The global warehouse management system market was valued at USD 3.94 billion in 2023 and is expected to grow at a compound annual growth rate (CAGR) of 19.5% from 2024 to 2030.
The expansion of economies worldwide has driven sectors such as healthcare, manufacturing, and retail to optimize their operations to boost output and meet consumer demand. To address increasing demands, logistics companies are continuously evolving to tackle challenges posed by fluctuating product markets and shipping schedules.
As businesses strive for efficiency and adaptability, adopting best practices in warehouse management becomes crucial. Implementing effective strategies can lead to significant improvements in productivity, accuracy, and overall operational efficiency. This article will delve into 24 warehouse management best practices to help you streamline your processes and achieve optimal performance.
One of the tools that can significantly aid in achieving these best practices is Deskera ERP. Deskera ERP is a comprehensive enterprise resource planning software designed to automate and integrate key business processes, including inventory management, order processing, and logistics.
By leveraging Deskera ERP, businesses can enhance their warehouse operations, gain real-time visibility into inventory levels, and improve decision-making capabilities. This powerful tool helps organizations manage their resources more effectively, ensuring they remain competitive in a dynamic market.
What is Warehouse Management?
Warehouse management involves the administration and control of operations within a warehouse. This encompasses a variety of activities aimed at ensuring the efficient and effective storage, handling, and movement of goods within the warehouse. Key aspects of warehouse management include:
- Inventory Control: Monitoring and managing stock levels to ensure optimal inventory, prevent stockouts, and minimize excess stock.
- Order Fulfillment: Picking, packing, and shipping orders accurately and efficiently to meet customer demands.
- Receiving and Putaway: Handling incoming shipments, checking for accuracy and quality, and placing items in the correct storage locations.
- Storage Management: Organizing the warehouse layout to maximize space utilization and facilitate easy access to items.
- Labor Management: Scheduling and managing warehouse staff to ensure tasks are completed efficiently and safely.
- Safety and Compliance: Ensuring that the warehouse operates in accordance with health, safety, and regulatory standards.
- Technology Utilization: Implementing warehouse management systems (WMS) and other technologies to automate processes, improve accuracy, and provide real-time data for better decision-making.
- Continuous Improvement: Regularly evaluating and optimizing warehouse processes to enhance productivity and reduce costs.
Effective warehouse management is crucial for maintaining a smooth supply chain, meeting customer expectations, and achieving business goals.
Importance of Good Warehousing Practices
Good warehousing practices are vital for the efficient and effective operation of a supply chain.
Here are detailed reasons highlighting the importance of these practices:
Improved Efficiency and Productivity
- Streamlined processes, such as optimized picking paths and automated workflows, reduce the time and effort required for picking, packing, and shipping.
- Advanced technologies like barcode scanners, RFID, and voice-directed picking can further enhance speed and accuracy, leading to faster order fulfillment and reduced labor costs.
Enhanced Inventory Accuracy
- Implementing systematic inventory control methods, such as cycle counting and ABC analysis, ensures accurate tracking of stock levels.
- This prevents stockouts and overstock situations, ensuring that the right amount of stock is available when needed, which helps in meeting customer demands and reducing excess inventory holding costs.
Cost Savings
- Efficient use of space through strategic layout planning and the use of vertical storage solutions reduces the need for additional warehouse space.
- Proper resource and labor management minimizes waste and optimizes the use of available resources, leading to significant operational cost reductions.
Customer Satisfaction
- Timely and accurate order fulfillment ensures that customers receive their products as expected, enhancing customer satisfaction and loyalty.
- Implementing real-time tracking and notifications improves transparency and keeps customers informed about their orders, further enhancing their experience.
Safety and Compliance
- Adhering to safety standards, such as OSHA regulations, and implementing proper safety protocols minimize the risk of workplace accidents and injuries.
- Regular training for employees on safety practices and the use of personal protective equipment (PPE) ensures a safer work environment.
Better Space Utilization
- Effective layout and storage solutions, like narrow aisle racking and mezzanine floors, maximize the use of available space.
- This allows for more inventory to be stored without the need for additional warehouse space, optimizing the overall storage capacity of the warehouse.
Improved Data Accuracy
- Implementing warehouse management systems (WMS) provides real-time data on inventory levels, order statuses, and warehouse operations.
- This data enables better decision-making, strategic planning, and timely response to market changes or operational issues.
Scalability
- Good practices allow for easier scaling of operations as the business grows, accommodating increased inventory and order volumes without compromising efficiency.
- Scalable solutions, like modular shelving systems and automated storage and retrieval systems (AS/RS), ensure that the warehouse can adapt to changing demands.
Reduced Shrinkage and Damage
- Proper handling and storage of goods, along with regular audits and security measures, reduce the risk of product damage and loss due to theft or mishandling.
- Implementing quality control checks at various stages ensures that inventory remains in saleable condition, maintaining product quality and reducing returns.
Enhanced Flexibility
- Efficient warehouse operations can adapt more quickly to changes in market demand, supply chain disruptions, or seasonal fluctuations.
- Flexible storage solutions, like mobile racking systems, and adaptable workforce management strategies, such as cross-training employees, ensure that the warehouse can respond promptly to varying needs.
In summary, good warehousing practices are essential for maintaining a competitive edge, optimizing operations, and achieving overall business success. They ensure that the warehouse functions as a crucial link in the supply chain, contributing to the smooth flow of goods from suppliers to customers.
Top 23 Warehouse Management Best Practices
In the dynamic world of logistics and supply chain management, mastering warehouse operations is crucial for optimizing efficiency, reducing costs, and ensuring customer satisfaction.
To stay competitive and meet the ever-evolving demands of the industry, businesses must adopt a comprehensive set of strategies.
Here, we explore the top 23 warehouse management best practices designed to enhance your operations, streamline processes, and drive success in the fast-paced realm of warehousing and distribution.
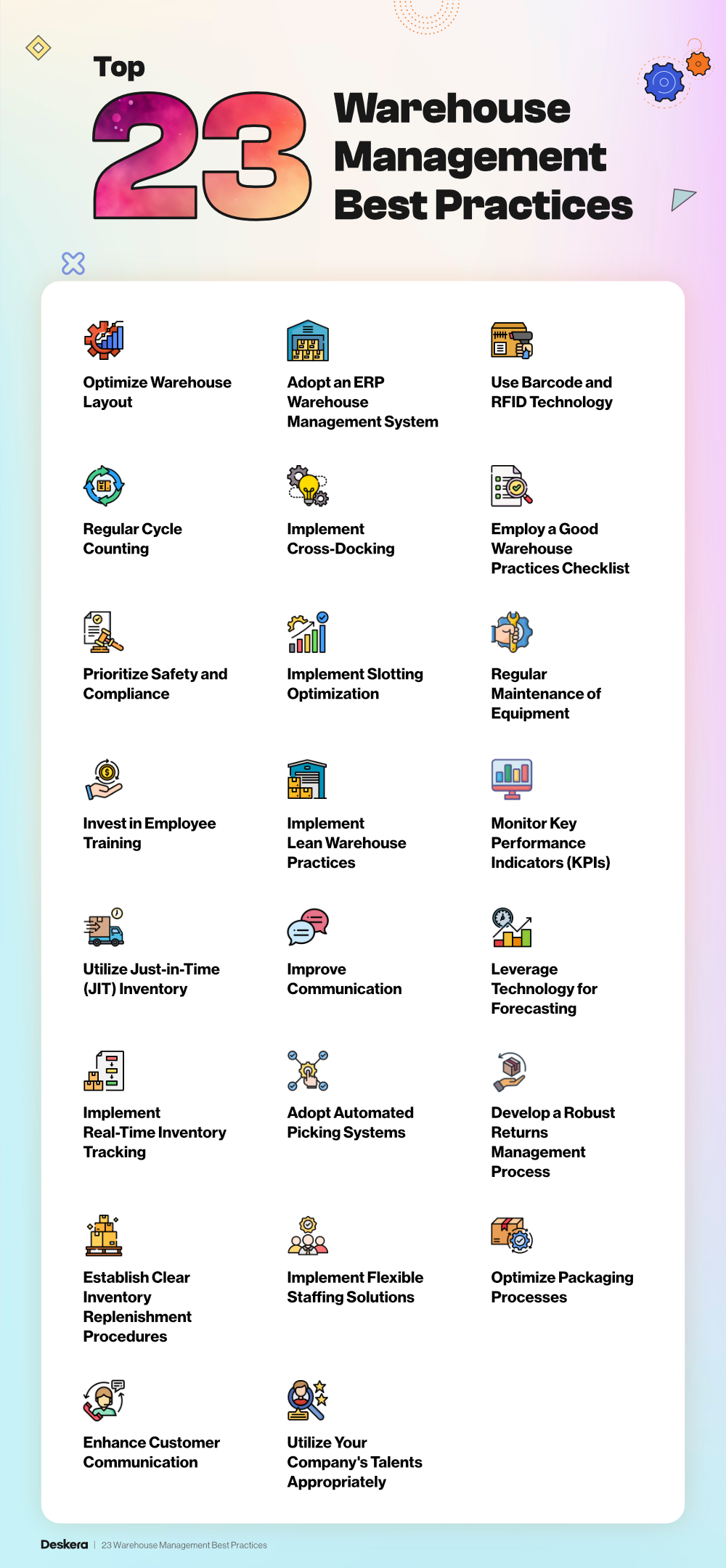
1.Optimize Warehouse Layout
Optimizing the warehouse layout is essential for improving operational efficiency, reducing handling times, and maximizing storage capacity.
