Plastic manufacturing is a dynamic and rapidly growing industry, with countless applications in different sectors of the economy. From packaging materials to medical devices, plastic products have become indispensable in our daily lives. However, with increasing demand and complexity comes the challenge of maintaining consistent quality standards.
Poor quality control can lead to costly recalls, lost customers, and even harm to the public. Therefore, it is critical for plastic manufacturers to implement robust quality control practices to ensure that their products meet or exceed industry standards.
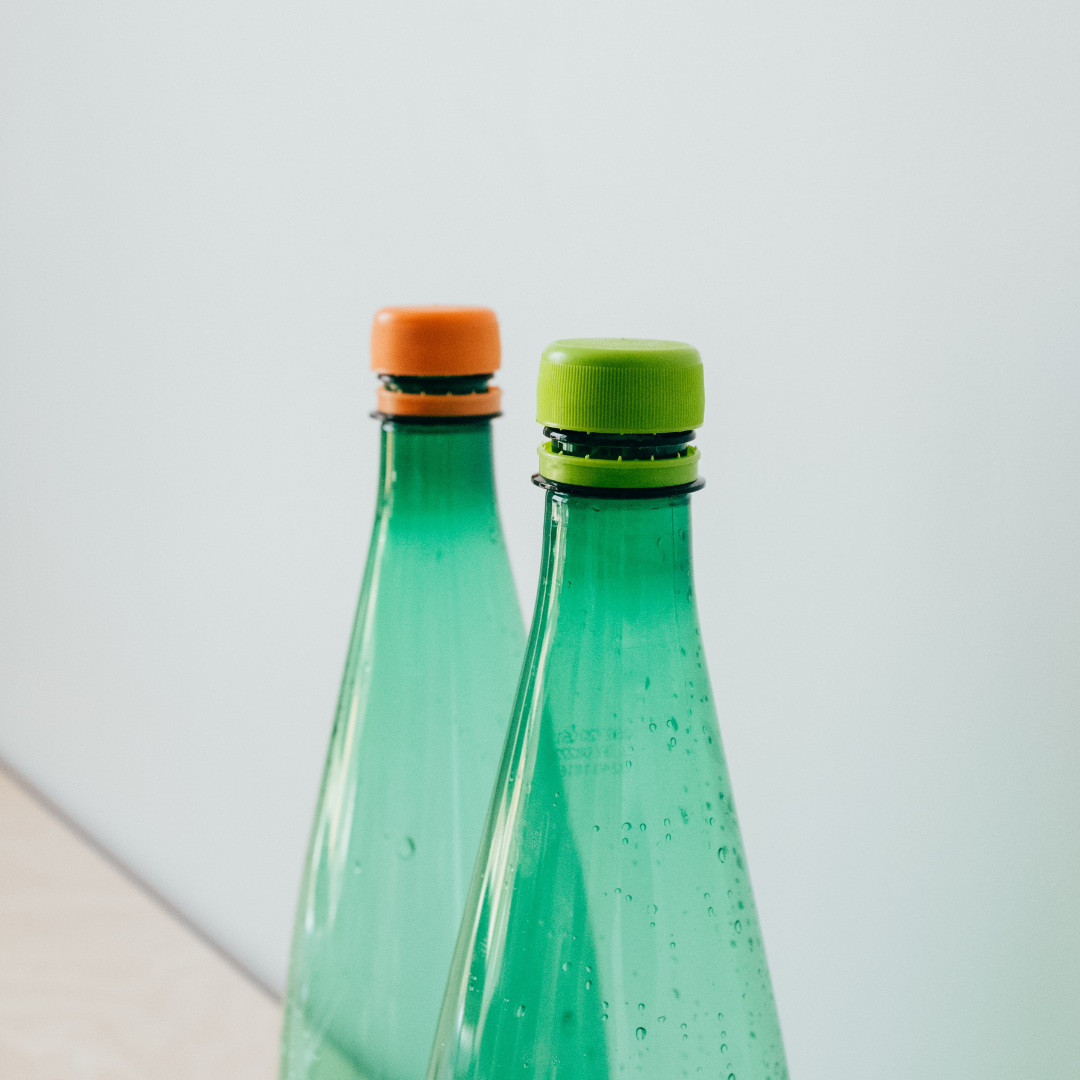
In this article, we will explore the best practices for plastic manufacturing quality control. We will delve into the various stages of the manufacturing process, from raw material inspection to finished product inspection, and highlight the key methods and tools for quality control.
We will also emphasize the importance of employee training and documentation to ensure that quality control practices are followed consistently. By implementing these best practices, plastic manufacturers can reduce costs, increase customer satisfaction, and maintain a competitive edge in the market.
- Importance of Quality Control in Plastic Manufacturing
- Quality Control Planning
- Steps Involved in Quality Control Planning for Plastic Manufacturing
- Raw Material Inspection
- Production Process Monitoring
- Quality Control Training and Documentation
- Need for ERP and MRP Software for Plastic Manufacturing Quality Control
- How can Deskera Help You?
- Key Takeaways
- Related Articles
Importance of Quality Control In Plastic Manufacturing
Quality control is essential in plastic manufacturing to ensure that the final product meets or exceeds the required quality standards. The importance of quality control in plastic manufacturing can be summarized as follows:
- Consistent Quality: Plastic products should meet the required quality standards to ensure their consistency and reliability. By implementing quality control measures, manufacturers can ensure that the products produced are uniform and of a consistently high quality, which in turn increases customer satisfaction and trust.
- Safety: Some plastic products are used in critical applications such as medical devices, automotive parts, and electrical components. Poor quality control can result in product failures and malfunctions, which can have serious safety consequences. By implementing quality control measures, manufacturers can reduce the risk of such incidents and ensure that their products meet the necessary safety requirements.
