Is your stockroom a mess due to the presence of stock that has previously been produced? It is just as detrimental to your business to have an excessive amount of inventory as it is to have little supply. Both will put a financial burden on your company.
Producing a finished good that is then put up for sale can be done in a number of different ways. Your production approach will have an effect on the management of your inventory, and consequently, the experience that your customers have.
The term "assemble-to-order," or ATO, refers to a business model in which individual components of a product are gathered in advance, and the finished product is only put together when a consumer has placed an order for it.
It is essential to conduct a cost-benefit analysis of the build-to-order manufacturing approach before moving further with its implementation. They are discussed in this article, along with advice on how to successfully adopt an assemble-to-order production model.
- Make-to-Order (MTO) Vs. Assemble-to-Order (ATO)
- Understanding Assembly-to-Order Manufacturing
- Assembly-To-Order Process
- Advantages of the Assemble-To-Order Manufacturing System
- Disadvantages of Assemble-to-Order Manufacturing System
- Examples of Assemble-to-Order Products
- Tips to get started with Assemble-to-Order Manufacturing
- How can Deskera Help You with Assemble-to-Order Manufacturing?
- Key Takeaways
- Related Articles
The manufacturing procedures used today are very modern and have been perfected to maximize productivity. Methodologies, technologies, and even physical installations can scale up to have a tremendous influence on the bottom line if they can produce an ounce of additional savings or slash costs.
In today's industrial and manufacturing sectors, digital technologies for monitoring, synchronizing, and managing everything have become the driving force behind many efficiencies. This is not surprising when one considers the complexity of the processes that are involved. The industry has come to rely heavily on digital insights and management approaches to maintain smooth operations as a result of an increase in the number of orders received, a busier factory floor, and more packed production lines.
Make-to-Order (MTO) Vs. Assemble-to-Order (ATO)
First, a general introduction to Make to Order (MTO) and Assemble-to-Order (ATO) manufacturing processes.
Make to Order (MTO) and Assemble to Order (ATO) are two of the most popular manufacturing philosophies that are utilized today. Each technique makes it possible to respond quickly and nimbly to changing order flows in various manufacturing environments.
Make to Order manufacturing is activated when an order is received, as the name suggests. Make to Order manufacturing. This type of approach is known as a "pull" strategy since work is carried out in response to an order. MTO is useful for dealing with orders of a limited number and products that are not mass-produced.
Products that are manufactured using MTO processes often have high costs and large margins. There may be several stages, as well as professionals and independent contractors engaged.
That sofa that you ordered to meet the exact measurements of your living room with the design that you picked from a design that you picked from a vast catalog and that you had to wait for for a total of six weeks?
That would be considered MTO production.
The MTO concept has been streamlined into the Assemble to Order process, which is effectively the same thing.
In this context, "goods that just need to be assembled for the purposes of shipping to the client" refers to items that do not require any specialist labor processes or additional customization before they can be sent out to the customer.
On the opposite side of the spectrum is the Make to Stock (MTS) practice. Now let us talk about products that are routinely sold in large quantities while having a lower cost and margin overall.
These are items that are purchased and shipped in large quantities.
Because its primary objective is to maintain a healthy supply chain, this tactic is known as a "push" strategy. MTS manufacturing is responsible for the production of virtually all of the items that are sold in supermarkets.
There is always going to be some degree of process flow management involved, regardless of the manufacturing strategy that is being implemented. Both MTO and ATO are examples of processes that are reactive to orders.
It is possible that the availability of components will not coincide with the receipt of the order, which will result in lead time concerns and require vendors to be spoken with.
On the other hand, they offer the necessary flexibility to deliver goods that do not have a steady and predictable demand or that require a large degree of customization. This is because they have the ability to adapt to changing market conditions.
Make to Stock production functions under the assumption of consistent demand and orders, which are then factored into a production schedule.This calls for a very high level of coordination between the inventory and the storage facilities.
