A BOM is a fact of life in the manufacturing world and plays a critical role in the development of any product. Simply put, you cannot manufacture a quality product without one.
In essence, a BOM is a comprehensive list detailing all the components and sub-assembled parts and raw materials needed to build your product. Let's find out what a BOM explosion is.
This article covers the following:
- What is a BOM explosion?
- What are the causes of a BOM explosion?
- How to mitigate the risk of a BOM explosion
- What is the cost of a BOM explosion
- What are the common scenarios of a BOM explosion
- How to avoid a BOM explosion
- What are the regulatory requirements for BOM explosion prevention?
- What are the best practices for BOM explosion prevention?
- How can Deskera assist you?
What is BOM Explosion?
BOM Explosion, or Bill of Materials Explosion, is a common term used in the manufacturing and supply chain industries. It refers to the process of breaking down a product’s components into a comprehensive list of individual components, materials, and specifications.
It is a critical step in the production process and is necessary for efficient and cost-effective manufacturing. The process of BOM explosion starts with an analysis of the product design and the required materials, components, and specifications. Each of the components is then broken down further into individual components, materials, and specifications.
This process is often referred to as “exploding” the BOM. The results of the BOM explosion are then used to determine the materials, components, and specifications that are necessary to produce the product. After the BOM is exploded, the materials, components, and specifications are then used to generate a complete bill of materials for the product.
This bill of materials includes detailed information about the components, materials, and specifications required to manufacture the product. It also includes any necessary instructions or other information that is necessary for the successful production of the product. Once the bill of materials is created, it is then used to create detailed instructions for the production process.
This includes the necessary steps to be taken, the order of steps, and the materials and components needed to complete the process. This information is used to create a production schedule that outlines how long each step will take and the resources necessary to complete the process. The BOM explosion process is an important part of the manufacturing process and is often used in conjunction with other processes such as quality control and product design.
This process is used to ensure that the product being manufactured meets all the necessary specifications, such as size, weight, and durability. It also helps to ensure that the product is produced efficiently and cost-effectively. Overall, BOM explosion is a critical part of the manufacturing process and is essential for ensuring that the product is produced efficiently and cost-effectively.
It is used to break down a product’s components into individual components, materials, and specifications and is used to create a detailed bill of materials for the product. It also helps to ensure that all the necessary instructions and resources are available for the successful production of the product.
What are the Causes of BOM Explosion?
The Bill of Materials (BOM) explosion is a phenomenon in the manufacturing industry that has caused a significant increase in the costs of the production process. It occurs when the number of components that are used in a product increases exponentially, resulting in an “explosion” of materials. While there are many factors that can cause a BOM explosion, some of the most common include
Complexity of Designs
As technology advances, the complexity of designs increases, resulting in more components being needed to create a product. In addition, as products become more sophisticated, the number of variants and versions of the product is also increasing, which further adds to the complexity of the BOM.
Increased Globalization of Manufacturing
With the advent of globalized manufacturing, the number of components used in a product can be sourced from different countries, resulting in a more complex BOM. In addition, the need to keep up with the latest trends and standards in different countries can also lead to increased complexity in the BOM.
Outsourcing
Many companies are turning to outsourcing for their production needs, resulting in an increase in the number of components that have to be sourced from different suppliers. This can also lead to a BOM explosion, as the components must be tracked and managed within the production process.
Increased Environmental Regulations
As environmental regulations become stricter; companies must adhere to stricter standards for their production processes. This can result in an increase in the number of components that are needed to meet the standards, leading to a BOM explosion.
Shortened Product Life Cycles
As companies strive to stay ahead of the competition, they often must shorten their product life cycles, resulting in an increase in the number of components that are needed to keep up with the latest trends. This can lead to a BOM explosion, as the components must be tracked and managed within the production process.
New Technologies
As new technologies become available; manufacturers must incorporate them into their production processes. This can result in an increase in the number of components that are needed to keep up with the latest trends, leading to a BOM explosion.