- Cost Reduction: Poor quality control can result in production inefficiencies, defects, and rejections, which can lead to increased costs. By implementing quality control measures, manufacturers can identify and eliminate the root causes of quality issues, thereby reducing production costs.
- Compliance: Plastic products are subject to various quality standards and regulations, such as those set by regulatory bodies, industry associations, and customer requirements. By implementing quality control measures, manufacturers can ensure that their products meet the necessary regulatory and customer requirements, thereby avoiding penalties, rejections, and loss of business.
In summary, quality control is critical in plastic manufacturing to ensure consistent quality, safety, cost reduction, and compliance with industry standards and regulations. By implementing effective quality control measures, manufacturers can improve their product quality, reduce costs, and maintain a competitive edge in the market.
Quality Control Planning
Quality Control Planning is a critical process in plastic manufacturing that aims to ensure that the finished products meet or exceed customer expectations. The process involves establishing standards for the product's quality, identifying potential defects or issues, and implementing measures to prevent or correct them.
The first step in quality control planning is to define the product specifications, including its dimensions, weight, material composition, and other relevant characteristics. The manufacturer must ensure that these specifications are consistent with the customer's requirements and industry standards.
Next, the manufacturer must establish procedures for monitoring the production process, including inspecting raw materials, testing product samples, and monitoring the manufacturing equipment's performance. These procedures should be designed to identify any deviations from the established standards and to prevent the production of defective products.
Once the production process is underway, the manufacturer must conduct ongoing inspections and quality checks to ensure that the products meet the established standards. This may involve visual inspections, measuring critical dimensions, and conducting tests to assess the product's performance.
Finally, the manufacturer must establish procedures for handling any defective products that are identified during the quality control process. These procedures should ensure that defective products are identified and segregated from the rest of the production, and that appropriate corrective actions are taken to prevent the production of similar defects in the future.
In summary, quality control planning is an essential process in plastic manufacturing that helps to ensure that the finished products meet or exceed customer expectations. By establishing clear product specifications, monitoring the production process, conducting ongoing inspections, and implementing procedures for handling defects, manufacturers can produce high-quality plastic products that meet the demands of the marketplace.
Steps Involved In Quality Control Planning For Plastic Manufacturing
Quality control planning is an essential process in plastic manufacturing that helps ensure that the finished products meet or exceed customer expectations. By defining product specifications, establishing standards and procedures, conducting inspections, taking corrective actions, and continuously improving the process, manufacturers can produce high-quality plastic products that meet the demands of the marketplace.
Here is how you can proceed:
- Setting quality goals and standards
- Determining measurement metrics
- Establishing quality control processes
Setting Quality Goals And Standards
Setting quality goals and standards in plastic manufacturing involves defining the quality objectives for a product and establishing the minimum acceptable quality levels that must be met. This process is critical in ensuring that the final product meets or exceeds customer expectations and is consistent with industry standards.
The quality goals and standards for plastic manufacturing may include a range of parameters, such as product dimensions, weight, material composition, strength, durability, and aesthetic features. These goals and standards are typically set in collaboration with the customer and are based on their specific needs and requirements.
The process of setting quality goals and standards involves several steps. These may include:
- Defining the product requirements: The first step is to clearly define the customer's product requirements, including the product's purpose, design specifications, and intended use.
- Identifying quality objectives: Based on the product requirements, the manufacturer must identify the quality objectives that must be met. These objectives should be specific, measurable, achievable, relevant, and time-bound (SMART).
- Establishing quality standards: Once the quality objectives are defined, the manufacturer must establish quality standards that specify the minimum acceptable quality levels for each parameter. These standards should be based on industry best practices and relevant regulations and standards.
- Communicating quality goals and standards: The quality goals and standards must be communicated to all stakeholders involved in the manufacturing process, including the production team, quality control personnel, and suppliers.
- Monitoring quality performance: The manufacturer must regularly monitor the quality performance of the production process to ensure that the quality goals and standards are being met. This may involve conducting quality control tests, analyzing production data, and reviewing customer feedback.
By setting quality goals and standards in plastic manufacturing, manufacturers can ensure that their products meet or exceed customer expectations and industry standards. This process helps to improve product quality, enhance customer satisfaction, and establish the manufacturer's reputation as a high-quality producer of plastic products.
Determining Measurement Metrics
Determining measurement metrics in plastic manufacturing quality control involves identifying the key parameters that must be measured and monitored to ensure that the finished product meets the established quality standards. These metrics provide a quantitative measure of the product's quality, which can be used to evaluate the performance of the production process and identify areas for improvement.
The measurement metrics for plastic manufacturing quality control may vary depending on the specific product and quality standards. However, some common metrics that are often used in plastic manufacturing quality control include:
- Dimensional accuracy: This metric measures the product's dimensions and ensures that they are within the acceptable tolerance range.
- Material properties: This metric measures the material properties of the plastic, such as strength, durability, and flexibility.
- Appearance: This metric measures the product's visual appearance, such as color, texture, and finish.
- Weight: This metric measures the weight of the product and ensures that it meets the specified weight requirements.
- Performance: This metric measures the product's performance, such as its ability to withstand stress, impact, or other environmental factors.
To determine the appropriate measurement metrics for plastic manufacturing quality control, manufacturers must consider the product requirements, customer expectations, and industry standards. Once the metrics are identified, the manufacturer must establish procedures for measuring and monitoring them throughout the production process. This may involve using specialized equipment, conducting tests and inspections, and collecting and analyzing data to identify trends and patterns.
By determining measurement metrics in plastic manufacturing quality control, manufacturers can ensure that their products meet the established quality standards and customer expectations. This process helps to improve product quality, enhance customer satisfaction, and establish the manufacturer's reputation as a high-quality producer of plastic products.