Even though the continuity of orders makes a high degree of stability possible, the integration of materials and processes still requires precise orchestration in order to prevent bottlenecks, guarantee that new orders are filled on time, and support the smooth movement of finished goods out the door.
The capability of MTS production to buy the necessary materials and components in large quantities, based on the anticipation of continuing and stable orders, is one of the production method's advantages.
Understanding Assembly-to-Order Manufacturing
Assembly-to-order manufacturing is a type of production system in which products are only assembled and delivered to customers after an order has been received. This is in contrast to mass production, in which products are manufactured in large quantities and then stored until they are sold.
There are several benefits to assembly-to-order manufacturing. It allows for greater customization of products, as each product can be built to meet the specific needs and preferences of the customer. Assembly-to-order also allows for more efficient use of resources, as products are only assembled as needed rather than being manufactured and stored in a warehouse. Additionally, because products are only assembled after an order has been received, there is less risk of excess inventory and associated carrying costs.
However, assembly-to-order manufacturing also has some challenges. It requires careful planning and coordination to ensure that the necessary components and materials are available when an order is received. It may also be more time-consuming and expensive to assemble products on an individual basis rather than in large batches.
Assembly-To-Order Process
In an assembly-to-order manufacturing system, the process typically starts with the receipt of an order from a customer. This order may include specific instructions or customizations for the product. The manufacturer then retrieves the necessary components and materials from inventory or orders them from suppliers, if necessary.
Next, the product is assembled according to the specifications of the order. This may involve using automated assembly equipment or manual labor. Once the product is complete, it is inspected for quality and then shipped to the customer.
In some cases, an assembly-to-order system may also include some level of modularity, where certain parts of the product can be customized or interchanged. This allows for even greater customization and can help to reduce lead times by allowing the manufacturer to use pre-assembled modules in the final product.
Overall, the goal of an assembly-to-order system is to efficiently produce customized products in a timely manner while minimizing excess inventory and waste.
Advantages of the Assemble-To-Order Manufacturing System
There are several benefits to using an assembly-to-order manufacturing system:
- Customization: Because products are only assembled after an order has been received, it is possible to offer a higher level of customization to customers. Each product can be built to meet the specific needs and preferences of the customer.
- Improved efficiency: An assembly-to-order system allows for more efficient use of resources because products are only assembled as needed, rather than being manufactured and stored in a warehouse. This can help to reduce excess inventory and associated carrying costs.
- Reduced lead times: Because products are only assembled after an order has been received, there is less risk of excess inventory and the need for long-term storage. This can help to reduce lead times and improve customer satisfaction.
- Improved quality: An assembly-to-order system allows for more thorough testing and inspection of each product before it is shipped to the customer. This can help to improve overall product quality.
- Flexibility: An assembly-to-order system can be more flexible and adaptable to changes in customer demand or market conditions. It allows manufacturers to adjust production to meet changing needs quickly.
Disadvantages of Assemble-to-Order Manufacturing System
While there are many benefits to using an assembly-to-order manufacturing system, there are also some disadvantages to consider:
- Higher cost: An assembly-to-order system may be more time-consuming and expensive to operate than mass production, as products are assembled on an individual basis rather than in large batches. This can increase the overall cost of the product.
- Planning and coordination: An assembly-to-order system requires careful planning and coordination to ensure that the necessary components and materials are available when an order is received. This can be a challenge, particularly if the manufacturer relies on a complex supply chain.
- Limited scalability: An assembly-to-order system may not be as efficient as mass production when it comes to producing large quantities of a single product. It may be more difficult to scale up production to meet high levels of demand.
- Limited efficiency: While an assembly-to-order system may be more efficient in terms of resource use, it may not be as efficient in terms of labor. Assembling products on an individual basis can be more time-consuming than mass production, which can impact overall efficiency.