Increased Competition
As competition between manufacturers increases, they often must reduce the cost of their products in order to remain competitive. This can result in a BOM explosion, as the number of components that must be sourced in order to keep the costs down increases. The BOM explosion phenomenon can have a significant impact on the costs of production, as well as the overall efficiency of the process.
In order to effectively manage the complexity of the BOM, manufacturers must ensure they are using the most efficient processes and that they are effectively tracking the components that are used in the production process. This will help to ensure that the costs associated with the BOM are kept to a minimum while still being able to meet the demands of the customer.
How to Mitigate the Risk of BOM Explosion?
The bill of materials (BOM) is a critical component of any manufacturing process. It is a document that lists all of the components, materials, and other items that are needed to produce a product.
The BOM provides a clear understanding of the components and materials needed to build the product, as well as their associated costs. However, a BOM explosion is a common problem and can lead to costly delays, mistakes, and other issues.
A BOM explosion occurs when a product has too many parts, and the complexity of the product increases exponentially. This can lead to a number of issues, such as an increase in manufacturing costs and an increase in the number of parts needed in the production process.
It can also lead to a decrease in quality, as more parts increase the likelihood of errors. Fortunately, there are a number of steps that can be taken to mitigate the risk of a BOM explosion.
The first step is to ensure that the BOM is well-organized and easy to read. This will help to reduce the complexity of the product, as well as make it easier to identify any potential issues with the parts. Additionally, it is important to create a comprehensive list of all the parts and materials needed in the manufacturing process.
This will allow for better planning and the ability to identify any potential issues with the parts more quickly. It is also important to limit the number of parts and materials used in the manufacturing process. This can be done by using standard parts and materials, as well as using fewer components in the product.
Additionally, it is important to test all parts and materials used in the production process, as this will help to ensure that they meet the required specifications. Finally, it is important to include a review process in the BOM.
This will allow for any potential issues to be identified and addressed before they become a problem. Additionally, this review process should include a risk assessment, which will help to identify any potential areas of concern. By following these steps, companies can significantly reduce the risk of a BOM explosion.
This will help to ensure that the production process runs smoothly and that the product meets the required quality standards. Additionally, it will help to reduce the overall costs associated with manufacturing, as fewer parts and materials are needed. Ultimately, mitigating the risk of a BOM explosion is essential for any successful manufacturing process.
What is the Cost of a BOM Explosion?
Bill of Materials (BOM) explosion is a term used to describe the drastic increase in the number of components required to produce a single product. It occurs when a manufacturer or a designer overlooks the complexity of the product they are creating and fails to identify the components necessary to create the desired product.
With the BOM explosion, the cost of production increases dramatically due to the additional components that must be purchased and assembled. The cost of a BOM explosion can be seen in the actual materials, labor, and time required to produce the product. In addition, it can also be seen in the cost of additional parts, labor, and production time required to assemble and test the product.
To understand the cost of a BOM explosion, one must first understand the concept of “component-level engineering,” which refers to the process of designing each component separately. This process often leads to additional components, which increase the cost of production. For example, a manufacturer may design a computer with five components.
However, if the components are not designed properly, the design may require seven components, which increases the cost of producing the computer. In addition, the cost of assembly, testing, and manufacturing of the additional components can be extremely costly.
The cost of a BOM explosion can also be seen in the cost of the materials and the labor required to produce the product. With the BOM explosion, the number of components required to create a product increases, requiring the manufacturer to purchase more expensive materials, such as components with higher quality or components that are difficult to find.
Furthermore, the labor cost associated with assembling the additional components can be much higher than the labor cost associated with assembling the original components. The cost of a BOM explosion can also be seen in the time required to produce the product.
With a BOM explosion, the number of components required to produce a product can increase significantly, requiring more time to assemble and test the product. This can lead to delays in production and delivery, resulting in a poor customer experience and potential financial losses.
Finally, the cost of a BOM explosion can be seen in the cost of additional testing and quality assurance. With a BOM explosion, the manufacturer may be forced to conduct additional testing and quality assurance in order to ensure the quality of the product. This can result in additional expenses, such as hiring a third-party testing agency or purchasing additional testing equipment.
