Chemical manufacturing is a complex process that involves numerous steps and requires strict quality control measures to ensure that the final product meets the desired specifications. Quality control is a critical aspect of chemical manufacturing, as it ensures that the products being produced are safe, effective, and of high quality. Quality control procedures need to be developed and implemented throughout the entire manufacturing process, from raw material receipt to final product release.
The purpose of this article is to provide an overview of the best practices for chemical manufacturing quality control.
- Establish Quality Control Procedures
- Train Personnel
- Maintain a Clean and Controlled Environment
- Conduct Rigorous Testing
- Use Appropriate Equipment
- Document Everything
- Continuously Improve
- How can Deskera Help You?
- Conclusion
- Related Articles
Establish Quality Control Procedures
Establishing quality control procedures is the first step towards ensuring that the products being manufactured meet the desired specifications. Quality control procedures should be developed for each step of the manufacturing process, including raw material receipt, storage, handling, production, testing, and final product release. The following are the steps involved in establishing quality control procedures:
- Define the quality control objectives: The first step is to define the quality control objectives. This involves determining the quality attributes that are important for the product and the acceptable limits for these attributes. For example, the purity of the final product may be an important quality attribute, and the acceptable limit may be 99%.
- Develop Standard Operating Procedures (SOPs): SOPs should be developed for each step of the manufacturing process. The SOPs should be detailed and specific, including instructions for handling and storing raw materials, sampling and testing of raw materials, production steps, required equipment, process parameters, and quality checks. The SOPs should also include instructions for documenting and reporting any deviations from the standard procedures.
- Implement the SOPs: Once the SOPs have been developed, they should be implemented consistently. All personnel involved in the manufacturing process should be trained on the SOPs and should follow them closely. Deviations from the standard procedures should be documented and reported.
- Monitor the process: The manufacturing process should be monitored regularly to ensure that it meets the desired quality standards. This can be achieved by conducting regular checks on the process parameters, equipment, and quality of raw materials. Any deviations from the standard procedures should be investigated, and corrective actions taken to prevent recurrence.
- Document everything: Detailed records should be kept of all quality control activities, including testing results, deviations, and corrective actions taken. These records should be easily accessible and kept for an appropriate amount of time.
- Continuously improve: Quality control procedures should be reviewed regularly to identify areas for improvement. Any deviations from the standard procedures should be investigated, and corrective actions taken to prevent recurrence. Data should be analyzed regularly to identify trends and patterns that can be used to improve the manufacturing process.
By following these steps, manufacturers can establish effective quality control procedures that ensure that the products being manufactured meet the desired specifications.
Train Personnel
Training personnel is a critical aspect of quality control in chemical manufacturing. All personnel involved in the manufacturing process, including production operators, quality control analysts, and laboratory technicians, should receive appropriate training to ensure that they understand the importance of quality control and can perform their jobs effectively. The following are the steps involved in training personnel:
- Identify the training needs: The first step is to identify the training needs of the personnel. This involves determining the specific skills and knowledge required to perform their jobs effectively. The training needs should be based on the job requirements, regulatory requirements, and the company's quality control procedures.
- Develop training materials: Once the training needs have been identified, appropriate training materials should be developed. This may include training manuals, videos, presentations, and hands-on training exercises. The training materials should be comprehensive and easy to understand, and should cover all aspects of quality control relevant to the job.
- Conduct training sessions: The training sessions should be conducted by qualified trainers who have experience in the manufacturing process and quality control procedures. The training sessions should be interactive, with opportunities for questions and discussions. The trainers should also provide practical examples and hands-on training exercises to reinforce the learning.
- Evaluate the training: Once the training is complete, it should be evaluated to ensure that the personnel have acquired the necessary skills and knowledge. This can be achieved through assessments and practical tests. The results of the evaluation should be used to identify areas for improvement and to modify the training materials if necessary.
- Provide ongoing training: Quality control procedures and regulations are subject to change, and new equipment and technologies may be introduced. Ongoing training should be provided to ensure that the personnel are up-to-date with the latest developments and can perform their jobs effectively.
By following these steps, manufacturers can ensure that their personnel are trained effectively and can perform their jobs to the required standards. This can help to ensure that the products produced are safe, effective, and of high quality.