- Limited product variety: An assembly-to-order system may not be well-suited to manufacturers that offer a wide variety of products, as it may be more difficult to keep all necessary components and materials in stock. This can limit the range of products that can be offered to customers.
Examples of Assemble-to-Order Products
There are many different types of products that can be produced using an assembly-to-order manufacturing system. Some examples include:
- Customized furniture: Companies that offer custom furniture often use an assembly-to-order system to produce pieces that are tailored to the specific needs and preferences of customers.
- Computers and electronics: Many computer and electronics manufacturers offer customizable options for their products, such as different processors, memory, or storage capacity. These options can be produced using an assembly-to-order system.
- Vehicles: Some car manufacturers offer a range of customizable options for their vehicles, such as different engines, trim levels, or exterior colors. These options can be produced using an assembly-to-order system.
- Industrial equipment: Companies that produce industrial equipment, such as conveyor systems or packaging machinery, may use an assembly-to-order system to build customized products that meet the specific needs of their customers.
- Home appliances: Some home appliance manufacturers offer customizable options for their products, such as different finishes or additional features. These options can be produced using an assembly-to-order system.
Tips to get started with Assemble-to-Order Manufacturing
If you are considering implementing an assembly-to-order production system, here are some tips to get started:
- Assess your business needs: Consider your business goals and the specific needs of your customers. Determine whether an assembly-to-order system is a good fit for your business and whether it will allow you to better meet the needs of your customers.
- Develop a plan: Create a detailed plan for implementing an assembly-to-order system. This should include identifying the necessary resources, establishing processes and procedures, and developing a timeline for implementation.
- Identify and prioritize customization options: Determine which customization options are most important to your customers and prioritize them. This will help you to more efficiently manage your inventory and production processes.
- Streamline your supply chain: An efficient supply chain is critical to the success of an assembly-to-order system. Work with your suppliers to ensure that the necessary components and materials are available when needed.
- Invest in technology: Technology can help to automate and streamline many aspects of an assembly-to-order production system. Consider investing in tools such as inventory management software or automated assembly equipment.
- Train your staff: Proper training is essential to the success of an assembly-to-order system. Make sure that your staff is familiar with the processes and procedures involved in assembling customized products.
How can Deskera Help You with Assemble-to-Order Manufacturing?
As a manufacturer or retailer, it is crucial that you stay on top of your manufacturing processes and resource management.
You must manage production cycles, resource allocations, safety stock, reorder points, and much more to achieve this.
Deskera MRP is the one tool that lets you do all of the above. With Deskera, you can:
- Track raw materials and finished goods inventory
- Manage production plans and routings
- Maintain bill of materials
- Optimize resource allocations
- Generate detailed reports
- Create custom dashboards
And a lot more.
It is also possible to export information and data on Deskera MRP from other systems. Additionally, Deskera MRP will give you analytics and insights to help you make better decisions.
So go ahead and book a demo for Deskera MRP today!
Key Takeaways
- The assemble-to-order production strategy benefits businesses with limited inventory storage and customers who are patient.
- Not only does it enable you to design products for which customers pay a premium, but it also eliminates dead stock, which costs retailers hundreds of dollars annually.
- Begin by picking products that lend themselves best to make-to-order production.
- Train your personnel on how to respond to ATO-related inquiries, and regularly monitor demand to avoid stockouts that drive away customers.
- Assemble-to-order (ATO) is a business technique in which items are rapidly produced from component parts upon the confirmation of an order. Assemble-to-order is a hybrid of make-to-stock and make-to-order.
- In a typical ATO approach, the costs associated with assembling the product from its components are low, whereas the costs associated with producing the many components can be high.
- For example, a PC manufacturer employing an assemble-to-order technique receives orders and then assembles customized computers using components such as keyboards, displays, and motherboards.