In summary, the cost of a BOM explosion can be seen in the actual materials, labor, time, and additional testing and quality assurance required to produce the product. The cost of a BOM explosion can be very high and should be taken into account when designing a product.
By understanding the potential cost of a BOM explosion, manufacturers and designers can take steps to prevent the occurrence of a BOM explosion and reduce the overall cost of production.
What are the Common Scenarios in BOM Explosion?
A bill of materials (BOM) explosion is the process of taking a single master bill of materials and expanding it out to create a detailed list of all the individual components that make up the product. This process is essential for manufacturing planning, procurement, and costing.
It allows manufacturers to efficiently source and purchase the components needed to build the product, as well as to accurately cost the product. The most common scenarios for a BOM explosion are when a manufacturer is developing a new product, when existing products are being modified, or when existing products are being reproduced.
For new product development, the BOM explosion is used to create a complete list of all the components that are required to manufacture the product. This includes parts, assemblies, and subassemblies. In addition to the individual components, the BOM explosion will also include information such as the quantity of each component needed, the source of supply, and the cost of each component.
This information is then used to create a complete inventory of all the components required to manufacture the product. For modifications to existing products, the BOM explosion is used to identify which components will need to be changed or added in order to make the desired modification.
This includes parts, assemblies, and subassemblies. Again, the BOM explosion will include information such as the quantity of each component needed, the source of supply, and the cost of each component. When existing products are being reproduced, the BOM explosion is used to ensure that the reproduced product is the same as the original. This includes parts, assemblies, and subassemblies.
The BOM explosion will also include information such as the quantity of each component needed, the source of supply, and the cost of each component. This ensures that the reproduced product is exactly the same as the original. In addition to the scenarios mentioned above, BOM explosions are also used for other purposes such as cost estimation, capacity planning, and parts list maintenance.
These are all essential steps in the manufacturing process and are used to ensure that the product is produced in a timely and cost-effective manner. Overall, BOM explosions are an essential part of the manufacturing process.
They allow manufacturers to accurately source and purchase the components needed to build the product, as well as to accurately cost the product. In addition, they are used for other purposes, such as cost estimation, capacity planning, and parts list maintenance. By using BOM explosions, manufacturers can ensure that their products are produced in a timely and cost-effective manner.
How to Avoid BOM Explosions?
The first step in avoiding a BOM explosion is to use a flexible bill of a materials management system. This system should allow for the creation of a detailed bill of materials that accurately reflects the complexity of the product being manufactured. The system should also allow for easy revision and updating of the BOM as necessary.
Having a comprehensive and up-to-date BOM is essential to reducing the likelihood of a BOM explosion. The second step to avoiding BOM explosion is to carefully examine each component and material used in the production process.
Manufacturers should ensure that each component and material used is necessary for the final product. Unnecessary components and materials should be removed, as they are likely to contribute to BOM explosion.
Additionally, a process should be created to ensure that components and materials are chosen based on their quality, cost, and availability. The third step in avoiding BOM explosion is to streamline the production process. This can be achieved through the use of automation, process simplification, and eliminating bottlenecks. Automation can reduce the amount of time spent on each task, simplifying the process and reducing the likelihood of errors.
Process simplification can also help to reduce the amount of time and materials needed to create the final product. By eliminating bottlenecks, production can be sped up, and BOM explosion can be avoided. The fourth step to avoiding a BOM explosion is to maintain a close relationship with suppliers.
By keeping suppliers informed of changes to the BOM and production process, manufacturers can ensure that the right components and materials are available when needed. This can help to reduce delays in production, as well as potential BOM explosions.
Finally, to avoid BOM explosion, manufacturers should review their BOMs regularly. This can help to identify any potential problems before they cause delays or increased costs. By performing regular reviews, manufacturers can ensure that their BOMs are accurate, up-to-date, and complete.
