sets regulations for the labeling, packaging, and testing of wood products to ensure that they are safe for consumers to use.
Quality control standards and regulations are crucial in ensuring that wood products manufactured meet the expected quality standards. The AWPA, ISO, FSC, and SFI are the quality control standards for wood manufacturing, while OSHA, EPA, and CPSC are the regulations governing the manufacturing process. Wood manufacturers must adhere to these standards and regulations to ensure that they produce quality and safe wood products for consumers.
Best Practices for Wood Manufacturing Quality Control
Wood manufacturing is an industry that is constantly growing and evolving. The quality of the products produced is an essential aspect that affects the reputation and success of the company.
Quality control is crucial in ensuring that the products meet the set standards, and the customers are satisfied. In this blog, we will discuss the best practices for wood manufacturing quality control.
Establish quality control standards and procedures:
The first step in quality control is to establish standards and procedures. This involves defining the quality attributes that are important to the customer and ensuring that the products meet these requirements. The standards should be measurable and achievable, and the procedures should be well documented and communicated to all employees.
Train employees
Employees are a crucial part of quality control. Properly trained employees are better equipped to identify and address quality issues. Training should be ongoing and cover all aspects of the manufacturing process, including safety, quality, and productivity.
Inspect raw materials
The quality of the finished product depends on the quality of the raw materials used. It is essential to inspect the raw materials before use to ensure that they meet the required standards. Any defects should be identified and addressed before the production process begins.
Monitor the production process
Monitoring the production process is essential to identify any quality issues that may arise. This involves regular inspections and testing of the products at different stages of the manufacturing process. Any defects should be identified and addressed promptly.
Use appropriate equipment
Using appropriate equipment is essential to ensure that the products meet the required standards. The equipment should be regularly maintained and calibrated to ensure that it is functioning correctly. Any defects in the equipment should be identified and addressed promptly.
Conduct final inspections
Final inspections are critical to ensure that the finished products meet the set standards. This involves inspecting the products for defects, measuring them to ensure that they meet the required dimensions, and testing them for strength and durability.
Implement corrective actions
Corrective actions should be taken promptly whenever quality issues are identified. This involves identifying the root cause of the issue and implementing measures to prevent it from happening again.
Conduct regular audits
Regular audits are essential to ensure that the quality control procedures are being followed correctly. Audits should be conducted by trained personnel who are not directly involved in the production process.
Quality control is essential in wood manufacturing to ensure that the products meet the required standards and the customers are satisfied. The best practices for wood manufacturing quality control include establishing quality control standards and procedures, training employees, inspecting raw materials, monitoring the production process, using appropriate equipment, conducting final inspections, implementing corrective actions, and conducting regular audits. By following these best practices, wood manufacturers can improve the quality of their products, reduce waste, and increase customer satisfaction.
Role of Training and Education in Wood Manufacturing Quality Control
Wood manufacturing is a complex and highly skilled process that involves several stages of production, including sawing, planning, sanding, and finishing. To ensure the quality of the end product, it is essential that each stage is carried out with precision and care.
The role of training and education in wood manufacturing quality control cannot be overstated. In this blog, we will discuss the importance of training and education in wood manufacturing quality control.
Proper Training of Employees
The first step in ensuring quality control in wood manufacturing is to train the employees. The employees should be trained on the proper use of tools and equipment, as well as the different stages of production.
Proper training ensures that employees have the necessary skills and knowledge to carry out their duties effectively. This, in turn, leads to a higher-quality end product.
Quality Control Procedures
Training and education are critical in establishing quality control procedures. Procedures should be established for each stage of production to ensure consistency and quality.
These procedures should be followed by every employee in the production process to guarantee the quality of the end product. Employees should also be trained on the importance of quality control procedures and how to adhere to them.
Safety Training
In addition to quality control procedures, safety procedures are equally important. Wood manufacturing involves the use of heavy machinery and sharp tools, which can be dangerous if not used properly.