A well-planned layout enhances workflow, minimizes travel time, and supports effective inventory management, leading to increased productivity and reduced costs.
- Conduct a Needs Assessment: Begin by assessing the specific needs and requirements of your warehouse operations. Consider factors such as inventory types, order volume, picking methods, and workflow processes. A thorough needs assessment helps design a layout that aligns with operational goals and optimizes space utilization.
- Design Efficient Storage Solutions: Choose appropriate storage solutions based on the types of inventory and the volume of goods handled. Options include pallet racking, shelving, bin storage, and automated storage systems. Efficient storage solutions maximize space, facilitate easy access, and support effective inventory management.
- Implement an Effective Flow Design: Design the warehouse layout to support a smooth flow of goods from receiving to storage, picking, packing, and shipping. Arrange workstations and storage areas to minimize unnecessary movement and handling. A well-planned flow design reduces travel time and enhances overall operational efficiency.
- Utilize Slotting Strategies: Apply slotting strategies to optimize the placement of inventory within the warehouse. Place high-turnover items in easily accessible locations and group similar items together. Slotting reduces travel time, improves picking efficiency, and ensures that frequently accessed items are readily available.
- Incorporate Technology and Automation: Integrate technology and automation into the warehouse layout to enhance efficiency. Implement systems such as conveyor belts, sorting systems, and automated picking solutions. Technology supports faster processing, reduces manual labor, and improves accuracy in handling goods.
- Optimize Aisle and Traffic Flow: Design aisles and traffic flow to facilitate smooth movement of goods and personnel. Ensure that aisles are wide enough for equipment and forklifts to maneuver safely. Plan for clear traffic patterns and avoid bottlenecks to maintain a streamlined flow of operations.
- Allocate Space for Staging and Sorting: Designate specific areas for staging and sorting goods. Staging areas are used for temporarily holding goods before they are processed or shipped, while sorting areas help organize items for efficient picking and packing. Properly allocated staging and sorting areas improve workflow and reduce congestion.
- Consider Future Growth and Flexibility: Design the warehouse layout with future growth and flexibility in mind. Allow for potential expansions, changes in inventory types, and adjustments to workflows. A flexible layout can accommodate evolving business needs and support long-term operational efficiency.
- Monitor and Review Layout Performance: Regularly monitor and review the performance of the warehouse layout to identify areas for improvement. Gather feedback from staff, analyze operational metrics, and assess the impact of layout changes on efficiency and productivity. Continuous review ensures that the layout remains effective and responsive to operational needs.
- Involve Employees in the Design Process: Engage warehouse staff in the layout design process to gain insights into practical challenges and preferences. Employees who are directly involved in warehouse operations can provide valuable input on workflow, storage needs, and efficiency improvements. Involving staff ensures that the layout meets their needs and enhances overall productivity.
2. Adopt an ERP Warehouse Management System
Adopting an Enterprise Resource Planning (ERP) Warehouse Management System (WMS) integrates inventory management with broader business processes, enhancing overall operational efficiency and data accuracy.
This means that an ERP warehouse management system will also give you the features of an warehouse inventory management system.
An ERP WMS streamlines warehouse operations, improves visibility, and supports strategic decision-making by providing a unified platform for managing inventory, orders, and logistics.
- Choose the Right ERP WMS Solution: Select an ERP WMS that aligns with your warehouse requirements and integrates seamlessly with your existing ERP system. Consider factors such as scalability, functionality, user interface, and compatibility with other business applications. The right solution should support your specific operational needs and facilitate smooth data flow across departments.
- Integrate Warehouse Operations with ERP: Ensure that the ERP WMS integrates with other business functions, such as finance, procurement, and sales. Integration provides a comprehensive view of inventory, orders, and financial data, enabling better coordination and reducing the risk of discrepancies. Seamless integration enhances overall efficiency and accuracy in warehouse operations.
- Automate Inventory Management: Utilize the automation capabilities of the ERP WMS to streamline inventory management tasks. Automated features, such as real-time tracking, reorder alerts, and stock level adjustments, help maintain accurate inventory records, reduce manual errors, and optimize stock levels based on demand.
- Enhance Order Processing: Leverage the ERP WMS to improve order processing efficiency. The system can automate order entry, manage picking and packing, and generate shipping labels. Enhanced order processing reduces lead times, increases order accuracy, and improves customer satisfaction by ensuring timely and accurate deliveries.
- Utilize Real-Time Data and Analytics: Take advantage of real-time data and analytics provided by the ERP WMS to monitor warehouse performance and make informed decisions. Access key metrics, such as inventory turnover, order fulfillment rates, and warehouse productivity. Real-time insights help identify trends, forecast demand, and implement data-driven improvements.
- Improve Inventory Visibility: The ERP WMS provides comprehensive visibility into inventory levels, locations, and movements. Track inventory in real-time across multiple locations, including warehouses, distribution centers, and retail stores. Improved visibility supports accurate inventory management, reduces stockouts, and helps prevent overstocking.
- Streamline Communication and Collaboration: Use the ERP WMS to enhance communication and collaboration among warehouse staff, suppliers, and other stakeholders. The system facilitates information sharing, updates on order status, and coordination of logistics activities. Effective communication improves efficiency, reduces errors, and supports better decision-making.
- Support Advanced Warehouse Strategies: Implement advanced warehouse strategies, such as cross-docking, wave picking, and dynamic slotting, with the help of the ERP WMS. The system can optimize workflows, manage complex processes, and enhance operational efficiency. Advanced strategies improve inventory turnover, reduce handling times, and increase overall productivity.
- Ensure System Scalability and Flexibility: Choose an ERP WMS that offers scalability and flexibility to accommodate future growth and changes in business needs. The system should be able to handle increasing volumes, adapt to evolving processes, and integrate with emerging technologies. Scalable and flexible solutions support long-term operational success.
- Provide Comprehensive Training and Support: Offer thorough training for employees on the ERP WMS to ensure effective usage and maximize the benefits of the system. Provide ongoing support and resources to address any issues or questions. Well-trained staff can leverage the full capabilities of the ERP WMS, leading to improved warehouse operations and performance.
3. Use Barcode and RFID Technology
Using barcode and RFID technology is a warehouse management best practice that significantly enhances inventory accuracy, efficiency, and traceability.
By implementing these technologies, warehouses can streamline operations, reduce errors, and improve overall productivity.
- Enhance Inventory Accuracy: Barcode and RFID systems provide precise and real-time data on inventory levels. Scanning barcodes or reading RFID tags ensures accurate updates to inventory records, reducing discrepancies and improving stock accuracy.
- Streamline Receiving Processes: Implement barcode and RFID technology to automate the receiving process. Scanning incoming shipments quickly verifies quantities and updates inventory systems, ensuring accurate records from the start.
- Speed Up Picking and Packing: Use barcode and RFID scanners to expedite picking and packing processes. These technologies guide employees to the correct items and quantities, reducing errors and increasing order fulfillment speed.
- Improve Traceability: Barcode and RFID systems offer enhanced traceability of products throughout the supply chain. This traceability helps track the movement of goods, manage recalls, and comply with regulatory requirements.
- Optimize Inventory Management: Integrate barcode and RFID technology with a Warehouse Inventory Management System (WIMS) to optimize inventory management. Real-time data enables better inventory control, demand forecasting, and replenishment planning.
- Reduce Manual Data Entry: Eliminate manual data entry by using barcode and RFID scanners. Automated data capture reduces human errors and saves time, allowing employees to focus on more value-added tasks.
- Monitor Expiry Dates and Lot Numbers: Use barcode and RFID systems to track expiry dates and lot numbers of perishable or regulated products. Accurate tracking ensures proper rotation and reduces waste.
- Facilitate Cross-Docking: Streamline cross-docking operations with barcode and RFID technology. Automated scanning quickly verifies incoming and outgoing shipments, facilitating faster transfer and reducing storage time.
- Improve Security Measures: Enhance security by using RFID technology to monitor and control access to restricted areas. RFID-enabled badges ensure only authorized personnel can enter specific zones.
- Support Cycle Counting: Use barcode and RFID scanners to support regular cycle counting. Automated counting improves accuracy and efficiency, ensuring up-to-date inventory records without the need for disruptive physical counts.
- Simplify Returns Management: Streamline returns processing with barcode and RFID technology. Scanning returned items updates inventory records and provides accurate data for restocking or disposal.
4. Regular Cycle Counting
Regular cycle counting is a warehouse management best practice that involves frequent, systematic counting of a portion of inventory to ensure accuracy and maintain inventory records.
Unlike annual physical inventory counts, cycle counting provides continuous monitoring and validation of stock levels, leading to more accurate inventory management and reduced discrepancies.