Establishing Quality Control Processes
Establishing quality control processes in plastic manufacturing involves developing a set of procedures and protocols to ensure that the final product meets the required quality standards. These processes include inspection, testing, and monitoring of various aspects of the production process to identify and correct any defects or issues that may arise.
The quality control process begins with the establishment of quality goals and standards, which define the specific requirements that the product must meet. Once these standards are established, the manufacturer must develop processes and procedures to ensure that the product meets these requirements.
Raw Material Inspection
Raw material inspection is an essential component of quality control in plastic manufacturing. It involves the evaluation and testing of the raw materials used in the production process to ensure that they meet the required specifications and are free from defects.
The quality of the raw materials used in plastic manufacturing can have a significant impact on the quality of the final product. Therefore, it is essential to inspect the raw materials to ensure that they are of the required quality before they are used in the production process. Some of the key steps involved in raw material inspection in plastic manufacturing quality control include:
- Sample collection: The first step in raw material inspection is to collect representative samples of the raw materials to be tested. The samples must be collected in a manner that ensures that they are representative of the entire batch of material.
- Visual inspection: The samples are then visually inspected to ensure that they meet the required quality standards. The inspection may include checking for defects such as cracks, discoloration, or foreign particles.
- Testing: The samples are then subjected to various tests to evaluate their properties and characteristics. The tests may include measuring the material's hardness, tensile strength, elongation, and other relevant properties.
- Record-keeping: The results of the raw material inspection must be recorded to ensure traceability and to facilitate further analysis if necessary.
If any defects or issues are identified during the raw material inspection, appropriate corrective actions must be taken to prevent the use of defective materials in the production process. This may involve rejecting the batch of material, returning it to the supplier, or implementing additional testing or processing steps to rectify the issue.
Raw material inspection is critical to ensuring the quality of the final plastic product. By conducting thorough inspections and testing of the raw materials used in the production process, manufacturers can ensure that their products meet or exceed customer expectations and industry standards.
Importance of Raw Material Inspection
Raw material inspection is crucial in ensuring the quality of the final product in any manufacturing process, including plastic manufacturing. Here are some reasons why raw material inspection is essential:
- Ensures compliance with quality standards: Raw material inspection is necessary to ensure that the raw materials used in the production process meet the required quality standards. By inspecting the raw materials before use, manufacturers can ensure that the final product meets or exceeds customer expectations and industry standards.
- Prevents defects and product failures: The quality of the raw materials used in plastic manufacturing can significantly impact the quality of the final product. Raw material inspection helps prevent defects and product failures by identifying and removing any defective materials from the production process.
- Saves time and money: Raw material inspection helps save time and money by preventing the production of defective products. By identifying and addressing any defects in the raw materials, manufacturers can avoid costly production delays and the need for expensive rework.
- Builds customer trust and loyalty: Providing high-quality products is crucial in building customer trust and loyalty. Raw material inspection ensures that the final product meets the required quality standards, which helps build customer confidence and trust in the manufacturer.
- Ensures traceability: Raw material inspection helps ensure traceability by recording the results of the inspection. This information can be used to track the source of any defects or issues that may arise and to implement corrective actions to prevent similar issues from occurring in the future.
Raw material inspection is an essential component of quality control in plastic manufacturing. It helps ensure compliance with quality standards, prevents defects and product failures, saves time and money, builds customer trust and loyalty, and ensures traceability.
Methods of Raw Material Inspection
There are several methods of raw material inspection that can be used in plastic manufacturing quality control, including:
- Visual inspection: This involves a manual examination of the raw materials to identify any visible defects such as discoloration, cracks, foreign particles, or irregularities in shape or size.
- Chemical analysis: This involves testing the raw materials for their chemical properties such as molecular weight, density, viscosity, and melting point. Chemical analysis can be done using various techniques such as gas chromatography, mass spectrometry, or infrared spectroscopy.
- Physical testing: This involves testing the raw materials for their physical properties such as hardness, tensile strength, elongation, and other relevant properties. Physical testing can be done using equipment such as a tensile tester, durometer, or impact tester.
- Thermal analysis: This involves testing the raw materials for their thermal properties such as thermal conductivity, heat capacity, and thermal expansion. Thermal analysis can be done using techniques such as differential scanning calorimetry or thermogravimetric analysis.
- Microscopic analysis: This involves examining the raw materials under a microscope to identify any microscopic defects or irregularities.
- Spectroscopic analysis: This involves using spectroscopy techniques such as UV-Vis spectroscopy, Raman spectroscopy, or X-ray fluorescence to analyze the chemical composition of the raw materials.
The method or combination of methods used for raw material inspection will depend on the type of raw material being inspected and the specific quality requirements of the manufacturer. By using a combination of these methods, manufacturers can ensure that the raw materials used in the production process meet the required quality standards and are free from defects.
Production Process Monitoring
Production process monitoring is the ongoing assessment of the manufacturing process to ensure that it is operating efficiently and producing products that meet the required quality standards. The purpose of production process monitoring is to identify and address any issues or inefficiencies in the production process that may affect the quality of the final product.
Production process monitoring involves the continuous collection and analysis of data from various stages of the manufacturing process. This data may include measurements of critical process parameters such as temperature, pressure, and flow rate, as well as data on product quality such as dimensional accuracy, color consistency, or strength.
The data collected during production process monitoring is used to identify any deviations from the expected process or product quality standards. If any deviations are detected, corrective actions are taken to address the issue and prevent the production of defective products. This may involve adjusting process parameters, changing raw materials, or modifying production procedures.
Importance of Production Process Monitoring
Production process monitoring is essential in ensuring the quality and consistency of the final product in any manufacturing process. Here are some reasons why production process monitoring is important:
- Improves product quality: Production process monitoring helps identify any deviations from the expected quality standards, which allows manufacturers to take corrective actions to address the issue and prevent the production of defective products. By continuously monitoring the production process, manufacturers can improve product quality and consistency, which helps build customer trust and loyalty.