Employees should be trained on proper safety procedures, such as how to use safety equipment and how to handle machinery and tools safely. Proper safety training helps to reduce accidents, which can lead to downtime and a decrease in product quality.
Continuing Education
Continuing education is essential in the wood manufacturing industry. As technology advances, new tools, equipment, and techniques are developed, and employees must stay up to date with these changes.
Continuing education ensures that employees are equipped with the latest knowledge and skills, which can lead to increased efficiency and higher-quality end products.
Improved Productivity
Training and education not only improve the quality of the end product but also improve productivity. When employees are properly trained, they can carry out their duties more efficiently, reducing production time and increasing output. This increased productivity leads to a higher quality end product, as well as increased profits for the company.
In conclusion, training and education are critical in wood manufacturing quality control. Proper training ensures that employees have the necessary skills and knowledge to carry out their duties effectively.
Quality control procedures and safety procedures should be established, and employees should be trained on how to adhere to them. Continuing education ensures that employees stay up to date with the latest technology and techniques, leading to increased efficiency and higher-quality end products. Finally, improved productivity leads to increased profits for the company.
How Can Deskera Assist You?
As a manufacturer, you must keep track of your inventory stock. The condition of your inventory has a direct impact on production planning. It also has a direct impact on people and machinery use and capacity utilization.
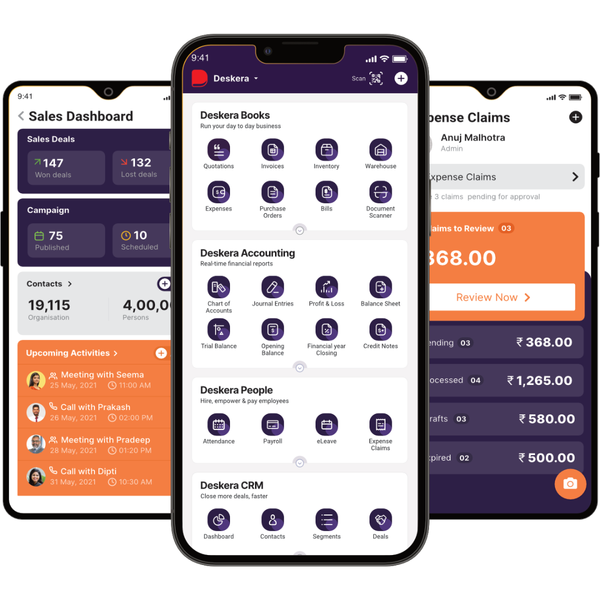
Deskera MRP is the one tool that lets you do all of the above. With Deskera, you can:
- Control production schedules
- Compile a Bill of Materials
- Produce thorough reports
- Make your dashboard
Deskera ERP is a complete solution that allows you to manage suppliers and track supply chain activity in real-time. It also allows you to streamline a range of other company functions.
Deskera Books allows you to manage your accounts and finances better. It helps maintain good accounting standards by automating billing, invoicing, and payment processing tasks.
Deskera CRM is a powerful tool that organizes your sales and helps you close deals rapidly. It enables you to perform crucial tasks like lead generation via email and gives you a comprehensive view of your sales funnel.
Deskera People is a straightforward application for centralizing your human resource management activities. Not only does the technology expedite payroll processing, but it also helps you to handle all other operations such as overtime, benefits, bonuses, training programs, and much more.
Key Takeaways:
- Sustainable wood is becoming increasingly popular as people become more conscious of the environment and their impact on it.
- Sustainable wood is a great choice for furniture and home décor, as it helps reduce our impact on the environment.
- When it comes to sustainability, wood is one of the most abundant and renewable resources available to us.
- With the increasing concern about global warming and deforestation, it's important to make sure the wood we buy is sourced from sustainable sources.
- Many companies are now labeling their wood with labels that indicate where the wood was sourced and how it was harvested. Look for labels that say FSC-certified, SFI-certified, or PEFC-certified.