- Develop a Cycle Counting Schedule: Establish a cycle counting schedule that fits your warehouse operations. Determine the frequency of counts based on factors such as inventory turnover, item value, and past discrepancies. High-value or high-turnover items may require more frequent counts.
- Segment Inventory for Counting: Divide inventory into manageable segments or zones for counting. This segmentation helps organize the counting process and ensures that all areas of the warehouse are covered systematically.
- Prioritize High-Value and High-Turnover Items: Focus on counting high-value and high-turnover items more frequently. These items are more critical to business operations and are more likely to experience discrepancies.
- Assign Trained Personnel: Ensure that trained and knowledgeable personnel conduct cycle counts. Proper training helps minimize errors during the counting process and ensures that counts are performed accurately.
- Use Barcode and RFID Technology: Leverage barcode and RFID technology to facilitate accurate and efficient cycle counting. Scanning barcodes or RFID tags reduces manual errors and speeds up the counting process.
- Integrate with Warehouse Management System (WMS): Integrate cycle counting processes with your WMS to automatically update inventory records. WMS integration ensures real-time data accuracy and streamlines inventory management.
- Reconcile Discrepancies Promptly: Address any discrepancies identified during cycle counts promptly. Investigate the causes of discrepancies and adjust inventory records accordingly to maintain accuracy.
- Track and Analyze Discrepancy Trends: Monitor and analyze trends in inventory discrepancies. Identifying patterns can help pinpoint underlying issues, such as procedural errors, theft, or supplier discrepancies.
- Implement Root Cause Analysis: Conduct root cause analysis for significant discrepancies to determine their origin and implement corrective actions. This approach helps prevent future discrepancies and improves overall inventory accuracy.
- Document Cycle Count Procedures: Develop clear and detailed cycle counting procedures. Documentation ensures that all personnel follow the same process and maintain consistency in counting.
- Perform Random Audits: Conduct random audits to verify the accuracy of cycle counts. Random audits serve as a quality control measure and help identify any potential issues with the counting process.
- Involve All Stakeholders: Engage all relevant stakeholders, including warehouse staff, inventory managers, and finance teams, in the cycle counting process. Collaboration ensures that everyone is aligned and committed to maintaining accurate inventory records.
- Adjust Counting Frequency Based on Results: Modify the frequency of cycle counts based on results and identified issues. Items with frequent discrepancies may require more regular counts, while consistently accurate items may need fewer counts.
- Provide Continuous Training: Offer continuous training for staff involved in cycle counting. Ongoing training ensures that employees stay updated on best practices and any changes in procedures.
5. Implement Cross-Docking
Implementing cross-docking is a strategic warehouse management practice that enhances efficiency by reducing storage time and accelerating the movement of goods.
Cross-docking involves transferring products directly from inbound to outbound transportation with minimal or no storage time in between, thereby streamlining operations, reducing inventory holding costs, and speeding up delivery times.
- Assess Suitability for Cross-Docking: Evaluate if cross-docking is appropriate for your warehouse operations. Consider factors like the types of products handled, demand patterns, and the capabilities of your warehouse infrastructure.
- Identify Suitable Products: Determine which products are ideal for cross-docking, such as high-demand items, perishable goods, or products with predictable demand.
- Analyze Demand Patterns: Examine demand patterns to identify cross-docking opportunities. Products with consistent and predictable demand are more suitable for this strategy.
- Design an Efficient Layout: Create a warehouse layout that supports cross-docking operations. Ensure the smooth flow of goods from receiving to shipping areas with minimal handling and movement.
- Allocate Dedicated Areas: Designate specific areas for inbound and outbound shipments near each other to minimize travel distance and handling time.
- Optimize Dock Positions: Position dock doors strategically to facilitate efficient unloading and loading processes. Ensure docks can handle multiple types of transportation vehicles and product sizes.
- Streamline Receiving and Shipping Processes: Develop streamlined processes for receiving and shipping goods to support efficient cross-docking operations. Implement procedures that minimize handling time and ensure accurate transfer of products.
- Coordinate Inbound and Outbound Schedules: Align inbound and outbound shipment schedules to reduce waiting times and ensure prompt transfer of goods.
- Implement Real-Time Tracking: Use real-time tracking technology, such as RFID or barcode scanning, to monitor the movement of goods through the cross-docking process.
- Utilize Technology for Cross-Docking: Leverage technology solutions, such as Warehouse Management Systems (WMS) and Transportation Management Systems (TMS), to optimize cross-docking operations.
- Integrate WMS and TMS: Ensure seamless integration between your WMS and TMS to coordinate warehouse and transportation activities.
- Automate Data Collection: Use automated data collection tools, such as barcode scanners and RFID readers, to capture real-time information on product movement.
- Train Staff on Cross-Docking Procedures: Provide comprehensive training for warehouse staff on cross-docking procedures, including the handling, sorting, and transferring of goods.
- Conduct Hands-On Training: Include hands-on training sessions to familiarize staff with cross-docking processes and technology.
- Emphasize Safety and Efficiency: Train staff on safety protocols and best practices to ensure that cross-docking operations are conducted safely and efficiently.
- Monitor and Evaluate Performance: Regularly monitor and evaluate the performance of cross-docking operations to identify areas for improvement.
- Track Key Metrics: Measure metrics such as transfer time, handling time, and shipment accuracy to assess the performance of cross-docking operations.
- Implement Continuous Improvement: Use insights from performance evaluations to implement continuous improvement initiatives.
- Collaborate with Supply Chain Partners: Work closely with supply chain partners, including suppliers, carriers, and customers, to coordinate cross-docking activities.
- Share Information: Share relevant information with supply chain partners to facilitate coordination and improve visibility.
- Align Objectives: Ensure that all partners are aligned on cross-docking objectives and procedures.
6. Employ a Good Warehouse Practices Checklist
Using a good warehouse practices checklist is an effective way to ensure that warehouse operations are efficient, safe, and compliant with industry standards.
A comprehensive checklist helps standardize procedures, maintain organization, and identify areas for improvement. Here's how to employ a good warehouse practices checklist:
- Develop a Comprehensive Checklist: Create a detailed checklist that covers all essential aspects of warehouse operations, including inventory management, safety protocols, equipment maintenance, and employee practices.
- Include Key Areas of Focus: Ensure the checklist addresses critical areas such as receiving, storage, picking, packing, shipping, safety, and compliance. Each section should have specific tasks and standards to be met.
- Standardize Procedures: Use the checklist to standardize warehouse procedures, ensuring consistency and reliability in operations. Standardization helps reduce errors, streamline processes, and improve overall efficiency.
- Train Employees on the Checklist: Provide training for all warehouse employees on how to use the checklist effectively. Ensure they understand the importance of each task and how it contributes to overall warehouse performance.
- Conduct Regular Audits: Use the checklist to conduct regular audits of warehouse operations. Regular audits help identify areas of non-compliance, inefficiency, or safety concerns that need to be addressed.
- Track and Analyze Performance: Use the checklist to track performance metrics, such as error rates, compliance levels, and operational efficiency. Analyze the data to identify trends and areas for improvement.
- Adapt to Changes: Regularly review and adapt the checklist to reflect changes in warehouse operations, technology, and regulations. Keeping the checklist up-to-date ensures its ongoing relevance and effectiveness.
- Encourage Feedback: Solicit feedback from employees on the checklist and its implementation. Employee insights can provide valuable information for improving procedures and enhancing overall operations.
7. Prioritize Safety and Compliance
Prioritizing safety and compliance in warehouse management is essential for protecting employees, minimizing risks, and adhering to regulatory standards. Effective safety and compliance practices not only prevent accidents and injuries but also promote a productive and positive work environment.
- Develop a Comprehensive Safety Plan: Create a detailed safety plan that outlines policies, procedures, and responsibilities related to workplace safety. The plan should address potential hazards, emergency response protocols, and safety training requirements.
- Conduct Regular Risk Assessments: Perform regular risk assessments to identify and mitigate potential hazards in the warehouse. Assessments should cover all aspects of warehouse operations, including equipment, storage areas, and employee practices.
- Implement Safety Training Programs: Provide ongoing safety training for all warehouse employees. Training should cover proper use of equipment, handling of hazardous materials, emergency procedures, and general workplace safety practices.
- Ensure Compliance with Regulations: Stay informed about relevant safety regulations and standards, such as OSHA (Occupational Safety and Health Administration) guidelines. Ensure that all warehouse operations comply with these regulations to avoid fines and ensure a safe work environment.
- Promote a Safety Culture: Foster a culture of safety within the warehouse by encouraging employees to prioritize safety and report hazards. Leadership should model safe behaviors and reinforce the importance of safety in daily operations.
8. Implement Slotting Optimization
Slotting optimization is a warehouse management best practice that involves strategically organizing inventory within the warehouse to maximize efficiency, reduce picking time, and improve overall productivity.
By placing high-demand items in easily accessible locations and organizing products logically, warehouses can streamline operations and enhance their performance.
- Identify High-Demand Items: Determine which items are picked most frequently and should be located in easily accessible areas to reduce picking time. High-demand items should be placed in prime locations near packing and shipping areas.