By following these five steps, manufacturers can reduce the likelihood of BOM explosion and its associated problems. By carefully managing their BOMs, streamlining their production processes, maintaining strong relationships with suppliers, and regularly reviewing their BOMs, manufacturers can create more efficient and cost-effective production processes.
What are the Regulatory Requirements for BOM Explosion Prevention?
BOM Explosion Prevention is a critical requirement for businesses that manufacture products. With the increasing complexity of products and the increasing number of components and materials used in the manufacturing process, it is essential for manufacturers to have effective measures in place to prevent BOM explosions.
A BOM (Bill of Materials) is a list of all the parts and components that are used in the production of a product. With a complex product, the BOM can include hundreds of individual items. If a BOM is not managed properly, it can lead to significant waste, delays, and, ultimately, a decrease in product quality.
A BOM explosion occurs when a product requires more components than originally anticipated, leading to a large number of additional components and materials that must be tracked and managed.
In order to prevent BOM explosions, manufacturers must comply with industry-specific regulatory requirements. These requirements vary from industry to industry but typically include:
Developing and implementing a comprehensive BOM management program:
This program should include all aspects of BOM management, including the creation, maintenance, and monitoring of BOMs.
Establishing a process for reviewing and updating BOMs on a regular basis:
This process should include a review of the BOM for accuracy and completeness, as well as a review of the materials and components used in the manufacturing process.
Working with suppliers to ensure that the correct parts and materials are being supplied. The supplier should be able to provide reliable and timely delivery of components and materials.
Ensuring that the BOM is updated in a timely manner to reflect any changes in the product design or components used. This can be done by having a formal process in place that requires all changes to be reviewed and approved.
Establishing a process for tracking and monitoring BOMs to ensure that the components are being used correctly and that any changes are being accurately reflected in the BOM. This can be done through an ERP system or other software.
Having an effective system for managing and archiving obsolete BOMs. This system should include a mechanism for tracking changes in the BOM and for keeping a historical record of the BOMs.
Establishing a process for validating changes to the BOM. This process should include a review of the changes to ensure that the revised BOM accurately reflects the components used in the manufacturing process.
By following these regulatory requirements and having an effective BOM management system in place, manufacturers can reduce the risk of BOM explosions and ensure the quality of their products.
A well-managed BOM system is essential for effectively managing the complexity of today’s products and ensuring that the components used in the manufacturing process are of the highest quality.
What are the Best Practices for BOM Explosion?
Utilizing Design for Manufacturing (DFM) Principles
Design for Manufacturing (DFM) principles can help ensure that a BOM explosion is prevented. These principles focus on the design aspect of a product and ensure that all components are optimized for the production process, eliminating any unnecessary components.
Use Modularity and Standardization
By utilizing modular components and standardizing parts, manufacturers can reduce the complexity of the BOM and avoid BOM explosion. This helps to reduce the number of components and makes them easier to source and manage.
Utilize Software Tools
There are a variety of software tools available to help manufacturers manage their BOMs and reduce BOM explosion. These tools help to automate the process of creating, managing, and tracking BOMs, ensuring accuracy and reducing the possibility of errors.
Perform Regular Reviews
Regular reviews of the BOM can help to identify any errors or unnecessary components. This allows manufacturers to make the necessary changes to their BOMs and avoid BOM explosion.
Communicate with Suppliers
Effective communication with suppliers can help to ensure that any changes to the BOM are communicated in a timely manner. This helps to avoid any confusion that could lead to a BOM explosion.
How Can Deskera Assist You?
Remember discussing best-in-class inventory software? There is no way you can find anything as well-equipped as the Deskera inventory software. Deskera inventory software allows you to closely monitor the manufacturing process.

Key Takeaways:
- Bom explosion refers to the process of breaking down a product’s components into a comprehensive list of individual components, materials, and specifications.
- With the advent of globalized manufacturing, the number of components used in a product can be sourced from different countries, resulting in a more complex BOM.
- The BOM explosion phenomenon can have a significant impact on the costs of production, as well as the overall efficiency of the process.
- Finally, to avoid BOM explosion, manufacturers should review their BOMs regularly.