Related Articles:
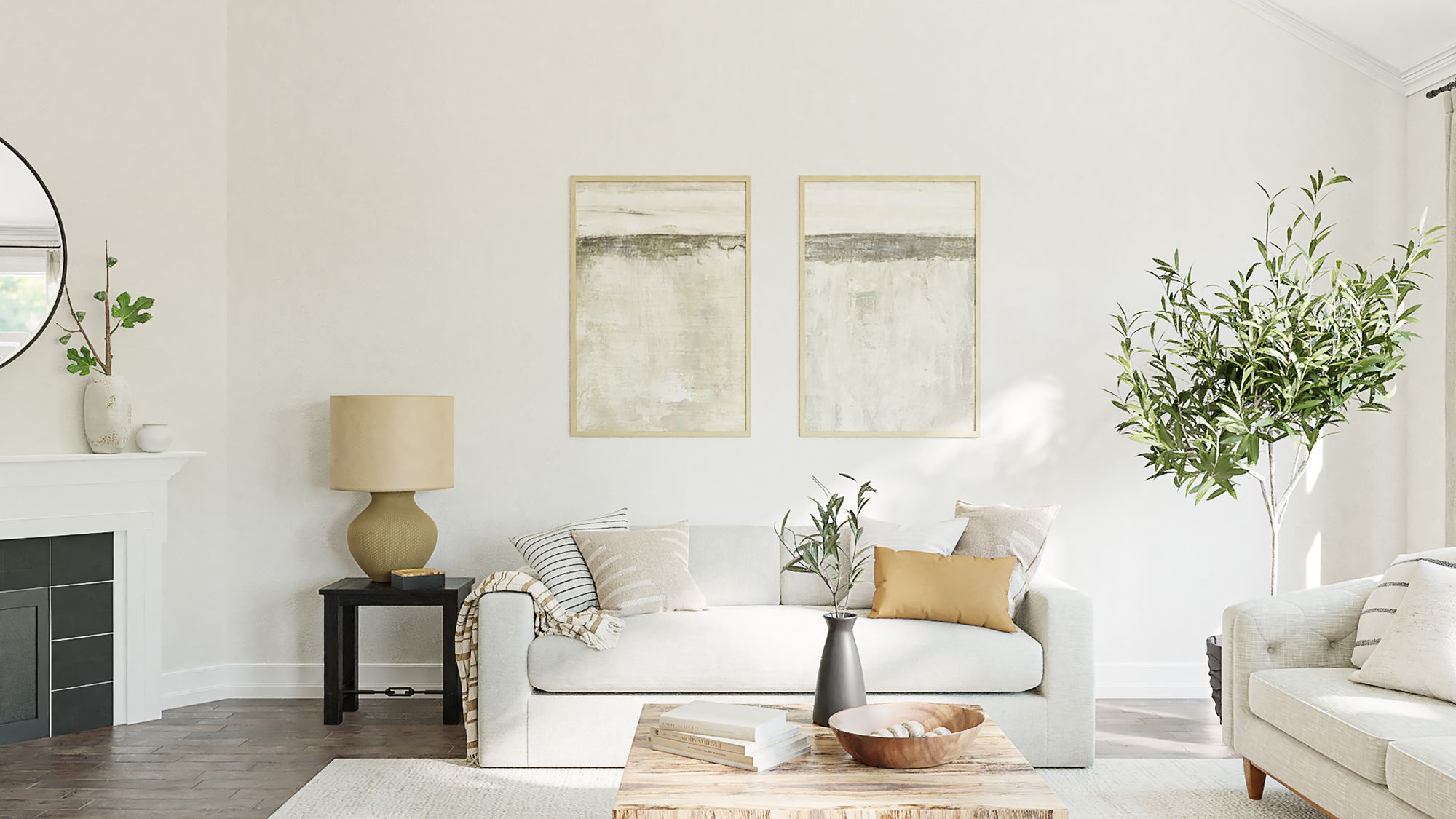