Maintain a Clean and Controlled Environment
Maintaining a clean and controlled environment is crucial in chemical manufacturing to prevent contamination and ensure product quality. The following are the steps involved in maintaining a clean and controlled environment:
- Establish cleaning procedures: Cleaning procedures should be established for all areas of the manufacturing facility, including the production area, storage areas, and laboratories. The cleaning procedures should be detailed and specific, including instructions for cleaning agents, cleaning equipment, and frequency of cleaning.
- Train personnel: Personnel responsible for cleaning should be trained on the cleaning procedures and the importance of maintaining a clean environment. They should also be trained on the proper use of cleaning agents and equipment.
- Conduct regular cleaning: Regular cleaning should be conducted to maintain a clean environment. The frequency of cleaning should be determined based on the nature of the product being manufactured and the level of cleanliness required. For example, high-purity products may require more frequent cleaning than products with lower purity requirements.
- Implement contamination controls: Contamination controls should be implemented to prevent contamination from entering the manufacturing process. This may include air filtration systems, gowning procedures, and restricted access to production areas.
- Monitor environmental conditions: Environmental conditions, such as temperature, humidity, and air quality, should be monitored regularly to ensure that they meet the required specifications. Any deviations should be investigated, and corrective actions taken to prevent recurrence.
- Validate cleaning procedures: Cleaning procedures should be validated to ensure that they are effective in removing contaminants. This can be achieved through swab testing or other analytical methods. The results of the validation should be used to modify the cleaning procedures if necessary.
- Document everything: Detailed records should be kept of all cleaning activities, including the cleaning procedures used, the frequency of cleaning, and the results of any validation testing. These records should be easily accessible and kept for an appropriate amount of time.
By following these steps, manufacturers can maintain a clean and controlled environment and prevent contamination, ensuring that the products produced are of high quality and meet the required specifications.
Conduct Rigorous Testing
Rigorous testing is a critical aspect of quality control in chemical manufacturing. Testing ensures that the products produced meet the required specifications and are safe and effective. The following are the steps involved in conducting rigorous testing:
- Establish testing procedures: Testing procedures should be established for all aspects of the manufacturing process, including raw materials, intermediate products, and finished products. The testing procedures should be detailed and specific, including instructions for testing methods, equipment, and acceptance criteria.
- Select appropriate testing methods: The appropriate testing methods should be selected based on the nature of the product being manufactured and the level of testing required. Testing methods may include physical, chemical, and microbiological testing.
- Calibrate equipment: All testing equipment should be calibrated to ensure accurate and reliable results. Calibration should be conducted on a regular basis, and records of calibration should be kept.
- Train personnel: Personnel responsible for testing should be trained on the testing procedures and the use of testing equipment. They should also be trained on the importance of accuracy and precision in testing.
- Conduct testing: Testing should be conducted at appropriate stages of the manufacturing process to ensure that the products meet the required specifications. Testing should be conducted in accordance with the established procedures, and records of testing should be kept.
- Validate testing methods: Testing methods should be validated to ensure that they are accurate and reliable. This can be achieved through analytical method validation, which involves demonstrating that the testing method is suitable for its intended purpose.
- Investigate deviations: Any deviations from the required specifications should be investigated to determine the root cause of the deviation. Corrective actions should be taken to prevent recurrence.
- Document everything: Detailed records should be kept of all testing activities, including the testing procedures used, the results of testing, and any deviations from the required specifications. These records should be easily accessible and kept for an appropriate amount of time.
By following these steps, manufacturers can ensure that rigorous testing is conducted throughout the manufacturing process, ensuring that the products produced meet the required specifications and are safe and effective.
Use Appropriate Equipment
Using appropriate equipment is crucial in ensuring quality control in chemical manufacturing. The following are the steps involved in using appropriate equipment:
- Identify equipment requirements: Equipment requirements should be identified based on the nature of the product being manufactured and the level of equipment required. This may include mixing equipment, reactors, distillation equipment, and analytical equipment.
- Select appropriate equipment: Appropriate equipment should be selected based on the identified equipment requirements. The equipment should be suitable for the intended use, and its performance should be validated.
- Calibrate equipment: All equipment used in the manufacturing process should be calibrated to ensure that it performs accurately and reliably. Calibration should be conducted on a regular basis, and records of calibration should be kept.
- Maintain equipment: All equipment should be maintained in accordance with the manufacturer's recommendations. This may include regular cleaning, lubrication, and replacement of parts.