Related Articles
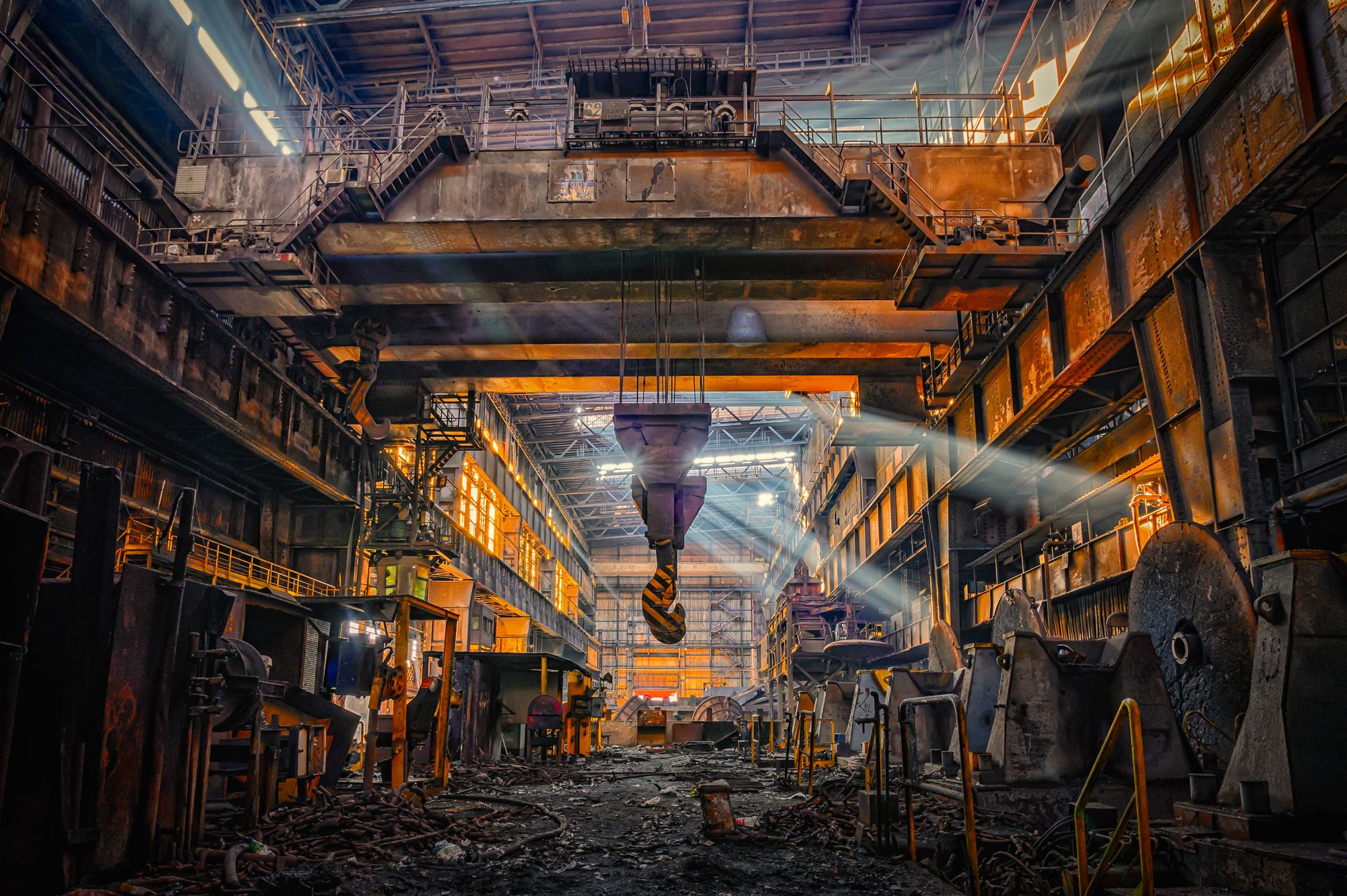