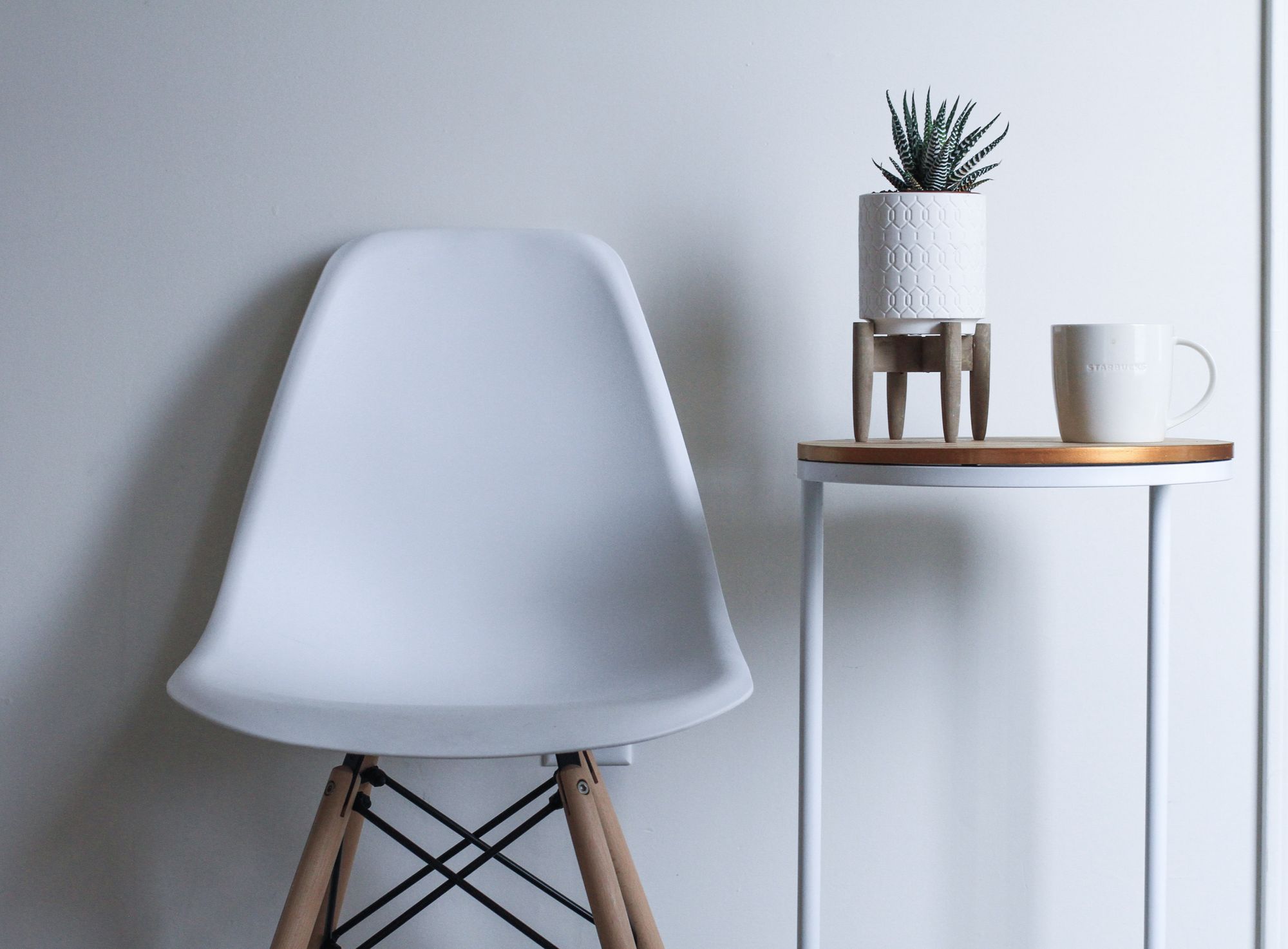