- Categorize Products: Group products based on similarities, such as size, weight, and picking frequency. Organizing items into categories allows for logical placement and improves efficiency.
- Implement ABC Analysis: Use ABC analysis to classify inventory into three categories: A (high-value, high-demand items), B (moderate-value, moderate-demand items), and C (low-value, low-demand items). This classification guides placement strategies.
- Designate Prime Picking Zones: Allocate prime picking zones for A-category items to minimize travel distance and picking time. These zones should be easily accessible and close to packing and shipping areas.
- Optimize Storage Locations: Ensure that storage locations are optimized based on product size, weight, and handling requirements. Heavy or bulky items should be placed in locations that minimize the need for excessive lifting or movement.
- Utilize Technology: Leverage warehouse management systems (WMS) and other technology solutions to support slotting optimization. Technology can provide real-time data and analytics to guide placement decisions and monitor performance.
- Enhance Picking Routes: Design picking routes that minimize travel distance and reduce the time spent locating items. Efficient picking routes improve productivity and reduce labor costs.
- Train Staff on Slotting Procedures: Provide training for warehouse staff on slotting procedures and the importance of maintaining organized storage areas. Well-trained staff can effectively implement and sustain slotting optimization strategies.
9. Regular Maintenance of Equipment
Regular maintenance of equipment is a critical warehouse management best practice that ensures the reliability, safety, and efficiency of operations.
Properly maintained equipment minimizes downtime, reduces repair costs, and extends the lifespan of machinery.
- Develop a Maintenance Schedule: Create a detailed maintenance schedule for all equipment, including forklifts, conveyor belts, pallet jacks, and other machinery. A well-structured schedule ensures that maintenance tasks are performed regularly and on time.
- Conduct Routine Inspections: Implement routine inspections to identify potential issues before they escalate. Regular inspections help detect wear and tear, mechanical problems, and safety hazards early on.
- Perform Preventive Maintenance: Engage in preventive maintenance practices to keep equipment in optimal working condition. Preventive maintenance includes tasks such as lubrication, cleaning, and minor adjustments that prevent major breakdowns.
- Keep Detailed Maintenance Records: Maintain detailed records of all maintenance activities, including inspections, repairs, and replacements. Accurate records provide a history of equipment performance and help track maintenance needs.
- Train Employees on Equipment Use: Ensure that employees are properly trained on the correct use of equipment. Proper usage minimizes wear and tear and reduces the risk of accidents caused by operator error.
- Establish Maintenance Checklists: Create maintenance checklists for each piece of equipment to guide maintenance tasks and ensure consistency. Checklists help ensure that no maintenance steps are overlooked.
- Use Manufacturer Guidelines: Follow manufacturer guidelines for maintenance and repairs. Adhering to these guidelines helps maintain equipment warranty coverage and ensures that maintenance is performed correctly.
- Invest in Quality Parts and Supplies: Use high-quality parts and supplies for repairs and replacements. Quality components extend the lifespan of equipment and improve reliability.
- Implement a Spare Parts Inventory: Maintain an inventory of essential spare parts to minimize downtime during repairs. Having readily available parts reduces waiting time and keeps operations running smoothly.
- Schedule Downtime for Maintenance: Plan maintenance activities during periods of low operational demand to minimize disruption. Scheduling downtime strategically ensures that maintenance does not impact productivity.
- Engage Professional Technicians: Utilize professional technicians for complex maintenance tasks and repairs. Skilled technicians have the expertise to address issues accurately and efficiently.
10. Invest in Employee Training
Investing in employee training is crucial for enhancing warehouse efficiency, reducing errors, and fostering a skilled workforce.
Well-trained employees contribute to smoother operations, better safety practices, and increased productivity. Here’s how to effectively invest in employee training for optimal warehouse performance:
- Assess Training Needs: Begin by conducting a thorough assessment to identify the specific training needs of your warehouse staff. Evaluate existing skill levels, job roles, and any gaps in knowledge or skills. Understanding these needs helps tailor training programs to address the most critical areas and align with operational goals.
- Develop Comprehensive Training Programs: Create comprehensive training programs that cover essential warehouse skills, including inventory management, equipment operation, safety procedures, and software usage. Programs should include both theoretical and practical components to ensure that employees understand concepts and can apply them in real-world scenarios.
- Utilize a Variety of Training Methods: Incorporate various training methods to accommodate different learning styles and preferences. Use a mix of classroom training, hands-on workshops, e-learning modules, and on-the-job training. A diverse approach helps engage employees and reinforces learning through multiple formats.
- Provide Safety Training: Ensure that all employees receive thorough safety training to minimize the risk of accidents and injuries. Training should cover proper equipment use, emergency procedures, hazard recognition, and personal protective equipment (PPE). Regular safety training promotes a culture of safety and compliance with regulatory standards.
- Offer Technology Training: Train employees on the use of warehouse technology and software, including Warehouse Management Systems (WMS), barcode scanners, and automated systems. Effective technology training helps employees use these tools efficiently, reducing errors and improving operational performance.
- Implement Continuous Learning Opportunities: Foster a culture of continuous learning by offering ongoing training and professional development opportunities. Provide access to advanced training programs, industry certifications, and workshops to help employees stay updated on the latest trends and technologies.
- Encourage Cross-Training: Implement cross-training programs to enable employees to perform multiple roles within the warehouse. Cross-training enhances workforce flexibility, improves coverage during absences, and prepares employees for career advancement. A versatile workforce contributes to overall operational efficiency.
- Monitor and Evaluate Training Effectiveness: Regularly monitor and evaluate the effectiveness of training programs. Collect feedback from employees, assess their performance, and analyze any changes in operational metrics. Use this information to refine training programs and address any areas that require improvement.
11. Implement Lean Warehouse Practices
Implementing lean warehouse practices is a strategic approach to improving operational efficiency, reducing waste, and maximizing value in warehouse management.
Lean principles focus on streamlining processes, optimizing resource utilization, and continuously improving workflows to enhance overall performance.
- Map and Analyze Value Streams: Conduct value stream mapping to visualize and analyze the flow of materials and information through your warehouse. Identify areas where waste occurs, such as excess handling, waiting times, or unnecessary movement. Analyzing value streams helps pinpoint inefficiencies and provides a basis for targeted improvements.
- Eliminate Waste: Apply lean principles to eliminate waste in all forms, including overproduction, excess inventory, waiting times, unnecessary movement, overprocessing, defects, and unused talent. Use techniques such as the 5S methodology (Sort, Set in Order, Shine, Standardize, Sustain) to organize and streamline warehouse operations, reducing waste and enhancing efficiency.
- Implement Standard Operating Procedures (SOPs): Develop and implement standard operating procedures for key warehouse tasks, such as receiving, picking, packing, and shipping. SOPs ensure consistency, reduce variability, and provide clear guidelines for employees, leading to more efficient and accurate operations.
- Adopt Just-in-Time (JIT) Inventory: Utilize Just-in-Time (JIT) inventory practices to align inventory levels with current demand and minimize excess stock. JIT reduces carrying costs, improves cash flow, and minimizes the risk of obsolescence. Coordinate closely with suppliers and implement efficient replenishment processes to support JIT inventory.
- Utilize Visual Management Tools: Employ visual management tools, such as signage, labels, and color-coded systems, to enhance communication and streamline warehouse operations. Visual tools help guide employees, standardize processes, and provide real-time information on inventory, workflows, and performance metrics.
12. Monitor Key Performance Indicators (KPIs)
Monitoring Key Performance Indicators (KPIs) is essential for assessing and improving warehouse performance, optimizing operations, and achieving strategic goals.
KPIs provide valuable insights into various aspects of warehouse management, enabling data-driven decision-making and continuous improvement.
- Identify Relevant KPIs: Determine which KPIs are most relevant to your warehouse operations. Common KPIs include inventory turnover rate, order accuracy, order cycle time, picking accuracy, and shipping accuracy. Select KPIs that align with your business objectives and operational priorities.
- Establish Benchmark Targets: Set benchmark targets for each KPI based on historical data, industry standards, and organizational goals. Benchmark targets provide a reference point for evaluating performance and identifying areas for improvement. Regularly review and adjust targets as needed to reflect changing business conditions.
- Create Dashboards and Reports: Develop dashboards and reports to visualize and track KPIs in real-time. Dashboards provide a comprehensive overview of performance metrics, while reports offer detailed analysis and historical data. Visual representations of KPIs facilitate easy interpretation and help identify trends and anomalies.
- Analyze KPI Data: Regularly analyze KPI data to assess performance, identify trends, and uncover underlying issues. Look for patterns, deviations from targets, and areas of concern. Data analysis helps diagnose problems, determine root causes, and implement corrective actions to improve warehouse operations.
- Communicate KPI Results: Share KPI results with relevant stakeholders, including warehouse staff, managers, and executives. Transparent communication of performance metrics helps ensure that everyone is aware of operational goals, progress, and areas needing attention. Regular updates keep teams informed and engaged in performance improvement efforts.