- Reduces waste and cost: By monitoring the production process, manufacturers can identify and address any inefficiencies in the process that may be contributing to waste or increased production costs. By making adjustments to the process, manufacturers can reduce waste and costs, which helps improve profitability and competitiveness.
- Ensures compliance with regulations: Production process monitoring helps ensure that the manufacturing process is in compliance with regulatory requirements. By monitoring the production process and collecting data, manufacturers can demonstrate compliance with regulations and avoid potential fines or penalties.
- Enables continuous improvement: By continuously monitoring the production process, manufacturers can identify areas for improvement and implement changes to improve process efficiency and product quality. This enables a culture of continuous improvement, which can help manufacturers stay competitive and meet evolving customer needs and industry standards.
- Provides traceability: Production process monitoring allows manufacturers to trace the production of each product back to its specific manufacturing process. This provides a record of the production process and can be used to identify the source of any issues or defects that may arise.
By continuously monitoring the production process and making necessary adjustments, manufacturers can improve product quality, efficiency, and profitability.
Methods of Production Process Monitoring
There are several methods of production process monitoring used in manufacturing, including:
- Statistical process control (SPC): SPC is a method of monitoring and controlling a process by collecting and analyzing data over time. This involves using statistical techniques to identify any trends or patterns in the data that may indicate a process is out of control.
- Process mapping: Process mapping is a technique used to visualize and analyze a production process. It involves creating a flowchart or diagram of the process, including all the inputs, outputs, and activities involved. This helps identify any inefficiencies or bottlenecks in the process that may be impacting product quality or productivity.
- Real-time monitoring: Real-time monitoring involves using sensors or other devices to collect data on process parameters such as temperature, pressure, or flow rate in real-time. This allows for immediate detection of any deviations from expected process parameters, enabling corrective actions to be taken quickly.
- Sampling and testing: Sampling and testing involves taking samples of the product at various stages of production and testing them for specific quality parameters. This helps ensure that the product meets the required quality standards and allows for any deviations to be identified and addressed.
- Process automation: Process automation involves using technology such as robotics, machine learning, or artificial intelligence to automate production processes. This can improve process efficiency, reduce waste, and improve product quality by minimizing human error.
- Root cause analysis: Root cause analysis involves identifying the underlying cause of any deviations or defects in the production process. This helps identify the root cause of the problem and enables corrective actions to be taken to prevent it from recurring.
The method or combination of methods used for production process monitoring will depend on the specific manufacturing process and the desired quality outcomes. By using a combination of these methods, manufacturers can ensure that their production processes are operating efficiently and producing products that meet the required quality standards.
Finished Product Inspection
Finished product inspection is a quality control process that involves examining the final product to ensure that it meets the required quality standards before it is released to the market or shipped to the customer. This involves inspecting the product for defects, such as cracks, warping, or other imperfections that may affect its performance or appearance.
Finished product inspection typically involves both visual and functional testing. Visual testing may involve inspecting the product for any visible defects or flaws, such as scratches or discoloration. Functional testing may involve testing the product to ensure that it performs as expected and meets the required specifications, such as checking the product's weight, size, or dimensions.
Finished product inspection is an important part of the quality control process, as it helps ensure that only products that meet the required quality standards are released to the market or shipped to the customer. This helps build customer trust and loyalty, as customers can be confident that they are receiving products that meet their expectations.
In addition to ensuring product quality, finished product inspection can also help identify areas for improvement in the manufacturing process. By collecting data on the types and frequency of defects found during the inspection process, manufacturers can identify patterns or trends that may indicate areas for improvement in the production process. This enables manufacturers to take corrective actions to improve product quality and process efficiency over time.
Importance of Finished Product Inspection
Finished product inspection is an essential step in the quality control process for any manufacturing operation. Here are some of the key reasons why finished product inspection is so important:
- Ensuring product quality: Finished product inspection helps ensure that the product meets the required quality standards before it is released to the market or shipped to the customer. This helps build customer trust and loyalty, as customers can be confident that they are receiving products that meet their expectations.
- Preventing defects and recalls: By identifying defects and flaws in the finished product before it is shipped, finished product inspection can help prevent product recalls and costly rework. This helps protect the company's reputation and bottom line.
- Identifying process improvements: By collecting data on the types and frequency of defects found during the inspection process, manufacturers can identify patterns or trends that may indicate areas for improvement in the production process. This enables manufacturers to take corrective actions to improve product quality and process efficiency over time.
- Compliance with regulations: Depending on the industry and product, there may be specific regulations or standards that the finished product must meet. Finished product inspection helps ensure compliance with these regulations and standards.
- Continuous improvement: Finished product inspection is an opportunity for manufacturers to continuously improve their products and processes. By identifying areas for improvement, manufacturers can take action to improve product quality, reduce waste, and increase efficiency over time.
Quality Control Training and Documentation
Quality control training and documentation are essential components of a successful quality control program in plastic manufacturing. Quality control training is the process of providing employees with the necessary skills and knowledge to perform quality control tasks effectively, while documentation involves recording and tracking quality control activities for future reference and continuous improvement.
Quality control training ensures that employees have the necessary skills and knowledge to perform quality control tasks effectively. This includes training in areas such as inspection techniques, use of measurement tools, and quality control processes and procedures. Training should be provided to all employees involved in quality control, including inspectors, supervisors, and managers. Regular training sessions should be conducted to ensure that employees are up-to-date with the latest quality control processes and techniques.