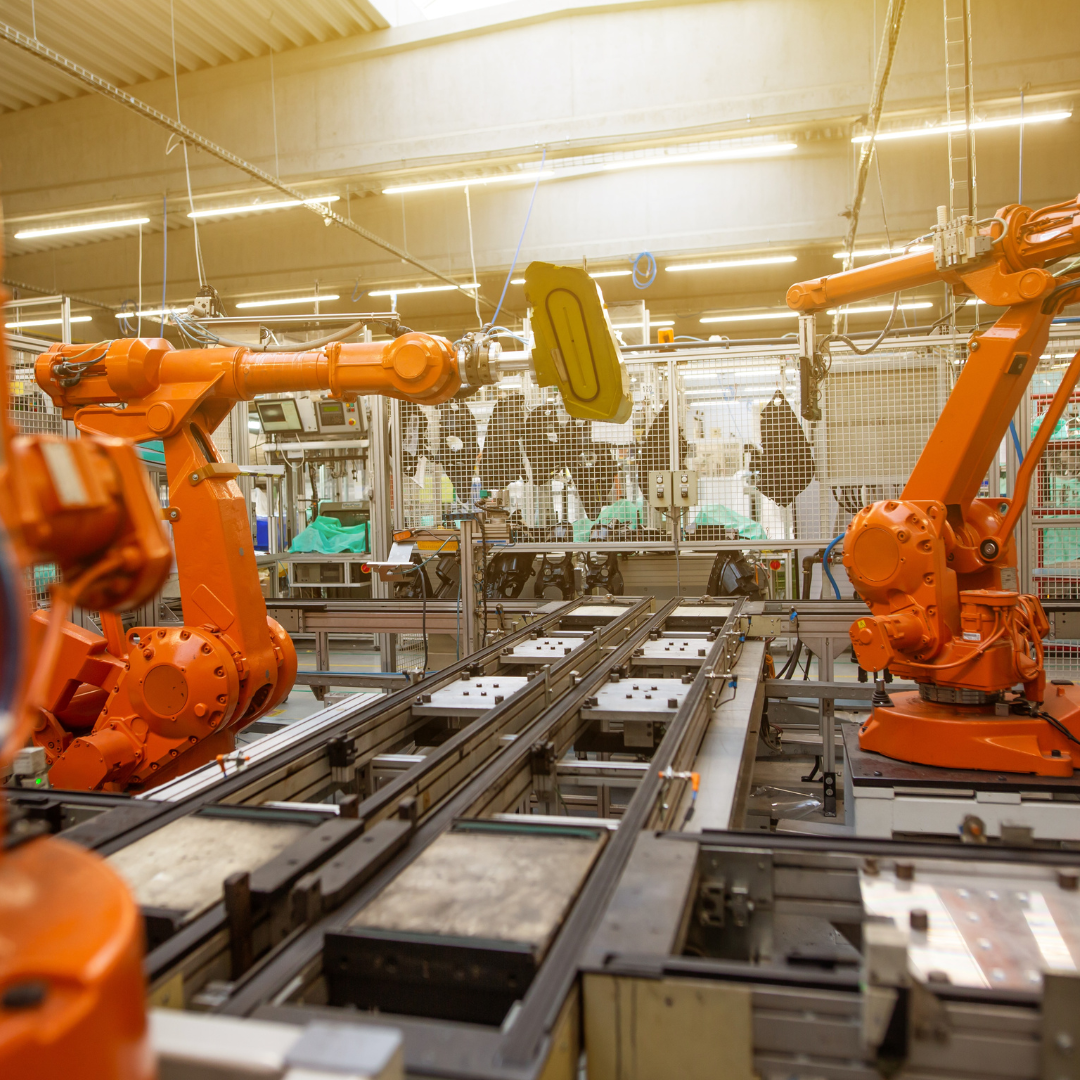