13. Utilize Just-in-Time (JIT) Inventory
Utilizing Just-in-Time (JIT) inventory is a strategic approach to managing inventory levels efficiently and reducing carrying costs.
JIT inventory focuses on aligning inventory with current demand, minimizing excess stock, and optimizing supply chain processes.
This method enhances operational efficiency and reduces waste, leading to improved profitability and customer satisfaction.
- Establish Strong Supplier Relationships: Develop robust relationships with suppliers to ensure reliable and timely deliveries. Effective communication and collaboration with suppliers are crucial for JIT inventory success. Work closely with suppliers to align delivery schedules with your inventory needs and address any potential issues that may arise.
- Implement Demand Forecasting: Use advanced forecasting tools to accurately predict customer demand and adjust inventory levels accordingly. Reliable demand forecasting helps prevent overstocking or stockouts by aligning inventory with actual consumption patterns. Utilize historical sales data, market trends, and seasonal patterns to refine forecasts.
- Optimize Inventory Replenishment: Set up a streamlined inventory replenishment process that triggers orders based on real-time data and demand signals. Automate replenishment decisions using inventory management software to ensure timely restocking and minimize delays. Efficient replenishment helps maintain optimal inventory levels without excess.
- Enhance Supply Chain Visibility: Invest in technologies that provide real-time visibility into your supply chain. Track inventory levels, shipments, and order statuses to monitor the flow of goods and anticipate potential disruptions. Enhanced visibility helps in making informed decisions and maintaining smooth JIT operations.
- Adopt Lean Manufacturing Principles: Integrate lean manufacturing principles into your JIT inventory strategy to minimize waste and optimize processes. Lean practices focus on reducing excess inventory, improving workflow efficiency, and eliminating non-value-added activities. Emphasize continuous improvement and process optimization.
- Implement Automated Inventory Systems: Utilize automated inventory management systems to track stock levels, manage orders, and forecast demand. Automated systems provide real-time data and alerts, ensuring timely responses to inventory changes and reducing manual intervention. Integration with other supply chain systems enhances overall efficiency.
- Streamline Order Processing: Optimize order processing workflows to ensure quick and accurate fulfillment. Efficient order processing reduces lead times and supports timely inventory replenishment. Implement systems and processes that facilitate rapid order fulfillment and minimize delays.
14. Improve Communication
Improving communication within warehouse operations is crucial for ensuring smooth workflows, enhancing coordination, and achieving operational excellence.
Effective communication strategies foster collaboration, reduce misunderstandings, and drive efficiency across all aspects of warehouse management.
- Establish Clear Communication Channels: Set up clear and reliable communication channels within the warehouse, including email, messaging apps, and intercom systems. Ensure that all team members have access to and are trained in using these channels. Clear channels facilitate timely information sharing and reduce the risk of miscommunication.
- Implement Regular Team Meetings: Schedule regular team meetings to discuss operational updates, address issues, and align on goals. Frequent meetings keep everyone informed about changes, upcoming tasks, and performance metrics. Regular communication helps to maintain focus and ensures that all team members are on the same page.
- Utilize Real-Time Communication Tools: Deploy real-time communication tools, such as instant messaging platforms or mobile apps, to enable quick and efficient exchanges of information. Real-time tools support immediate responses to issues, facilitate coordination between team members, and enhance overall operational agility.
- Provide Clear Instructions and Documentation: Ensure that all instructions, procedures, and processes are clearly documented and easily accessible. Use standard operating procedures (SOPs), visual aids, and checklists to provide clear guidance on tasks and responsibilities. Clear documentation helps prevent errors and ensures consistency in operations.
- Encourage Open Feedback: Create an environment where employees feel comfortable providing feedback and sharing their ideas. Encourage open dialogue about challenges, suggestions for improvements, and operational concerns. Constructive feedback helps identify areas for improvement and fosters a collaborative work culture.
15. Leverage Technology for Forecasting
Leveraging technology for forecasting is a strategic approach to enhancing inventory management, optimizing supply chain operations, and aligning inventory levels with demand patterns.
Advanced forecasting technologies help businesses predict future inventory needs with greater accuracy, leading to improved decision-making and operational efficiency.
- Utilize Predictive Analytics: Implement predictive analytics tools to analyze historical sales data, market trends, and seasonal patterns. Predictive analytics uses algorithms and machine learning models to forecast future demand, helping businesses make data-driven decisions and prepare for fluctuations in inventory requirements.
- Adopt Demand Planning Software: Invest in demand planning software that integrates with your existing inventory management system. This software uses advanced algorithms and statistical models to forecast demand based on historical data, promotional activities, and market trends. Accurate demand planning helps align inventory levels with anticipated sales and reduces the risk of stockouts or overstocking.
- Incorporate Artificial Intelligence (AI): Leverage artificial intelligence (AI) to enhance forecasting accuracy. AI algorithms can process large volumes of data, identify patterns, and make predictions based on complex variables. AI-driven forecasting tools continuously learn from new data, improving their accuracy over time and adapting to changing market conditions.
- Integrate with Supply Chain Management (SCM) Systems: Ensure that your forecasting technology is integrated with supply chain management (SCM) systems. Integration allows for seamless data flow between forecasting, inventory management, and procurement processes. This alignment improves coordination and ensures that inventory levels are adjusted in response to forecasted demand.
16. Implement Real-Time Inventory Tracking
Implementing real-time inventory tracking is essential for maintaining accurate inventory levels, enhancing operational efficiency, and improving customer satisfaction.
Real-time tracking allows businesses to monitor inventory continuously, respond to changes promptly, and make data-driven decisions to optimize their supply chain.
- Utilize RFID Technology: Integrate Radio Frequency Identification (RFID) technology to track inventory in real time. RFID tags attached to products or pallets transmit data to RFID readers throughout the warehouse. This technology provides instant visibility into inventory location and movement, improving accuracy and reducing manual checks.
- Adopt Barcode Scanning Systems: Implement barcode scanning systems to capture and update inventory data in real time. Scanners and mobile devices can quickly read barcodes on products, updating inventory levels automatically in your warehouse management system (WMS). This method enhances accuracy and speed in tracking inventory.
- Integrate with Warehouse Management Software (WMS): Ensure that your real-time inventory tracking system is integrated with your WMS. A well-integrated system allows for seamless data exchange, real-time updates, and accurate inventory management. This integration helps prevent discrepancies and ensures that inventory data is current and reliable.
- Implement IoT Sensors: Use Internet of Things (IoT) sensors to monitor inventory conditions such as temperature, humidity, and movement. IoT sensors provide valuable data on the environment and status of inventory items, helping to ensure product quality and reduce spoilage or damage.
- Enable Mobile Access: Equip warehouse staff with mobile devices that provide real-time access to inventory information. Mobile access allows employees to update inventory records, verify stock levels, and perform tasks on the go, improving operational efficiency and accuracy.
17. Adopt Automated Picking Systems
Adopting automated picking systems is a transformative strategy for improving efficiency, accuracy, and speed in warehouse operations.
Automated picking systems leverage technology to streamline the order fulfillment process, reduce labor costs, and enhance overall operational performance.
- Implement Automated Picking Robots: Utilize automated picking robots, such as robotic arms or autonomous mobile robots (AMRs), to handle the picking of items from shelves. These robots can navigate the warehouse, select products, and deliver them to packing stations. Automated picking robots improve speed and accuracy while reducing the physical strain on human workers.
- Integrate Picking Systems with Warehouse Management Software: Ensure that your automated picking systems are integrated with warehouse management software (WMS). This integration allows for real-time data synchronization, accurate inventory tracking, and seamless order processing. A cohesive system enhances overall efficiency and minimizes errors.
- Optimize Workflow with Automated Conveyor Systems: Deploy automated conveyor systems to transport items between picking stations, packing areas, and shipping zones. Conveyors reduce the need for manual handling, streamline the movement of products, and improve overall operational efficiency.
- Incorporate Drones for Inventory Management: Use drones equipped with barcode scanners or RFID readers for inventory management tasks. Drones can quickly scan and verify inventory levels, locate misplaced items, and perform regular stock checks, reducing the need for manual inventory counts.
- Leverage Automated Sorting Systems: Implement automated sorting systems to categorize and route items to their appropriate destinations based on order requirements. Sorting systems enhance efficiency by automating the sorting process and reducing the time needed to prepare orders for shipping.
18. Develop a Robust Returns Management Process
A robust returns management process is essential for efficiently handling returned items, maintaining customer satisfaction, and minimizing operational disruptions.
An effective returns management process ensures that returned goods are processed smoothly, accurately, and in a way that aligns with company policies and customer expectations.
- Establish Clear Return Policies: Develop and communicate clear return policies that outline the conditions under which returns are accepted, the timeframe for returns, and any associated fees. Ensure that these policies are easily accessible to customers and clearly stated on your website and other relevant platforms.
- Implement a Returns Management System: Integrate a returns management system within your inventory and warehouse management software. This system should track returned items, manage return authorizations, and update inventory levels in real-time. Automation helps streamline the returns process and reduces manual errors.
- Set Up a Returns Processing Area: Designate a specific area within the warehouse for processing returns. This area should be equipped with the necessary tools and resources to inspect, sort, and restock returned items. A dedicated space helps maintain organization and efficiency in handling returns.