- It is essential for manufacturers to have effective measures in place to prevent BOM explosions.
- There are a variety of software tools available to help manufacturers manage their BOMs and reduce BOM explosion.
Related Articles:
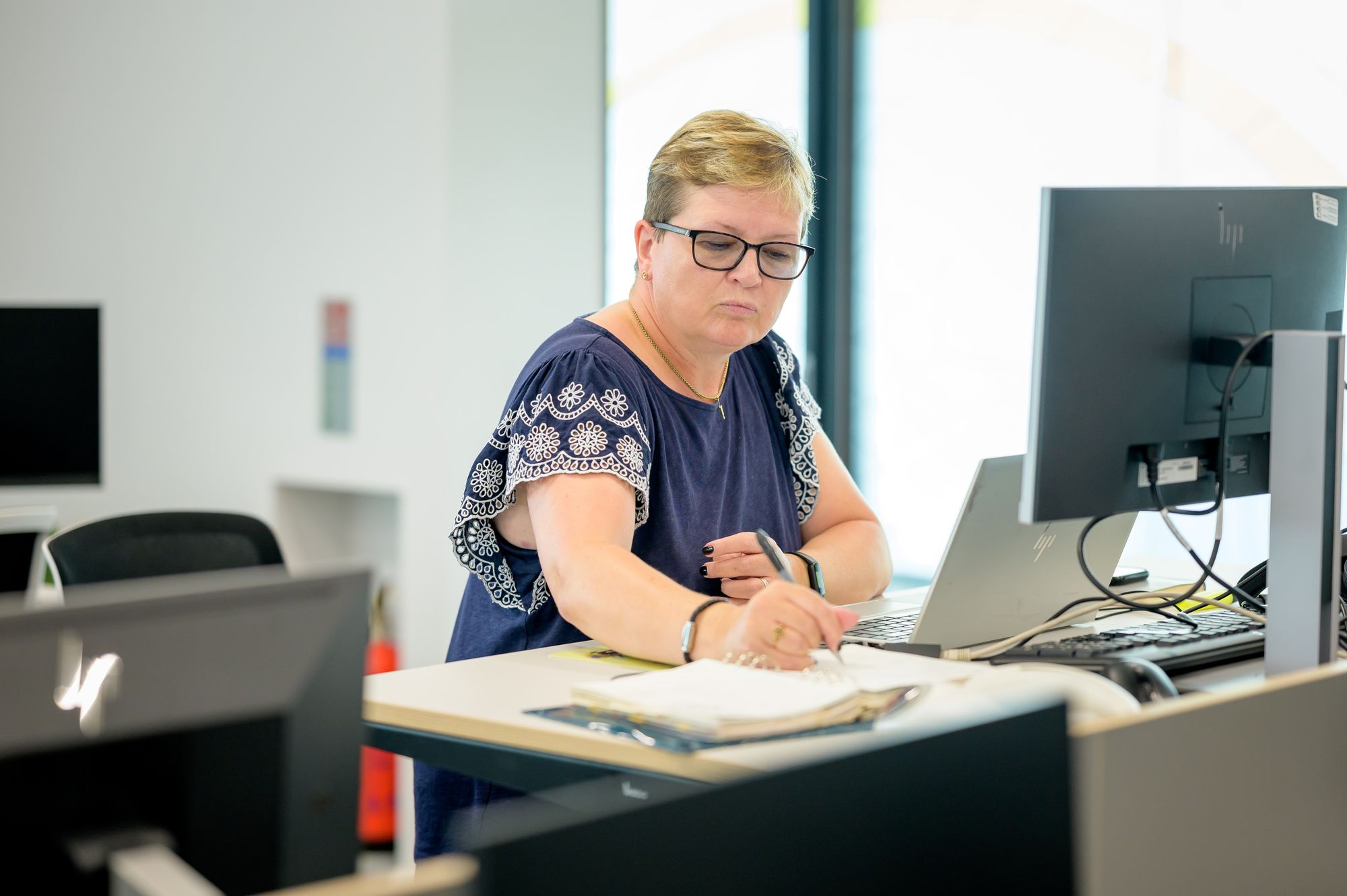
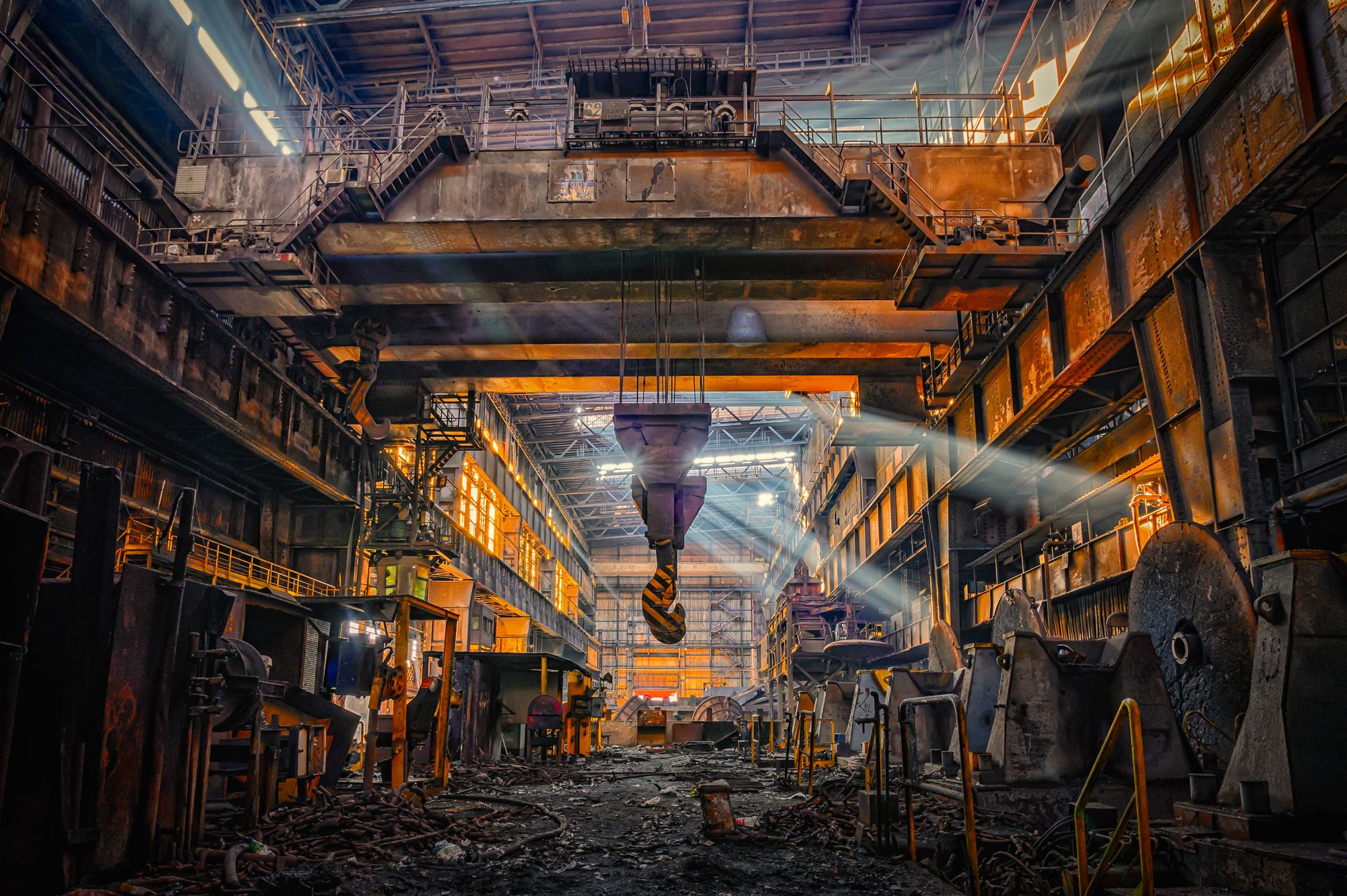
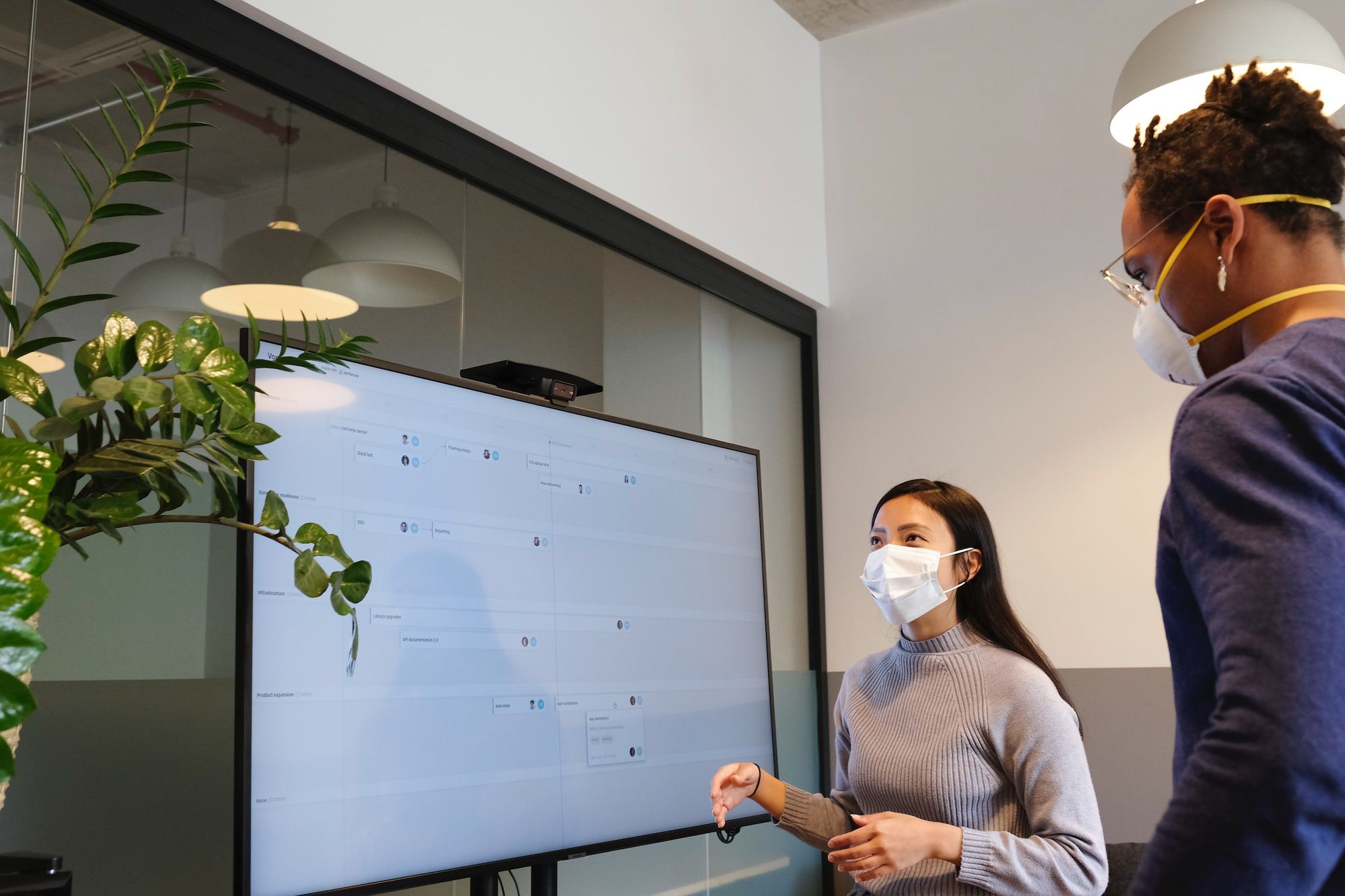