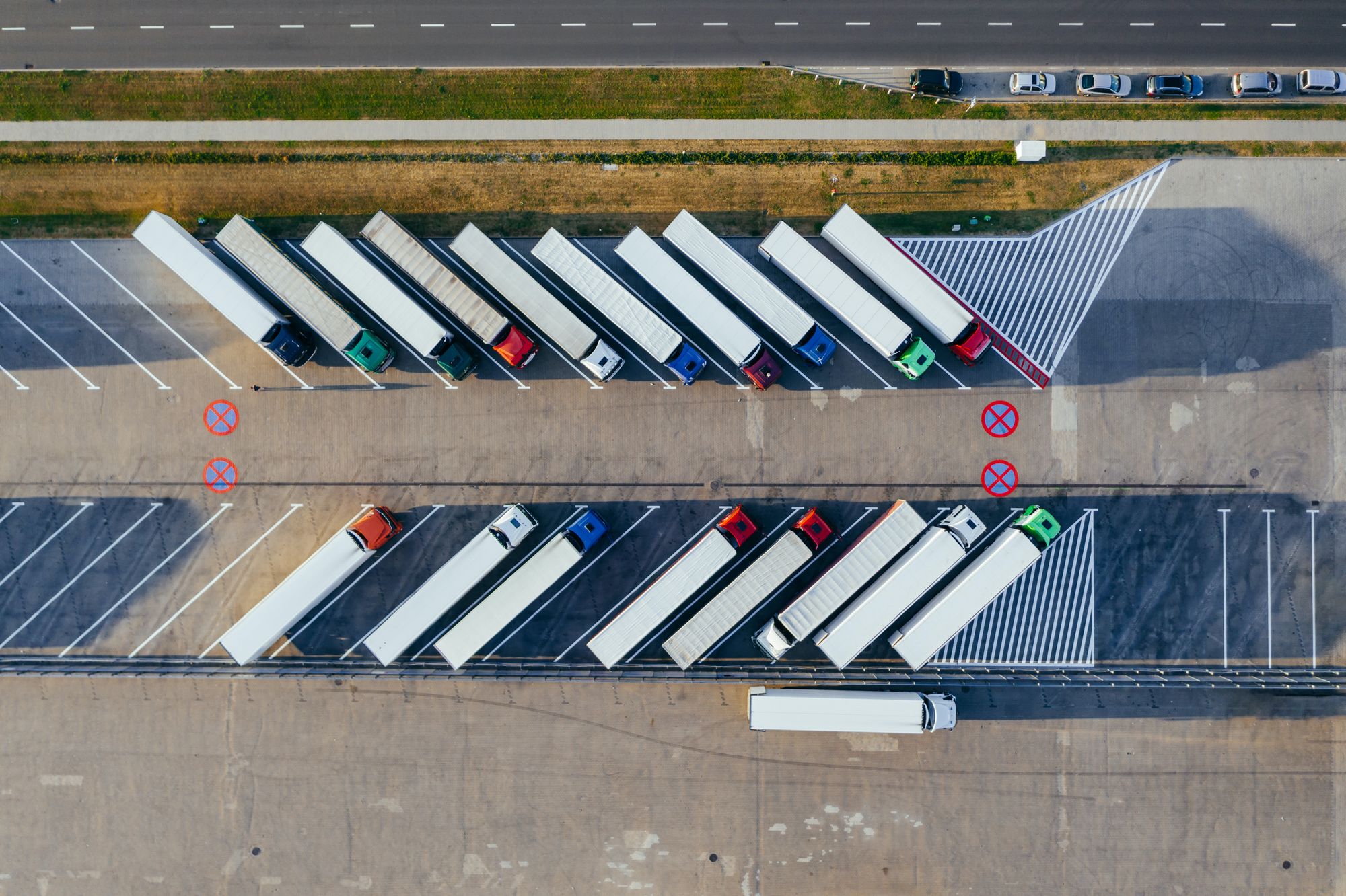