- Implement Inspection and Quality Control: Establish procedures for inspecting returned items to assess their condition and determine whether they can be restocked or require repairs. Quality control checks help ensure that returned products meet standards before being resold or disposed of.
- Update Inventory Management: Ensure that your inventory management system accurately reflects the status of returned items. Update inventory levels promptly to avoid discrepancies and maintain accurate stock records. This helps in managing inventory efficiently and prevents stockouts or overstock situations.
- Analyze Return Data: Collect and analyze data on returns to identify trends and patterns. Understand the reasons for returns, such as product defects, shipping issues, or customer dissatisfaction. Use this data to address underlying problems, improve product quality, and enhance overall customer experience.
19. Establish Clear Inventory Replenishment Procedures
Establishing clear inventory replenishment procedures is essential for maintaining optimal stock levels, avoiding stockouts, and ensuring smooth warehouse operations.
Well-defined procedures help manage inventory efficiently, align with demand patterns, and support overall supply chain effectiveness.
- Define Replenishment Triggers: Set specific criteria or triggers for initiating inventory replenishment. These triggers can be based on inventory levels, reorder points, sales forecasts, or lead times. By defining clear triggers, you ensure that inventory is replenished proactively and in a timely manner.
- Develop Reorder Point Systems: Implement a reorder point system to determine when inventory levels reach a threshold that requires replenishment. Reorder points should be based on historical sales data, demand variability, and lead times. This system helps prevent stockouts and maintains adequate inventory levels.
- Utilize Inventory Management Software: Integrate inventory management software to automate and streamline replenishment processes. The software can track inventory levels in real-time, generate reorder alerts, and facilitate automatic reordering based on predefined criteria. This technology enhances accuracy and efficiency in replenishment.
- Establish Safety Stock Levels: Maintain safety stock levels to buffer against unexpected demand fluctuations or supply chain disruptions. Safety stock ensures that you have an additional inventory reserve to handle variations in demand or delays in replenishment. Determine safety stock levels based on historical data and variability in demand.
- Implement Forecasting Techniques: Use forecasting techniques to predict future inventory needs based on historical sales data, market trends, and seasonal patterns. Accurate forecasting helps optimize replenishment schedules and ensures that inventory levels align with anticipated demand.
- Coordinate with Suppliers: Develop strong relationships with suppliers and establish clear communication channels for replenishment. Share forecasted demand and inventory levels with suppliers to ensure timely and accurate deliveries. Collaborate with suppliers to manage lead times and address potential supply chain issues.
20. Implement Flexible Staffing Solutions
Implementing flexible staffing solutions is essential for managing workforce requirements efficiently, especially in the dynamic environment of warehouse operations.
By adapting staffing levels and roles to meet fluctuating demands, businesses can maintain productivity, reduce costs, and ensure smooth operations during peak periods and beyond.
- Utilize Temporary and Seasonal Workers: Engage temporary or seasonal staff during peak periods or high-demand seasons to manage increased workloads without committing to long-term hires. Temporary workers can help alleviate pressure on permanent staff and ensure that operations continue smoothly during busy times.
- Cross-Train Employees: Train employees to perform multiple roles within the warehouse. Cross-training enhances workforce flexibility, allowing staff to shift between different tasks as needed. This versatility supports operational efficiency and ensures that critical functions are covered, even when staff members are absent or during peak times.
- Implement Part-Time and Flexible Hours: Offer part-time or flexible work hours to accommodate varying demand levels and employee preferences. Flexible scheduling options, such as shift adjustments or staggered start times, help balance workload and reduce employee turnover by providing work arrangements that fit diverse needs.
- Leverage Workforce Management Software: Utilize workforce management software to optimize staffing levels based on real-time data and forecasts. This technology helps schedule shifts, track attendance, and manage labor costs more effectively. Automated tools can predict staffing needs based on historical data and seasonal trends.
- Create a Pool of On-Call Workers: Establish a pool of on-call workers who can be called in during unexpected surges in demand or short-term absences. Having a ready-to-deploy workforce ensures that you can quickly address staffing shortages and maintain operational continuity.
- Offer Incentives for Flexible Work: Provide incentives such as bonuses, overtime pay, or additional benefits for employees who take on flexible or extra shifts. Incentives help motivate staff to adapt to varying work schedules and support operational needs.
21. Optimize Packaging Processes
Optimizing packaging processes is crucial for enhancing efficiency, reducing costs, and ensuring that products are shipped safely and effectively.
Streamlined packaging processes improve operational productivity, minimize waste, and contribute to overall customer satisfaction.
- Standardize Packaging Materials: Implement standardized packaging materials and sizes to simplify the packaging process. Consistent materials reduce complexity, minimize errors, and streamline inventory management. Standardization also helps in negotiating better rates with suppliers and ensures compatibility with automated packaging systems.
- Automate Packaging Tasks: Invest in automated packaging solutions such as packing machines, conveyors, and robotic arms. Automation increases speed, consistency, and accuracy in the packaging process. Automated systems can handle repetitive tasks efficiently, reducing manual labor and minimizing human errors.
- Optimize Packaging Layout: Design an efficient packaging layout that minimizes movement and workflow interruptions. Position packing stations, tools, and materials strategically to streamline the packaging process. An optimized layout reduces time spent on packaging tasks and enhances overall productivity.
- Implement Packaging Best Practices: Develop and enforce best practices for packaging procedures. This includes guidelines for proper packing techniques, use of protective materials, and adherence to packaging standards. Clear procedures ensure that packaging is done consistently and meets quality standards.
- Reduce Packaging Waste: Adopt eco-friendly and minimalistic packaging solutions to reduce waste. Use recyclable or biodegradable materials, and minimize excess packaging. Implementing waste reduction practices not only lowers costs but also supports sustainability initiatives.
22. Enhance Customer Communication
Enhancing customer communication is a fundamental warehouse management best practice that improves service levels, builds trust, and ensures a positive customer experience.
Effective communication strategies help manage expectations, address concerns promptly, and provide clear and accurate information about orders, deliveries, and inventory.
- Provide Real-Time Order Tracking: Implement systems that offer customers real-time visibility into their orders. This includes tracking numbers, shipment status updates, and estimated delivery times. Real-time tracking enhances transparency, reduces customer anxiety, and allows customers to plan accordingly.
- Send Proactive Notifications: Communicate proactively with customers about important updates, such as order confirmations, shipping delays, or changes in delivery schedules. Automated notifications via email, SMS, or app notifications keep customers informed and minimize the need for them to reach out for updates.
- Offer Multiple Communication Channels: Provide customers with various communication options, including phone support, email, live chat, and social media. Offering multiple channels ensures that customers can reach out through their preferred method, enhancing accessibility and convenience.
- Implement a Customer Service Platform: Utilize a robust customer service platform to manage and streamline customer interactions. This platform should integrate with your warehouse management system and CRM to provide a unified view of customer interactions, allowing for more efficient and personalized service.
- Ensure Accurate and Timely Responses: Train customer service representatives to respond to inquiries and issues promptly and accurately. Efficient handling of customer requests and concerns improves satisfaction and demonstrates a commitment to high service standards.
- Provide Self-Service Options: Implement self-service tools, such as online portals or mobile apps, where customers can track their orders, manage returns, and access account information. Self-service options empower customers to resolve issues independently and at their convenience.
- Solicit and Act on Feedback: Regularly solicit customer feedback through surveys, reviews, and direct communication. Use this feedback to identify areas for improvement, address recurring issues, and enhance your communication strategies based on customer needs and preferences.
23. Utilize Your Company's Talents Appropriately
Effectively utilizing your company's talents is a vital warehouse management best practice that ensures employees' skills and expertise are leveraged to maximize productivity and operational efficiency.
By aligning tasks and responsibilities with individual strengths and capabilities, businesses can enhance performance, foster a positive work environment, and achieve strategic goals.
- Align Roles with Expertise: Assign tasks and responsibilities based on employees' skills, experience, and strengths. For example, leverage analytical talent for inventory forecasting, operational expertise for process optimization, and technical skills for managing warehouse technology. This alignment ensures that each employee contributes effectively to their area of expertise, leading to better outcomes and higher productivity.
- Encourage Specialization: Foster specialization within your workforce by identifying areas where employees can develop deep expertise. Specialized roles, such as inventory management or quality control, benefit from employees who focus on specific aspects of warehouse operations. This specialization enhances efficiency and accuracy, as employees become more proficient in their areas of responsibility.
- Promote Cross-Training: Implement cross-training programs to equip employees with multiple skills and knowledge across various functions. This versatility allows staff to handle different tasks and adapt to changing demands or operational needs. Cross-training also supports team flexibility, reduces dependency on specific individuals, and ensures coverage during peak periods or absences.
- Leverage Leadership Skills: Utilize employees with strong leadership qualities to oversee teams and manage key warehouse functions. Effective leaders can drive performance, mentor team members, and implement best practices. By placing skilled leaders in appropriate roles, you enhance team cohesion and operational efficiency.