- Train personnel: Personnel responsible for operating equipment should be trained on the proper use and maintenance of the equipment. They should also be trained on the importance of equipment performance and reliability in ensuring product quality.
- Conduct performance qualification: Equipment performance should be qualified to ensure that it meets the required specifications. This may include operational qualification (OQ), which involves demonstrating that the equipment operates within its specified parameters, and performance qualification (PQ), which involves demonstrating that the equipment performs its intended function.
- Document everything: Detailed records should be kept of all equipment activities, including calibration, maintenance, and qualification. These records should be easily accessible and kept for an appropriate amount of time.
By following these steps, manufacturers can ensure that appropriate equipment is used throughout the manufacturing process, ensuring that the products produced meet the required specifications and are safe and effective.
Document Everything
Documentation is a critical aspect of quality control in chemical manufacturing. Documentation provides a record of all activities related to the manufacturing process, including the procedures used, the equipment used, the testing conducted, and any deviations from the required specifications. The following are the steps involved in documenting everything:
- Establish documentation requirements: Documentation requirements should be established based on the nature of the product being manufactured and the level of documentation required. This may include standard operating procedures (SOPs), batch records, equipment logs, and testing records.
- Develop documentation: Documentation should be developed in accordance with the established requirements. The documentation should be detailed and specific, including instructions for all aspects of the manufacturing process.
- Review and approve documentation: All documentation should be reviewed and approved by authorized personnel. This ensures that the documentation is accurate, complete, and up-to-date.
- Maintain documentation: All documentation should be maintained in accordance with the established requirements. This may include organizing the documentation in a logical and systematic manner, ensuring that it is easily accessible and searchable.
- Retain documentation: Documentation should be retained for an appropriate amount of time, as specified by regulatory requirements or company policies. This ensures that the documentation is available for future reference or review.
- Conduct periodic reviews: Periodic reviews of the documentation should be conducted to ensure that it remains current and accurate. Any necessary updates or revisions should be made promptly.
By following these steps, manufacturers can ensure that documentation is complete, accurate, and up-to-date, providing a clear record of all activities related to the manufacturing process. This facilitates quality control, regulatory compliance, and continuous improvement efforts.
Continuously Improve
Continuous improvement is a crucial aspect of quality control in chemical manufacturing. Continuous improvement involves continuously evaluating and improving all aspects of the manufacturing process, including procedures, equipment, personnel training, documentation, and testing. The following are the steps involved in continuously improving:
- Establish a culture of continuous improvement: A culture of continuous improvement should be established throughout the organization. This involves creating a mindset that encourages questioning and challenging current practices and seeking out opportunities for improvement.
- Collect and analyze data: Data should be collected and analyzed to identify areas for improvement. This may include analyzing product quality data, equipment performance data, and process data.
- Identify improvement opportunities: Based on the analysis of data, improvement opportunities should be identified. This may involve identifying areas for process optimization, equipment upgrades or replacement, or personnel training.
- Develop and implement improvement plans: Improvement plans should be developed and implemented to address the identified opportunities. This may involve developing new procedures, upgrading or replacing equipment, or providing additional personnel training.
- Monitor and evaluate progress: The progress of the improvement plans should be monitored and evaluated on an ongoing basis. This involves tracking the effectiveness of the implemented changes and making adjustments as necessary.
- Communicate and share results: The results of the improvement efforts should be communicated throughout the organization to encourage further improvement and to recognize the contributions of those involved in the improvement efforts.
By following these steps, manufacturers can continuously improve the manufacturing process, ensuring that products are consistently manufactured to the required specifications and that the manufacturing process remains efficient and cost-effective.
How can Deskera Help You?
Deskera's integrated financial planning tools allow investors to better plan their investments and track their progress. It can help investors make decisions faster and more accurately.
Deskera Books can assist you in automating your accounting and mitigating business risks. Deskera makes it easier to create invoices by automating many other procedures, reducing your team's administrative workload.
Deskera also offers a suite of integrated applications to help businesses manage their financials, inventory, and operations. Furthermore, other business aspects such as HR (Deskera People), CRM (Deskera CRM), and ERP are provided by Deskera. These could be crucial and can help short sellers keep track of their businesses and make better decisions.