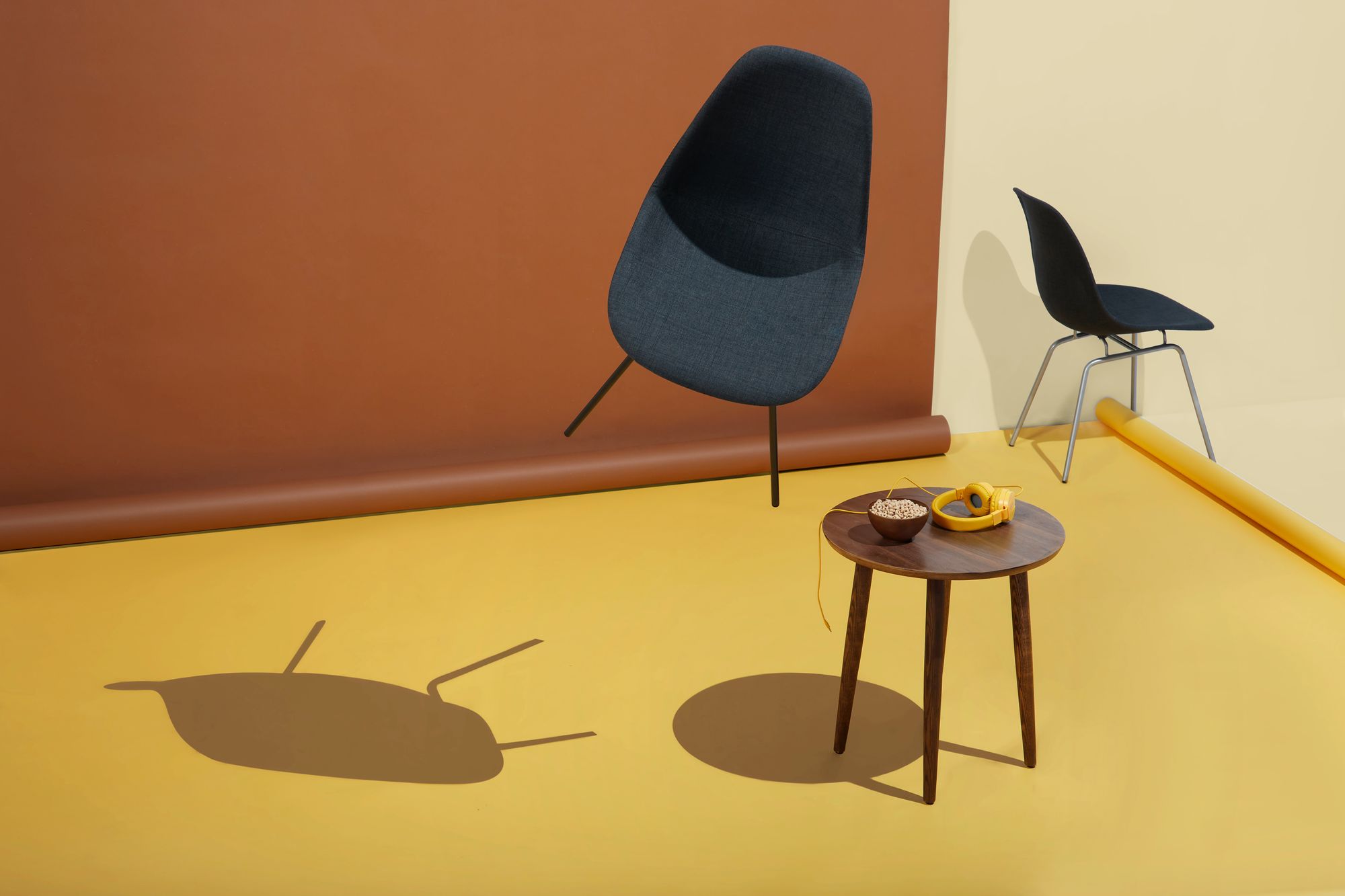