- Support Professional Development: Invest in ongoing training and development opportunities to help employees acquire new skills and advance their careers. Providing access to industry certifications, workshops, and educational resources keeps your team up-to-date with best practices and emerging trends, leading to continuous improvement and innovation.
- Recognize and Reward Contributions: Acknowledge and reward employees for their exceptional performance and contributions. Recognition programs, performance bonuses, and career advancement opportunities motivate staff and reinforce a culture of excellence. Recognizing talent and rewarding achievements contribute to higher job satisfaction and employee retention.
- Facilitate Open Communication: Encourage open communication between employees and management to understand individual strengths, career aspirations, and areas for growth. Regular feedback sessions and performance reviews provide insights into how employees can best contribute to the organization’s goals and help identify opportunities for skill development.
- Optimize Team Dynamics: Formulate teams based on complementary skills and diverse expertise to enhance collaboration and problem-solving. Effective team dynamics leverage the collective talents of team members, leading to improved decision-making, innovation, and overall performance.
How Can Deskera ERP Help You with Warehouse Management ?
Deskera ERP is a powerful enterprise resource planning software designed to streamline and optimize warehouse management.
Here are the key features of Deskera ERP and how they can help with warehouse management:
Inventory Management:
- Real-Time Inventory Tracking: Deskera ERP provides real-time visibility into inventory levels across multiple locations, ensuring accurate stock data and timely replenishment.
- Automated Reordering: Set automated reorder points to maintain optimal inventory levels, preventing stockouts and overstocking.
Order Fulfillment:
- Efficient Order Processing: Streamline order processing from picking to shipping with Deskera ERP’s automated workflows, reducing lead times and improving customer satisfaction.
- Integrated Shipping: Integrate shipping processes within the ERP system to manage shipments, track deliveries, and handle returns seamlessly.
Barcode and RFID Integration:
- Accurate Data Capture: Use Deskera ERP’s barcode and RFID integration for accurate and efficient data capture, reducing manual entry errors and speeding up inventory audits.
- Inventory Audits: Conduct quick and precise inventory audits using barcode scanners and RFID readers.
Cycle Counting:
- Regular Inventory Audits: Schedule and perform regular cycle counts with Deskera ERP to maintain accurate inventory records and minimize discrepancies.
- Discrepancy Resolution: Quickly identify and resolve inventory discrepancies to ensure data accuracy.
Returns Management:
- Efficient Returns Processing: Streamline the returns process by automatically updating inventory records and tracking returns to improve efficiency and customer satisfaction.
Warehouse Operations:
- Task Automation: Automate routine warehouse tasks such as picking, packing, and shipping to improve operational efficiency and reduce labor costs.
- Performance Monitoring: Monitor key performance indicators (KPIs) to identify areas for improvement and optimize warehouse operations.
Reporting and Analytics:
- Comprehensive Reporting: Generate detailed reports on inventory levels, order fulfillment, and warehouse performance to gain insights and make data-driven decisions.
- Data Analytics: Utilize advanced data analytics tools within Deskera ERP to forecast demand, manage inventory levels, and enhance operational efficiency.
Compliance and Safety:
- Regulatory Compliance: Ensure compliance with industry regulations and standards through accurate record-keeping and reporting.
- Safety Protocols: Implement and monitor safety protocols to protect employees and inventory, ensuring a safe working environment.
Integration with Other Systems:
- Seamless Integration: Integrate Deskera ERP with other business systems such as CRM, accounting, and procurement for a unified approach to warehouse management.
- Real-Time Data Sync: Ensure real-time synchronization of data across systems for accurate and up-to-date information.
Key Takeaways
Implementing best practices in warehouse management is crucial for ensuring efficiency, accuracy, and safety in warehouse operations. By adopting a strategic approach and leveraging advanced technologies, warehouses can significantly enhance their performance, reduce costs, and improve customer satisfaction.
The top 23 warehouse management best practices discussed here provide a comprehensive framework for optimizing various aspects of warehouse operations.
1.Optimize Warehouse Layout: Design an efficient warehouse layout to maximize space utilization and streamline workflows.
2. Adopt an ERP Warehouse Management System: Integrate warehouse operations with an ERP system for enhanced data visibility and decision-making.
3. Use Barcode and RFID Technology: Implement barcode and RFID technology to improve inventory accuracy and streamline processes.
4. Regular Cycle Counting: Conduct frequent cycle counts to maintain accurate inventory records and minimize discrepancies.
5. Implement Cross-Docking: Expedite order fulfillment and reduce storage time by directly transferring inbound shipments to outbound destinations.
6. Employ a Good Warehouse Practices Checklist: Standardize and monitor essential tasks to ensure compliance and operational efficiency.
7. Prioritize Safety and Compliance: Implement robust safety protocols and ensure compliance with industry regulations to protect employees and inventory.
8. Implement Slotting Optimization: Efficiently organize inventory to minimize travel time and improve picking accuracy.
9. Regular Maintenance of Equipment: Ensure equipment reliability and safety through routine maintenance and inspections.
10. Invest in Employee Training: Provide comprehensive training to ensure employees are skilled and knowledgeable about best practices and technologies.
11. Implement Lean Warehouse Practices: Adopt lean principles to eliminate waste, reduce costs, and improve operational efficiency.
12. Monitor Key Performance Indicators (KPIs): Track performance metrics to identify areas for improvement and ensure operational efficiency.
13. Utilize Just-in-Time (JIT) Inventory: Minimize inventory holding costs and reduce waste by synchronizing inventory levels with demand.
14. Improve Communication: Maintain clear and proactive communication with employees and customers to manage expectations and enhance service.
15. Leverage Technology for Forecasting: Use data analytics and forecasting tools to predict demand and manage inventory levels proactively.
16. Implement Real-Time Inventory Tracking: Utilize real-time tracking to maintain accurate inventory records and support just-in-time practices.
17. Adopt Automated Picking Systems: Implement automated picking systems to increase picking speed and accuracy while reducing labor costs.
18. Develop a Robust Returns Management Process: Implement effective procedures to handle returns efficiently and maintain customer satisfaction.
19. Establish Clear Inventory Replenishment Procedures: Develop and maintain clear procedures for inventory replenishment to avoid stockouts and overstocking.
20. Implement Flexible Staffing Solutions: Adjust staffing levels based on demand to maintain productivity and manage labor costs.
21. Optimize Packaging Processes: Streamline packing procedures to improve efficiency and ensure the safe transport of goods.
22. Enhance Customer Communication: Communicate proactively with customers to manage expectations and improve overall service quality.
23. Utilize Your Company's Talents Appropriately: Assign tasks based on employees' strengths and skills to maximize productivity and job satisfaction.