Documentation is also a critical component of quality control in plastic manufacturing. Documentation includes recording and tracking quality control activities such as inspections, tests, and audits. This information can be used to identify areas for improvement in the manufacturing process, and to ensure that products meet the required quality standards. Documentation should be clear, concise, and easily accessible to all relevant employees.
In addition to providing a record of quality control activities, documentation also helps to ensure consistency in quality control processes. By having clear and standardized procedures documented, employees can follow the same processes and procedures to ensure consistency in quality control activities.
Overall, quality control training and documentation are important for ensuring the success of a quality control program in plastic manufacturing. By investing in training and documentation, manufacturers can ensure that employees have the necessary skills and knowledge to perform quality control tasks effectively, and that quality control activities are recorded and tracked for future reference and continuous improvement.
Importance of Quality Control Training and Documentation
Quality control training and documentation are essential for the success of a quality control program in any manufacturing industry, including plastic manufacturing. Here are some of the key reasons why quality control training and documentation are so important:
- Ensuring consistent quality: Quality control training and documentation help ensure that all employees involved in quality control activities are using the same processes and procedures. This helps to ensure that the products manufactured meet the required quality standards consistently.
- Identifying areas for improvement: Documentation of quality control activities provides valuable data that can be used to identify areas for improvement in the manufacturing process. This enables manufacturers to take corrective actions and continuously improve product quality and process efficiency.
- Compliance with regulations: In many industries, there are specific regulations or standards that products must meet. Quality control training and documentation help ensure compliance with these regulations and standards.
- Improving customer satisfaction: Quality control training and documentation can help improve customer satisfaction by ensuring that products meet their requirements consistently.
- Reducing costs: By identifying and correcting issues early in the production process, quality control training and documentation can help reduce costs associated with rework, scrap, and customer returns.
By investing in training and documentation, manufacturers can ensure consistent quality, comply with regulations, and continuously improve product quality and process efficiency, leading to increased customer satisfaction and reduced costs.
Importance of Employee Training
Employee training is an essential component of any organization, including manufacturing companies such as plastic manufacturing. Here are some of the key reasons why employee training is so important:
- Improved job performance: Proper training provides employees with the necessary knowledge and skills to perform their jobs effectively. This improves job performance and leads to better quality products, increased efficiency, and higher levels of customer satisfaction.
- Increased safety: Training helps employees understand safety procedures and protocols. This helps prevent accidents and injuries, which can be costly to the organization and harmful to employees.
- Compliance with regulations: Many industries have specific regulations that organizations must comply with. Employee training ensures that employees understand and follow these regulations, which reduces the risk of non-compliance and associated penalties.
- Employee satisfaction and retention: Investing in employee training shows employees that the organization values their professional development. This can lead to increased job satisfaction and employee retention.
- Innovation and adaptation: Training can help employees learn new skills and techniques that can be used to innovate and adapt to changes in the industry. This is particularly important in rapidly evolving industries such as plastic manufacturing.
By providing employees with the necessary knowledge and skills to perform their jobs effectively, ensuring compliance with regulations, and promoting innovation and adaptation, organizations can improve their performance and competitiveness. Additionally, investing in employee training can lead to increased employee satisfaction and retention, which is beneficial for both employees and the organization.
Importance of Maintaining Accurate Records of Quality Control Activities
Maintaining accurate records of quality control activities is crucial for any manufacturing company, including plastic manufacturing. Here are some of the key reasons why it's important:
- Compliance with regulations: Many industries have specific regulations or standards that products must meet. Maintaining accurate records of quality control activities helps ensure compliance with these regulations and standards.
- Traceability: Accurate records allow for traceability of products, from raw materials to finished goods. This helps identify any quality issues that arise and enables manufacturers to take corrective actions and prevent similar issues in the future.
- Continuous improvement: Accurate records of quality control activities provide valuable data that can be used to identify areas for improvement in the manufacturing process. This enables manufacturers to take corrective actions and continuously improve product quality and process efficiency.
- Customer satisfaction: Maintaining accurate records of quality control activities can help improve customer satisfaction by ensuring that products meet their requirements consistently and providing evidence of quality control activities.
- Legal protection: In the event of a product liability lawsuit, accurate records of quality control activities can provide legal protection for manufacturers by demonstrating that they took all reasonable steps to ensure product quality and safety.
It helps ensure compliance with regulations, provides traceability of products, enables continuous improvement, improves customer satisfaction, and provides legal protection. By investing in proper record-keeping procedures and systems, manufacturers can reap these benefits and ensure the success of their quality control program.
Need for ERP and MRP Software for Plastic Manufacturing Quality Control
ERP (Enterprise Resource Planning) and MRP (Material Requirements Planning) software are essential tools for plastic manufacturing quality control. Here are some of the key reasons why:
- Streamlined processes: ERP and MRP software can streamline processes by automating tasks such as inventory management, production planning, and scheduling. This reduces the risk of errors and saves time, allowing quality control personnel to focus on critical tasks such as monitoring the production process and inspecting finished products.
- Real-time visibility: ERP and MRP software provide real-time visibility into the production process, enabling quality control personnel to identify and address issues as they arise. This allows for faster corrective actions, reduces the risk of defects, and improves overall product quality.
- Improved data accuracy: ERP and MRP software help ensure data accuracy by reducing the need for manual data entry and providing a centralized database for all quality control activities. This eliminates errors that can occur when data is entered manually or stored in multiple locations.
- Compliance with regulations: Many industries have specific regulations that products must meet, and ERP and MRP software can help ensure compliance by providing automated processes for quality control activities such as inspection and testing.
- Better decision-making: ERP and MRP software provide data analytics and reporting tools that can help quality control personnel make better decisions. This allows for continuous improvement in product quality and process efficiency.
Overall, ERP and MRP software are essential tools for plastic manufacturing quality control. They provide streamlined processes, real-time visibility, improved data accuracy, compliance with regulations, and better decision-making. By investing in these software tools, manufacturers can improve their quality control program and ensure the consistent production of high-quality products.