Conclusion
In conclusion, the best practices for chemical manufacturing quality control can be summarized in the following bullet points:
- Develop a quality control plan and ensure that it is followed
- Use appropriate raw materials and ensure they are properly stored and handled
- Establish quality control procedures and maintain a clean and controlled environment
- Train personnel on proper procedures, safety, and quality control
- Conduct rigorous testing at all stages of the manufacturing process
- Use appropriate equipment and ensure it is calibrated, maintained, and qualified for performance
- Document all activities related to the manufacturing process and retain records for an appropriate amount of time
- Continuously evaluate and improve all aspects of the manufacturing process, including procedures, equipment, personnel training, documentation, and testing
By following these best practices, manufacturers can ensure that products are consistently manufactured to the required specifications, meet regulatory requirements, and are safe and effective for their intended use.
Related Articles
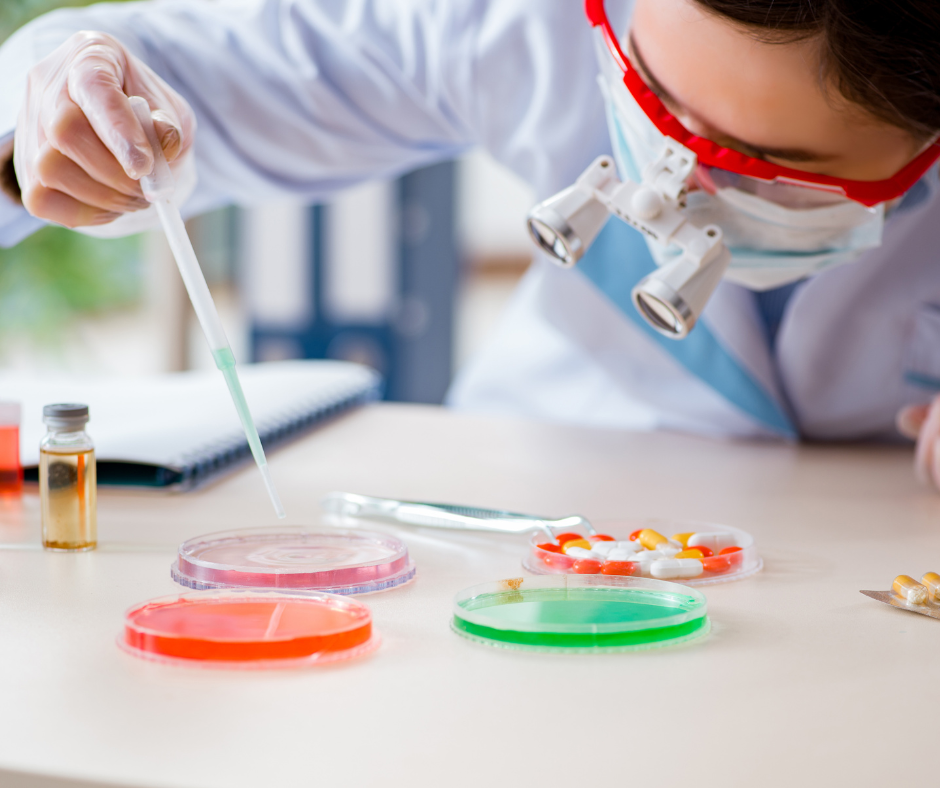
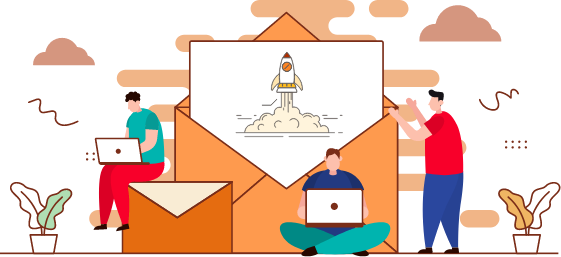
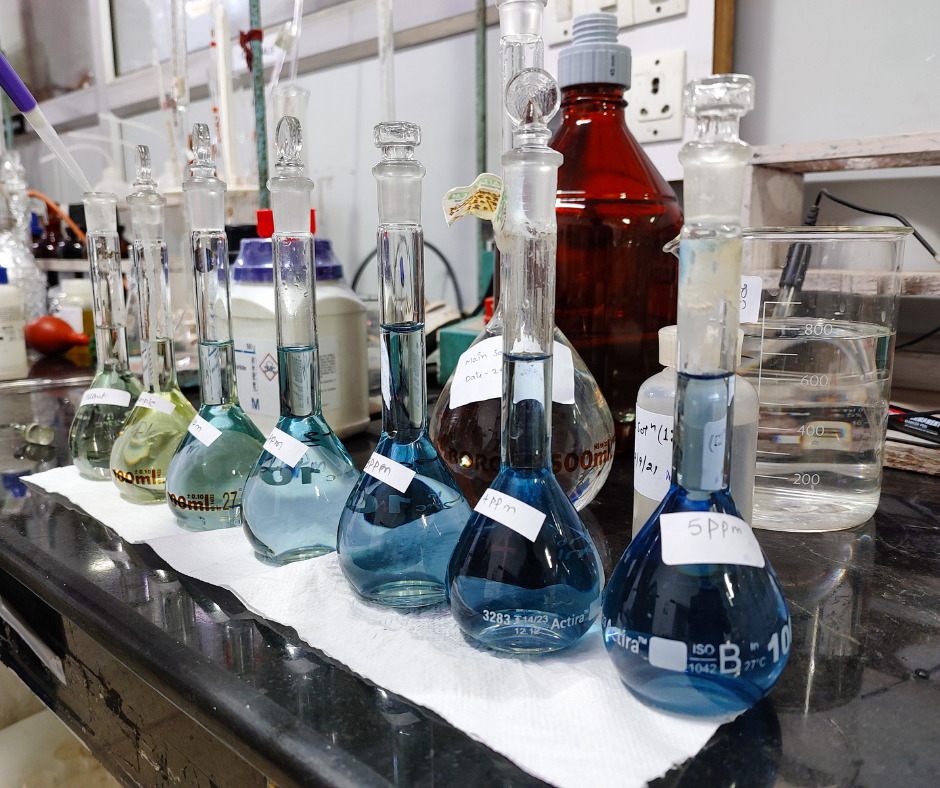
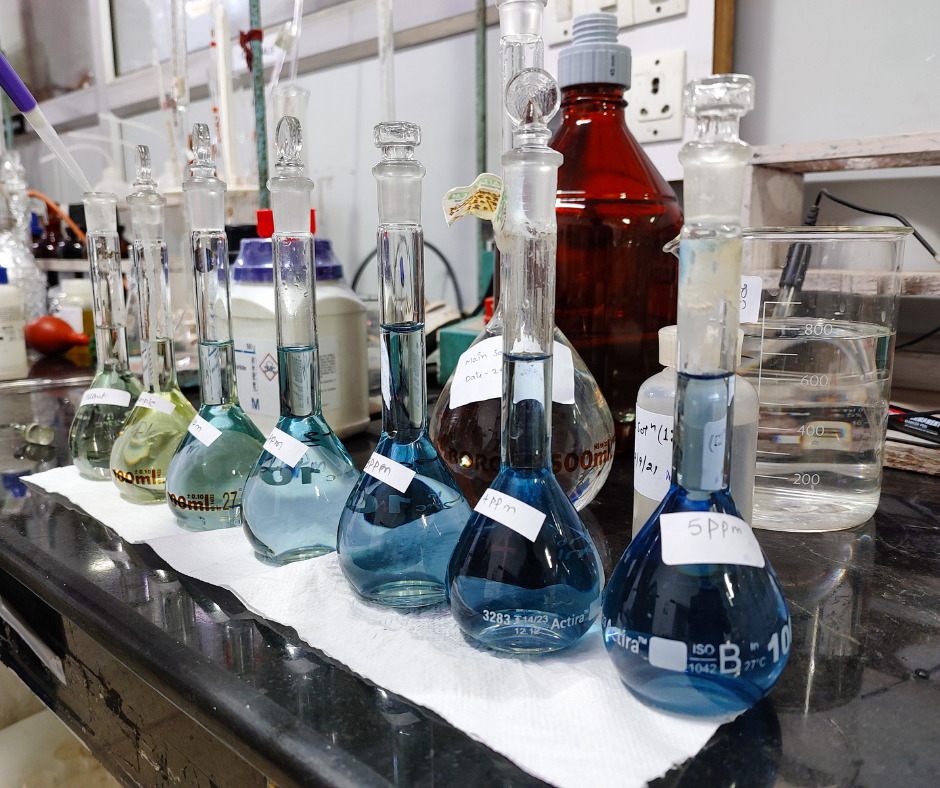