Related Articles
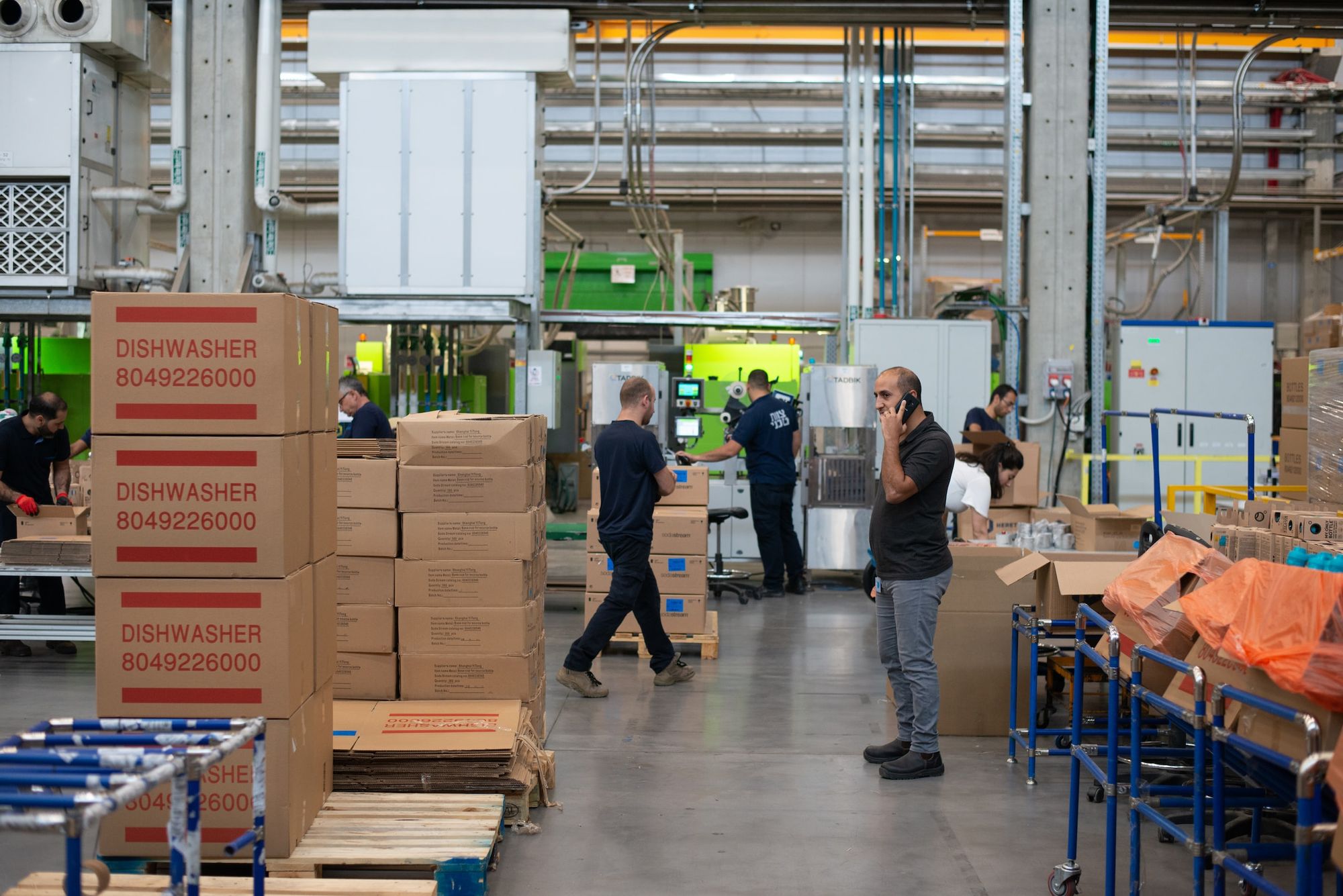
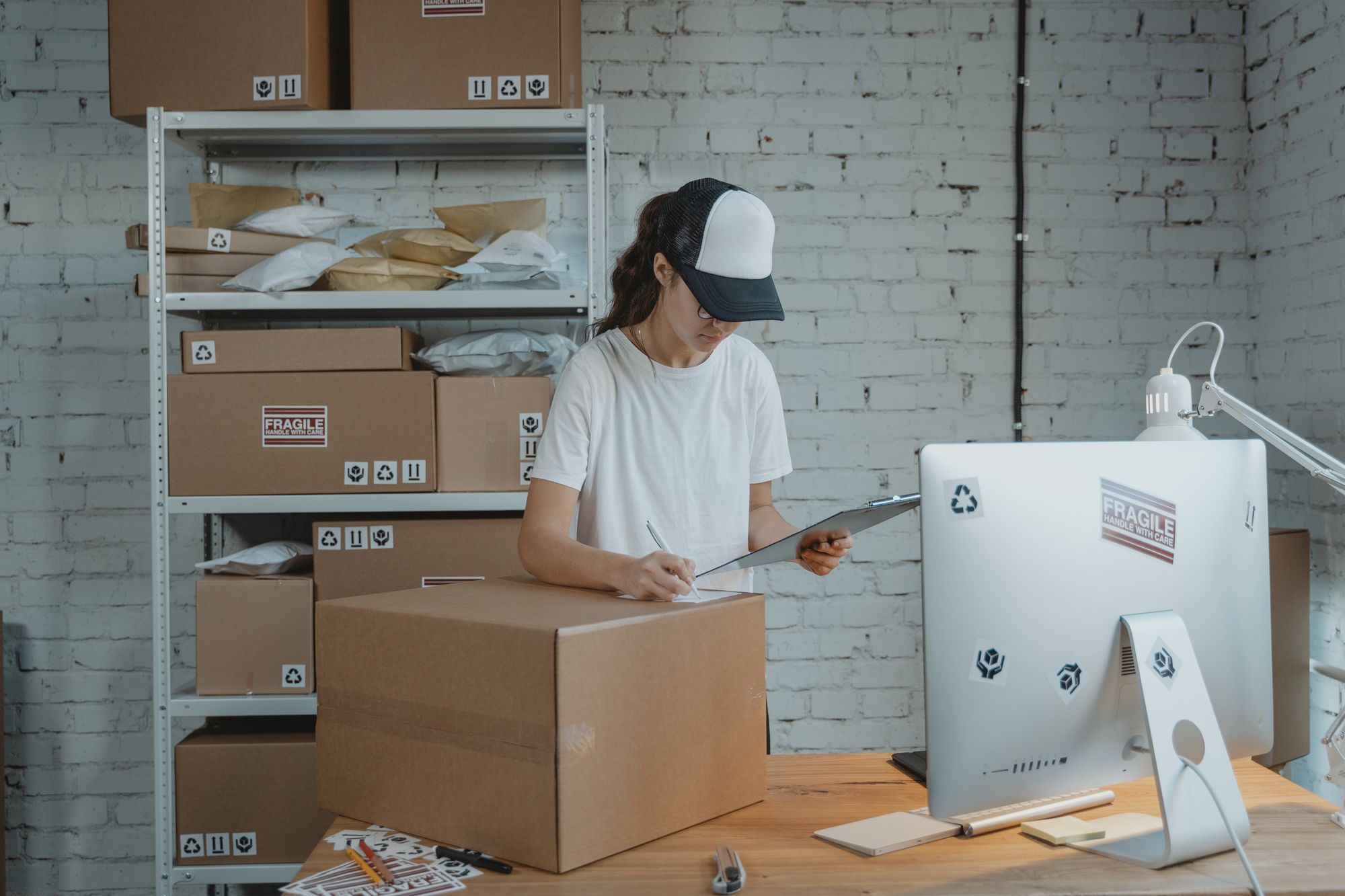
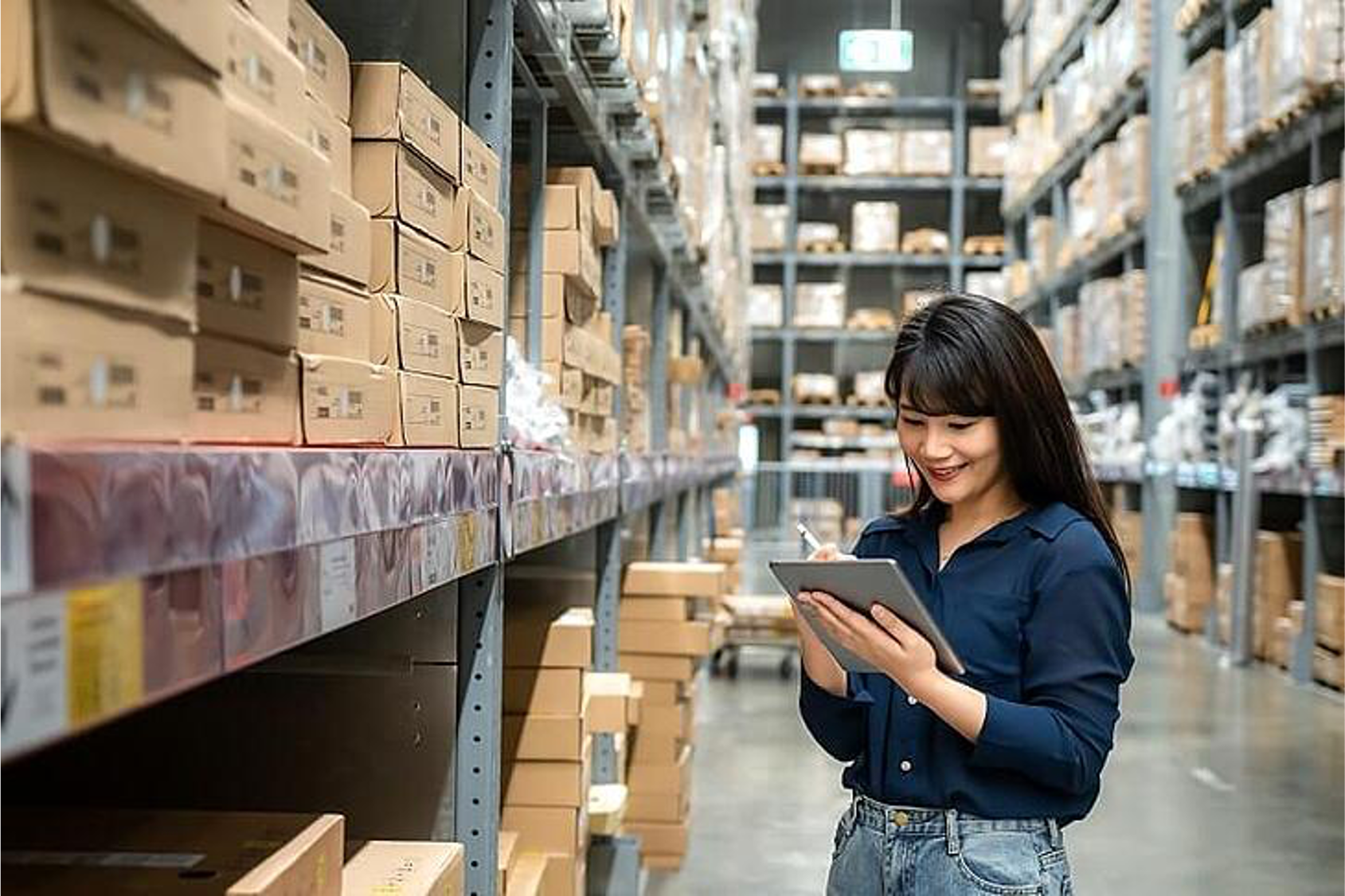