How can Deskera Help You?
Deskera ERP and MRP systems help you to keep your business units organized. The system's primary functions are as follows:
- Keep track of your raw materials and final items inventories
- Control production schedules and routings
- Keep a bill of materials
- Produce thorough reports
- Make your own dashboards
Deskera's integrated financial planning tools enable investors to better plan and track their investments. It can assist investors in making faster and more accurate decisions.
Deskera Books allows you to better manage your accounts and finances. Maintain good accounting practices by automating tasks like billing, invoicing, and payment processing.
Deskera CRM is a powerful solution that manages your sales and helps you close deals quickly. It not only enables you to perform critical tasks like lead generation via email, but it also gives you a comprehensive view of your sales funnel.
Deskera People is a straightforward tool for centralizing your human resource management functions.
Key Takeaways
- Define quality goals and standards for raw materials, production processes, and finished products.
- Identify critical quality metrics and establish a system for measuring and monitoring them.
- Implement processes for raw material inspection, production process monitoring, and finished product inspection.
- Train employees on quality control processes and procedures to ensure consistency and adherence to quality standards.
- Keep detailed and accurate records of all quality control activities, including inspections, tests, and audits.
- Implement ERP and MRP software to automate and streamline quality control processes.
- Ensure that all raw materials meet quality standards and specifications before they are used in production.
- Monitor production processes to identify and correct any issues that could impact product quality.
- Conduct regular inspections of finished products to ensure that they meet quality standards and customer requirements.
- Establish a system for identifying and addressing non-conforming products or processes.
- Continuously review quality control processes and metrics to identify areas for improvement and implement changes to enhance product quality and process efficiency.
- Establish a culture of quality that emphasizes the importance of quality control and encourages continuous improvement.
Related Articles
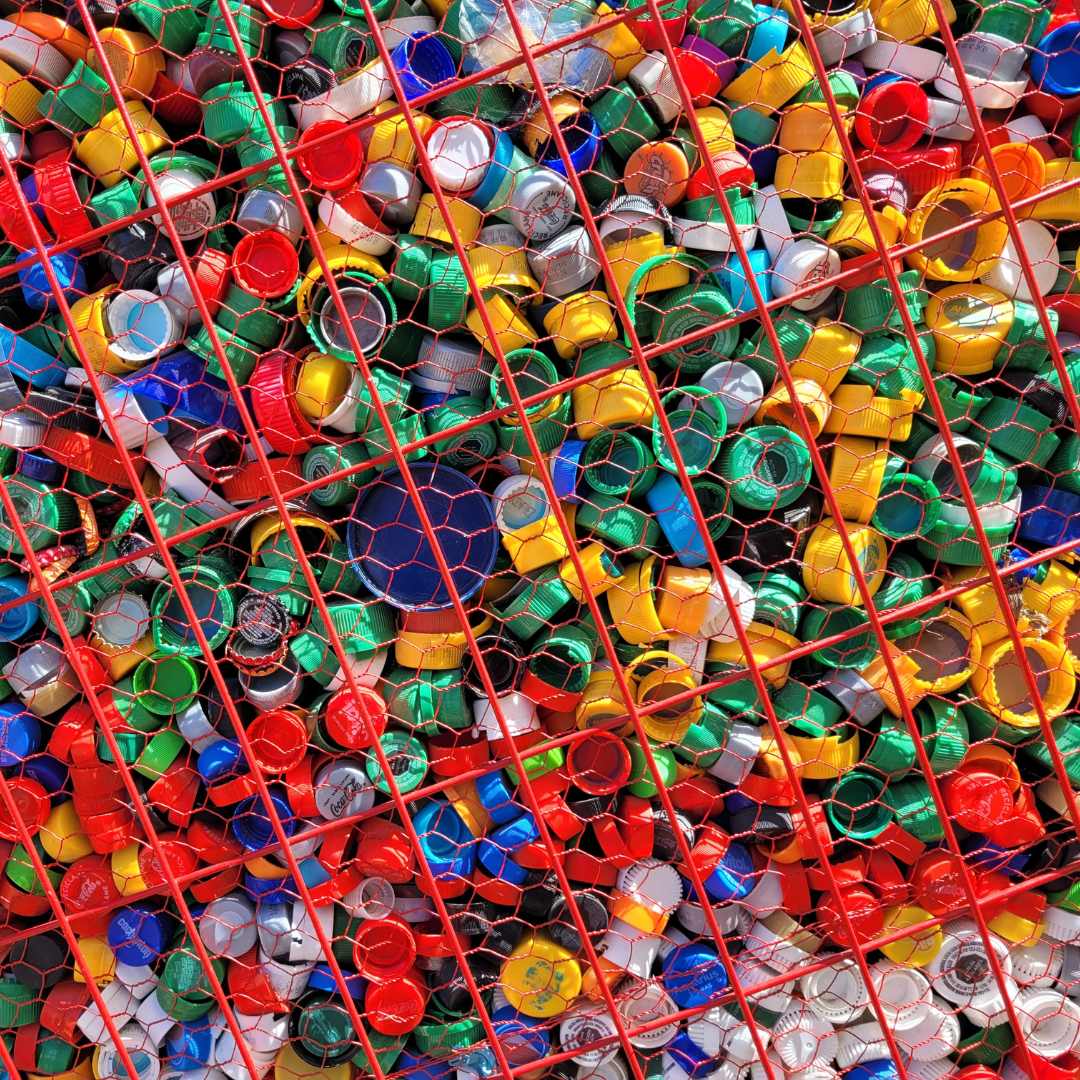
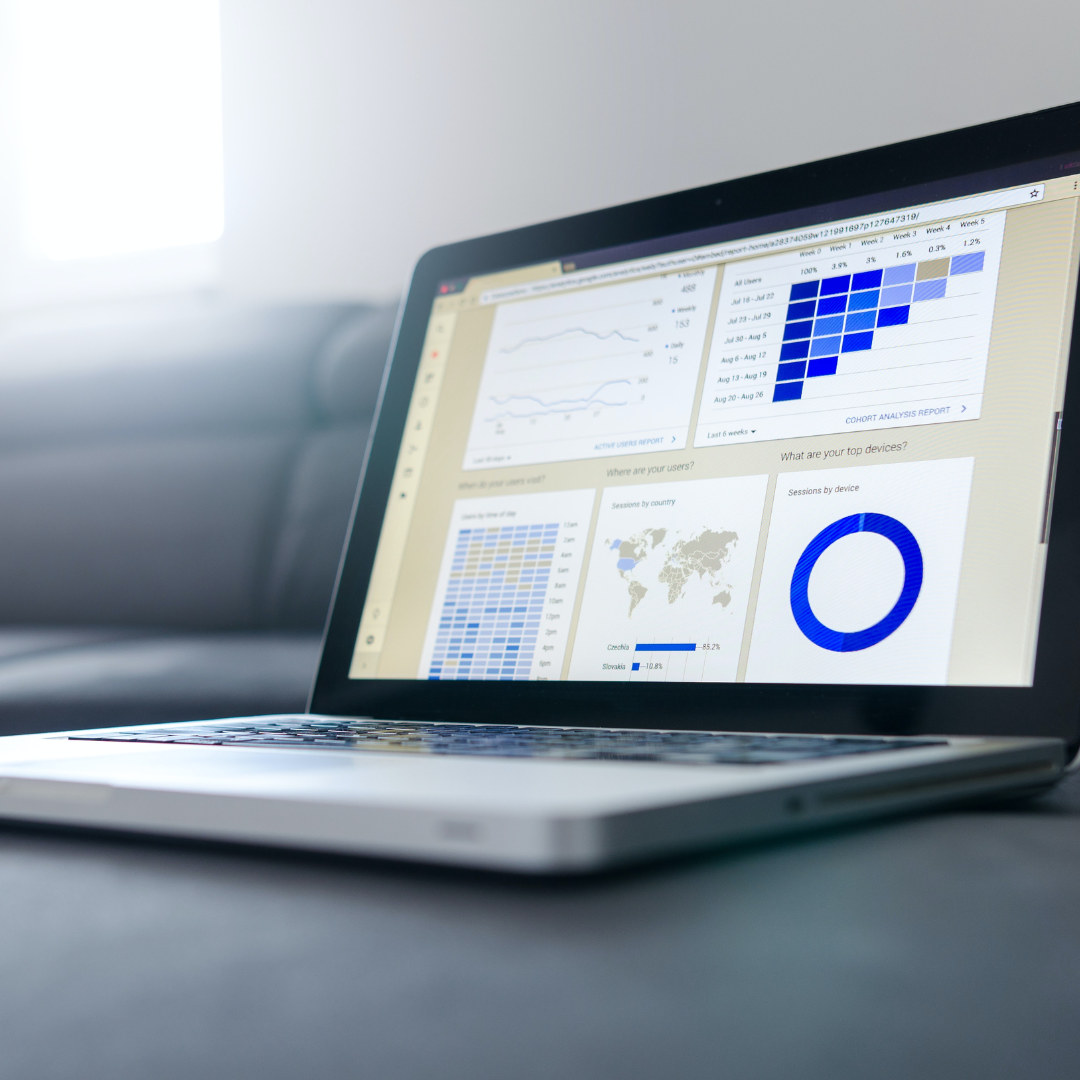
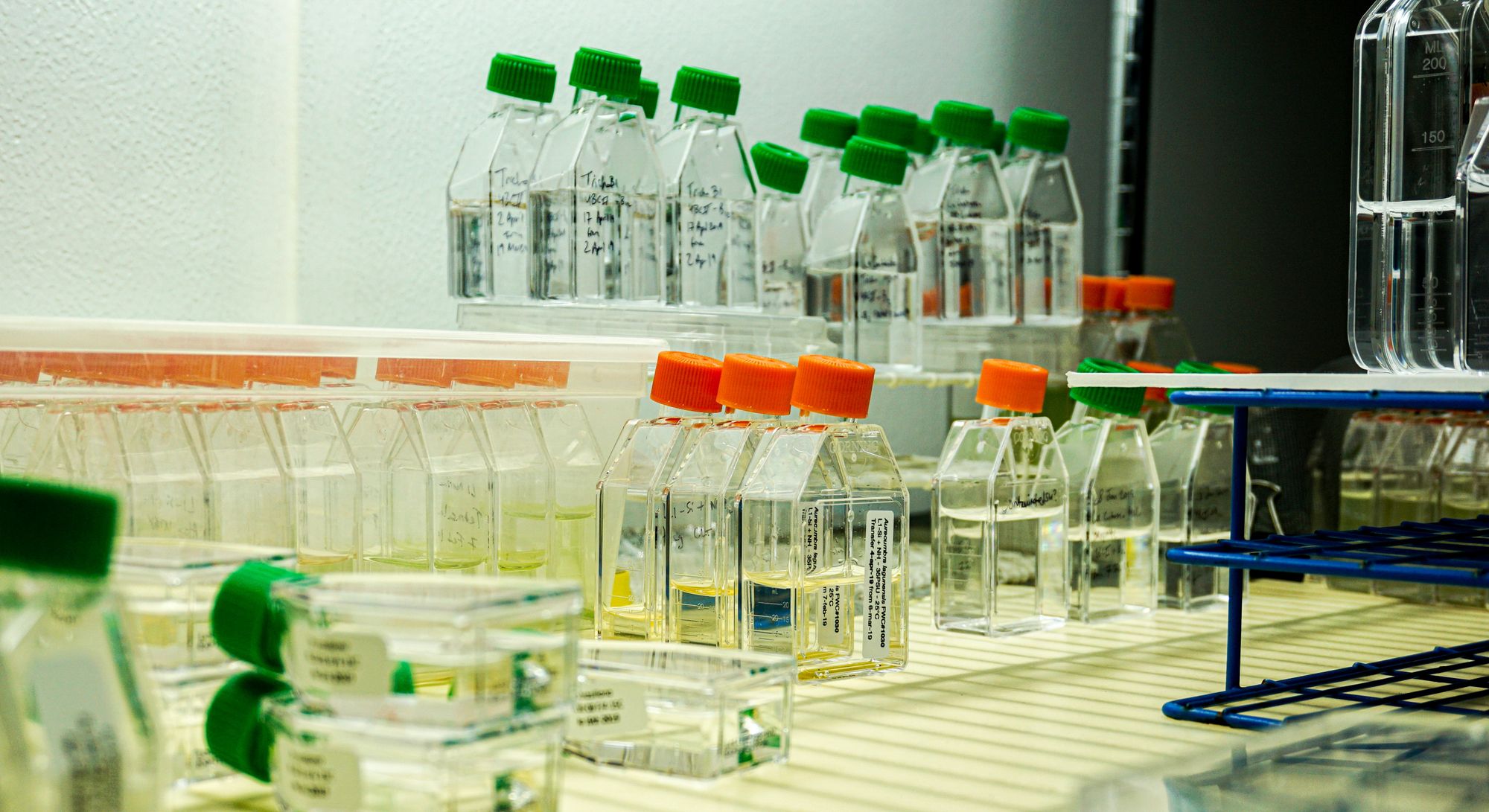
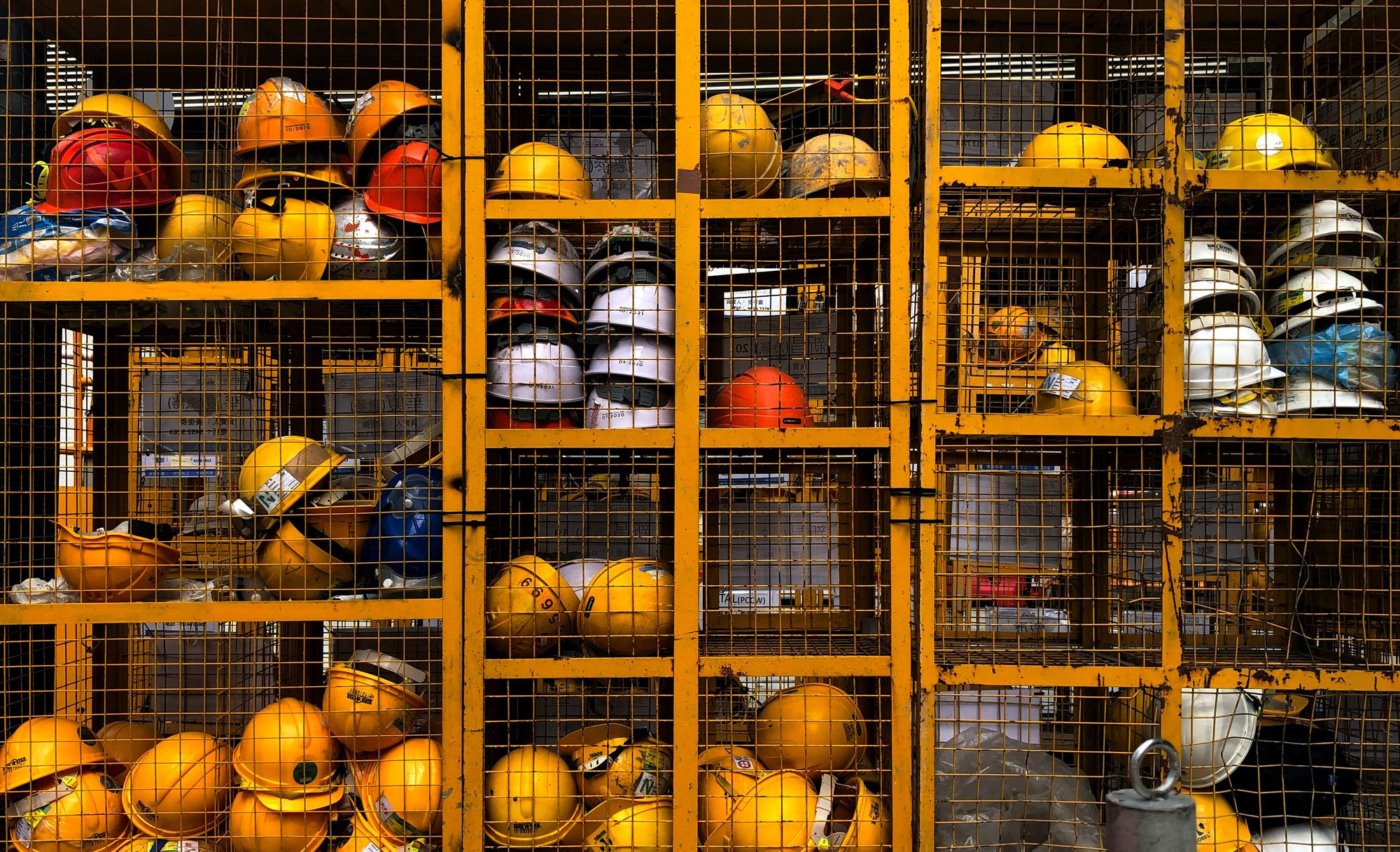