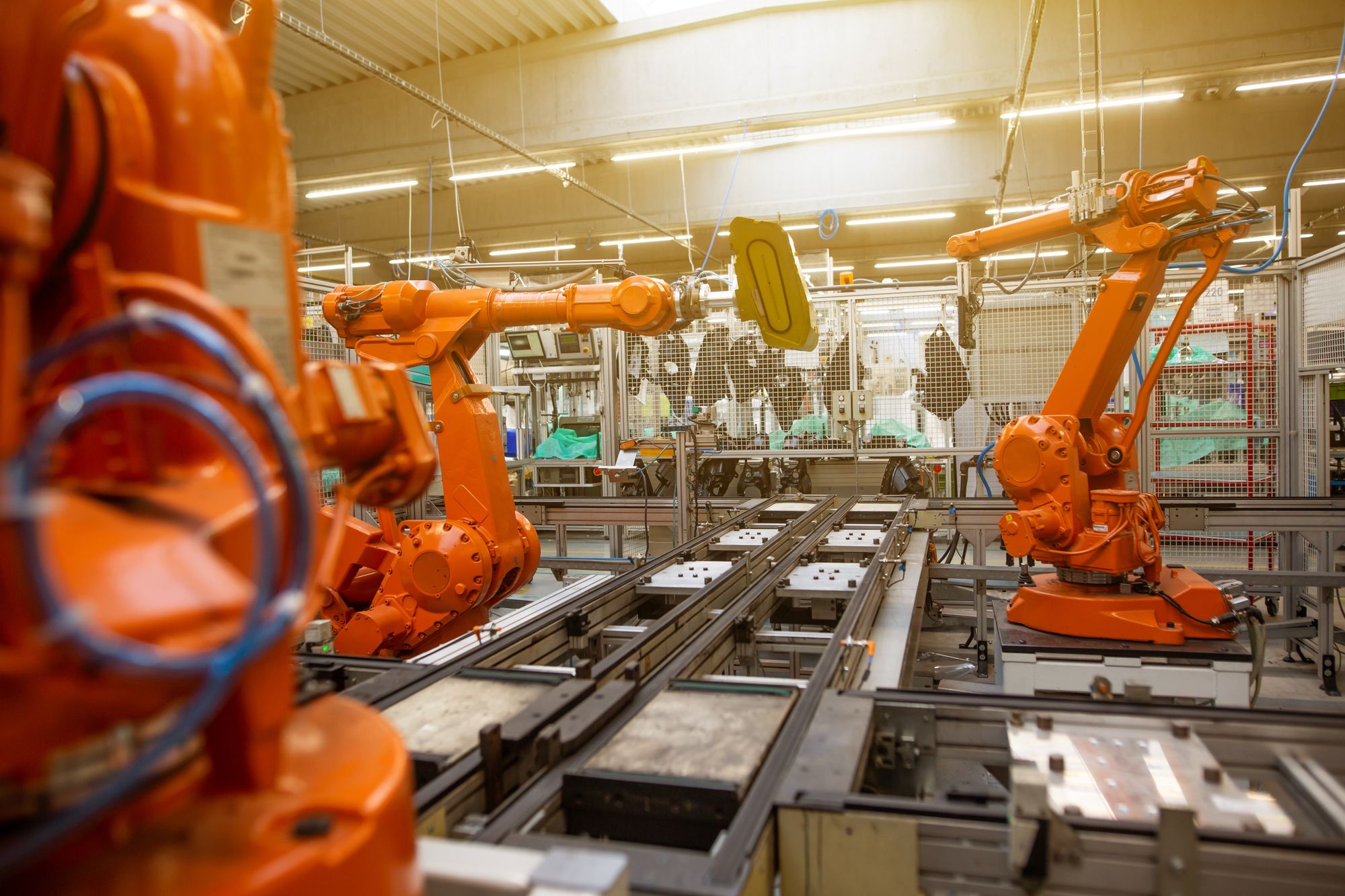